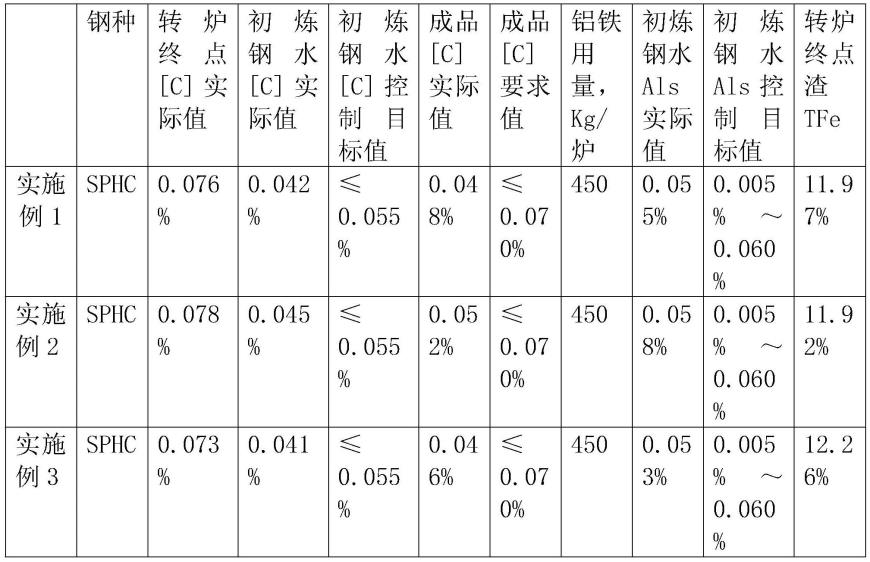
1.本发明涉及钢铁冶金技术领域,具体为一种低碳钢碳含量的控制方法。
背景技术:
2.转炉生产低碳钢种,尤其是生产sphc等成品碳含量[c]≤0.07%的低碳铝镇静钢,其工艺流程为:铁水预处理
→
转炉
→
吹氩站
→
lf精炼炉
→
连铸,如图1所示。因后道工序无降碳措施,且钢水在lf炉精炼过程中,电极加热与调整合金成分存在一定的增碳作用,尤以电极增碳为主,据计算,lf炉生产sphc等低碳铝镇静钢最高增碳量可达0.01%,为保证成品碳合格,现有技术中,转炉终点钢水碳含量通常按低于该钢种成品碳含量规格上限0.020%以下控制,转炉终点钢水碳含量控制普遍偏低。由于转炉终点钢水碳-氧浓度积相对恒定,终点钢水碳含量[c]低则氧含量[o]就高。当终点钢水碳含量[c]≤0.050%时,随着钢水碳含量[c]的进一步降低,钢水氧含量[o]和渣中tfe急剧增加,从而造成钢铁料消耗增加、对炉衬侵蚀加剧、转炉炉况维护困难、出钢脱氧合金消耗增加、钢中夹杂物含量增加、钢水质量变差等一系列不良影响。
[0003]
国内外针对转炉冶炼低碳钢种,尤其是成品碳含量[c]≤0.070%的低碳铝镇静钢所存在的以上不良影响,现有技术多从提高顶底复吹转炉的复吹比及复吹效果,采用大流量底吹后搅工艺来降低转炉终点钢水的碳-氧浓度积。通常转炉终点钢水碳含量[c]均按0.050%以下进行控制,当转炉终点钢水碳含量[c]低于该钢种成品碳含量规格上限0.020%以下,达到控制要求时,停止顶吹氧枪供氧,然后采用大流量底吹氩气后搅工艺来降低转炉终点钢水的碳-氧浓度积,从而降低钢水中氧含量及渣中tfe含量。复吹转炉的底吹后搅工艺,大流量底吹惰性气体提供的良好动力学条件,具有降低钢水氧含量、降低渣中tfe含量、降低钢水磷含量、降低钢水碳含量的作用。后搅工艺通常多在转炉冶炼低碳或超低碳钢种钢水碳低氧高时采用,其主要目的是降低钢水氧含量及渣中tfe含量,也有利用后搅工艺降低钢水磷含量的,但往往都忽视了其降碳作用在转炉冶炼低碳钢种上的合理应用。通常顶底复吹转炉的复吹效果随着炉龄的增加而逐渐变弱,尤其炉龄达到5000~6000炉以后,复吹效果更不明显或基本丧失,所以,对于以复吹效果来衡量转炉是否经济的炉龄一般不超过6000炉。对于顶吹转炉或炉龄长的顶底复吹转炉的炉役中后期,在生产低碳或超低碳钢种时所存在的不良影响,更需要有效的解决办法。
[0004]
文献《复吹转炉冶炼终点零位底吹搅拌工艺》提及“零位底吹搅拌具有停氧后继续促进碳氧反应,并降低钢水碳含量的作用”,但并未说明怎么去主动合理应用。
[0005]
文献《后搅工艺在100t转炉与应用》提及后搅工艺的降碳作用,但其后搅目的主要是为了“通过强化搅拌达到降低钢水磷含量和控制碳、锰烧损的目的。”冶炼低碳钢时,“当钢水[p]>0.020%时采用后搅模式”。利用后搅替代补吹脱磷操作,减轻钢水过氧化,而不是为了降碳。
[0006]
中国专利文献(cn 112094987 a)一种钢水碳含量的控制方法,该方法转炉终点钢水碳含量按低于所炼低碳钢种成品碳含量上限0.01%~0.02%控制;转炉出钢过程中,采
用全程钢罐底吹氩气搅拌,底吹氩气流量在技术规程允许的范围内,按大
→
大
→
