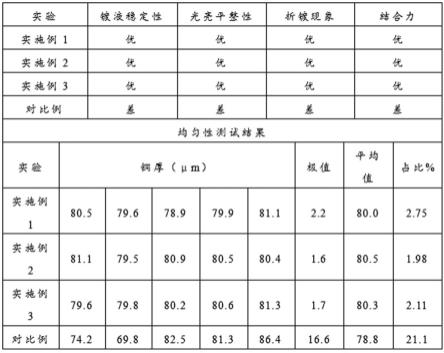
1.本发明涉及铜电镀技术领域,尤其涉及一种应用于薄膜电镀铜添加剂及其电镀工艺。
背景技术:
2.半导体薄膜电镀铜工艺是目前市场应用最广,性价比较高的电镀技术,是在半导体阻挡层上电沉积一层铜,作为后续工序生产的基底。许多关于晶圆上的电镀铜技术被开发使用,在专利cn110541179a中提出一种高铜电镀溶液,但该溶液得到铜层均匀性比较差;另外在专利cn103290438a提出一种晶圆电镀铜溶液,但是该溶液酸性过强,废液处理成本高,与目前环保趋势不相符合。
3.随着环保压力日益严重,工业废水处理成本较高,给不少企业带了巨大压力,在满足市场需求情况下,开发出既性能优异,又具备可以降低废水处理成本实现环保,是目前发展的必然趋势。为此,本发明旨在提供一种半导体薄膜电镀铜溶液以解决目前的问题。
技术实现要素:
4.针对上述技术中存在的不足之处,本发明提供一种应用于薄膜电镀铜添加剂及其电镀工艺。该发明溶液属于中性电镀铜溶液,废水处理简单,镀液稳定性能优异,镀层均匀光亮结合力好,且使用电流密度范围广。
5.为实现上述目的,本发明提供一种应用于薄膜电镀铜添加剂,包括以下质量浓度的组分:包括以下质量浓度的组分:硫酸铜60-90g/l、复合光亮剂40-120mg/l、复合整平剂30
‑ꢀ
90mg/l、润湿剂10-40mg/l、防折镀剂20-60mg/l、电解质0.1-0.5g/l、稳定剂20-45mg/l,ph为5.5-6.5操作温度25-35℃电流密度为0.1-6.5a/dm2所述复合整平剂为三环唑和2-丙炔基-2-羟烷基醚两者的组合物,且二者在使用时的质量浓度比为1:1,本发明采用复合整平剂可以促进电流密度均匀分布,实现镀层平整提高镜面效果。
6.其中,所述复合光亮剂为吡啶丙烷磺酸内盐、n,n-二乙基丙炔胺硫酸盐和烯丙基磺酸钠,三者在使用时的质量浓度比为1:1:2,吡啶丙烷磺酸内盐为10-30mg/l,n,n-二乙基丙炔胺硫酸盐为10-30mg/l,烯丙基磺酸钠为20-60mg/l。本发明采用复合光亮剂可以实现大电流密度范围内正常电镀,不出现铜瘤产生,与市面上电镀铜溶液比较具有巨大优势。
7.其中,所述电解质为硫酸钾。
8.其中,所述稳定剂为磺基水杨酸。可以提高槽液使用寿命,市面上电镀铜溶液因为使用时间延长,在生产过程中带入杂质过多,致使电镀铜溶液失衡,稳定剂可以极大锌铁等杂质离子对电镀铜液的影响。
9.其中,所述防折镀剂为3-[[(苄硫基)硫代羰基]硫基]丙酸;所述润湿剂为1-烯丙氧基-3-(4-壬基苯酚)-2-丙醇聚氧乙烯(10)醚硫酸铵。
[0010]
为实现上述目的,本发明还提供一种应用于薄膜电镀铜添加剂的电镀工艺,包括以下具体步骤:第一步骤,将基材打磨,纯水冲洗三遍,氢氟酸洗,再纯水三遍,中性除油1min,再通过25khz超声波清洗5min、钌活化1min、纯水水洗一遍;第二步骤,化学镀锌,超声清洗后的基材进入化学镀锌槽进行化学镀锌,得到一层致密的化学锌层,再纯水清洗三遍;第三步骤,化学镀铜,基材通过化学镀锌水洗后进入化学镀铜槽,进行化学镀铜,形成铜种子层;第四步骤,电镀铜,使用前用拖缸板进行预拖2h,以防止铜瘤产生,经过化学镀铜后的基材先纯水水洗三遍后进入电镀铜槽,所使用的电镀铜液为具有上述任意一项所述铜添加剂的电镀铜液,电镀铜完毕,清洗吹干即可。
[0011]
其中,所述第二步骤化学镀锌的具体操作流程是:基材经过活化后进入化学镀锌槽,通过浸泡方式在化学镀锌液中直接还原镀2min,随后纯水水洗一遍,再用退锌溶液脱锌,再纯水水洗一遍,再返回钌活化槽,纯水水洗一遍,再进入镀锌槽进行镀锌2min,可得一层致密的锌层。
