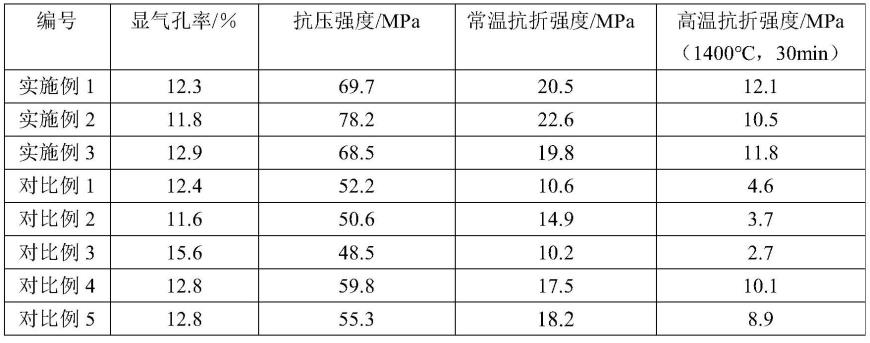
1.本技术属于耐火砖技术领域,特别涉及一种耐火砖材料及其制备方法与应用。
背景技术:
2.高铝耐火砖是指氧化铝含量在48wt%以上,以氧化铝(al2o3)和二氧化硅(sio2)为主要成分的一种硅酸铝质耐火材料。高铝耐火砖由矾土或其他氧化铝含量较高的原料经成型、煅烧而成,其热稳定性强,耐火度达1770℃以上,抗渣性好,成本低,力学性能优异,广泛应用于高炉、热风炉、电炉、鼓风炉、反射炉、回转窑等。氧化铝(al2o3)和二氧化硅(sio2)在烧结过程中形成二元化合物-莫来石相,而莫来石相是一种非化学计量型二元化合物,莫来石相中氧化铝的含量在75%左右。然而,高铝耐火砖在实际生产过程中工艺较粗放,普遍采用铝矾土作为氧化铝源,导致制成的高铝耐火砖除含有莫来石相外,还含有较多的杂质,如 tio2、fe2o3、cao等氧化物,部分杂质氧化物会在高温下与莫来石相形成低熔点化合物,导致基体的弱化,极易造成高铝耐火砖提前断裂、异常断裂及抗冲刷能力的降低。
3.在高炉等工业炉中,若耐火材料因提前断裂、异常断裂破碎,将会造成熔体污染、炉壳异常升温甚至熔穿等事故,导致炉子提前下线,造成严重的经济损失和安全事故。然而,氢气等还原性气体易通过孔隙进入高铝耐火砖内部,与二氧化硅等物质发生反应,造成高铝耐火砖的酥化,导致高铝耐火砖的性能(如力学性能)的下降。
技术实现要素:
4.鉴于以上所述现有技术的缺点,本技术的目的在于提供一种耐火砖材料及其制备方法与应用,以提高耐火砖的力学性能。
5.本技术提供一种耐火砖材料的制备方法,所述制备方法包括以下步骤:
6.s1.将钼纤维和纳米氧化铝置于氢氧化铝溶液中,搅拌至底部无沉淀,静置后烘干,得到预处理后的钼纤维;
7.s2.混合基料和辅料,得到所述耐火砖材料,所述基料包括刚玉料、二氧化硅和处理后的钼纤维。
8.可选地,步骤s1中,所述钼纤维的长径比>10。
9.可选地,步骤s1中,所述纳米氧化铝的粒径为20-50目,优选为30-50目。
10.可选地,步骤s1中,所述钼纤维与纳米氧化铝的质量比为50-100:1,优选为50-80:1。
11.可选地,步骤s1中,钼纤维与氢氧化铝溶液的配比为1g钼纤维:10-30ml氢氧化铝溶液,优选为1g钼纤维:20-30ml氢氧化铝溶液。
12.可选地,步骤s1中,所述氢氧化铝溶液的浓度为0.1-1.0mol/l,优选为0.5-1.0mol/l。
13.可选地,步骤s1中,所述钼纤维与氢氧化铝的质量比为1-10:1,优选为2-10:1。
14.可选地,步骤s1中,所述烘干的温度为50-350℃,优选为100-350℃;烘干的时间为
5-48h,优选为15-48h。
15.可选地,步骤s2中,所述刚玉料包括板状刚玉、球形刚玉和纳米氧化铝。
16.可选地,步骤s2中,所述刚玉料、二氧化硅与处理后的钼纤维的质量比为70-80:15-20: 2-10。
17.可选地,步骤s2中,所述二氧化硅的粒径为20-600目,优选为20-100目。
18.可选地,步骤s2中,所述板状刚玉的粒径为20-100目,优选为20-50目。
19.可选地,步骤s2中,所述球形刚玉的粒径为350-600目,优选为350-400目。
20.可选地,步骤s2中,所述纳米氧化铝的粒径为20-200nm,,优选为20-100nm。
21.可选地,步骤s2中,所述板状刚玉、球形刚玉和纳米氧化铝的质量比为60-70:20-30: 5-15,优选为65-70:25-30:10-15。
22.可选地,步骤s2中,所述辅料包括粘结剂和水。
