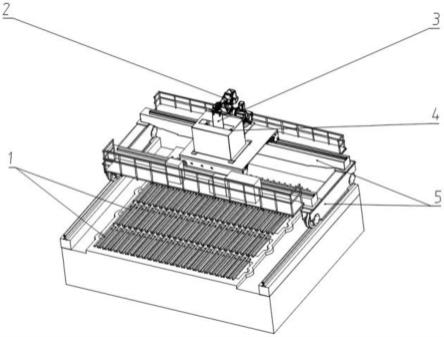
1.本发明涉及智能行车技术领域,更具体的说是涉及一种电解铜极板短路在线排除系统。
背景技术:
2.高杂铜精矿冶炼产出了高杂铜阳极板,高杂铜阳极板还需要进一步进行电解精炼。在电解精炼过程中,铜阳极板中的杂质溶解或不溶解,直接脱落于电解液中,该电解精炼过程,受阳极板杂质的析出,产出阳极泥而悬浮或半悬浮于电解液中,受电解槽面人工作业的扰动和电解作业时间的推移,难免在阴极表面长出“粒子”,随着阴极表面“粒子”的进一步生长,长到足够长时候,会直接搭触到阳极表面,从而形成短路,该短路将导致极板发热或烧蚀的无效电耗,有时候也导致阴极板上已长好的阴极铜再次返溶,从而降低阴极铜产量。此外,受操作员工技能差异的影响,还存在极板装槽时,出现极板断路,即断开状态,未通电,这将导致阳极板不溶解、阴极板表面不长阴极铜的无效作业,对电解阴极铜产量的提高和作业效率的提高,非常不利。
3.目前,国内铜冶炼精炼行业对电解槽生产通电极板是短路或断路故障,均通过人工手持高斯仪表进行监测判断,该方法人工劳动强度较大,还存在人工监测的不可控或不可靠性,人工手持高斯仪表在电解槽面上走动扫描,还存在踩踏极板导致极板上阳极泥脱落,同时对电解液扰动,而带来阳极泥悬浮,不沉降或沉降效果差,可能导致阴极铜表面长颗粒的现象,直接影响最终阴极铜产量和质量,进一步加重电解极板故障的出现,不利于铜的高效电解及阴极铜产品质量和指标的提高;此外,当通过人工判断出故障的极板后,还需通过人工干预的方式对极板故障进行排出,在很大程度上降低了铜电解生产效率。
4.因此,如何克服上述缺陷,提供一种自动的电解铜极板短路在线排除系统,以取代人工识别、人工处理是本领域技术人员亟需解决的问题。
技术实现要素:
5.有鉴于此,本技术基于专利号201110442601.4公开的《一种提高铜电解极板故障信息判断准确度的装置及方法》中所述的故障识别系统,进一步提出电解铜极板短路在线排除系统和方法,以降低铜电解生产过程中人力、物力的投入,提升铜电解生产效率。
6.为了实现上述目的,本发明采用如下技术方案:
7.一方面,本技术公开了一种电解铜极板短路在线排除系统,包括电解槽,其特征在于,还包括:
8.铜板短路识别系统,用于识别短路的电解铜极板,所述电解铜极板在所述电解槽中电解;
9.智能行车系统,用于将运板系统移动到所述短路的电解铜极板的上方;
10.运板系统,用于将所述短路的电解铜极板从所述电解槽中取出运至粒子铣削系统或从所述粒子铣削系统放回至所述电解槽中;
11.所述粒子铣削系统,用于对所述短路的电解铜极板进行自动铣削;
12.所述铜板短路识别系统、所述智能行车系统、所述运板系统以及所述粒子铣削系统均与所述中心处理器电连。
13.优选的,所述智能行车系统,包括:
14.纵向导轨,两条平行的所述纵向导轨安装于所述电解槽的两侧,
15.横向导轨,两条平行的所述横向导轨安装于所述纵向导轨上,并能延所述纵向导轨移动,
16.支撑平台,安装于所述横向导轨,并能延所述横向导轨移动。
17.优选的,所述运板系统包括机器人基台,多轴机器人和抓取装置,所述机器人基台固定于所述支撑平台上,并通过齿轮连接所述多轴机器人,所述多轴机器人端部活动连接所述抓取装置。
