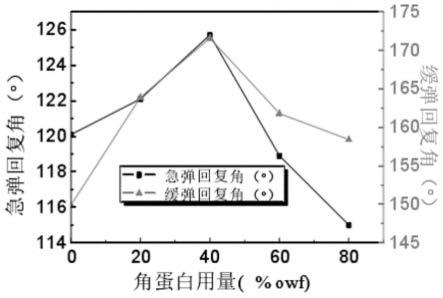
1.本发明属于纳米纤维功能型织物领域,具体涉及一种纳米纤维抗皱西服的生产工艺及应用,具体为运用静电纺丝技术与传统梳棉以及成纱装置相结合制备多功能纳米纤维纱线,然后对得到的纳米纤维纱线用羊毛角蛋白液和粘合剂的混合液进行抗皱处理,最后将得到的面料制成西服。
背景技术:
2.在功能性纺织品中,静电纺纳米纤维在聚合物和功能性材料的选择上具有较大的灵活性,同时具有高比表面积、高孔隙率等特点,因此负载能力更高,可应用于防护服、给药、创面敷料、过滤等功能性纺织品领域。远红外线是指波长范围为6-15μm的电磁波,其可以传入人体组织2-3
㎜
,与人体内分子形成共振效应,加剧分子运动,从而达到蓄热保暖、增强血液微循环和提高新陈代谢的作用,远红外纺织品可以吸收太阳光中的短波能量或人体散发的热量,并将其以远红外辐射方式作用于人体,在医疗保健、纺织品等领域具有广阔的应用前景。远红外辐射材料是影响纺织品远红外吸收和发射功能的关键因素,zro2常温远红外辐射率相对最高,对红外线的温度感应最强;al2o3作为过渡元素氧化物同样具有优异的远红外辐射性能,并且独特的结构赋予其优异的物理化学性质,在紫外线屏蔽、抗菌、光电材料等方面具有广阔的应用前景。将具有远红外辐射性能的zro2和al2o3纳米粒子添加到聚氨酯pu溶液中,通过静电纺丝装置将纳米纤维沉积在不断前进的棉线上,通过后续成纱工艺制备远红外/抗菌多功能纳米纤维纱线。
3.角蛋白是一种富含多种氨基酸和大量亲水性基团(如-nh2、-cooh等)的天然大分子蛋白质,具有良好的生物相容性、天然吸湿性及生物可降解性等特性,因此可用于纺织行业进行织物整理,赋予织物某种所需功能。另外角蛋白是含量最丰富的蛋白质之一,能够被自然界中的微生物降解,不会带来严重的环境污染,这反而拓宽了粗毛废料的回收利用,在缓解环境压力的同时也可以增加企业的经济效益,此外角蛋白这些特性使其在防治、生物医药、护肤化妆品、饲料及高分子材料等领域都表现出良好的应用前景。将提取出来的角蛋白溶液处理织物制备织物整理剂,不仅可以改善织物的某项性能,同时也可以降低整理后服装对皮肤的刺激性,达到对特异反应症、过敏性皮炎低刺激性的加工效果,是一种保健、舒适的加工方法。目前羊毛角蛋白主要应用于织物的亲水性整理、舒适性整理和负离子纤维制品加工等。通过适当的方法在织物表面引入大量的极性基团可以在一定程度上改善织物的服用性能,适量的角蛋白沉积在棉织物纤维间形成沉积交联,从而提高棉织物的折皱回复性。
技术实现要素:
4.为了解决上述问题,本发明提出了一种纳米纤维抗皱西服的生产工艺及应用,具体为运用静电纺丝技术与传统梳棉以及成纱装置相结合制备多功能纳米纤维纱线,然后对得到的纳米纤维纱线用羊毛角蛋白液和粘合剂的混合液进行抗皱处理,最后将得到的面料
制成西服,其特征在于,包括:
5.s1,取zro2和al2o3颗粒各0.5-1g于dmf:thf=1:1的混合溶剂中,磁力搅拌10min,将混合溶液置于超声清洗器中处理30-50min,得到分散均匀的纳米粒子分散液;
6.s2,在s1所得的混合溶液中加入2-3g pu颗粒,将zro2/al2o3/pu溶液在室温下搅拌6-12h,得到pu纺丝液,用改进的静电纺丝装置将抗菌纳米纤维沉积在向前移动的棉纤维网上,形成负载功能性纳米纤维的棉网,其中纺丝电压为15kv,纺丝接收距离为15cm,推注速度为0.08mm/min,接收速度为140r/min,再通过传统纺纱工艺制成远红外抗菌纳米纤维混纺纱;