23.可选地,步骤s2中,所述基料与辅料的质量比为100:5-12,优选为100:6-12。
24.可选地,步骤s2中,所述粘结剂选自氢氧化铝或磷酸铝或二者的混合物。
25.可选地,步骤s2中,所述粘结剂与水的质量比为0.5-2:5-10,优选为1-2:5-10。
26.另一个方面,本技术提供一种根据如上所述的制备方法制得的耐火砖材料。
27.再一个方面,本技术提供一种耐火砖,其由如上所述的耐火砖材料经压制成型、烘干、梯度烧结而成。
28.可选地,所述烘干的温度为90-200℃,优选为100-200℃;烘干的时间为36-72h,优选为40-72h。
29.可选地,所述梯度烧结包括:先于900-1100℃温度下烧结3-15h,接着于1200-1600℃温度下烧结3-15h,然后于1400-1750℃温度下烧结12-20h,优选地,先于1000-1100℃温度下烧结4-15h,接着于1400-1600℃温度下烧结4-15h,然后于1550-1750℃温度下烧结12-20h。
30.如上所述,本技术的耐火砖材料及其制备方法与应用,具有以下有益效果:
31.本技术利用刚玉和莫来石相等高温稳定性材料为基体,莫来石相呈现连续网络状骨架,刚玉相分布于莫来石骨架之间,大量钼纤维均匀分布于基体中,起到承载应力的作用,进而有效提高了制成的耐火砖的力学性能。
具体实施方式
32.以下通过特定的具体实例说明本技术的实施方式,本领域技术人员可由本说明书所揭露的内容轻易地了解本技术的其他优点与功效。本技术还可以通过另外不同的具体实施方式加以实施或应用,本说明书中的各项细节也可以基于不同观点与应用,在没有背离本技术的精神下进行各种修饰或改变。应理解的是,除特别说明外,本技术所述份数指质量份。
33.本技术提供一种耐火砖材料的制备方法,包括以下步骤:
34.s1.将长径比>10的钼纤维和粒径为20-50目的纳米氧化铝置于浓度为0.1-1mol/l的氢氧化铝溶液中,搅拌至底部无沉淀,静置后于50-350℃烘干5-48h,得到预处理后的钼纤维;
35.其中,步骤s1中,钼纤维与氢氧化铝溶液的配比为1g钼纤维:10-30ml氢氧化铝溶
液;
36.s2.按照质量比100:5-12混合基料和辅料,得到耐火砖材料;
37.其中,步骤s2中,基料包括刚玉料、粒径为20-600目的二氧化硅和处理后的钼纤维,刚玉料、二氧化硅与处理后的钼纤维的质量比为70-80:15-20:2-10;
38.刚玉料包括粒径为20-100目的板状刚玉、粒径为350-600目的球形刚玉和粒径为 20-200nm的纳米氧化铝,板状刚玉、球形刚玉和纳米氧化铝的质量比为60-70:20-30:5-15;
39.辅料包括粘结剂和水,粘结剂与水的质量比为0.5-2:5-10,粘结剂选自氢氧化铝或磷酸铝或二者的混合物。
40.另一个方面,本技术提供一种根据如上所述的制备方法制得的耐火砖材料。
41.再一个方面,本技术提供一种耐火砖,该耐火砖由如上所述的耐火砖材料压制成型、然后于90-200℃温度下烘干36-72h、随后于900-1100℃温度下烧结3-15h,接着于1200-1600℃温度下烧结3-15h,然后于1400-1750℃温度下烧结12-20h。
42.下面通过具体的例举实施例以详细说明本技术。同样应理解,以下实施例只用于对本技术进行具体的说明,不能理解为对本技术保护范围的限制,本领域的技术人员根据本技术的上述内容作出的一些非本质的改进和调整均属于本技术的保护范围。下述示例具体的工艺参数等也仅是合适范围中的一个示例,即本领域技术人员可以通过本文的说明做合适的范围内选择,而并非要限定于下文示例的具体数值。
