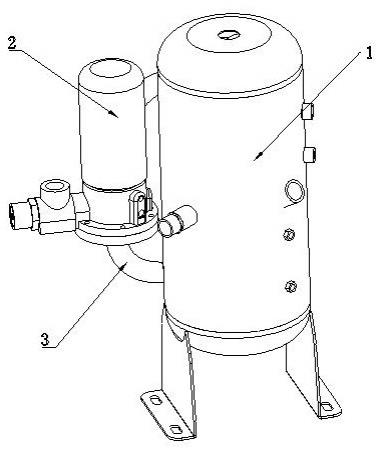
1.本实用新型属于空压机领域,具体涉及一种用于螺杆空压机的油气分离器。
背景技术:
2.螺杆空压机在压缩气体时,一些油同时被喷入螺杆机的齿间容积中,因而形成了油气混合物。为了确保压缩气体的质量,必须利用油气分离器来分离压缩空气中多余的油,同时将分离出来的润滑油循环利用。油气分离器作为喷油螺杆机的主要设备之一,其作用是将压缩空气中形成的油气混合物进行油和气的分离,既可降低压缩气体中的含油量,又可循环利用分离出来的润滑油。
3.其工作原理为:从空压机排出的空气夹带着大小不一的油滴,沿切线进入油气分离器,大油滴靠重力沿管壁下滑到分离器的底部,经排油管排出。同时,夹带悬浮状(小油滴)油状气体因密度小而上升,进入到带微米级玻纤滤的油气分离滤芯,油雾经过滤材的拦截,扩散和聚合后,小油滴很快聚合成大油滴,在气动的作用下通过滤层,沉降在滤芯底部。这些油通过滤芯底部的回油口进口,不断返回润滑系统,脱油后的气体投入外部使用。
4.目前市面上有两种模式的油气分离器,一种是内置油气分离滤芯总成(由油气分离滤芯及滤芯底座组成的滤芯总成设置在油气分离器本体内部),另外一种是顶置油气分离滤芯总成(由油气分离滤芯及滤芯底座5组成的滤芯总成设置在油气分离器本体顶部),如图1所示。内置油气分离滤芯总成,维修更换滤芯很麻烦,费用很高,费时费力;方形静音箱内的螺杆机6和电动机7是纵向直连,其宽度决定了整机的宽度,油气分离器高度比螺杆机和电动机高很多,其高度决定了整机的高度;顶置油气分离滤芯总成的高度为本体加上油气分离滤芯总成及滤芯底座5的高度,使油气分离器越来越高,增加了规则立方体外壳及包装箱的体积,不利于整机静音箱的设计,增加包装及运输成本。
技术实现要素:
5.本实用新型在于克服现有油气分离器不易维修、高度过高的缺陷,提出一种便于维修且整体高度较低的用于螺杆空压机的油气分离器。
6.一种用于螺杆空压机的油气分离器,包括本体和滤芯总成,其要点在于,所述滤芯总成设置在本体侧面,滤芯总成和本体之间采用空心管连接,所述空心管固定在本体内,且空心管一部分从本体穿出与滤芯总成连接。
7.本实用新型将滤芯总成外移到本体侧面,维修和更换滤芯总成时不用拆装本体,操作便捷;另一方面,滤芯总成和本体采用空心管连接,能够将滤芯总成和本体相对位置从竖直叠放状态改变为并列,从而降低滤芯总成的高度,减少油气分离器对整体高度的影响,有利于整机静音箱的设计;最后,通过一条管把滤芯总成从内部或顶部改成并列,充分利用了三维空间,并且也节省其它的管路,例如进油管、回油管等,各系统均有一定的间隔,由于滤芯总成宽度较小,将滤芯总成放置在合适的间隔处,无需增大静音箱及包装箱的宽度。
8.进一步地,所述滤芯总成的油气混合物入口低于本体的油气混合物出口,所述空
心管存在拐弯点。
9.将滤芯总成油气混合物入口设置得低于本体的油气混合物出口,油气混合物在通过拐弯点时撞击管壁,能够使油滴留在管道内,促进油气分离。
10.进一步地,所述空心管是s型硬管。通过焊接与本体和滤芯总成连接,工艺简单且防泄漏。
11.进一步地,所述空心管是z型硬管。
12.s型管、z型管均能将本体内的油气混合物输送到滤芯总成进行油气分离,同时能够将滤芯总成油气混合物入口设置得低于本体的油气混合物出口。多个拐弯点的管道,使油气混合物不断地改变运动方向,增加油气混合物的扰动度,有利于多个细小的油滴因碰撞而聚合成大体积的油滴,增加油滴的重量,尤其是管道中段使油气混合物从上而下运动,加剧油滴在重力的作用下留在管道的底部。