[0012]
其中,所述第二步骤化学镀锌液包括以下组分:氧化锌20-50g/l、氢氧化钠50g/l、酒石酸钾钠15g/l、琥珀酸钠5g/l、op-10 1ml/l、乙氧基化丁炔二醇60mg/l、醋酸铅30mg/l、dmab 0.2-0.8g/l;且该化学镀锌的参数为:温度25-35℃,锌镀层厚度保持在0.1-0.5微米,所述退锌溶液包含30%体积浓度的硝酸及30-60mg/l的烟酸,脱锌时间为30s。本发明在形成铜种子层时为了提高铜的沉积,实现种子层的完全覆盖,强碱性化学镀锌液可以对提高阻挡层的粗糙度,同时预先得到一层很薄的致密锌层,与传统的直接活化进行沉积铜种子层相比较,锌层可以提高阻挡层的阻挡效果,同时会弥补铜种子层空洞带来漏镀现象,对结合力没有影响,且本发明提供的镀锌液得到锌层致密,有利于置换后的种子层铜比较致密。
[0013]
其中,所述第一步骤中钌活化的钌活化液包括硫酸钌15-25mg/l、月桂酸无规聚醚lpe-1200 50-70mg/l、1-乙烯基咪唑的三元共聚物30-60mg/l及1,2,4-三氮唑0.05-0.15g/l,且钌活化的参数为:温度35-45℃、时间0.5-2min,本发明使用专门的研发的钌活化液可以提高锌的还原活性,促进锌的快速沉积。
[0014]
其中,所述第四步骤的具体条件是:操作温度25-35℃,电流密度为0.1-6.5a/dm2,在氩气保护下进行电镀铜,且氩气通入压力为1.5-2.5kg/cm
2,
目的是取代氮气实现完全排氧。
[0015]
本发明的有益效果是:与现有技术相比,本发明提供的一种应用于薄膜电镀铜添加剂及其电镀工艺,存在以下优势:1)本发明提供复合光亮剂为吡啶丙烷磺酸内盐、n,n-二乙基丙炔胺硫酸盐和烯丙基磺酸钠,三者在使用时的质量浓度比为1:1:2,吡啶丙烷磺酸内盐为10-30mg/l,n,n-二乙基丙炔胺硫酸盐为10-30mg/l,烯丙基磺酸钠为20-60mg/l,可以实现大电流密度范围内正常电镀,不出现铜瘤产生,与市面上电镀铜溶液比较具有巨大优势。
[0016]
2)本发明采无硫酸电镀铜溶液体系,废液处理成本低,与传统高硫酸电镀铜溶液
相比更具有环保性。
[0017]
3)本发明采用复合整平剂为三环唑和2-丙炔基-2-羟烷基醚两者的组合物,且二者在使用时的质量浓度比为1:1,采用复合形式的整平剂可以促进电流密度均匀分布,实现镀层平整提高镜面效果。
[0018]
4)本发明在形成铜种子层时为了提高铜的沉积,实现种子层的完全覆盖,强碱性化学镀锌液可以对提高阻挡层的粗糙度,同时预先得到一层很薄的致密锌层,与传统的直接活化进行沉积铜种子层相比较,锌层可以提高阻挡层的阻挡效果,同时会弥补铜种子层空洞带来漏镀现象,对结合力没有影响,且本发明提供的镀锌液得到锌层致密,有利于置换后的种子层铜比较致密。
附图说明
[0019]
图1为本发明中实施例与对比例的测试结果判断标准图;图2为本发明中实施例与对比例的测试结果图。
具体实施方式
[0020]
为了更清楚地表述本发明,下面根据文字及附图对本发明作进一步地描述。
[0021]
本发明提供一种应用于薄膜电镀铜添加剂,包括以下质量浓度的组分: 硫酸铜60-90g/l、复合光亮剂40-120mg/l、复合整平剂30
‑ꢀ
90mg/l、润湿剂10-40mg/l、防折镀剂20-60mg/l、电解质0.1-0.5g/l、稳定剂20-45mg/l,ph为5.5-6.5操作温度25-35℃电流密度为0.1-6.5a/dm2所述复合整平剂为三环唑和2-丙炔基-2-羟烷基醚两者的组合物,且二者在使用时的质量浓度比为1:1。
