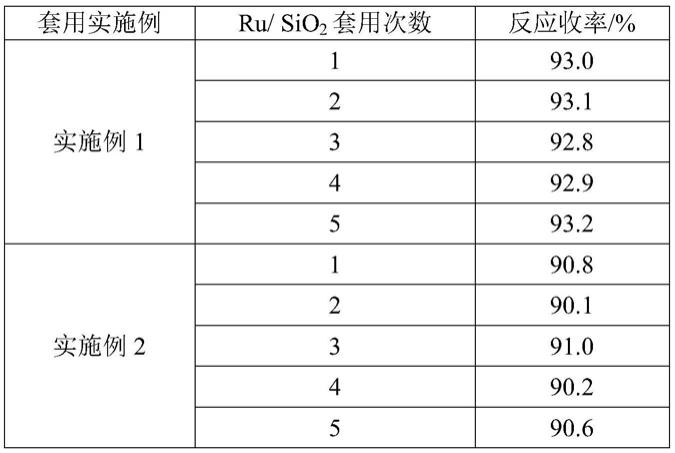
一种一锅法制备
β
‑
胡萝卜素的方法
技术领域
1.本发明涉及一种制备β
‑
胡萝卜素的方法,尤其涉及一种一锅法制备β
‑
胡萝卜素的方法。
背景技术:
2.β
‑
胡萝卜素是维生素a类中的重要组成,广泛应用于饲料、食品和药品领域,有着非常广阔的市场前景。
3.现有技术以维生素a为原料合成β
‑
胡萝卜素,一般是先分别制成维生素a三苯基膦盐和维生素a醛,二者再进一步反应生成β
‑
胡萝卜素,详见法国专利fr1383944a;但相应的产品收率较低,该专利报道仅为19.11%,而且维生素a醛化学性质不稳定,不适合工业化生产。反应表达式如下:
[0004][0005]
bernhard schulz等,于1977年报道了两分子维生素a三苯基膦盐通过氧化偶联反应直接制备β
‑
胡萝卜素,该方法工艺简单,反应收率更高。反应表达式如下:
[0006][0007]
专利cn101041631a、cn108047112a通过上述方法并采用次氯酸盐、过氧化物等强氧化剂进行氧化偶联反应,但强氧化剂会破坏反应中生成的β
‑
胡萝卜素,导致反应收率大幅降低;而且工业化过程中大量使用过氧化物有一定的危险性。
[0008]
专利cn101081829a通过两相反应避免氧化剂破坏产物β
‑
胡萝卜素,但同时两相反应导致反应中间体无法快速转化为β
‑
胡萝卜素,反应收率偏低。
[0009]
专利cn110452147a以氧气作氧化剂,在环糊精类化合物相转移催化剂、钯催化剂及弱碱性化合物存在下使维生素a三苯基膦盐氧化偶联制备β
‑
胡萝卜素,但钯催化剂价格昂贵、杂质耐受性差,并且不能回收利用,该方法不适用于工业化生产。
技术实现要素:
[0010]
为了解决以上技术问题,本发明提出一种一锅法制备β
‑
胡萝卜素的方法。本发明在钌催化剂和弱碱的催化下,采用分子氧为氧化剂,以维生素a为原料通过一锅法制备β
‑
胡萝卜素。该方法工艺简单,安全性好,反应收率高,并且钌催化剂价格便宜、杂质耐受性好并且在本反应体系中可以多次套用,有效降低了生产成本。
[0011]
为实现上述目的,本发明所采用的技术方案如下:
[0012]
一种一锅法制备β
‑
胡萝卜素的方法,包括以下步骤:
[0013]
a、使维生素a与三苯基膦在醇类溶剂中反应,制得包含维生素a三苯基膦盐的反应液;
[0014]
b、向步骤a获得的反应液中加入钌催化剂和弱碱,并以分子氧为氧化剂,使维生素a三苯基膦盐氧化偶联生成β
‑
胡萝卜素。
[0015]
本发明以分子氧作为氧化剂,由于分子氧本身的氧化性较弱,且反应中生成的β
‑
胡萝卜素以固体形式存在,因此可以避免对产品β
‑
胡萝卜素造成破坏,提高反应收率;并且成本低,安全性好。
[0016]
钌催化剂在步骤b反应体系中具有较高的氧化活性,可以催化维生素a三苯基膦盐快速氧化生成活性中间体,该活性中间体在弱碱的催化作用下,随着浓度的提升可以更高效的偶联生成β
‑
胡萝卜素;此外,钌催化剂还可以为分子氧提供附着位点,弥补分子氧氧化性不足的问题,有效提升反应的速度和收率。
[0017]
进一步地,步骤a中,维生素a与三苯基膦的添加量按摩尔比计,为1:(1
‑
1.8),优选1:(1
‑
1.5)。
[0018]
进一步地,所述维生素a为维生素a醇、维生素a醋酸酯中的至少一种或包含它们中任意一种或多种的结晶母液。
[0019]
进一步地,步骤a中反应在强酸的作用下进行,且强酸的用量为维生素a摩尔量的1
‑
1.5倍,优选1.1
‑
1.2倍;
[0020]
优选地,所述强酸为硫酸、盐酸、氢溴酸、对甲苯磺酸中的一种或多种。
[0021]
