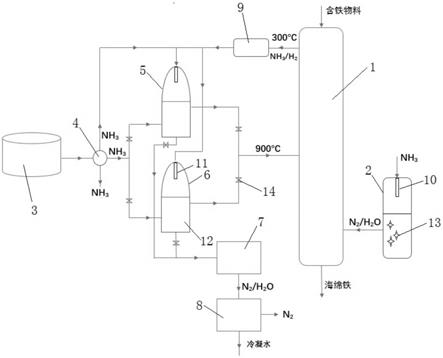
1.本实用新型涉及直接还原铁技术领域,尤其涉及一种氨气直接还原铁实现近零排放的系统。
背景技术:
2.直接还原炼铁是用气体或固体还原剂在低于铁矿石软化温度下,在反应装置内将铁矿石还原成金属铁的方法,其产品称直接还原铁(dri),这种铁保留了失氧前的外形,因失氧形成大量微孔隙,显微镜下形似海绵结构,故又称海绵铁。
3.气基竖炉直接还原炼铁因其操作容易、能耗低、效率高等优点,已经成为当今世界主流的海绵铁生产方法。目前,气基直接还原炼铁一般采用co和h2作为气体还原剂来生产海绵铁。但是,co用作气体还原存在还原气析碳、铁矿石易还原粉化粘接、冷却设备复杂、产生温室气体co2等问题。h2用作气体还原剂存在长时间储存及远距离运输不便等问题。
4.公开号为cn111575427a的中国专利申请公开了“一种近零排放的氢冶金工艺”,其采用氢气将铁矿原料直接还原铁。气体供应与循环系统包括水制氢系统、第二氢气压缩机、调节阀组、第三氢气压缩机、加热器和预热器等,设备组成复杂。实际上,采用水制备氢气的方式很难满足大型钢铁冶炼系统还原铁矿原料时对氢气的需求。氢气不便于长时间储存和远距离运输的问题将制约该工艺的应用,而在钢铁企业内部建立大型储氢站存在巨大的安全隐患。
5.公告号为cn209798009u的中国实用新型专利公开了“一种采用氢气生产热态海绵铁的系统”,其采用氢气生产热态海绵铁,直接还原竖炉的热态氢气入口取代了传统的还原气入口,促进铁矿石还原更加有效。该技术方案中没有明确说明氢气的供给和储存方式,而大型钢铁冶炼系统还原铁矿原料时对氢气需求量巨大,因此同样存在氢气不便于长时间储存和远距离运输的问题制约其应用,而在钢铁企业内部建立大型储氢站存在巨大的安全隐患的问题。
6.公开号为cn107299176a的中国专利申请公开了“一种竖炉生产直接还原铁的系统及其方法”,其利用低阶煤热解制备还原气,经调质后通入竖炉将铁矿直接还原为海绵铁。其调质煤气中含有co、co2和ch4,无法解决co还原存在还原气析碳、铁矿石易还原粉化粘接、冷却设备复杂和co2温室气体排放等问题。
7.综上所述,目前,需要寻找一种新的气体还原剂以解决上述问题。
8.氨气作为无碳燃料,同时也是一种富氢气体,其中氢的质量百分比为17.6%,其在高温时会分解成氮气和氢气,有还原作用。氨气可在常温下加压液化或常压下冷却液化,且液氨的体积能量密度高于液氢,因此液氨更便于储存和运输,是氢的理想载体。
技术实现要素:
9.本实用新型提供了一种氨气直接还原铁实现近零排放的系统,实现了氨气直接还原铁的工业化生产,且工艺过程简单,不产生co2等温室气体或有害气体;采用高效低氮燃
烧器结合scr脱硝等烟气处理装置,实现no近零排放;还原过程中产生的粉尘经过除尘后实现粉尘近零排放;工艺过程无废水产生,海绵铁为固态,无常规高炉冶炼渣产生。
10.为了达到上述目的,本实用新型采用以下技术方案实现:
11.一种氨气直接还原铁实现近零排放的系统,包括直接还原竖炉、蓄热式换热装置、氨气燃烧及预处理装置;
12.所述直接还原竖炉的顶部设含铁物料入口,底部设海绵铁出口;直接还原竖炉的上部设还原气出口,中部设高温氨气入口,下部设高温烟气入口;
