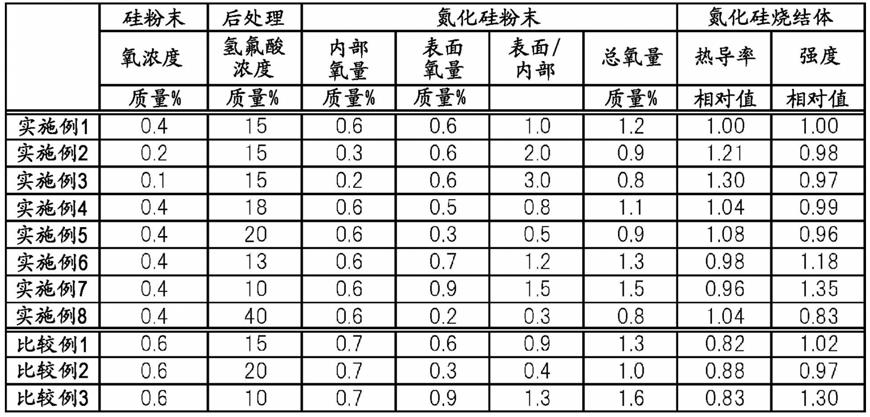
1.本公开文本涉及氮化硅粉末及其制造方法、以及氮化硅烧结体的制造方法。
背景技术:
2.氮化硅为强度、硬度、韧性、耐热性、耐腐蚀性、耐热冲击性等优异的材料,因此被用于压铸机及熔炼炉等各种工业用的部件及汽车部件等。另外,氮化硅由于高温下的机械特性也优异,因此研究了应用于要求高温强度、高温蠕变特性的燃气轮机部件的情况。例如,在专利文献1中,作为提高氮化硅烧结体的高温特性的方法,研究了将氮化硅粉末的总氧量设为1.5质量%以下以减少烧结时纯化的晶界相,并将熔点维持得高来提高高温特性的方法。
3.还研究了氮化硅基板作为汽车及工作机械等的电力模组等的绝缘基板使用的情况。例如,在专利文献2中,提出了铝
‑
陶瓷接合基板使用氮化硅基板的方案。在这样的用途中,要求具有高绝缘性及散热性。
4.现有技术文献
5.专利文献
6.专利文献1:日本特开平7
‑
206409号公报
7.专利文献2:日本特开2011
‑
077546号公报
技术实现要素:
8.发明要解决的课题
9.作为氮化硅基板,为了实现优异的散热性,要求具有高热导率。在基板使用的氮化硅烧结体中,作为对热导率产生影响的因素,可举出氮化硅烧结体中存在的缺陷的量。就氮化硅烧结体中的缺陷的量而言,认为不仅受烧结条件影响,也受氮化硅烧结体中使用的氮化硅粉末的物性的影响。因此,在本公开文本中,提供能够制得具有高热导率的氮化硅烧结体的氮化硅粉末及其制造方法。另外,在本公开文本中,提供具有高热导率的氮化硅烧结体的制造方法。
10.用于解决课题的手段
11.本公开文本的一个方面涉及的氮化硅粉末的内部氧量为0.6质量%以下。这样的氮化硅粉末由于内部氧量足够低,因此在作为烧结原料使用时,能够制得具有高热导率的氮化硅烧结体。作为其理由,认为能够通过使用内部氧量少的氮化硅粉末来减少氮化硅烧结体内部的缺陷。
12.上述氮化硅粉末的表面氧量可以为内部氧量以下。由此,能够制得具有更高的热导率的氮化硅烧结体。
13.上述氮化硅粉末的表面氧量可以大于内部氧量。若表面氧量增大,则烧结时容易形成液相,能够提高氮化硅烧结体的强度。
14.本公开文本的一个方面涉及的氮化硅粉末的制造方法具有下述工序:在包含氮与
选自由氢及氨组成的组中的至少一者的混合气氛下对氧浓度为0.4质量%以下的硅粉末进行烧成而制得烧成物的工序;和使用氟化氢浓度为10~40质量%的氢氟酸对烧成物进行处理的工序。根据该制造方法,由于使用氧浓度足够低的硅粉末,因此能够制得内部氧量足够低的氮化硅粉末。另外,由于使用氟化氢浓度为10~40质量%的氢氟酸对烧成物进行处理,因此表面氧量也能够调节为与内部氧相差不大的范围。因此,能够优选用作用于制造具有充分的强度且具有高热导率的氮化硅烧结体的氮化硅粉末。
15.本公开文本的一个方面涉及的氮化硅烧结体的制造方法具有对包含由上述氮化硅粉末的制造方法制造的氮化硅粉末的烧结原料进行成型并烧成的工序。根据该制造方法,能够制造具有高热导率的氮化硅烧结体。
16.发明的效果
17.根据本公开文本,能够提供可制得具有高热导率的氮化硅烧结体的氮化硅粉末及其制造方法。另外,能够提供具有高热导率的氮化硅烧结体的制造方法。
附图说明
18.图1是示出氧/氮分析图表的一例的图。
19.图2是示出实施例1的氧/氮分析图表的图。
具体实施方式
20.以下,根据情况,参照附图对本公开文本的一个实施方式进行说明。但是,以下实施方式为用于说明本公开文本的例示,并非旨在将本公开文本限定为以下的内容。
21.一个实施方式涉及的氮化硅粉末(si3n4粉末)的内部氧量为0.6质量%以下。内部氧为未在氮化硅粉末的表面露出而存在于粉末的内部的氧。在作为氮化硅烧结体的原料使用时,从进一步提高氮化硅烧结体的热导率的观点出发,内部氧量可以是0.5质量%以下,也可以是0.4质量%以下。该内部氧量的下限没有特别限定,但从制造容易性的观点出发,可以是0.1质量%以上,也可以是0.2质量%以上。内部氧量能够通过改变氮化硅粉末的原料中的氧浓度来调节。
