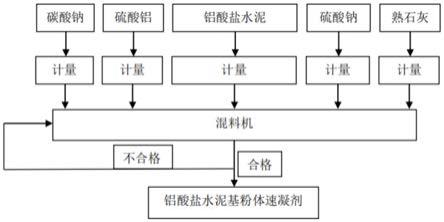
1.本发明属于建筑材料外加剂技术领域,具体涉及一种铝酸盐水泥基粉体速凝剂及其制备方法和应用。
背景技术:
2.喷射混凝土在工程中常用来快速加固或修补,而速凝剂是喷射混凝土必不可少的一种外加剂,它不仅决定着混凝土能否实现速凝快硬,而且对混凝土的后期性能也会产生较大的影响。目前,根据碱的含量,可分为有碱速凝剂和无碱速凝剂;根据速凝剂的成分,可分为无机速凝剂和有机速凝剂;根据速凝剂的状态,可分为粉体速凝剂和液体速凝剂。其中无碱速凝剂是最受欢迎的,但由于无碱速凝剂的速凝效果不明显,使用时需要采用较大掺量,生产时原料成本相对较高,加上掺量较大,其使用成本往往很难被接受;有碱速凝剂虽然具有速凝效果好、掺量小和成本低等特点,但通常会存在后期强度损失大,即28d抗压强度小等缺点。
3.因此,需要提供一种针对上述现有技术不足的改进技术方案。
技术实现要素:
4.本发明的目的在于提供一种铝酸盐水泥基粉体速凝剂及其制备方法和应用,以解决现有速凝剂的速凝效果不能满足需求、28d抗压强度损失大、成本高等问题。
5.为实现上述目的,本发明提供以下技术方案:
6.一种铝酸盐水泥基粉体速凝剂,包括铝酸盐水泥、碳酸钠、硫酸铝、硫酸钠、熟石灰;所述粉体速凝剂中各组分的重量比为:铝酸盐水泥:碳酸钠:硫酸铝:硫酸钠:熟石灰=(40~60):(10~20):(10~20):(10~20):(5~20)。
7.优选地,所述铝酸盐水泥为符合国家标准《铝酸盐水泥》gb/t 201
‑
2015表1中要求的铝酸盐水泥。
8.优选地,所述碳酸钠为符合国标《工业碳酸钠》gb210
‑
1992中ii类一等品和/或合格品要求的工业纯碱。
9.优选地,所述硫酸铝为符合化工行业标准《工业硫酸铝》hg/t 2225
‑
2010中i类或ii类硫酸铝固体粉末颗粒。
10.优选地,所述硫酸钠为符合化工行业标准《化妆品用硫酸钠》hg/t4535
‑
2013表1中无水硫酸钠固体粉末颗粒。
11.优选地,所述硫酸铝、所述硫酸钠的颗粒大小均不小于200目。
12.优选地,所述熟石灰为符合建材行业标准《建筑消石灰粉》jc/t481
‑
92中钙质消石灰粉的一等品和/或合格品要求的消石灰粉。
13.本发明还提供上述的铝酸盐水泥基粉体速凝剂的制备方法,所述制备方法包括以下步骤:将各组分按所述重量比研磨、混合均匀,即得;所述铝酸盐水泥基粉体速凝剂的比表面积为300~500m2/kg。
14.本发明还提供上述的铝酸盐水泥基粉体速凝剂在水泥中的应用。
15.优选地,所述水泥为符合国家标准《通用硅酸盐水泥》gb175
‑
2020表1、表2和表3中的硅酸盐水泥、普通硅酸盐水泥、复合硅酸盐水泥、粉煤灰硅酸盐水泥、矿渣硅酸盐水泥中的任一种。
16.有益效果:
17.本发明的铝酸盐水泥基粉体速凝剂具有速凝效果好、28d抗压强度损失小和成本低等特点。并且,本发明的铝酸盐水泥基粉体速凝剂用于喷射混凝土时,初凝时间在3~7min之间可调,终凝时间在5~12min之间可调;1d抗压强度高,在7~11mpa之间可调;28d抗压强度损失小,并且与各种硅酸盐水泥适用性好。本发明对生产设备及人员要求低,生产周期短,生产成本低,全过程不产生三废,不影响环境。
附图说明
