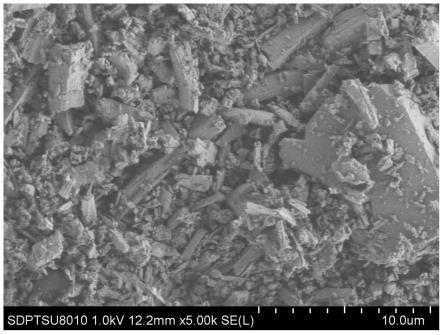
1.本发明属于精细化工技术领域,具体涉及一种高耐磨复合填料及其制备方法和应用。
背景技术:
2.塑料作为主要的工业原材料之一,已广泛应用在国民经济各行各业和人民生活中,成为不可缺少的重要物质,随着现代科学技术发展,对塑料制品材料性能提出了更高的要求。塑料填充改性已成为改善塑料制品性能、降低生产成本、节约石油资源以及实现绿色环保的重要途径,其中,矿物粉体是塑料填充改性中用量最大的材料。
3.塑料的耐磨性是决定塑料应用领域和使用寿命的重要指标,目前,提高塑料耐磨性常用的方法,就是在塑料制品中添加矿物粉体填料,比如硫酸钡或滑石粉等,这些填料能够在一定程度上改善材料的耐磨性,但是仍然很难满足对塑料的耐磨性能的要求。
技术实现要素:
4.本发明的目的在于提供一种高耐磨复合填料及其制备方法和应用,本发明提供的高耐磨复合填料可以赋予高分子材料优异的耐磨性能。
5.为了实现上述目的,本发明提供如下技术方案:
6.本发明提供了一种高耐磨复合填料的制备方法,包括以下步骤:
7.(1)将硅灰石粉体、二氧化硅粉体、云母粉体和研磨助剂干法研磨,得到复合粉体;
8.(2)将所述复合粉体、分散剂、耐磨助剂、抗静电剂和水湿法研磨后依次进行闪蒸干燥和解聚打散,得到高耐磨复合粉体;
9.(3)将所述高耐磨复合粉体和改性剂混合进行改性,得到高耐磨复合填料;所述改性剂包括硅烷偶联剂和季铵盐中的一种或几种。
10.优选的,所述硅灰石粉体和二氧化硅粉体的质量比为3~6:3~6;
11.所述二氧化硅粉体和云母粉体的质量比为3~6:1;
12.所述硅灰石粉体、二氧化硅粉体和云母粉体的总质量与研磨助剂的质量之比为1000:6~9。
13.优选的,所述复合粉体和分散剂的质量比为1006~1009:8~12;
14.所述复合粉体和耐磨助剂的质量比为1006~1009:7~10;
15.所述复合粉体和抗静电剂的质量比为1006~1009:6~9。
16.优选的,所述分散剂包括聚丙烯酸钠、十二烷基苯磺酸钠、全氟辛基磺酸钠和月桂酸磺酸钠中的一种或几种;
17.所述耐磨助剂包括聚硅氧烷偶联剂和钛酸酯偶联剂中的一种或几种;
18.所述抗静电剂包括单硬脂酸甘油酯、二羟乙基十八胺、聚酰胺聚氧乙醚、十八烷基三甲基氯化铵和甲氧基聚乙二醇-甲基丙烯酸酯共聚物中的一种或几种。
19.优选的,所述湿法研磨中浆料的温度为70~80℃,湿法研磨的转速为2800~
3000rpm,时间为2~3小时。
20.优选的,所述硅烷偶联剂包括γ-氨丙基三乙氧基硅烷、γ-氨丙基甲基二甲氧基硅烷、γ-氨丙基三甲氧基硅烷、γ-氨丙基甲基二乙氧基硅烷、γ-二乙胺基甲基三乙氧基硅烷、γ-二乙烯三胺基丙基三甲氧基硅烷中的一种或几种;所述季铵盐包括双十八烷基二甲基氯化铵、双十八烷基二甲基氯化铵、十二烷基苄基二甲基氯化铵、十二烷基苄基二甲基氯化铵和十八烷基三甲基氯化铵中的一种或几种。
21.优选的,所述复合粉体和改性剂的质量比为1006~1009:8~15。
22.优选的,所述硅灰石粉体的粒径为5~10毫米,所述二氧化硅粉体的粒径为5~10毫米,所述云母粉体的粒径为5~10毫米。
23.本发明还提供了上述方案所述制备方法得到的高耐磨复合填料,粒径为2.0~3.0微米。
24.本发明还提供了上述方案所述高耐磨复合填料在高分子材料中的应用。
