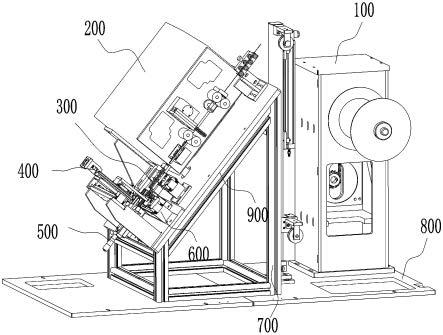
1.本发明涉及火工品制造领域,特别是一种脚线打磨组件、脚线打磨机构和脚线制备装置。
背景技术:
2.塑料插塞是电雷管的核心元件,主要由脚线和圆柱状塑料构成,脚线用于电雷管工作时的电流传导,塑料插塞制造过程采用热固性塑料模压成型。塑料插塞脚线原材料为漆包铜线,其原始状态为盘绕在塑料圆盘上的线卷,在塑料插塞模压成型前,需要先将原始漆包铜线进行定长裁剪。塑料插塞模压成型时,为提高脚线与模压塑料的结合力,防止脚线松动使塑料插塞桥路电阻受到影响,塑料插塞在模压前,脚线局部需进行漆层去除和芯线毛化处理,即将脚线局部的表层漆层去除,并在金属芯线表面形成一定深度凹凸痕迹。
3.目前,塑料插塞脚线制备通过定长裁剪、局部去漆毛化过程2个独立的步骤完成,首先使用电脑剥线机定长裁剪漆包铜线,裁剪过程中人工辅助进行放线操作,防止漆包线与电脑剥线机轮组间打滑影响造成长度超差;漆包线定长裁剪后,再由操作者将已裁剪的单根漆包线在工装中采用锉刀局部修锉实现漆层去漆和芯线毛化。
4.目前,针对漆包线漆层去除,工程上应用比较广泛的方法有激光去除和旋转打磨方式,激光去除漆层和旋转打磨两种方式不能在芯线表面形成一定深度凹凸痕迹,难以满足塑料插塞脚线的毛化要求。
5.目前的塑料插塞脚线制备方式下,存在制备一致性控制难、人工成本高和效率低等不足。
技术实现要素:
6.本发明的目的在于克服现有技术的缺点,提供一种脚线打磨组件、脚线打磨机构和脚线制备装置,解决现有技术制备一致性控制难、人工成本高和效率低等不足。
7.本发明的目的通过以下技术方案来实现:一种脚线打磨组件,包括第四直线模组、横向设置的第三直线模组和凹模,凹模上纵向开设有第二纵向滑槽,凹模上横向开设有横向凹槽,线材可转动的放置在第二纵向滑槽内,且线材的上外缘突出横向凹槽的槽底,第三直线模组上安装有第四直线模组,且第四直线模组可沿第三直线模组横向移动,第四直线模组上安装有第二滑座,第二滑座位于凹模的上方,且第二滑座通过第四直线模组远离或靠近凹模,第二滑座上安装有与第二滑座移动方向平行的直线移动副,直线移动副上安装有滑板,滑板的底部安装有可插入横向凹槽内的打磨件,滑板的顶部安装有拉簧,拉簧的另一端与第二滑座连接。
8.可选的,脚线打磨组件还包括清扫机构,在第四直线模组沿第三直线模组横向过程中,打磨件的打磨端通过清扫机构清扫。
9.可选的,清扫机构包括折弯的固定架,固定架的一端与第三直线模组的架体连接,固定架的另一端安装有柔软的清扫件。
10.可选的,直线移动副包括滑块和导轨,滑块安装在滑板上靠近第二滑座的侧壁上,滑块上开设有导向滑槽,导轨安装在第二滑座上,且导向滑槽滑动配合在导轨上,滑板的顶部安装有一支板,拉簧的一端安装在支板上,且拉簧的拉伸方向与滑板的移动方向平行。
11.一种脚线打磨机构,包括倾斜的安装板、安装板上安装有定位调节机构和工位切换机构,还安装有上述脚线打磨组件,脚线打磨组件的凹模安装在工位切换机构上,工位切换机构具有打磨工位和卸料工位,凹模在打磨工位完成线材上料和线材打磨,凹模在卸料工位完成线材卸料,定位调节机构位于工位切换机构的打磨工位后侧,且打磨工位上的线材后端抵在定位调节机构上。
12.可选的,工位切换机构包括支座、第二直线模组和凹模定位板,支座安装在安装板上,第二直线模组安装在支座上,凹模定位板安装在第二直线模组上,且第二直线模组工作带动凹模定位板横向移动,凹模安装在凹模定位板上,凹模定位板位于第二直线模组的中部时,凹模处于打磨工位,凹模定位板位于第二直线模组的两端时,凹模处于卸料工位。
13.可选的,第二直线模组的端部安装有通气块,通气块从第二纵向滑槽的进料端往第二纵向滑槽的出料端吹风。