小进行控制,即前期大、中期大、后期小,从出钢开始到出钢至4/5采用大流量底吹,出钢4/5至出钢结束采用小流量底吹;出钢3/4时,向钢罐内加入合金,合金对准钢流,加在钢流冲击部位,以促进合金快速与钢液反应并熔于钢液中;出钢结束后,钢水在吹氩站采用中等流量底吹氩搅拌1分钟后运送至lf炉进行精炼。该方法利用转炉出钢过程利于钢水中碳氧反应的热力学和动力学原理,通过合理调节钢罐底吹氩气流量并适当推迟加入合金的方法,使钢罐内钢水中部分的[c]与[o]在合金加入之前进一步反应生成{co}气体排出,钢水中的[c]与[o]同时降低,这样,既减轻了转炉拉低碳的压力,又能保证钢水碳含量满足钢种成分要求,同时还有效降低了钢水中的氧含量,提高合金收得率,在转炉低碳钢冶炼上,虽然取得一定的效果,但同时也存在不足,主要表现在:
[0007]
(1)该方法出钢3/4时,向钢罐内加入合金,则剩余流入钢罐1/4钢水中的[c]由于合金的加入而不再降低,出钢降碳不够完全,影响转炉终点碳的进一步提高。
[0008]
(2)对于无称重系统的钢罐车,转炉出钢时,钢罐内的钢水量完全靠操作工目测判断,存在较大偏差,易导致合金加入过早或过晚。合金加入过早,达不到转炉出钢降碳的预期目标,合金加入过晚,则影响转炉出钢后期挡渣,尤其是随合金加入复合渣料的炉次,瞬间产生的烟气易造成下渣检测系统误报警,影响对出钢下渣的判断
技术实现要素:
[0009]
本发明的目的在于提供一种低碳钢碳含量的控制方法,改变了现有转炉生产低碳钢后搅工艺及出钢脱氧工艺传统模式,充分利用后搅降碳及出钢降碳原理,在满足lf炉对初炼钢水碳含量要求的前提下,转炉终点碳含量较现有技术提高0.02%~0.03%,实现了转炉生产低碳钢种也能“留碳出钢”,解决了转炉终点碳低所引起的一系列不良影响。
[0010]
为实现上述目的,本发明提供如下技术方案:
[0011]
一种低碳钢碳含量的控制方法,适用于底吹效果好的顶底复吹转炉,包括以下步骤:
[0012]
s1:根据所炼钢种成品碳的要求,确定转炉终点钢水碳含量的控制目标;
[0013]
s2:转炉达到终点控制目标要求时,停止氧枪供氧,先立炉采用大流量底吹后搅降碳,然后出钢;
[0014]
s3:转炉出钢过程中,采用全程钢罐底吹氩气搅拌,底吹氩气流量全程按大流量控制,为转炉出钢降碳创造动力学条件;
[0015]
s4:出钢过程不加合金,不对钢水脱氧,为出钢过程钢水充分降碳创造条件;出钢1/4时,向钢罐内加入精炼活性石灰25
±
5kg/t,精炼活性石灰对准钢流,加在钢流冲击部位,用于促进熔化成渣,覆盖钢液面;
[0016]
s5:出钢结束后,对准钢罐钢水吹氩亮圈部位加入合金,加合金时采用大流量底吹氩,然后钢水进吹氩站采用中等流量底吹氩搅拌2分钟后运送至lf炉进行精炼。
[0017]
更进一步地,s1中转炉终点钢水碳含量按所炼钢种成品碳含量上限
±
0.010%控制,并根据后搅时间的长短适当提高转炉终点钢水温度以补偿后搅造成的温度损失。
[0018]
更进一步地,复吹转炉的后搅工艺是在转炉冶炼到达所炼钢种要求的终点时,顶吹氧枪停止供氧,通过加大底吹氩气流量,在底吹气体强搅拌作用下,转炉终点钢水溶解的
过剩氧与钢水中的溶解的碳发生反应c o=co生成co气体排出。
[0019]
更进一步地,搅拌用于增加钢-渣的接触面积,钢中溶解的碳与渣中的feo或fe2o3发生c feo=co fe或3c fe2o3=3co 2fe,其反应生成的co气体在通过渣层排出过程中,部分co气体与渣中的feo或fe2o3发生feo co=co2 fe或3co fe2o3=3co2 2fe,从而实现降碳和降低渣中的tfe。