13.所述直接还原竖炉的高温烟气入口通过高温烟气管道连接氨气燃烧及预处理装置的高温烟气出口,氨气燃烧及预处理装置设氨气燃烧器,氨气燃烧器的燃烧气体入口连接氨气气源;氨气燃烧及预处理装置中的高温烟气流动路径上设有海绵铁容纳空间;
14.所述直接还原竖炉的高温氨气入口通过高温氨气管道连接蓄热式换热装置的高温氨气出口;蓄热式换热装置设混合气燃烧器,混合气燃烧器的燃烧气体入口管分别连接氨气气源及直接还原竖炉的还原气出口;蓄热式换热装置中设蓄热体,对应蓄热体两端的蓄热式换热装置上分别设氨气入口及高温氨气出口;氨气入口连接氨气气源;蓄热式换热装置的烟气出口连接烟气处理系统。
15.所述氨气气源由液氨储罐及气化装置组成;所述液氨储罐的液氨出口连接气化装置的液氨入口;气化装置设第一氨气出口、第二氨气出口和第三氨气出口,第一氨气出口通过第一氨气管道连接蓄热式换热装置的氨气入口,第二氨气出口通过第二氨气管道连接蓄热式换热装置上混合气燃烧器的燃烧气体入口管;第三氨气出口通过第三氨气管道连接氨气燃烧及预处理装置上氨气燃烧器的燃烧气体入口。
16.所述烟气处理系统至少包括scr脱硝装置及冷凝器;蓄热式换热装置的烟气出口通过烟气管道依次连接scr脱硝装置及冷凝器。
17.所述蓄热式换热装置由至少2个蓄热式换热器组成,蓄热式换热器之间并联设置。
18.所述直接还原竖炉的还原气出口通过还原气管道连接蓄热式换热装置上混合气燃烧器的燃烧气体入口管;所述还原气管道上设除尘装置;所述氨气燃烧器、混合气燃烧器采用高效低氮燃烧器。
19.所述直接还原竖炉的含铁物料入口处设密封加料装置。
20.与现有技术相比,本实用新型的有益效果是:
21.1)实现了氨气直接还原铁的工业化生产,且工艺过程简单;
22.2)绿色环保,不产生co2等温室气体或有害气体;采用高效低氮燃烧器结合scr脱硝等烟气处理装置,实现no近零排放;还原过程中产生的粉尘经过除尘后实现粉尘近零排放;工艺过程无废水产生,海绵铁为固态,无常规高炉冶炼渣产生。
附图说明
23.图1是本实用新型所述一种氨气直接还原铁实现近零排放的系统的结构示意图。
24.图中:1.直接还原竖炉2.氨气燃烧及预处理装置3.液氨储罐4.气化装置5.蓄热式换热器一6.蓄热式换热器二7.scr脱硝装置8.冷凝器9.除尘装置10.氨气燃烧器11.混合气燃烧器12.蓄热体13.海绵铁14.阀门
具体实施方式
25.下面结合附图对本实用新型的具体实施方式作进一步说明:
26.如图1所示,本实用新型所述一种氨气直接还原铁实现近零排放的系统,包括直接还原竖炉1、蓄热式换热装置(包括蓄热式换热器一6、蓄热式换热器二7)、氨气燃烧及预处理装置2;
27.所述直接还原竖炉1的顶部设含铁物料入口,底部设海绵铁出口;直接还原竖炉1的上部设还原气出口,中部设高温氨气入口,下部设高温烟气入口;
28.所述直接还原竖炉1的高温烟气入口通过高温烟气管道连接氨气燃烧及预处理装置2的高温烟气出口,氨气燃烧及预处理装置2设氨气燃烧器10,氨气燃烧器10的燃烧气体入口连接氨气气源;氨气燃烧及预处理装置2中的高温烟气流动路径上设有海绵铁容纳空间;