18.构成本发明的一部分的说明书附图用来提供对本发明的进一步理解,本发明的示意性实施例及其说明用于解释本发明,并不构成对本发明的不当限定。其中:
19.图1是本发明实施例中的铝酸盐水泥基粉体速凝剂的制备流程图。
具体实施方式
20.下面将对本发明实施例中的技术方案进行清楚、完整地描述,显然,所描述的实施例仅仅是本发明的一部分实施例,而不是全部的实施例。基于本发明中的实施例,本领域普通技术人员所获得的所有其他实施例,都属于本发明保护的范围。
21.下面将参考附图并结合实施例来详细说明本发明。需要说明的是,在不冲突的情况下,本发明中的实施例及实施例中的特征可以相互组合。
22.本发明以铝酸钙水泥为主料,辅以其它化工原料,进行了优质高效铝酸盐水泥基速凝剂的研制。本发明铝酸盐水泥基粉体速凝剂,速凝效果好,初凝时间可短至2min,终凝时间可短至5min;力学性能好,1d的抗压强度可高达10mpa以上,28d抗压强度比(掺速凝剂砂浆28d抗压强度与不掺速凝剂砂浆28d抗压强度的百分比,具体见国标jc 477
‑
2005)可高达90%以上;与不同类型水泥的匹配性好,在掺量4~8%范围内(掺量,即粉体速凝剂的质量与水泥的质量之比),对硅酸盐水泥、普通硅酸盐水泥、粉煤灰硅酸盐水泥(它们的具体区别见国家标准《通用硅酸盐水泥》gb175
‑
2020中的表1、表2和表3)等均具有较好的适用性。本发明对生产设备及人员要求低,生产周期短,生产成本低,全过程不产生三废,不影响环境。
23.本发明的铝酸盐水泥基粉体速凝剂,包括铝酸盐水泥、碳酸钠、硫酸铝、硫酸钠、熟石灰;所述粉体速凝剂中各组分的重量比为:铝酸盐水泥:碳酸钠:硫酸铝:硫酸钠:熟石灰=(40~60):(10~20):(10~20):(10~20):(5~20),例如重量比为40:10:20:10:20、60:20:10:20:5、50:15:15:15:15、45:10:10:10:10、55:12:18:12:10。
24.进一步,铝酸盐水泥为符合国家标准《铝酸盐水泥》gb/t 201
‑
2015表1中要求的铝酸盐水泥。
25.进一步,碳酸钠为符合国标《工业碳酸钠》gb210
‑
1992中ii类一等品和/或合格品要求的工业纯碱。
26.进一步,硫酸铝为符合化工行业标准《工业硫酸铝》hg/t 2225
‑
2010中i类或ii类硫酸铝固体粉末颗粒,颗粒大小不小于200目。
27.进一步,硫酸钠为符合化工行业标准《化妆品用硫酸钠》hg/t 4535
‑
2013表1中无水硫酸钠固体粉末颗粒,颗粒大小不小于200目。
28.进一步,熟石灰为符合建材行业标准《建筑消石灰粉》jc/t481
‑
92中钙质消石灰粉的一等品和/或合格品要求的消石灰粉。
29.本发明的铝酸盐水泥基粉体速凝剂的比表面积为300~500m2/kg(例如300m2/kg、350m2/kg、380m2/kg、400m2/kg、420m2/kg、450m2/kg、500m2/kg)。
30.本发明的铝酸盐水泥基粉体速凝剂的制备方法,如图1所示,具体包括以下步骤:将铝酸盐水泥、碳酸钠、硫酸铝、硫酸钠、熟石灰按上述重量比加入混料机中混合均匀,按建材行业标准《喷射混凝土用速凝剂》(jc 477
‑
2005)进行检验,经检测合格后得铝酸盐水泥基粉体速凝剂。
