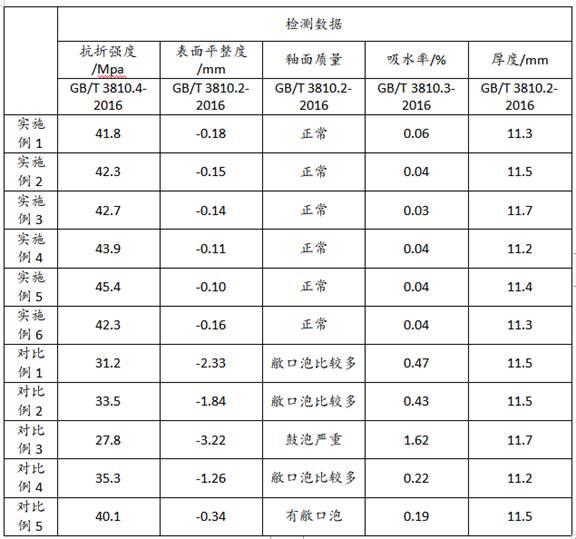
1.本发明涉及陶瓷技术领域,尤其涉及一种利用废料制造的陶瓷砖及其制备方法。
背景技术:
2.普通的瓷砖坯体,如大理石瓷砖坯体的原料均需要采用优质的泥料、砂及石粉等,制备瓷砖坯体时矿产资源的需求较大,且制备成本高,能耗也较高。
3.因此,部分工厂开始研究采用抛光废渣加入至瓷砖原料中,替代部分瓷砖原料,以降低陶瓷砖的生产成本。但抛光废渣由于含有碳化硅和有机树脂,在烧制中会释放出大量气体导致陶瓷坯体容易发泡,降低其机械强度;普通坯体配方硅铝比较固定,保证坯体莫来石晶相形成,坯体抗折强度达标,同时泥类占比较固定,熔剂钾、钠含量变化小。但陶瓷砖的抛光废渣含有大量烧熟的釉料,从而引入了部分钙、镁等助溶剂,由于其配方结构变化大,需要进行多次试验以确定配方的稳定性,且制得的瓷砖吸水率及抗折强度均不达标,由于坯料部分结构的改变,会使陶瓷砖的坯体和釉面在烧成中不适配导致釉层的缺陷增多。
技术实现要素:
4.本发明的主要目的是提供一种利用废料制造的陶瓷砖及其制备方法,旨在改善现有的利用废固陶瓷制备的陶瓷砖吸水率、抗折强度较差,且容易导致面釉层缺陷增多的技术问题。
5.为实现上述目的,本发明提出一种利用废料制造的陶瓷坯体的制备工艺,包括如下步骤:s1.人造石抛光渣和陶瓷抛光渣压滤后,置入树脂解胶剂中浸泡24h以上,再经沉淀和压滤后,分别搅拌均匀得到人造石处理渣和陶瓷处理渣;s2.将塑性原料、废渣、脊性原料、增强辅料与水混合,水料比为1:(2~3),然后经球磨、陈腐后得到浆料;所述废渣为陶瓷处理渣、人造石处理渣和压滤泥,所述陶瓷处理渣、所述人造石处理渣和所述压滤泥的质量比为(0.6
‑
6):(0.5
‑
1.5):(0.5
‑
1.5);s3.浆料经喷雾造粒后得到粉料,通过压机压制成型,干燥后得到陶瓷坯体;s4.陶瓷坯体经丝网印刷与喷墨打印,上釉后烧成,即得到所述利用废料制造的陶瓷砖。
6.利用废料制造的陶瓷坯体的原料包括塑性原料、废渣、脊性原料、增强辅料与水,塑性原料包括白泥、黑泥或高岭土类等原料,在坯体中起塑化和结合作用,是坯体成型的基础;脊性原料包括长石类、石英等,在坯体中起骨架作用,增强辅料为坯体生产中的常规添加剂,其在球磨时添加用于改善坯体的强度。本方案中的废渣主要包括陶瓷抛光渣、人造石抛光渣和压滤泥,较为常规的陶瓷原料更为节能环保,在保证陶瓷坯体性能不会降低的同时,又降低了生产成本,其中,陶瓷抛光渣为熟料,在制备利用废料制造的陶瓷坯体时,经二次烧成后的陶瓷抛光废渣能降低陶瓷坯体的烧成温度,本方案使用常规的陶瓷抛光渣即
可,例如,陶瓷抛光渣按质量百分比包括如下化学组成的原料:sio260~75%;al2o
3 15~23%;cao 1~4%;mgo 2~5%;fe2o