[0022]
在本实施例中,所述复合光亮剂为吡啶丙烷磺酸内盐、n,n-二乙基丙炔胺硫酸盐和烯丙基磺酸钠,三者在使用时的质量浓度比为1:1:2,吡啶丙烷磺酸内盐为10-30mg/l,n,n-二乙基丙炔胺硫酸盐为10-30mg/l,烯丙基磺酸钠为20-60mg/l。
[0023]
在本实施例中,所述电解质为硫酸钾。
[0024]
在本实施例中,所述稳定剂为磺基水杨酸。
[0025]
在本实施例中,所述防折镀剂为3-[[(苄硫基)硫代羰基]硫基]丙酸;所述润湿剂为1-烯丙氧基-3-(4-壬基苯酚)-2-丙醇聚氧乙烯(10)醚硫酸铵。
[0026]
本发明还提供了一种含以上应用于薄膜电镀铜添加剂的电镀铜工艺,其具体步骤如下:第一步骤,将基材打磨,纯水冲洗三遍,氢氟酸洗,再纯水三遍,中性除油1min,再通过25khz超声波清洗5min、钌活化1min、纯水水洗一遍;第二步骤,化学镀锌,超声清洗后的基材进入化学镀锌槽进行化学镀锌,得到一层致密的化学锌层,再纯水清洗三遍;第三步骤,化学镀铜,基材通过化学镀锌水洗后进入化学镀铜槽,进行化学镀铜,形成铜种子层;第四步骤,电镀铜,使用前用拖缸板进行预拖2h,以防止铜瘤产生,经过化学镀铜
后的基材先纯水水洗三遍后进入电镀铜槽,所使用的电镀铜液为上述所述的任意一项电镀铜液,电镀完毕,清洗吹干即可。
[0027]
在本实施例中,所述第二步骤化学镀锌的具体操作流程是:基材经过活化后进入化学镀锌槽,通过浸泡方式在化学镀锌液中直接还原镀2min,随后纯水水洗一遍,再用退锌溶液脱锌,再纯水水洗一遍,再返回钌活化槽,纯水水洗一遍,再进入镀锌槽进行镀锌2min,可得一层致密的锌层。
[0028]
在本实施例中,所述第二步骤化学镀锌液的主要组分及工艺参数为:化学镀锌液组分包括氧化锌20-50g/l、氢氧化钠50g/l、酒石酸钾钠15g/l、琥珀酸钠5g/l、op-10 1ml/l、乙氧基化丁炔二醇60mg/l、醋酸铅30mg/l、dmab 0.2-0.8g/l,温度25-35℃,锌镀层厚度保持在0.1-0.5微米,所述退锌溶液包含30%体积浓度的硝酸及30-60mg/l的烟酸,脱锌时间为30s。
[0029]
在本实施例中,所述第一步骤中钌活化的主要组分及工艺参数为:硫酸钌15-25mg/l、月桂酸无规聚醚lpe-1200 50-70mg/l、1-乙烯基咪唑的三元共聚物30-60mg/l及1,2,4-三氮唑0.05-0.15g/l,温度35-45℃、时间0.5-2min。
[0030]
在本实施例中,所述第四步骤的具体条件是:操作温度25-35℃,电流密度为0.1-6.5a/dm2,氩气保护下进行电镀铜,氩气通入压力为1.5-2.5kg/cm2,目的是取代氮气实现完全排氧。
[0031]
本发明的有益效果是:与现有技术相比,本发明提供的一种应用于薄膜电镀铜添加剂及其电镀工艺,存在以下优势:1)本发明提供复合光亮剂为吡啶丙烷磺酸内盐、n,n-二乙基丙炔胺硫酸盐和烯丙基磺酸钠,三者在使用时的质量浓度比为1:1:2,吡啶丙烷磺酸内盐为10-30mg/l,n,n-二乙基丙炔胺硫酸盐为10-30mg/l,烯丙基磺酸钠为20-60mg/l,可以实现大电流密度范围内正常电镀,不出现铜瘤产生,与市面上电镀铜溶液比较具有巨大优势。
[0032]
2)本发明采无硫酸电镀铜溶液体系,废液处理成本低,与传统高硫酸电镀铜溶液相比更具有环保性。
[0033]