14.可选的,定位调节机构包括调节支座、调节件和定位挡块,调节支座安装在安装板上,调节支座上纵向开设有第三纵向滑槽,定位挡块上设置有滑杆,滑杆滑动配合在第三纵向滑槽内,调节件通过螺纹安装在调节支座上,且调节件的顶端穿入第三纵向滑槽内,且调节件的顶端抵在滑杆上。
15.一种脚线制备装置,包括放线机构、剥线机和上述的脚线打磨机构,剥线机安装在脚线打磨机构的安装板上,且剥线机位于脚线打磨机构的前方,放线机构位于安装板的前方,且放线机构放出的线材进入到剥线机内,线材通过剥线机牵引、校直和剪切后进入到脚线打磨机构的第二纵向滑槽内。
16.可选的,安装板上还安装有缓存机构,当打磨机构在对线材进行打磨时,放线机构剪切后的线材则缓存在缓存机构内。
17.可选的,缓存机构包括支撑架、挡板和导向板,支撑架的顶部安装有第一直线模组,第一直线模组上安装有缓存座,缓存座上安装有接料板,且接料板在第一直线模组的作用下横向移动,接料板上开设有第一纵向滑槽,挡板位于第一直线模组的后侧,且挡板安装在升降元件上,升降元件安装在安装板上,当接料板在缓存线材时,挡板通过升降元件挡在第一纵向滑槽和打磨工位上的第二纵向滑槽之间,且第一纵向滑槽与打磨工位上的第二纵向滑槽之间的间距小于线材的1/2长度,导向板位于第一直线模组的前方,且导向板上纵向开设有导向槽,且导向板安装在导向支架上,导向支架安装在安装板上。
18.可选的,脚线打磨机构的工位切换机构上安装有两个横向并排的凹模,当一凹模位于打磨工位时,另一凹模位于卸料工位。
19.可选的,放线机构包括驱动单元和立架,驱动单元的转轴上安装有可拆卸的料盘,立架位于料盘与剥线机之间,立架的顶部安装有可转动的上滑轮,立架的底部竖向安装有滑轨,滑轨上安装有第一滑座,第一滑座上安装有下滑轮,料盘上的线材依次绕过下滑轮和上滑轮并最终通过剥线机的牵引组件牵引,立架上还安装有检测第一滑座位置的传感器,传感器均与剥线机和驱动单元信号连接。
20.本发明具有以下优点:
1、本发明的脚线打磨组件采用压力控制往复修锉去漆和芯线毛化,提高了脚线制备质量一致性,解决了脚线制备一致性控制难的问题;2、本发明的脚线制备装置采用多工位连续无人化操作,降低了人工成本,提高了脚线制备效率。
附图说明
21.图1 为脚线制备装置的结构示意图;图2 为放线机构的结构示意图;图3 为缓存机构的结构示意图;图4 为工位切换机构的结构示意图;图5 为脚线打磨组件的结构示意图;图6 为定位调节机构的结构示意图;图7 为剥线机、缓存机构、脚线打磨机构的相对位置示意图;图8 为凹模的结构示意图;图中,100-放线机构,200-剥线机,300-缓存机构,400-脚线打磨机构,500-定位调节机构,600-工位切换机构,700-斜坡支架,800-机架平台,900-安装板,101-料盘,102-转轴,103-下滑轮,104-第一滑座,105-滑轨,106-立架,107-上滑轮,108-传感器,109-驱动单元,201-牵引组件、202-校直组件,203-剪切组件,301-接料板,302-第一直线模组,303-挡板,304-升降元件,305-支撑架,306-第一通气块,307-导向支架,308-导向板,309-第一纵向滑槽,310-导向滑槽,311-缓存座,401-打磨支架,402-第三直线模组,403-第四直线模组,404-第二滑座,405-直线移动副,406-滑板,407-拉簧,408-压板,409-打磨件,410-清扫件,411-固定架,412-模组连接板,501-定位挡块,502-第三纵向滑槽,503-调节件,504-调节支座,601-前凹模,602-后凹模,603-第二通气块,604-第三通气块,605-第二直线模组,606-凹模定位板,607-支座,608-横向凹槽,609-第二纵向滑槽,610-凹模。
具体实施方式
