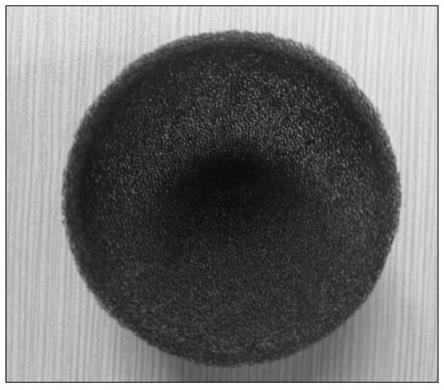
1.本发明属于多孔碳材料制备技术领域,具体涉及一种网状玻璃态多孔碳薄壁异形件及其制备方法。
背景技术:
2.网状玻璃态多孔碳是一种由玻璃态碳泡沫组成的三维网状微孔材料,开孔率高达90%~97%,密度小(0.03g/cm3),具有较高的化学稳定性、比表面积和导电率,导热率和热膨胀系数都很低,结构强度大,对流体的阻力小,生产成本较低等特点,在航空(如宇宙飞船的隔热层)、电化学、生物医学、环境保护等领域的应用非常广泛。
3.目前,国外在网状玻璃态多孔碳材料研究应用方面取得了较大进展。zimmer公司研发的多孔钽骨科植入材料在临床上的成功应用,使网状玻璃态多孔碳支架成为医疗领域广泛应用的材料之一。a.czerwinski等人在网状玻璃态多孔碳表面电沉积pb和pbo2用作铅酸电池的正负极板栅集流体。czerwinski等人用镀铂的网状玻璃态多孔碳电极对酸性溶液中co2的吸附进行研究。t.schoetz等人利用导电聚合物的独特特性,以网状玻璃态多孔碳为衬底,制备导电聚合物的纳米/微孔薄膜作为储能材料,提高了电极容量。国内对网状玻璃态多孔碳的研究主要停留在简单形状的制备和应用阶段。公开号为cn1907914a的中国专利公开了以三维网状石墨泡沫或网状玻璃碳制作医用多孔钽。尉晓蔚等人将自制的网状玻璃碳与犬骨髓基质干细胞进行培养,研究显示多孔玻璃碳支架在体外能促进骨髓基质干细胞的黏附与增殖,在体内具有良好的骨诱导特性。
4.相比国外研究,国内制备的网状玻璃态多孔碳材料存在强度低,易掉渣,加工难度大,尤其是在异形件制备上存在很大难度,限制了该材料在复杂形状环境要求下的应用。
技术实现要素:
5.本发明所要解决的技术问题在于针对上述现有技术的不足,提供一种网状玻璃态多孔碳薄壁异形件的制备方法。该方法采用前驱体聚氨酯海绵填充加工结合固化件埋粉烧结工艺,改善了坯料的可加工性,保证了形成玻璃态碳过程中固化件的体积收缩均匀,提高了产物薄壁异形件的尺寸精度,从而实现了高尺寸精度网状玻璃态多孔碳薄壁异形件的顺利成型,解决了网状玻璃态多孔碳薄壁异形件难以制备的问题。
6.为解决上述技术问题,本发明采用的技术方案为:一种网状玻璃态多孔碳薄壁异形件的制备方法,其特征在于,该方法包括以下步骤:
7.步骤一、将前驱体聚氨酯海绵放置于容器中,然后在前驱体聚氨酯海绵上部铺放聚乙烯蜡粉并转移至真空干燥箱中,进行真空加热保温,降至室温卸真空后取出,得到坯料;
8.步骤二、将步骤一中得到的坯料进行机械加工;
9.步骤三、将步骤二中经机械加工后的坯料浸入密闭的混合溶液中进行加热保温,并重复多次后取出,得到除蜡坯件;
10.步骤四、将步骤三中得到的除蜡坯件反复清洗,然后烘干;
11.步骤五、对步骤四中经烘干后的除蜡坯件进行浸渍挂浆,除去多余料浆后阴干,然后进行高温固化,得到固化件;
12.步骤六、将步骤五中得到的固化件埋没于石墨粉中进行高温碳化,得到网状玻璃态多孔碳薄壁异形件。
13.本发明采用聚氨酯海绵作为前驱体,在其上部铺放聚乙烯蜡粉后进行真空加热保温,通过加热保温使得聚乙烯蜡粉熔化并在重力作用下渗入前驱体聚氨酯海绵的孔隙中,结合真空条件有效去除了孔隙中的空气,提高了聚乙烯蜡粉的填充效率,得到坯料,经机械加工获得聚氨酯海绵薄壁异形件,由于聚乙烯蜡粉的填充大大提高了前驱体聚氨酯海绵的强度,改善了坯料的可加工性,进而保证了坯料经机械加工后得到的聚氨酯海绵薄壁异形件的尺寸精度;将机械加工后的坯料进行加热保温以充分去除孔隙中的聚乙烯蜡粉,经反复清洗和烘干后进行浸渍挂浆并进行阴干和高温固化,通过浸渍挂浆向经烘干后的除蜡坯件中引入树脂碳化物,有利于提高网状玻璃态多孔碳薄壁异形件中的碳含量;经阴干后