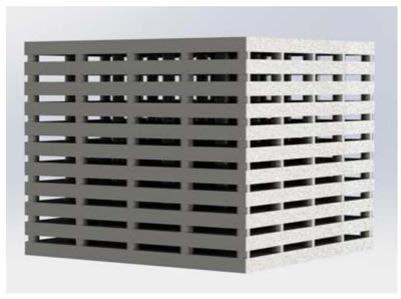
1.本发明涉及层状陶瓷的制备技术,具体地说是一种致密的层状碳化硅陶瓷及其制备方法。
背景技术:
2.碳化硅具有优异的高硬度、耐高温、抗氧化、耐酸碱腐蚀、抗热震性能和半导体特性,在装甲防护、耐磨、耐烧蚀和密封等领域获得了广泛的应用。但是,碳化硅陶瓷固有脆性特征限制了其作为结构件的应用范围。层状碳化硅陶瓷为陶瓷复合材料设计提供了充足的设计空间,是实现陶瓷增韧的有效方法之一。
3.目前,层状陶瓷制备有以下几种方法:流延成型法、冷冻干燥法、电泳沉积法、3d增材制造法等。
4.流延成型法是将含有一定量陶瓷微粉、溶剂、有机添加剂、分散剂、粘接剂等利用球磨等配制成分散效果良好的陶瓷料浆,除气后在不同材质的薄板上流延成薄层预制体,通过切割、堆积获得层状结构预制体,通过中温除掉有机物,高温烧结获得层状陶瓷。
5.冷冻干燥法、利用陶瓷料浆中的水或有机溶剂在低温环境中的定向凝固,形成规则的晶体结构,然后在真空状态下升华除去水或有机溶剂,留下层状结构,通过高温烧结过的规则排列的层状陶瓷。
6.电泳沉积法是指在定向电场的作用下,悬浮液中的荷电陶瓷颗粒沉积到相反极性的电极上通过不同荷电陶瓷颗粒多次交叉沉积,形成层状结构。
7.3d增材制造法,利用计算模型通过3d打印技术可以逐层增材制造出几乎任何复杂结构的材料,是一种创新性的材料制造方法。
技术实现要素:
8.本发明的目的在于提供一种致密的层状碳化硅陶瓷及其制备方法,用该方法制备的层状碳化硅陶瓷中的陶瓷密度高、残余硅含量低、组织致密均匀。
9.本发明的技术方案是:
10.一种致密的层状碳化硅陶瓷,层状碳化硅陶瓷以薄片状碳化硅陶瓷为基本单元,各基本单元以叠层方式利用分立式碳化硅陶瓷柱连接的三层以上结构;层状碳化硅陶瓷中,碳化硅陶瓷基本单元和碳化硅陶瓷柱的相对致密度≥99%;按重量百分比计,碳化硅陶瓷基本单元和碳化硅陶瓷柱各自的成份由90%~98%的碳化硅和10%~2%的硅组成,平均晶粒尺寸在50nm~50μm。
11.所述的致密的层状碳化硅陶瓷的制备方法,致密的层状碳化硅陶瓷的制备工艺包括:以碳化硅粉和高产碳率树脂为原料,配制碳化硅料浆
→
以铝箔为模板,在铝箔单面或双面均匀涂挂碳化硅浆料
→
热压致密化
→
热解
→
反应烧结
→
高温除残余硅。
12.所述的致密的层状碳化硅陶瓷的制备方法,具体包括如下步骤:
13.(1)碳化硅料浆配制
14.按碳化硅粉、高产碳率树脂、固化剂、乙醇之间重量百分比例为60wt%~20wt%:19wt%~30wt%:1wt%~10wt%:20wt%~40wt%,将碳化硅粉、高产碳率树脂、固化剂和乙醇混合,经机械搅拌后,球磨、过滤得料浆;
15.(2)涂挂
16.将铝箔剪裁成所需形状和尺寸,单面或双面均匀地涂挂陶瓷,通过限位刮板除去多余料浆,使料浆达到设计的厚度,采用风干和加热方式使陶瓷料浆半固化,得到单层碳化硅陶瓷前驱体;
17.(3)热压致密化
18.将单层碳化硅陶瓷前驱体依次叠层,获得叠层前驱体;按照确定孔径尺寸和孔间距分布在叠层前驱体上钻孔;将均布钻孔的叠层前驱体放入加热的模具中进行高温、高压固化;在加热加压过程中,铝箔表面涂挂的部分半固化陶瓷料浆在高温高压的作用下,流动到叠层前驱体预钻孔的孔隙中,填充孔隙并逐渐固化,形成均匀分布的碳化硅陶瓷柱,使得叠层前驱体连接在一起,获得致密的层状碳化硅陶瓷前驱体;
19.(4)热解
