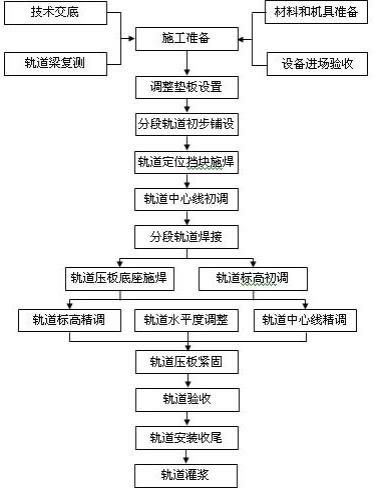
1.本发明涉及冶金设备施工技术领域,具体是一种门型、半门型中间包车轨道的测量安装方法。
背景技术:
2.连铸机主要由浇铸系统、铸流系统构成,中间包车是用于支撑、运输、更换中间包的承载装置。中间包车轨道安装的好坏,直接影响中间包车能否顺利运行。门型中间包车的轨道在结晶器的内外弧两侧,车跨在结晶器的上方,水口位于车的主梁内,由于中间包的重心位于两条轨道之间,车身受力合理、平稳;但操作人员在观察结晶器液面和加保护渣时不太方便。半门型中间包车位于结晶器的外弧侧,其内弧侧轨道在高架梁上,外弧侧轨道铺设在浇铸平台上。中间包车运行迅速,结晶器上方供操作的空间大,便于观察结晶器液面,操作方便。但结构中心偏移,车子不稳,需在车身的另一端加配重或反倾力矩结构,同时对轨道安装精度要求更高。常规门型、半门型中间包车轨道测量安装方法 ,调整精度低,后期生产过程中轨道受力后,变形量大,影响中间包车正常运行和生产。
技术实现要素:
3.本发明的目的在于克服上述缺陷,提出一种安全可靠、施工方便、成本较低的门型、半门型中间包车轨道的测量安装方法。
4.为了达到上述目的,本发明是这样实现的:一种门型、半门型中间包车轨道的测量安装方法,包括步骤1、施工准备;步骤1.1、轨道安装施工准备包括技术交底、轨道梁复测、材料和机具准备、设备进场验收;步骤1.2、技术交底:提前编制分项技术交底卡,专业技术员对所有参与的施工人员,包括驾驶行车的司机进行书面的技术交底;步骤1.3、轨道梁复测:根据上道工序工艺钢结构平台轨道梁安装结果的有关数据,使用设备安装埋设的基准点即钢包回转台混凝土上的永久性基准点,连铸机浇铸正切线(即浇铸弧线的中心标板,对轨道梁上表面中心位置的标高、中心线进行测量,计算得到数据,进行数据比对,轨道梁满足中间包车轨道施工要求,方可进行工序交接;步骤1.4、材料和机具准备中主要包括:1)、调整垫板,垫板为不锈钢材质,耐腐蚀,规格200
×
150
×
0.3、200
×
150
×
0.5、200
×
150
×
1、200
×
150
×
2、200
×
150
×
5,单位:mm;数量:根据轨道梁复测数据,结合轨道压板组数预定加工;2)、两套辅助中心线钢丝及配件,包括设备调整专用线坠、拉紧器、线轮、钢结构支架;要求钢线ф0.5mm;3)、轨道定位挡块150
×
25
×
25;斜锲150
×
25
×
20
×
10,数量:分段运至现场中间
包车轨道数量的4倍,单位:mm;4)、精密水准仪、经纬仪、电弧焊设备两套、氧气、乙炔气割工具两套;5)、半门型中间包车内弧侧轨道梁上要挂设ф8mm钢线安全绳,门型、半门型中间包车工艺平台结晶器振动框架洞口处要有安全防护措施;步骤1.5、设备进场验收:中间包车轨道一般采用qu100型号的重型钢轨,通常每根长度12m,由于中间包车轨道整体超长,根据车辆运输长度能力,制作厂宜分段将轨道运至安装现场,每段连接处制作加工焊接坡口,每段接口处宜做好标志编号,测量每段轨道平直无扭曲变形,目测表面无锈蚀,轨道压板宜采用cgwk型号,供货数量应比设计数量余出5%;步骤2、调整垫板设置:依据轨道梁复测数据,在中间包车轨道敷设区域,每间隔2m,布置一组调整垫板,垫板组合不应超过5片,且薄垫板夹在厚垫片中间使用;调整垫板标高=设计轨顶标高
‑ꢀ
qu100钢轨,调整垫板敷设时,测量标高宜高出设计标高0.3
‑