除去浆料中的溶剂,再经高温固化使得树脂碳化物发生化学变化并逐渐硬化成型,提高产物薄壁异形件的强度,得到固化件;将固化件埋没于石墨粉中进行高温碳化,使得固化件中的树脂碳化物和前驱体聚氨酯海绵在高温碳化过程中发生小分子脱离、大分子链热解断裂及脱水转化成玻璃态碳,形成网状玻璃态多孔碳结构,而利用固态的碳材料石墨粉填埋,对埋没于石墨粉中的固化件形成空间约束,保证高温碳化过程中固化件的体积收缩均匀,避免了产物薄壁异形件的变形,保证了网状玻璃态多孔碳薄壁异形件的顺利成型,并提高了产物薄壁异形件的尺寸精度。
14.上述的一种网状玻璃态多孔碳薄壁异形件的制备方法,其特征在于,步骤一中所述聚乙烯蜡粉的分子量为1500。聚合物的熔点随分子量的减小而降低,优选选用低分子量的聚乙烯蜡粉填充,有利于降低后续加热保温去除聚乙烯蜡粉时的加热温度,改善去除效果。
15.上述的一种网状玻璃态多孔碳薄壁异形件的制备方法,其特征在于,步骤一中所述真空加热保温的真空度不超过100pa,温度为90℃~110℃,保温时间为1h~2h。该优选的真空加热保温的工艺参数保证了聚乙烯蜡粉的充分熔化并填充到聚氨酯海绵的孔隙中,同时不影响聚氨酯海绵的性能。
16.上述的一种网状玻璃态多孔碳薄壁异形件的制备方法,其特征在于,步骤二中所述坯料的机械加工过程中预留10%~20%的加工余量以弥补后续烧结引起的尺寸收缩。采用该预留加工余量的措施有利于消除工艺对产物的不良影响误差,保证异形件的顺利成型,提高了产物薄壁异形件的尺寸精度。
17.上述的一种网状玻璃态多孔碳薄壁异形件的制备方法,其特征在于,步骤三中所述混合溶液由二甲苯与正庚烷按照1:4~1:8的质量比组成;所述加热保温采用的设备为带有回流冷凝装置的玻璃瓶。该优选的混合溶液组成有利于充分溶解聚乙烯蜡,提高了聚乙烯蜡的去除效果;同时,由于二甲苯与正庚烷均为易挥发且有毒性的化学试剂,采用带有回流冷凝装置的玻璃瓶作为加热保温的设备,使得混合溶液受热挥发后进入回流冷凝装置中遇冷液化,回流到混合溶液中,既防止有毒气体挥发危及健康,又保证混合溶液的成分处于动态平衡状态,即加热保温的过程伴随冷凝回流过程。
18.上述的一种网状玻璃态多孔碳薄壁异形件的制备方法,其特征在于,步骤三中所述加热保温的温度为90℃~110℃,时间为30min~60min,重复的次数为3~5次。低分子量如分子量1500的聚乙烯蜡粉是非极性晶态高聚物,在上述优选的加热保温条件下充分溶解在混合溶液中,保证了聚乙烯蜡粉完全被去除。
19.上述的一种网状玻璃态多孔碳薄壁异形件的制备方法,其特征在于,步骤四中所述反复清洗采用的试剂为乙醇、乙醚或氯仿,反复清洗的次数为2~4次;所述烘干的温度为60℃,时间为1h。该优选的试剂均能有效去除除蜡坯件内残留的二甲苯和正庚烷,优选采用更安全的乙醇;该优选的烘干温度有利于试剂尤其是乙醇的充分挥发,从而得到无任何杂质污染的除蜡坯件。
20.上述的一种网状玻璃态多孔碳薄壁异形件的制备方法,其特征在于,步骤五中所述浸渍挂浆采用的浆料为氨酚醛树脂/糠醇树脂的醇溶液,或者氨酚醛树脂/糠醇树脂的醇溶液与沥青粉的混合物。该优选的浆料中均含有热固性树脂,经后续阴干和高温固化工艺,保证了固化件具有一定的硬度,不会轻易变形,且提高了产物含碳量,进而提高了产物的强度,避免了因强度低导致坍塌,从而保证了网状玻璃态多孔碳薄壁异形件的成型。
21.上述的一种网状玻璃态多孔碳薄壁异形件的制备方法,其特征在于,步骤六中所述高温碳化的温度为800℃~1000℃,升温速率为1℃/min。
22.另外,本发明还提供了一种上述的方法制备的网状玻璃态多孔碳薄壁异形件。
23.本发明与现有技术相比具有以下优点:
24.1、本发明将前驱体聚氨酯海绵填充聚乙烯蜡粉制成坯料后进行机械加工,通过提高前驱体聚氨酯海绵的强度改善了坯料的可加工性,提高了产物薄壁异形件的尺寸精度,结合固化件埋粉烧结工艺,保证了形成玻璃态碳过程中固化件的体积收缩均匀,避免了产物薄壁异形件的变形,从而实现了高尺寸精度网状玻璃态多孔碳薄壁异形件的顺利成型,解决了网状玻璃态多孔碳薄壁异形件难以制备的问题。
25.2、本发明采用低分子量的聚乙烯蜡粉填充聚氨酯海绵前驱体,既有利于在较低温度下进行充分填充以提高前驱体聚氨酯海绵的强度,又降低了后续除蜡时的加热温度,减少了在产物薄壁异形件中的不良残留。
26.3、本发明通过浸渍挂浆向经烘干后的除蜡坯件中引入树脂碳化物,有利于提高产物网状玻璃态多孔碳薄壁异形件中的碳含量,进而提高产物薄壁异形件的强度,避免其形状坍塌。
27.4、本发明有成本低、可操作性强、工艺稳定性较好等优点,可广泛应用于多孔碳材料薄壁异形件的制备技术中。
28.下面通过附图和实施例对本发明的技术方案作进一步的详细描述。
附图说明
29.图1为本发明实施例3制备的网状玻璃态多孔碳薄壁异形件的图片。
具体实施方式
30.实施例1
31.本实施例包括以下步骤:
32.步骤一、将前驱体聚氨酯海绵放置于容器中,然后在前驱体聚氨酯海绵上部铺放聚乙烯蜡粉并转移至真空干燥箱中,抽真空至真空度不超过100pa后升温至90℃保温1h进行真空加热保温,降至室温卸真空后取出,得到坯料;所述前驱体聚氨酯海绵为具有三维网状开孔结构的块体,且前驱体聚氨酯海绵的孔隙率不小于98%;所述聚乙烯蜡粉的分子量为1500;
33.步骤二、将步骤一中得到的坯料进行机械加工,并预留10%的加工余量以弥补后续烧结引起的尺寸收缩;
34.步骤三、将步骤二中经机械加工后的坯料浸入密闭的混合溶液中进行加热至90℃保温40min,并重复3次后取出,得到除蜡坯件;所述混合溶液由二甲苯与正庚烷按照1:8的质量比组成,加热保温采用的设备为带有回流冷凝装置的玻璃瓶;
35.步骤四、采用乙醇将步骤三中得到的除蜡坯件反复清洗2次,然后在60℃烘干1h;
36.步骤五、对步骤四中经烘干后的除蜡坯件进行浸渍挂浆,除去多余料浆后阴干,然后在150℃下进行高温固化,得到固化件;所述浸渍挂浆采用的浆料为糠醇树脂的醇溶液,浆料中糠醛树脂与乙醇的质量比为1:1,且浆料中含有5wt%的1mol/l磷酸溶液固化剂;
37.步骤六、将步骤五中得到的固化件埋没于石墨粉中进行高温碳化,采用1℃/min的升温速率加热至800℃进行高温碳化,得到网状玻璃态多孔碳薄壁异形件。
38.本实施例步骤四中反复清洗采用的溶剂还可为乙醚或氯仿。
39.实施例2
40.本实施例包括以下步骤:
41.步骤一、将前驱体聚氨酯海绵放置于容器中,然后在前驱体聚氨酯海绵上部铺放聚乙烯蜡粉并转移至真空干燥箱中,抽真空至真空度不超过100pa后升温至100℃保温1.5h进行真空加热保温,降至室温卸真空后取出,得到坯料;所述前驱体聚氨酯海绵为具有三维网状开孔结构的块体,且前驱体聚氨酯海绵的孔隙率不小于98%;所述聚乙烯蜡粉的分子量为1500;
42.步骤二、将步骤一中得到的坯料进行机械加工,并预留15%的加工余量以弥补后续烧结引起的尺寸收缩;
43.步骤三、将步骤二中经机械加工后的坯料浸入密闭的混合溶液中进行加热至110℃保温60min,并重复4次后取出,得到除蜡坯件;所述混合溶液由二甲苯与正庚烷按照1:6的质量比组成,加热保温采用的设备为带有回流冷凝装置的玻璃瓶;
44.步骤四、采用乙醇将步骤三中得到的除蜡坯件反复清洗3次,然后在60℃烘干1h;
45.步骤五、对步骤四中经烘干后的除蜡坯件进行浸渍挂浆,除去多余料浆后阴干,然后在170℃下进行高温固化,得到固化件;所述浸渍挂浆采用的浆料为氨酚醛树脂的醇溶液,浆料中氨酚醛树脂与乙醇的质量比为1:1;