20.将致密的层状碳化硅陶瓷前驱体在保护气氛或真空条件下进行热解,保护气氛为氩气、氮气或其它惰性气体,升温速率每分钟1~5℃,升温至600~1200℃,保温0.5~2小时,获得层状碳化硅陶瓷前驱体碳骨架;
21.(5)反应烧结
22.将热解后的层状碳化硅陶瓷前驱体碳骨架通过反应烧结渗硅,在层状碳化硅陶瓷前驱体碳骨架上方放置硅块,硅块尺寸范围为20mm~20目,硅块与碳骨架的重量比为(0.2~0.7):1,在保护气氛或真空条件下进行,保护气氛为氩气、氮气或其它惰性气体,升温速率为每分钟5~15℃,温度为1500~1900℃,保温0.5~4小时,得富“硅”的层状碳化硅陶瓷材料;
23.(6)高温除掉残余硅
24.将富“硅”的层状碳化硅陶瓷材料放在富“碳”的垫板上,富“碳”的垫板为石墨纸、石墨板或碳颗粒,在真空条件下进行,升温速率为每分钟5~15℃,温度为1700~1900℃,保温0.5~2小时,除掉层状碳化硅陶瓷材料的层间隙中未反应的残余硅,获得致密的层状碳化硅陶瓷。
25.所述的致密的层状碳化硅陶瓷的制备方法,步骤(1)中,高产碳率树脂选自环氧树脂、酚醛树脂、糠醛树脂、酚醛/酚糠醛树脂之一种或两种以上,固化剂选自对甲苯磺酸、五洛脱品、草酸或柠檬酸,固化剂的含量为树脂重量的1~20%,碳化硅粉的平均粒度为10nm~50μm,料浆中固形物的重量为料浆总量的30~80%。
26.所述的致密的层状碳化硅陶瓷的制备方法,步骤(2)中,半固化时的加热方式为:在50~100℃温度下,时间10分钟~2小时。
27.所述的致密的层状碳化硅陶瓷的制备方法,步骤(3)中,热压致密化过程中,加压的压力为10~80mpa,加热的温度在100~300℃,升温速度1~5℃,保温5分钟~3小时。
28.所述的致密的层状碳化硅陶瓷的制备方法,步骤(4)中,在热解过程中,热解温度在800~1000℃范围,升温速率2~4℃/min。
29.所述的致密的层状碳化硅陶瓷的制备方法,铝箔为工业包装用铝箔,厚度0.1~
1mm;热解后的层状碳化硅陶瓷前驱体需要除去铝箔,除去铝箔的方法有两种:一是利用反应烧结的高温使铝箔气化除掉铝箔;二是在热解后利用酸碱溶液与铝反应除掉铝箔。
30.所述的致密的层状碳化硅陶瓷的制备方法,当步骤(5)中的硅块与碳骨架的重量比为(0.2~0.3):1范围内,取消高温除掉残余硅过程。
31.本发明的设计思想是:
32.将碳化硅粉与高产碳率树脂混合制成料浆。选择合适厚度的铝箔,将铝箔剪裁成所需形状和尺寸,单面或双面均匀地涂挂料浆,通过限位刮板除去多余料浆,使料浆达到设计的厚度,采用风冷和加热方式使料浆半固化。将若干单层涂挂碳化硅陶瓷料浆的铝箔叠层,获得一定厚度的叠层前驱体。按照确定孔径尺寸和孔间距分布在叠层前驱体上钻孔。将均布钻孔的叠层前驱体放入加热的模具中进行高温、高压固化。
33.将固化后的叠层前驱体在真空或惰性气体保护炉中进行树脂热解,得到由碳化硅与热解碳组成的层状碳骨架。经过反应烧结过程,层状碳骨架中的碳与气相或液相硅反应生成碳化硅,并与层状骨架中的原始碳化硅颗粒结合起来,通过高温除硅的方法将层间隙中未反应的残余硅除掉,从而得到致密的层状碳化硅陶瓷。
34.本发明具有如下优点及有益效果:
35.1、层状陶瓷致密度高、显微组织均匀、残余硅量少
36.本发明采用热压固化层状陶瓷前驱体的方法,不仅显著提高了层状陶瓷前驱体的初始密度,还消除了涂挂过程中形成的显微组织不均匀问题。热压固化措施的采用使陶瓷的致密度保持在99%以上、残余硅含量减少到10%以下(一般在5%以下)、显微组织十分均匀,见图1(a)-(b)、图2(a)-(b)。