22.如图1所示,一种脚线制备装置,包括放线机构100、剥线机200和脚线打磨机构400,在本实施例中,以线材的移动方向为后,剥线机200安装在脚线打磨机构400的安装板900上,且剥线机200位于脚线打磨机构400的前方,放线机构100位于安装板900的前方,且放线机构100放出的线材进入到剥线机200内,如图4所示,线材通过剥线机200牵引、校直和剪切后进入到脚线打磨机构400的第二纵向滑槽609内,在本实施例中,如图7所示,剥线机200属于市购产品,剥线机200具有牵引组件201、校直组件202和剪切组件203,牵引组件201包括若干压紧轮组,线材通过牵引组件201送料,即压紧轮组转动开始送料,到达设备的制备长度后,将线材切断,由于在本技术中,如图1所示,安装板900是倾斜安装的,在机架平台800上安装有斜坡支架700,安装板900则安装在斜坡支架700的斜面上,因此安装板900是倾斜的,在本实施例中,安装板900的倾斜角度以能够让线材在重力作用下滑动为准,优选的,斜坡支架700的斜面与水平面之间的夹角为50
°
,进一步的,剥线机200和脚线打磨机构400是垂直安装在安装板900后,因此剥线机200和脚线打磨机构400与水平面之间也存在夹角,当斜坡支架700的斜面与水平面之间的夹角为50
°
时,则剥线机200和脚线打磨机构400与水
平面之间的夹角则为40
°
,由于剥线机200和脚线打磨机构400与水平面存在夹角,被剪切后的线材则滑入到脚线打磨机构400上,完成线材的打磨。
23.在本实施例中,为了保证线材的打磨效率,在线材打磨的时候,剥线机200依然能够间歇性的输送切断后的线材,如图1所示,安装板900上还安装有缓存机构300,当打磨机构在对线材进行打磨时,如图3所示,放线机构100剪切后的线材则缓存在缓存机构300内。在本实施例中,缓存机构300包括支撑架305、挡板303和导向板308,支撑架305的顶部安装有第一直线模组302,第一直线模组302上安装有缓存座311,缓存座311上安装有接料板301,且接料板301在第一直线模组302的作用下横向移动,第一直线模组302的主要作用是为了实现接料板301的横向移动,因此第一直线模组302实现的方式可以有多种,接料板301上开设有第一纵向滑槽309,为了增加缓存机构300缓存线材的个数,接料板301上则开设有若干横向并排的第一纵向滑槽309,优选的,第一纵向滑槽309的数量为三条,因此第一纵向滑槽309在工作时,需要间歇性的带动接料板301横向移动,当接料板301储料完成后,接料板301上的线材进入到脚线打磨机构400后,接料板301还需要复位,因此,第一直线模组302优选的选用由伺服电机驱动的丝杠传动机构。
24.在本实施例中,如图3所示,挡板303位于第一直线模组302的后侧,且挡板303安装在升降元件304上,升降元件304安装在安装板900上,当接料板301在缓存线材时,挡板303通过升降元件304挡在第一纵向滑槽309和打磨工位上的第二纵向滑槽609之间,且第一纵向滑槽309与打磨工位上的第二纵向滑槽609之间的间距小于线材的1/2长度,因此升降元件304工作,挡板303升起后,挡板303能够挡住线材,避免接料板301上缓存的线材掉出接料板301,同时也避免了当挡板303复位后,线材在进入到脚线打磨机构400的过程中掉落,优选的,升降元件304选用升降气缸。
25.在本实施例中,如图3所示,导向板308位于第一直线模组302的前方,且导向板308上纵向开设有导向槽,且导向板308安装在导向支架307上,导向支架307安装在安装板900上,在线材缓存过程中,接料板301每间歇性的移动一次,接料板301上则具有一第一纵向滑槽309与导向槽正对,而当线材在被剪切时,线材至少有1/2以上的长度位于导向槽内,当线材被剪切后,线材则在重力作用下通过导向槽的导向滑入到接料板301的第一纵向滑槽309内,且线材的后端则被挡住,进一步的,在剥线机200的后端还具有一组压紧轮组,该压紧轮组位于剪切组件203与导向板308之间,当线材被剪切后,该压紧轮组转动,可以给线材一个初始的速度,进而保证了线材在重力的作用下进入到第一纵向滑槽309内的可靠性。
