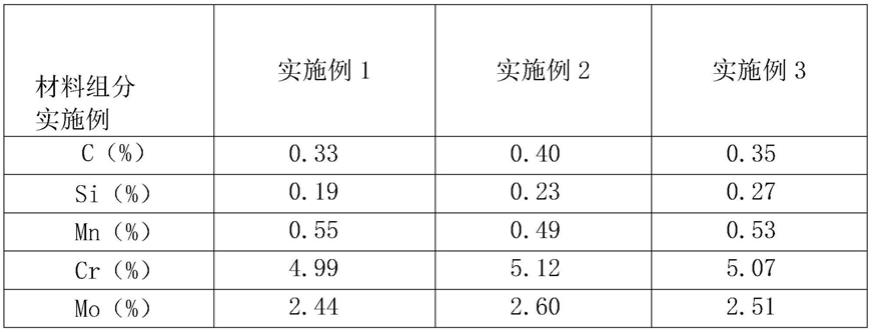
1.本发明涉及模具钢技术领域,具体为一种耐高温和高韧性的热作模具钢及其生产工艺。
背景技术:
2.热作模具钢主要是指对金属进行热变形加工的模具用的合金工具钢,如热锻模、热挤压模、压铸模、热镦模等。由于热作模具长时间处于高温高压条件下工作,因此,要求模具材料具有高的强度、硬度及热稳定性,特别是应有高热强性、热疲劳性、韧性等性能。模具加工成型具有生产效率高、质量好、节约材料和成本低等一系列优点,应用范围及其广泛,热作模具钢是指适宜于对镁铝等金属进行热变形加工的模具所用的合金钢,如热锻模、热挤压模、压铸模等。目前,热作模具正在向大型、精密、长寿命的方向发展,对热作模具钢的性能提出了更高的要求。
3.h13钢在600℃以下工作,具有良好的热稳定性和抗热疲劳性能,较好的强韧性结合,但在600℃以上,材料的强度和热稳定性急剧下降,失去了原来的优异性能。而高耐热性的h21钢在高温条件下抗热疲劳性能较差,模具常常因发生龟裂纹而失效,这大大降低了模具的使用寿命,增加了生产成本。因此,为了提高模具钢的耐高温性能和韧性,使得制备后的产品有较好的组织性能和力学性能更好地适应现代生产对高端模具的要求,本发明提出了一种耐高温和高韧性的热作模具钢及其生产工艺。
技术实现要素:
4.本发明的目的是为了解决现有技术中存在的缺点,而提出的一种耐高温和高韧性的热作模具钢及其生产工艺。
5.为了实现上述目的,本发明采用了如下技术方案:
6.一种耐高温和高韧性的热作模具钢,所述的热作模具钢由如下重量百分比的成分组成:c:0.31~0.42%;si:0.17~0.28%;mn:0.40~0.60%;cr:4.90~5.15%;mo:2.40~2.65%;v:0.55~0.60%;ni:0.20~0.35%;p≤0.01%;s≤0.003%;cu≤0.10%;[h]≤1.5ppm;[o]≤18ppm;[n]≤75ppm;fe余量。
[0007]
优选的,包括以下步骤:
[0008]
s1电炉冶炼、精炼、真空脱气、二次真空脱气:将重量百分比为c:0.31~0.42%;si:0.17~0.28%;mn:0.40~0.60%;cr:4.90~5.15%;mo:2.40~2.65%;v:0.55~0.60%;ni:0.20~0.35%;p≤0.01%;s≤0.003%;cu≤0.10%;[h]≤1.5ppm;[o]≤18ppm;[n]≤75ppm;fe余量的钢料放入电炉中冶炼成钢水,再将制成的钢水放入精炼炉中精炼,最后在vd钢包精炼炉内对钢水进行真空脱气与二次真空脱气处理;
[0009]
s2浇注φ520mm(平均直径)自耗电极:将s1步骤中进行二次真空脱气处理后的钢水浇注到模具内,冷却成型后得到平均直径为520mm的自耗电极电极坯,浇注过程中采用氩气保护浇注并使用封闭式氩气保护罩;
[0010]
s3退火:自耗电极电极坯再结晶退火;
[0011]
s4锯切冒口:切割掉s3步骤中自耗电极电极坯的冒口和浇道制得自耗电极;
[0012]
s5电极焊接:将s4步骤中的自耗电极抛光至见金属色,然后将假电极与自耗电极焊接;
[0013]
s6电渣重熔φ710mm(平均直径)锭:对自耗电极进行电渣重熔,得到钢锭;
[0014]
s7高温锻造均质化:对s6步骤中的钢锭进行高温锻造加工,形成一均质化锻件;
[0015]
s8锻后球化退火:对s7步骤中的锻件进行球化退火处理;
