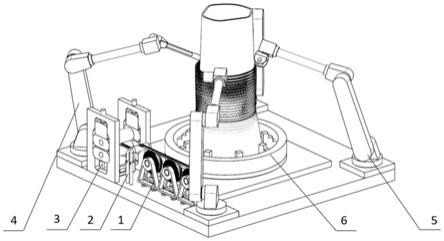
1.本发明涉及一种箔带缠绕装置,具体涉及一种用于金属箔带分散叠层铺放制坯的缠绕装置。
背景技术:
2.在航空航天领域,新一代飞行器追求着更高的飞行速度、更远的航行距离以及更大的承载能力,这对关键结构如发动机进气道、尾喷管、发动机涡轮叶片、热防护蒙皮等构件的轻量化和高温力学性能提出了更高要求。因此,新型轻质耐高温结构材料如nial/tial合金逐渐成为研究重点。除了耐热温度高,nial/tial金属间化合物还具有密度低、硬度好、抗氧化性优良、抗腐蚀性好、结构稳定性高等优点。
3.目前nial/tial金属间化合物的制备方法有熔铸法、燃烧合成法、热压法、粉末冶金法、元素箔叠层轧制法、元素箔反应合成法等方式。对于钛合金、高温合金等材料,目前制造复杂薄壁构件的方法,都是直接采用轧制等方法获得的薄壁平面板坯或管坯为原材料,通过超塑成形、热冲压成形等成形制造技术获得最终的薄壁构件。可以说,钛合金、高温合金的原始板坯/管坯的制备和后续成形制造复杂薄壁构件是两个相对独立的过程。但是由于nial/tial材料的本征脆性,很难制备获得大尺寸的nial/tial薄壁平面板坯或管坯,即使可制备出平面板坯或管坯,在室温和温热状态下也极难变形为复杂构件。为解决此问题,发明专利(申请号:201710448620.5和201910444894.6)提出了nial合金曲面板件与管件的合成制备和成形一体化方法,该方法将大尺寸ni箔与a1箔交替叠放后进行热压制坯,再通过热气胀成形获得构件形状,接着通过高温真空热处理等步骤获得最终的nial合金零件。由于该方法最初制备的坯料形状简单,所以在热气胀过程中坯料会发生较大且复杂的变形,容易出现局部减薄、开裂、起皱等缺陷。为减少上述缺陷的产生,发明专利(申请号:202010031405.7)提出了一种采用金属箔带铺放制坯的耐高温薄壁构件一体化制造方法,发明专利(申请号:202010811707.6)提出了一种采用金属箔带缠绕芯模制备金属间化合物曲面薄壁构件的方法。这两种方法都是利用金属箔带直接缠绕铺放出最终零件的形状,然后在高温高压下反应合成实现材料改性,最终获得材料、形状均符合需求的零件。在缠绕金属箔带过程中,当采用单层箔带缠绕时,由于特征区域的复杂程度不同,箔带铺放过程中同层相邻箔带之间会出现间隙、堆叠,甚至褶皱等现象,无论同层箔带之间是采用间隙还是搭接方式,在后续的扩散合成反应过程都会因局部缺少某种元素,导致反应不完全形成中间过渡态的金属间化合物。此外,箔带的缠绕路径以及箔带对支撑芯模的紧密程度也都会对坯料最终成形的质量和精度产生重要的影响。采用叠层箔带缠绕时,虽然避免了单层箔带缠绕时局部缺少某种元素的问题,可以制备出任意的均一特性金属间化合物,但同样会出现单层箔带缠绕时难以获取高精度、高质量的预制坯的问题,此外还需要减少叠层箔带间的间隙以提高叠层箔带的致密性,以便进行箔带的缠绕、提高后续成形时的密封性。此外,对于大尺寸构件,如果采用人工往返缠绕金属箔带的方式,则效率很低,并且缠绕精度低,可重复性差。