25.本发明提供了一种高耐磨复合填料的制备方法。本发明将硅灰石粉体、二氧化硅粉体和云母粉体三种矿物粉体复合,充分发挥各矿物粉体的功能特性,硅灰石粉体、二氧化硅粉体和云母粉体硬度偏高且耐磨性好,并且硅灰石粉体为针状结构,二氧化硅粉体为球状结构,云母粉体为片状结构,三种粉体复合,结构互补,从而可以显著提高复合填料的耐磨性,最终得到了一种高耐磨复合填料。此外,本发明通过硅烷偶联剂和季铵盐对高耐磨复合粉体进行改性,可以提高后续加工过程中复合粉体的流动性、分散性以及与基体树脂的相容性,从而进一步提升所得材料的耐磨性。本发明提供的复合矿物粉体可显著提高塑料等高分子材料的耐磨性,同时使高分子材料获得优异的综合物理力学性能。
26.本发明还提供了上述方案所述制备方法得到的高耐磨复合填料,粒径为2.0~3.0微米。本发明提供的高耐磨复合填料可以赋予高分子材料优异的耐磨性能,解决塑料等高分子材料的耐磨性能不足的问题。
27.本发明还提供了上述方案所述高耐磨复合填料在高分子材料中的应用。本发明提供的高耐磨复合填料应用广泛,可以用于各种高分子材料,比如塑料,尤其是热塑性弹性体材料,可以明显提高材料的耐磨性等力学性能。
附图说明
28.为了更清楚地说明本发明实施例或现有技术中的技术方案,下面将对实施例中所需要使用的附图作简单地介绍,显而易见地,下面描述中的附图仅仅是本发明的一些实施例,对于本领域普通技术人员来讲,在不付出创造性劳动性的前提下,还可以根据这些附图获得其他的附图。
29.图1为本发明提供的高耐磨复合填料的工艺流程图;
30.图2为本发明实施例1制备的高耐磨复合填料的5000倍电镜照片。
具体实施方式
31.本发明提供了一种高耐磨复合填料的制备方法,包括以下步骤:
32.(1)将硅灰石粉体、二氧化硅粉体、云母粉体和研磨助剂干法研磨,得到复合粉体;
33.(2)将所述复合粉体、分散剂、耐磨助剂、抗静电剂和水湿法研磨后依次进行闪蒸
干燥和解聚打散,得到高耐磨复合粉体;
34.(3)将所述高耐磨复合粉体和改性剂混合进行改性,得到高耐磨复合填料;所述改性剂包括硅烷偶联剂和季铵盐中的一种或几种。
35.本发明将硅灰石粉体、二氧化硅粉体、云母粉体和研磨助剂干法研磨,得到复合粉体。在本发明中,所述硅灰石粉体的粒径优选为5~10毫米,更优选为6~9毫米;所述硅灰石粉体的制备方法优选包括以下步骤:将优质硅灰石依次进行粗破碎、清洗和一次破碎得到硅灰石粗粉体,将所述硅灰石粗粉体进行二次破碎,得到硅灰石粉体;所述硅灰石粗粉体的粒径优选为5~10厘米,更优选为6~8厘米;所述一次破碎的设备优选为颚式破碎机;所述二次破碎优选通过自动投料机将硅灰石粗粉体加入锤式破碎机料仓中粉碎,粉碎完成后收集在料仓中;所述二氧化硅粉体的粒径优选为5~10毫米,更优选为6~8毫米;所述云母粉体的粒径优选为5~10毫米,更优选为7~9毫米;所述二氧化硅粉体和云母粉体的制备方法与硅灰石粉体一致,在此不再赘述。
36.在本发明中,所述研磨助剂优选包括聚乙二醇、聚羧酸钠和木质素磺酸钠中的一种或几种,更优选为聚乙二醇、聚羧酸钠和木质素磺酸钠,所述聚乙二醇、聚羧酸钠和木质素磺酸钠的质量比优选为2:1:1;所述硅灰石粉体和二氧化硅粉体的质量比优选为3~6:3~6,更优选为3~6:4~5,进一步优选为4~5:3~6;所述二氧化硅粉体和云母粉体的质量比优选为3~6:1,更优选为3~5:1,进一步优选为4~5:1;所述硅灰石粉体、二氧化硅粉体和云母粉体的总质量与研磨助剂的质量之比优选为1000:6~9,更优选为1000:7~9,进一步优选为1000:8;所述干法研磨的转速优选为1500~2000r/min,更优选为1600~1800r/min,时间优选为15~30min,更优选为20~25min;所述干法研磨的设备优选为198型环辊磨;所述干法研磨优选将硅灰石粉体、二氧化硅粉体和云母粉体经皮带输送至198型环辊磨,在环辊磨进口处加入研磨助剂。
