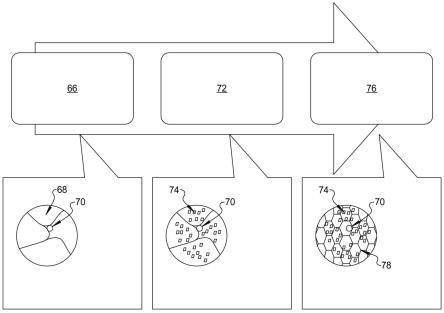
1.本公开涉及包括汽车车轮的锻造和旋压成型制品。
背景技术:
2.当前用于形成汽车车辆合金车轮的工艺包括铸造含镁金属锭、挤压镁坯料、从挤压坯料锻坯、对坯料进行旋压成型和预加工以及进行最终机加工操作,例如完成轮毂直径、轮辐和凸耳孔。铝材料也常用于汽车车轮,因为其在旋压成型工艺中的固有成型性非常好,无需预挤压。
3.镁合金材料,例如包含镁-锌-锆合金的zk30也可用作上述用途,并具有优异的成形性,但由于添加了锆(zr)材料以提高旋压成型的可成形性,因此成本很高。所以zk30目前仅限于利基市场使用。与zk30合金相比,已知的不含锆的材料例如包含镁-铝-锌合金的az80价格不贵,但是在锻造后的旋压成型过程中存在成形性不足和开裂的问题。az80合金的低成形性导致其无法在汽车车轮应用的大规模生产过程中使用。
4.因此,虽然现有的铝和镁锌锆合金材料达到了其预期目的,仍需要一种新型改进的系统和方法来形成轴对称制品,如汽车车轮。
技术实现要素:
5.根据若干方面,一种形成镁制品的方法包括:在炉中加热包括镁、铝、锰和锡在内的材料以形成具有以下成分的合金;含量大于或等于材料重量的90%的镁;含量占材料重量的约2.0%至约4.0%的铝;含量占材料重量的约0.43%至约0.6%的锰;含量占材料重量的约1%至约3%的锡;冷铸所述合金以形成铸坯;在约380℃至约420℃的温度范围内加热所述铸坯并保温约4小时至10小时以使元素分布均匀。
6.在本公开的另一方面,所述方法进一步包括以单步或多步锻造操作锻造所述铸坯以形成锻坯;以及对所述锻坯进行旋压成型以形成限定预加工坯料的最终形状。
7.在本公开的另一方面,所述方法进一步包括锻造所述铸坯时,锻造温度保持在约350℃至450℃。
8.在本公开的另一方面,所述方法进一步包括在约300℃至约450℃的温度范围内挤压铸坯,挤压比为约2到约10,以改进所述铸坯的成形性。
9.在本公开的另一方面,所述方法进一步包括锻造挤压后的坯料时,锻造温度保持在约350℃至450℃。
10.在本公开的另一方面,所述方法进一步包括进行旋压成型之前,将所述锻坯加热到约300℃至420℃。
11.在本公开的另一方面,所述方法进一步包括在工作温度约为0℃至100℃的范围内,对旋压成型后的所述加热锻坯进行淬火。
12.在本公开的另一方面,方法进一步包括在约150℃至200℃的温度下,对旋压成型后的所述加热锻坯进行2小时至20小时的时效处理。
13.在本公开的另一方面,所述方法进一步包括对所述预加工坯料进行精加工以形成预期产品,如轴对称镁制品。
14.在本公开的另一方面,所述方法进一步包括锻造所述铸坯时,锻造出限定具有周向轮辋的锻坯的轮毂和多个轮辐。
15.根据若干方面,一种通过锻造和旋压成型形成轴对称镁制品的方法包括:在铸造过程中熔炼包括镁(mg)、铝(al)、锰(mn)和锡(sn)的多种材料;将铸造过程中的多种材料凝固成铸锭;对铸锭进行热处理,温度约为400℃,时间约为5小时,以使al/mn纳米颗粒从镁基体中析出;将经过热处理的铸锭锻造成锻坯;并将所述锻坯旋压成型制成预加工坯料。
16.在本公开的另一方面,所述方法进一步包括通过在约300℃至约420℃的温度范围内进行旋压成型,将sn溶解到mg基体中。