所述醇类溶剂为甲醇、乙醇、丙醇、异丙醇等小分子醇中的一种或多种,优选醇类溶剂的用量为维生素a质量的2
‑
8倍,更优选4
‑
6倍。
[0022]
进一步地,步骤a中反应条件为:先在
‑
10~5℃下、0.5
‑
1h内向反应体系中加入强酸,然后室温反应5
‑
12h。
[0023]
进一步地,所述钌催化剂为负载型催化剂,其中金属钌的负载量为0.1
‑
0.5%,优选0.1
‑
0.3%,所述钌催化剂优选ru/sio2、ru/活性炭、ru/硅藻土、ru/硅胶中的一种或多种,更优选ru/sio2。
[0024]
本发明对所述钌催化剂的来源不做任何限制,可以是通过市售商业途径购买获得,例如ru/sio2和ru/活性炭催化剂可以通过江苏欣诺科催化剂有限公司购买;市面购买不到的钌催化剂选型也可以通过常规催化剂制备方法如浸渍法、共沉淀法、共混合法等进行简单制备。
[0025]
进一步地,所述弱碱为碳酸钠、碳酸钾、碳酸氢钠、碳酸氢钾中的一种或多种,优选碳酸钠或碳酸钾。
[0026]
进一步地,所述钌催化剂的用量以金属钌的摩尔量计,为维生素a摩尔量的0.05
‑
2%,优选0.1
‑
0.5%;
[0027]
优选地,所述弱碱的用量为维生素a摩尔量的1.2
‑
3倍,优选1.2
‑
1.6倍。
[0028]
进一步地,所述分子氧的存在形式为含氧气的混合气体,其中氧气含量以体积分数计为15
‑
100%;所述分子氧优选为空气;
[0029]
进一步地,步骤b中反应在水的存在下进行,水的添加量优选为步骤a中维生素a质量的1
‑
2.5倍,优选1.5
‑
2倍。
[0030]
优选地,所述分子氧的用量通过反应压力进行控制,所述反应压力为0.5
‑
5mpa,优选1.5
‑
2.5mpa。
[0031]
进一步地,步骤b中反应温度为0
‑
40℃,优选5
‑
15℃;反应时间为5
‑
24h,优选7
‑
10h。
[0032]
本发明步骤b中反应完成后,固体为钌催化剂和β
‑
胡萝卜素的混合物,而无机盐和三苯基氧膦等杂质存在于流动相中,通过简单过滤再用二氯甲烷溶解即可得到产品β
‑
胡萝卜素,并高效回收钌催化剂。
[0033]
本发明与现有技术相比,有益效果如下:
[0034]
1、避免使用双氧水、次氯酸盐和有机过氧化物等强氧化剂,成本低,工艺安全,产品β
‑
胡萝卜素不容易被氧化;
[0035]
2、采用钌催化剂提高维生素a三苯基膦盐的氧化速率,弥补分子氧氧化性不足的问题,产品收率高,反应速率高;
[0036]
3、钌催化剂相较于钯催化剂对反应液中的杂油、成盐反应中生成的脱水产物和异构产物等杂质的耐受性更高,无需对步骤a中反应液进行萃取除杂即可直接用于下一步氧化偶联反应,因此整个反应过程在一个反应釜中即可完成,一锅法制备更有工业应用优势;
[0037]
4、钌催化剂在反应结束后不会失活,并且回收简单,可以多次套用,更有利于工业化生产。
具体实施方式
[0038]
下面通过具体实施例对本发明做进一步说明,本发明所述实施例只是作为对本发明的说明,不限制本发明的范围。
[0039]
一、实施例中主要原料信息:
[0040]
维生素a醋酸酯(280万iu)纯度98%、va结晶母液(包含全反式va醋酸酯42wt%、13
‑
顺式va醋酸酯38wt%、反式va醇14wt%)购自浙江新和成股份有限公司;维生素a醇,纯度≥96%,购自厦门金达威维生素有限公司;
[0041]
三苯基膦,纯度>99%,购自北京伊诺凯科技有限公司;
[0042]
rucl3·
3h2o、亚硝酰硝酸钌水溶液(ru含量31.3%),购自上海源叶生物科技有限公司;ru(so4)2购自上海植信化工有限公司。
[0043]
其它原料和试剂均为通用市售化学纯试剂。
[0044]
二、主要分析方法及仪器:
[0045]