37.得到复合粉体后,本发明将所述复合粉体、分散剂、耐磨助剂、抗静电剂和水湿法研磨后依次进行闪蒸干燥和解聚打散,得到高耐磨复合粉体。在本发明中,所述复合粉体的粒径优选为20~30微米,更优选为22~27微米;所述分散剂优选包括聚丙烯酸钠、十二烷基苯磺酸钠、全氟辛基磺酸钠和月桂酸磺酸钠中的一种或几种,更优选为月桂酸磺酸钠、十二烷基苯磺酸钠和全氟辛基磺酸钠,所述月桂酸磺酸钠、十二烷基苯磺酸钠和全氟辛基磺酸钠的质量比优选为1:2:1,本发明通过加入上述分散剂,可以将复合粉体和耐磨助剂等组分充分分散到水中,避免发生团聚和沉降现象;所述耐磨助剂优选包括聚硅氧烷偶联剂和钛酸酯偶联剂中的一种或几种,更优选为聚硅氧烷偶联剂和硅酸酯偶联剂,所述聚硅氧烷偶联剂和硅酸酯偶联剂的质量比优选为1:2,本发明通过加入上述耐磨助剂,与复合粉体共同作用,有利于提高复合填料的耐磨性能;所述聚硅氧烷偶联剂优选为上海哲华化工材料有限公司生产的型号为psi-500的聚硅氧烷偶联剂;所述钛酸酯偶联剂优选为氧代乙酰螯合型钛酸酯偶联剂;所述氧代乙酰螯合型钛酸酯偶联剂优选包括二氧代乙酰基钛酸酯和二甲基丙烯酰基氧代乙酰基钛酸酯中的一种或两种;所述抗静电剂优选包括单硬脂酸甘油酯、二羟乙基十八胺、聚酰胺聚氧乙醚、十八烷基三甲基氯化铵和甲氧基聚乙二醇-甲基丙烯酸酯共聚物中的一种或几种,更优选为单硬脂酸甘油酯、二羟乙基十八胺和甲氧基聚乙二醇-甲基丙烯酸酯共聚物,所述单硬脂酸甘油酯、二羟乙基十八胺和甲氧基聚乙二醇-甲基丙烯酸酯共聚物的质量比优选为2:1:1,本发明通过加入上述抗静电剂,可以减少复合粉体等组
分的静电积累,有利于各组分的充分分散。
38.在本发明中,所述复合粉体和分散剂的质量比优选为1006~1009:8~12,更优选为1006~1009:9~11;所述复合粉体和耐磨助剂的质量比优选为1006~1009:7~10,更优选为1006~1009:8~9;所述复合粉体和抗静电剂的质量比优选为1006~1009:6~9,更优选为1006~1009:7~8;所述复合粉体、分散剂、耐磨助剂和抗静电剂的总质量与水的质量之比优选为3~5:6,更优选为4~5:6;所述湿法研磨的设备优选为立式搅拌磨;所述湿法研磨的转速优选为2800~3000r/min,更优选为2850-2950r/min,时间优选为1.5~2.5小时,更优选为2小时;所述湿法研磨中浆料的温度优选为70~80℃,更优选为73~77℃;所述湿法研磨所得浆料的细度优选为2.0~3.0微米,更优选为2.2~2.8微米;所述闪蒸干燥优选包括:将湿法研磨所得浆料加入闪蒸干燥机,用干净的热空气进行闪蒸干燥;所述热空气的进风温度优选为340~360℃,更优选为350℃;所述闪蒸干燥结束后优选对闪蒸干燥所得产物用布袋收集;所述解聚打散优选包括:将收集后的产物经螺旋铰刀喂料器加入解聚打散机,通过解聚打散使团聚的粉体得到解散,保持原料粉体的原生粒子的粒径;所述高耐磨复合粉体的粒径优选与硅灰石粉体、二氧化硅粉体或云母粉体一致。