17.在本公开的另一方面,所述方法进一步包括通过在旋压成型后进行淬火使部分sn过饱和进入镁基体。
18.在本公开的另一方面,所述方法进一步包括对淬火后的旋压成型坯料进行2至20小时的时效处理,温度为150℃至200℃,以使mg/mn颗粒沉淀来提高强度。
19.在本公开的另一方面,所述方法进一步包括将重量小于3%的锌(zn)添加到熔体中。
20.在本公开的另一方面,所述方法进一步包括按材料的以下重量添加材料:含量大于或等于材料重量的90%的镁;含量约占材料重量的2.0%至约4.0%的铝;含量约占材料重量的0.43%至0.6%的锰。
21.根据若干方面,一种汽车车辆轴对称镁制品,包括:镁(mg)、铝(al)、锰(mn)、锡(sn)多种材料;含量大于或等于材料重量的90%的镁;含量约占材料重量的2.0%至约4.0%的铝;含量约占材料重量的0.43%至约0.6%的锰;含量约占材料重量的1.0%至约3.0%的锡;从镁基体中析出的多个al/mn纳米颗粒,此多个纳米颗粒细化了多个动态再结晶晶粒,并抑制了动态再结晶晶粒的生长。
22.在本公开的另一方面,将轮辋预热到约300℃到420℃之后,对其进行旋压成型。
23.在本公开的另一方面,汽车车轮包括由所述预加工坯料加工而成的周向轮辋。
24.在本公开的另一方面,辊压成型后周向轮辋中drx晶粒的平均等效直径比外侧凸缘中的drx晶粒的平均等效直径小10%以上。所述周向轮辋中动态再结晶晶粒的平均等效直径小于10μm。
25.根据本文的描述,其它适用领域将变得明显。应当理解,描述和具体示例仅用于说明目的,并不用于限制本公开的范围。
附图说明
26.在此描述的附图仅用于说明目的,并不旨在以任何方式限制本公开的范围。
27.图1是根据示例性方面的形成轴对称制品的多个阶段的图解;
28.图2是形成图1所示物品的方法步骤的流程图;
29.图3是本发明合金的示例性晶粒间的晶界图;
30.图4是图1所示轴对称制品形成过程中的旋压成型步骤示意图;
31.图5是图1所示制品的材料和材料重量百分比表;以及
32.图6是本公开的形成阶段期间合金的微观结构(microstructure)演变图示。
具体实施方式
33.以下描述本质上仅是示例性的,并不旨在限制本公开、应用或用途。
34.参考图1,本公开的轴对称镁制品10形成于多个制品阶段,包括:第一制品阶段,限定通过mg-al-mn-sn材料合金的定向冷硬铸造形成的铸锭12。第二制品阶段,对铸锭12进行热处理以平滑形成mg-al-mn-sn材料合金的al-mn纳米颗粒,且元素分布均匀,以限定铸坯14。第三制品阶段,限定在锻造工位中以单步或多步锻造操作由铸坯14形成的锻坯16。锻坯16包括轮毂,轮辐和周向轮辋18。周向轮辋18比预期的整体车轮结构的轮辋的形状更厚且更窄。第四制品阶段,限定通过对锻坯16进行旋压成型的预加工坯料20。轴对称镁制品10限定了第五制品阶段,从预加工坯料产生成品和机加工制品,如精加工的并具有最终的轮辋形状的汽车车辆整体车轮结构20。
35.参考图2并再次参考图1,通过锻造和旋压成型形成图1所示的轴对称镁制品10的方法22包括第一工序24,包括在具有以下图5描述的成分的炉中熔炼镁-铝-锰-锡原料。第二工序26,对第一工序24中形成的熔炼材料进行冷铸以产生参照图1所示的铸坯14。第三工序28,随后加热铸坯14到约380℃至约420℃,并在锻造铸坯14之前保温约4至10小时之间的时间段以平滑形成mg-al-mn-sn材料合金的al-mn纳米颗粒,且元素分布均匀。