37.2、工艺简单,适合批量生产
38.本发明铝箔表面涂挂碳化硅料浆工艺简单,可操作性强,铝箔为工业包装用铝箔,除去铝箔的方法简单、技术成熟。
39.反应烧结碳化硅技术是一种成本低、适合于工业大规模生产的技术方法,具有致密化温度低、时间短、收缩率低、变形程度小的特点,适合于大尺寸、复杂形状构件的制造,易于获得净尺寸产品,减少后续加工成本。
40.3、本发明层状碳化硅陶瓷为复合材料开发提供了广泛的设计空间,并提出了一种陶瓷结构增韧的思路。
附图说明
41.图1(a)-(b)为层状碳化硅陶瓷的结构图。其中,图1(a)为立体示意图,图1(b)为宏观形貌。
42.图2(a)-(b)为层状碳化硅陶瓷的微观形貌。其中,图2(a)为抛光后的微观形貌图,图2(b)为碳化硅陶瓷断口微观形貌图。
43.图3为层状碳化硅陶瓷与铝合金复合后的宏观形貌图。
具体实施方式
44.在具体实施过程中,致密的层状碳化硅陶瓷制备方法的流程如下:配制碳化硅陶瓷料浆
→
在铝箔单面或双面均匀涂挂碳化硅浆料
→
热压致密化
→
热解
→
反应烧结
→
高温
除残余硅。改善碳化硅陶瓷韧性提高其抗冲击性能是碳化硅陶瓷研究的重要方向。层状陶瓷是一种特殊的结构陶瓷,以薄片状碳化硅为基本单元,各基本单元以叠层方式利用分立式碳化硅陶瓷柱连接的多层结构。利用层状碳化硅陶瓷的层状结构间隙,将韧性相(如:金属、聚合物等)填充到层状结构间隙中,在承受冲击载荷时,可以改变裂纹的传输途径、扩展机制、降低材料对裂纹的敏感性,进而提高陶瓷的韧性。
45.下面,通过实施例详述本发明。
46.实施例1
47.本实施例中,将重量比分别为50%:25%:5%:20%的平均粒度2μm碳化硅粉、氨酚醛树脂、对甲苯磺酸、无水乙醇配料,球磨3小时,过滤制成料浆。将0.5mm厚度的铝箔剪裁成所需形状和尺寸,单面均匀地涂挂料浆,通过限位刮板除去多余料浆控制料浆厚度0.6mm,风干后于烘箱中进行半固化,温度50℃,时间10分钟,得到单层碳化硅陶瓷前驱体。将30层碳化硅陶瓷前驱体叠层,按照确定孔径尺寸φ4mm和孔间距10mm分布在叠层前驱体上钻孔。将均布钻孔的叠层前驱体放入加热的模具中进行高温、高压固化,压力12mpa,升温至250℃,升温速度3℃,保温1小时固化,得到钻孔中充满碳化硅料浆并且是完全固化的前驱体。将前驱体在氩气保护下热解,升温速率每分钟2℃,升温至800℃,保温0.5小时,生成层状碳化硅陶瓷前驱体碳骨架。热解后,进行反应烧结,硅块(平均尺寸2mm)与碳骨架的重量比为0.5:1,反应温度1800℃,全程抽真空,升温速率为10℃/分钟,保温1小时,得到富“硅”的层状碳化硅陶瓷材料。将富“硅”的层状碳化硅陶瓷材料放在石墨纸上,在真空条件下进行,升温速率为每分钟5℃,温度为1750℃,保温1小时,除掉层间隙中未反应的残余硅,获得致密层状碳化硅陶瓷材料。碳化硅陶瓷基本单元和碳化硅陶瓷柱的相对致密度为99%,按重量百分比计,碳化硅陶瓷基本单元和碳化硅陶瓷柱各自的成份由96%的碳化硅和4%的残余硅组成,碳化硅平均晶粒粒度为2.8μm。
48.实施例2
