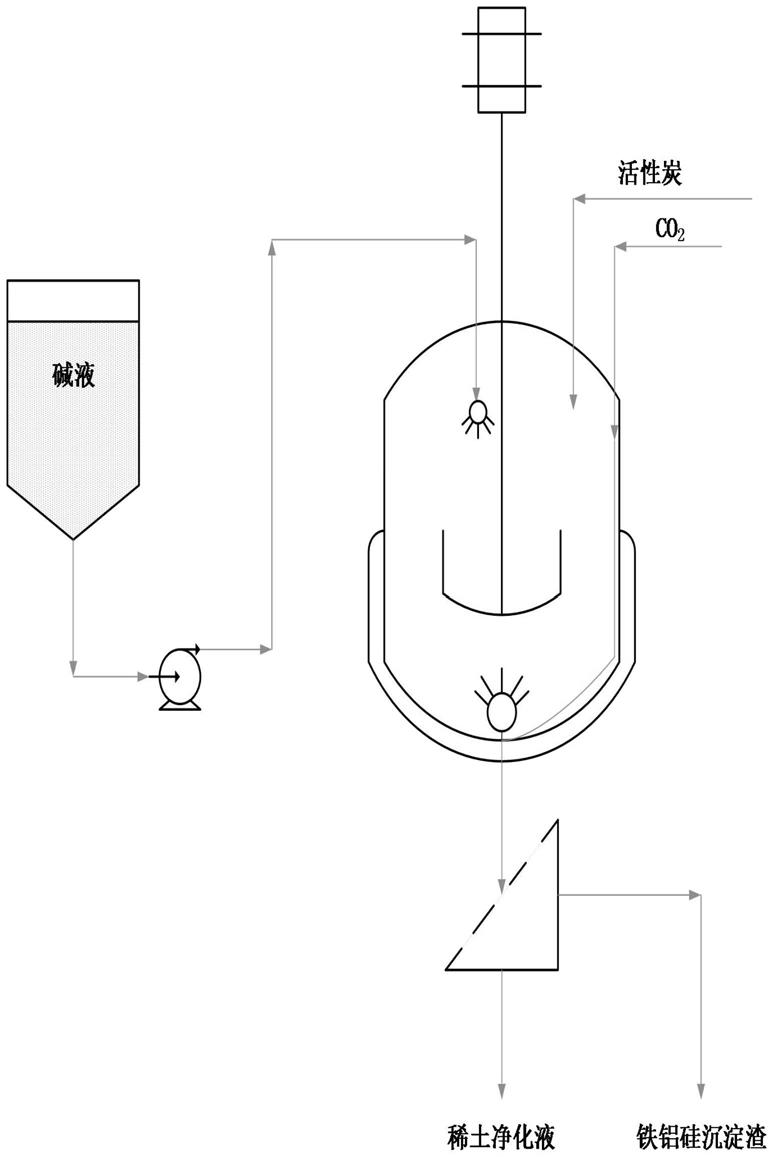
1.本发明涉及一种从稀土浸出液中脱除铁、铝、硅等杂质的方法,属于有色金属冶金领域。
技术背景
2.稀土元素因其优异的磁、光、电性能,被誉为“工业催化剂”和“高新技术产业的维生素”。我国是稀土资源和生产大国,特别是高精尖的中重稀土,更是世界独有。据报道,全球稀土储量为1.2亿吨,我国有4400万吨,占有率超过38%。2018年全球稀土矿产品产量约19.5万吨,中国产量约12万吨,占62%;全球稀土冶炼分离产量约为14.6万吨,其中中国产量12.5万吨,约占86%。尽管我国在稀土开采、冶炼、加工方面具有较为明显的优势,但作为一种不可再生资源,如何提升稀土的资源利用率和产业的竞争力是对我国稀土产业的可持续发展具有重要的意义。
3.铁、铝、硅是稀土浸出液中主要的杂质元素,特别是铝,其含量高低对稀土产品的品质和价值影响十分显著。此外,当浸出液中杂质含量过高时,铁、铝、硅在萃取分离系统中水解形成水包油型乳状液,使得萃取剂产生乳化现象,导致生产难以进行。目前,铁、铝脱除方法包括萃取、沉淀、离子交换等工艺,其中以萃取应用最为广泛。萃取通常以环烷酸体系(环烷酸 煤油 异辛醇)为萃取体系,在ph=0.5-1条件下,对稀土浸出液进行萃取除杂,然后采用盐酸进行反萃。环烷酸对铝的脱除效果较好,对铁和硅的脱除效果较差。此外,环烷酸在使用过程中易老化降解,这使得其在应用过程中指标波动较大,控制难度较高。
4.沉淀法以液碱、氨水等为中和剂,将稀土浸出液ph调至5.0以上,使得铁、铝、硅发生水解沉淀,从而使得其稀土浸出液中被脱除。尽管沉淀法可以脱除杂质,但稀土损失较大,碱耗较高,加之所得沉淀通常为胶体,过滤十分困难,无法满足生产要求,因而一直未被推广应用。
5.离子交换法的除杂原理同萃取法相似,对铝具有较好的脱除效果,对铁、硅的脱除效果不佳。此外,其使用过程产生大量废水、且稀土损失较大,因而,这一方法目前仍停留在研究阶段。
6.因此,当前无论环烷酸萃取除杂,还是沉淀法除杂,均存在明显的不足,如铁、铝、硅的脱除效果不佳、使用成本较高、稀土损失大。尽管环烷酸是目前主流的除杂工艺,但其仅对铝具有较好的分离效果,对铁、硅效果不佳,且由于其老化现象明显,这使得企业在生产管理和经营上面临诸多困难,因而业界亟需开发一种工艺简单、可同步脱除杂质、低成本的稀土浸出液净化方法。
技术实现要素:
7.本发明以上述发现为立足点,针对现有稀土浸出液中铁、铝、硅脱除方法的不足,提供了一种工艺简单、成本低廉、可同步脱除铁、铝、硅杂质的稀土浸出液除杂方法。
8.稀土矿物不同于其他常规的金属矿物,其有价稀土相含量较低,且铁、铝、硅等杂
质相含量高是困扰稀土矿物浸出的主要因素。与其它常见有色金属湿法浸出和净化工艺不同,稀土采用盐酸浸出体系,其对铁、铝等杂质的溶解能力更强,同时大多数金属离子与氯离子能够形成配合物,这使得铁、铝等杂质在盐酸浸出体系中脱除难度较大。尤其是,铝和稀土的溶液性质较为相似,两者分离十分困难,这也是稀土净化除杂的难点之一。
9.针对稀土元素的除杂,现有技术通常是通过提高稀土浸出液ph,达到将铁、铝、硅等杂质沉淀脱除的目的,该方法虽能达到一定的效果,但存在两个致命的缺陷,第一,所得沉淀物稀土含量高达2-5%,这使得稀土损失较高,技术经济指标不佳;第二,所得沉淀物为无定型的胶体物质,液固分离十分困难,导致生产过程无法应用。为此,本发明人通过深入研究,提供以下技术方案:
10.一种稀土浸出液除杂方法,包括以下步骤:
11.步骤(1):将碱液以雾化的方式添加至包含晶种的稀土浸出液中,在剪切搅拌下进行除杂反应,控制除杂反应终点溶液的ph≧5.0;所述的稀土浸出液为含有铁、铝、硅中至少一种杂质元素的溶液;
12.步骤(2):随后向浸出反应溶液体系中鼓入含co2气体,进行陈化反应;最后经固液分离,得到稀土净化液和杂质渣。
13.为了改善溶液中稀土和铁、铝、硅中至少一种杂质元素的选择性,本发明提供了所述的技术方案,其通过碱液加料方式、分散方式、晶种作用以及二氧化碳选择性分离等改进手段协同改善溶液中稀土和铁、铝、硅中至少一种杂质元素的选择性,从而改善杂质元素的脱除率,降低稀土的损失。
14.本发明技术方案,通过改进加料和分散方式,将碱液采用雾化的方式加入,配合剪切搅拌分散方式以及晶种作用,如此可以改善杂质与稀土的分离选择性,提升杂质的脱除率,且降低稀土的沉淀损失。在此基础上,进一步配合后续二氧化碳陈化操作,可进一步有效降低杂质渣中稀土含量,降低稀土损失率。此外,本发明技术方案,还可有效改变杂质渣形态,抑制杂质形成无定型的胶体物质,提高过滤效率的同时减少液固分离时间。因此,通过雾化加料、剪切分散,二氧化碳的选择性溶解和晶种的联合,可有效降低沉淀渣中稀土含量,改善沉淀渣的过滤性能。
15.本发明创新地利用雾化方式使稀土浸出液表面与碱雾接触,并在晶种辅助、剪切分散下进行选择性除杂反应,如此能够有效改善稀土和铁、铝、硅的分离选择性,此外,利用晶种沉积和吸附作用改变沉淀物形态。此外,本发明技术方案未对步骤(1)的体系进行固液分离,直接通入二氧化碳陈化,如此可进一步改善稀土和铁、铝、硅选择性,在避免杂质返溶的同时,有效溶解沉淀的稀土,进一步降低稀土的损失。不仅如此,还有效改善沉淀形态,降低固液分离难度。本发明技术方案可通过一次固液分离,即可实现稀土和杂质的高效分离。
16.本发明中,所述的稀土浸出液中的稀土元素可以为行业内能够获知的任意稀土元素,例如为la、nd、y、sm、gd、ce、dy中的至少一种。
17.本发明中,所述稀土浸出液为稀土元素水溶性盐溶液(水溶液);优选为稀土盐酸盐(氯化稀土)溶液;优选地,稀土浸出液的ph为1-5。
18.例如,所述的稀土浸出液可以是稀土矿物的盐酸浸出液。
19.本发明中技术方案,可用于脱除稀土浸出液中的铁、铝、硅中的至少一种杂质。所述的稀土浸出液中,铁、铝、硅含量分别不低于5、300、40mg/l。
20.本发明中,所述晶种为活性炭、焦炭粉或木炭粉中的至少一种。
21.优选地,晶种的粒度大于325目。
22.本发明中,晶种的添加量可基于使用需求进行调整,例如为0.1~1g/l(每l稀土浸出液中添加0.1~1g晶种);优选为0.3~0.75g/l。
23.本发明中,所述高速剪切搅拌的搅拌速度不低于2000rpm;优选为2500~6000rpm。
24.本发明中,所述碱液为氢氧化钠、氨水、碳酸氢铵或碳酸氢钠中的至少一种水溶液。
25.作为优选,所述的碱液的浓度为2~5m;优选为2~3m。
26.本发明中,可采用现有雾化方式,将所述的碱液制成碱雾。
27.作为优选:所述碱液的雾化方式为压力雾化。
28.本发明中,除杂反应过程无额外加热,作为优选,所述浸出反应过程的温度≦50℃。
29.本发明中,除杂反应终点的溶液的ph控制在5.1~5.5。