39.得到高耐磨复合粉体后,本发明将所述高耐磨复合粉体和改性剂混合进行改性,得到高耐磨复合填料。在本发明中,所述改性剂包括硅烷偶联剂和季铵盐中的一种或几种;所述硅烷偶联剂优选包括γ-氨丙基三乙氧基硅烷、γ-氨丙基甲基二甲氧基硅烷、γ-氨丙基三甲氧基硅烷、γ-氨丙基甲基二乙氧基硅烷、γ-二乙胺基甲基三乙氧基硅烷、γ-二乙烯三胺基丙基三甲氧基硅烷中的一种或几种;所述季铵盐优选包括双十八烷基二甲基氯化铵、双十八烷基二甲基氯化铵、十二烷基苄基二甲基氯化铵、十二烷基苄基二甲基氯化铵和十八烷基三甲基氯化铵中的一种或几种;所述改性剂更优选为γ-氨丙基甲基二甲氧基硅烷、γ-二乙烯三胺基丙基三甲氧基硅烷和双十八烷基二甲基氯化铵;所述γ-氨丙基甲基二甲氧基硅烷、γ-二乙烯三胺基丙基三甲氧基硅烷和双十八烷基二甲基氯化铵的质量比优选为2:2:1;所述复合粉体和改性剂的质量比优选为1006~1009:8~15,更优选为1006~1009:10~14。本发明通过改性剂对高耐磨复合粉体进行改性处理,利用改性剂包覆高耐磨复合粉体粉体,可以提高所得高耐磨复合填料的流动性、分散性以及与高分子材料的相容性,降低粉体的极性,从而提高耐磨性。本发明优选将所得无机阻燃复合填料进行包装;所述包装的设备优选为自动包装机。
40.图1为本发明提供的高耐磨复合填料的工艺流程图:本发明首先将硅灰石、二氧化硅和云母原矿破碎,然后加入研磨助剂进行干法研磨,得到粒径20~30微米的复合粉体,将所得复合粉体加水配制浆料,再加入复合分散剂、耐磨助剂和抗静电剂湿法研磨,得到粒径2.0~3.0微米的浆料,将所得浆料依次闪蒸干燥、解聚打散和布袋收集,加入改性剂复合改性,得到成品后包装。
41.本发明还提供了上述方案所述制备方法得到的高耐磨复合填料,粒径为2.0~3.0微米。
42.在本发明中,所述高耐磨复合填料的粒径为2.0~3.0微米,优选为2.2~2.8微米,更优选为2.4~2.6微米。
43.本发明还提供了上述方案所述高耐磨复合填料在高分子材料中的应用。
44.在本发明中,所述应用优选包括以下步骤:将高耐磨复合填料和高分子材料混炼,
得到耐磨材料。在本发明中,所述高耐磨复合填料和高分子材料的质量比优选为3:3~5,更优选为3:3~4;所述高分子材料优选为树脂;所述树脂优选为热塑性弹性体;所述热塑性弹性体优选包括sebs和pp中的一种或两种。本发明提供的高耐磨复合填料应用广泛,可以用于各种高分子材料,比如塑料,尤其是热塑性弹性体材料,可以明显提高材料的耐磨性等力学性能。
45.为了进一步说明本发明,下面结合附图和实施例对本发明的方案进行详细地描述,但不能将它们理解为对本发明保护范围的限定。
46.实施例1
47.一种高耐磨复合填料的制备方法,包含以下步骤:
48.分别将优质硅灰石、二氧化硅和云母原矿经粗破碎、清洗和一次破碎后,得到粒径为5~10厘米的粗粉体,再放入料仓中进行二次破碎,得到粒径为5~10毫米的粉体;将硅灰石粉体、二氧化硅粉体和云母粉体按质量比3:3:1与6
‰
(占硅灰石粉体、二氧化硅粉体和云母粉体质量和的6
‰
)研磨助剂(具体为聚乙二醇、聚羧酸钠和木质素磺酸钠,三者的质量比为2:1:1)进行干法研磨,得到20~30微米的复合粉体;
49.将所述复合粉体与水配成40%固含量的浆料,在配制过程中加入复合粉体质量8
‰
的复合分散剂(具体为月桂酸磺酸钠、十二烷基苯磺酸钠和全氟辛基磺酸钠,三者的质量比为1:2:1)、7
‰