29.所述直接还原竖炉1的高温氨气入口通过高温氨气管道连接蓄热式换热装置的高温氨气出口;蓄热式换热装置设混合气燃烧器11,混合气燃烧器11的燃烧气体入口管分别连接氨气气源及直接还原竖炉1的还原气出口;蓄热式换热装置中设蓄热体12,对应蓄热体12两端的蓄热式换热装置上分别设氨气入口及高温氨气出口;氨气入口连接氨气气源;蓄热式换热装置的烟气出口连接烟气处理系统。
30.所述氨气气源由液氨储罐3及气化装置4组成;所述液氨储罐3的液氨出口连接气化装置4的液氨入口;气化装置4设第一氨气出口、第二氨气出口和第三氨气出口,第一氨气出口通过第一氨气管道连接蓄热式换热装置的氨气入口,第二氨气出口通过第二氨气管道连接蓄热式换热装置上混合气燃烧器11的燃烧气体入口管;第三氨气出口通过第三氨气管道连接氨气燃烧及预处理装置2上氨气燃烧器10的燃烧气体入口。
31.所述烟气处理系统至少包括scr脱硝装置7及冷凝器8;蓄热式换热装置的烟气出口通过烟气管道依次连接scr脱硝装置7及冷凝器8。
32.所述蓄热式换热装置由至少2个蓄热式换热器组成,蓄热式换热器之间并联设置。
33.所述直接还原竖炉1的还原气出口通过还原气管道连接蓄热式换热装置上混合气燃烧器11的燃烧气体入口管;所述还原气管道上设除尘装置9;所述氨气燃烧器10、混合气燃烧器11采用高效低氮燃烧器。
34.所述直接还原竖炉1的含铁物料入口处设密封加料装置。
35.本实用新型所述一种氨气直接还原铁实现近零排放的系统的工艺过程如下:
36.1)氨气在氨气燃烧及预处理装置2中燃烧,产生的高温烟气内含有氮气、水蒸气和微量的no,高温烟气经过氨气燃烧及预处理装置2中填充的海绵铁后,no还原成n2而被脱除;温度为940℃~950℃和高温烟气进入直接还原竖炉1内,对含铁物料进行预热;含铁物料预热到900℃以上时停止加热,氨气燃烧及预处理装置2停止运行;
37.2)含铁物料通过密封加料装置从直接还原竖炉1的顶部加入,直接还原竖炉1的高温区预热温度为900℃~920℃,出口段预热温度为300℃~350℃;
38.3)液氨储罐3中的液氨经过气化装置4后产生氨气;一部分氨气经蓄热式换热装置加热到900℃~950℃后,部分分解成h2和n2,并且分解后h2的浓度为30%~35%;由nh3、h2和n2组成的高温混合气体进入直接还原竖炉1内,完成含铁物料的还原过程,生成的海绵铁自海绵铁出口送出;
39.4)直接还原竖炉1内的还原过程完成后,炉顶的还原气成分包括nh3、h2、n2及h2o,其中nh3的浓度为20%~30%,h2的浓度为15%~25%;温度为300℃以上的还原气经过除尘装置9除尘后,与设定量的氨气混合后进入蓄热式换热装置的混合气燃烧器11中燃烧,产生的高温烟气用于加热蓄热体12,并通过蓄热体12对进入直接还原竖炉1的氨气进行预热;
40.5)蓄热式换热装置中,待蓄热体12的高温区升温到920℃~930℃时停止加热;高温烟气经过蓄热体12换热,温度降低到180℃以下后进入scr脱硝装置7,将燃烧产生的no还原成n2,产生含n2的水蒸气;水蒸气经冷凝器8冷凝后的冷凝水作为工艺用水,冷凝产生的热量用于为气化装置4提供热源,n2直接排放到大气中。