43.实施例1
44.一种耐火砖,具体按照以下步骤制备而得:
45.s1.将50份长径比为11的微米级钼纤维和1份粒径为20目的纳米氧化铝置于10ml浓度为0.1mol/l的氢氧化铝溶液中,搅拌至底部无沉淀,静置10h后于100℃温度下烘干24h,得到预处理后的钼纤维;
46.钼纤维与氢氧化铝溶液的配比为1g钼纤维:20ml氢氧化铝溶液;
47.s2.在轮碾机中按照质量比100:6混合基料和辅料,混合时间为20min,得到混合料,基料由刚玉料、粒径为20目的二氧化硅和处理后的钼纤维按照质量比80:20:5组成,刚玉料由粒径为50目板状刚玉、粒径为400目的球形刚玉和粒径为50nm的纳米氧化铝按照质量比 65:25:10组成,辅料由氢氧化铝和去离子水按照质量比1:5组成;
48.s3.将混合料置于摩擦压砖机中缓慢压制成型,得到坯体;
49.s4.将坯体于180℃温度下烘干72h,随后于1100℃温度下烧结5h,接着于1400℃温度下烧结5h,然后于1550℃温度下烧结20h。
50.实施例2
51.一种耐火砖,具体按照以下步骤制备而得:
52.s1.将100份长径比为15的微米级钼纤维和1份粒径为50目的纳米氧化铝按照质量比置于30ml浓度为1mol/l的氢氧化铝溶液中,搅拌至底部无沉淀,静置30h后于350℃温度下烘干30h,得到预处理后的钼纤维;
53.步骤s1中,钼纤维与氢氧化铝溶液的配比为1g钼纤维:30ml氢氧化铝溶液;
54.s2.在轮碾机中按照质量比100:10.5混合基料和辅料,混合时间为20min,得到混合料,基料由刚玉料、粒径为100目的二氧化硅和处理后的钼纤维按照质量比75:20:5组成,刚玉料由粒径为50目板状刚玉、粒径为400目的球形刚玉和粒径为50nm纳米氧化铝按照质
量比65:30:5组成,辅料由氢氧化铝和去离子水按照质量比1:10组成;
55.s3.将混合料置于摩擦压砖机中缓慢压制成型,得到坯体;
56.s4.将坯体于180℃温度下烘干36h,随后于1100℃温度下烧结15h,接着于1400℃温度下烧结15h,然后于1550℃温度下烧结12h。
57.实施例3
58.一种耐火砖,具体按照以下步骤制备而得:
59.s1.将80份长径比为20的微米级钼纤维和1份粒径为30目的纳米氧化铝按照质量比置于20ml浓度为0.5mol/l的氢氧化铝溶液中,搅拌至底部无沉淀,静置20h后于250℃烘干 18h,得到预处理后的钼纤维;
60.步骤s1中,钼纤维与氢氧化铝溶液的配比为1g钼纤维:10ml氢氧化铝溶液;
61.s2.在轮碾机中按照质量比100:7混合基料和辅料,混合时间为20min,得到混合料,基料由刚玉料、粒径为500目的二氧化硅、处理后的钼纤维,刚玉料、二氧化硅与处理后的钼纤维的质量比为80:18:2,刚玉料由粒径为50目的板状刚玉、粒径为400目的球形刚玉和粒径为50nm的纳米氧化铝按照质量比60:20:10组成,辅料由氢氧化铝、磷酸铝和去离子水按照质量比1:1:5组成;
62.s3.将混合料置于摩擦压砖机中缓慢压制成型,得到坯体;
63.s4.将坯体于150℃温度下烘干60h,随后于1050℃温度下烧结10h,接着于1500℃温度下烧结10h,然后于1700℃温度下烧结10h。
64.对比例1
65.除以下条件外,以与实施例1相同的方式制备耐火砖:
66.在轮碾机中按照质量比100:6混合基料和辅料,混合时间为20min,得到混合料,基料由刚玉料和粒径为20目的二氧化硅按照质量比80:20组成,刚玉料由粒径为50目板状刚玉、粒径为400目的球形刚玉和粒径为50nm的纳米氧化铝按照质量比65:25:10组成,辅料由氢氧化铝和去离子水按照质量比1:5组成。
