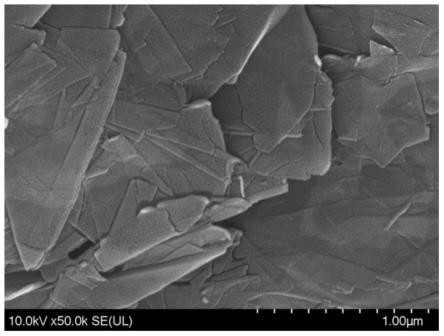
1.本发明涉及复合催化剂领域,特别涉及一种用作电解水制氢的碳化钼/石墨纳米片高效复合催化剂的制备方法。
背景技术:
2.贵金属催化剂活性高,但在较高的温度下易烧结,使活性降低,而且贵金属资源有限,价格昂贵,所以无法大规模使用。非贵金属催化剂价格较贵金属便宜,但催化活性较低。碳化钼具有间隙合金结构,具有较好的电催化析氢性能,但受限于活性位点的数量以及析氢过程中碳化钼与氢原子之间的结合能。除此之外,形成碳化钼所需的高温条件往往会导致碳化钼出现团聚现象,从而影响催化性能。
3.现有技术中,cn107694586b一种石墨烯缠绕碳化钼/碳微球电催化剂及其制备方法以及在酸性条件下电解水制氢中应用,以钼酸盐和氧化石墨烯为原料,溶剂为壳聚糖、乙酸和去离子水混合溶液,制备石墨烯缠绕碳化钼/碳微球电催化剂,制得的催化剂10ma cm-2
时过电位为148mv,该催化剂制备方法还涉及其他成分的应用和多步反应,cn110575840b一种二维碳化钼/石墨烯纳米片复合材料的制备方法,按照氧化石墨烯与可溶性钼源的质量比为0.01~0.02∶1,十六烷基三甲基溴化铵加入量为氧化石墨烯质量的9~65倍,将溶解有十六烷基三甲基溴化铵的氧化石墨烯乙醇分散液加入到可溶性钼源水溶液中,于100~120℃水热反应10~12h,再将反应产物在800~900℃碳化不少于2h,得到二维碳化钼/石墨烯纳米片复合材料,该技术方案也涉及较多的原料和操作步骤,本发明提出更为简便的、电催化性能更优的碳化钼/石墨纳米片高效复合催化剂制备方法。
技术实现要素:
4.鉴以此,本发明提出一种用作电解水制氢的碳化钼/石墨纳米片高效复合催化剂的制备方法,制备一种电性能更优的碳化钼/石墨纳米片高效复合催化剂。
5.用作电解水制氢的碳化钼/石墨纳米片高效复合催化剂的制备方法,包括以下步骤:
6.(1)将石墨纳米片和钼盐溶于水中,搅拌,制得混合溶液;
7.(2)将混合溶液烘干,制得前驱体g@(nh4)2moo4;
8.(3)将前驱体g@(nh4)2moo4置于管式炉中分步升温烧结,制得成品。
9.进一步的,步骤(1)中,所述石墨纳米片、水和钼盐质量比为20-5:75-15:1。
10.进一步的,步骤(1)中,所述钼盐为磷钼酸、钼酸铵中的一种。
11.进一步的,步骤(2)中,所述烘干为置于60-80℃烘箱中干燥10-15h,将干燥后的粉末进行研磨。
12.进一步的,步骤(3)中,所述将前驱体g@(nh4)2moo4置于管式炉中分步升温烧结,第一步升温至440-460℃,保温时间为1.5-2.5h,第二步升温至850-950℃,保温时间为3-4h。
13.本发明中采用分步升温法,第一步升温能够充分去除样品中的水分和氮气,同时使用氩气氛围进行保温,进一步的控制氩气通入速率,能够防止氮化钼(mo2n)生成。第二步升温至850-950℃,保温时间为3-4h,有利于形成更加稳定的β相mo2c,提高碳化钼/石墨纳米片高效复合催化剂的电催化性能。
14.进一步的,所述升温速率为1.5-2.5℃/min。
15.本发明中的管式炉升温速率能够有效减少碳化钼高温团聚现象,并使碳化钼颗粒在石墨纳米片上分布均匀,有利于提高碳化钼/石墨纳米片高效复合催化剂的电催化性能。
16.进一步的,所述第一步升温结束通入氩气,所述氩气通入速率为1.5-2.5℃/min。
17.进一步的,所述石墨纳米片、水和钼酸铵质量比为20:75:1或10:30:1或5:15:1。
18.进一步的,所述搅拌为使用50-80r/min搅拌11.5-12.5h。
19.本发明的有益效果为:
20.本发明以石墨纳米片和钼酸铵为原料,水为溶剂,采用分步加热的方法进行煅烧,制得碳化钼/石墨纳米片高效复合催化剂。本发明中采用合理的升温速率有利于减少碳化钼高温团聚现象,使碳化钼颗粒在石墨纳米片上分布均匀,采用较大的氩气通入速率,有利于去除样品中的水分与氨气,防止生成氮化钼(mo2n)。本发明制得的碳化钼/石墨纳米片高效复合催化剂呈片状,其他组分均匀的生长在石墨纳米片的表面,采用交换电流密度为10ma cm-2
进行测试,碳化钼/石墨纳米片高效复合催化剂过电位达到255mv。
附图说明
21.图1实施例1电镜扫描图