3 0 .5~2%;na2o 1~5%;k2o 1~4%;sic 0 .5~2%;压滤泥为陶瓷厂底料和面料清洗浆池及喷雾塔清洗后经过沉降池二次处理后,经压滤机挤压水分后而剩余的泥浆,本方案可使用常规的压滤泥,例如,压滤泥按质量百分比包括如下化学组成的原料:sio263~70%、al2o317~22%、fe2o30.5~1.5%、cao0.5~0.1%、mgo0.7~2%、k2o3~6%、na2o2~5%、tio20.1~0.5%和loi4~7%;人造石抛光渣主要为高硅含量的工业废料,此外还含有少许树脂等有机含量。本方案利用陶瓷抛光废渣进行二次烧成,使烧成温度降低,此外,人造石抛光渣引入了石英相,压滤泥引入了少量钙、镁元素,进一步降低了烧成温度,使得瓷砖烧结后的性能参数达标。
7.人造石抛光渣和陶瓷抛光渣在使用前需要经过预处理,由于陶瓷砖及人造石在抛光工序中需要用到大量的水进行冲洗,之后抛光渣和废水一并排放到浆池中,步骤s1中的初次压滤主要是将大量的水排除,留下抛光渣固体,之后将人造抛光渣和陶瓷抛光渣分别浸渍在树脂解胶剂中1天以上,以脱除人造抛光渣和陶瓷抛光渣中的树脂,提高陶瓷砖的强度和吸水效果;再经沉淀和压滤后排出多余水分,搅拌均匀得到人造石处理渣和陶瓷处理渣。塑性原料、废渣、脊性原料、增强辅料和水混合均匀后,处理后得到浆料,经喷雾造粒成为粉料,压制得到陶瓷坯体,经丝网印刷和喷墨打印图案后,施加保护釉料,烧成后得到利用废料制造的陶瓷砖,不同于现有技术中由废料制得的陶瓷砖强度较低,吸水率数据较差,该陶瓷砖具有较好的抗折强度和吸水率,釉面质量较好,平整且缺陷较少,满足gb/t 4100标准中吸水率小于0.5的干压陶瓷砖的性能要求。
8.优选地,按质量百分比计,所述树脂解胶剂由以下原料组成:二氯甲烷70~83%、甲酸7~18%、苯酚3~8%、石蜡1%~2%和硫酸1~4%。树脂解胶剂主要用于除掉人造石抛光渣和陶瓷抛光渣中的(环氧)树脂组分,以减少人造石抛光渣和陶瓷抛光渣组分中的杂质,能有效地减少抛光渣在烧成过程中排放的气体,作为坯体原料使用时可以增加生坯和熟坯的坯体强度。
9.优选地,步骤s2中,按质量百分比计,各原料的用量为:塑性原料27~51%、废渣20~50%和脊性原料14~28%,增强辅料的用量为上述三种原料(塑性原料、废渣和脊性原料)总质量的0.25
‑
0.7%;所述塑性原料为金发白泥、燕湖泥、福源高岭土和茶太混合泥;所述脊性原料为煅烧铝矾土、钾长石和钠长石。塑性原料选用上述金发白泥、燕湖泥和茶太混合泥,其有机质含量与常规泥不同,制得的坯体强度可以得到进一步改善。其中,金发白泥按质量百分比包括如下化学组成的原料:sio261.54%、al2o324.85%、fe2o31.53%、cao0.23%、mgo0.18%、k2o1.73%、na2o0.3%、tio20.65%和loi8.66%;燕湖泥按质量百分比包括如下化学组成的原料:sio259.60%、al2o327.02%、fe2o31.54%、cao0.03%、mgo0.34%、k2o2.07%、na2o0.23%、tio21%和loi8.56%;茶太混合泥按质量百分比包括如下化学组成的原料:sio264.96%、al2o322.35%、fe2o31.03%、cao0.30%、mgo0.15%、k2o0.70%、na2o0.23%、tio21.17%和loi9.18%。
