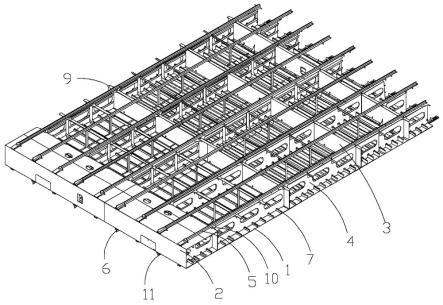
1.本实用新型涉及集装箱船领域,具体涉及集装箱船横舱壁结构及安装胎架。
背景技术:
2.横舱壁是沿船宽方向设置的分隔船舶舱室的垂直隔板,集装箱船的横舱壁将集装箱船分隔为多个装置集装箱的舱室。集装箱船的横舱壁上安装有多根竖直的轨道,集装箱在装船过程中,集装箱的四角沿着轨道的限位竖直向下。所以作为分隔舱室的横舱壁,其前后侧面上均需要安装轨道。
3.传统的集装箱船横隔舱的建造方法,即在横舱壁正胎状态下,先将胎板支承在胎架上,安装胎板上的角钢,再交替安装各层平台与垂直桁及其他构件,最后安装横隔舱的前壁板。在横隔舱结构全部安装到位后再安装胎板上的前导轨,之后使用门吊将做好部分的横隔舱翻身后,再安装胎板上的后导轨。由于超大型集装箱船横隔舱一般后壁为板架结构,前壁只有上侧箱体为板架结构,结构弱且外形尺寸大,翻身过程中很容易变形。这种传统的横隔舱建造方法在胎时间长且在吊装翻身时容易变形,显然不能满足现代造船快速化及科学化的需求。因此需要对横舱壁结构补强并设计专用胎架,避免翻身动作。
技术实现要素:
4.为了克服大型集装箱船横舱壁存在的结构若以及翻身建造工艺的工时长、易变形的问题,本实用新型的目的在于提供集装箱船横舱壁结构及安装胎架。
5.为达到以上目的,本实用新型采取的技术方案为:
6.集装箱船横舱壁结构及安装胎架,横舱壁结构包括胎板、前壁板、若干块平台板、若干块垂直桁、前轨道以及后轨道,前壁板安装于胎板前侧的顶端,平台板水平设置并焊接安装于胎板的前侧面,在胎板上形成自上而下的多层平台;垂直桁竖直设置并固定焊接与胎板的前侧,垂直桁的上下两端与相邻的两层平台板或者平台板与前壁板焊接;若干的垂直桁在胎板上形成沿胎板宽度方向分布的多个竖直支撑,前轨道竖直安装在胎板的前侧,与前壁板以及垂直桁的外侧面焊接连接;后轨道竖直安装在胎板的背面前轨道对应设置;安装胎架包括矩阵分布的多个支撑单元,多个支撑单元支撑放置于地面并均布支撑胎板,所述支撑单元包括一对角钢支撑、横向槽钢支撑,一对纵向槽钢支撑以及水平横档,角钢支撑固定竖直安装于地面,所述横向槽钢支撑安装于一对角钢支撑顶部;一对纵向槽钢支撑固定安装于横向槽钢支撑的顶面,水平横档水平安装于一对纵向槽钢支撑之间,所述水平横档中部设有定位槽,所述定位槽与所述后轨道前侧的角钢配合;所述胎板支撑于纵向槽钢支撑的顶面,所述后轨道支承于横档,后轨道的背部安装面与纵向槽钢支撑的顶面平齐。
7.进一步地,一对所述的纵向槽钢支撑中的其中一个槽钢的底端固定安装于地面并与横向槽钢支撑焊接连接。
8.进一步地,所述横向槽钢支撑与纵向槽钢支撑间安装有角钢斜撑。
9.进一步地,所述胎板上安装有若干根平行的水平角铁;所述垂直桁宽度方向的一
侧设有多个连接口,所述连接口与所述角钢配合连接;垂直桁宽度方向的另一侧安装有支撑板,所述支撑板与前轨道的安装面连接。
10.进一步地,平台板宽度方向的一端与所述角钢配合连接,平台板的宽度方向另一端也设有安装板,所述垂直桁的安装板与所述平台板的安装板焊接连接。
11.再进一步地,所述前轨道通过沿其长度方向均布的轨道支撑件与垂直桁以及前壁板连接。
12.采取以上技术方案后,本实用新型的有益效果为:
[0013] 1.对横舱壁的胎架设计,在常规的角钢支撑胎架的基础上增加通横向槽钢支撑以及纵向槽钢支撑,使得胎架的结构更加稳固,在通横向槽钢支撑以及纵向槽钢支撑之间安装角钢斜撑,进一步增加胎架的稳定性,避免因胎架变形对横舱壁施工精度产生影响。
[0014]
2.通过在纵向槽钢之间安装横档,利用横档上的定位槽与后轨道上角铁的配合将后轨道定位,利用横档的安装高度控制,使得后轨道的安装面刚好贴合支撑于胎架的胎板的背面,实现无需将横舱壁翻身就可以安装后轨道,且定位精度高,便于施工,节约工时。
[0015]
3.通过胎板上角铁与垂直桁连接口的配合,对垂直桁进行支撑,并增加垂直桁与胎板的连接强度,通过平台板以及垂直桁的安装板的设置,提高平台板与垂直桁间的连接强度,同时增加横舱壁的整体结构强度。
[0016]
本技术方案的安装胎架能够有效提高轨道的安装精度,避免横舱壁分段的翻身动作,降低横舱壁分段的在胎时间。
附图说明
[0017]
图1为横舱壁的结构示意图。
[0018]
图2为胎板的结构示意图.
