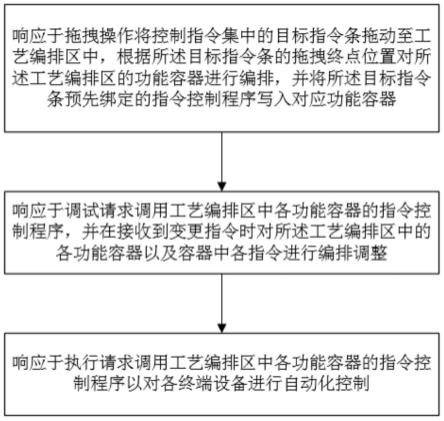
1.本发明涉及自动化控制技术领域,尤其涉及一种生产工艺编排方法、系统、设备及计算机可读存储介质。
背景技术:
2.流程行业中由于生产流程中所投入的设备数量较多,工艺流程相对复杂,解决流程行业中工艺流程的配置问题成为工业自动化控制最重要的需求。现阶段市面上推出了专门为了解决流程行业中工业配方的配置问题的软件系统,该软件系统需要专业的工控编程人员对整个生产流程进行熟悉后再编写出整个生产流程的工控程序从而实现整个工艺流程的自动化控制;但是目前该软件系统往往是设备厂商帮忙定制成较为固化的底层程序,流程行业的现场生产人员只能对该软件系统中的参数进行调整,却无法根据实际生产需求对整个生产流程进行重新编排,无法满足不同场景下的自动化生产情况。
技术实现要素:
3.为了克服现有技术的不足,本发明的目的之一在于提供一种生产工艺编排方法,让现场生产人员可根据实际生产需求随时调整配方工艺步骤,提高配置灵活性。
4.本发明的目的之二在于提供一种生产工艺编排系统,通过可视化方式进行工艺编排,大幅度提升了现场的调试速度。
5.本发明的目的之三在于提供一种电子设备。
6.本发明的目的之四在于提供一种计算机可读存储介质。
7.本发明的目的之一采用如下技术方案实现:
8.一种生产工艺编排方法,包括:
9.响应于拖拽操作将目标指令条拖动至工艺编排区中,根据所述目标指令条的拖拽终点位置对所述工艺编排区的功能容器进行编排,并将所述目标指令条预先绑定的指令控制程序写入对应功能容器中;
10.响应于执行请求依次调用工艺编排区中各功能容器所对应的指令控制程序以对各终端设备进行自动化控制。
11.进一步地,所述目标指令条预先存储于控制指令集,所述控制指令集还包括有若干个用于控制各终端设备执行动作的指令条,每个所述指令条预先绑定对应的指令控制程序。
12.进一步地,根据所述目标指令条的拖拽终点位置对所述工艺编排区的功能容器进行编排的方法为:
13.在所述拖拽操作的拖拽终点位置新建所述目标指令条所对应的功能容器,将新增的所述功能容器插入至已排序的功能容器中,并更新各功能容器间的排列顺序。
14.进一步地,还包括:
15.响应于参数设置请求对所述功能容器进行参数设置。
16.进一步地,接收所述执行请求前,还包括:
17.响应于调试请求按照各容器的编排顺序依次调用工艺编排区中各功能容器的指令控制程序,并在接收到变更指令时对所述工艺编排区中的功能容器进行编排调整。
18.本发明的目的之二采用如下技术方案实现:
19.一种生产工艺编排系统,包括:
20.前端编排模块,包括可视化界面,基于可视化界面的拖拽操作将控制指令集中的目标指令条拖动至工艺编排区中,根据所述目标指令条的拖拽终点位置对所述工艺编排区的功能容器进行编排,并将所述目标指令条预先绑定的指令控制程序写入对应功能容器;
21.后端调用模块,用于根据执行请求调用工艺编排区中各功能容器所对应的指令控制程序以对各终端设备进行自动化控制。
22.进一步地,所述可视化界面中每个所述功能容器均设有指令编辑按键,通过指令编辑按键对功能容器进行参数设置。
23.进一步地,还包括:
24.错误提醒模块,在运行各功能容器的指令控制程序时若出现报错情况则立即做出告警提醒。
25.本发明的目的之三采用如下技术方案实现:
26.一种电子设备,其包括处理器、存储器及存储于所述存储器上并可在所述处理器上运行的计算机程序,所述处理器执行所述计算机程序时实现如上述的生产工艺编排方法。
27.本发明的目的之四采用如下技术方案实现:
28.一种计算机可读存储介质,其上存储有计算机程序,所述计算机程序被执行时实现如上述的生产工艺编排方法。
29.相比现有技术,本发明的有益效果在于:
30.本发明预先将每个终端设备的指令控制程序预先封装为对应的指令条,现场人员通过拖拽操作将控制指令集中的目标指令条拖动至工艺编排区中,即可根据所述目标指令条的拖拽终点位置对所述工艺编排区的功能容器进行编排,从而将目标指令条按照现场人员需求添加至工艺流程中,使得工艺流程配置不再固化,做到随时调整工艺流程步骤的效果,提高配置灵活性。
附图说明