30.本发明技术方案,对浸出的混悬体系不进行固液分离,直接进行二氧化碳陈化,如此有助于改善除杂选择性,改善杂质脱除率,降低稀土的损失。不仅如此,还有助于降低固液分离次数,且改善沉淀的形态,降低固液分离的难度以及“穿滤”现象。
31.作为优选,含co2气体为包含二氧化碳的气体,其可以为纯二氧化碳气体或者二氧化碳混合气;其中二氧化碳的浓度不低于30%。
32.本发明技术方案,直接向除杂反应体系中鼓入含co2气体,利用曝气洗涤的方式,进一步降低稀土损失。
33.作为优选,陈化的时间为2-6h。
34.本发明技术方案,通过简单的固液分离手段,例如过滤,即可实现稀土和杂质的选择性分离。
35.本发明一种优选的从稀土浸出液中同步脱除铁、铝、硅的方法,首先,以稀土浸出液为底液,加入一定量晶种,开启高速剪切搅拌,然后将碱液以雾化的方式加入其中,控制浸出终点ph为5.0以上,加料完成后,鼓入co2继续陈化反应2-6h后,过滤即可得到低杂质的稀土净化液和低稀土含量的杂质沉淀渣。
36.本发明进一步优选的从稀土浸出液中同步脱除铁、铝、硅的方法,包括下述步骤:
37.步骤一:将稀土浸出液加入到反应釜中,并加入一定量的晶种,开启高速剪切搅拌,然后将碱液按照一定速度以雾化的方式加入反应釜中,控制终点ph大于5.0。
38.步骤二:待料液ph≧5.0后,向反应釜中鼓入co2,继续反应2-6h,即可结束反应,过滤获得低杂质的稀土净化液和富含铁铝硅的沉淀渣。沉淀渣经洗涤后送渣库堆存,稀土净化液则送萃取工序进行不同稀土元素的分离。
39.原理和优势
40.本发明通过雾化、剪切和晶种的联合作用下,可提升杂质和稀土的分离选择性,进一步配合所述的晶种以及二氧化碳鼓泡陈化,有助于进一步促进杂质沉淀渣与稀土的有效分离。通过上述工作,实现稀土浸出液中铁、铝、硅等杂质的高效、深度脱除,同时,降低稀土的损失,提高稀土的回收。
41.本发明与现有技术相比较具有以下优势:
42.(1)本发明工艺简单、易于操作、装备要求低,易于实现产业化。
43.(2)本发明杂质脱除深度高、成本低,可有效提升稀土产品的品质,提高产品附加值。
44.(3)本发明杂质沉淀渣稀土含量低,稀土回收率高,且过滤性能好,有利于稀土生产效率的提升。
45.(4)本发明环境友好,无废气、废水的产生,并可实现稀土资源的高效利用和废渣的减量化。
附图说明
46.附图1为本发明的工艺流程图
具体实施方式
47.以下实施例旨在进一步说明本发明内容,而不是限制本发明权利要求保护的范围。
48.实施例1:
49.在反应釜中加入8m3的稀土浸出液(fe:865mg/l、al:1425mg/l、si:177mg/l、ph:1.5)中,加入4kg活性炭粉,开启高速剪切搅拌机,搅拌速度为3500rpm,然后向反应釜中以雾化的方式加入3m氨水溶液,加料速度为0.2m3/h。待浸出液ph上升至5.2时,继续搅拌45min,控制反应终点的ph为5.2;然后向反应釜中通入浓度为60%的co2气体,气体流量为3.2m3/h,继续反应4h后,即可结束反应,经液固分离后,得到沉淀渣和稀土净化液,其中沉淀渣(以干重计)中稀土(稀土总量)含量为0.34%(重量),稀土净化液中铁、铝、硅含量分别为3.7、247.5、34.5mg/l。
50.对比例1:
51.和实施例1相比,区别仅在于,未采用雾化方式加入碱,具体为:
52.在反应釜中加入8m3的稀土浸出液(fe:865mg/l、al:1425mg/l、si:177mg/l、ph:1.5)中,加入4kg活性炭粉,开启搅拌,搅拌速度为300rpm,然后向反应釜中加入3m氨水溶液,加料速度为0.2m3/h。待浸出液ph上升至5.2时,继续搅拌45min,控制反应终点的ph为5.2;然后向反应釜中通入浓度为60%的co2气体,气体流量为3.2m3/h,继续反应4h后,即可结束反应,经液固分离后,得到沉淀渣和稀土净化液,其中沉淀渣中稀土含量为1.07%,稀土净化液中铁、铝、硅含量分别为34.7、871.6、67.3mg/l。
53.附表1为实施例1和对比例1所得沉淀渣xrf结果
54.表1
[0055] landysmgdceonas实施例10.180.0840.0220.0030.0120.07323.3220.4410.026对比例10.8570.5860.1470.1580.1140.60425.3580.3440.051 srsialfemgcabaclk实施例10.00224.2115.3145.5670.2040.2433.3220.0273.209对比例10.01223.8744.5214.3160.1670.2122.3580.9722.547
[0056]
由表1可以看出,实施例1所得杂质沉淀渣的稀土含量明显低于对比例1,这充分证
实了加料方式、高速剪切分散等措施能够有效解决碱液局部过浓的问题,从而降低稀土的沉淀,在此基础上,通过co2曝气选择性溶解沉淀渣中的稀土,从而有效降低沉淀渣中稀土,避免稀土的损失。
[0057]
实施例2:
[0058]
在反应釜中加入8m3的稀土浸出液(fe:1308mg/l、al:907mg/l、si:204mg/l、ph:1.2)中,加入5kg活性炭粉,开启高速剪切搅拌机,搅拌速度为5000rpm,然后向反应釜中以雾化的方式加入2.8m碳酸氢铵溶液,加料速度为0.35m3/h。待浸出液ph上升至5.1时,继续搅拌80min,控制反应终点的ph为5.1;然后向反应釜中通入浓度为75%的co2气体,气体流量为4.5m3/h,继续反应5h后,即可结束反应,经液固分离后,得到沉淀渣和稀土净化液,其中沉淀渣中稀土含量为0.41%,稀土净化液中铁、铝、硅含量分别为3.1、285.7、32.7mg/l。
[0059]
对比例2:
[0060]
和实施例2相比,区别仅在于,未进行二氧化碳鼓泡陈化,具体为:
[0061]
在反应釜中加入8m3的稀土浸出液(fe:1308mg/l、al:907mg/l、si:204mg/l、ph:1.2)中,加入5kg活性炭粉,开启高速剪切搅拌机,搅拌速度为5000rpm,然后向反应釜中以雾化的方式加入2.8m碳酸氢铵溶液,加料速度为0.35m3/h。待浸出液ph上升至5.1时,继续搅拌80min,即可结束反应,控制反应终点的ph为5.1;经液固分离后,得到沉淀渣和稀土净化液,其中沉淀渣中稀土含量为2.87%,稀土净化液中铁、铝、硅含量分别为13.7、415.1、48.7mg/l。
[0062]
通过实施例2和对比例2比较可知,通过二氧化碳的鼓泡陈化,可选择性溶出稀土,且能够使沉淀颗粒发生沉淀转化,颗粒增大,减少了“穿滤”现象的发生,从而进一步降低沉淀渣中稀土损失,改善沉淀渣的过滤性能。
[0063]
实施例3:
[0064]