18.优选的,所述抓取装置包括机架和抓取手柄,所述机架一侧与所述多轴机器人端部活动连接,另一侧下部具有开口的中空腔体,所述抓取手柄通过活动轴活动铰接于所述中空腔体内,
19.所述抓取手柄包括主动杆组和从动杆组,所述主动杆组和所述从动杆组对称布置并通过齿轮相互咬合,所述主动杆组与驱动元件传动轴固定连接,所述驱动元件固定于所述机架上。
20.优选的,所述主动杆组和所述从动杆组依次包括齿轮件、活动连杆以及凹槽杆件,所述活动连杆还固定于所述中控腔体上。
21.优选的,所述粒子铣削系统包括竖直提升装置,
22.所述竖直提升装置包括支撑桁架、活动基座、提升装置驱动组件和柔性连接件,所述支撑桁架固定于所述支撑平台上,所述支撑桁架的立柱前端设有导向槽,所述活动基座嵌入所述导向槽内,
23.所述支撑桁架的顶端前后设有导向滑轮组件,背部有立板,所述立板后面安装所述提升装置驱动组件,所述柔性连接件通过所述导向滑轮组件连接所述提升装置驱动组件和所述活动基座。
24.优选的,所述粒子铣削系统还包括水平移动装置,
25.所述水平移动装置,包括所述活动基座,所述活动基座上宽缘两侧设有第一导轨,所述第一导轨之间设有螺杆轴承支座,所述螺杆轴承支座上活动连接第一驱动螺杆,所述第一驱动螺杆的端部安装有第一驱动电机,
26.所述第一驱动螺杆通过齿轮与铜粒子铣削组件支座相连接,且所述粒子铣削组件支座底部嵌入所述第一导轨。
27.优选的,所述粒子铣削系统还包括粒子铣削组件,所述粒子铣削组件固定在滑台上,所述滑台与第二驱动螺杆通过齿轮啮合连接,通过所述第二驱动螺杆固定于所述粒子铣削组件支座上,所述第二驱动螺杆的两端通过轴承固定于所述粒子铣削组件支座顶部,外侧一端连接有第二驱动电机。
28.优选的,所述滑台上安装有铣刀盘电机,所述铣刀盘电机轴端安装组合式铣刀盘,所述组合式铣刀盘外侧安装有铣刀。
29.经由上述的技术方案可知,与现有技术相比,本发明公开提供的基于智能行车的
电解铜极板短路在线排除系统,可高效完成铜板极板短路自动识别以及自动故障排除等工作,并能够提高铜电解生产过程中的智能化水平,降低铜电解生产过程中人力、物力的投入,有效的解决铜冶炼行业铜电解过程中因铜板短路导致电解铜生产效率降低问题;
30.另外,本发明提供的抓取装置,能够与极板紧固贴合,实现自动抓取;本发明提供的粒子自动铣削装置能够自动识别粒子位置,并能准确的控制铣刀到识别的粒子位置进行铣削。
附图说明
31.为了更清楚地说明本发明实施例或现有技术中的技术方案,下面将对实施例或现有技术描述中所需要使用的附图作简单地介绍,显而易见地,下面描述中的附图仅仅是本发明的实施例,对于本领域普通技术人员来讲,在不付出创造性劳动的前提下,还可以根据提供的附图获得其他的附图。
32.图1附图为本发明提供的电解铜极板短路在线排除系统整体结构示意图;
33.图2附图为本发明提供的运板系统结构示意图;
34.图3附图为本发明提供的抓取装置结构示意图;
35.图4附图为本发明提供的抓取装置结构侧视图;
36.图5附图为本发明提供的粒子铣削系统结构示意图;
37.图6附图为本发明提供的粒子铣削系统结构侧视图。
38.附图标记说明:
39.1电解槽
ꢀꢀꢀꢀꢀꢀꢀꢀꢀꢀꢀꢀ
2运板系统
ꢀꢀꢀꢀꢀꢀꢀꢀꢀꢀꢀ
201机器人基台
40.202多轴机器人
ꢀꢀꢀꢀꢀꢀꢀ
3电解极板
ꢀꢀꢀꢀꢀꢀꢀꢀꢀꢀꢀ
4铜粒子铣削系统防护罩