10.优选地,所述人造石抛光渣为人造石英石抛光渣,按质量百分比计,其组分为sio287~94%和不饱和环氧树脂6~13%。采用人造石英石抛光渣时,其杂质相较于其他人造石更少,作为陶瓷坯体的原料,能引入大量的石英相,加固了坯体的骨架构成,对坯体的整体性能的改善效果最好。
11.优选地,所述增强辅料包括坯体增强剂和三聚磷酸钠。坯体增强剂包括羧甲基纤维素、硅酸钠、膨润土和硅灰石,其主要作用是增强生坯的强度。而三聚磷酸钠作为解胶剂,其主要作用则是用来提高陶瓷坯体的流动性,使其浆料的流动性能更好,不絮凝沉淀,便于后续工序的进行。
12.优选地,步骤s2中,球磨8~10h;所述浆料的细度为2.0~2.3%,含水率为32.5~34.5%,流速为35~65s,比重为1.71~1.73。通过对上述参数的控制,使浆料保持在较为适宜的范围内,从而使制得的粉料和坯体具有较好的质量。
13.优选地,步骤s3中,所述粉料的容重>0.92g/cm3,含水率为6.5~7.8%;所述粉料包括以下粒径的颗粒:小于20目的占比<1%,20目
‑
60目占比35~50%,60目
‑
100目占比35~50%,大于100目占比10
‑
15%;干燥时间为70~80min,干燥后陶瓷坯体的含水率<0.05%。
14.优选地,步骤s4中,烧成温度为1225~1235℃,烧成时间为60~70min,烧成后所述利用废料制造的陶瓷坯体的吸水率<0.5%。本方案中的陶瓷砖烧成温度较低,且经烧成后的陶瓷砖吸水率控制在0.5%以下,符合gb/t 4100标准中吸水率小于0.5的干压陶瓷砖的标准,整体烧结程度较好,致密性好,相对的抗污能力越好。
15.优选地,按质量百分比计,所述陶瓷坯体的化学成分组成为:sio262~74%、al2o318~24%、fe2o30.5~2%、cao0.3~0.8%、mgo0.4~2%、k2o2~4%、na2o0.8~2.5%、tio20.2~0.6%和loi3~6%。
16.本发明还提出一种利用废料制造的陶瓷坯体,由上述利用废料制造的陶瓷砖的制备方法所制得。参照上述实施例,由于利用废料制造的陶瓷坯体采用了上述所有实施例的全部技术方案,因此至少具有上述实施例的技术方案所带来的所有效果,在此不再一一赘述。
17.所述陶瓷坯体由如下原料制备而成:金发白泥12~18%、燕湖泥4~10%、福源高岭土3~10%、茶太混合泥8~13%、陶瓷抛光渣10~30%、压滤泥5~15%、人造石抛光渣5~15%、煅烧铝矾土1~3%、钾长石7~12%、钠长石6~13%、坯体增强剂0.15~0.4%和三聚磷酸钠的0.1~0.3%。
18.与现有技术相比,本发明的技术方案具有以下有益效果:1.将废渣中的陶瓷抛光渣、人造抛光石及压滤泥作为陶瓷坯体的主要制备原料,添加量在20%以上,清除陶瓷厂工业废料,实现了固废材料的再次利用,节能环保的同时,降低了生产成本。
19.2. 本方案中通过将人造石抛光渣浸入至树脂解胶剂进行预处理,使引入的人造石(石英石)抛光渣对陶瓷坯体成品的性能影响较小。严格废渣中的陶瓷抛光渣、人造石抛光渣和压滤泥的质量比为(0.6
‑
6):(0.5
‑
1.5):(0.5
‑