0.5mm;使用记号笔画出垫板放置位置,防止轨道敷设时有窜动;观测基准点使用钢包回转台混凝土基础上的永久性基准点,进行标高计算;其中,半门型中间包车轨道内弧侧轨道与外弧侧轨道存在悬殊的高低差,应在内弧侧轨道梁上设置一个辅助基准点,标高观测时精密水准仪架设在钢包回转体上;步骤3、分段轨道初步铺设:使用本跨行车吊装就位中间包车轨道,分别按标志编号敷设外弧侧中间包车轨道和内弧侧中间包车轨道;步骤4、轨道定位挡块施焊:轨道定位挡块安放位置延轨道运行方向,距离轨道中心线两侧各86~88mm范围内,铸流方向定位挡块位置布置在中间包车轨道分段接口,距离各接口200mm范围处;轨道定位挡块两端施焊,长度方向外侧段焊;步骤5、轨道中心线初调:步骤5.1、从正切线或浇铸弧线引出两条辅助线,辅助线标板位置设置在中间包车轨道梁长度方向两端,作为临时中心线辅助观测点,辅助观测点设置位置便于调整轨道中心线;步骤5.2、中心线调整:在两根轨道梁上分别挂设辅助中心线钢线,配合设备调整中心线专用线坠,使用钢板尺测量轨面侧面最宽点至线坠鱼线的最小距离,通过计算得到理论值,用理论值与实际值比较,得到需要调整的数据; 步骤5.3、通过测量得到数据后,使用轨道定位挡块配合斜锲,用八磅手锤击打斜锲,轨道两侧配合调整,边调整边测量,最终使中间包车轨道移动到正确位置,纵向中心线安装规范要求允许误差2.0mm,轨距0~ 2.0mm,完成轨道中心线初调;注意斜锲插入方向,始终无斜度侧靠近轨道定位挡块;步骤6、分段轨道焊接:步骤6.1、焊接准备:轨道接头焊接前,应仔细清理坡口及附近的油、锈、污物,直到露出金属光泽,焊材依据等强原则,匹配碱性焊条;步骤6.2焊接:焊接轨道接头的顺序是由下而上,先轨底后轨腰、轨头,逐层逐道进行堆焊,最后修补周围,根据轨道端头的范围各为40mm,同时进行预热,预热及层间温度控制在300℃~350℃;在全部施焊过程中,须随时用直钢板尺检查钢轨接头的变形情况;随时
调整接头的高度位置控制钢轨接头的变形;步骤6.3、在施焊每层焊波时,尤其在施焊轨底的每层焊波时,应使用一根焊条焊完,中间避免接用焊条而断弧,前后两层焊波的施焊方向应相反,每个轨道接头的焊接工作应连续进行,以使轨端头保持在较高温度下焊接,温度范围300℃~350℃;步骤6.4、在焊接后,应当消除应力热处理,消除应力热处理温度为620℃~650℃,从焊缝中心算起两侧各为40mm作为消除应力热处理的范围;消除应力热处理的温度达到后,恒温加热必须保证在20~30min以上,用电焊防火毯保温棉包好,保温缓冷,直到常温;步骤6.5、钢轨焊接接头已消除应力热处理并冷却到大气温度以后,对轨道顶面和两侧面的焊缝进行磨平处理;当焊接凸起过大时,用砂轮磨光机进行打磨处理,直到与轨面齐平,最后将表面磨光;步骤7、轨道压板底座施焊:布置轨道压板底座前,轨道压板底座与配件t型螺栓先组装在一起,安装距离图纸无要求时,应按照规范每组间隔距离为500mm,轨道压板底座与轨道底面之间应有1
‑
2mm间隙,用于轨道中心线精调,轨道压板底座材质一般为q345,应采用e5015型焊条,三边6mm角焊缝,施工时,应考虑焊接轨道压板底座时对轨道梁扰度变化的影响;步骤8、轨道标高初调,步骤8.1、在轨道上表面每隔2m标记一个观测点,观测点轨道下方应有调整垫板,测量得到数据,数据满足安装要求时,观测点处的轨道压板紧固;其中,放入楔形调整板,并使有刻槽的面朝上;依次安装钢轨压板、垫圈、弹簧垫圈及螺母;打动楔形调整板,调整压轨器在垂直于钢轨方向的位置,当钢轨压板与钢轨下翼缘紧密压紧后,再拧紧螺母,t型螺栓为8.8级,拧紧力矩为终拧力矩220n.m的50%;步骤8.2、测量得到数据,数据不满足安装要求时:1)打击松开步骤5中定位斜锲,使轨道处在自由状态,使用起道机缓慢提升轨道,提升高度满足增减调整垫片的空间,垫板调整后缓慢降落轨道;2)重复步骤5,再重复9.1,返复调整测量,直到数据满足安装要求,轨道压板紧固;步骤9、轨道标高精调;在每组轨道压板处的轨道底板下方,塞紧一组调整垫板,轨道压板紧固,拧紧力矩为初拧力矩