67.对比例2
68.除以下条件外,以与实施例2相同的方式制备耐火砖:
69.在轮碾机中按照质量比100:10.5混合基料和辅料,混合时间为20min,得到混合料,基料由刚玉料和粒径为100目二氧化硅按照质量比75:20组成,刚玉料由粒径为50目板状刚玉、粒径为400目的球形刚玉和粒径为50nm的纳米氧化铝按照质量比65:30:5组成,辅料由氢氧化铝和去离子水按照质量比1:10组成。
70.对比例3
71.除以下条件外,以与实施例1相同的方式制备耐火砖:
72.在轮碾机中按照质量比100:10.5混合基料和辅料,混合时间为20min,得到混合料,基料由刚玉料、粒径为100目二氧化硅和长径比为11的微米级钼纤维(来源与实施例1相同)按照质量比75:20:5组成,刚玉料由粒径为50目板状刚玉、粒径为400目的球形刚玉和粒径为50nm的纳米氧化铝按照质量比65:30:5组成,辅料由氢氧化铝和去离子水按照质量比1:10组成。
73.对比例4
74.除以下条件外,以与实施例1相同的方式制备耐火砖:
75.将50份长径比为11的微米级钼纤维置于10ml浓度为0.1mol/l的氢氧化铝溶液中,搅拌至底部无沉淀,静置10h后于100℃温度下烘干24h,得到预处理后的钼纤维;
76.钼纤维与氢氧化铝溶液的配比为1g钼纤维:20ml氢氧化铝溶液。
77.对比例5
78.除以下条件外,以与实施例1相同的方式制备耐火砖:
79.将50份长径比为11的微米级钼纤维和1份粒径为20nm的纳米氧化铝进行混合,得到预处理后的钼纤维。
80.性能检测
81.按照gb/t 2997-2015致密定形耐火制品体积密度、显气孔率和真气孔率试验方法》检测实施例1-3及对比例1-3制得的耐火砖的显气孔率;
82.按照《gb/t 5072-2008《耐火材料常温耐压强度试验方法》检测实施例1-3及对比例1-5 制得的耐火砖的抗压强度;
83.按照《gb/t 3001-2017耐火材料常温抗折强度试验方法》检测实施例1-3及对比例1-5 制得的耐火砖的常温抗折强度;
84.按照《gb/t 3002-2017耐火材料高温抗折强度试验方法》检测实施例1-3及对比例1-5 制得的耐火砖的高温抗折强度;
85.检测结果如表1所示,以上指标检测过程中,环境温度为25℃,相对湿度为55%rh。
86.表1检测结果
[0087][0088]
由表1可知,与对比例1-2相比,实施例1-2的耐火砖的抗压强度、常温抗折强度及高温抗折强度均显著提高,该结果表明,钼纤维能够显著改善制得的耐火砖的力学性能。
[0089]
由表1可知,与对比例3相比,实施例1的耐火砖的抗压强度、常温抗折强度及高温抗折强度均显著提高,该结果表明,预处理能够显著改善制得的耐火砖的力学性能。
[0090]
由表1可知,与对比例4-5相比,实施例1的耐火砖的抗压强度、常温抗折强度及高温抗折强度均显著提高,该结果表明,纳米氧化铝和氢氧化铝溶液能够显著改善了制得的耐火砖的力学性能。
[0091]
上述实施例仅例示性说明本技术的原理及其功效,而非用于限制本技术。任何熟悉此技术的人士皆可在不违背本技术的精神及范畴下,对上述实施例进行修饰或改变。因此,举凡所属技术领域中具有通常知识者在未脱离本技术所揭示的精神与技术思想下所完成的一切等效修饰或改变,仍应由本技术的权利要求所涵。
再多了解一些
本文用于创业者技术爱好者查询,仅供学习研究,如用于商业用途,请联系技术所有人。