41.401铣削系统基座
ꢀꢀꢀꢀꢀ
402支撑桁架
ꢀꢀꢀꢀꢀꢀꢀꢀꢀ
403变频减速电机
42.404滚筒护罩
ꢀꢀꢀꢀꢀꢀꢀꢀꢀ
405柔性连接件
ꢀꢀꢀꢀꢀꢀꢀ
406滑轮组件
43.407第一导轨
ꢀꢀꢀꢀꢀꢀꢀꢀꢀ
408第一驱动螺杆
ꢀꢀꢀꢀꢀ
409第一螺杆轴承支座
44.410第一驱动电机
ꢀꢀꢀꢀꢀ
411铣刀
ꢀꢀꢀꢀꢀꢀꢀꢀꢀꢀꢀꢀꢀ
412红外摄像头
45.413铣刀盘驱动电机 414第二螺杆组件
ꢀꢀꢀꢀꢀ
415第二驱动电机
46.416铣刀盘
ꢀꢀꢀꢀꢀꢀꢀꢀꢀꢀ
417铜粒子收集托盘 5智能行车
47.6抓取装置
ꢀꢀꢀꢀꢀꢀꢀꢀꢀꢀꢀ
601抓取支架
ꢀꢀꢀꢀꢀꢀꢀꢀꢀ
602抓取手柄
48.603活动连杆
ꢀꢀꢀꢀꢀꢀꢀꢀꢀ
604伺服电机
具体实施方式
49.下面将结合本发明实施例中的附图,对本发明实施例中的技术方案进行清楚、完整地描述,显然,所描述的实施例仅仅是本发明一部分实施例,而不是全部的实施例。基于本发明中的实施例,本领域普通技术人员在没有做出创造性劳动前提下所获得的所有其他实施例,都属于本发明保护的范围。
50.本发明实施例公开了一种基于智能行车的电解铜极板短路在线排除系统,下面参考附图描述本发明实施例提供的电解铜极板短路在线排除系统,
51.一方面,本发明基于智能行车的电解铜极板短路在线排除系统,包括电解槽1,另外还包括:
52.铜板短路识别系统,用于识别短路的电解铜极板,其中电解铜极板在电解槽中点解;
53.智能行车系统5,用于将运板系统移动到短路的所述电解铜极板的上方;
54.运板系统2,用于完成短路的所述电解铜极板的取出和放回;
55.粒子铣削系统,用于对短路的所述电解铜极板进行铣削;
56.中心处理器,用于对所述铜板短路识别系统、所述智能行车系统、所述运板系统和所述粒子铣削系统进行控制。
57.对于铜板短路识别系统,本发明采用专利号201110442601.4公开的《一种提高铜电解极板故障信息判断准确度的装置及方法》中所述的故障识别系统,该专利提出的自动判定电解铜极板故障信息的方法为:将红外热成像仪安装于电解槽上方,高清摄像头对电解槽槽面及其铜电解极板拍照成像,内置微型处理器将红外热成像信号转换成数字信号,并将该数字信号传送给中心处理器。红外热成像仪安装位置为高于电解槽水平槽面高度12m左右处,对垂直中心半径为45m范围内的电解槽槽面及其铜电解极板可进行高清红外扫描成像、识别,红外热成像仪扫描范围可在0~200m半径内调节,内置微型处理器支持1080p高清热成像图片、码流为2~4mbps的速度向中心处理器传输,中心处理器支持图片储存超过30天,并支持现场图片和视频回放。红外热成像仪每0.5~10ms(可调节扫描速度)对扫描范围内电解槽槽面铜电解极板巡检扫描成像一次,通过频繁扫描对槽面铜电解极板的红外温度数据进行采集和识别,内置微型处理器将红外热成像信号转换成数字信号,并通过网络或wifi将转换的数字信号传送至中心处理器。抗磁干扰隔离罩可滤去电解槽的电磁场干扰等不相干信息,实现红外热成像仪对铜电解极板的成像信息的高清晰采集。该专利优点是能自动高效识别出电解铜极板故障信息以及相对应的具体位置。
58.进一步,如图1所示,本发明智能行车系统,包括:
59.纵向导轨,两条平行的纵向导轨安装于电解槽的两侧,