[0020]
更进一步地,s3中转炉出钢过程中,全程采用钢罐底吹氩气搅拌,对于co气体来说,氩气泡相当于一个个小真空室,co气体将自动向其中扩散并被带出钢水,同时,从转炉出钢口以一定的高度差流出的钢流对钢罐内钢水的冲击搅拌作用,为碳氧反应提供了良好的动力学条件。
[0021]
本发明提供另一种技术方案:一种低碳钢碳含量的控制方法,适用于无底吹的顶吹转炉或底吹效果差的复吹转炉,包括以下步骤:
[0022]
s1:根据所炼钢种成品碳的要求,确定转炉终点钢水碳含量的控制目标,转炉终点钢水碳含量按低于所炼钢种成品碳含量上限0~0.010%控制;
[0023]
s2:转炉达到终点控制目标要求时,停止氧枪供氧,直接出钢;
[0024]
s3:转炉出钢过程中,采用全程钢罐底吹氩气搅拌,底吹氩气流量全程按大流量控制,为转炉出钢降碳创造动力学条件;
[0025]
s4:出钢过程不加合金,不对钢水脱氧,为出钢过程钢水充分降碳创造条件;出钢1/4时,向钢罐内加入适量精炼活性石灰25
±
5kg/t,精炼活性石灰对准钢流,加在钢流冲击部位,用于促进熔化成渣,覆盖钢液面;
[0026]
s5:出钢结束后,对准钢罐钢水吹氩亮圈部位加入合金,加合金时采用大流量底吹氩,然后钢水进吹氩站采用中等流量底吹氩搅拌2分钟后运送至lf炉进行精炼。
[0027]
与现有技术相比,本发明的有益效果是:
[0028]
1、本发明提供的一种低碳钢碳含量的控制方法,在转炉生产低碳钢种时改变了复吹转炉的底吹后搅工艺模式,将传统的“钢水低碳”后搅模式改为“钢水留碳”后搅模式,同钢种后搅前转炉终点钢水碳含量[c]提高了0.02%~0.03%,降低了转炉终点钢水的原始氧含量,减轻了转炉终点钢水对底吹供气元件的熔损。
[0029]
2、本发明提供的一种低碳钢碳含量的控制方法,改变了传统转炉生产低碳钢的脱氧工艺模式,将原出钢过程脱氧改为出钢结束后脱氧,充分利用转炉出钢过程降碳条件,并与复吹转炉后搅降碳相结合,同钢种转炉终点钢水碳含量提高0.02%~0.03%,减轻了转炉拉低碳的压力,实现了转炉生产低碳铝镇静钢的“留碳出钢”,有效降低了转炉钢水的氧化性和终点渣中tfe含量,既降低了金属铁的损失又提高了溅渣护炉效果。
[0030]
3、本发明提供的一种低碳钢碳含量的控制方法,通过合理运用转炉底吹后搅降碳及出钢降碳原理,钢水中的[c]与[o]同时降低,在满足下一道工序lf精炼炉对初炼钢水碳含量要求,进而满足钢种成品碳含量要求的同时,提高了铝铁合金的收得率,减少了脱氧产物al2o3总量,提高了钢水质量。
[0031]
4、本发明提供的一种低碳钢碳含量的控制方法,通过本发明的实施,转炉生产sphc等成品碳含量[c]≤0.07%的低碳铝镇静钢,终点渣中tfe含量平均下降4.9%,调渣剂镁球平均降低2.5kg/t,铝铁消耗平均减少0.42kg/t,合计降本22元/t。
附图说明
[0032]
图1为本发明的低碳钢生产工艺流程图;
[0033]
图2为本发明的技术方案一控制示意图;
[0034]
图3为本发明的技术方案二控制示意图。
具体实施方式
[0035]