4.为解决薄壁异形构件分散叠层铺放制坯时存在箔带缠绕路径复杂、箔带对支撑芯模的贴模度低、叠层箔带的致密性差,以及采用人工往返铺放制备大尺寸构件时缠绕金属箔带效率低、缠绕精度低、可重复性差等问题,需要一种用于金属箔带分散叠层铺放制坯的缠绕装置。
技术实现要素:
5.为解决薄壁异形构件分散叠层铺放制坯时存在箔带缠绕路径复杂、箔带对支撑芯模的贴模度低、叠层箔带的致密性差,以及采用人工往返铺放制备大尺寸构件时缠绕金属箔带效率低、缠绕精度低、可重复性差等问题,提出了一种用于金属箔带分散叠层铺放制备薄壁异形构件坯料的缠绕装置。
6.本发明技术方案如下:
7.一种用于金属箔带分散叠层铺放制坯的缠绕装置包括箔带盘1、换向装置2、热辊压系统3、箔带铺放机械臂4、辊压机械臂5、旋转平台6、八爪卡盘22、支撑芯模23、底座24、热辊压头25、喷嘴26和喷粉机械臂27;
8.所述箔带盘1包括箔带7、带轮8、三脚架9和支撑底座10;下端支撑底座10与三脚架9相连;带轮8固定在两三脚架9间;带轮8放置箔带7;
9.所述换向装置2由两套相同的机构组成,每套机构包括机架11、调节螺栓12、连杆13和换向轮14;连杆13通过调节螺栓12固定于机架11上,换向轮14孔轴配合与连杆13连接,调节螺栓12用于调节连杆13的高度,进而改变换向轮14的高度;使两套机构的高度不同,完成箔带的换向。
10.所述热辊压系统3包括电阻加热箱15、定位板16、芯轴17、限位块18、夹紧板19、紧固螺母20和热辊21;电阻加热箱15通过加热铜管与芯轴17相连;芯轴17固定于限位块18上,并且芯轴17外套装有热辊21;限位块18固定在定位板16内,通过夹紧板19控制其在竖直方向上滑动;紧固螺母20调节夹紧板19对限位块18的压力,进而调节轧制力;
11.箔带铺放机械臂4、辊压机械臂5、旋转平台6和两个喷粉机械臂27均固定在底座24上;热辊压头25固定在辊压机械臂5前端;喷嘴26固定在喷粉机械臂27前端;箔带铺放机械臂4、辊压机械臂5和两个喷粉机械臂27均实现多自由度空间移动和摆动;支撑芯模23通过八爪卡盘22固定在旋转平台6上,随旋转平台6一同旋转。
12.所述热辊压系统3替换为环境加热辊压系统组成本缠绕装置的第二种方式;环境加热辊压系统包括加热炉28、辊筒29、电机及减速装置31、水冷板32、隔热板33和冷水机34;加热炉28的外壳上开有箔带输送孔30,辊筒29位于加热炉28外壳内用于辊压叠层箔带;电机及减速装置31与辊筒29相连并为其旋转提供动力,二者间依次设置隔热板33和水冷板32用于隔绝加热炉28余温,其中隔热板33位于加热炉28外侧;水冷板32内有流通水道与冷水机34相连。
13.一种用于金属箔带分散叠层铺放制坯的缠绕装置的使用方法,具体包括以下步骤:
14.步骤一、单层元素箔带盘出带;根据箔带7的种类以及数量确定箔带盘1的数量;两个三脚架9通过带轮8连接,下端支撑底座10与三脚架9相连,便于箔带盘1的拆卸和移动;根据实验要求确定各层箔带7的宽度与厚度,接着根据构件所需缠绕箔带量选择不同直径与
宽度的带轮8;各层箔带7存放于各自箔带盘1上;当需要缠绕支撑芯模时,各箔带盘1依次出带;
15.步骤二、各层箔带7进入热辊压系统3;换向装置2通过调节螺栓12调节连杆13的高度,进而改变换向轮14高度,从而保证各层箔带7经过两个换向轮14后汇聚一起并顺利地进入热辊压系统3;