31.本发明提供的铝酸盐水泥基粉体速凝剂具有:(1)速凝效果好,初凝时间在3~7min之间可调,终凝时间在5~12min之间可调;(2)1d抗压强度高,在7~11mpa之间可调;(3)28d抗压强度损失小;(4)与不同水泥适用性好等特点。
32.本发明对生产设备及人员要求低,生产周期短,生产成本低,全过程不产生三废,不影响环境。
33.以下实施例中:
34.铝酸盐水泥为符合国家标准《铝酸盐水泥》gb/t 201
‑
2015表1中要求的ca60型铝酸盐水泥;
35.碳酸钠为符合国标《工业碳酸钠》gb210
‑
1992中ii类一等品要求的工业纯碱;
36.硫酸铝为符合化工行业标准《工业硫酸铝》hg/t 2225
‑
2010中i类硫酸铝固体粉末颗粒,颗粒大小为200目;
37.硫酸钠为符合化工行业标准《化妆品用硫酸钠》hg/t 4535
‑
2013表1中无水硫酸钠固体粉末颗粒,颗粒大小为200目;
38.熟石灰为符合建材行业标准《建筑消石灰粉》jc/t481
‑
92中钙质消石灰粉一等品要求的消石灰粉。
39.实施例1
40.本实施例的铝酸盐水泥基粉体速凝剂,制备方法为:将铝酸盐水泥5000g、碳酸钠1500g、硫酸铝1000g、硫酸钠1000g、熟石灰500g,加入研磨混料机中混合均匀,比表面积达到350m2/kg,按建材行业标准《喷射混凝土用速凝剂》(jc 477
‑
2005)进行检验,经检测合格后得铝酸盐水泥基粉体速凝剂。
41.分别采用不同的水泥,例如硅酸盐水泥、普通硅酸盐水泥、复合硅酸盐水泥、粉煤灰硅酸盐水泥、矿粉硅酸盐水泥,按照建材行业标准《喷射混凝土用速凝剂》中的规定进行凝结时间的测试,其中水泥400g、铝酸盐水泥基粉体速凝剂24g、水160g,测试结果见表1。
42.分别采用不同的水泥,例如硅酸盐水泥、普通硅酸盐水泥、复合硅酸盐水泥、粉煤灰硅酸盐水泥、矿粉硅酸盐水泥,按照建材行业标准《喷射混凝土用速凝剂》中的规定进行抗压强度的测试,其中水泥900g、标准砂1350g、铝酸盐水泥基粉体速凝剂54g、水450g,测试结果见表1。
43.表1不同水泥的凝结时间和抗压强度测试结果
[0044][0045]
从表1可以看出,本发明铝酸盐水泥基粉体速凝剂与各种硅酸盐水泥的匹配性好,在固定其掺量为6%时,对硅酸盐水泥、普通硅酸盐水泥、粉煤灰硅酸盐水泥等均具有较好的适用性。其中,本发明铝酸盐水泥基粉体速凝剂对硅酸盐水泥和普通硅酸盐水泥的速凝效果更好,其初凝时间均小于3min,终凝时间均小于7min,且力学性能更好,1d的抗压强度可高达10mpa以上,28d抗压强度比可高达90%以上。(可以理解的是,对于凝结时间和抗压强度的测试数值,每次测试结果都不会完全一样,为了更好地进行对比,本发明对于同一表中同一编号的两种体系在同时间段内进行测试)
[0046]
本实施例还研究了粉体速凝剂掺量不同时,对体系的凝结时间和抗压强度的影响,以硅酸盐水泥为例,结果如下表2所示。
[0047]
表2不同掺量粉体速凝剂的凝结时间和抗压强度测试结果
[0048][0049]
从表2可以看出,随着铝酸盐水泥基粉体速凝剂掺量的增加,初凝时间和终凝时间逐渐缩短,尤其是掺量从4%增加至6%时,但随着掺量继续增加,凝结时间基本上不再缩短;同样,1d抗压强度和28d抗压强度比随粉体速凝剂掺量的增加,与凝结时间的变化规律一致,先是大幅提升,但随后增加的幅度较小,甚至是稍有降低(但在实际应用中认为基本不变)。在掺量范围内,均能较好地满足对凝结时间和抗压强度的要求。
