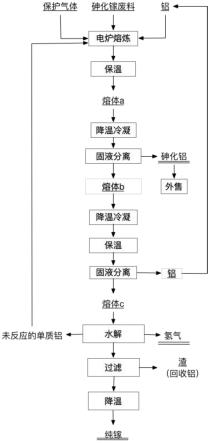
1.本发明涉及资源综合回收及高值利用领域,具体涉及一种砷化镓废料熔体萃取分离方法。
背景技术:
2.砷化镓是继单晶硅后第二代新型半导体材料中最重要、相关技术最成熟、用途最广泛的材料。其广泛用于新一代移动通讯、电子信息技术、全球卫星定位系统、巡航制导、卫星雷达等多个领域。随着相关产业的不断发展,砷化镓需求量日益攀升,产生了大量砷化镓废料;同时在砷化镓生产过程中也会产生大量的次品和边角料。砷化铝和高铝组分的algaas具有很强的选择性,而且形成的氧化层性能稳定,电绝缘性好,折射率低,这种氧化工艺在
ⅲ‑ⅴ
族半导体器件制备及光电集成中有着广阔的应用前景。现有砷化镓废料处理工艺主要有(1) 砷化镓废料硝酸分解-中和沉淀分离;(2)砷化镓废料硝酸分解-硫化沉淀分离;(3)砷化镓废料氯化分解-蒸馏分离;(4)砷化镓废料真空热分解回收镓、砷。工艺(1)、(2)、(3)为湿法处理工艺,存在工艺流程长,操作环境差,产生大量含砷废水、含碱/酸废水、含有机废水等问题。工艺(4)为火法处理工艺,具有短流程、高效等特点,但其所需温度达到1000℃以上。
3.公开号为cn 108707927 a的专利,公开了一种以含有砷化镓的废料为阳极,在含镓的碱性电解液中进行电解,得到金属镓和含有砷酸盐的电解残液的工艺,该发明关键点在于采用电化学手段处理砷化镓废料。公开号为cn 108728641 a的专利,采用酸浸-萃取-镓有机相直接电积工艺以解决砷化镓废料回收过程中电积效率低等问题。公开号为cn 106399696 a的专利,提出了一种从砷化镓芯片生产废料中制备砷的硫化物的方法,其关键在于,废料与升华硫混合均匀,在氮气氛围下进行加热反应,得到相应的硫化物。公开号为cn 106498168 a的专利,提供了一种从含油砷化镓泥浆中回收镓的方法,该方法通过采用减压蒸馏除油、控电位氧化浸出、萃取除砷、造液电解,得到金属镓。
技术实现要素:
4.本发明提供了一种砷化镓废料熔体萃取分离方法,用以解决目前现有砷化镓处理分离效率低、效果差、对环境不友好,产品附加值低或需进一步处理才可应用的技术问题。
5.为解决上述技术问题,本发明采用以下技术方案:
6.一种砷化镓废料熔体萃取分离方法,采用单质铝与所述砷化镓废料共同升温至设定温度进行熔体萃取得到熔融体系,萃取完成后对熔融体系进行分段降温、分步冷凝依次得到砷化铝、铝和镓铝合金。
7.上述技术方案的设计思路在于,发明人发现,铝熔体对砷化镓废料中的砷具备上佳的选择性,对砷对萃取效果好,因此本发明利用该特性实现选择性萃取镓、砷的分离,再通过利用砷化铝、铝、镓等物质的凝固点不同,采用分步冷凝实现砷化铝、铝及镓铝合金熔体的分离,得到砷化铝、铝和镓铝合金。上述产品中,砷化铝附加值高,且可直接进行再利
用,无需经过进一步的处理,金属铝可返回用于前步中砷化镓的熔体萃取,整体分离过程中无废渣、废水产生,工艺流程短、操作简便,具有良好的工业化应用前景。
8.作为上述技术方案的进一步优选,所述砷化镓废料熔体萃取分离方法包括以下步骤:
9.(1)将单质铝和所述砷化镓废料放入加热装置,并通入保护性气体进行升温,升温至设定温度后保温处理,得到熔体a;所述单质铝和砷化镓废料的质量比大于3:1;
10.(2)对所述熔体a进行降温,使熔体a析出砷化铝固体,分离得到砷化铝合金和熔体 b;
11.(3)对所述熔体b进行降温,使熔体b析出铝固体,分离得到单质铝和熔体c;
12.(4)对所述熔体c进行降温和搅拌,得到镓铝合金。
