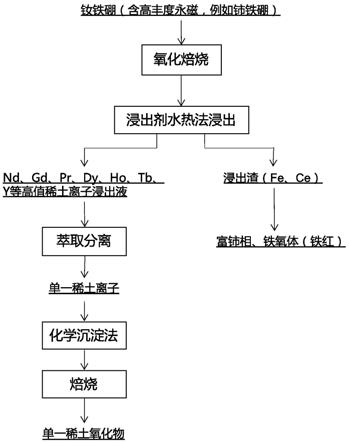
1.本发明涉及稀土分离回收,资源二次利用领域。具体涉及一种利用铵盐以及离子液体在高温高压下水热法溶萃一体化绿色浸出回收稀土永磁废料中稀土金属的方法。
背景技术:
2.因具有特殊的物理和化学性质,稀土元素被广泛应用于各种高新技术领域,从而已经成为我们现代生活所不可缺少的元素。轻稀土在地壳中普遍丰度高,资源充沛,但中重稀土资源稀缺,往往供不应求,而很多产业的发展又离不开中重稀土。例如,电机中高矫顽力的磁体中,中重稀土是必不可少的。据估计,镨、钕、镝、铽的需求量每年都会增加,其中如稀土镝在2020年需求将超过800吨,高于2011年的400吨,但它的储备并不丰富,虽然大部分在中国南方,但长期开采的策略是不可持续的。因此,为了减轻供应风险,平衡资源的利用,稀土二次资源的综合回收利用,近年越来越收到重视。
3.每年,在中国稀土消耗量最多的就是永磁材料,但在钕铁硼生产过程中,会产生约30%的废料,其中含有30%左右的高价值稀土元素,此外,钕铁硼稀土永磁材料广泛应用于硬盘驱动器、风力发电机、电动助力转向、混合动力和电动汽车、电动自行车、电子消费品和家用电器等新技术和产品上。这些产品有使用年限,到期失效。例如,音圈电机使用年限为8年、混合动力/电动汽车使用年限为15年、消费电机使用年限为15年、风电电机使用年限为20年等。2017年中国风电装机容量超过188gw,每装机1.5mw容量,约需要1吨钕铁硼永磁体。因此,回收稀土重要资源,可以平衡需求,并为稀土资源的高效利用提供重要的支撑。
4.自2000年以来,我国风电装机容量逐年增加,尤其近10年来增长迅猛。其中以钕铁硼为例,2016年全球报废稀土钕铁硼永磁体总量在5~6万吨,中国占比60%以上,且报废量逐年增加。在钕铁硼稀土永磁材料中镨、钕、镝等稀土元素含量高达25~30%,其余主要是金属铁、钴、镍,以及元素硼等。大量的废旧钕铁硼稀土永磁体如果得不到回收,将不但产生大量的污染源和二次污染,而且会造成资源浪费,有悖于循环经济的发展。因此,从废旧稀土永磁材料中回收金属元素不仅有助于生态环境保护,而且可以缓解稀土资源危机和促进资源循环生产,这对环境保护和经济发展都具有重要意义。
5.而目前,稀土永磁废料虽然实现了产业化回收,但是目前主要以湿法和火法两种方法为主。其中湿法主要以全浸出为主,浸出方法工艺复杂、操作困难、酸耗量大、有废气排放,且为了达到高浸出率,对废料的目数要求严苛,不仅拉高回收成本而且一定程度上造成环境污染,且全元素浸出,还要进行后续萃取工艺进行分离。火法工艺是依据物料中元素的赋存状态,或者借助氧化还原反应改变物料中元素化学状态,高温下回收合金的冶金过程。火法工艺具有流程短、环境友好、产品附加值高等优点,但与湿法工艺比较,火法工艺处理量小,回收率低,能耗高,回收成本高,对原料品质要求高。
6.由此可见,提出一种新型绿色高效的废料及废旧产品中回收稀土二次资源的方法,从而有效克服以往工艺缺陷,最大化提高稀土回收价值,实现稀土资源的循环利用,是
稀土可持续发展的迫切需要和必然选择。
技术实现要素:
7.为了克服上述技术问题,本发明提供一种利用水热法溶萃一体化绿色浸出回收稀土永磁废料中稀土金属的新方法,通过利用铵盐以及离子液体一系列结构类似的浸出剂,在高温高压下溶萃回收稀土永磁废料中的稀土元素。本发明方法可以在回收第一步溶解部分的同时分离铁与稀土元素,因此无需进一步萃取除铁步骤,从而有效地缩短了回收工艺流程,且本发明方法具有浸出率高、分离率高、浸出剂廉价易得、环境友好等优点,并结合了液-液相分离的冶金学特点和多金属组分在液相分离系统中的选择性分配规律,从而有效解决了稀土永磁废料中包括稀土和铁以及硼元素的综合高效回收和循环再利用等问题,因此具有可观的经济和社会环境保护效益。
8.本发明是通过如下技术方案实现所述技术效果的:
9.一种回收稀土永磁废料中稀土金属的浸出剂,包括甜菜碱盐酸盐以及一系列结构类似的铵盐及离子液体化合物,其结构式如下:
[0010][0011]
式中,x代表阴离子,例如x可以为tf2n-,pf
6-,bf
4-,f-,cl-,br-,i-等中的一种;r1,r2,r3分别代表c
nh4n-2
(n=1-16);r4代表c1-c8的碳链;r5代表c。
[0012]
本发明提供一种利用铵盐水热法溶萃一体回收稀土永磁废料中稀土的方法,包括以下步骤:
[0013]
(1)预处理:将稀土永磁加入洗涤液进行洗涤,除去其中有机物等杂质后水洗离心并干燥,研磨至成小颗粒;
[0014]
(2)氧化焙烧:将研磨后的稀土永磁均匀平铺在坩埚内在马弗炉里氧化焙烧,得到稀土永磁的氧化物;
[0015]
(3)溶萃一体浸出:用铵盐浸出剂对氧化物进行溶萃一体化浸出,浸出稀土元素的基础上实现铁与稀土的分离,其率先溶萃稀土离子,使稀土离子进入液相,铁留在废渣当中;
[0016]
(4)分离:恢复室温后,将液相固相分离,得到稀土离子溶液和废渣,以备后续实验进行。
[0017]
根据本发明的实施方案,步骤(1)中所回收的稀土永磁的化学组成主要包括过渡金属元素、轻稀土元素和中稀土元素。
[0018]
根据本发明的实施方案,所述过渡金属元素主要包括fe、al、co、cu;所述轻稀土元素包括ce、pr、nd、sm;所述中稀土包括gd、dy、tb。
[0019]
根据本发明的实施方案,步骤(1)中水洗干燥后的废渣在研钵中进行研磨后过筛,筛目优选为150-250目。
[0020]
根据本发明的实施方案,步骤(2)中氧化焙烧稀土永磁使金属相完全氧化成最高价氧化物的温度,经由热重测试测得。
[0021]
根据本发明的实施方案,步骤(2)中氧化温度为800-1000℃;示例性为800℃,900℃,1000℃;优选为900℃。
[0022]
根据本发明的实施方案,步骤(2)中氧化时间为2-8h;优选为3-6h;示例性为2h,3h,4h,5h,6h,7h,8h。
[0023]
根据本发明的实施方案,步骤(3)浸出过程使用的铵盐浸出剂的用量应大于理论用量,浸出时间为2-8h;优选为5-8h;示例性为2h,5h,8h。
[0024]
根据本发明的实施方案,步骤(3)浸出温度为150-250℃;优选为180~220℃;示例性为150℃,180℃,200℃,220℃,250℃。
[0025]
根据本发明的实施方案,步骤(3)浸出剂铵盐浓度为0.2-1.0m,固液比0.5-5g/l;铵盐浸出剂的摩尔质量为金属离子总量的100-500%,浸出后得到液-固混合物料。
[0026]
根据本发明的实施方案,步骤(4)中利用过滤器进行固液分离,滤渣经过水系干燥待进一步检测。
[0027]
根据本发明的实施方案,步骤(4)中得到的固相废渣中,主要含有90-99%铁的氧化物,少量的b以及微量的稀土元素,经精炼后可以得到铁红以进行二次利用。在得到的浸出液相中,nd、pr、gd的浸出率可以达到总量的93-99.9%,其中浸出率顺序为pr》gd》nd,铁元素的浸出率小于1.9%,然后混合稀土含有nd、pr、gd以及dy或tb以离子态存在于溶液中,萃取分离后可优选草酸沉淀处理得到单一和/或混合稀土氧化物,和/或通过溶剂萃取的方法获得高纯单一稀土氧化物,用于生产稀土永磁材料。
[0028]
本发明的设计思想是:
[0029]
考虑到以往浸出经验,盐酸作为浸出剂具有优秀的效果,其中氯离子的存在必不可少。并且,根据应用情况,离子液体也被认为是绿色溶剂,在以往的研究中,[hbet][tf2n]被提出用于稀土的选择性溶解,而不溶解钕铁硼废渣中的其他成分。氧化铁和氧化铝不能溶于[hbet][tf2n]中,这与回收利用高度相关,所以理论上优选离子液体作为浸出剂。稀土离子由甜菜碱配体进行配位,溶解是由位于离子液体阳离子上的羧酸基团的反应性驱动的,甜菜碱配体是一种退质子时的两性离子化合物。[hbet][tf2n]中的阴离子只是作为旁观者阴离子,不参与络合物的形成,[tf2n]的存在意义在于形成一种疏水离子液体。然而,对于ndfeb废料的固相浸出并不需要疏水相,而[hbet][cl]是一种水溶性盐,相较于离子液体非常廉价易得,羧基和氯离子对稀土离子的浸出有协同效果,在没有与离子液体进行接枝的情况下,就可以在低成本条件下拥有高度选择性以及浸出率,符合资源回收的理念,可以将废料中的稀土元素一次性溶萃到液相当中。