16.步骤三、热辊压系统3辊压形成叠层箔带;各层箔带7在温度和压力的作用下紧密贴合,反应合成,其中电阻加热箱15加热芯轴17使热辊21达到所需温度;紧固螺母20通过调节夹紧板19对限位块18的压力改变两个热辊21间的距离,达到不同轧制力的目的;
17.步骤四、机械臂夹持叠层箔带;反应合成后,叠层箔带离开热辊压系统3,箔带铺放机械臂4夹持叠层箔带准备缠绕;
18.步骤五、旋转平台带动支撑芯模23旋转并缠绕叠层箔带;旋转平台6通过八爪卡盘22定位并夹紧支撑芯模23,并且通过旋转带动支撑芯模23进而缠绕箔带7,箔带铺放机械臂4夹持箔带7进行协同动作,根据设计路径实时调整箔带7缠绕位置与角度,实现往返缠绕箔带7;
19.步骤六、机械臂前端热辊压头25压紧叠层箔带,喷嘴26添加粉末;在箔带7缠绕过程中,辊压机械臂5前端热辊压头25压紧叠层箔带,喷粉机械臂27前端喷嘴26喷洒相同元素水或粉将单层相邻箔带7之间的缝隙填满,不同机械臂协同完成铺放制坯工作;
20.步骤七,叠层箔带铺放完成后取件;箔带铺放机械臂4利用前端夹头剪断箔带7,机械臂退回初始位置,旋转平台6停止旋转,八爪卡盘22松开,最后取出铺放后的支撑芯模23。
21.本发明的有益效果:
22.一、本缠绕装置在叠层箔带缠绕支撑芯模前,对叠层箔带进行加热辊压处理,使松散的多层箔带结合成为一体,提高了叠层箔带致密性,便于后续缠绕工作。
23.二、本缠绕装置通过机械臂夹持箔带控制箔带上升角度与方向,并根据路径实时调整,提高箔带铺放路径的准确性以及增加箔带铺放过程的张紧力,并且保证构件连续制造的稳定性与可重复性。
24.三、本缠绕装置通过机械臂前端的热辊对箔带进行辊压,使其与支撑芯模紧密贴合,提高叠层构件的贴模度以及最终成形的精度与质量,避免由于特征区域的复杂程度不同,而导致铺放的箔带起皱、堆叠、难以获取接近最终零件的预制坯的问题,同时利用热辊轧实现相邻层箔带的粘接也解决了负曲率型面的铺放缠绕困难的问题。
25.四、本缠绕装置对于缠绕大尺寸构件的支撑芯模,通过整套装置的紧凑布局以及机械臂之间的相互配合,能够有效避免人工往返缠绕金属箔带效率低,并且缠绕精度低,可重复性差等缺陷。
附图说明
26.图1为一种用于金属箔带分散叠层铺放制坯的缠绕装置工作原理示意图。
27.图2为一种用于金属箔带分散叠层铺放制坯的缠绕装置三维示意图。
28.图3为单层元素箔带盘三维示意图。
29.图4为换向装置三维示意图。
30.图5为箔带输送过程二维示意图。
31.图6为箔带辊压过程二维示意图。
32.图7为热辊压系统三维示意图。
33.图8为机械臂协同工作铺放制坯三维示意图
34.图9为机械臂协同工作铺放制坯俯视图。
35.图10为环境加热辊压系统三维示意图。
36.图11(a)为柱状热辊压头三维示意图。
37.图11(b)为球状热辊压头三维示意图。
38.其中1
‑
箔带盘,2
‑
换向装置,3
‑
热辊压系统,4
‑
箔带铺放机械臂,5
‑
辊压机械臂,6
‑
旋转平台,7
‑
箔带,8
‑
带轮,9
‑
三脚架,10
‑
支撑底座,11
‑
机架,12
‑
调节螺栓,13
‑
连杆,14
‑
换向轮,15
‑