[0016]
s9判切:对s8步骤中的锻件切割取样,用于检验;
[0017]
s10超细化处理:对s8步骤中的锻件进行超细化处理;
[0018]
s11精整、探伤、检验:对锻件进行表面精整加工后进行喷丸处理,通过ut检测锻件内部缺陷,最后对锻件进行理化检验和尺寸检验;
[0019]
s12入库:检验合格后入库并登记。
[0020]
优选的,所述s1的电炉冶炼步骤中:
[0021]
s101在钢料的熔化期氧气压力控制在0.42~0.55mpa,保持温度≥1561℃,并配[mo]至下限;
[0022]
s102氧化期氧气压力控制在0.61~0.79mpa,吹氧氧化脱碳去磷;
[0023]
s103氧化期末加90kg si
‑
mn合金或c
‑
mn合金,钢水净沸腾时间≥5.5min;
[0024]
s104当满足温度大于1650℃,磷含量≤0.001%的条件时,进行拉渣;
[0025]
s105加稀薄渣料295kg的cao和75kg的caf2推渣化匀;
[0026]
s106开出电炉炉体加fecr;
[0027]
s107吹氧化铬,要求氧压≥0.85mpa;
[0028]
s108预还原:飘入fe
‑
si粉3.5
‑
5.5kg/t钢,至渣转色变稀;
[0029]
s109插入al 0.48kg/t,补加稀薄渣料520kg cao和105kg caf2,推渣均匀加c
‑
si粉和c
‑
al粉各3.5
‑
5.5kg/t还原造白渣;
[0030]
s110调整[c]、[mn]、[cr]、[mo]、[ni]的含量;
[0031]
s111当满足温度≥1620℃,渣况转白,合金加入时间≥8.5分钟,钢包中加al 1.1kg/t后出钢。
[0032]
优选的,所述s1的精炼步骤中:
[0033]
s112加热精炼炉,并加渣料cao 495kg、caf
2 75kg和c
‑
si粉还原调整渣系,总体渣量按出钢量的5%控制;
[0034]
s113当温度满足≥1570℃且渣白时,加入[v]调整成份,取样分析;
[0035]
s114当温度满足≥1650℃,白渣时间≥30min时,加入火砖块2.2~3.1kg/t调整好炉渣流动性,喂al线。
[0036]
优选的,所述s1的真空脱气、二次真空脱气步骤中:vd钢包精炼炉内真空度达66pa,保真空时间≥18min,[h]≤1.5ppm、[n]≤60ppm,二次真空脱气处理12分钟,二次真空脱气后镇静软吹氩时间15~30分钟。
[0037]
优选的,所述假电极的直径为299mm,假电极与自耗电极之间的焊缝有效高度≥32mm,其采用er50
‑
6的焊丝焊接,所述焊缝的上下两端分别设有上引弧板和下引弧板,所述下引弧板采用外圆直径为820mm且厚为10mm的q235板,所述上引弧板采用尺寸≥300*300mm
且厚度≥15mm的一块与自耗电极同钢种钢板,引弧时间85min;11hz加渣25min,16hz至加渣结束,加渣时间50min;自耗电极重量到达390kg时进入补缩,剩余35kg时结束熔炼,熔化率7.5kg/min,补缩时间65
‑
85min;冷却:模冷100分钟,扣罩缓冷≤3.5天;冷却后脱罩割除引弧板。
[0038]
优选的,所述s2中的液相线温度为1490℃,模具的模温控制在40~60℃,浇注过热度控制在45~55℃。
[0039]