49.本实施例中,将重量比分别为50%:20%:3%:27%的平均粒度7μm碳化硅粉、氨酚醛树脂、对甲苯磺酸、无水乙醇配料,球磨1小时,过滤制成料浆。将0.3mm厚度的铝箔剪裁成所需形状和尺寸,单面均匀地涂挂料浆,通过限位刮板除去多余料浆控制料浆厚度0.5mm,风干后放于烘箱中进行半固化,温度50℃,时间10分钟,得到单层碳化硅陶瓷前驱体。将30层碳化硅陶瓷前驱体叠层,按照确定孔径尺寸φ4mm和孔间距10mm分布在叠层前驱体上钻孔。将均布钻孔的叠层前驱体放入加热的模具中进行高温、高压固化,压力20mpa,升温至250℃,升温速度2℃,保温1小时固化,得到钻孔中充满碳化硅料浆并且是完全固化的前驱体。将前驱体在氩气保护下热解,升温速率每分钟2℃,升温至800℃,保温0.5小时,生成层状碳化硅陶瓷前驱体碳骨架。将碳骨架放入浓度30wt%、温度90℃的氢氧化钠水溶液中处理30min,取出清水冲洗后烘干;进行反应烧结,硅块(平均尺寸15mm)与碳骨架的重量比为0.4:1,反应温度1800℃,在氩气保护下,升温速率为10℃/分钟,保温1小时,得到富“硅”的层状碳化硅陶瓷材料。将富“硅”的层状碳化硅陶瓷材料放在石墨板上,在真空条件下进行,升温速率为每分钟5℃,温度为1700℃,保温1小时,除掉层间隙中未反应的残余硅,获得致密层状碳化硅陶瓷材料。碳化硅陶瓷基本单元和碳化硅陶瓷柱的相对致密度为99%,按重量百分比计,碳化硅陶瓷基本单元和碳化硅陶瓷柱各自的成份由95%的碳化硅和5%的残余硅组成,碳化硅平均晶粒粒度为8μm。
50.实施例3
51.本实施例中,将重量比分别为45%:25%:3%:27%的平均粒度2μm碳化硅粉、氨酚醛树脂、对甲苯磺酸、无水乙醇配料,球磨1小时,过滤制成料浆。将0.5mm厚度的铝箔剪裁成所需形状和尺寸,单面均匀地涂挂料浆,通过限位刮板除去多余料浆控制料浆厚度0.6mm,风干后于烘箱中进行半固化,温度50℃,时间10分钟,得到单层碳化硅陶瓷前驱体。将30层碳化硅陶瓷前驱体叠层,按照确定孔径尺寸φ3mm和孔间距8mm分布在叠层前驱体上钻孔。将均布钻孔的叠层前驱体放入加热的模具中进行高温、高压固化,压力40mpa,升温至200℃,升温速度4℃,保温1小时固化,得到钻孔中充满碳化硅料浆并且是完全固化的前驱体。将前驱体在氩气保护下热解,升温速率每分钟2℃,升温至1000℃,保温0.5小时,生成层状碳化硅陶瓷前驱体碳骨架。热解后,进行反应烧结,硅块(平均尺寸8目)与碳骨架的重量比为0.4:1,反应温度1700℃,全程抽真空,升温速率为10℃/分钟,保温1小时,得到富“硅”的层状碳化硅陶瓷材料。将富“硅”的层状碳化硅陶瓷材料放在辅成平面的碳颗粒上(80~120目),在真空条件下进行,升温速率为每分钟5℃,温度为1900℃,保温0.5小时,除掉层间隙中未反应的残余硅,获得致密层状碳化硅陶瓷材料。碳化硅陶瓷基本单元和碳化硅陶瓷柱的相对致密度为99%,按重量百分比计,碳化硅陶瓷基本单元和碳化硅陶瓷柱各自的成份由95%的碳化硅和5%的残余硅组成,碳化硅平均晶粒粒度为2.8μm。
52.实施例4
53.本实施例中,将重量比分别为45%:30%:5%:20%的平均粒度14μm碳化硅粉、氨酚醛树脂、对甲苯磺酸、无水乙醇配料,球磨2小时,过滤制成料浆。将0.1mm厚度的铝箔剪裁成所需形状和尺寸,双面均匀地涂挂料浆,通过限位刮板除去多余料浆控制料浆厚度0.3mm,风干后放于烘箱中进行半固化,温度50℃,时间10分钟,得到单层碳化硅陶瓷前驱体。将30层碳化硅陶瓷前驱体叠层,按照确定孔径尺寸φ2mm和孔间距6mm分布在叠层前驱体上钻孔。将均布钻孔的叠层前驱体放入加热的模具中进行高温、高压固化,压力30mpa,升温至250℃,升温速度1℃,保温1小时固化,得到钻孔中充满碳化硅料浆并且是完全固化的前驱体。将前驱体在氩气保护下热解,升温速率每分钟2℃,升温至800℃,保温0.5小时,生成层状碳化硅陶瓷前驱体碳骨架。