26.在本实施例中,如图2所示,放线机构100包括驱动单元109和立架106,驱动单元109的转轴102上安装有可拆卸的料盘101,驱动单元109包括伺服电机和安装伺服电机的箱体,箱体安装在机架平台800上,而伺服电机则安装在箱体内,通过伺服电机转动,进而带动料盘101转动,从而实现放线,属于现有技术,因此则不再进行赘述,在本实施例中,立架106位于料盘101与剥线机200之间,而立架106也安装在机架平台800上,立架106的顶部安装有可转动的上滑轮107,立架106的底部竖向安装有滑轨105,滑轨105上安装有第一滑座104,第一滑座104上安装有下滑轮103,为了保证第一滑座104和滑轨105滑动配合的可靠性,优选的,第一滑座104上开设的是燕尾槽,料盘101上的线材依次绕过下滑轮103和上滑轮107并最终通过剥线机200的牵引组件201牵引,在本实施例中,如图4所示,立架106上还安装有检测第一滑座104位置的传感器108,传感器108均与剥线机200和驱动单元109信号连接,工
作时,放线机构100先进行放线,使得下滑轮103位于下行程,此时传感器108检测到第一滑座104处于下行程后,传感器108将信号发送给驱动单元109,该驱动单元109的伺服电机停止工作,然后剥线机200的牵引机构则开始工作,剥线机200的牵引机构将线材往后输送,此时线材对下滑轮103具有一上行的拉力,第一滑座104在拉力的作用下上行,当第一滑座104移动到上行程后,此时,传感器108则将信号分别给剥线机200和驱动单元109的伺服电机,如图7所示,剥线机200的剪切组件203则将线材进行剪切,且剥线机200的牵引组件201则停止工作,而此时,驱动单元109的伺服电机工作,料盘101则开始放线,下滑轮103又开始下行,在本实施例中,下滑轮103和上滑轮107在上行和下行的过程中,线材都处于绷直状态,因此,通过传感器108检测第一滑座104的上行程和下行程,然后剥线机200和驱动单元109根据传感器108的检测信号,可以控制线材放线的长度,以及线材剪切后的长度,保证线材剪切后的长度一致。
27.在本实施例中,如图1所示,脚线打磨机构400包括倾斜的安装板900,安装板900上安装有定位调节机构500、工位切换机构600和脚线打磨组件, 如图4所示,脚线打磨组件的凹模610安装在工位切换机构600上,如图1所示,定位调节机构500位于工位切换机构600的打磨工位后侧,且打磨工位上的线材后端抵在定位调节机构500上,如图3所示,挡板303下行后,接料板301上的线材则进入到脚线打磨组件上,此时线材的后端则抵在定位调节机构500上,由于线材的长度是一致的,而定位调节机构500的位置在设定好后也是一致的,因此线材上的打磨区域也就是一致的,从而能够保证线材加工的一致性,而打磨好的线材,则通过工位切换机构600切换到卸料工位,然后完成线材的卸料。
28.在本实施例中,如图5所示,脚线打磨组件包括第四直线模组403、横向设置的第三直线模组402和凹模610,第三直线模组402上具有打磨支架401,打磨支架401安装在安装板900上,优选的,打磨支架401为龙门架,如图4所示,凹模610上纵向开设有第二纵向滑槽609,凹模610上横向开设有横向凹槽608,凹模610则安装在工位切换机构600上,在本实施例中,工位切换机构600具有打磨工位和卸料工位,凹模610在打磨工位完成线材上料和线材打磨,凹模610在卸料工位完成线材卸料,当凹模610处于打磨工位时,第二纵向滑槽609则与对应的第一纵向滑槽309处于同一直线上,因此第一纵向滑槽309内的线材能够轻易的进