下面将结合本发明实施例中的附图,对本发明实施例中的技术方案进行清楚、完整地描述,显然,所描述的实施例仅仅是本发明一部分实施例,而不是全部的实施例。基于本发明中的实施例,本领域普通技术人员在没有做出创造性劳动前提下所获得的所有其他实施例,都属于本发明保护的范围。
[0036]
本发明实施例中的复吹转炉的后搅工艺是在转炉冶炼到达所炼钢种要求的终点时,顶吹氧枪停止供氧,通过加大底吹氩气流量,提高供气强度,在底吹气体强搅拌作用下,转炉终点钢水溶解的过剩氧与钢水中的溶解的碳发生反应c o=co生成co气体排出。同时,在底吹强搅过程中,由于大量底吹氩气带着co气体不断排出炉口以及上浮排出的氩气对熔池液面上co的稀释作用,降低了co分压,也有利于c o=co反应。由于强搅拌增加了钢-渣的接触面积,钢中溶解的碳与渣中的(feo)或(fe2o3)发生c feo=co fe或3c fe2o3=3co 2fe,而以上这些反应生成的co气体在通过渣层排出过程中,部分co气体又会与渣中的(feo)或(fe2o3)发生feo co=co2 fe或3co fe2o3=3co2 2fe。以上就是本发明复吹转炉后搅工艺降碳和降低渣中tfe的原理。
[0037]
另外,本发明转炉出钢过程中存在以下碳氧进一步反应的有利条件:
[0038]
(1)由于碳氧反应c o=co是一个放热反应,转炉出钢过程中,随着钢水温度的降低,钢水中的c会与钢水中过剩的o生成co气体析出;
[0039]
(2)转炉出钢过程中,全程采用钢罐底吹氩气搅拌,对于co气体来说,氩气泡相当于一个个小真空室,co气体将自动向其中扩散并被带出钢水,同时,小氩气泡也是碳氧反应的理想地点;
[0040]
(3)出钢过程中,钢罐底吹氩气对钢罐内钢水的搅拌作用,以及从转炉出钢口以一定的高度差流出的钢流对钢罐内钢水的冲击搅拌作用,也为碳氧反应提供了良好的动力学条件。
[0041]
而随着脱氧合金的加入,钢水中的o将优先于钢水中的c与脱氧合金发生反应,则钢水中的c与o的反应被抑制。现有技术在生产低碳钢种时,转炉终点钢水碳含量通常按低于该钢种成品碳含量规格上限0.020%以下控制,出钢过程采用全程钢罐底吹氩气搅拌,底吹氩气流量在技术规程允许的范围内,按大
→
中
→
小进行控制,从出钢开始到出钢至1/3采用大流量,出钢1/3至2/3采用中等流量,出钢2/3至出钢结束采用小流量,合金普遍在出钢1/3时加入钢罐,由于合金加入较早,过早地抑制了碳氧反应,故出钢过程降碳作用不明显。
[0042]
本发明实施例利用上述复吹转炉的后搅工艺降碳及转炉出钢过程降碳的原理,生产低碳钢种时,首先根据转炉的底吹效果及所炼钢种的要求,分别确定转炉终点钢水碳含量c的控制范围;底吹效果好的复吹转炉,在钢水碳含量c达到所确定的相应控制范围,钢水其他成分及温度也满足出钢要求时停止顶吹氧枪供氧,先利用底吹进行后搅降碳,然后再利用出钢过程碳氧反应的有利条件进一步降低钢水碳含量c,对于无底吹的顶吹转炉或底
吹效果差的复吹转炉,终点钢水碳含量c按照所确定的相应控制范围进行控制,钢水其他成分及温度也满足出钢要求时,直接出钢,利用出钢过程碳氧反应的有利条件降低钢水碳含量c。从而,在满足下一道工序lf精炼炉对初炼钢水碳含量要求,进而满足钢种成品碳含量要求的前提下,降低转炉拉低碳的压力、降低转炉终点钢水氧含量和终点渣中tfe含量、提高溅渣护炉效果、降低合金消耗、减少钢中夹杂物、提高钢水质量。
[0043]
为了克服现有技术存在的缺陷与不足,本发明根据转炉底吹效果分为以下两种技术方案,如图2-3所示:
[0044]
技术方案一:适用于底吹效果好的顶底复吹转炉,其具体技术方案包括以下步骤:
[0045]
第一步:根据所炼钢种成品碳的要求,确定转炉终点钢水碳含量的控制目标,转炉终点钢水碳含量按该钢种成品碳含量上限
±
0.010%控制,考虑到后续采用后搅的降温作用,根据后搅时间的长短适当提高转炉终点钢水温度以补偿后搅造成的温度损失。
[0046]
第二步:转炉达到终点控制目标要求时,停止氧枪供氧,先立炉采用大流量底吹后搅降碳,然后出钢。
[0047]
第三步:转炉出钢过程中,采用全程钢罐底吹氩气搅拌,底吹氩气流量在技术规程允许的范围内,全程按大流量控制,为转炉出钢降碳创造良好的动力学条件。
[0048]
第四步:出钢过程不加合金,不对钢水脱氧,为出钢过程钢水充分降碳创造条件;出钢1/4时,向钢罐内加入适量精炼活性石灰(25
±
5)kg/t,精炼活性石灰对准钢流,加在钢流冲击部位,以促进熔化成渣,覆盖钢液面防止吸气。
[0049]
第五步:出钢结束后,对准钢罐钢水吹氩亮圈部位加入合金,加合金时采用大流量底吹氩,然后钢水进吹氩站采用中等流量底吹氩搅拌2分钟后运送至lf炉进行精炼。
[0050]
技术方案二:适用于无底吹的顶吹转炉或底吹效果差的复吹转炉,其具体技术方案包括以下步骤:
[0051]
第一步:根据所炼钢种成品碳的要求,确定转炉终点钢水碳含量的控制目标,转炉终点钢水碳含量按低于该钢种成品碳含量上限0~0.010%控制。
[0052]
第二步:转炉达到终点控制目标要求时,停止氧枪供氧,直接出钢。
[0053]
第三步:转炉出钢过程中,采用全程钢罐底吹氩气搅拌,底吹氩气流量在技术规程允许的范围内,全程按大流量控制,为转炉出钢降碳创造良好的动力学条件。
[0054]
第四步:出钢过程不加合金,不对钢水脱氧,为出钢过程钢水充分降碳创造条件;出钢1/4时,向钢罐内加入适量精炼活性石灰(25
±
5)kg/t,精炼活性石灰对准钢流,加在钢流冲击部位,以促进熔化成渣,覆盖钢液面防止吸气。
[0055]
第五步:出钢结束后,对准钢罐钢水吹氩亮圈部位加入合金,加合金时采用大流量底吹氩,然后钢水进吹氩站采用中等流量底吹氩搅拌2分钟后运送至lf炉进行精炼。
[0056]
为了进一步更好的解释说明本发明,本发明实施例通过120t顶底复吹转炉冶炼低碳钢的实施例来进一步说明本发明的实施步骤及操作控制要点。所述实施例为120t转炉,但本发明不仅仅局限于120t转炉,而是适用于所有吨位的转炉。实施例1~3为底吹效果好的顶底复吹转炉冶炼,执行技术方案一;实施例4~6为底吹效果差的顶底复吹转炉冶炼,执行技术方案二。
[0057]
实施例1:
[0058]
转炉冶炼低碳铝镇静钢sphc,装入量为128.2t,其中铁水104.0t,废钢24.2t,该钢
种成品成分规格要求碳含量[c]≤0.070%,初炼钢水成分要求[c]≤0.055%(以吹氩站成分为准),出钢温度控制目标1600℃~1630℃,考虑到后搅的降温作用,单纯后搅降温(5~6)℃/min转炉终点目标温度按1606℃~1630℃控制,铝铁加入量450kg,出钢过程精炼活性石灰300kg。
[0059]
步骤1:根据所炼钢种成品碳的要求,确定转炉终点钢水碳含量的控制目标,转炉终点钢水碳含量按该钢种成品碳含量上限
±