电阻加热箱,16
‑
定位板,17
‑
芯轴,18
‑
限位块,19
‑
夹紧板,20
‑
紧固螺母,21
‑
热辊,22
‑
八爪卡盘,23
‑
支撑芯模,24
‑
底座,25
‑
热辊压头,26
‑
喷嘴,27
‑
喷粉机械臂,28
‑
加热炉,29
‑
辊筒,30
‑
箔带输送孔,31
‑
电机及减速装置,32
‑
水冷板,33
‑
隔热板,34
‑
冷水机。
具体实施方式
39.下面结合附图和技术方案,进一步说明本发明的具体实施方式。
40.具体实施方式一:结合图1至图9说明,本发明为一种用于金属箔带分散叠层铺放制坯的缠绕装置包括箔带盘1、换向装置2、热辊压系统3、箔带铺放机械臂4、辊压机械臂5、旋转平台6、八爪卡盘22、支撑芯模23、底座24、热辊压头25、喷嘴26和喷粉机械臂27。
41.本实施例中的一种用于金属箔带分散叠层铺放制坯的缠绕装置工作原理,如图1所示,具体包括以下步骤:
42.步骤一、单层元素箔带盘出带。根据箔带的种类以及数量确定箔带盘的数量,两个三脚架9通过带轮8连接,下端支撑底座10通过螺栓与三脚架9相连,便于箔带盘1的拆卸和移动,同时根据实验要求确定a、b单层元素箔带的宽度与厚度,接着根据构件所需缠绕箔带量选择不同直径与宽度的带轮a、b。单层a元素箔带存放于a箔带盘上,单层b元素箔带存放于b箔带盘上,当需要缠绕支撑芯模时,箔带盘a、b依次出带。
43.步骤二、各层元素箔带进入热辊压系统。换向装置2通过调节螺栓12调节连杆13的高度,进而改变换向轮14高度从而保证各层元素箔带经过两个换向轮14后汇聚一起并顺利地进入热辊压系统。
44.步骤三、热辊热辊压形成叠层箔带。各层箔带在温度和压力的作用下紧密贴合,反应合成,其中电阻加热箱15加热芯轴17使热辊21达到所需温度,紧固螺母20调节夹紧板19对限位块18的压力改变两个热辊21间的距离,达到不同轧制力的目的。
45.步骤四、机械臂夹持叠层箔带。反应合成后,叠层箔带离开热辊压系统3,箔带铺放机械臂4夹持叠层箔带准备缠绕;
46.步骤五、旋转平台带动支撑芯模2旋转并缠绕叠层箔带。旋转平台6通过八爪卡盘22定位并夹紧支撑芯模,并且通过旋转带动支撑芯模23进而缠绕箔带7,箔带铺放机械臂4夹持箔带7进行协同动作,根据设计路径实时调整箔带缠绕位置与角度,实现往返缠绕箔带;
47.步骤六、机械臂前端热辊压头压紧叠层箔带,喷嘴添加粉末。在箔带缠绕过程中,辊压机械臂5前端热辊压头25压紧叠层箔带,喷粉机械臂27前端喷嘴26喷洒a水/粉或b水/
粉将单层相邻箔带之间的缝隙填满,不同机械臂协同完成铺放制坯工作。
48.步骤七,叠层箔带铺放完成后取件。箔带铺放机械臂4利用前端夹头剪断箔带,机械臂退回初始位置,旋转平台6停止旋转,八爪卡盘22松开,最后取出铺放后的支撑芯模。
49.具体实施方式二:结合图2至图9说明,对于叠层箔带缠绕,同样以金属间化合物nial合金为例进行说明,选择双层或者三层箔带叠层后同时缠绕。本实施例中以三层箔带同时缠绕为例,在步骤一中箔带盘使用两个ni箔带盘,一个al箔带盘,按ni
‑
al
‑