液相色谱表征:安捷伦1260型液相色谱仪,色谱柱sphersorb c18柱(φ4.6
×
250mm),紫外可见分光检测器hitachi l7420,色谱工作站数据处理系统chomatopd c
‑
ria,固定相zorbax
‑
sil。色谱条件:流动相为甲醇/乙腈=9/1(v/v)混合物,检测温度40℃,流速1ml/min,波长455nm。对产品进行定性、定量分析。
[0046]
【准备实施例1】制备ru/sio2催化剂
[0047]
称取0.26g的rucl3·
3h2o固体,溶于500ml的蒸馏水中;向溶液中加入100g二氧化硅后搅拌25min,所得悬浊液超声30min。超声完成后,置于恒温磁力搅拌器中,调节转速为400r/min,设定还原温度30℃。称取0.96g的硼氢化钠,溶于500ml蒸馏水中,置于滴液漏斗,滴加至上述混合溶液中,滴加结束后再恒温搅拌30min。抽滤,用蒸馏水洗涤滤液至中性。真空60℃干燥5h,研磨成粉,制得负载量为0.1%的ru/sio2催化剂。
[0048]
【准备实施例2】制备ru/硅胶催化剂
[0049]
称取0.3g的ru(so4)2固体,溶于700ml的蒸馏水中;向溶液中加入35g硅胶后搅拌
25min,所得悬浊液超声30min。超声完成后,置于恒温磁力搅拌器中,调节转速为400r/min,设定还原温度25℃。称取1.3g的硼氢化钠,溶于700ml蒸馏水中,置于滴液漏斗,滴加至上述混合溶液中,滴加结束后再恒温搅拌30min。抽滤,用蒸馏水洗涤滤液至中性。真空60℃干燥5h,研磨成粉,即得负载量为0.3%的ru/硅胶催化剂。
[0050]
【准备实施例3】制备ru/活性炭催化剂
[0051]
称取0.4g的亚硝酰硝酸钌水溶液,加入200ml蒸馏水稀释;向溶液中加入25g活性炭后搅拌25min,所得悬浊液超声30min。超声完成后,置于恒温磁力搅拌器中,调节转速为400r/min,设定还原温度35℃。称取1.09g的硼氢化钠,溶于500ml蒸馏水中,置于滴液漏斗,滴加至上述混合溶液中,滴加结束后再恒温搅拌30min。抽滤,用蒸馏水洗涤滤液至中性。真空60℃干燥5h,研磨成粉,即得负载量为0.5%的ru/活性炭催化剂。
[0052]
【实施例1】
[0053]
向1l高压釜中加入67.0g维生素a醋酸酯(0.2mol,98%),62.9g三苯基膦(0.24mol),335g甲醇,搅拌下冷却到0℃,维持0
‑
5℃向体系内缓慢加入22g浓硫酸(0.22mol,98%),于1h滴加完毕;之后室温(25℃)下反应8h得有机膦盐反应液。
[0054]
向所得的有机膦盐反应液中加入100.5g水,20.2g准备实施例1制备的ru/sio2催化剂(ru 0.2mmol),25.4g碳酸钠(0.24mol),冲入空气加压至2.0mpa,恒温10℃反应10h;过滤反应液得到β
‑
胡萝卜素和ru催化剂的混合物,使用二氯甲烷溶解β
‑
胡萝卜素回收ru催化剂,滤液回收溶剂后加入300g甲醇回流2h后过滤干燥得β
‑
胡萝卜素51.1g,hplc检测纯度为98.0%,总收率93.2%。
[0055]
【实施例2】
[0056]
将实施实例1中的维生素a醋酸酯替换为69.9g va结晶母液,其他条件相同,制得有机膦盐反应液。
[0057]
向所得的有机膦盐反应液中加入100.5g水,20.2g准备实施例1制备的的ru/sio2催化剂(0.2mmol),27.6g碳酸钠(0.26mol),冲入空气加压至2.0mpa,恒温10℃反应10h;过滤反应液得到β
‑
胡萝卜素和ru催化剂的混合物,使用二氯甲烷溶解β
‑
胡萝卜素回收ru催化剂,滤液回收溶剂后加入300g甲醇回流2h后过滤干燥得β
‑