7.s3,称取未经处理的粗毛15-30g,经清水洗涤后去除可溶性杂质后放5-7g/l的naoh溶液中超声30min以去除粗毛上的羊毛脂,然后将羊毛取出,用清水洗涤羊毛,取出残留的naoh避免对后续步骤产生影响;
8.s4,将s3中的羊毛洗涤完成后将粗毛弄成蓬松状态放入60-80℃烘箱中烘干至恒重;
9.s5,将s4中烘干后的粗毛剪碎成1cm放入到含有na2s2o3用量50%owf、尿素用量650%owf、sds用量5%owf的混合溶液中,80-100℃反应1-2h,每12h换一次蒸馏水,透析结束倒出透析袋内溶液于烧杯中,50-70℃真空干燥,研磨制得羊毛角蛋白粉;
10.s6,将织物剪成相应大小布条称重并放入有标号的烧杯中,往烧杯中加入羊毛角蛋白用量40%owf、粘合剂pa用量40%owf的混合溶液,混合溶液的浴比为1:20,将带有样品的烧杯放入超声波清洗机中超声30min,每2min搅拌一次以使得织物浸渍均匀;
11.s7,对s6中浸渍的织物进行浸轧处理,浸轧工艺为:在温度为50℃下浸渍60min,然后在100℃下预烘5min,然后在140℃下烘焙5min;
12.优选地,所述s1中选用的远红外辐射材料为zro2和al2o3;
13.优选地,所述s2中进行静电纺丝工艺的参数为纺丝电压为15kv,纺丝接收距离为15cm,推注速度为0.08mm/min,接收速度为140r/min;
14.优选地,所述s5中对羊毛角蛋白的提取使用的还原剂是na2s2o3;
15.优选地,所述s5中还原剂na2s2o3的用量为50%owf;
16.优选地,所述s5中尿素用量650%owf;
17.优选地,所述s6中羊毛角蛋白的用量为40%owf;
18.优选地,所述s6中粘合剂pa的用量为40%owf;
19.优选地,所述s7中的浸渍时间为60min;
20.优选地,所述s7中的浸渍温度为50℃。
21.应用本发明的有益效果在于:
22.1.通过在纺丝液中添加远红外辐射材料zro2和al2o3.通过静电纺丝技术与传统梳棉以及成纱装置相结合制备多功能纳米纤维纱线具有柔软、顺滑、透气性好等优点。本发明选用的远红外辐射材料为zro2和al2o3,远红外辐射材料是影响纺织品远红外吸收和发射功能的关键因素,zro2常温远红外辐射率相对最高,对红外线的温度感应最强,al2o3作为过渡元素氧化物同样具有优异的远红外辐射性能。本发明中对羊毛角蛋白的提取使用的还原剂是na2s2o3,粗毛比商品毛有更大的纤维直径、更高的结晶度和更加致密的显微结构而更难以溶解,只有采用更强的还原剂和更为强烈的反应条件才能高效提取粗毛中的角蛋白,还
原剂na2s2o3是一种还原性比nahso3强的还原剂,在一定条件下可以高效断裂粗毛中的二硫键从而达到高效提取粗毛中角蛋白的目的。本发明中在羊毛角蛋白的提取过程中尿素的存在可以促进羊毛纤维的溶胀过程从而促进还原剂进入羊毛纤维内部,加速了羊毛纤维中二硫键等各种化学键的断裂。
23.2.通过添加天然的大分子蛋白质羊毛角蛋白对面料进行抗皱处理,可以使制得的面料的抗皱性能得到提升,而且羊毛角蛋白具有良好的生物相容性,可降解,对环境十分友好。
24.3.本发明操作简单,可以批量生产。
附图说明
25.为了更清楚地说明本发明实施例中的技术方案,下面将对实施例或现有技术描述中所需要使用的附图作简单地介绍,显而易见地,下面描述中的附图仅仅是本发明的一些实施例,对于本领域普通技术人员来讲,在不付出创造性劳动性的前提下,还可以根据这些附图获得其他的附图。
26.图1为本发明实施例所制得的远红外抗菌纳米纤维混纺纱的sem图。
27.图2为本发明中实施例2和对比例1-4中角蛋白用量对棉织物性能的影响。
28.图3为本发明中实施例3和对比例5-8中粘合剂浓度对棉织物性能的影响。
