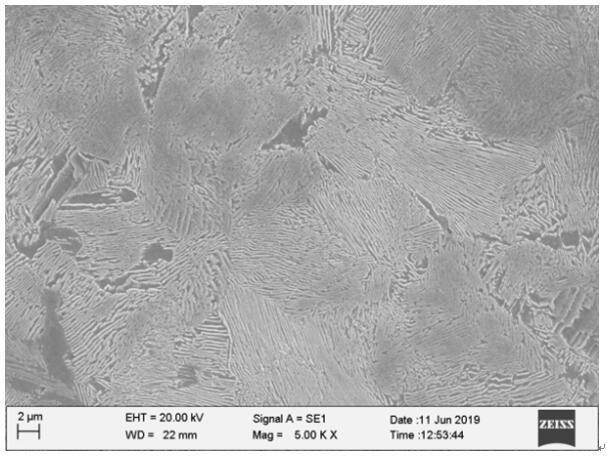
一种车辆减震弹簧钢65mn盘条生产工艺
技术领域
1.本发明属于弹簧钢生产技术领域,具体涉及一种车辆减震弹簧钢65mn盘条生产工艺。
背景技术:
2.由于摩托车和电动车行业的迅速发展,对弹簧钢的需求量越来越大。目前国内弹簧钢主要以电炉生产。由于弹簧钢丝工作环境比较恶劣,因此性能要求比较严格;同时由于弹簧本身长度较短,弹簧的制作过程实际上是对盘条通条性能的检验、考核过程,工艺要求高,许多线材生产厂家无实力生产此类产品。弹簧生产企业只能高价进口或者采用高碳钢盘条替代,采用高碳钢盘条生产的弹簧强度低、耐疲劳性能差,产品质量无法提高。
3.弹簧主要作用是储存弹性应变能、减轻震动和冲击。弹簧一般在动负荷(反复弯曲应力和反复扭转应力)条件下使用,故要求弹簧钢具有极高的弹性极限、高的屈服强度、抗拉强度、高的屈强比以及高的抗疲劳性能,并有足够的塑性和韧性,较好的淬透性和低的脱碳敏感性,以便于在高冷状态下易于成型和热处理后获得所需的性能。
4.车辆减震弹簧钢65mn盘条在后续加工过程中需要进行表面除鳞、冷拉拔、热处理等工艺,所以对其表面质量有较高的要求。车辆减震弹簧钢65mn盘条要求具有较高的洁净度和成分均匀性,需严格控制表面脱碳层。要保证均匀的组织及性能,否则会引起盘条的通条性能不均匀,造成拉拔过程断丝率偏高,影响成品的成材率。
5.由于车辆减震弹簧的受力特点和工作特点,弹簧钢表面脱碳层会明显降低弹簧的疲劳寿命。需要对车辆减震弹簧盘条的轧制工艺和加热工艺进行系统的研究,达到优化车辆减震弹簧钢65mn的金相组织及综合性能的目的。
技术实现要素:
6.本发明提供了一种车辆减震弹簧钢65mn盘条生产工艺,目的在于解决上述技术问题。
7.为此,本发明采用如下技术方案:一种车辆减震弹簧钢65mn盘条生产工艺,减震弹簧钢65mn盘条化学成分按重量百分比计为:c:0.62%~0.68%,si:0.17%~0.30%,mn:0.90%~1.00%,p:≤0.015%,s:≤0.015%,其余为fe及不可避免的杂质。生产工艺包括铁水脱硫、转炉冶炼、吹氩、lf精炼、连铸、方坯加热、高线轧制、斯太尔摩控冷。
8.铁水脱硫工序中,入厂铁水各元素重量百分比含量为:s≤0.045%、mn≤0.90%、cu≤0.030%,si≤0.080%,来料铁水温度≥1250℃,铁水扒渣;转炉冶炼工序中,挡渣出钢,渣层厚度≤50mm,中渣碱度r控制在3.0~3.5,终点碳控制≤70%,氧控制在0.040~0.070%,出钢目标温度1490~1515℃;lf精炼工序中,控制炉渣碱度3.0~4.0,使用含sio2、al2o3、cao的材料造白渣,调整炉渣流动性;
连铸工序中,采用全程保护浇铸,采用全程保护浇铸,减少外来夹杂物的卷入,保证钢水良好的流动性,防止水口结瘤;同时采用低过热度浇铸和电磁搅拌,铸坯拉速控制在1.6~1.8m/min;方坯加热工序时,控制加热段温度1030~1070℃,均热段温度1090~1120℃,断面温度差≤30℃,在炉时间120