110n.m;每1m标记一个观测点,轨道标高宜为正标高,相邻观测点的标高差不应大于0.5mm,同时保证两轨道高低差控制在1.0mm;步骤10、轨道水平度调整;规范要求轨道水平度1mm/m,使用铁水平,精度0.5mm/m,每1m标记一个观测点,数据不满足安装要求时,重复9.2的施工方法,纵向水平度应综合考虑相邻两组垫板的调整量,横向规范无要求,但是也应检查轨道是否倾斜,严重倾斜时,会造成车轮与轨道线接触,发生啃轨现象,影响中间包车正常运行;建议使用铁水平观测,不满足水平度1mm/m时,调整垫板中的薄垫板应切半使用,用来调整倾斜;步骤11、轨道中心线精调;测量和调整方法按照步骤5进行,精调中心线时,同时要兼顾轨道标高和水平度的变化;步骤12、轨道压板紧固;
轨道压板终拧紧固实在步骤9、10、11完成后进行,紧固时轨道两侧成组同时紧固,拧紧力矩为终拧力矩220n.m;步骤13、轨道验收;步骤14、轨道安装收尾;拆除安装辅助线及支架;拆除影响其他工序的安全防护措施;半门型中间包车内弧侧轨道轨压板器锁紧螺栓防锈处理;步骤15、轨道灌浆;半门型中间包车外弧侧轨道灌浆;门型中间包车两条轨道都要灌浆;按照图纸要求轨道周围使用钢板进行围挡,钢板段焊在工艺平台上,钢板高度与后期工序工艺平台浇铸混凝土的表面等高;灌浆高度不超过轨道高度的一半,采用c40高强无收缩灌浆料;灌浆料配比和施工方法应按照灌浆料使用说明书进行。
5.所述的门型、半门型中间包车轨道的测量安装方法,步骤5.2中心线的调整:在辅助中心线观测点的延伸线上架设经纬仪,使用经纬仪观测钢板尺测量轨面侧面最宽点到经纬仪镜头内影像夹角之间的距离数据,用理论值与实际值比较。特点提高工作效率。
6.所述的门型、半门型中间包车轨道的测量安装方法,步骤7与步骤8并行施工。
7.所述的门型、半门型中间包车轨道的测量安装方法,步骤12、轨道压板紧固,与步骤10、步骤11配合施工。
8.本安装方法与传统中间包车轨道安装调整对比,保证了门型、半门型中间包车轨道安装的精准性,降低了安装带来的安全风险,减少了施工难度,有效缩短了施工工期。
附图说明
9.图1为本发明所提呕出的门型、半门型中间包车轨道测量安装工艺流程图。
10.图2为本发明中半门型中间包车在工艺平台上的位置示意图。
11.图3为本发明种半门型中间包车轨道标高测量示意图。
12.图4为本发明中门型中间包车轨道纵向中心线测量示意图。
具体实施方式
13.以下通过具体实施例进一步说明本发明。
14.如图1~图4所示,门型、半门型中间包车轨道测量安装方法,包括下述步骤:步骤1、施工准备;1.1轨道安装施工准备包括技术交底、轨道梁复测、材料和机具准备、设备进场验收。
15.1.2技术交底:提前编制分项技术交底卡,专业技术员对所有参与的施工人员,包括驾驶行车的司机进行书面的技术交底。
16.1.3轨道梁复测:根据上道工序工艺钢结构平台轨道梁安装结果的有关数据,使用设备安装埋设的基准点(钢包回转台4混凝土上的永久性基准点),连铸机浇铸正切线6(浇铸弧线)的中心标板,对轨道梁上表面中心位置的标高、中心线进行测量,计算得到数据,进行数据比对,轨道梁满足中间包车轨道施工要求,方可进行工序交接。
17.1.4材料和机具准备中主要包括:
1)调整垫板,垫板为不锈钢材质,耐腐蚀,规格200
×
150
×
0.3、200
×
150
×
0.5、200
×
150
×
1、200
×
150
×
2、200
×
150
×
5,单位:mm;数量:根据轨道梁复测数据,结合轨道压板组数预定加工。
18.2)两套辅助中心线钢丝及配件(设备调整专用线坠、拉紧器、线轮、钢结构支架);要求钢线ф0.5mm。
19.3)轨道定位挡块150
×
25
×
25;斜锲150
×
25
×
20