31.图1为本发明生产工艺编排方法的流程示意图;
32.图2为本发明可视化界面图;
33.图3为本发明各功能容器编辑界面图之一;
34.图4为本发明各功能容器编辑界面图之二;
35.图5为本发明并行容器的编辑界面图;
36.图6为本发明生产工艺编排系统的模块示意图。
具体实施方式
37.下面,结合附图以及具体实施方式,对本发明做进一步描述,需要说明的是,在不
相冲突的前提下,以下描述的各实施例之间或各技术特征之间可以任意组合形成新的实施例。
38.实施例一
39.本实施例提供一种生产工艺编排方法,该方法应用在内容管理系统(content management system,cms)上,通过创建的工艺编排工具搭建工艺流程逻辑,最终形成所需的工艺配方流程。
40.如图1所示,所述生产工艺编排方法具体包括如下步骤:
41.步骤s1:响应于拖拽操作将控制指令集中的目标指令条拖动至工艺编排区中,根据所述目标指令条的拖拽终点位置对所述工艺编排区的功能容器进行编排,并将所述目标指令条预先绑定的指令控制程序写入对应功能容器。
42.步骤s2:响应于执行请求调用工艺编排区中各功能容器的指令控制程序以对各终端设备进行自动化控制。
43.本实施例中预先将工艺流程中各个终端设备的指令控制程序逐一进行编写后封装为若干个指令条,每个指令条都代表着一个终端设备执行一个或多个动作。其中所述终端设备可以是电机、阀门、温控器等设备。与此同此,根据设备类型抽象为一个通用的功能容器,将各功能容器按照工艺流程进行搭建和拼接,最终可形成现场需要的工艺配方。
44.如图2所示,所述内容管理系统设有可视化界面,在可视化界面中主要划分为控制指令集以及工艺编排区,所述控制指令集中展示有所有预先编写好指令控制程序的指令条;本实施例中所述控制指令集包括有设备指令条以及系统指令条,其中设备指令条用于与底层设备交互参数信息,系统指令则是工艺引擎内按照本身逻辑执行的。图2中虚线所框住的指令条为所述设备指令条,其可根据实际工艺流程所使用到的设备进行设计,例如包括预混缸设备的指令条、调漆缸设备的指令条等;所述系统指令条则包括qc质检、定时指令、循环指令、流程分支、智能投料、串行容器、并行容器、提示指令等。
45.现场人员通过拖拽操作将控制指令集中的任一目标指令条拖动至可视化界面中的工艺编排区中,在工艺编排区中根据目标指令条的设备类型生成对应的功能容器,根据各功能容器在工艺编排区中的编排顺序分别调动对应的终端设备执行对应的控制操作,从而将各设备动作编排串联起来形成完整的生产工艺流程。
46.当现场人员执行拖拽操作时,系统识别所述拖拽操作的起点位置和终点位置,将起点位置所对应的指令条标记为目标指令条,经过拖拽操作后在所述拖拽操作的拖拽终点位置新建所述目标指令条所对应的功能容器,并将新增的所述功能容器插入工艺编排区中已排列好的功能容器中。同时根据拖拽的终点位置的坐标以及所述工艺编排区中原有的功能容器的区域坐标确定新建的功能容器与其周边原有的功能容器的顺序关系,根据该顺序关系重新调整所述工艺编排区中各功能容器间的排列顺序。
47.现场人员可通过拖拽方式新建功能容器,并对工艺编排区中各功能容器进行顺序编排外,还可对每个功能容器进行独立的参数设置;当系统接收到现场人员发起的参数设置请求后,系统即可根据现场人员所编辑的内容对各功能容器的运行参数进行自定义设置;结合图3、图4和图5所示,其自定义设置方法为:
48.若将qc质检的指令条添加至工艺编排区,则代表需要进行质检环节,若qc质检环节合格,则可按照配方顺序执行后续指令;若qc质检环节不合格,系统进行弹窗提醒并重新
进入编排界面进行步骤编排。
49.若将定时指令添加至工艺流程的任一环节中,可对定时的时间进行设置,则代表工艺流程运行到该环节时,系统按照设定时间等待一定秒数后才按照配方顺序继续执行。
50.若将循环指令的指令条添加至工艺编排区生成对应的功能容器,则可对循环次数进行设置,还可将其他指令条添加至循环指令的功能容器中,并对所有在该功能容器中的指令循环预设次数后跳出循环,然后继续按照配方顺序执行。
51.将流程分支的指令条添加至工艺编排区生成流程分支容器,该容易内可供生产人员选择不同分支的配方内容往下执行。