本发明的有益效果是:本发明中优化了热作模具钢的原料配占比,使得钢的纯净度提高,进而使得制备的模具钢具有优异的硬度、耐高温形成和高韧性,在电炉冶炼、精炼、真空脱气和二次真空脱气步骤中,将c、mn、cr、si、v、mo以及ni等元素的含量限制在精准的调控范围内,真空脱气和二次真空脱气进一步降低了钢液中n、h、o气体元素含量,mo、cr碳化物的细小析出相在使用过程中起着弥散强化作用,提高了材料的性能,使材料具有高韧性,v可细化组织晶粒,提高强度和韧性,同时利用mo元素对模具钢的铁素体产生固溶强化作用,同时也提高碳化物的稳定性,从而提高钢的强度,改善了钢的延展性和韧性,通过ni元素的加入来提升模具钢的淬透性,保证固溶冷却后得到马氏体组织,细化铁元素体晶粒,在强度相同的条件下,提高钢的韧性,本发明相比常规的热作系列模具钢相比提高了耐高温性能和抗回火性能。
附图说明
[0040]
图1为本发明的生产工艺的流程框图。
具体实施方式
[0041]
以下是本发明的具体实施例,并说明对本发明的技术方案作进一步的描述,但本发明并不限于这些实施例。
[0042]
实施例1
‑
3,其中热作模具钢由如下重量百分比的成分组成:c:0.31~0.42%;si:0.17~0.28%;mn:0.40~0.60%;cr:4.90~5.15%;mo:2.40~2.65%;v:0.55~0.60%;ni:0.20~0.35%;p≤0.01%;s≤0.003%;cu≤0.10%;[h]≤1.5ppm;[o]≤18ppm;[n]≤75ppm;fe余量。
[0043]
实施例1
‑
3中材料组分如表1所示:
[0044]
表1:材料组分
[0045]
[0046][0047]
实施例1的生产工艺,包括以下步骤:
[0048]
s1电炉冶炼、精炼、真空脱气、二次真空脱气:取表1中实施例1材料组分的钢料放入电炉中冶炼成钢水,再将制成的钢水放入精炼炉中精炼,最后在vd钢包精炼炉内对钢水进行真空脱气与二次真空脱气处理;
[0049]
s1的电炉冶炼步骤中:s101在钢料的熔化期氧气压力控制在0.42~0.55mpa,保持温度≥1561℃,并配[mo]至下限;
[0050]
s102氧化期氧气压力控制在0.61~0.79mpa,吹氧氧化脱碳去磷;
[0051]
s103氧化期末加90kg si
‑
mn合金或c
‑
mn合金,钢水净沸腾时间≥5.5min;
[0052]
s104当满足温度大于1650℃,磷含量≤0.001%的条件时,进行拉渣;
[0053]
s105加稀薄渣料295kg的cao和75kg的caf2推渣化匀;
[0054]
s106开出电炉炉体加fecr;
[0055]
s107吹氧化铬,要求氧压≥0.85mpa;
[0056]
s108预还原:飘入fe
‑
si粉3.5
‑
5.5kg/t钢,至渣转色变稀;
[0057]
s109插入al 0.48kg/t,补加稀薄渣料520kg cao和105kg caf2,推渣均匀加c
‑
si粉和c
‑
al粉各3.5
‑
5.5kg/t还原造白渣;
[0058]
s110调整[c]、[mn]、[cr]、[mo]、[ni]的含量;
[0059]
s111当满足温度≥1620℃,渣况转白,合金加入时间≥8.5分钟,钢包中加al 1.1kg/t后出钢;
[0060]
s1的精炼步骤中:s112加热精炼炉,并加渣料cao 495kg、caf
2 75kg和c
‑
si粉还原调整渣系,总体渣量按出钢量的5%控制;
[0061]
s113当温度满足≥1570℃且渣白时,加入[v]调整成份,取样分析;