[0030]
本发明的优点以及有益效果是:
[0031]
(1)本发明首次提出在反应釜内以铵盐作为浸出剂进行高温高压浸出,有效解决了传统工艺有废气排放、浸出剂利用率低等节能环保问题,最大化的提高了稀土永磁废料的回收价值,实现了稀土二次资源的循环利用。
[0032]
(2)采用本发明提供的技术方案,在高压釜中,采用铵盐高温高压浸出工艺,有利于物料之间的裂解渗透、溶胀,使盐酸与物料接触更充分,动力学条件更优越,故对浸出原料粒度要求范围宽,最低只需100目,从而避免了因原料的精细研磨过程而产生的大量粉
[0049]
re o2→
re2o3[0050]
钕铁硼废料经焙烧后物料中铁主要以高价铁氧化物fe2o3的物相存在,稀土主要以re2o3、rebo3和refeo3的物相存在。如图2所示,为废磁泥热重曲线,以确定完全氧化温度。
[0051]
(3)溶萃一体浸出
[0052]
用铵盐对氧化物进行溶萃一体化浸出,浸出稀土元素的基础上实现铁与稀土的分离,率先结合稀土离子,使稀土离子进入液相,铁留在废渣当中。铵盐用量为理论用量的1.05倍以上,浸出时间为2-8h,浸出温度为150-250℃,浸出剂铵盐浓度为0.2-1.0m,固液比0.5-5g/l。
[0053]
废料中可溶性组分为re2o3、al2o3、feo、b2o3,溶解过程消耗铵盐,铵盐浸出剂结构式如图3所示,它是一种水溶性盐,羧基和氯离子有协同效果,可以将废料中的99%稀土元素一次性溶萃到液相当中。
[0054]
(4)分离
[0055]
恢复室温后,将液相固相分离,得到稀土离子溶液和废渣,以备后续实验进行。在得到的浸出液相中,nd、pr、gd的浸出率可以达到总量的93-99%,其中浸出率顺序为pr》gd》nd,铁元素的浸出率小于总量的1%,然后混合稀土含有nd、pr、gd以及dy或tb以离子态存在于溶液中,萃取分离或直接草酸处理得到稀土单一或混合氧化物,用于生产钕铁硼永磁材料。
[0056]
下面结合具体实施方式进行说明:
[0057]
本发明以下各实施例选用的钕铁硼废磁泥,化学成分(质量百分数)为:
[0058][0059]
氧化焙烧后的主要成分为:
[0060][0061]
实施例1
[0062]
一种利用铵盐水热法溶萃一体回收稀土永磁废料中稀土金属的新方法,包括以下步骤:
[0063]
(1)将市面上收购的废旧钕铁硼磁泥水洗醇洗后烘干备用,烘干后的废料研磨后过筛200目使粒度均匀便于氧化以及浸出;
[0064]
(2)通过热重曲线测得完全氧化温度,将废料粉末均匀分布在刚玉坩埚内在900℃温度下6h完全氧化,使非磁泥中的金属元素转化为最高价氧化物,氧化后得到深红色混合金属氧化物;
[0065]
(3)取部分稀土永磁的氧化物置于水热釜中,按照3.33g/l的固液比加入0.2m甜菜碱盐酸盐水溶液,在200℃温度下保温静置浸出8h,浸出后得到液-固混合物料;
[0066]
(4)反应后混合物用过滤器进行固液分离,将浸出液进行检测得到如下浸出率。
[0067]
元素cefegdndpr浸出率(%)56.240.295.5197.0599.81
[0068]
由上表结果可得稀土平均浸出率可以达到97%以上,而fe的浸出率只有0.2%。由此表明甜菜碱盐酸盐对稀土金属元素表现出了极高的选择性,从而实现了废旧钕铁硼中稀土金属元素的溶萃一体化浸出回收过程。
[0069]
实施例2
[0070]
一种利用铵盐水热法溶萃一体回收稀土永磁废料中稀土金属的新方法,包括以下步骤:
[0071]
(1)将市面上收购的废旧钕铁硼磁泥水洗醇洗后烘干备用,烘干后的废料研磨后过筛200目使粒度均匀便于氧化以及浸出;
[0072]
(2)通过热重曲线测得完全氧化温度,将废料粉末均为分布在刚玉坩埚内在900℃温度下3h完全氧化,使非磁泥中的金属元素转化为最高价氧化物,氧化后得到深红色混合金属氧化物;