13.作为上述技术方案的进一步优选,步骤(1)中所述设定温度为700~900℃,保温时间为 5~10h。
14.作为上述技术方案的进一步优选,步骤(2)中对所述熔体a降温至650~800℃,并保温 4~10h使熔体a析出砷化铝固体。
15.作为上述技术方案的进一步优选,步骤(3)中对所述熔体b降温至300~650℃,并保温 3~10h使熔体b析出铝固体。
16.作为上述技术方案的进一步优选,步骤(4)中对所述熔体c降温至20~300℃,搅拌速度为10~200r/min。
17.作为上述技术方案的进一步优选,步骤(4)中得到所述镓铝合金后,对所述镓铝合金水解制得氢气和金属镓。
18.作为上述技术方案的进一步优选,所述水解操作包括以下步骤:将镓铝合金粉碎后放入水中,控制温度为60~90℃进行水解反应,收集得到氢气和反应液,将反应液过滤后冷却至 10℃,即得固体金属镓。
19.作为上述技术方案的进一步优选,步骤(1)中所述保护气体为氩气或氮气。
20.与现有技术相比,本发明的优点在于:
21.本发明采用铝熔体萃取实现砷化镓的分解,同时利用砷化铝、铝、镓等物质的凝固点不同,采用分步冷凝实现砷化铝、铝及镓铝合金熔体的分离,得到砷化铝、铝和镓铝合金;最后对镓铝合金进行水解制氢,同时产出金属镓。使用本发明所提供工艺对砷化镓废料进行处理,可实现砷化镓中砷铝的高效分离,同时得到高值产品砷化铝、铝、氢气、纯镓产品,无废含砷废水产生,工艺中所用的辅料铝除生成砷铝合金和镓铝合金水解制氢消耗外,无其他消耗,剩余的铝可继续返回铝熔体萃取工艺,实现了试剂循环利用及低消耗。
附图说明
22.图1为本发明各实施例的砷化镓废料熔体萃取分离方法的工艺流程图。
具体实施方式
23.以下结合具体实施例对本发明作进一步详细说明,下述各实施例中,“砷化镓废料”是指废弃砷化镓废料及在外延片生长、制作电极、减薄、划片以及测试等生产环节产生的边角料和残次品等,其化学成分组成如下表1所示:
24.表1各实施例中砷化镓废料化学组成(%,ωt)
25.编号ga(%)as(%)mg(%)si(%)其他砷化镓废料47520.010.0010.989
26.下述各实施例所用铝单质为购买的分析纯试剂。
27.实施例1:
28.如图1所示,本实施例的砷化镓废料熔体萃取分离方法,包括以下步骤:
29.(1)取500g砷化镓废料#1磨碎至200目后与2000g铝一起加入熔炉内(单质铝比砷化镓废料质量比为4:1),通入氮气直至完全置换炉内空气;
30.启动升温程序,升温至900℃并保温8h,得到熔体a;
31.(2)对熔体a启动降温程序降温至700℃并保温4h后进行渣液分离,得到砷化铝渣 315g(砷94.89%进入砷化铝渣)和熔体b;
32.(3)对熔体b启动降温程序,降温至300℃并保温4h,得到铝渣1728g和熔体c;
33.(4)对熔体c进行降温处理,降温的同时以20r/min进行搅拌,降温至20℃,得到凝固铝镓合金452g;将铝镓合金研磨至200目,在60℃下与水反应,收得氢气22g,过滤后将滤液降温至10℃后从溶液底部收得镓220.5g(镓回收率93.8%)。
34.实施例2:
35.如图1所示,本实施例的砷化镓废料熔体萃取分离方法,包括以下步骤:
36.(1)取500g砷化镓废料#1磨碎至200目后与3000g铝一起加入熔炉内(单质铝比砷化镓废料质量比为6:1),通入氮气直至完全置换炉内空气;启动升温程序,升温至850℃并保温10h,得到熔体a;