29.图4为本发明中实施例4和对比例9-12中浸渍时间对棉织物性能的影响。
30.图5为本发明中实施例4和对比例13-15中浸渍温度对棉织物性能的影响。
具体实施方式
31.为了使本发明所要解决的技术问题、技术方案及有益效果更加清楚明白,以下结合附图及实施例,对本发明进行进一步详细说明。应当理解,此处所描述的具体实施例仅仅用以解释本发明,并不用于限定本发明。
32.实施例1
33.s1,取zro2和al2o3颗粒各0.5g于dmf:thf=1:1的混合溶剂中,磁力搅拌10min,将混合溶液置于超声清洗器中处理30min,得到分散均匀的纳米粒子分散液;
34.s2,在s1所得的混合溶液中加入2g pu颗粒,将zro2/al2o3/pu溶液在室温下搅拌6h,得到pu纺丝液,用改进的静电纺丝装置将抗菌纳米纤维沉积在向前移动的棉纤维网上,形成负载功能性纳米纤维的棉网,其中纺丝电压为15kv,纺丝接收距离为15cm,推注速度为0.08mm/min,接收速度为140r/min,再通过传统纺纱工艺制成远红外抗菌纳米纤维混纺纱;
35.s3,称取未经处理的粗毛15g,经清水洗涤后去除可溶性杂质后放5g/l的naoh溶液中超声30min以去除粗毛上的羊毛脂,然后将羊毛取出,用清水洗涤羊毛,取出残留的naoh避免对后续步骤产生影响;
36.s4,将s3中的羊毛洗涤完成后将粗毛弄成蓬松状态放入60℃烘箱中烘干至恒重;
37.s5,将s4中烘干后的粗毛剪碎成1cm放入到含有na2s2o3用量50%owf、尿素用量650%owf、sds用量5%owf的混合溶液中,80℃反应1h,每12h换一次蒸馏水,透析结束倒出透析袋内溶液于烧杯中,50℃真空干燥,研磨制得羊毛角蛋白粉;
38.s6,将织物剪成相应大小布条称重并放入有标号的烧杯中,往烧杯中加入羊毛角
蛋白用量40%owf、粘合剂pa用量40%owf的混合溶液,混合溶液的浴比为1:20,将带有样品的烧杯放入超声波清洗机中超声30min,每2min搅拌一次以使得织物浸渍均匀;
39.s7,对s6中浸渍的织物进行浸轧处理,浸轧工艺为:在温度为50℃下浸渍60min,然后在100℃下预烘5min,然后在140℃下烘焙5min;
40.本发明选用的远红外辐射材料为zro2和al2o3,远红外辐射材料是影响纺织品远红外吸收和发射功能的关键因素,zro2常温远红外辐射率相对最高,对红外线的温度感应最强,al2o3作为过渡元素氧化物同样具有优异的远红外辐射性能。
41.本发明中对羊毛角蛋白的提取使用的还原剂是na2s2o3,粗毛比商品毛有更大的纤维直径、更高的结晶度和更加致密的显微结构而更难以溶解,只有采用更强的还原剂和更为强烈的反应条件才能高效提取粗毛中的角蛋白,还原剂na2s2o3是一种还原性比nahso3强的还原剂,在一定条件下可以高效断裂粗毛中的二硫键从而达到高效提取粗毛中角蛋白的目的。
42.本发明中在羊毛角蛋白的提取过程中尿素的存在可以促进羊毛纤维的溶胀过程从而促进还原剂进入羊毛纤维内部,加速了羊毛纤维中二硫键等各种化学键的断裂。
43.本发明通过静电纺丝技术将远红外抗菌纳米纤维沉积在棉纤维表面,生产远红外抗菌纳米纤维混纺纱,并将其加工成具有远红外抗菌功能的织物,随后用羊毛角蛋白对织物进行抗皱处理。利用电子显微镜观察纳米纤维在棉纱中的分布情况,如图1所示,zro2和al2o3相互协同使得制得的纳米纤维粗细均匀,能够更好地与羊毛角蛋白结合,制得的织物平整光滑,zro2/al2o3/pu纳米纤维均匀分布在棉纤维中,通过加捻形成相互缠绕的紧密结构,保证了功能粒子在纱线上的高效稳定负载。
44.实施例2