[0019]
图3为平台板和垂直桁的安装示意图。
[0020]
图4为胎架的结构示意图。
具体实施方式
[0021]
以下结合附图对本实用新型的具体实施方式做进一步详述:
[0022]
如图1所示,集装箱船横舱壁结构,由胎板1、前壁板中组立2、若干块平台板3、若干块垂直桁4、若干根前轨道5以及若干根后轨道6组成。在横舱壁分段完成后吊装至船舱后,胎板1为竖直状态。前壁板中组立2安装于胎板1前侧的顶端,平台板3水平设置并焊接安装于胎板1的前侧面,在胎板1上形成自上而下的多层水平的平台;垂直桁4竖直设置并固定焊接于胎板1的前侧,垂直桁4的上下两端与相邻的两层平台板3或者平台板3与前壁板2焊接,垂直桁4起到支撑连接平台板3,增强横舱壁结构以及安装前导轨5的作用;若干的垂直桁4在胎板上形成沿胎板1宽度方向分布的多个自上而下的竖直支撑。
[0023]
如图2-3所示,为了便于安装平台板3以及垂直桁4,胎板前侧面上焊接安装有多根水平的角铁7,垂直桁4与胎板1连接的一侧设有多个与角铁7配合的缺口状连接口8,各连接口8分别卡于对应的角铁7并焊接连接,增加连接强度;平台板3与胎板1连接的一侧与角铁7贴合并焊接,在垂直桁4支撑平台板的同时,通过角铁7对平台板3支撑并增加连接强度。平台板3以及垂直桁4远离胎板的一侧分别设有安装板9,垂直桁4的安装板9与平台板3的安装
板垂直焊接连接。
[0024]
前轨道5竖直安装在胎板1的前侧,并支撑在前壁板中组立2以及垂直桁4的安装板9上。前轨道5底部设有均布的轨道支撑件10,通过轨道支撑件10与前壁板中组立2以及垂直桁4的安装板9固定。相邻的轨道间距为集装箱的宽度对应,前、后轨道的前侧面上安装有一对沿轨道长度方向的竖直的导向角铁11,集装箱装箱时,集装箱两侧壁边缘沿着一对轨道的相对的导向角铁11向下导向。
[0025]
后轨道6安装在胎板1的背面,在横舱壁安装在集装箱船后,横舱壁作为两个舱室的分隔壁,所以前后侧面上均需安装轨道。后轨道6与胎板1的背面焊接,后轨道6与前轨道5对应设置。由于横舱壁较大,放置在胎架上时胎板背面朝下,无法对后轨道6定位支撑,所以一般需要翻身后安装后轨道6。
[0026]
本技术方案提出了安装胎架结构,如图4所示,由横向槽钢支撑12和纵向槽钢支撑13组成,横向槽钢12底部有角钢支撑14,纵向槽钢13支撑安装在横向槽钢支撑12的顶部,施工时,胎板1支承在纵向槽钢支撑13的顶面。胎板1面积较大,一般在胎板1的底部均布上述胎架机构,防止胎板1的变形。为了能够实现后导轨6在翻身前的安装,在一对纵向槽钢支撑13之间焊接安装有水平的横档15,利用后轨道6的前侧面上有一对导向角铁11的特点,在横档15上加工定位槽16,后轨道6直接支承在横档15上,其导向角铁11插入定位槽16内,将后轨道6完成定位和支撑。当后轨道6支承在横档15后,其顶部的安装面与纵向槽钢支撑13的顶面平齐,即在胎板1支承在胎架后,后轨道6与胎板1背面贴合,直接焊接施工即可,无需翻身。
[0027]
为了提高胎架的强度,其中一个或者两个纵向槽钢支撑13均与地面固定连接并支撑横向槽钢支撑12,在横向槽钢支撑12与纵向槽钢支撑13间安装斜撑角铁17,斜撑角铁17可支撑至横档15的底部,防止横档15的变形,影响后导轨的安装精度。
[0028]
利用胎架的施工过程如下:
[0029]
1.制作胎架,使用横向、纵向槽钢支撑焊接形成胎架,并在纵向槽钢支撑13之间设安装横档15形成凹槽,凹槽的深度为在胎架上安装后导轨所需的高度,使用水平仪保证所有纵向槽钢支撑13的顶面位于同一水平高度,所有凹槽上表面位于同一水平高度。
[0030]
2.后导轨预埋,在胎板1吊至胎架之前将后导轨6放置在相应的凹槽内,利用凹槽内横档的定位槽16将后导轨6固定在凹槽内。
[0031]
3.胎板1吊至胎架,并在胎板安装角铁7;交替安装各层平台板3与垂直桁4及其他构件,并将预制好的前壁板中组立2翻身安装到胎板1上。
[0032]
4.安装预埋的后导轨6,根据横隔舱整体分段的胎架基准面数据,对后导轨6连接板修割、调平,然后将后导轨6焊接在胎板1背面。
[0033]
5.安装前导轨5,根据横隔舱整体分段的胎架基准面数据对前导轨支撑件修割、调平,然后将前导轨5焊接在垂直桁4的安装板9以及前壁板中组立2上。
再多了解一些
本文用于创业者技术爱好者查询,仅供学习研究,如用于商业用途,请联系技术所有人。