胡萝卜素49.8g,hplc检测纯度为97.6%,总收率90.5%。
[0058]
【实施例3】
[0059]
将实施实例1中的维生素a醋酸酯替换为59.7g维生素a醇(0.2mol),其他条件相同,制得有机膦盐反应液。
[0060]
向所得的有机膦盐反应液中加入100.5g水,20.2g准备实施例1制备的ru/sio2催化剂(0.2mmol),27.6g碳酸钠(0.26mol),冲入空气加压至2.0mpa,恒温10℃反应10h;过滤反应液得到β
‑
胡萝卜素和ru催化剂的混合物,使用二氯甲烷溶解β
‑
胡萝卜素回收ru催化剂,滤液回收溶剂后加入300g甲醇回流2h后过滤干燥得β
‑
胡萝卜素50.7g,hplc检测纯度为98.2%,总收率92.9%。
[0061]
【实施例4】
[0062]
向2l高压釜中加入67.0g维生素a醋酸酯(0.2mol,98%),94.4g三苯基膦(0.36mol),536g乙醇,搅拌下冷却到0℃,维持0
‑
5℃向体系内缓慢加入36.5g浓盐酸(0.3mol,37%),于1h滴加完毕;之后室温(25℃)下反应5h得有机膦盐反应液。
[0063]
向所得的有机膦盐反应液中加入167.5g水,404g准备实施例1制备的ru/sio2催化剂(4.0mmol),50.4g碳酸氢钠(0.6mol),冲入氧含量15%的氮氧混合气体加压至5mpa,恒温40℃反应5h;过滤反应液得到β
‑
胡萝卜素和ru催化剂的混合物,使用二氯甲烷溶解β
‑
胡萝卜素回收ru催化剂,滤液回收溶剂后加入300g甲醇回流2h后过滤干燥得β
‑
胡萝卜素49.0g,hplc检测纯度为98.0%,总收率89.5%。
[0064]
【实施例5】
[0065]
向1l高压釜中加入67.0g维生素a醋酸酯(0.2mol,98%),52.5g三苯基膦(0.2mol),268g异丙醇,搅拌下冷却到0℃,维持0
‑
5℃向体系内缓慢加入20g浓硫酸(0.2mol,98%),于0.5h滴加完毕;之后室温(25℃)下反应12h得有机膦盐反应液。
[0066]
向所得的有机膦盐反应液中加入134g水,2.02g准备实施例3制备的ru/活性炭催化剂(0.1mmol),33.2g碳酸钾(0.24mol),冲入纯氧加压至0.5mpa,恒温0℃反应24h;过滤反应液得到β
‑
胡萝卜素和ru催化剂的混合物,使用二氯甲烷溶解β
‑
胡萝卜素回收ru催化剂,滤液回收溶剂后加入300g甲醇回流2h后过滤干燥得β
‑
胡萝卜素49.5g,hplc检测纯度为97.5%,总收率90.1%。
[0067]
【实施例6】
[0068]
向1l高压釜中加入67.0g维生素a醋酸酯(0.2mol,98%),78.7g三苯基膦(0.3mol),402g丙醇,搅拌下冷却到0℃,维持0
‑
5℃向体系内缓慢加入28.2g氢溴酸(0.24mol,68.8%),于1h滴加完毕;之后室温(25℃)下反应8h得有机膦盐反应液。
[0069]
向所得的有机膦盐反应液中加入100.5g水,20.2g准备实施例3制备的ru/活性炭催化剂(1mmol),60.1g碳酸氢钾(0.6mol),冲入空气加压至2.5mpa,恒温15℃反应7h;过滤反应液得到β
‑
胡萝卜素和ru催化剂的混合物,使用二氯甲烷溶解β
‑
胡萝卜素回收ru催化剂,滤液回收溶剂后加入300g甲醇回流2h后过滤干燥得β
‑
胡萝卜素50.0g,hplc检测纯度为97.7%,总收率91.2%。
[0070]
【实施例7】
[0071]
向1l高压釜中加入67.0g维生素a醋酸酯(0.2mol,98%),52.5g三苯基膦(0.22mol),402g甲醇,搅拌下冷却到0℃,维持0
‑
5℃向体系内缓慢加入24g浓硫酸(0.24mol,98%),于1h滴加完毕;之后室温(25℃)下反应12h得有机膦盐反应液。