1.5),使陶瓷坯体的生坯强度得到保证,同时使整个配方体系在烧结后的莫来石含量在正常水平,保证了瓷砖的抗折强度。同时采用三聚磷酸钠对解胶性有进一步提升,使浆料的流速和比重达到正常陶瓷坯体的水平。原料配方中的氧化铝含量控制在适宜范围内,以提高瓷砖本身熔融软化后的高温粘度,使瓷砖不易变形,使得瓷砖的平整度更为可控。
具体实施方式
20.下面将对本发明实施例中的技术方案进行清楚、完整地描述,显然,所描述的实施例仅仅是本发明的一部分实施例,而不是全部的实施例。基于本发明中的实施例,本领域普
通技术人员在没有作出创造性劳动前提下所获得的所有其他实施例,都属于本发明保护的范围。
21.另外,各个实施例之间的技术方案可以相互结合,但是必须是以本领域普通技术人员能够实现为基础,当技术方案的结合出现相互矛盾或无法实现时应当认为这种技术方案的结合不存在,也不在本发明要求的保护范围之内。
22.一种利用废料制造的陶瓷砖的制备方法,包括如下步骤:s1.人造石抛光渣和陶瓷抛光渣压滤后,分别置入树脂解胶剂中浸泡24h以上,再经沉淀和压滤后,分别搅拌均匀得到人造石处理渣和陶瓷处理渣;按质量百分比计,所述树脂解胶剂由以下原料组成:二氯甲烷70~83%、甲酸10~16%、苯酚4~6%、石蜡1%~2%和硫酸1.5~2.5%;s2.将塑性原料、废渣、脊性原料、增强辅料与水混合,水料比为1:(2~3),然后经球磨8~10h、陈腐24h以上后得到浆料,浆料的细度为2.0~2.3%,含水率为32.5~34.5%,流速为35~65s,比重为1.71~1.73;按质量百分比计,各原料的用量为:塑性原料27~51%、废渣20~50%和脊性原料14~28%,增强辅料的用量为上述三种原料总质量的0.25
‑
0.7%;所述塑性原料为金发白泥、燕湖泥、福源高岭土和茶太混合泥;所述脊性原料为煅烧铝矾土、钾长石和钠长石;所述废渣为陶瓷处理渣、人造石处理渣和压滤泥,所述陶瓷抛光渣、所述人造石抛光渣和所述压滤泥的质量比为(0.6
‑
6):(0.5
‑
1.5):(0.5
‑
1.5);所述人造石抛光渣为人造石英石抛光渣,按质量百分比计,其组分为sio287~94%和不饱和环氧树脂6~13%;所述增强辅料包括坯体增强剂和三聚磷酸钠;s3.浆料经喷雾造粒后得到粉料,通过压机压制成型,干燥后得到陶瓷坯体,粉料的容重>0.92g/cm3,含水率为6.5~7.8%;所述粉料包括以下粒径的颗粒:小于20目的占比<1%,20目
‑
60目占比35~50%,60目
‑
100目占比35~50%,大于100目占比10
‑
15%;干燥时间为70~80min,干燥后陶瓷坯体的含水率<0.05%;s4.陶瓷坯体经丝网印刷与喷墨打印,上釉后烧成,烧成温度为1225~1235℃,烧成时间为60~70min,即得到所述利用废料制造的陶瓷砖。
23.以下结合具体实施例对本发明的技术方案作进一步详细说明,应当理解,以下实施例仅仅用以解释本发明,并不用于限定本发明。