ni形式堆叠,根据实验要求选用0.15mm厚的al箔带,0.05mm厚的ni箔带,箔带带宽均10mm;再根据构件所需缠绕箔带量选择直径为300mm、宽度为40mm的带轮a、b;在步骤三中,热辊压系统温度需达到500℃以上但须低于ni、al两者熔点较低者的熔点660℃,轧制压下量为0.15mm,控制叠层箔带厚度为0.1mm。在步骤六中,只需机械臂5前端热辊压头25压紧叠层箔带,无需喷洒粉末,其它步骤与实施例一相同。
50.本实施方式的有益效果是:叠层箔带缠绕时根据箔带的种类以及数量确定层数进而确定箔带盘的数量,叠层箔带缠绕制坯可以制备出任意的均一特性金属间化合物a
x
b
y
,没有中间产物。同时箔带盘可拆卸,可以随时改变位置,也可以作为箔带的存放装置,再根据构件所需缠绕箔带量选择不同直径与宽度的带轮,可以制备出不同尺寸的薄壁异形构件坯料。热辊压系统使叠层箔带在温度和压力的作用下紧密贴合,反应合成,提高了叠层箔带致密性,便于后续缠绕工作。
51.具体实施方式三:结合图3、9说明,对于单层箔带缠绕,以金属间化合物nial合金为例进行说明,其中一箔带为ni箔带,另一箔带为al箔带,ni、al箔带交替缠绕,完成最后构件的叠层铺放。在步骤一中箔带盘只需使用一个ni箔带盘,一个al箔带盘,本实施例中根据实验要求选用0.06mm厚的al箔带,0.1mm厚的ni箔带,箔带带宽10mm;再根据构件所需缠绕箔带量选择直径都为300mm、宽度为40mm的带轮a、b;省略步骤二、三,无需进入热辊压系统;从步骤四到步骤七,机械臂先夹持ni箔,然后旋转平台6带动支撑芯模23旋转并缠绕ni箔,随后机械臂5前端热辊压头25压紧ni箔,喷粉机械臂27前端喷嘴26喷洒ni水/粉将单层相邻ni箔带之间的缝隙填满。最后箔带铺放机械臂4前端夹头剪断ni箔。重复上述步骤缠绕al箔,实现ni、al箔带交替缠绕。
52.本实施方式的有益效果是:该装置各部分均可拆卸,满足单层、叠层两种不同形式的箔带缠绕方式。单层箔带缠绕时,无需热辊压系统,节约空间。通过喷粉机械臂27前端喷嘴26喷洒ni水/粉或al水/粉将单层相邻箔带之间的缝隙填满,可以保证两者反应生成均匀的合金材料,不会因为局部缺少原料而反应不完全,辊压机械臂5前端热辊压头25压紧箔带使相邻层箔带粘接性更好进而使相邻层箔带反应完全。
53.具体实施方式四:结合图10说明在步骤三中热辊压系统替换为环境加热辊压系统,通过加热炉20对输送过来的叠层箔带进行加热,同时辊筒21对叠层箔带进行辊压,进而实现箔带的热辊压处理。
54.本实施方式的有益效果是:环境加热辊压系统实现对箔带的加热,箔带先进入加热炉运输一段距离后,辊筒才会对其辊压,提前预热使箔带温度更加均匀,在辊压过程中不同箔带的变形更加均匀,辊压效果更好。
55.具体实施方式五:结合图11说明在步骤六中机械臂前端热辊压头压紧箔带时温度需达500℃以上但须低于ni、al两者熔点较低者的熔点660℃;并且对于不同复杂程度薄壁
构件选用不同类型热辊压头,构件型面曲率变化较小时用柱状热辊压头,构件型面曲率变化较大或者为负曲率型面时用球状热辊压头。
56.本实施方式的有益效果是:热辊压头辊压不仅可以提高叠层箔带的致密性,还可以实现相邻层箔带的粘接,解决了负曲率型面的铺放缠绕困难的问题。
再多了解一些
本文用于企业家、创业者技术爱好者查询,结果仅供参考。