3)本发明采用复合整平剂为三环唑和2-丙炔基-2-羟烷基醚两者的组合物,且二者在使用时的质量浓度比为1:1,可以促进电流密度均匀分布,实现镀层平整提高镜面效果。
[0034]
4)本发明在形成铜种子层时为了提高铜的沉积,实现种子层的完全覆盖,强碱性化学镀锌液可以对提高阻挡层的粗糙度,同时预先得到一层很薄的致密锌层,与传统的直接活化进行沉积铜种子层相比较,锌层可以提高阻挡层的阻挡效果同时会弥补铜种子层空洞带来漏镀现象,对结合力没有影响,且本发明提供的镀锌液得到锌层致密,有利于置换后的种子层铜比较致密。
[0035]
以下为本发明的几个具体实施例:实施例与对比例的测试结果判断标准如图1所示,其中均匀性测试为每一组实验采用同一类型板的一块基材做测试,分别取四边和中间五个点作为测试对象。
[0036]
实施例1一种应用于薄膜电镀铜添加剂:硫酸铜75g/l、吡啶丙烷磺酸内盐为10mg/l、n,n-二乙基丙炔胺硫酸盐为10mg/l、
烯丙基磺酸钠为20mg/l、三环唑15mg/l、2-丙炔基-2-羟烷基醚15mg/l、1-烯丙氧基-3-(4-壬基苯酚)-2-丙醇聚氧乙烯(10)醚硫酸铵10mg/l、3-[[(苄硫基)硫代羰基]硫基]丙酸20mg/l、硫酸钾0.1g/l、磺基水杨酸20mg/l,ph=6,余量为纯水。
[0037]
操作温度25℃电流密度为1.5a/dm2时间100min。
[0038]
实施例2一种应用于薄膜电镀铜添加剂:硫酸铜75g/l、吡啶丙烷磺酸内盐为20mg/l、n,n-二乙基丙炔胺硫酸盐为20mg/l、烯丙基磺酸钠为40mg/l、三环唑30mg/l、2-丙炔基-2-羟烷基醚30mg/l、1-烯丙氧基-3-(4-壬基苯酚)-2-丙醇聚氧乙烯(10)醚硫酸铵40mg/l、3-[[(苄硫基)硫代羰基]硫基]丙酸60mg/l、硫酸钾0.5g/l、磺基水杨酸45mg/l,ph=6,余量为纯水。
[0039]
操作温度25℃电流密度为2.5a/dm2时间65min。
[0040]
实施例3一种应用于薄膜电镀铜添加剂:硫酸铜80g/l、吡啶丙烷磺酸内盐为30mg/l、n,n-二乙基丙炔胺硫酸盐为30mg/l、烯丙基磺酸钠为60mg/l、三环唑40mg/l、2-丙炔基-2-羟烷基醚40mg/l、1-烯丙氧基-3-(4-壬基苯酚)-2-丙醇聚氧乙烯(10)醚硫酸铵30mg/l、3-[[(苄硫基)硫代羰基]硫基]丙酸40mg/l、硫酸钾0.3g/l、磺基水杨酸30mg/l,ph=6,余量为纯水。
[0041]
操作温度25℃电流密度为5.5a/dm2时间30min。
[0042]
对比例一种应用于薄膜电镀铜添加剂:硫酸铜75g/l、1-烯丙氧基-3-(4-壬基苯酚)-2-丙醇聚氧乙烯(10)醚硫酸铵10-40mg/l、硫酸钾0.1-0.5g/l,ph为5.5-6.5,余量为纯水。
[0043]
操作温度25℃电流密度为5.5a/dm2时间30min。
[0044]
每个实施例取五块板子做一组,最终得到的测试结果如图2所示,通过图2中实施例1-3与对比例的相对比,得出的结论是:实施例1,2,3均得到镀液稳定性优、光亮平整性优、折镀现象优、结合力优、均匀性优。对比例与实施例比较缺少复合光亮剂、复合整平剂、稳定剂、防折镀剂,得到实验结果为镀液稳定性差、光亮平整性差、折镀现象差、结合力差、均匀性差。以上实验条件均是本次实验设置,具体生产可依据相应要求作出改变。
[0045]
以上公开的仅为本发明的实施例,但是本发明并非局限于此,任何本领域的技术人员能思之的变化都应落入本发明的保护范围。
再多了解一些
本文用于创业者技术爱好者查询,仅供学习研究,如用于商业用途,请联系技术所有人。