24.实施例1一种利用废料制造的陶瓷砖的制备方法,包括如下步骤:s1.人造石英石抛光渣和陶瓷抛光渣压滤后,置入树脂解胶剂中浸泡27h,再经沉淀和压滤后,分别搅拌均匀得到人造石处理渣和陶瓷处理渣;按质量百分比计,所述树脂解胶剂由以下原料组成:二氯甲烷78%、甲酸12%、苯酚5%、石蜡2%和硫酸3%;s2.按质量百分比计,将34%的塑性原料、40%的废渣(陶瓷处理渣、人造石英石处理渣和压滤泥的质量比为6:1:1)和26%的脊性原料,加入上述三种原料总质量的0.5%的增强辅料(羧甲基纤维素、硅酸钠和三聚磷酸钠)与水混合,水料比为1:2,然后球磨8h、陈腐24h
后得到浆料,浆料的细度为2.1%,含水率为33.6%,流速为47s,比重为1.71;塑性原料为12%的金发白泥、4%的燕湖泥、10%的福源高岭土和8%的茶太混合泥;脊性原料为3%的煅烧铝矾土、12%的钾长石和11%的钠长石;人造石英石抛光渣的组分为sio290%和不饱和环氧树脂10%;s3.浆料经喷雾造粒后得到粉料,通过压机压制成型,干燥后得到陶瓷坯体,粉料的容重0.94g/cm3,含水率为6.9%;所述粉料包括以下粒径的颗粒:20目
‑
60目占比42%,60目
‑
100目占比48%,大于100目占比10%;干燥时间为72min,干燥后陶瓷坯体的含水率0.03%;s4.陶瓷坯体经丝网印刷与喷墨打印,上釉后烧成,烧成温度为1226℃,烧成时间为65min,即得到所述利用废料制造的陶瓷砖。
25.实施例2一种利用废料制造的陶瓷砖的制备方法,包括如下步骤:s1.人造石英石抛光渣和陶瓷抛光渣压滤后,置入树脂解胶剂中浸泡27h,再经沉淀和压滤后,分别搅拌均匀得到人造石处理渣和陶瓷处理渣;按质量百分比计,所述树脂解胶剂由以下原料组成:二氯甲烷75%、甲酸15%、苯酚6%、石蜡2%和硫酸2%;s2.按质量百分比计,将44%的塑性原料、29%的废渣(陶瓷处理渣、人造石英石处理渣和压滤泥的质量比为1:0.9:1)和27%的脊性原料,加入上述三种原料总质量的0.6%的增强辅料(羧甲基纤维素、硅酸钠和三聚磷酸钠),水料比为1:3,然后经球磨9h、陈腐24h以上后得到浆料,浆料的细度为2.1%,含水率为33.1%,流速为52s,比重为;塑性原料为18%的金发白泥、10%的燕湖泥、3%的福源高岭土和13%的茶太混合泥;脊性原料为3%的煅烧铝矾土、12%的钾长石和12%的钠长石;人造石英石抛光渣的组分为sio289%和不饱和环氧树脂11%;s3.浆料经喷雾造粒后得到粉料,通过压机压制成型,干燥后得到陶瓷坯体,粉料的容重0.93g/cm3,含水率为7.2%;所述粉料包括以下粒径的颗粒:20目
‑
60目占比43%,60目
‑
100目占比46%,大于100目占比11%;干燥时间为73min,干燥后陶瓷坯体的含水率0.02%;s4.陶瓷坯体经丝网印刷与喷墨打印,上釉后烧成,烧成温度为1231℃,烧成时间为65min,即得到所述利用废料制造的陶瓷砖。