将碳骨架放入浓度40wt%、温度70℃的盐酸溶液中处理60min,取出清水冲洗后烘干;进行反应烧结,硅块(平均尺寸5mm)与碳骨架的重量比为0.2:1,反应温度1900℃,全程抽真空,升温速率为10℃/分钟,保温1小时,得到致密层状碳化硅陶瓷材料。碳化硅陶瓷基本单元和碳化硅陶瓷柱的相对致密度为99%,按重量百分比计,碳化硅陶瓷基本单元和碳化硅陶瓷柱各自的成份由94%的碳化硅和6%的残余硅组成,碳化硅平均晶粒粒度为16μm。
54.实施例5
55.本实施例中,将重量比分别为45%:30%:5%:20%的平均粒度3.5μm碳化硅粉、氨酚醛树脂、对甲苯磺酸、无水乙醇配料,球磨2小时,过滤制成料浆。将0.1mm厚度的铝箔剪裁成所需形状和尺寸,双面均匀地涂挂料浆,通过限位刮板除去多余料浆控制料浆厚度0.3mm,风干后放于烘箱中进行半固化,温度50℃,时间10分钟,得到单层碳化硅陶瓷前驱体。将30层碳化硅陶瓷前驱体叠层,按照确定孔径尺寸φ2mm和孔间距6mm分布在叠层前驱体上钻孔。将均布钻孔的叠层前驱体放入加热的模具中进行高温、高压固化,压力30mpa,升温至250℃,升温速度5℃,保温1小时固化,得到钻孔中充满碳化硅料浆并且是完全固化的
前驱体。将前驱体在氩气保护下热解,升温速率每分钟2℃,升温至800℃,保温0.5小时,生成层状碳化硅陶瓷前驱体碳骨架。进行反应烧结,硅块(平均尺寸2mm)与碳骨架的重量比为0.3:1,反应温度1550℃,在氩气保护下,升温速率为10℃/分钟,保温1小时,得致密层状碳化硅陶瓷材料。碳化硅陶瓷基本单元和碳化硅陶瓷柱的相对致密度为99%,按重量百分比计,碳化硅陶瓷基本单元和碳化硅陶瓷柱各自的成份由96%的碳化硅和4%的残余硅组成,碳化硅平均晶粒粒度为4μm。
56.如图1(a)-(b)所示,从层状碳化硅陶瓷的结构图可以看出,层状碳化硅陶瓷以薄片状碳化硅陶瓷为基本单元,各基本单元以叠层方式利用分立式碳化硅陶瓷柱连接的三层以上结构。在薄片状碳化硅陶瓷之间存在间隙,可以利用挤压铸造的方法将熔融的金属(如:铝合金、铜合金等)压注到间隙中,获得碳化硅陶瓷/金属复合材料;利用等静压的方法将高分子(如:硅橡胶、聚脲、树脂等)压注到间隙中,获得碳化硅陶瓷/高分子复合材料。
57.如图2(a)-(b)所示,从层状碳化硅陶瓷的结构图可以看出,由微观形貌(a)看,抛光后的碳化硅陶瓷表面平整、组织均匀致密,未见明显的气孔。其原因在于制备过程中采用了热压致密化工艺,在高温高压作用下,半固化的碳化硅涂层中的树脂具有一定的流动性,可以填充碳化硅颗粒之间的间隙,显著降低预制体中的气孔率,提高了致密度。由微观形貌(b)看,碳化硅陶瓷的断裂方式是穿晶断裂和沿晶断裂,以穿晶断裂为主,表明陶瓷颗粒的结合良好,也进一步说明了碳化硅陶瓷具有很高的致密性。
58.如图3所示,从层状碳化硅陶瓷与铝合金复合后的宏观形貌图可以看出,层状碳化硅陶瓷与zl101铝合金分层清晰,界面结合良好,铝合金无疏松气孔等缺陷。
59.实施例结果表明,本发明提出的以铝箔为模板涂挂陶瓷料浆、热压成型、反应烧结的制备层状碳化硅陶瓷材料的方法,其优势在于:工艺简单、层间尺寸可控,可以快速低成本制备层状碳化硅陶瓷。采用热压多层陶瓷预制体的技术可以显著提高层状陶瓷致密度,利用层状结构增韧来提高碳化硅陶瓷的抗冲击性能是碳化硅陶瓷增韧的一个有效途径、对扩大碳化硅陶瓷应用范围具有重要的实际意义。
再多了解一些
本文用于企业家、创业者技术爱好者查询,结果仅供参考。