±
30min;高线轧制工序中,控制开轧温度1000
±
50℃,开轧温度要保证钢在粗轧和中轧过程中的温度避开热脆区,并使钢的塑性尽量高,但开轧温度过高,意味着在炉温度也要高,对该钢来说在炉温度过高会使钢变形,变形的轧件往往会造成轧线的堆钢事故;精轧机入口温度900
±
20℃,为了控制钢的强度,精轧机入口温度和吐丝温度之差不能太大,减定径机温度880
±
20℃;斯太尔摩控冷工序中,控制吐丝温度880
±
15℃;斯太尔摩控冷线辊道速度设定方法为:φ6.5~8.0mm规格的钢,入口速度0.88~1.12m/s,最大速度1.35~1.49m/s;φ10~12.0mm规格的钢,入口速度为0.79~1.35m/s,最大速度为1.45~1.69m/s。
9.本发明与现有技术相比,运用了高线机组的设备优势,高温轧制成盘条采用8 4机型的精轧机、减定径机组。通过优化轧制前的加热制度、控制轧制、控制冷却工艺,降低了盘条的表面脱碳,提供成品弹簧的疲劳寿命,改善了金相组织以获得高索氏体提高车辆减震弹簧钢盘条的强度和塑性,达到了优化车辆减震弹簧钢65mn热轧盘条的金相组织和综合性能的目的。
附图说明
10.图1是原工艺吐丝温度为900℃条件下5000
×
倍金相组织照片;图2是本发明吐丝温度为850℃条件下5000
×
倍金相组织照片;图3是原工艺吐丝温度为900℃条件下15000
×
倍金相组织照片;图4是本发明吐丝温度为850℃条件下15000
×
倍金相组织照片;图5是原工艺吐丝温度为900℃条件下25000
×
倍金相组织照片;图6是本发明吐丝温度为850℃条件下25000
×
倍金相组织照片;图7是原工艺吐丝温度为900℃条件下盘条一侧总脱碳层(铁素体 过渡层)检验照片;图8是本发明吐丝温度为850℃条件下盘条一侧总脱碳层(铁素体 过渡层)检验照片。
具体实施方式
11.下面结合附图对本发明作进一步说明:一种车辆减震弹簧钢65mn盘条生产工艺,减震弹簧钢65mn盘条化学成分按重量百分比计为:c:0.62%~0.68%,si:0.17%~0.30%,mn:0.90%~1.00%,p:≤0.015%,s:≤0.015%,其余为fe及不可避免的杂质。生产工艺包括铁水脱硫、转炉冶炼、吹氩、lf精炼、连铸、方坯加热、高线轧制、斯太尔摩控冷。
12.铁水脱硫工序中,入厂铁水各元素重量百分比含量为:s≤0.045%、mn≤0.90%、cu≤0.030%,si≤0.080%,来料铁水温度≥1250℃,铁水扒渣。
13.转炉冶炼工序中,挡渣出钢,渣层厚度≤50mm,中渣碱度r控制在3.0~3.5,终点碳控制≤70%,氧控制在0.040~0.070%,出钢目标温度1490~1515℃。
14.lf精炼工序中,控制炉渣碱度3.0~4.0,使用专用材料造白渣,调整炉渣流动性。
15.连铸工序中,采用全程保护浇铸,采用全程保护浇铸,减少外来夹杂物的卷入,保证钢水良好的流动性,防止水口结瘤;同时采用低过热度浇铸和电磁搅拌,铸坯拉速控制在1.6~1.8m/min。