[0073]
(3)取部分稀土永磁的氧化物置于水热釜中,按照3.33g/l的固液比加入0.5m甜菜碱盐酸盐水溶液,在200℃温度下保温静置浸出5h,浸出后得到液-固混合物料;
[0074]
(4)反应后混合物用过滤器进行固液分离,将浸出液进行检测得到如下浸出率。
[0075]
元素cefegdndpr浸出率(%)76.021.8698.6598.6299.40
[0076]
由上表结果可得稀土平均浸出率可以达到98%以上,而fe的浸出率只有1.86%。由此表明甜菜碱盐酸盐对稀土金属元素表现出了极高的选择性,从而实现了废旧钕铁硼中稀土金属元素的溶萃一体化浸出回收过程。
[0077]
实施例3
[0078]
一种利用铵盐水热法溶萃一体回收稀土永磁废料中稀土金属的新方法,包括以下步骤:
[0079]
(1)将市面上收购的废旧钕铁硼磁泥水洗醇洗后烘干备用,烘干后的废料研磨后过筛200目使粒度均匀便于氧化以及浸出;
[0080]
(2)通过热重曲线测得完全氧化温度,将废料粉末均为分布在刚玉坩埚内在900℃温度下6h完全氧化,使非磁泥中的金属元素转化为最高价氧化物,氧化后得到深红色混合金属氧化物;
[0081]
(3)取部分稀土永磁的氧化物置于水热釜中,按照5g/l的固液比加入0.5m[hbet][ntf2]水溶液,在200℃温度下保温静置浸出8h,浸出后得到液-固混合物料;
[0082]
(4)反应后混合物用过滤器进行固液分离,将浸出液进行检测得到如下浸出率。
[0083]
元素cefegdndpr浸出率(%)33.251.4789.2092.8394.91
[0084]
由上表结果可得稀土平均浸出率可以达到92%以上,而fe的浸出率只有1.47%。由此表明[hbet][ntf2]对稀土金属元素表现出了极高的选择性,从而实现了废旧钕铁硼中稀土金属元素的溶萃一体化浸出回收过程。
[0085]
实施例4
[0086]
一种利用铵盐水热法溶萃一体回收稀土永磁废料中稀土金属的新方法,包括以下步骤:
[0087]
(1)将市面上收购的废旧钕铁硼磁泥水洗醇洗后烘干备用,烘干后的废料研磨后过筛200目使粒度均匀便于氧化以及浸出;
[0088]
(2)通过热重曲线测得完全氧化温度,将废料粉末均为分布在刚玉坩埚内在900℃温度下6h完全氧化,使非磁泥中的金属元素转化为最高价氧化物,氧化后得到深红色混合金属氧化物;
[0089]
(3)取部分稀土永磁的氧化物置于水热釜中,按照5g/l的固液比加入1m[hbet]br水溶液,在200℃温度下保温静置浸出5h,浸出后得到液-固混合物料;
[0090]
(4)反应后混合物用过滤器进行固液分离,将浸出液进行检测得到如下浸出率。
[0091]
元素cefegdndpr浸出率(%)33.250.6490.3794.5695.12
[0092]
由上表结果可得稀土平均浸出率可以达到93%以上,而fe的浸出率只有0.64%。由此表明[hbet]br对稀土金属元素表现出了极高的选择性,从而实现了废旧钕铁硼中稀土金属元素的溶萃一体化浸出回收过程。
[0093]
当然,除了实施例1至实施例4列举的情况,其他处理过程中的参数、原料组分的比例等均可以实现稀土永磁废料中稀土金属的一体化回收。
[0094]
综上所述,本发明方法可以在回收第一步溶解部分分离铁与稀土元素,不需要进一步萃取除铁,有效地缩短了回收工艺流程、浸出率高、分离率高、浸出剂廉价易得、环境友好,结合液-液相分离的冶金学特点和多金属组分在液相分离系统中的选择性分配规律,解决钕铁硼废料包括稀土和铁以及硼元素的综合高效回收和循环再利用等问题,具有可观的经济、社会环境保护效益。
[0095]
以上,对本发明的实施方式进行了说明。但是,本发明不限定于上述实施方式。凡在本发明的精神和原则之内,所做的任何修改、等同替换、改进等,均应包含在本发明的保护范围之内。
再多了解一些
本文用于企业家、创业者技术爱好者查询,结果仅供参考。