45.s1,取zro2和al2o3颗粒各0.7g于dmf:thf=1:1的混合溶剂中,磁力搅拌10min,将混合溶液置于超声清洗器中处理40min,得到分散均匀的纳米粒子分散液;
46.s2,在s1所得的混合溶液中加入2.5g pu颗粒,将zro2/al2o3/pu溶液在室温下搅拌8h,得到pu纺丝液,用改进的静电纺丝装置将抗菌纳米纤维沉积在向前移动的棉纤维网上,形成负载功能性纳米纤维的棉网,其中纺丝电压为15kv,纺丝接收距离为15cm,推注速度为0.08mm/min,接收速度为140r/min,再通过传统纺纱工艺制成远红外抗菌纳米纤维混纺纱;
47.s3,称取未经处理的粗毛20g,经清水洗涤后去除可溶性杂质后放6g/l的naoh溶液中超声30min以去除粗毛上的羊毛脂,然后将羊毛取出,用清水洗涤羊毛,取出残留的naoh避免对后续步骤产生影响;
48.s4,将s3中的羊毛洗涤完成后将粗毛弄成蓬松状态放入65℃烘箱中烘干至恒重;
49.s5,将s4中烘干后的粗毛剪碎成1cm放入到含有na2s2o3用量50%owf、尿素用量650%owf、sds用量5%owf的混合溶液中,85℃反应1.5h,每12h换一次蒸馏水,透析结束倒出透析袋内溶液于烧杯中,60℃真空干燥,研磨制得羊毛角蛋白粉;
50.s6,将织物剪成相应大小布条称重并放入有标号的烧杯中,往烧杯中加入羊毛角蛋白用量40%owf、粘合剂pa用量40%owf的混合溶液,混合溶液的浴比为1:20,将带有样品的烧杯放入超声波清洗机中超声30min,每2min搅拌一次以使得织物浸渍均匀;
51.s7,对s6中浸渍的织物进行浸轧处理,浸轧工艺为:在温度为50℃下浸渍60min,然后在100℃下预烘5min,然后在140℃下烘焙5min;
52.对比例1除步骤s6中羊毛角蛋白的用量为0外,其余各步骤均与实施例2相同。
53.对比例2除步骤s6中羊毛角蛋白的用量为20%owf外,其余各步骤均与实施例2相同。
54.对比例3除步骤s6中羊毛角蛋白的用量为60%owf外,其余各步骤均与实施例2相同。
55.对比例4除步骤s6中羊毛角蛋白的用量为80%owf外,其余各步骤均与实施例2相同。
56.表1角蛋白用量对棉织物性能的影响
[0057][0058][0059]
从图2中可以看出不同角蛋白用量整理后的棉织物的急弹回复角和缓弹回复角均随角蛋白用量的增加而逐渐增加,多次实验表明在角蛋白用量为40%owf时达到最大值,而后随着角蛋白含量的继续增加棉织物的急弹回复角和缓弹回复角随角蛋白的用量的增加而逐渐降低。主要原因是角蛋白用量的增加有利于角蛋白在棉织物中的沉积,角蛋白出现在棉纤维之间时会携带大量的极性基团(-oh、——cooh、—nh2等)进入到棉织物内部,这些极性基团可以与棉纤维中的极性基团形成形成氢键和范德华力的作用形成沉积交联,进而阻碍了织物在发生折皱的过程中棉纤维间的相对滑移,棉织物的折皱回复性有所改善,而当角蛋白含量太高时,大部分角蛋白只能吸附在纤维表面不利于角蛋白分子沉积交联,造成棉织物的折皱回复性有所降低。
[0060]
实施例3
[0061]
s1,取zro2和al2o3颗粒各0.8g于dmf:thf=1:1的混合溶剂中,磁力搅拌10min,将混合溶液置于超声清洗器中处理45min,得到分散均匀的纳米粒子分散液;
[0062]
s2,在s1所得的混合溶液中加入3g pu颗粒,将zro2/al2o3/pu溶液在室温下搅拌10h,得到pu纺丝液,用改进的静电纺丝装置将抗菌纳米纤维沉积在向前移动的棉纤维网上,形成负载功能性纳米纤维的棉网,其中纺丝电压为15kv,纺丝接收距离为15cm,推注速度为0.08mm/min,接收速度为140r/min,再通过传统纺纱工艺制成远红外抗菌纳米纤维混纺纱;