0.010%控制。sphc钢种成品碳含量上限为0.070%,则转炉终点碳含量[c]控制目标为0.070%~0.080%,本炉次转炉终点碳含量实际值为0.076%,温度为1612℃。
[0060]
步骤2:转炉达到终点要求停止氧枪供氧后,立炉采用大流量底吹后搅降碳,底吹氩气流量为1080nm3/h,后搅时间为1分钟后,钢水碳含量[c]为0.062%,温度为1607℃。
[0061]
步骤3:转炉出钢过程中,采用全程钢罐底吹氩气搅拌,底吹氩气流量技术规程要求为6~24m3/h,全程底吹流量22m3/h,为转炉出钢降碳创造良好的动力学条件。
[0062]
步骤4:出钢过程不加合金,不对钢水脱氧,为出钢过程钢水充分降碳创造条件;出钢1/4时,向钢罐内加入适量精炼活性石灰300kg,精炼活性石灰对准钢流,加在钢流冲击部位,以促进熔化成渣,覆盖钢液面防止吸气。
[0063]
步骤5:出钢结束后,对准钢罐钢水吹氩亮圈部位加入铝铁合金450kg,加合金时底吹氩气流量为22m3/h,然后钢水进吹氩站采用15m3/h中等流量底吹氩搅拌2分钟后运送至lf炉进行精炼。氩站钢水碳含量[c]为0.043%。
[0064]
实施例2:
[0065]
转炉冶炼低碳铝镇静钢sphc,装入量为128.0t,其中铁水104.0t,废钢24.0t,该钢种成品成分规格要求碳含量[c]≤0.070%,初炼钢水成分要求[c]≤0.055%(以吹氩站成分为准),出钢温度控制目标1600℃~1630℃,考虑到后搅的降温作用,单纯后搅降温(5~6)℃/min转炉终点目标温度按1606℃~1630℃控制,铝铁加入量450kg,出钢过程精炼活性石灰300kg。
[0066]
步骤1:根据所炼钢种成品碳的要求,确定转炉终点钢水碳含量的控制目标,转炉终点钢水碳含量按该钢种成品碳含量上限
±
0.010%控制。sphc钢种成品碳含量上限为0.070%,则转炉终点碳含量[c]控制目标为0.070%~0.080%,本炉次转炉终点碳含量实际值为0.078%,温度为1626℃。
[0067]
步骤2:转炉达到终点要求停止氧枪供氧后,立炉采用大流量底吹后搅降碳,底吹氩气流量为1080nm3/h,后搅时间为1分钟后,钢水碳含量[c]为0.063%,温度为1620℃。
[0068]
步骤3:转炉出钢过程中,采用全程钢罐底吹氩气搅拌,底吹氩气流量技术规程要求为6~24m3/h,全程底吹流量22m3/h,为转炉出钢降碳创造良好的动力学条件。
[0069]
步骤4:出钢过程不加合金,不对钢水脱氧,为出钢过程钢水充分降碳创造条件;出钢1/4时,向钢罐内加入适量精炼活性石灰300kg,精炼活性石灰对准钢流,加在钢流冲击部位,以促进熔化成渣,覆盖钢液面防止吸气。
[0070]
步骤5:出钢结束后,对准钢罐钢水吹氩亮圈部位加入铝铁合金450kg,加合金时底吹氩气流量为22m3/h,然后钢水进吹氩站采用15m3/h中等流量底吹氩搅拌2分钟后运送至lf炉进行精炼。氩站钢水碳含量[c]为0.045%。
[0071]
实施例3:
[0072]
转炉冶炼低碳铝镇静钢sphc,装入量为127.9t,其中铁水104.0t,废钢23.9t,该钢种成品成分规格要求碳含量[c]≤0.070%,初炼钢水成分要求[c]≤0.055%(以吹氩站成分为准),出钢温度控制目标1600℃~1630℃,考虑到后搅的降温作用,单纯后搅降温(5~6)℃/min转炉终点目标温度按1606℃~1630℃控制,铝铁加入量450kg,出钢过程精炼活性石灰300kg。