36.然后通过诸如机器人将铸坯14传送到锻造工位,在第四工序30中,预热的铸坯14在约350℃至约450℃的锻造温度下进行单步或多步锻造操作。锻造操作形成轮毂和轮辐,所述轮毂和轮辐限定了具有如图1所示的周向轮辋18的锻坯16。在第五工序32中,随后根据需要将锻坯16预热至约300℃至420℃之间的温度并进行旋压成型以形成限定预加工坯料20的最终形状,之后可将其从工作温度淬火至大约0℃至100℃,然后在大约150℃至200℃的温度下进行2至20小时的时效处理。随后对预加工的坯料20进行精加工以形成所需的物品,如轴对称镁制品10。
37.参考图3,材料图34确认了镁的固有特性是在晶界40处硬取向晶粒36和软取向晶粒38之间的变形不相容性。变形时,塑性应变将集中在软取向晶粒中38。作为携带变形应变的晶格缺陷,位错44会产生并堆积在晶界40处。在采用低应变率的热变形过程中,例如锻造过程,硬取向晶粒36在软取向晶粒38上或进入软取向晶粒38的晶界膨胀消除了堆积在晶界40处的位错44以降低相邻材料晶粒的不相容性,这降低了在晶界40处开裂的可能性。然而,在采用高应变率的热变形过程中,例如旋压成型过程,晶界运动可能会受到抑制,从而不存在晶界膨胀。如果不存在晶界膨胀,这种不相容性可能导致晶间开裂42,当合金中的铝含量高于预定的最大含量时,在旋压成型过程中已确认会出这种情况。
38.继续参考图3,影响晶界膨胀的微观结构特征包括:溶质和沉淀颗粒。根据若干方面,当合金中的al含量增加到4%以上时,镁基al溶质的拖曳效应显著阻碍了晶界的迁移;并且在晶界40处含有mg17al12颗粒的动态析出颗粒的钉扎效应也可能阻碍晶界40的移动。因此,需要调整合金中的al含量以避免al溶质的强拖曳效应和mg17al12颗粒的析出。
39.铝的添加可提高铸造性能和强度。根据若干方面,铝含量在2.0%-4.0%之间,以平衡晶界迁移率和铸造性能。
40.锡(sn)溶质对边界迁移率的拖曳作用较弱。因此,加入一定量的sn以提高合金的
铸造性能和强度,以弥补al含量的降低。在约300℃至452℃的温度范围内进行的旋压成型工艺中,sn可以溶解在mg基体中。通过淬火,sn可以在mg基体中过饱和。随后在150℃至200℃下进行2至20小时的时效处理中,mg-sn颗粒将析出以提高强度。为避免成本显著增加,sn的添加量控制在1%到3%的范围内。
41.与sn类似,锌(zn)溶质对边界迁移率的拖曳作用较弱。此外,当zn的添加量等于或小于3%时,有利于铸造熔体的流动性。由于固溶强化效应,锌的添加还将提高最终产品的强度性能。
42.虽然钙和稀土元素可能有助于改变微观结构的织构并提高成型性,但是钙和稀土元素往往偏析到晶界并对晶界运动有很强的拖曳作用。因此,本公开的合金基本上不含钙和稀土元素,其含量低于0.05%。