[0063]
s3,称取未经处理的粗毛25g,经清水洗涤后去除可溶性杂质后放7g/l的naoh溶液中超声30min以去除粗毛上的羊毛脂,然后将羊毛取出,用清水洗涤羊毛,取出残留的naoh避免对后续步骤产生影响;
[0064]
s4,将s3中的羊毛洗涤完成后将粗毛弄成蓬松状态放入70℃烘箱中烘干至恒重;
[0065]
s5,将s4中烘干后的粗毛剪碎成1cm放入到含有na2s2o3用量50%owf、尿素用量
650%owf、sds用量5%owf的混合溶液中,90℃反应2h,每12h换一次蒸馏水,透析结束倒出透析袋内溶液于烧杯中,65℃真空干燥,研磨制得羊毛角蛋白粉;
[0066]
s6,将织物剪成相应大小布条称重并放入有标号的烧杯中,往烧杯中加入羊毛角蛋白用量40%owf、粘合剂pa用量40%owf的混合溶液,混合溶液的浴比为1:20,将带有样品的烧杯放入超声波清洗机中超声30min,每2min搅拌一次以使得织物浸渍均匀;
[0067]
s7,对s6中浸渍的织物进行浸轧处理,浸轧工艺为:在温度为50℃下浸渍60min,然后在100℃下预烘5min,然后在140℃下烘焙5min;
[0068]
对比例5除步骤s6中粘合剂的用量为0外,其余各步骤均与实施例3相同。
[0069]
对比例6除步骤s6中粘合剂的用量为20%owf外,其余各步骤均与实施例3相同。
[0070]
对比例7除步骤s6中粘合剂的用量为60%owf外,其余各步骤均与实施例3相同。
[0071]
对比例8除步骤s6中粘合剂的用量为80%owf外,其余各步骤均与实施例3相同。
[0072]
表2粘合剂浓度对棉织物性能的影响
[0073][0074][0075]
由图3可得添加不同用量粘合剂整理后的棉织物急弹回复角和缓弹回复角均随着粘合剂用量的增加而逐渐增加,多次实验表明在粘合剂用量为40%owf时达到最大值,而后棉织物的急弹回复角和缓弹回复角随着粘合剂的用量的增加而逐渐降低,其原因可能是粘合剂可以在棉织物表面形成一层致密的薄膜,薄膜的存在使棉织物中纤维表面及纤维间的发生沉积交联的角蛋白的位置相对固定,进而阻碍了织物在发生折皱的过程中棉纤维间的相对滑移,棉织物的折皱回复性有所改善,但随着粘合剂用量的继续增加,会使织物变得越来越厚实,折皱形成后会阻碍织物的折皱回复过程,使其也更难以恢复到原来的状态,进而影响棉织物的折皱回复性。
[0076]
实施例4
[0077]
s1,取zro2和al2o3颗粒各1g于dmf:thf=1:1的混合溶剂中,磁力搅拌10min,将混合溶液置于超声清洗器中处理50min,得到分散均匀的纳米粒子分散液;
[0078]
s2,在s1所得的混合溶液中加入3g pu颗粒,将zro2/al2o3/pu溶液在室温下搅拌12h,得到pu纺丝液,用改进的静电纺丝装置将抗菌纳米纤维沉积在向前移动的棉纤维网上,形成负载功能性纳米纤维的棉网,其中纺丝电压为15kv,纺丝接收距离为15cm,推注速度为0.08mm/min,接收速度为140r/min,再通过传统纺纱工艺制成远红外抗菌纳米纤维混纺纱;
[0079]
s3,称取未经处理的粗毛30g,经清水洗涤后去除可溶性杂质后放7g/l的naoh溶液中超声30min以去除粗毛上的羊毛脂,然后将羊毛取出,用清水洗涤羊毛,取出残留的naoh
避免对后续步骤产生影响;
[0080]
s4,将s3中的羊毛洗涤完成后将粗毛弄成蓬松状态放入80℃烘箱中烘干至恒重;
[0081]