22.图2mo2c/g-a,mo2c/g-b与mo2c/g-c的x射线粉末衍射图谱
23.图3mo2c/g-a,mo2c/g-b与mo2c/g-c的lsv曲线,从左至右依次为mo2c/g-a,mo2c/g-c、mo2c/g-b和pt/c的lsv曲线
具体实施方式
24.为了更好理解本发明技术内容,下面提供具体实施例,对本发明做进一步的说明。
25.本发明实施例所用的实验方法如无特殊说明,均为常规方法。
26.本发明实施例所用的材料、试剂等,如无特殊说明,均可从商业途径得到。
27.实施例1用作电解水制氢的碳化钼/石墨纳米片高效复合催化剂的制备方法
28.(1)将石墨纳米片和钼酸铵溶于水中,所述石墨纳米片、水和钼酸铵质量比为20:75:1,使用60r/min搅拌12h,制得混合溶液;
29.(2)将混合溶液烘干,所述烘干为置于70℃烘箱中干燥12h,将干燥后的粉末进行研磨,制得前驱体g@(nh4)2moo4;
30.(3)将前驱体g@(nh4)2moo4置于管式炉中分步升温烧结,第一步升温至450℃,第一步升温结束通入氩气,所述氩气通入速率为2℃/min,第一步保温时间为2h,第二步升温至900℃,第二步保温时间为3h,所述第一步和第二步升温速率为2℃/min,制得成品。
31.实施例2用作电解水制氢的碳化钼/石墨纳米片高效复合催化剂的制备方法
32.(1)将石墨纳米片和钼酸铵溶于水中,所述石墨纳米片、水和钼酸铵质量比为10:30:1,使用50r/min搅拌11.5h,制得混合溶液;
33.(2)将混合溶液烘干,所述烘干为置于60℃烘箱中干燥10h,将干燥后的粉末进行研磨,制得前驱体g@(nh4)2moo4;
34.(3)将前驱体g@(nh4)2moo4置于管式炉中分步升温烧结,第一步升温至440℃,第一步升温结束通入氩气,所述氩气通入速率为1.5℃/min,第一步保温时间为1.5h,第二步升温至850℃,第二步保温时间为3h,所述第一步和第二步升温速率为1.5℃/min,制得成品。
35.实施例3用作电解水制氢的碳化钼/石墨纳米片高效复合催化剂的制备方法
36.(1)将石墨纳米片和钼酸铵溶于水中,所述石墨纳米片、水和钼酸铵质量比为5:15:1,使用70r/min搅拌12.5h,制得混合溶液;
37.(2)将混合溶液烘干,所述烘干为置于80℃烘箱中干燥15h,将干燥后的粉末进行研磨,制得前驱体g@(nh4)2moo4;
38.(3)将前驱体g@(nh4)2moo4置于管式炉中分步升温烧结,第一步升温至460℃,第一步升温结束通入氩气,所述氩气通入速率为2.5℃/min,第一步保温时间为2.5h,第二步升温至950℃,第二步保温时间为4h,所述第一步和第二步升温速率为2.5℃/min,制得成品。
39.对比例1
40.(1)将石墨纳米片和钼酸铵溶于水中,所述石墨纳米片、水和钼酸铵质量比为20:75:1,使用60r/min搅拌12h,制得混合溶液;
41.(2)将混合溶液烘干,所述烘干为置于70℃烘箱中干燥12h,将干燥后的粉末进行研磨,制得前驱体g@(nh4)2moo4;
42.(3)将前驱体g@(nh4)2moo4置于管式炉中分步升温烧结,第一步升温至450℃,第一步升温结束通入氩气,所述氩气通入速率为2℃/min,第一步保温时间为2h,第二步升温至900℃,第二步保温时间为3h,所述第一步和第二步升温速率为5℃/min,制得成品。
43.对比例1和实施例1的区别在于,调整管式炉烧结过程中的升温速率,提高升温速率,碳化钼颗粒出现高温团聚现象,导致碳化钼颗粒在石墨纳米片上分步不均匀,制得的碳化钼/石墨纳米片高效复合催化剂电催化性能下降。
44.对比例2
45.(1)将石墨纳米片和钼酸铵溶于水中,所述石墨纳米片、水和钼酸铵质量比为20:75:1,使用60r/min搅拌12h,制得混合溶液;
46.(2)将混合溶液烘干,所述烘干为置于70℃烘箱中干燥12h,将干燥后的粉末进行研磨,制得前驱体g@(nh4)2moo4;
47.(3)将前驱体g@(nh4)2moo4置于管式炉中分步升温烧结,第一步升温至450℃,第一步升温结束通入氩气,所述氩气通入速率为1℃/min,第一步保温时间为2h,第二步升温至900℃,第二步保温时间为3h,所述第一步和第二步升温速率为2℃/min,制得成品。