46.步骤六、将步骤五中得到的固化件埋没于石墨粉中进行高温碳化,采用1℃/min的升温速率加热至900℃进行高温碳化,得到网状玻璃态多孔碳薄壁异形件。
47.本实施例步骤四中反复清洗采用的溶剂还可为乙醚或氯仿。
48.实施例3
49.本实施例包括以下步骤:
50.步骤一、将前驱体聚氨酯海绵放置于容器中,然后在前驱体聚氨酯海绵上部铺放
聚乙烯蜡粉并转移至真空干燥箱中,抽真空至真空度不超过100pa后升温至90℃保温2h进行真空加热保温,降至室温卸真空后取出,得到坯料;所述前驱体聚氨酯海绵为具有三维网状开孔结构的块体,且前驱体聚氨酯海绵的孔隙率不小于98%;所述聚乙烯蜡粉的分子量为1500;
51.步骤二、将步骤一中得到的坯料进行机械加工,并预留20%的加工余量以弥补后续烧结引起的尺寸收缩;
52.步骤三、将步骤二中经机械加工后的坯料浸入密闭的混合溶液中进行加热至90℃保温30min,并重复5次后取出,得到除蜡坯件;所述混合溶液由二甲苯与正庚烷按照1:4的质量比组成,加热保温采用的设备为带有回流冷凝装置的玻璃瓶;
53.步骤四、采用乙醇将步骤三中得到的除蜡坯件反复清洗4次,然后在60℃烘干1h;
54.步骤五、对步骤四中经烘干后的除蜡坯件进行浸渍挂浆,除去多余料浆后阴干,然后在150℃下进行高温固化,得到固化件;所述浸渍挂浆采用的浆料为氨酚醛树脂的醇溶液,浆料中氨酚醛树脂与乙醇的质量比为1:1,且浆料中含有10wt%的沥青粉;
55.步骤六、将步骤五中得到的固化件埋没于石墨粉中进行高温碳化,采用1℃/min的升温速率加热至900℃进行高温碳化,得到网状玻璃态多孔碳薄壁异形件。
56.图1为本实施例制备的网状玻璃态多孔碳薄壁异形件的图片,从图1可以看出,该多孔碳薄壁异形件为空腔半球体形状的多孔碳髋臼支架,壁厚为3mm,直径为50mm,开孔率不小于96%。
57.本实施例步骤四中反复清洗采用的溶剂还可为乙醚或氯仿。
58.实施例4
59.本实施例包括以下步骤:
60.步骤一、将前驱体聚氨酯海绵放置于容器中,然后在前驱体聚氨酯海绵上部铺放聚乙烯蜡粉并转移至真空干燥箱中,抽真空至真空度不超过100pa后升温至110℃保温1h进行真空加热保温,降至室温卸真空后取出,得到坯料;所述前驱体聚氨酯海绵为具有三维网状开孔结构的块体,且前驱体聚氨酯海绵的孔隙率不小于98%;所述聚乙烯蜡粉的分子量为1500;
61.步骤二、将步骤一中得到的坯料进行机械加工,并预留15%的加工余量以弥补后续烧结引起的尺寸收缩;
62.步骤三、将步骤二中经机械加工后的坯料浸入密闭的混合溶液中进行加热至100℃保温50min,并重复4次后取出,得到除蜡坯件;所述混合溶液由二甲苯与正庚烷按照1:6的质量比组成,加热保温采用的设备为带有回流冷凝装置的玻璃瓶;
63.步骤四、采用乙醇将步骤三中得到的除蜡坯件反复清洗3次,然后在60℃烘干1h;
64.步骤五、对步骤四中经烘干后的除蜡坯件进行浸渍挂浆,除去多余料浆后阴干,然后在150℃下进行高温固化,得到固化件;所述浸渍挂浆采用的浆料为糠醇树脂的醇溶液,浆料中糠醛树脂与乙醇的质量比为1:1,且浆料中含有5wt%的1mol/l磷酸溶液和10wt%的沥青粉;
65.步骤六、将步骤五中得到的固化件埋没于石墨粉中进行高温碳化,采用1℃/min的升温速率加热至1000℃进行高温碳化,得到网状玻璃态多孔碳薄壁异形件。
66.本实施例步骤四中反复清洗采用的溶剂还可为乙醚或氯仿。
67.以上所述,仅是本发明的较佳实施例,并非对本发明作任何限制。凡是根据发明技术实质对以上实施例所作的任何简单修改、变更以及等效变化,均仍属于本发明技术方案的保护范围内。
再多了解一些
本文用于企业家、创业者技术爱好者查询,结果仅供参考。