13.进一步地,所述本体内部设有倾斜的隔板,隔板固定在本体的上半部,隔板下表面固定有圆形隔筒,隔筒外壁与本体内壁及隔板形成油气通道,本体侧面设有与本体内壁相切的油气管道。
14.由于油气管道和本体内壁相切,油气混合物从油气管道进入本体后会在油气通道内旋转,倾斜隔板的存在使油气混合物在本体内壁更能形成涡流,能够增加油气混合物与本体内壁碰撞的机会,使油气分离更彻底。
15.进一步地,隔筒的中心轴与本体的中心轴平行但不重合,且隔筒的中心轴远离油气管道。
16.隔筒与本体的偏心设置使得油气通道的截面积有变化,随着油气混合物的旋转,油气通道的截面积逐渐减小,进一步增加油气混合物与油气通道壁的碰撞机会,使油气分离更彻底。
17.进一步地,所述空心管一端固定在油气通道上方,空心管管体纵向穿过隔筒内部,从本体下半部侧面的通孔穿出,与滤芯总成连接。
18.进一步地,所述空心管一半以上设置在本体内部。
19.空心管一端固定在油气通道上方,即本体上半部,穿过隔筒后从本体的下半部穿出,可见空心管大部分都在本体内,较少占用本体外部的空间,本体和滤芯总成之间更紧凑。
20.本实用新型利用s型或z型空心管将油气分离滤芯总成移到油气分离本体侧面,能够降低滤芯总成的高度使其位于油气分离器最高点下方,本实用新型的油气分离器克服了内置式的不易维修的缺点,同时也克服了顶置式高度过高的缺点。
附图说明
21.图1为现有带顶置油气分离滤芯总成的螺杆空压机
22.图2为本实用新型立体图1
23.图3为本实用新型立体图2
24.图4为使用的螺杆空压机结构示意图
25.图5为图4的俯视图(不含顶盖)
26.图6为本实用新型俯视图
27.图7为图6的a
‑
a剖视图
28.其中:1本体、11隔筒、12隔板、13油气通道、14油气入口、15集油槽、2滤芯总成、3空心管、4油气管道、5底座、6螺杆机、7电动机、8静音箱。
具体实施方式
29.下面结合视图对本实用新型进行详细的描述,所列举的实施例可以使本专业的技术人员更理解本实用新型,但不以任何形式限制本实用新型。
30.如图2至图7所示,本实用新型公开一种用于螺杆空压机的油气分离器,它包括油气分离器本体1和滤芯总成2。油气分离器本体1是空心圆柱形,本体1内部设有隔筒11,隔筒11固定在本体上部的隔板12下表面,且隔筒11的高度不大于本体1高度的一半,隔筒11外壁与本体1内壁及隔板12之间形成油气通道13。本体1侧面设有油气入口14,油气入口14上连接油气管道4,油气管道4与本体1内壁相切,使油气混合物切向进入油气分离器本体1,其中图7箭头为油气混合物走向。油气混合物进入本体1后在油气通道13内旋转,旋转过程中油气混合物多次碰撞油气通道壁,使较大颗粒的油滴落到本体1下半部的集油槽15。
31.油气分离本体1顶部设有空心管3与油气分离滤芯总成2连接,滤芯总成2的油气混合物入口低于本体1的油气混合物出口,进一步地,滤芯总成2低于本体1。空心管3存在拐弯点,其中空心管3可以是s型硬管或z型硬管,油气混合物在通过拐弯点时撞击管壁,能够使油滴留在管道内,使油气混合物分离,必要时将分离出的润滑油引流,此处不作赘述。滤芯总成2可将经过油气通道13和空心管3后未被分离的油气混合物扩散和聚合后,使小油滴聚合成大油滴,在气动的作用下通过滤层,沉降在滤芯总成底部,从而将油气混合物进一步分离。