耐磨助剂(具体为psi-500聚硅氧烷偶联剂和二氧代乙酰基钛酸酯,三者的质量比为1:2)和6
‰
抗静电剂(具体为单硬脂酸甘油酯、二羟乙基十八胺和甲氧基聚乙二醇-甲基丙烯酸酯共聚物,三者的质量比为2:1:1),保证浆料温度在80℃进行恒温高速搅拌湿法研磨,立式搅拌机转速为2800r/min,搅拌2小时,得到粒径2.0~3.0微米的复合浆料,再经干燥、收集和解聚打散,加入复合粉体质量8
‰
的改性剂(具体为γ-氨丙基甲基二甲氧基硅烷、γ-二乙烯三胺基丙基三甲氧基硅烷和双十八烷基二甲基氯化铵型,三者的质量比为2:2:1)进行表面改性,最终得到高耐磨复合填料。图2为实施例1制备的高耐磨复合填料的5000倍电镜照片图,根据图2可以看出,本实施例得到的高耐磨复合填料组分均匀,纯度高,无明显杂质。
50.实施例2
51.一种高耐磨复合填料的制备方法,包含以下步骤:
52.分别将优质硅灰石、二氧化硅和云母原矿经粗破碎、清洗和一次破碎后,得到粒径为5~10厘米的粗粉体,再放入料仓中进行二次破碎,得到粒径为5~10毫米的粉体;将所得硅灰石粉体、二氧化硅粉体和云母粉体按质量比为5:3:1与7
‰
(占硅灰石粉体、二氧化硅粉体和云母粉体质量和的7
‰
)研磨助剂(具体为聚乙二醇、聚羧酸钠和木质素磺酸钠,三者质量比为2:1:1)进行干法研磨,得到粒径为20~30微米的复合粉体;
53.将所述复合粉体与水配成50%固含量的浆料,在配制过程中加入复合粉体质量10
‰
的复合分散剂(具体为月桂酸磺酸钠、十二烷基苯磺酸钠和全氟辛基磺酸钠,三者质量比为1:2:1)、8
‰
耐磨助剂(具体为psi-500聚硅氧烷偶联剂和二氧代乙酰基钛酸酯,两者质量比为1:2)和7
‰
抗静电剂(具体为单硬脂酸甘油酯、二羟乙基十八胺、甲氧基聚乙二醇-甲基丙烯酸酯共聚物,三者质量比为2:1:1),保证浆料温度在80℃进行恒温高速搅拌湿法研磨,立式搅拌机转速为2800r/min,搅拌2小时,得到粒径为2.0~3.0微米的复合浆料,再经干燥、收集和解聚打散,加入复合粉体质量9
‰
的改性剂(具体为γ-氨丙基甲基二甲氧基硅
烷、γ-二乙烯三胺基丙基三甲氧基硅烷和双十八烷基二甲基氯化铵型,三者质量比为2:2:1)进行表面改性,最终得到高耐磨复合填料。
54.实施例3
55.一种高耐磨复合填料的制备方法,包含以下步骤:
56.分别将优质硅灰石、二氧化硅和云母原矿经粗破碎、清洗和一次破碎后,得到粒径为5~10厘米的粗粉体,再放入料仓中进行二次破碎,得到粒径为5~10毫米的粉体;将硅灰石粉体、二氧化硅粉体和云母粉体按质量比为3:5:1与8
‰
(占硅灰石粉体、二氧化硅粉体和云母粉体质量和的8
‰
)研磨助剂(具体为聚乙二醇、聚羧酸钠和木质素磺酸钠,三者质量比为2:1:1)进行干法研磨,得到粒径为20~30微米的复合粉体;
57.将所述复合粉体与水配成50%固含量的浆料,在配制过程中加入复合粉体质量11
‰
的复合分散剂(具体为月桂酸磺酸钠、十二烷基苯磺酸钠和全氟辛基磺酸钠,三者质量比为1:2:1)、9
‰
耐磨助剂(具体为psi-500聚硅氧烷偶联剂和二氧代乙酰基钛酸酯,两者质量比为1:2)和8
‰
抗静电剂(具体为单硬脂酸甘油酯、二羟乙基十八胺、甲氧基聚乙二醇-甲基丙烯酸酯共聚物,三者质量比为2:1:1),保证浆料温度在80℃进行恒温高速搅拌湿法研磨,立式搅拌机转速为2800r/min,搅拌2小时,得到粒径为2.0~3.0微米的复合浆料,再经干燥、收集和解聚打散,加入复合粉体质量10