16.方坯加热工序时,控制加热段温度1030~1070℃,均热段温度1090~1120℃,断面温度差≤30℃,在炉时间120
±
30min。
17.高线轧制工序中,控制开轧温度1000
±
50℃,开轧温度要保证钢在粗轧和中轧过程中的温度避开热脆区,并使钢的塑性尽量高,但开轧温度过高,意味着在炉温度也要高,对该钢来说在炉温度过高会使钢变形,变形的轧件往往会造成轧线的堆钢事故;精轧机入口温度900
±
20℃,为了控制钢的强度,精轧机入口温度和吐丝温度之差不能太大,减定径机温度880
±
20℃。
18.斯太尔摩控冷工序中,控制吐丝温度880
±
15℃;斯太尔摩控冷线辊道速度设定方法为:φ6.5~8.0mm规格的钢,入口速度0.88~1.12m/s,最大速度1.35~1.49m/s;φ10~12.0mm规格的钢,入口速度为0.79~1.35m/s,最大速度为1.45~1.69m/s。
19.具体而言车辆减震弹簧钢65mn钢盘条的生产工艺参考下述实施例:详细步骤如下:高炉铁水
→
50吨转炉炼钢
→
lf炉外精炼
→
保护浇注
→
钢坯检查
→
钢坯入炉
→
步进式加热炉加热
→
高压水除鳞
→
粗轧六架轧制
→
1#飞剪切头
→
中轧六架轧制
→
2#飞剪切尾
→
中轧四架轧制
→
预精轧四架轧制
→
zn1wb1水冷箱冷却
→
精轧机八架轧制
→
zn2wb2水冷箱冷却
→
减定径四架轧制
→
zn3wb2水冷箱冷却
→
吐丝机吐丝
→
散卷冷却
→
集卷收集
→
p/f线钩式运输机运输
→
精整取样、检查修整
→
瑞典打包机打包
→
称重挂牌
→
卸卷
→
盘条入库
→
成品外发。
20.其中,加热炉中的连铸坯加热条件控制如下表所示:预热段的中间测温点控制在880-920℃之间,炉内气氛以还原性为主,使连铸坯头、中、尾的温度差不超过30℃。
21.盘条进入精轧机入口温度为860-880℃,盘条进入减定径机组入口温度为860-880℃,吐丝温度控制为870-890℃。
22.轧后控制冷却采用标准型斯太尔摩控冷线进行,斯太尔摩辊道速度及风机风量如下表。使冷却后进入集卷筒的盘条搭接点温度≤450℃。
23.此表为现场不同规格斯太尔摩控冷工序中风机开启量。
24.本实施例中所要达到的力学性能指标如下表所示:由上表可知,试制的∮6.5~∮12.0mm车辆减震弹簧钢盘条力学性能均达到内控要求值,且断面收缩率普遍远高于内控要求值,盘条的索氏体化率基本控制在90%,力学性能优异。根据本发明的车辆减震弹簧钢65mn盘条具备拉拔前期铅浴淬火后盘条的力学性能,由此可以满足取消前期的铅浴淬火工艺的要求。
25.综上所述,采用本发明的车辆减震弹簧钢65mn盘条的生产工艺,可以充分利用目前高速线材轧制的先进生产装备以及配套的轧制谁冷却系统及斯太尔摩控冷线,并通过控温控轧技术控制高碳钢盘条的金相组织,获得较高的索氏体率。不仅取得盘条较好的强韧性配合,而且可以取消拉拔前期的铅浴淬火工艺,降低环境污染,达到了绿色环保的要求。
再多了解一些
本文用于企业家、创业者技术爱好者查询,结果仅供参考。