22.从充分降低氮化硅烧结体的热导率的观点出发,氮化硅粉末的表面氧量可以是内部氧量以下。表面氧为结合或附着于氮化硅粉末的表面的氧。表面氧量例如可以为0.6质量%以下,可以为0.5质量%以下,也可以为0.4质量%以下。该表面氧量的下限没有特别限定,但从制造容易性的观点出发,可以是0.05质量%以上,也可以是0.1质量%以上、0.2质量%以上。表面氧量能够通过对氮化硅粉末进行表面处理来调节。
23.在其他实施方式中,在作为氮化硅烧结体的原料使用时,从提高氮化硅烧结体的强度的观点出发,氮化硅粉末的表面氧量可以大于内部氧量,可以是0.7质量%以上,也可以是0.8质量%以上。该表面氧量的上限没有特别限定,但从制造容易性的观点出发,可以是1.5质量%以下,也可以是1.0质量%以下。
24.氮化硅粉末的总氧量可以是0.5质量%以上,可以是0.7质量%以上,也可以是1.0质量%以上。氮化硅粉末的总氧量可以是2.0质量%以下,也可以是1.5质量%以下。作为一例,可以是0.5~2.0质量%,也可以是0.7~1.5质量%。在本公开文本中,总氧量是氧的质量相对于氮化硅粉末的整体质量的比率。另一方面,内部氧量是内部的氧的质量相对于氮
化硅粉末的整体质量的比率。另外,表面氧量是表面的氧的质量相对于氮化硅粉末的整体质量的比率。因此,下式是成立的。
25.总氧量(质量%)=内部氧量(质量%) 表面氧量(质量%)
26.本公开文本中的内部氧量、表面氧量及总氧量通过以下的步骤求出。使用氧氮分析仪对氮化硅粉末的氧量及氮量进行分析。在氦气氛中,以8℃/秒的升温速度使测定用的试样从20℃升温至2000℃。与升温相伴,对脱离的氧进行检测。在升温初始,结合于氮化硅粉末的表面的氧脱离。通过确定脱离的氧量来求出表面氧量。
27.其后,在温度到达1400℃附近时,氮化硅开始分解。氮化硅的分解开始能够通过氮的检测开始来把握。若氮化硅开始分解,则位于氮化硅粉末的内部的氧脱离。通过对在该阶段脱离的氧进行定量,从而求出内部氧量。
28.图1是通过氮化硅的氧/氮分析得到的图表的一例。峰1为表面氧的峰,峰2为内部氧的峰。峰3为氮的峰。直线4表示升温直线。峰1与峰2由开始产生氮的温度t1划分。温度t1为峰3的检测开始的温度,通常处于1350~1500℃之间。峰1的检测开始的温度(峰1的左端的温度)为例如750~1200℃。峰2的检测结束的温度(峰2的右端的温度)为例如1600~1800℃。由峰1、2的累计值(面积)基于标准曲线求出内部氧量和表面氧量。另外,内部氧量与表面氧量的合计为总氧量。
29.在图1中,峰3的左端(温度t1)与峰1、2的谷部的最深部一致,但二者也可以不完全一致。但通常而言,温度t1(峰3的左端)位于检测到峰1与峰2各自的顶部的温度之间。
30.图1的氮化硅粉末由于内部氧量足够低,因此若作为烧结原料使用,则能够制得热导率优异的氮化硅烧结体。作为其理由,认为能够通过使用内部氧量少的氮化硅粉末来减少氮化硅烧结体的内部的缺陷。如图1所示,氮化硅粉末的表面氧量可以是内部氧量以下。由此,能够制得具有更高热导率的氮化硅烧结体。
31.在图1中,峰2的累计值大于峰1的累计值,但不限定于该大小关系。例如,也可以是峰1的累计值大于峰2的累计值。在该情况下,表面氧量大于内部氧量,能够制造强度优异的氮化硅烧结体。从充分提高氮化硅烧结体的热导率的观点出发,峰1的累计值相对于峰2的累计值之比、即表面氧量相对于内部氧量之比可以是1以上,可以是1.2以上,也可以是1.3以上。