‰
的改性剂(具体为γ-氨丙基甲基二甲氧基硅烷、γ-二乙烯三胺基丙基三甲氧基硅烷和双十八烷基二甲基氯化铵型,三者质量比为2:2:1)进行表面改性,最终得到高耐磨复合填料。
58.实施例4
59.一种高耐磨复合填料的制备方法,包含以下步骤:
60.分别将优质硅灰石、二氧化硅和云母原矿经粗破碎、清洗和一次破碎后,得到粒径为5~10厘米的粗粉体,再放入料仓中进行二次破碎,得到粒径为5~10毫米的粉体;将硅灰石粉体、二氧化硅粉体和云母粉体按质量比5:5:1与9
‰
(占硅灰石粉体、二氧化硅粉体和云母粉体质量和的9
‰
)研磨助剂(具体为聚乙二醇、聚羧酸钠和木质素磺酸钠,三者质量比为2:1:1)进行干法研磨,得到粒径为20~30微米的复合粉体;
61.将所述复合粉体与水配成50%固含量的浆料,在配制过程中加入复合粉体质量12
‰
的复合分散剂(具体为月桂酸磺酸钠、十二烷基苯磺酸钠和全氟辛基磺酸钠,三者质量比为1:2:1)、9
‰
耐磨助剂(具体为psi-500聚硅氧烷偶联剂和二氧代乙酰基钛酸酯,两者质量比为1:2)和8
‰
抗静电剂(具体为单硬脂酸甘油酯、二羟乙基十八胺、甲氧基聚乙二醇-甲基丙烯酸酯共聚物,三者质量比为2:1:1),保证浆料温度在80℃进行恒温高速搅拌湿法研磨,立式搅拌机转速为2800r/min,搅拌2小时,得到粒径为2.0~3.0微米的复合浆料,再经干燥、收集和解聚打散,加入复合粉体质量11
‰
的改性剂(具体为γ-氨丙基甲基二甲氧基硅烷、γ-二乙烯三胺基丙基三甲氧基硅烷和双十八烷基二甲基氯化铵型,三者质量比为2:2:1)进行表面改性,最终得到高耐磨复合填料。
62.实施例5
63.一种高耐磨复合填料的制备方法,包含以下步骤:
64.分别将优质硅灰石、二氧化硅和云母原矿经粗破碎、清洗和一次破碎后,得到粒径为5~10厘米的粗粉体,再放入料仓中进行二次破碎,得到粒径为5~10毫米的粉体;将硅灰石粉体、二氧化硅粉体和云母粉体按质量比为3:6:1与9
‰
(占硅灰石粉体、二氧化硅粉体和
云母粉体质量和的9
‰
)研磨助剂(具体为聚乙二醇、聚羧酸钠和木质素磺酸钠,三者质量比为2:1:1)进行干法研磨,得到粒径为20~30微米的复合粉体;
65.将所述复合粉体与水配成50%固含量的浆料,在配制过程中加入复合粉体质量12
‰
的复合分散剂(具体为月桂酸磺酸钠、十二烷基苯磺酸钠和全氟辛基磺酸钠,三者质量比为1:2:1)、10
‰
耐磨助剂(具体为psi-500聚硅氧烷偶联剂和二氧代乙酰基钛酸酯,两者质量比为1:2)和9
‰
抗静电剂(具体为单硬脂酸甘油酯、二羟乙基十八胺、甲氧基聚乙二醇-甲基丙烯酸酯共聚物,三者质量比为2:1:1),保证浆料温度在80℃进行恒温高速搅拌湿法研磨,立式搅拌机转速为2800r/min,搅拌2小时,得到粒径为2.0~3.0微米的复合浆料,再经干燥、收集和解聚打散,加入复合粉体质量13
‰
的改性剂(具体为γ-氨丙基甲基二甲氧基硅烷、γ-二乙烯三胺基丙基三甲氧基硅烷和双十八烷基二甲基氯化铵型,三者质量比为2:2:1)进行表面改性,最终得到高耐磨复合填料。
66.实施例6
67.一种高耐磨复合填料的制备方法,包含以下步骤:
68.分别将优质硅灰石、二氧化硅和云母原矿经粗破碎、清洗和一次破碎后,得到粒径为5~10厘米的粗粉体,再放入料仓中进行二次破碎,得到粒径为5~10毫米的粉体;将硅灰石粉体、二氧化硅粉体和云母粉体按质量比为6:3:1与8
‰