滤芯总成2与本体1之间采用空心管3作为过渡使本体1和滤芯总成2形成间接连接,所以滤芯总成2的位置不受本体1的限制,为了维修方便,本实用新型将滤芯总成2放置在本体1外部。进一步地,为了便于静音箱8等配件的设计,降低规则立方体外壳和包装的高度,将滤芯总成2的位置设置在本体1侧面,静音箱8内的本体及螺杆机6和变频电动机7是纵向直联,占的是横向空间,油器分离器本体1和滤芯总成2上下结构占的是高度空间,通过一条管把滤芯总成从内部或顶部改成并列,充分利用了三维空间,并且也节省其它的管路,比如进油管回油管等,各系统均有一定的间隔,由于滤芯总成2宽度较小,将滤芯总成2设置在合适的间隔处,无需增大静音箱8及包装箱的宽度。从整体高度来说滤芯总成2低于本体1,因此滤芯总成2侧置不增加整体的高度,而且由于滤芯总成2侧置还使本体内部结构简单(相对于内置式),高度下降,滤芯总成内置式的油气分离器整体高度约80cm,滤芯总成顶置式的油气分离器整体高度约100cm,本实用新型滤芯总成侧置式的油气分离器整体高度约70cm,由此可见,将滤芯总成设置在本体侧面有利于降低油气分离器的高度,在维修方便的基础上与滤芯总成内置式的油气分离器高度一致。而滤芯总成的宽度约为14cm,如图6和图7所示,可在并列放置的各系统间隔中放置滤芯总成。
32.为了使油气分离器整体的结构更紧凑,进一步减少油气分离器占用的空间,将空心管3的大部分设置在本体1内部,具体地,空心管3的一端固定在油气通道13上方,即本体1内壁和隔板12之间,空心管3纵向穿过隔筒11内部,从本体1下半部侧面的通孔穿出后与滤芯总成2连接。空心管3的大部分都在本体1内部,减少了空心管3占用的空间,尤其是滤芯总成2和本体1侧壁之间的空间,使本体1和滤芯总成2能够紧挨放置,减少油气分离器的体积,
也便于后期其他装置的设计。
33.油气分离器本体1内的圆形隔筒11与空心圆柱形本体1的中心轴平行但不重合,即本体1和隔筒11是偏心设置,这样使得油气通道13的横截面积不等。油气分离器的油气入口14设置在本体1侧壁且油气通道13横截面积最大的位置,油气管道4与本体1内壁是切向设置,油气混合物切向进入本体1在油气通道13内旋转,由于本体1和隔筒11是偏心设置且油气入口14处油气通道13的横截面积最大,所以油气混合物经过的油气通道13的横截面积逐渐减小,即宽进窄出,增加油气混合物与本体1内壁的碰撞机会,促进油气分离得更彻底。隔筒11的存在还能够防止油气混合物进入到本体1内部后直接进入空心管3,以便于油气混合物中的大油滴在本体1内被分离。
34.隔筒11固定在本体1内的隔板12上,所述隔板12倾斜设置在本体1内,隔板12与隔筒11外壁及本体1内壁形成油气通道13,倾斜的隔板12使油气通道13的纵截面积产生变化。油气入口14一侧的隔板12高于另一侧,且隔板12的最高点与油气入口14处在同一母线上,油气混合物经过的油气通道13的纵截面积逐渐减小,油气混合物在本体内更能形成涡流,增加油气混合物与本体1内壁碰撞的机会,进一步促进油气分离得更彻底。
35.未述部分与现有技术相同。
36.以上实施例仅为说明本实用新型的技术思想,不能以此限定本实用新型的保护范围,凡是按照本实用新型提出的技术思想,在技术方案基础上所做的任何改进与等同替换,均落入本实用新型保护范围之内。
再多了解一些
本文用于企业家、创业者技术爱好者查询,结果仅供参考。