s5,将s4中烘干后的粗毛剪碎成1cm放入到含有na2s2o3用量50%owf、尿素用量650%owf、sds用量5%owf的混合溶液中,100℃反应2h,每12h换一次蒸馏水,透析结束倒出透析袋内溶液于烧杯中,70℃真空干燥,研磨制得羊毛角蛋白粉;
[0082]
s6,将织物剪成相应大小布条称重并放入有标号的烧杯中,往烧杯中加入羊毛角蛋白用量40%owf、粘合剂pa用量40%owf的混合溶液,混合溶液的浴比为1:20,将带有样品的烧杯放入超声波清洗机中超声30min,每2min搅拌一次以使得织物浸渍均匀;
[0083]
s7,对s6中浸渍的织物进行浸轧处理,浸轧工艺为:在温度为50℃下浸渍60min,然后在100℃下预烘5min,然后在140℃下烘焙5min;
[0084]
对比例9除步骤s6中浸渍时间为0min外,其余各步骤均与实施例4相同。
[0085]
对比例10除步骤s6中浸渍时间为30min外,其余各步骤均与实施例4相同。对比例11除步骤s6中浸渍时间为90min外,其余各步骤均与实施例4相同。对比例12除步骤s6中浸渍时间为120min外,其余各步骤均与实施例4相同。
[0086]
表3浸渍时间对棉织物性能的影响
[0087][0088]
由图4可得浸渍时间较短时棉织物的急弹回复角和缓弹回复角随着浸渍时间的增加而逐渐增加,多次实验表明在浸渍时间为60min时增加量是最大的而后随着浸渍时间的增加而趋于稳定。其原因是随着浸渍时间的不断延长,棉织物对角蛋白的吸附也变得越来越充分,角蛋白在棉织物内部的沉积交联也会变得更加充分,在浸渍时间为60min时棉织物的急弹回复角和缓弹回复角增加量达到最大,而后随着浸渍时间的不断增加棉织物的急弹回复角和缓弹回复角趋于稳定,这说明当棉织物对角蛋白的吸附达到饱和后再继续增加浸渍时间并不能增加角蛋白在在织物内部的沉积,也不会对角蛋白在织物内部的交联状况产生较大影响,因此棉织物的折皱回复性不在发生变化,综合考虑棉织物抗皱整理过程中角蛋白溶液的浸渍时间为60min。
[0089]
对比例13除步骤s6中浸渍温度为30℃外,其余各步骤均与实施例4相同。
[0090]
对比例14除步骤s6中浸渍温度为40℃外,其余各步骤均与实施例4相同。
[0091]
对比例15除步骤s6中浸渍温度为60℃外,其余各步骤均与实施例4相同。
[0092]
表4浸渍温度对棉织物性能的影响
[0093][0094]
由图5可知,角蛋白对棉织物的抗皱整理过程中浸渍温度对棉织物的折皱回复性有较大的影响。浸渍温度较低时,棉织物的急弹回复角和缓弹回复角随浸渍温度的增加而逐渐增加,多次实验表明在浸渍温度为50℃时达到最大值,而后随着浸渍温度的逐渐增加而降低。其主要原因是浸渍温度的不断增加整理液中各物质的分子运动也在不断加剧,在浸渍过程中向织物内部的扩散也越来越快,角蛋白在棉织物内部的沉积交联过程也越来越快,因此随着浸渍温度的增加棉织物的折皱回复性逐渐改善,棉织物的急弹回复角和缓弹回复角逐渐增加,在浸渍温度为50℃时达到最大值,但浸渍温度过高反而不利于角蛋白在棉织物内部的沉积交联过程,因此此时浸渍温度的逐渐增加棉织物的折皱回复性也随之下降,急弹回复角和缓弹回复角也逐渐减小,综合考虑棉织物抗皱整理过程中角蛋白溶液的浸渍温度为50℃。
[0095]
最后应说明的是:以上所述的各实施例仅用于说明本发明技术方案,而非对其限制;尽管参照前述实施例对本发明进行了详细的说明,本领域的普通技术人员应当理解:其依然可以对前述实施例所记载的技术方案进行修改,或者对其中部分或全部技术特征进行等同替换;而这些修改或替换,并不使相应技术方案的本质脱离本发明各实施例技术方案的范围。
再多了解一些
本文用于创业者技术爱好者查询,仅供学习研究,如用于商业用途,请联系技术所有人。