在反应釜中加入8m3的稀土浸出液(fe:865mg/l、al:1425mg/l、si:177mg/l、ph:1.5)中,加入2kg活性炭粉,开启高速剪切搅拌机,搅拌速度为4000rpm,然后向反应釜中以雾化的方式加入2.2m naoh溶液,加料速度为0.12m3/h。待浸出液ph上升至5.1时,继续搅拌60min,控制反应终点的ph为5.1;然后向反应釜中通入浓度为90%的co2气体,气体流量为5m3/h,继续反应3h后,即可结束反应,经液固分离后,得到沉淀渣和稀土净化液,其中沉淀渣中稀土含量为0.44%,稀土净化液中铁、铝、硅含量分别为4.4、266.4、36.7mg/l。
[0065]
实施例4:
[0066]
在反应釜中加入8m3的稀土浸出液(fe:865mg/l、al:1425mg/l、si:177mg/l、ph:1.5)中,加入6kg活性炭粉,开启高速剪切搅拌机,搅拌速度为6000rpm,然后向反应釜中以雾化的方式加入2m碳酸氢钠溶液,加料速度为0.15m3/h。待浸出液ph上升至5.3时,继续搅拌100min,控制反应终点的ph为5.3;然后向反应釜中通入浓度为40%的co2气体,气体流量为5m3/h,继续反应6h后,即可结束反应,经液固分离后,得到沉淀渣和稀土净化液,其中沉淀渣中稀土含量为0.46%,稀土净化液中铁、铝、硅含量分别为2.1、231.4、27.3mg/l。
[0067]
实施例5:
[0068]
在反应釜中加入8m3的稀土浸出液(fe:1297mg/l、al:1672mg/l、si:185mg/l、ph:1.1)中,加入3kg活性炭粉,开启高速剪切搅拌机,搅拌速度为3000rpm,然后向反应釜中以雾化的方式加入2.7m氨水溶液,加料速度为0.4m3/h。待浸出液ph上升至5.3时,继续搅拌
50min,控制反应终点的ph为5.3;然后向反应釜中通入浓度为80%的co2气体,气体流量为4.5m3/h,继续反应5h后,即可结束反应,经液固分离后,得到沉淀渣和稀土净化液,其中沉淀渣中稀土含量为0.38%,稀土净化液中铁、铝、硅含量分别为2.4、257.8、30.9mg/l。
[0069]
实施例6:
[0070]
在反应釜中加入8m3的稀土浸出液(fe:1308mg/l、al:907mg/l、si:204mg/l、ph:1.2)中,加入2.5kg活性炭粉,开启高速剪切搅拌机,搅拌速度为4000rpm,然后向反应釜中以雾化的方式加入2.4m碳酸氢钠溶液,加料速度为0.2m3/h。待浸出液ph上升至5.3时,继续搅拌70min,控制反应终点的ph为5.3;然后向反应釜中通入浓度为70%的co2气体,气体流量为4m3/h,继续反应4.5h后,即可结束反应,经液固分离后,得到沉淀渣和稀土净化液,其中沉淀渣中稀土含量为0.44%,稀土净化液中铁、铝、硅含量分别为4.3、281.8、34.9mg/l。
[0071]
实施例7:
[0072]
在反应釜中加入8m3的稀土浸出液(fe:1297mg/l、al:1672mg/l、si:185mg/l、ph:1.1)中,加入4kg活性炭粉,开启高速剪切搅拌机,搅拌速度为2500rpm,然后向反应釜中以雾化的方式加入2m碳酸氢铵溶液,加料速度为0.3m3/h。待浸出液ph上升至5.1时,继续搅拌80min,控制反应终点的ph为5.1;然后向反应釜中通入浓度为85%的co2气体,气体流量为5m3/h,继续反应6h后,即可结束反应,经液固分离后,得到沉淀渣和稀土净化液,其中沉淀渣中稀土含量为0.47%,稀土净化液中铁、铝、硅含量分别为4.4、276.8、34.7mg/l。
再多了解一些
本文用于企业家、创业者技术爱好者查询,结果仅供参考。