[0073]
步骤1:根据所炼钢种成品碳的要求,确定转炉终点钢水碳含量的控制目标,转炉终点钢水碳含量按该钢种成品碳含量上限
±
0.010%控制。sphc钢种成品碳含量上限为0.070%,则转炉终点碳含量[c]控制目标为0.070%~0.080%,本炉次转炉终点碳含量实际值为0.073%,温度为1618℃。
[0074]
步骤2:转炉达到终点要求停止氧枪供氧后,立炉采用大流量底吹后搅降碳,底吹氩气流量为1080nm3/h,后搅时间为1分钟后,钢水碳含量[c]为0.059%,温度为1613℃。
[0075]
步骤3:转炉出钢过程中,采用全程钢罐底吹氩气搅拌,底吹氩气流量技术规程要求为6~24m3/h,全程底吹流量22m3/h,为转炉出钢降碳创造良好的动力学条件。
[0076]
步骤4:出钢过程不加合金,不对钢水脱氧,为出钢过程钢水充分降碳创造条件;出钢1/4时,向钢罐内加入适量精炼活性石灰300kg,精炼活性石灰对准钢流,加在钢流冲击部位,以促进熔化成渣,覆盖钢液面防止吸气。
[0077]
步骤5:出钢结束后,对准钢罐钢水吹氩亮圈部位加入铝铁合金450kg,加合金时底吹氩气流量为22m3/h,然后钢水进吹氩站采用15m3/h中等流量底吹氩搅拌2分钟后运送至lf炉进行精炼。氩站钢水碳含量[c]为0.041%。
[0078]
实施例4:
[0079]
转炉冶炼低碳铝镇静钢sphc,装入量为127.8t,其中铁水104.0t,废钢23.8t,该钢种成品成分规格要求碳含量[c]≤0.070%,初炼钢水成分要求[c]≤0.055%(以吹氩站成分为准),出钢温度控制目标1600℃~1630℃,铝铁加入量450kg,出钢过程精炼活性石灰300kg。
[0080]
步骤1:根据所炼钢种成品碳的要求,确定转炉终点钢水碳含量的控制目标,转炉终点钢水碳含量按低于该钢种成品碳含量上限0~0.010%控制。sphc钢种成品碳含量上限为0.070%,则转炉终点碳含量[c]控制目标为0.060%~0.070%,本炉次转炉终点碳含量实际值为0.070%,温度为1622℃。
[0081]
步骤2:转炉出钢过程中,采用全程钢罐底吹氩气搅拌,底吹氩气流量技术规程要求为6~24m3/h,全程底吹流量22m3/h,为转炉出钢降碳创造良好的动力学条件。
[0082]
步骤3:出钢过程不加合金,不对钢水脱氧,为出钢过程钢水充分降碳创造条件;出钢1/4时,向钢罐内加入适量精炼活性石灰300kg,精炼活性石灰对准钢流,加在钢流冲击部位,以促进熔化成渣,覆盖钢液面防止吸气。
[0083]
步骤4:出钢结束后,对准钢罐钢水吹氩亮圈部位加入铝铁合金450kg,加合金时底吹氩气流量为22m3/h,然后钢水进吹氩站采用15m3/h中等流量底吹氩搅拌2分钟后运送至lf炉进行精炼。氩站钢水碳含量[c]为0.048%。
[0084]
实施例5:
[0085]
转炉冶炼低碳铝镇静钢sphc,装入量为128.1t,其中铁水104.0t,废钢24.1t,该钢种成品成分规格要求碳含量[c]≤0.070%,初炼钢水成分要求[c]≤0.055%(以吹氩站成
分为准),出钢温度控制目标1600℃~1630℃,铝铁加入量450kg,出钢过程精炼活性石灰300kg。
[0086]