60.横向导轨,两条平行的所述横向导轨安装于纵向导轨上,并能延纵向导轨移动,
61.支撑平台,安装于所述横向导轨,并能延横向导轨移动。
62.其中,纵向导轨和横向导轨上等间隔设置编码器,编码器将电解槽网格化,用于根据编码器对短路的电解铜极板进行定位。即当故障识别系统识别到短路的电解铜极板时,将相应的具体位置发送至中心处理器,中心处理器根据该位置信息确定横纵向编码器的位置,进而控制支撑平台延纵向导轨和横向导轨移动到短路铜极板所在位置,从而实现短路铜极板的精确定位。
63.支撑平台上安装有运板系统2,如图2,运板系统具体包括机器人基台201,多轴机器人202和抓取装置6,机器人基台201固定于支撑平台上,并通过齿轮连接多轴机器人202,即机器人基台的外齿圈与多轴机器人底部内齿圈向啮合,多轴机器人端部活动连接抓取装置6。
64.运板系统用于通过多轴机器人及抓取装置完成短路的所述电解铜极板的取出和放回,其中,在一种实施例中,多轴机器人具体安装在支撑平台纵向边缘的中心位置,在对短路铜极板进行定位抓取时,是沿纵向导轨的方向将电解槽一分为二,以短路的电解铜极板同侧的支撑平台边缘为基准对短路的电解铜极板进行定位,而对于通过中心处理器实现对多轴机器人的控制实现抓取的方法,市面上已广泛存在,且对于本领域普通技术人员而
言都是已知的,此处不在详细描述。
65.但需要注意的是,本发明抓取装置包括机架601、抓取手柄602、活动连杆603以及驱动元件604,如图3所示,机架一侧与多轴机器人端部活动连接,另一侧为下部开口的中空腔体,抓取手柄通过活动轴活动铰接于所述中空腔体内,在一种实施例中,抓取手柄有多组,以使运送过程抓取更加稳固。
66.进一步,抓取手柄包括主动杆组和从动杆组,主动杆组和从动杆组对称布置并通过齿轮相互咬合,主动杆组与驱动元件传动轴固定连接,驱动元件固定于机架上。
67.而主动杆组和从动杆组又依次包括齿轮件、活动连杆以及凹槽杆件,活动连杆还固定于中控腔体上,其中,主动杆组及从动杆组上半部分为齿轮相互咬合,通过主动杆组齿轮中心与驱动电机活动链接,从而通过驱动电机轴转动来驱动主动杆组并带动从动杆组闭合或者张开。
68.驱动电机与中心处理器连接,以便于实现自动抓取。
69.一般情况下,电解极板设有中空部位,为使抓取手柄提取短路铜极板时能够更加贴合紧固,在一种实施例中,在本发明中抓取手柄下方为90度托板,如图4下方所示。
70.当运板系统将短路铜极板取出后,由中心处理器控制其自动放入粒子铣削系统中,以对电解铜极板进行铣削;
71.具体而言,粒子铣削系统包括竖直提升装置和水平移动装置,如图5所示,
72.其中,竖直提升装置包括支撑桁架402、活动基座、提升装置驱动组件和柔性连接件405,支撑桁架安放于多轴机器人便于取放的位置,并通过铣削系统基座401固定于支撑平台上,支撑桁架402的立柱前端设有导向槽,活动基座嵌入导向槽内,
73.支撑桁架的顶端前后设有导向滑轮组件,其中,与前导向滑轮组件固定的桁架下方设置有极板接触面板,极板接触面板上方设有凸起结构,该凸起结构与极板解除面板形成极板固定沟槽,用于通过极板挂耳悬挂固定故障的电解铜极板;
74.进一步,支撑桁架的背部设有立板,立板后面安装所述提升装置驱动组件,柔性连接件通过所述导向滑轮组件连接所述提升装置驱动组件和所述活动基座,一种实施例中,柔性连接件为钢丝绳。