[0072]
向所得的有机膦盐反应液中加入100.5g水,20.2g准备实施例2制备的ru/硅胶催化剂(0.6mmol),33.9g碳酸钠(0.32mol),冲入空气加压至1.5mpa,恒温5℃反应10h;过滤反应液得到β
‑
胡萝卜素和ru催化剂的混合物,使用二氯甲烷溶解β
‑
胡萝卜素回收ru催化剂,滤液回收溶剂后加入300g甲醇回流2h后过滤干燥得β
‑
胡萝卜素50.4g,hplc检测纯度为97.2%,总收率91.4%。
[0073]
【实施例8】
[0074]
向1l高压釜中加入67.0g维生素a醋酸酯(0.2mol,98%),52.5g三苯基膦(0.22mol),402g甲醇,搅拌下冷却到0℃,维持0
‑
5℃向体系内缓慢加入137.8g对甲苯磺酸水溶液(0.24mol,30%),于1h滴加完毕;之后室温(25℃)下反应7h得有机膦盐反应液。
[0075]
向所得的有机膦盐反应液中加入100.5g水,20.2g准备实施例2制备的ru/硅胶催化剂(0.6mmol),33.9g碳酸钠(0.32mol),冲入空气加压至2.0mpa,恒温10℃反应8h;过滤反应液得到β
‑
胡萝卜素和ru催化剂的混合物,使用二氯甲烷溶解β
‑
胡萝卜素回收ru催化剂,
滤液回收溶剂后加入300g甲醇回流2h后过滤干燥得β
‑
胡萝卜素50.4g,hplc检测纯度为97.2%,总收率91.4%。
[0076]
【实施例9】
[0077]
向1l高压釜中加入67.0g维生素a醋酸酯(0.2mol,98%),68.2g三苯基膦(0.26mol),335g甲醇,搅拌下冷却到0℃,维持0
‑
5℃向体系内缓慢加入24g浓硫酸(0.24mol,98%),于1h滴加完毕;之后恢复室温(25℃)反应9h得有机膦盐反应液。
[0078]
向所得的有机膦盐反应液中加入134g水,60.6g准备实施例1制备的ru/sio2催化剂(0.6mmol),29.7g碳酸钠(0.28mol),冲入空气加压至2.0mpa,恒温10℃反应8h;过滤反应液得到β
‑
胡萝卜素和ru催化剂的混合物,使用二氯甲烷溶解β
‑
胡萝卜素回收ru催化剂,滤液回收溶剂后加入300g甲醇回流2h后过滤干燥得β
‑
胡萝卜素50.7g,hplc检测纯度为98.1%,总收率92.8%。
[0079]
【对比例1】
[0080]
按照实施例1中方法制备有机膦盐反应液,然后将ru/sio2催化剂替换为相同质量的sio2,继续制备β
‑
胡萝卜素。相同反应条件下,制得β
‑
胡萝卜素28.4g,hplc检测纯度为98.2%,总收率51.9%。
[0081]
【对比例2】
[0082]
按照实施例1中方法制备有机膦盐反应液,然后将ru/sio2催化剂替换为相同质量的sio2,并补充44.9mg醋酸钯作为催化剂,保持实施例1中其他条件继续制备β
‑
胡萝卜素。最终制得β
‑
胡萝卜素33.7g,hplc检测纯度为97.5%,总收率61.3%。
[0083]
催化剂套用实验:
[0084]
将实施例1和实施例2反应后回收的催化剂ru/sio2分别按其实施例中记载的方法进行套用,套用后催化反应的收率如表1所示:
[0085]
表1、催化剂套用后产品收率测试结果
[0086][0087]
对比例2中钯催化剂在反应结束后以离子的形式分布在水相和有机相中,回收困难,在本发明中不再进行套用测试。
[0088]
以上所述仅是本发明的优选实施方式,应当指出,对于本领域技术的普通技术人
员,在不脱离本发明方法的前提下,还可以做出若干改进和补充,这些改进和补充也应视为本发明的保护范围。
再多了解一些
本文用于企业家、创业者技术爱好者查询,结果仅供参考。