(占硅灰石粉体、二氧化硅粉体和云母粉体质量和的8
‰
)研磨助剂(具体为聚乙二醇、聚羧酸钠和木质素磺酸钠,三者质量比为2:1:1)进行干法研磨,得到粒径为20~30微米的复合粉体;
69.将所述复合粉体与水配成50%固含量的浆料,在配制过程中加入复合粉体质量10
‰
的复合分散剂(具体为月桂酸磺酸钠、十二烷基苯磺酸钠和全氟辛基磺酸钠,三者质量比为1:2:1)、10
‰
耐磨助剂(具体为psi-500聚硅氧烷偶联剂和二氧代乙酰基钛酸酯,两者质量比为1:2)和9
‰
抗静电剂(具体为单硬脂酸甘油酯、二羟乙基十八胺、甲氧基聚乙二醇-甲基丙烯酸酯共聚物,三者质量比为2:1:1),保证浆料温度在80℃进行恒温高速搅拌湿法研磨,立式搅拌机转速为2800r/min,搅拌2小时,得到粒径为2.0~3.0微米的复合浆料,再经干燥、收集和解聚打散,加入复合粉体质量15
‰
的改性剂(具体为γ-氨丙基甲基二甲氧基硅烷、γ-二乙烯三胺基丙基三甲氧基硅烷和双十八烷基二甲基氯化铵型,三者质量比为2:2:1)进行表面改性,最终得到高耐磨复合填料。
70.对本发明实施例1~6制备的高耐磨复合填料进行性能检测,测试标准参照gb/t-3249.3-2013,设置对照组1(4000目重晶石粉)、对照组2(4000目硅灰石粉)、对照组3(4000目二氧化硅粉)和对照组4(4000目云母粉),测试结果如表1所示。
71.表1本发明实施例1~6制备的高耐磨复合填料的性能数据
[0072][0073]
根据表1可知,与传统的单一耐磨矿物粉体填料,如重晶石粉、硅灰石粉、二氧化硅粉和云母粉对比,本发明提供的高耐磨复合填料的吸油值大幅降低,表面活化度大幅提升,均达97%以上,可见本发明提供的高耐磨复合填料的整体性能更优。
[0074]
对填充本发明实施例1~6制备的高耐磨复合填料的高分子材料进行性能测试,设置对照组1(4000目重晶石粉)、对照组2(4000目硅灰石粉)、对照组3(4000目二氧化硅粉)和对照组4(4000目云母粉),检测方法为:将本发明实施例1~6制备的高耐磨复合填料和对照组1~4的单一粉体分别加入tpe鞋材料中,得到测试样品;tpe鞋材料配方为:sebs300份、石蜡油300份、pp150份和高耐磨复合填料320份;耐磨性能按照gb/t1689-2014测试,拉伸和断裂性能按照gb/t1040-2006测试,拉伸速率为250mm/min,测试结果如表2所示。
[0075]
表2填充实施例1~6制备的高耐磨复合填料的高分子材料的性能数据
[0076][0077]
根据表2的结果可知,与传统的单一耐磨矿物粉体填料,如重晶石粉、硅灰石粉、二氧化硅粉和云母粉对比,本发明提供的高耐磨复合矿物粉体应用于高分子材料中具有更低的磨耗量,耐磨性能更好,同时拉伸强度和断裂伸长率比更高,填充本发明提供的高耐磨复合填料的塑料制品的综合力学性能更好。
[0078]
由以上实施例可知,本发明提供的高耐磨复合填料吸油值低,表面活化度高,可以赋予高分子材料优异的耐磨性能,解决塑料等高分子材料的耐磨性能不足的问题,同时使高分子材料获得优异的综合物理力学性能。
[0079]
尽管上述实施例对本发明做出了详尽的描述,但它仅仅是本发明一部分实施例,而不是全部实施例,还可以根据本实施例在不经创造性前提下获得其他实施例,这些实施例都属于本发明保护范围。
再多了解一些
本文用于创业者技术爱好者查询,仅供学习研究,如用于商业用途,请联系技术所有人。