75.在另一种实施例中,提升装置驱动组件包括变频式减速电机403、滚筒和轴承,如图6所示,其中,滚筒和轴承各有两组,并分布于变频式减速电机的两侧。变频式减速电机机座与立板及支撑平台刚性固定,电机转动轴连接驱动轴,具体与驱动轴通过齿轮啮合传输动力,驱动轴另一端与轴承活动链接,轴承固定在轴承支座上,轴承支座固定于支撑平台上,进一步,滚筒与驱动轴固定连接的同时,与柔性连接件的一端固定连接,以便于随驱动轴转动,实现对活动基座的提升。
76.在一种实施例中,滚筒外侧设有滚筒护罩404,滚筒护罩为中控壳体,并刚性固定于轴承支座外侧,
77.对于水平移动装置,包括活动基座,活动基座上宽缘两侧设有第一导轨 407,第一导轨之间设有螺杆轴承支座409,在一种实施例中,螺杆轴承支座 409有两组,并位于活动基座的两端,螺杆轴承支座上活动连接第一驱动螺杆 408,第一驱动螺杆408的端部安装有第一驱动电机410,第一驱动电机倒装固定,通过端部的齿轮与第一驱动螺杆端部齿轮通过同步带连接并进行动力传输,
78.其次,第一驱动螺杆408通过齿轮与粒子铣削组件支座相连接,通过齿轮啮合进行动力传输,且粒子铣削组件支座底部嵌入第一导轨中,便于实现稳定的移动。
79.进一步,粒子铣削系统还包括粒子铣削组件,粒子铣削组件固定在滑台上,滑台与第二驱动螺杆414通过齿轮啮合连接,并通过第二驱动螺杆固定于粒子铣削组件支座上,以实现滑台的进退移动,第二驱动螺杆的两端通过轴承及轴承座固定于粒子铣削组件支座顶部,并在外侧一端连接有第二驱动电机415,其中,外侧是指远离立板的一端,且第二驱动电机415仍采用倒装固定,即通过端部的齿轮与第一驱动螺杆端部齿轮通过同步带连接并进行动力传输。
80.滑台上安装有铣刀盘电机413,铣刀盘电机413轴端安装组合式铣刀盘 416,组合式铣刀盘外侧安装有铣刀411,一种实施例中,铣刀为十组端面铣刀,
81.另外,支撑桁架立柱内侧嵌有两组光感式热成像红外摄像头412,其中,摄像头端面与支撑桁架内侧面平行,用于识别短路铜极板的厚度,传输至中心处理器,从而控制滑台的进退距离。
82.一种实施例中,在铣削装置底部还设有铜粒子收集托盘417,用于收集被剥离的铜粒子,
83.一种实施例中,粒子铣削系统外侧还设有铜粒子铁削系统防护罩4,
84.当粒子铣削系统接收到中心处理器的受板指令后,光感式热成像红外摄像头开始对短路极板内外两侧板面平整度进行扫描并将扫描后的图像信号转化为数字信号上传至中心处理器进行信号采集识别,板面平整度扫描完成后,竖直提升装置、水平移动装置以及粒子铣削组件在中心处理器的控制下并行联动,将铜板单面粒子进行铣削,铣削完成后由多轴机器人将铜板再次提起,将铜内外两侧进行调换,铣削装置再次作业,铣削后的电解铜粒子由铜粒子收集托盘进行收集。
85.另一方面,基于本发明公开的电解铜极板短路在线排除系统,本发明还公开了一种基于智能行车的电解铜极板短路在线排除方法,具体步骤包括:
86.s1、铜板短路识别系统监测到极板短路故障时,将信号传输至中心处理器,所述中心处理器进行定位识别后,控制所述智能行车系统到达短路铜极板上方;
87.s2、运板系统通过多轴机器人将所述故障铜极板取出,并放入所述粒子铣削系统内,由所述粒子铣削系统对所述故障铜极板的内外两侧进行铣削;