41.所述步骤1)中,在氨气燃烧及预处理装置2内被氧化后的海绵铁,在含铁物料预热结束后送入直接还原竖炉1重新进行还原反应。
42.所述含铁物料为天然块矿或球团矿,粒径为10~20mm。
43.所述蓄热式换热装置由蓄热式换热器一5和蓄热式换热器二6组成,蓄热式换热器一5与蓄热式换热器二6交替工作,每个蓄热式换热器5、6均按照燃烧
‑
休止
‑
送风
‑
休止
‑
燃烧的顺序循环运行,即当蓄热式换热器一5送风时,蓄热式换热器二6处于燃烧状态;当蓄热式换热器一5温度降低后,燃烧后处于休止状态的蓄热式换热器二6投入送风,蓄热式换热器一5此时停止送风并开始燃烧、蓄热直至温度达到要求后,转入休止状态等待下一次送风。
44.本实用新型解决了现有常规钢铁冶炼排放大量二氧化碳、废气废渣、污染环境等问题。采用氨气作为燃料和还原剂,无co2和废水产生,nox和so2几乎无排放,粉尘排放量比传统冶炼工艺降低90%以上,是一种无碳环保的绿色炼铁工艺。
45.以下实施例在以本实用新型技术方案为前提下进行实施,给出了详细的实施方式和具体的操作过程,但本实用新型的保护范围不限于下述的实施例。下述实施例中所用方法如无特别说明均为常规方法。
46.【实施例】
47.如图1所示,本实施例中,一种氨气直接还原铁实现近零排放的系统包括直接还原竖炉1、氨气燃烧及预处理装置2、液氨储罐3、气化装置4、蓄热式换热器一5、蓄热式换热器二6、除尘装置9、scr脱硝装置7及冷凝器8。蓄热式换热器一5、蓄热式换热器二6并联设置。
48.所述直接还原竖炉1的顶部设含铁物料入口,底部设海绵铁出口;直接还原竖炉1的上部设还原气出口,中部设高温氨气入口,下部设高温烟气入口。
49.所述直接还原竖炉1的高温烟气入口通过高温烟气管道连接氨气燃烧及预处理装置2的高温烟气出口,氨气燃烧及预处理装置2设氨气燃烧器10,氨气燃烧器10的燃烧气体入口连接氨气气源;氨气燃烧及预处理装置2中的高温烟气流动路径上设有海绵铁容纳空间;即氨气燃烧及预处理装置2中填充有海绵铁。
50.所述直接还原竖炉1的高温氨气入口通过高温氨气管道连接蓄热式换热器一5、蓄热式换热器二6的高温氨气出口;高温氨气管道上分别设阀门14;蓄热式换热器一5、蓄热式换热器二6分别设混合气燃烧器11,混合气燃烧器11的燃烧气体入口管分别连接氨气气源及直接还原竖炉1的还原气出口;蓄热式换热器一5、蓄热式换热器二6中分别设蓄热体12,对应蓄热体12两端的蓄热式换热器一5、蓄热式换热器二6上分别设氨气入口及高温氨气出口。
51.本实施例中,氨气气源由液氨储罐3及气化装置4组成;所述液氨储罐3的液氨出口连接气化装置4的液氨入口;气化装置4设第一氨气出口、第二氨气出口和第三氨气出口,第一氨气出口通过第一氨气管道连接蓄热式换热器一5、蓄热式换热器二6的氨气入口,且连接2个蓄热式换热器5、6的第一氨气管道上分别设阀门14。第二氨气出口通过第二氨气管道连接蓄热式换热器一5、蓄热式换热器二6上混合气燃烧器11的燃烧气体入口管;第三氨气出口通过第三氨气管道连接氨气燃烧及预处理装置2上氨气燃烧器10的燃烧气体入口。
52.本实施例中,烟气处理系统包括scr脱硝装置7及冷凝器8;蓄热式换热器一5、蓄热式换热器二6的烟气出口分别通过烟气管道依次连接scr脱硝装置7及冷凝器8。