52.将智能投料的指令条添加至工艺编排区生成智能投料容器,智能投料容器中的配方指令,按照序号顺序轮询判断指令是否可执行,直至完成容器内所有指令内容。
53.提示指令则用于人为设定提示指令内容,配方执行过程中人为确定后,才可继续按照配方顺序执行。
54.将串行容器的指令条添加至工艺编排区后,还可在串行容器中添加多个指令或容器,串行容器内的指令或容器按照顺序依次执行。
55.将并行容器的指令条添加至工艺编排区后,并行容器内可配置任意指令或容器,使得该容器内指令或容器同时执行。参考图5所示,序号3的并行容器中可根据实际需求添加系统指令条以进一步构建起串行容器、流程分支容器等,还可在每个容器中进一步自定义设置对应的设备指令条,以实现完整工艺流程。
56.当现场人员完成工艺编排区中各功能容器的编排和设置后,可发起调试请求,系统响应于调试请求即可根据工艺编排区中各功能容器的编排顺序依次调用各功能容器所对应的指令控制程序,以对编排好的整个工艺流程进行测试;期间,若在测试过程中出现逻辑上的错误则可自动生成告警提示,现场人员发现工艺流程上的错误后即可发出变更指令以对工艺编排区中的各功能容器以及各指令进行重新编排和调整,确保整个工艺流程与现场人员所需的工艺流程相符。
57.在测试通过后即可投入实际生产中,实际生产中现场人员发起执行请求,系统响应于执行请求调用工艺编排区中各功能容器中各指令的指令控制程序以对各终端设备进行自动化控制。
58.本实施例通过可视化界面对整个工艺流程进行灵活配置,使得工艺配方不再固化,可直接面向现场生产人员,真正做到随时调整配方工艺步骤,而非只能调整参数;此外,在实际使用过程中通过简单的拖拽方式即可编排整个工艺流程,无需根据项目耗费大量精力去编写底层程序,由系统软件调用各功能容器中各指令的指令控制程序来实现自动化控制,可简化开发难度和降低对人员的专业要求,同时还可提升了现场的调试速度和交付速度,适用于各流程行业。
59.实施例二
60.本实施例提供一种生产工艺编排系统,所述系统执行如实施例一所述的生产工艺编排方法,如图6所示,所述系统包括有前端编排模块和后端调用模块。
61.所述前端编排模块包括可视化界面,基于可视化界面的拖拽操作将控制指令集中的目标指令条拖动至工艺编排区中,根据所述目标指令条的拖拽终点位置对所述工艺编排区的功能容器进行编排,并将所述目标指令条预先绑定的指令控制程序写入对应功能容
器;
62.所述后端调用模块则用于根据执行请求调用工艺编排区中各功能容器的指令控制程序以对各终端设备进行自动化控制。
63.现场人员可通过前端编排模块的可视化界面进行工艺流程编排,在整个工艺流程编排完成后通过所述后端调用模块调用相应指令控制程序以实现整个工艺流程的自动化控制。
64.而在所述可视化界面中每个所述功能容器上都设有指令编辑按键,现场人员可按下指令编辑按键后录入自定义参数以对功能容器进行参数设置。
65.此外,所述系统还包括有错误提醒模块,在运行各功能容器的指令控制程序时若系统出现报错情况则立即做出告警提醒,现场人员发现工艺流程上的错误后即可发出变更指令以对工艺编排区中的各功能容器进行重新编排和调整,确保整个工艺流程与现场人员所需的工艺流程相符。
66.在一些实施例中,还提供一种电子设备,其包括处理器、存储器及存储于所述存储器上并可在所述处理器上运行的计算机程序,所述处理器执行所述计算机程序时实现实施例一中的生产工艺编排方法;
67.另外,在一些实施例中,还提供一种计算机可读存储介质,其上存储有计算机程序,所述计算机程序被执行时实现实施例一中的生产工艺编排方法。
68.上述系统、设备及存储介质与前述实施例中的方法是基于同一发明构思下的多个方面,在前面已经对方法实施过程作了详细的描述,所以本领域技术人员可根据前述描述清楚地了解本实施例中的系统、设备及存储介质的结构及实施过程,为了说明书的简洁,在此就不再赘述。
69.上述实施方式仅为本发明的优选实施方式,不能以此来限定本发明保护的范围,本领域的技术人员在本发明的基础上所做的任何非实质性的变化及替换均属于本发明所要求保护的范围。
再多了解一些
本文用于创业者技术爱好者查询,仅供学习研究,如用于商业用途,请联系技术所有人。