32.表面氧量相对内部氧量之比可以是0.8以上,可以是1.0以上,也可以是1.5以上。特别是,通过使总氧量为1.0质量%以下并使表面氧量相对于内部氧量之比为1.5以上,从而能够进一步改善热导率。该比优选为1.8以上,更加优选为2.0以上。表面氧量相对于内部氧量之比的上限可以是5.0,也可以是4.0。
33.一个实施方式涉及的氮化硅粉末的制造方法具有下述工序:前处理工序,使用含有氢氟酸的前处理液对硅粉末进行前处理从而制得氧浓度为0.4质量%以下的硅粉末;烧成工序,在包含氮与氢的混合气氛下对该硅粉末进行烧成而制得烧成物;粉碎工序,对烧成物进行粉碎;和后处理工序,使用氟化氢浓度为10~40质量%的氢氟酸对粉碎后的烧成物进行处理。
34.在前处理工序中,使用含有氢氟酸的前处理液来减少与硅粉末结合的氧。前处理液可以使用作为氢氟酸与盐酸的混合物的混酸,也可以仅使用氢氟酸。前处理工序中的前处理液的温度为例如40~80℃。另外,浸渍在前处理液中的时间为例如1~10小时。
35.在前处理工序中制得的硅粉末的氧浓度为0.4质量%以下,优选为0.3质量%以下,更加优选为0.2质量%以下。该氧浓度的下限没有特别限制,从制造容易性的观点出发,可以是0.1质量%以上。
36.在烧成工序中,在包含氮与选自由氢及氨组成的组中的至少一者的混合气氛下对硅粉末进行烧成而制得氮化物。混合气氛中的氢及氨的含有比例的合计可以是10~40体积%。烧成温度可以是例如1100~1450℃,也可以是1200~1400℃。烧成时间可以是例如30~100小时。
37.在烧成工序中制得的氮化硅变为锭状的情况下,实施对烧成物进行粉碎的粉碎工序。粉碎也可以分为粗粉碎和微粉碎的多个阶段进行。粉碎例如也可以使用球磨机以湿式进行。氮化硅可以粉碎至比表面积变为8.0~15.0m2/g。
38.在后处理工序中,将粉碎后的烧成物与氟化氢浓度为10~40质量%的氢氟酸配合来进行处理。例如,也可以使烧成物分散到氢氟酸中进行处理。氢氟酸中的氟化氢浓度可以是12~30质量%。后处理工序中的氢氟酸的温度为例如40~80℃。另外,将氮化硅粉末浸渍在氢氟酸中的时间为例如1~10小时。
39.通过这样的制造方法,能够将氮化硅粉末的总氧量、内部氧量及表面氧量调节为上述范围。使用按照这种方式制得的氮化硅粉末所形成的氮化硅烧结体具有高热导率。
40.一个实施方式涉及的氮化硅烧结体的制造方法具有对包含上述氮化硅粉末作为主成分的烧结原料进行成型并烧成的工序。烧结原料除了氮化硅粉末以外,也可以包含氧化物系烧结助剂。作为氧化物系烧结助剂,可举出y2o3、mgo及al2o3等。烧结原料中的氧化物系烧结助剂的含量可以为例如3~10质量%。
41.在上述工序中,以例如3.0~30mpa的成型压力对上述的烧结原料进行加压以制得成型体。成型体也可以进行单轴加压来制备,也可以通过cip来制备。另外,也可以一边通过热压进行成型一边进行烧成。成型体的烧成可以在氮气或氩气等非活性气体气氛中进行。烧成时的压力可以是0.7~1mpa。烧成温度可以是1860~2100℃,也可以是1880~2000℃。该烧成温度中的烧成时间可以是6~20小时或8~16小时。至烧成温度为止的升温速度可以是例如1.0~10.0℃/小时。
42.按照这种方式制造的氮化硅烧结体具有高热导率,因此散热性优异。另外,通过使原料中使用的氮化硅粉末的表面氧量增高,从而能够制成强度也优异的氮化硅烧结体。氮化硅烧结体的热导率在例如25℃的环境下可以是100w/mk以上,也可以是110w/mk以上。氮化硅烧结体的3点弯曲强度例如于室温可以是500mpa以上,也可以是600mpa以上。
43.以上,对几个实施方式进行了说明,但本公开文本不受上述实施方式的任何限制。
44.实施例
45.参照实施例及比较例,更详细地说明本公开文本的内容,但本公开文本并不限定于下述实施例。
46.(实施例1)