入到第二纵向滑槽609内,当然,为了进一步保证线材能够从第一纵向滑槽309滑入到第二纵向滑槽609内,而第二纵向滑槽609的进料口呈y形,同理,如图3所示,第一纵向滑槽309的进料口和导向滑槽310的进料口均呈y形,进一步的,如图8所示,线材可转动的放置在第二纵向滑槽609内,优选的,第二纵向滑槽609的槽宽大于线材的周长,进一步的,导向滑槽310、第一纵向滑槽309和第二纵向滑槽609的槽宽一致,因此线材则可以在第二纵向滑槽609内转动,在本实施例中,线材的上外缘突出横向凹槽608的槽底,从而可以将线材的打磨区突出横向凹槽608的槽底,从而便于打磨,为了防止线材修锉弯曲,第二纵向滑槽609的深度与横向凹槽608的深度差应与线材的打磨直径相当,如据线材直径0.6mm,毛化直径0.56mm
±
0.03mm,此处第二纵向滑槽609的深度与横向凹槽608的深度差则为0.5mm。
29.在本实施例中,如图5所示,第三直线模组402上通过模组连接板412安装有第四直线模组403,且第四直线模组403可沿第三直线模组横向移动,第四直线模组403上安装有第二滑座404,第二滑座404位于凹模610的上方,且第二滑座404通过第四直线模组403远离或靠近凹模610,即第四直线模组403和第三直线模组在第三直线模组的所在的投影面上是正
交的,第二滑座404上安装有与第二滑座404移动方向平行的直线移动副405,直线移动副405上安装有滑板406,滑板406的底部安装有可插入横向凹槽608内的打磨件409,在本实施例中,打磨件409呈l形块状体,在滑板406的底部开设有插槽,打磨件409的顶部则插入到插槽内,然后在滑板406上通过锁紧螺钉安装有压板408,锁紧螺钉锁紧后,压板408则压住打磨件409,从而实现打磨件409的安装,进一步的,打磨件409的顶部直接插入到插槽的槽底,因此打磨件409的顶部与插槽则具有足够的接触面积,另外再在压板408的压力作用下,从而打磨件409在横向移动过程中,然后能够相对滑板406静止,滑板406的顶部安装有拉簧407,拉簧407的另一端与第二滑座404连接,当第二纵向滑槽609内线材上料完成后,第三直线模组402则开始工作,第四直线模组403则沿第三直线模组402横向移动,从而带动打磨件409横向移动,当第四直线模组403移动到制定位置后,第四直线模组403则开始工作,使得打磨件409朝向横向凹槽608移动,并最终进入到横向凹槽608内,当打磨件409与线材接触后,此时打磨件409则无法继续移动,此时第四直线模组403持续工作,由于打磨件409无法继续移动,此时滑板406的顶部与第四直线模组403的顶部之间的间距则会缩短,而滑动板的顶部与第二滑座404之间的间距则会增大,因此拉簧407则被拉伸,由于拉簧407拉伸后,因此拉簧407则对滑板406具有一拉力,从而使得打磨件409与线材之间则会产生预压力,然后第三直线模组402在再工作,从而带动第四直线模组403横向移动,第四直线模组403在横向移动过程中,从而对线材进行打磨,由于打磨件409与线材之间具有预压力,在打磨件409横向移动过程中,打磨件409则会带动线材圆周滚动,进而对打磨件409的打磨区域进行圆周打磨,优选的,打磨件409的打磨端开设有若干锯齿槽,锯齿槽在横向移动过程中,能够与线材的外缘发生相对移动,同时线材也在锯齿槽与线材的摩擦力的作用下周向转动。