43.参考图4并再次参考图1和图2,形成图1的轴对称镁制品10的方法22进一步包括以下工艺。热处理后,转移锻坯16,例如使用机器人50转移到辊轧成型工位52。在辊轧成型期间,周向轮辋18定位在芯轴54上。辊子56在挤压方向58上移动以将压力施加到周向轮辋18,并且在成形方向60上进一步移动以将周向轮辋18滚轧成形为包括预加工坯料的外侧凸缘62的完整形式20。在本公开的过程中,仅轮辋部分发生变形。对于轮毂和外侧法兰等其他部分,保持在高温可能会导致微观结构的粗化,从而导致机械性能的下降。因此,提高了锻坯16微观结构的热稳定性,来避免微观结构的不良粗化。
44.本公开的合金在铸造66之后的热处理72期间产生大量的al-mn纳米颗粒74以提高新mg-al合金的热稳定性。al-mn纳米颗粒74有助于在锻造过程76中细化动态再结晶晶粒并抑制其生长,从而进一步促进晶界强化。通常在商品az80和az31合金中添加锰(mn),以中和铁(fe)对耐腐蚀性能的负面影响。在本公开的合金中,添加mn以生成大量的al-mn纳米颗粒以提高锻坯中微观结构的热稳定性。al-mn纳米颗粒74的体积大于az80中形成的类似颗粒,优选低铝和高锰。由于锰在镁中的溶解度有限,所以在铸造过程中难以对锰进行微合金化。因此,考虑到规模化生产的可加工性,目前合金中的锰含量限制在0.6%。添加高于0.6%含量的锰可能形成铸态微观结构中未溶解的含mn金属间粗颗粒70,不利于后续的成形过程和成品的塑性。
45.参考图5并再次参考图1和图2,表64提供了本公开的合金中按重量计算的材料数量的示例范围。如表64所示,镁含量约为重量的90%,甚至更高。根据若干方面,铝含量约为重量的2.0%至4.0%。根据进一步的方面,铝含量约为重量的2.5%至3.0%。根据若干方面,锰含量约为重量的0.43%至0.6%。根据进一步的方面,锰含量约为重量的0.45%至0.55%。根据若干方面,锡含量约为重量的1.0%至3.0%。根据进一步的方面,锡含量约为重量的1.5%至2.5%。根据若干方面,锌含量约为重量的0%至3.0%。根据进一步的方面,锌含量约为重量的0.5%至1/5%。
46.参考图6并再次参考图1至图5,为了使预加工坯料20保持良好的机械性能,锻坯16中的细晶粒微观结构需要具有良好的热稳定性。从图5中可以看出,为了使mg-al合金具有良好的旋压成型成形性,选择了铝重量小于4%的“贫”铝。在以上定义为第二工序26的铸造阶段66期间,形成过饱和含锰金属间化合物70的镁(mg)基体68。铸件凝固之后,锰在镁枝晶中的过饱和。当铸件随后在上述第三工序中被加热时,在均匀化阶段,al-mn分散体74在含锰(mn)金属间化合物70中沉淀。在上述第四工序30期间的锻造阶段76中,al-mn分散体74与
含mn金属间化合物70共同用于细化动态再结晶(drx)晶粒78,从而抑制再结晶晶粒的生长。
47.继续参考图1、图4和图6,辊压成形后周向轮辋18中drx晶粒的平均等效直径比外侧凸缘62中的drx晶粒的平均等效直径小10%以上。周向轮辋18中drx晶粒的平均等效直径小于10μm。
48.形成本公开的轴对称镁制品10的方法具有若干优点,包括提供一种基于可旋压成型的无锆合金系统(mg-al-mn-sn)的镁铝合金化学结构,一种适用于旋压成型的微观结构,以及一种用于生产轴对称镁部件(如汽车车轮)的制造工艺。
49.本公开的描述本质上仅是示例性的,并且不脱离本公开的主旨的变型旨在属于本公开的范围内。此类变型不应视为背离本公开的精神和范围。
再多了解一些
本文用于创业者技术爱好者查询,仅供学习研究,如用于商业用途,请联系技术所有人。