88.当所述智能行车行驶至故障极板上方后,所述中心处理器向所述运板系统发送作业指令,所述运板系统开始作业,并通过多轴机器人将所述抓取装置运送至故障极板上方,此时故障极板顶部的导电棒位于所述抓取装置垂直面的中心,之后所述抓取装置开始工作,所述两组伺服电机驱动所述两组抓取手柄向外张开,且所述多轴机器人带动所述抓取手柄垂直向下运动,当所述抓取手柄下移到底部与故障极板导电棒下方的方孔对齐后所述多轴机器人停止运动,此时所述两组伺服电机向相反方向转动从而控制所述两组抓取手柄向内运动,从而夹住并紧贴故障极板,之后所述多轴机器人将故障极板垂直提升将其从电解槽中取出,并放入所述粒子铣削系统内,故障极板导电棒两端分别挂入铣削系统两侧的极板固定沟槽内,所述粒子识别系统开始工作,即两组红外摄像头开始工作,分别检测故障极板阴阳两面平整度,当极板表面出现粒子时,红外摄像头衍射出的图像则会出现异常光斑,中心处理器通过对图像进行分析处理并判断光斑所处位置,从而给铣削系统发送作业
指令,粒子铣削系统对故障铜极板进行铣削;当铣削完成后,以同样的方式铣削故障铜极板另一面;
89.s3、铣削完成后,由所述多轴机器人将所述故障铜极板放入电解槽内。
90.具体的,在铜电解生产过程中,铜板短路识别系统对电解槽面极板温度数据进行实时监测,并将极板温度
±
3℃以内判定为正常温度,高于平均温度 3℃时,判定为极板短路故障。
91.当识别到有短路铜极板时,将短路故障信号传入中心处理器,中心处理器短路极板进行定位识别并向智能行车下达指令。
92.智能行车接收到中心处理器下达的指令后,通过纵横导轨移动到短路极板上方,之后铜板抓取装置开始工作,首先,多轴机器人将电解铜板抓取装置移动到短路极板上方,每组抓取手柄卡槽与短路极板中空部位处于同一水平位置,抓取手柄将短路极板贴合并夹紧,然后提起找正位置将短路极板两侧吊耳分别放入所述支撑桁凹槽内;
93.铣削系统接收到受板指令后,光感式热成像红外摄像头开始对短路极板内外两侧板面的平整度进行扫描,并将扫描后的图像信号转化为数字信号上传至中心处理器进行信号采集识别,
94.板面平整度扫描完成后,竖直提升装置、水平移动装置以及粒子铣削系统共同在中心处理器的控制下并行联动,将铜板单面粒子进行铣削,铣削完成后多轴机器人将铜板再次提起,将铜内外两侧进行调换,铣削装置再次作业,铣削后的电解铜粒子由所述铜粒子收集托盘进行收集;
95.铜板粒子铣削完成后,多轴机器人将铜板再次提取放入电解槽内继续完成铜电解生产。
96.值得注意的是,本实用新型实施例中未作详细描述的内容属于本领域专业技术人员公知的现有技术。
97.本说明书中各个实施例采用递进的方式描述,每个实施例重点说明的都是与其他实施例的不同之处,各个实施例之间相同相似部分互相参见即可。对于实施例公开的装置而言,由于其与实施例公开的方法相对应,所以描述的比较简单,相关之处参见方法部分说明即可。
98.对所公开的实施例的上述说明,使本领域专业技术人员能够实现或使用本发明。对这些实施例的多种修改对本领域的专业技术人员来说将是显而易见的,本文中所定义的一般原理可以在不脱离本发明的精神或范围的情况下,在其它实施例中实现。因此,本发明将不会被限制于本文所示的这些实施例,而是要符合与本文所公开的原理和新颖特点相一致的最宽的范围。
再多了解一些
本文用于创业者技术爱好者查询,仅供学习研究,如用于商业用途,请联系技术所有人。