×
10,数量:分段运至现场中间包车轨道数量的4倍,单位:mm。
20.4)精密水准仪3、经纬仪、电弧焊设备两套、氧气、乙炔气割工具两套,钳工常用机具。
21.5)半门型中间包车内弧侧轨道梁上要挂设ф8mm钢线安全绳,门型、半门型中间包车工艺平台结晶器振动框架洞口处要有安全防护措施。
22.1.5设备进场验收:中间包车轨道一般采用qu100型号的重型钢轨,通常每根长度12m,由于中间包车轨道1、2整体超长,根据车辆运输长度能力,制作厂宜分段将轨道运至安装现场,每段连接处制作加工焊接坡口,每段接口处应做好标志编号。测量每段轨道平直无扭曲变形,目测表面无锈蚀。轨道压板宜采用cgwk型号,供货数量宜比设计数量余出5%。
23.步骤2、轨道垫板设置;依据轨道梁复测数据,在中间包车轨道1、2敷设区域,每间隔2m,布置一组调整垫板,垫板组合不应超过5片,且薄垫板夹在厚垫片中间使用。调整垫板标高=设计轨顶标高
‑ꢀ
qu100钢轨(高度150mm),调整垫板敷设时,测量标高宜高出设计标高0.3
‑
0.5mm。使用记号笔画出垫板放置位置,防止轨道1、2敷设时有窜动。观测基准点使用钢包回转台4混凝土基础上的永久性基准点,进行标高计算。需要特别说明的是半门型中间包车轨道内弧侧轨道2与外弧侧轨道1存在悬殊的高低差,需要在内弧侧轨道梁上设置一个辅助基准点,标高观测时精密水准仪3架设在钢包回转体4上。
24.步骤3、分段轨道初步铺设;使用本跨行车吊装就位中间包车轨道1、2,分别按标志编号敷设外弧侧中间包车轨道1和内弧侧中间包车轨道2。
25.步骤4、轨道定位挡块施焊;轨道定位挡块安放位置延轨道运行方向,距离轨道中心线两侧各86~88mm (qu100底面宽150mm,定位挡块与轨道底面边距预留11
‑
13mm的间隙)范围内,铸流方向定位挡块位置布置在中间包车轨道分段接口,距离各接口200mm范围处。轨道定位挡块两端施焊,长度方向外侧段焊。
26.步骤5、轨道中心线初调;5.1从正切线(浇铸弧线)引出2条辅助线7、8,辅助线标板位置设置在中间包车轨道梁长度方向两端,作为临时中心线辅助观测点,辅助观测点设置位置便于调整轨道中心线。
27.5.2中心线调整可采用2种方法,第一种:在2根轨道梁上分别挂设辅助中心线钢线7、8,配合设备调整中心线专用线坠,使用钢板尺测量轨面侧面最宽点至线坠鱼线的最小距离(轨面最宽尺寸108mm),通过计算得到理论值。用理论与与实际值比较,得到需要调整的数据。特点节省人工。
28.5.3第二种:在辅助中心线7、8观测点的延伸线上架设经纬仪,使用经纬仪观测钢板尺测量轨面侧面最宽点到经纬仪镜头内影像夹角之间的距离数据,用理论值与实际值比较。特点提高工作效率。
29.5.4通过测量得到数据后,使用轨道定位挡块配合斜锲,用八磅手锤击打斜锲,轨道两侧配合调整,边调整边测量,最终使中间包车轨道移动到正确位置,纵向中心线安装规范要求允许误差2.0mm,轨距0~ 2.0mm,完成轨道中心线初调。注意斜锲插入方向,始终无斜度侧靠近轨道定位挡块。
30.步骤6、分段轨道焊接;6.1焊接准备:轨道接头焊接前,应仔细清理坡口及附近的油、锈等污物,直到露出金属光泽,焊材依据等强原则,匹配碱性焊条;6.2焊接:焊接轨道接头的顺序是由下而上,先轨底后轨腰、轨头,逐层逐道进行堆焊,最后修补周围,根据轨道端头的范围各为40mm,同时进行预热,预热及层间温度控制在300℃~350℃。在全部施焊过程中,必须随时用直钢板尺检查钢轨接头的变形情况。随时调整接头的高度位置控制钢轨接头的变形。
31.6.3在施焊每层焊波时,尤其在施焊轨底的每层焊波时,应使用l根焊条焊完,中间避免接用焊条而断弧,前后2层焊波的施焊方向应相反;每个轨道接头的焊接工作应连续进行,以使轨端头保持在较高温度下焊接(300℃~350℃)。