步骤1:根据所炼钢种成品碳的要求,确定转炉终点钢水碳含量的控制目标,转炉终点钢水碳含量按低于该钢种成品碳含量上限0~0.010%控制。sphc钢种成品碳含量上限为0.070%,则转炉终点碳含量[c]控制目标为0.060%~0.070%,本炉次转炉终点碳含量实际值为0.063%,温度为1616℃。
[0087]
步骤2:转炉出钢过程中,采用全程钢罐底吹氩气搅拌,底吹氩气流量技术规程要求为6~24m3/h,全程底吹流量22m3/h,为转炉出钢降碳创造良好的动力学条件。
[0088]
步骤3:出钢过程不加合金,不对钢水脱氧,为出钢过程钢水充分降碳创造条件;出钢1/4时,向钢罐内加入适量精炼活性石灰300kg,精炼活性石灰对准钢流,加在钢流冲击部位,以促进熔化成渣,覆盖钢液面防止吸气。
[0089]
步骤4:出钢结束后,对准钢罐钢水吹氩亮圈部位加入铝铁合金450kg,加合金时底吹氩气流量为22m3/h,然后钢水进吹氩站采用15m3/h中等流量底吹氩搅拌2分钟后运送至lf炉进行精炼。氩站钢水碳含量[c]为0.045%。
[0090]
实施例6:
[0091]
转炉冶炼低碳铝镇静钢sphc,装入量为128.1t,其中铁水104.0t,废钢24.1t,该钢种成品成分规格要求碳含量[c]≤0.070%,初炼钢水成分要求[c]≤0.055%(以吹氩站成分为准),出钢温度控制目标1600℃~1630℃,铝铁加入量450kg,出钢过程精炼活性石灰300kg。
[0092]
步骤1:根据所炼钢种成品碳的要求,确定转炉终点钢水碳含量的控制目标,转炉终点钢水碳含量按低于该钢种成品碳含量上限0~0.010%控制。sphc钢种成品碳含量上限为0.070%,则转炉终点碳含量[c]控制目标为0.060%~0.070%,本炉次转炉终点碳含量实际值为0.066%,温度为1610℃。
[0093]
步骤2:转炉出钢过程中,采用全程钢罐底吹氩气搅拌,底吹氩气流量技术规程要求为6~24m3/h,全程底吹流量22m3/h,为转炉出钢降碳创造良好的动力学条件。
[0094]
步骤3:出钢过程不加合金,不对钢水脱氧,为出钢过程钢水充分降碳创造条件;出钢1/4时,向钢罐内加入适量精炼活性石灰300kg,精炼活性石灰对准钢流,加在钢流冲击部位,以促进熔化成渣,覆盖钢液面防止吸气。
[0095]
步骤4:出钢结束后,对准钢罐钢水吹氩亮圈部位加入铝铁合金450kg,加合金时底吹氩气流量为22m3/h,然后钢水进吹氩站采用15m3/h中等流量底吹氩搅拌2分钟后运送至lf炉进行精炼。氩站钢水碳含量[c]为0.047%。
[0096]
下表为以上实施例数据与常规控制相关数据对比情况:
[0097][0098][0099]
从上表所列数据可以看出,本发明在生产低碳钢sphc时,根据转炉底吹效果,采用转炉终点留碳后搅与出钢降碳相结合的方法,在满足下一道工序lf精炼炉对初炼钢水碳含量要求,进而满足钢种成品碳含量要求的前提下,转炉终点碳含量提高0.02%~0.03%,终渣tfe降低7.37%,钢水氧化性明显降低,在每炉少加50kg铝铁的情况下,氩站钢水als含量提高了0.020%。
[0100]
以上所述,仅为本发明较佳的具体实施方式,但本发明的保护范围并不局限于此,任何熟悉本技术领域的技术人员在本发明披露的技术范围内,根据本发明的技术方案及其发明构思加以等同替换或改变,都应涵盖在本发明的保护范围之内。
再多了解一些
本文用于创业者技术爱好者查询,仅供学习研究,如用于商业用途,请联系技术所有人。