53.直接还原竖炉1的还原气出口通过还原气管道连接蓄热式换热装置上混合气燃烧器11的燃烧气体入口管;所述还原气管道上设除尘装置9;所述氨气燃烧器10、混合器燃烧器11采用高效低氮燃烧器。
54.本实施例中,一种氨气直接还原铁实现近零排放的工艺过程如下:
55.液氨储罐3中的液氨经过气化装置4产生氨气,一部分氨气送入氨气燃烧及预处理装置2中燃烧,产生950℃高温烟气后进入直接还原竖炉1,预热粒径为10~20mm的天然块矿,将天然块矿加热到900℃;氨气经过蓄热式换热器一5或蓄热式换热器二6被加热到900℃,然后从下部进入直接还原竖炉1;天然块矿经过氨气和氢气共同还原后形成海绵铁,并从直接还原竖炉1的炉底排出;海绵铁排出后运送至高温冶炼炉;直接还原竖炉1炉顶温度为300℃的还原气经过除尘装置9净化后,与自气化装置4引出的部分氨气混合,进入蓄热式换热器一5或蓄热式换热器二6中,经混合气燃烧器11燃烧产生高温烟气加热蓄热体12,待蓄热体12高温区升温到920℃时停止加热。高温烟气与蓄热体12换热后温度降低到180℃,进入后续的scr脱硝装置7,将燃烧产生的no还原成n2,含n2的水蒸气经过冷凝器8后的冷凝水回收作为企业工艺用水,n2直接排放到大气中。
56.本实施例中,氨气直接还原铁的反应过程如下:
57.2nh3=n2 3h258.3fe2o3 h2=2fe3o4 h2o
59.fe3o4 h2=3feo h2o
60.feo h2=fe h2o
61.9fe2o3 2nh3=6fe3o4 n2 3h2o
62.3fe3o4 2nh3=9feo n2 3h2o
63.3feo 2nh3=3fe n2 3h2o。
64.本实施例中,蓄热式换热器一5与蓄热式换热器二6交替工作,每个蓄热式换热器均按照燃烧
‑
休止
‑
送风
‑
休止
‑
燃烧的顺序循环运行,即当蓄热式换热器一5送风时,蓄热式换热器二6处于燃烧状态;当蓄热式换热器一5温度降低后,燃烧后处于休止状态的蓄热式换热器二6投入送风,蓄热式换热器一5此时停止送风并开始燃烧、蓄热直至温度达到要求后,转入休止状态等待下一次送风。
65.本实施例中,蓄热式换热器一5、蓄热式换热器二6主要由本体、混合气燃烧器11和蓄热体12组成。混合气燃烧器11采用高效低氮燃烧器,所使用的燃料为氨气、氢气和氮气组成的混合气体。蓄热体12采用蜂窝陶瓷蓄热体。在蓄热式换热器一5或蓄热式换热器二6中,混合气体与空气在混合气燃烧器11中混合燃烧产生高温烟气,高温烟气通过与蓄热体12进
行热交换过程将其携带的热量传递到蓄热体12中,燃烧60min后进行状态切换,即停止燃烧,通入氨气;氨气通过蓄热体12进行热交换获得热量,将温度升至900℃后送入直接带原竖炉1还原铁矿石。
66.以上所述,仅为本实用新型较佳的具体实施方式,但本实用新型的保护范围并不局限于此,任何熟悉本技术领域的技术人员在本实用新型揭露的技术范围内,根据本实用新型的技术方案及其实用新型构思加以等同替换或改变,都应涵盖在本实用新型的保护范围之内。
再多了解一些
本文用于企业家、创业者技术爱好者查询,结果仅供参考。