[0050]
实施例2
[0051]
本实施例的铝酸盐水泥基粉体速凝剂,与实施例1的区别在于各原料的添加量不同,具体的,铝酸盐水泥4000g、碳酸钠2000g、硫酸铝1500g、硫酸钠1500g、熟石灰1000g,制备方法及性能测试方法均与实施例1中的相同,不再赘述。
[0052]
本实施例的铝酸盐水泥基粉体速凝剂与不同水泥的凝结时间和抗压强度测试结果如表3所示。
[0053]
表3不同水泥的凝结时间和抗压强度测试结果
[0054][0055]
从表3与表2对比可以看出,当在规定的比例范围内,变化粉体速凝剂的组成时,本发明铝酸盐水泥基粉体速凝剂与各种硅酸盐水泥仍具有较好的匹配性。同样,在固定其掺量为6%时,对硅酸盐水泥、普通硅酸盐水泥、粉煤灰硅酸盐水泥等均具有较好的适用性。其中,本发明铝酸盐水泥基粉体速凝剂对硅酸盐水泥的速凝效果更好,其初凝时间小于3min,终凝时间小于6min,且力学性能更好,1d的抗压强度可高达10mpa以上,28d抗压强度比可高达90%以上。
[0056]
实施例3
[0057]
本实施例的铝酸盐水泥基粉体速凝剂,与实施例1的区别在于各原料的添加量不同,具体的,铝酸盐水泥6000g、碳酸钠1000g、硫酸铝1000g、硫酸钠1000g、熟石灰1000g,制备方法及性能测试方法均与实施例1中的相同,不再赘述。
[0058]
本实施例的铝酸盐水泥基粉体速凝剂与不同水泥的凝结时间和抗压强度测试结果如表4所示。
[0059]
表4不同水泥的凝结时间和抗压强度测试结果
[0060][0061]
从表4与表2、表3的对比可以看出,当在规定的比例范围内,变化速凝剂的组成时,本发明铝酸盐水泥基粉体速凝剂与各种硅酸盐水泥仍具有较好的匹配性。同样,在固定其掺量为6%时,对硅酸盐水泥、普通硅酸盐水泥、粉煤灰硅酸盐水泥等均具有较好的适用性。其中,本发明铝酸盐水泥基粉体速凝剂对硅酸盐水泥的速凝效果更好,其初凝时间小于3min,终凝时间小于6min,且力学性能更好,1d的抗压强度可高达10mpa以上,28d抗压强度比可高达90%以上。
[0062]
对比例1
[0063]
本对比例固定粉体速凝剂的掺量为水泥质量(即胶凝材料质量)的6%,且固定碳酸钠为1500g,硫酸铝为1500g,硫酸钠为1500g,熟石灰为1500g,变化铝酸盐水泥的量分别为0g、2000g、4000g、5000g、6000g、8000g,采用硅酸盐水泥,对比观察铝酸盐水泥对凝结时间、1d抗压强度、28d抗压强度比的变化规律。其他操作与实施例1相同。
[0064]
参照实施例1的测试方法,本对比例的测试结果见表5。
[0065]
表5铝酸盐水泥对凝结时间和抗压强度测试的影响
[0066]
[0067]
从表5可以看出,在固定其掺量为6%时,变化粉体速凝剂组分中的铝酸盐水泥的用量,发现其随着铝酸盐水泥量的增加,硅酸盐水泥的初凝时间和终凝时间均先缩短后延长,1d的抗压强度则呈现先增大后减小,同样,28d抗压强度比也呈现先增大后减小的规律。
[0068]
以上所述仅为本发明的优选实施例,并不用于限制本发明,对于本领域的技术人员来说,本发明可以有各种更改和变化。凡在本发明的精神和原则之内,所作的任何修改、等同替换、改进等,均应包含在本发明的保护范围之内。
再多了解一些
本文用于企业家、创业者技术爱好者查询,结果仅供参考。