30.在本实施例中,线材在打磨后,会产生碎屑,部分碎屑则在吸附在打磨件409上,为了避免碎屑影响线材的打磨精度,需要对打磨件409上的碎屑进行清扫,因此,如图5所示,脚线打磨组件还包括清扫机构,在第四直线模组403沿第三直线模组402横向过程中,打磨件409的打磨端通过清扫机构清扫,进一步的,清扫机构包括折弯的固定架411,固定架411的一端与第三直线模组402的架体连接,即固定架411的一端与打磨支架401连接,固定架411的另一端安装有柔软的清扫件410,优选的,清扫件410为毛刷,而固定架411呈l形,在打磨工位的投影面上,清扫件410位于打磨工位的一侧,因此打磨件409在对线材打磨的过程中,清扫件410不会对线材的打磨造成影响,而当线材打磨完成后,第四直线模组403工作带动滑板406以及打磨件409复位,然后第三直线模组402工作,带动第四直线模组403复位,而第四直线模组403复位的过程中,打磨件409的打磨端则与清扫件410发生干涉,清扫件410则对打磨件409进行清扫,从而清理到打磨件409上的碎屑,而第四直线模组403复位后,打磨件409则需要越过清扫件410,而当需要对线材打磨时,第四直线模组403在到达打磨工位上方的过程中,打磨件409又会与清扫件410发生干涉,因此又能对打磨件409进行清扫,保证打磨件409的洁净度,从而保证线材打磨的精度。
31.在本实施例中,第三直线模组402和第四直线模组403都是实现直线往复运动,因此实现的方式有多种,可以通过市购获得,优选的,第三直线模组402和第四直线模组403均为带伺服电机的丝杠传动机构,当伺服电机接收到执行信号后,伺服电机则带动对应的丝杠传动机构工作。
32.在本实施例中,如图5所示,直线移动副405包括滑块和导轨,滑块安装在滑板406
上靠近第二滑座404的侧壁上,滑块上开设有导向滑槽310,导轨安装在第二滑座404上,且导向滑槽310滑动配合在导轨上,滑板406的顶部安装有一支板,拉簧407的一端安装在支板上,且拉簧407的拉伸方向与滑板406的移动方向平行,由于第二滑座404的移动方向与水平面具有夹角,因此无需担心第二滑座404脱离滑块,当然为了保证第二滑座404滑动的可靠性,导向滑槽310则为燕尾槽,而导轨则为与导向滑槽310滑动配合的燕尾块,另外在滑板406的顶部安装支板,拉簧407安装后,拉簧407的一端在支板上,拉簧407的另一端在第二滑座404上,优选的,第二滑座404的横向外侧壁上设置有横向支出的挂柱,而支板的横向外侧壁上也设置有指出的柱体,而拉簧407顶部为一圆环,该圆环则挂在柱体上,优选的,柱体为螺杆,柱体与支板的连接为螺纹连接,而拉簧407的底部则具有挂钩,挂钩则勾在挂柱上,当拉簧407安装完成后,拉簧407的拉伸方向与滑板406的移动方向平行,因此当拉簧407拉伸后,其拉力的方向与滑板406的移动方向平行,从而能够更好的控制打磨件409对线材的预压力,在本实施例中,拉簧407为两个,分别位于滑板406的横向两侧。
33.在本实施例中,如图6所示,定位调节机构500位于工位切换机构600的打磨工位后侧,且打磨工位上的线材后端抵在定位调节机构500上,进一步的,定位调节机构500包括调节支座504、调节件503和定位挡块501,调节支座504安装在安装板900上,调节支座504上纵向开设有第三纵向滑槽502,定位挡块501上设置有滑杆,滑杆滑动配合在第三纵向滑槽502内,调节件503通过螺纹安装在调节支座504上,且调节件503的顶端穿入第三纵向滑槽502内,且调节件503的顶端抵在滑杆上,优选的,定位挡块501为t型结构,其定位挡块501的纵向杆则为滑杆,而为了保证定位挡块501安装的可靠性,第三纵向滑槽502可为燕尾槽,当然也可以在第三纵向滑槽502的横向侧壁上纵向开设条形槽,而滑杆则按照第三纵向滑槽502的结构进行相适配即可,在本实施例中,调节件503优选的采用螺旋千分尺,而螺旋千分尺纵向安装,通过调节螺旋千分尺,从而可以通过螺旋千分尺的顶部顶住定位挡块501,然后控制定位挡块501的位置,进而控制定位挡块501与凹模610之间的间距,从而可以控制线材的打磨位置,在本实施例中,对于同一型号的线材,当定位挡块501的位置控制好后,其定位挡块501的位置则不变。