47.<氮化硅粉末的制备>
48.将市售的硅粉末(比表面积:3.0m2/g)浸渍在混酸中来实施前处理。在前处理中,将硅粉末放入温度调节为60℃的上述混酸中并浸渍2小时。作为前处理中使用的混酸,使用将市售的盐酸(浓度:35质量%)和氢氟酸(浓度:55质量%)以10:1的质量比配合的物质。其
后,将硅粉末从混酸取出并用水清洗,在氮气氛下进行干燥。干燥后的硅粉末的氧浓度为0.4质量%。该氧浓度通过红外线吸收法测定。
49.使用干燥后的硅粉末制备成型体(体积密度:1.4g/cm3),使用电炉于1400℃烧成烧成60小时来制备氮化硅锭。烧成时的气氛为氮与氢的混合气氛(n2:h2=80:20,体积基准)。将所制得的锭进行粗粉碎后,使用球磨机进行湿式粉碎。作为湿式粉碎时的溶剂,使用水。
50.进行下述后处理:将进行湿式粉碎所制得的氮化硅粉末在温度为60℃的氢氟酸(氟化氢浓度:15质量%)中浸渍2小时。其后,将氮化硅粉末从氢氟酸中取出并用水清洗,在氮气氛下干燥。像这样,制得实施例1的氮化硅粉末。
51.<氮化硅粉末的评价>
52.通过以下步骤测定氮化硅粉末的内部氧量和表面氧量。将测定用的试样0.01g放置在氧氮分析仪(堀场制作所制,装置名称:emga
‑
920)中。在氦气氛中,以8℃/秒的升温速度从20℃升温至2000℃。在升温中对氧及氮进行检测。将测定结果示于图2。如图2所示,检测到源自于表面氧的峰1、源自于内部氧的峰2、源自于氮的峰3。直线4表示温度。
53.峰3开始出现的温度、即划分峰1与峰2的温度t1为1392℃。根据峰1、2的累计值和另行求出的峰累计值和氧量的标准曲线,求出表面氧量及内部氧量。其结果如表1所示。
54.<氮化硅烧结体的制备>
55.将90质量份所制备的氮化硅粉末、5质量份平均粒径为1.5μm的y2o3粉末及5质量份平均粒径为1.2μm的yb2o3粉末配合,在甲醇中湿式混合4小时。其后,将干燥而得的混合粉末以10mpa的压力进行模具成型,其后,进一步以25mpa的压力进行cip成型。将所制得的成型体与由氮化硅粉末及bn粉末的混合粉末形成的填充粉末一并放入碳制坩埚中,在1mpa的氮加压气氛下于温度1900℃进行12小时烧成,制造氮化硅烧结体。
56.<氮化硅烧结体的评价>
57.对氮化硅烧结体进行研削加工,制备热导率测定用的的圆盘体。通过激光闪光法(基于jis r1611)测定热扩散率和比热容量,计算烧结体的密度、热扩散率及比热容量的乘积,作为室温时的热导率。另外,基于jis r1601:2008制备强度测定用的试验片,测定室温时的3点弯曲强度。测定结果以实施例1的测定值为基准,以相对值示于表1中。
58.(实施例2~8、比较例1~3)
59.以1~5小时的期间对前处理时金属硅粉末在混酸中的浸渍时间进行变更,如表1所示,改变硅粉末的氧浓度及将后处理中使用的氢氟酸的浓度(氟化氢的浓度)按照表1的方式变更,除此以外,以与实施例1同样的方式制备氮化硅粉末。在实施例4~8中,将前处理时金属硅粉末在混酸中浸渍时间设为与实施例1相同的2小时。在实施例2、3中,将其浸渍时间分别设为3小时、5小时。在比较例1~3中,将其浸渍时间设为1小时。以与实施例1同样的方式,求出各实施例及各比较例的表面氧量及内部氧量。另外,求出表面氧量相对于内部氧量之比(在表1中表示为“表面/内部”)。结果如表1所示。
60.以与实施例1同样的方式,使用氮化硅粉末制备氮化硅烧结体并进行评价。测定结果作为以实施例1的测定值为基准的相对值而示于表1。
61.[表1]
[0062][0063]
产业上的可利用性
[0064]
根据本公开文本,可提供能够制得具有高热导率的氮化硅烧结体的氮化硅粉末及其制造方法。另外,可提供具有高热导率的氮化硅烧结体的制造方法。
再多了解一些
本文用于企业家、创业者技术爱好者查询,结果仅供参考。