48.对比例2和实施例1的区别在于,调整氩气的通入速率,经过测试,制得的碳化钼/石墨纳米片高效复合催化剂电催化性能下降,经过分析,降低氩气的通入速率,导致未能完全去除样品中的水分与氨气,生成氮化钼(mo2n),进一步影响成品电催化性能。
49.对比例3
50.(1)将石墨纳米片和钼酸铵溶于水中,所述石墨纳米片、水和钼酸铵质量比为30:90:1,使用60r/min搅拌12h,制得混合溶液;
51.(2)将混合溶液烘干,所述烘干为置于70℃烘箱中干燥12h,将干燥后的粉末进行
研磨,制得前驱体g@(nh4)2moo4;
52.(3)将前驱体g@(nh4)2moo4置于管式炉中分步升温烧结,第一步升温至450℃,第一步升温结束通入氩气,所述氩气通入速率为2℃/min,第一步保温时间为2h,第二步升温至900℃,第二步保温时间为3h,所述第一步和第二步升温速率为2℃/min,制得成品。
53.对比例3和实施例1的区别在于,对比例3调整石墨纳米片和钼酸铵的质量比,导致碳化钼/石墨纳米片高效复合催化剂电催化性能下降。
54.对比例4
55.(1)将石墨纳米片和钼酸铵溶于水中,所述石墨纳米片、水和钼酸铵质量比为20:75:1,使用60r/min搅拌12h,制得混合溶液;
56.(2)将混合溶液烘干,所述烘干为置于70℃烘箱中干燥12h,将干燥后的粉末进行研磨,制得前驱体g@(nh4)2moo4;
57.(3)将前驱体g@(nh4)2moo4置于管式炉中分步升温烧结,第一步升温至300℃,第一步升温结束通入氩气,所述氩气通入速率为2℃/min,第一步保温时间为2h,第二步升温至750℃,第二步保温时间为3h,所述第一步和第二步升温速率为2℃/min,制得成品。
58.对比例4和实施例1的区别在于,对比例4调整烧结温度,导致碳化钼/石墨纳米片高效复合催化剂电催化性能下降,经过分析,本发明中的烧结温度设置,有利于控制产物的成品样貌结构和去除钼酸铵分解出的氨气和烧结过程中的水分,进一步提高催化剂的电催化性能。
59.对比例5
60.(1)将石墨纳米片和钼酸铵溶于水中,所述石墨纳米片、水和钼酸铵质量比为20:75:1,使用60r/min搅拌12h,制得混合溶液;
61.(2)将混合溶液烘干,所述烘干为置于70℃烘箱中干燥12h,将干燥后的粉末进行研磨,制得前驱体g@(nh4)2moo4;
62.(3)将前驱体g@(nh4)2moo4置于管式炉中升温烧结,在氩气氛围下进行煅烧,所述氩气通入速率为2℃/min,以2℃/min升温速率升温至900℃,保温3h。
63.对比例5和实施例1的区别在于,调整烧结方法,导致碳化钼/石墨纳米片高效复合催化剂电催化性能下降,经过分析,本发明中将前驱体g@(nh4)2moo4置于管式炉中分步升温烧结,有利于控制产物的成品样貌结构,提高催化剂的电催化性能。
64.试验例1
65.采用sem电镜对实施例1的样品进行分析,采用x射线衍射、交换电流密度为10ma cm-2
对实施例1-3的样品进行分析。实施例1-3的制得的成品分别标记为mo2c/g-a,mo2c/g-b与mo2c/g-c。
66.参见图1,实施例1样品的扫描电镜照片,所得产物呈片状,主要是由于石墨纳米片的层状结构和本发明的制备工艺,其它组分均匀地生长于石墨纳米片表面。
67.参见图2,mo2c/g-a,mo2c/g-b与mo2c/g-c的x射线粉末衍射图谱,位于26
°
,54
°
,77
°
左右的尖峰归属于石墨(g)的特征峰,其余的衍射峰则与归属于mo2c。这表明合成产物为mo2c和g的复合物。
68.参见图3,mo2c/g-a,mo2c/g-b与mo2c/g-c的lsv曲线。在交换电流密度为10ma cm-2
时,mo2c/g-a,mo2c/g-b与mo2c/g-c的过电位分别达到255,136以及183mv,具有较好的电催
化性能,表明mo2c/g系列复合物具有较多的活性位点,有利于电催化析氢反应。
69.以上所述仅为本发明的较佳实施例而已,并不用以限制本发明,凡在本发明的精神和原则之内,所作的任何修改、等同替换、改进等,均应包含在本发明的保护范围之内。
再多了解一些
本文用于创业者技术爱好者查询,仅供学习研究,如用于商业用途,请联系技术所有人。