37.(2)对熔体a启动降温程序降温至700℃并保温6h后进行渣液分离,得到砷化铝渣 435g(砷93.62%进入砷化铝渣)和熔体b;
38.(3)对熔体b启动降温程序,降温至650℃并保温10h,得到铝渣2434g和熔体c;
39.(4)对熔体c进行降温处理,降温的同时以200r/min进行搅拌,降温至300℃,得到凝固铝镓合金926g;将铝镓合金研磨至200目,在90℃下与水反应,收得氢气70g,过滤后将滤液降温至10℃后从溶液底部收得镓211.9g(镓回收率90.2%)。
40.实施例3:
41.如图1所示,本实施例的砷化镓废料熔体萃取分离方法,包括以下步骤:
42.(1)取500g砷化镓废料#1磨碎至200目后与2000g铝一起加入熔炉内(单质铝比砷化镓废料质量比为4:1),通入氮气直至完全置换炉内空气;启动升温程序,升温至850℃并保温10h,得到熔体a;
43.(2)对熔体a启动降温程序降温至680℃并保温6h后进行渣液分离,得到砷化铝渣 335g(砷95.74%进入砷化铝渣)和熔体b;
44.(3)对熔体b启动降温程序,降温至400℃并保温4h,得到铝渣1667g和熔体c;
45.(4)对熔体c进行降温处理,降温的同时以100r/min进行搅拌,降温至100℃,得到凝固铝镓合金493g;将铝镓合金研磨至200目,在80℃下与水反应,收得氢气27g,过滤后将滤液降温至10℃后从溶液底部收得镓208.5g(镓回收率88.7%)。
46.实施例4:
47.如图1所示,本实施例的砷化镓废料熔体萃取分离方法,包括以下步骤:
48.(1)取500g砷化镓废料#1磨碎至200目后与3000g铝一起加入熔炉内(单质铝比砷化镓废料质量比为6:1),通入氮气直至完全置换炉内空气;启动升温程序,升温至900℃并保温7h,得到熔体a;
49.(2)对熔体a启动降温程序降温至700℃并保温5h后进行渣液分离,得到砷化铝渣 385g(砷99.14%进入砷化铝渣)和熔体b;
50.(3)对熔体b启动降温程序,降温至500℃并保温3h,得到铝渣2579g和熔体c;
51.(4)对熔体c进行降温处理,降温的同时以200r/min进行搅拌,降温至250℃,得到凝固铝镓合金531g;将铝镓合金研磨至200目,在80℃下与水反应,收得氢气29g,过滤后将滤液降温至10℃后从溶液底部收得镓223.7g(镓回收率95.2%)。
52.实施例5:
53.如图1所示,本实施例的砷化镓废料熔体萃取分离方法,包括以下步骤:
54.(1)取500g砷化镓废料#1磨碎至200目后与3000g铝一起加入熔炉内,通入氮气直至完全置换炉内空气;启动升温程序,升温至700℃并保温10h,得到熔体a;
55.(2)对熔体a启动降温程序降温至650℃并保温10h后进行渣液分离,得到砷化铝渣432g(砷97.87%进入砷化铝渣)和熔体b;
56.(3)对熔体b启动降温程序,降温至500℃并保温3h,得到铝渣2528g和熔体c;
57.(4)对熔体c进行降温处理,降温的同时以150r/min进行搅拌,降温至200℃,得到凝固铝镓合金535g;将铝镓合金研磨至200目,在60℃下与水反应,收得氢气27g,过滤后将滤液降温至10℃后从溶液底部收得镓221.3g(镓回收率94.2%)。
58.以上所述仅是本发明的优选实施方式,本发明的保护范围并不仅局限于上述实施例。对于本技术领域的技术人员来说,在不脱离本发明技术构思前提下所得到的改进和变换也应视为本发明的保护范围。
再多了解一些
本文用于创业者技术爱好者查询,仅供学习研究,如用于商业用途,请联系技术所有人。