26.实施例3一种利用废料制造的陶瓷砖的制备方法,包括如下步骤:s1.人造石抛光渣石英石抛光渣和陶瓷抛光渣压滤后,置入树脂解胶剂中浸泡27h,再经沉淀和压滤后,分别搅拌均匀得到人造石处理渣和陶瓷处理渣;按质量百分比计,所述树脂解胶剂由以下原料组成:二氯甲烷83%、甲酸7%、苯酚7%、石蜡1%和硫酸2%;s2.按质量百分比计,将42%的塑性原料、43%的废渣(陶瓷处理渣、人造石英石处理渣和压滤泥的质量比为2:1.1:1.2)和15%的脊性原料,加入上述三种原料总质量的0.5%的增强辅料(羧甲基纤维素、硅酸钠和三聚磷酸钠)与水混合,水料比为1:3,然后经球磨9h、陈腐24h以上后得到浆料,浆料的细度为2.2%,含水率为33.8%,流速为47s,比重为1.72;塑性原料为16%的金发白泥、8%的燕湖泥、8%的福源高岭土和10%的茶太混合泥;脊
性原料为2%的煅烧铝矾土、7%的钾长石和6%的钠长石;人造石英石抛光渣的组分为sio289%和不饱和环氧树脂11%;s3.浆料经喷雾造粒后得到粉料,通过压机压制成型,干燥后得到陶瓷坯体,粉料的容重0.96g/cm3,含水率为7.2%;所述粉料包括以下粒径的颗粒:20目
‑
60目占比41%,60目
‑
100目占比46%,大于100目占比13%;干燥时间为75min,干燥后陶瓷坯体的含水率0.02%;s4.陶瓷坯体经丝网印刷与喷墨打印,上釉后烧成,烧成温度为1228℃,烧成时间为67min,即得到所述利用废料制造的陶瓷砖。
27.对比例1本对比例的各项参数均与实施例3保持一致,区别仅在于:人造石抛光渣和陶瓷抛光渣不进行预处理步骤,即取消步骤s1。
28.对比例2本对比例的各项参数均与实施例3保持一致,区别仅在于:采用常规的解胶剂(碳酸钠20%、三聚磷酸钠57%和腐殖酸钠23%)。
29.实施例4本实施例的各项参数均与实施例3保持一致,区别仅在于:陶瓷抛光渣15%、人造石抛光渣15%和压滤泥13%(质量比为1:1:1.3)。
30.对比例3本对比例的各项参数均与实施例3保持一致,区别仅在于:陶瓷抛光渣37%、人造石抛光渣3%和压滤泥3%(质量比为37:1:1)。
31.对比例4本对比例的各项参数均与实施例3保持一致,区别仅在于:二氯甲烷60%、甲酸3%、苯酚20%、石蜡10%和硫酸7%。
32.实施例5本实施例的各项参数均与实施例4保持一致,区别仅在于,树脂解胶剂由以下原料组成:二氯甲烷79%、甲酸9%、苯酚8%、石蜡1%和硫酸3%。
33.实施例6本实施例的各项参数均与实施例3保持一致,区别仅在于,35%的塑性原料、38.5%的废渣、26%的脊性原料和0.5%的增强辅料。
34.对比例5本对比例的各项参数均与实施例3保持一致,区别仅在于,塑性原料为湖南界牌东湖泥、江苏宜兴东山白泥、浙江宁海黏土和浙江龙泉宝溪瓷土,用量保持不变。
35.将实施例1
‑
6及对比例1
‑
5进行性能测试,测试结果如下表:表1 性能测试结果
从上表的测试结果可以看出,本发明的利用废料制造的陶瓷砖尽管原料中添加了较多比例的废渣,但对于陶瓷砖整体的性能影响较小,陶瓷砖具有较高的抗折强度,均保持在41mpa以上,同时还具有较小的吸水率,陶瓷砖的表面不存在缺陷,成品的质量较高。
36.以上所述仅为本发明的优选实施例,并非因此限制本发明的专利范围,凡是在本发明的发明构思下,利用本发明说明书内容所作的等效结构变换,或直接/间接运用在其他相关的技术领域均包括在本发明的专利保护范围内。
再多了解一些
本文用于企业家、创业者技术爱好者查询,结果仅供参考。