34.在本实施例中,如图4所示,工位切换机构600包括支座607、第二直线模组605和凹模定位板606,支座607安装在安装板900上,第二直线模组605安装在支座607上,凹模定位板606安装在第二直线模组605上,且第二直线模组605工作带动凹模定位板606横向移动,凹模610安装在凹模定位板606上,凹模定位板606位于第二直线模组605的中部时,凹模610处于打磨工位,凹模定位板606位于第二直线模组605的两端时,凹模610处于卸料工位,优选的,第二直线模组605为带伺服电机的丝杠传动机构,第二直线模组605的端部安装有通气块,通气块从第二纵向滑槽609的进料端往第二纵向滑槽609的出料端吹风,由于线材打磨后,线材的打磨区域与第二纵向滑槽609的摩擦力则会增加,通过通气块的辅助,通气孔吹出来的风,能够对夹线的滑动起到推动作用,因此线材在重力和风力的作用下,能够可靠的从第二纵向滑槽609滑出,进而完成线材的卸料,而且通气孔吹出来的风,还能够对第二纵向滑槽609内的打磨碎屑进行清理,避免碎屑对线材的打磨造成影响。
35.在本实施例中,如图4所示,脚线打磨机构400的工位切换机构600上安装有两个横向并排的凹模610,当一凹模610位于打磨工位时,另一凹模610位于卸料工位,在本实施例中,两个凹模610则为第一凹模和第二凹模,而第二直线模组605的横向两端则为卸料工位,
由于有两个卸料工位,因此通气块也为两个,即第二通气块603和第三通气块604,当第一凹模位于打磨工位时,线材则从第一纵向滑槽309滑入到第一凹模的第二纵向滑槽609内,并完成线材的打磨,而第二凹模则在卸料工位,与第二凹模同侧的第三通气块604则吹出气体对线材的卸料提供助力,同时对第二凹模进行气吹清理,而当第二凹模位于打磨工位时,线材则从第一纵向滑槽309滑入到第二凹模的第二纵向滑槽609内,并完成线材的打磨,而第一凹模则在卸料工位,与第一凹模同侧的第二通气块603则吹出气体对线材的卸料提供助力,同时对第一凹模进行气吹清理,在本实施例中,为了保证第一纵向滑槽309内的线材能够顺利的滑动到第二纵向滑槽609内,在接料板301的进料端安装有第一通气块306,当挡板303位于下行程后,此时第一通气块306吹气,第一纵向滑槽309内的线材在重力和气流的推动作用下滑出第一纵向滑槽309。
36.利用上述装置进行脚线制备的方法如下:包括以下步骤:s1:如图2所示,将料盘101安装在驱动单元109的转轴102上,并在转轴102的末端使用旋拧压紧固定;s2:如图2所示,牵引线材端头使线材分别绕过下滑轮103、上滑轮107,然后分别穿过剥线机200的牵引组件201、校直组件202、剪切组件203,整理线材使下滑轮103处于提升状态;s3:如图6所示,通过旋转螺旋千分尺调整定位挡块与凹模610之间的距离,设置脚线制备长度、打磨下压行程、打磨次数等参数;s4:上述制备装置运行,如图3所示,升降气缸动作升起挡板303;s5:如图7和图3所示,剥线机200牵引组件201牵引开始送料,到达设定的制备长度后,将线材切断,线材在自重下进入导向板308的导向滑槽310内,随后经导向滑槽310导引进入接料板301的第一个第一纵向滑槽309内,当传感器108检测到下滑轮103位置上升至设定值后,转轴102旋转一定角度,进行送料,下滑轮103位置下降,此时牵引组件201停止牵引;s6:如图3所示,第一直线模组302工作,带动接料板301横向移动,接料板301切换至第二个第一纵向滑槽309对齐导向板308的导向滑槽310,然后再重复执行步骤s5,完成第二根线材裁剪和缓存;然后第一直线模组302再进行工作,带动接料板301横向移动,接料板301切换至第三个第一纵向滑槽309对齐导向板308的导向滑槽310,然后再重复执行步骤s5,完成第三根线材裁剪和缓存;s7:升降气缸动作降下挡板303