[0062]
s114当温度满足≥1650℃,白渣时间≥30min时,加入火砖块2.2~3.1kg/t调整好炉渣流动性,喂al线;
[0063]
s1的真空脱气、二次真空脱气步骤中:vd钢包精炼炉内真空度达66pa,保真空时间≥18min,[h]≤1.5ppm、[n]≤60ppm,二次真空脱气处理12分钟,二次真空脱气后镇静软吹氩时间15~30分钟;
[0064]
s2浇注φ520mm(平均直径)自耗电极:将s1步骤中进行二次真空脱气处理后的钢水浇注到模具内,冷却成型后得到平均直径为520mm的自耗电极电极坯,浇注过程中采用氩气保护浇注并使用封闭式氩气保护罩;液相线温度为1490℃,模具的模温控制在40~60℃,
浇注过热度控制在45~55℃;
[0065]
s3退火:自耗电极电极坯再结晶退火;
[0066]
s4锯切冒口:切割掉s3步骤中自耗电极电极坯的冒口和浇道制得自耗电极;
[0067]
s5电极焊接:将s4步骤中的自耗电极抛光至见金属色,然后将假电极与自耗电极焊接;假电极的直径为299mm,假电极与自耗电极之间的焊缝有效高度≥32mm,其采用er50
‑
6的焊丝焊接,焊缝的上下两端分别设有上引弧板和下引弧板,下引弧板采用外圆直径为820mm且厚为10mm的q235板,上引弧板采用尺寸350*350mm*25mm的一块与自耗电极同钢种钢板,引弧时间85min;11hz加渣25min,16hz至加渣结束,加渣时间50min;自耗电极重量到达390kg时进入补缩,剩余35kg时结束熔炼,熔化率7.5kg/min,补缩时间65
‑
85min;冷却:模冷100分钟,扣罩缓冷≤3.5天;冷却后脱罩割除引弧板;
[0068]
s6电渣重熔φ710mm(平均直径)锭:对自耗电极进行电渣重熔,得到钢锭;
[0069]
s7高温锻造均质化:对s6步骤中的钢锭进行高温锻造加工,形成一均质化锻件;
[0070]
s8锻后球化退火:对s7步骤中的锻件进行球化退火处理;
[0071]
s9判切:对s8步骤中的锻件切割取样,用于检验;
[0072]
s10超细化处理:对s8步骤中的锻件进行超细化处理;
[0073]
s11精整、探伤、检验:对锻件进行表面精整加工后进行喷丸处理,通过ut检测锻件内部缺陷,最后对锻件进行理化检验和尺寸检验;
[0074]
s12入库:检验合格后入库并登记。
[0075]
实施例2和实施例2的生产工艺类似于实施例的生产工艺。
[0076]
性能测试
[0077]
取实施例1、实施例2、实施例3的热作模具钢样品做硬度、屈服强度(常温和600℃)、冲击韧性、热疲劳性性能测试,同时与h13模具钢进行性能对比,对比结果如下:
[0078]
表2:实施例1
‑
3部分性能测试结果
[0079][0080]
表3:实施例1
‑
3热疲劳性能测试结果(主裂纹长度mm)
[0081][0082]
从中可以看出,本发明生产的耐高温和高韧性的热作模具钢的硬度、屈服强度、600℃屈服强度、冲击韧性(v口)和热疲劳性能均优于传统的h13钢种,具有优良的耐高温性能和抗回火性能,提升了我国模具制造水平和市场竞争力,满足客户的使用需求。
[0083]
尽管已经示出和描述了本发明的实施例,对于本领域的普通技术人员而言,可以理解在不脱离本发明的原理和精神的情况下可以对这些实施例进行多种变化、修改、替换和变型,本发明的范围由所附权利要求及其等同物限定。
再多了解一些
本文用于企业家、创业者技术爱好者查询,结果仅供参考。