32.6.4在焊接后,应当消除应力热处理,消除应力热处理温度为620℃~650℃,从焊缝中心算起两侧各为40mm作为消除应力热处理的范围;消除应力热处理的温度达到后,恒温加热必须保证在20~30min以上,用电焊防火毯保温棉包好,保温缓冷,直到常温。
33.6.5钢轨焊接接头已消除应力热处理并冷却到大气温度以后,对轨道顶面和两侧面的焊缝进行磨平处理。当焊接凸起过大时,用砂轮磨光机进行打磨处理,直到与轨面齐平,最后将表面磨光。
34.步骤7、轨道压板底座施焊;布置轨道压板底座前,轨道压板底座与配件t型螺栓先组装在一起,安装距离图纸无要求时,应按照规范每组间隔距离为500mm,轨道压板底座与轨道底面之间应有1
‑
2mm间隙,用于轨道中心线精调,轨道压板底座材质一般为q345,应采用e5015型焊条,三边6mm角焊缝,施工时,应考虑焊接轨道压板底座时对轨道梁扰度变化的影响。
35.步骤8、轨道标高初调;8.1在轨道1、2每隔2m标记一个观测点下应有调整垫板,测量铟钢尺5得到数据,数据满足安装要求时,观测点处的轨道压板紧固。
36.注意:放入楔形调整板,并使有刻槽的面朝上;依次安装钢轨压板、垫圈、弹簧垫圈及螺母;打动楔形调整板,调整压轨器在垂直于钢轨方向的位置,当钢轨压板与钢轨下翼缘紧密压紧后,再拧紧螺母,t型螺栓为8.8级,拧紧力矩为终拧力矩220n.m的50%。
37.8.2测量得到数据,数据不满足安装要求时:1)打击松开步骤5中定位斜锲,使轨道处在自由状态,使用起道机缓慢提升轨道,提升高度可以增减调整垫片即可。垫板调整后缓慢降落轨道。
38.2)重复步骤5,再重复9.1,返复调整测量,直到数据满足安装要求,轨道压板紧固。
39.步骤9、轨道标高精调;
在每组轨道压板处的轨道底板下方,塞紧一组调整垫板,轨道压板紧固,拧紧力矩为初拧力矩110n.m。每1m标记一个观测点,铟钢尺5垂直立在观测点上,轨道标高宜为正标高,相邻观测点的标高差不应大于0.5mm,同时保证两轨道高低差控制在1.0mm。
40.步骤10、轨道水平度调整;规范要求轨道1、2水平度1mm/m,使用铁水平,精度0.5mm/m,每1m标记一个观测点,数据不满足安装要求时,要重复9.2的施工方法,纵向水平度应综合考虑相邻两组垫板的调整量,横向规范无要求,但是也应检查轨道1、2是否倾斜,严重倾斜时,会造成车轮与轨道1、2线接触,发生啃轨现象,影响中间包车正常运行。建议使用铁水平观测,不满足水平度1mm/m时,调整垫板中的薄垫板应切半使用,用来调整倾斜。
41.步骤11、轨道中心线精调;测量和调整方法按照步骤5进行,需要注意的是,精调中心线时,同时要兼顾轨道1、2标高和水平度的变化。
42.步骤12、轨道压板紧固;轨道压板终拧紧固实在步骤9、10、11完成后进行,紧固时注意轨道两侧,成组同时紧固,拧紧力矩为终拧力矩220n.m。
43.步骤13、轨道验收;轨道1、2验收前,应首先进行自检,自检合格后,通知监理单位和相关方,并应提交自检报告,现场验收包括中心线、标高、水平度数据核查,接口焊接质量检查,轨道压板器底板焊接、锁紧螺栓紧固情况检查。
44.步骤14、轨道安装收尾;拆除安装辅助线及支架;拆除影响其他工序的安全防护措施;半门型中间包车内弧侧轨道2轨道压板器锁紧螺栓防锈处理。
45.步骤15、轨道灌浆;半门型中间包车外弧侧轨道2灌浆。门型中间包车两条轨道1、2都要灌浆。按照图纸要求轨道周围使用钢板进行围挡,钢板段焊在工艺平台上,钢板高度与后期工序工艺平台浇铸混凝土的表面等高。灌浆高度不超过轨道高度的一半,采用c40高强无收缩灌浆料。灌浆料配比和施工方法应按照灌浆料使用说明书进行。
再多了解一些
本文用于企业家、创业者技术爱好者查询,结果仅供参考。