,同时第一通气块306送入压缩空气,线材在自重和空气共同作用下进入前凹模601的第二滑槽;s8:如图5所示,第三直线模组402动作,带动第四直线模组403移动到打磨工位上方,此时打磨件409通过清扫件410清扫,然后第四直线模组403工作,带动滑板406和打磨件409向下移动,使打磨件409进入前凹模601的横向凹槽608内,当打磨件409抵住线材后,第四直线模组403继续工作,此时滑板406则相对第四直线模组403上行,而拉簧407则被拉升伸,而打磨件409则在拉簧407的弹性回复力的作用下以一定压力压紧线材;s9:第三直线模组402往复移动进行线材固定位置打磨,打磨完成后,第四直线模组403动作,使得打磨件409复位,此时,打磨件409脱离横向凹槽608,拉簧407复位,然后第三直线模组402工作,将第四直线模组403复位,第四直线模组403在横向移动复位过程中,
打磨件409与清扫件410发生干涉,清扫架能对打磨件409再次进行清扫,同时,第二直线模组605动作带动前凹模601横向移动至卸料工位,使前凹模601的第二纵向滑槽609脱离定位挡块501的限位,线材在自重和前通气块压缩空气作用下从前凹模601的第二纵向凹槽中退出,完成卸料;而此时,后凹模602则移动到打磨工位,接料板301上的线材则在自重和空气动力的作用下进入到后凹模602的第二纵向滑槽609内,然后在重复步骤s8,使得打磨件409压紧线材,然后第三直线模组402和第四直线模组403在执行相同的动作,完成后凹模602上的线材打磨,而打磨完成后,第二直线模组605动作,使得前凹模601位于打磨工位而后凹模602位于卸料工位,然后在后凹模602卸料的同时,前凹模601完成线材的上料,在线材打磨的同时,该装置的步骤s1~s6照常工作,完成线材的裁剪和缓存,从而实现脚线的连续制备。
37.在该脚线制备之前,需要根据脚线的型号确定制备过程的主要参数,以某型号脚线(长度55mm
±
0.2mm、去漆毛化宽度2.1mm
±
0.1 mm、去漆毛化位置11mm
±
0.2mm、去漆毛化直径0.56mm
±
0.03mm)为例,其确定的制备过程主要参数如下:a)确定打磨件409宽度:打磨件409宽度应与毛化宽度相同,依据去漆和毛化宽度为2.1mm
±
0.1mm,此处取打磨件409宽度取2.1mm;b)确定拉簧407刚度:根据试验,打磨压力8n情况下,打磨质量最优,打磨下压行程设定在4mm,则拉簧407刚度选用1n/mm;c)确定打磨次数:根据试验,往复打磨次数为五次情况下,打磨质量最优,此处打磨次数设定为五次;d)确定送料气压:根据试验,送料气压为0.2mpa情况下,送料可靠,不会出现物料不能顺利转移的情况,此处送料气压设定为0.2mpa;e)确定第二纵向滑槽609的宽度:根据线材整周旋转打磨要求,线材在第二纵向滑槽609内应可旋转一周,第二纵向滑槽609宽度应大于线材周长,依据线材直径φ0.6mm,线材周长为1.88mm,此处第二纵向滑槽609宽度设定为2mm;f)确定第二纵向滑槽609深度与横向凹槽608深度差值:第二纵向滑槽609深度与横向凹槽608深度差应小于线材直径,同时为防止线材修锉弯曲,第二纵向滑槽609的深度与横向凹槽608深度差应尽量与线材打磨直径相当,依据线材直径φ0.6mm,毛化直径0.56mm
±
0.03mm,此处第二纵向滑槽609深度与横向凹槽608深度的差值取0.5mm。
38.尽管参照前述实施例对本发明进行了详细的说明,对于本领域的技术人员来说,其依然可以对前述各实施例所记载的技术方案进行修改,或者对其中部分技术特征进行等同替换,凡在本发明的精神和原则之内,所作的任何修改、等同替换、改进等,均应包含在本发明的保护范围之内。
再多了解一些
本文用于创业者技术爱好者查询,仅供学习研究,如用于商业用途,请联系技术所有人。