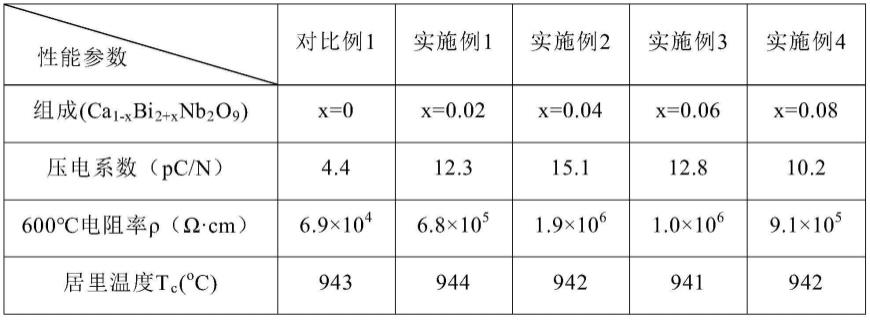
1.本发明属于压电陶瓷材料的制备领域,涉及一种自组分调控具有高压电性能及高温电阻率的铌酸铋钙压电陶瓷及其制备方法。
背景技术:
2.压电材料是一种可以实现电能和机械能相互转换的信息功能材料,广泛应用于航天航空、超声探测、水声探测等领域。压电材料分为压电单晶、压电陶瓷、压电高分子以及压电复合材料等,但是压电陶瓷因其优异的压电性能,丰富的组分可调性及简单的制备工艺,占据了大部分的市场份额,在很多器件中都有着无法替代的作用,拥有着非常广阔的前景。压电陶瓷材料是高温振动传感器的核心元件。随着我国航空航天事业的迅猛发展,对在高温恶劣环境中工作的高精度驱动器、高温压电振动传感器等压电器件提出了更高的要求,这就要求压电陶瓷材料兼具优异压电性能和高使用温度并且能够稳定、可靠的工作。并且,近年来美国对中国关键材料及器件的限制,使得研究用于600℃以上高温振动传感器用的压电陶瓷材料迫在眉睫。其中,铌酸铋钙压电陶瓷是铋层状压电陶瓷材料中已知的具有最高居里温度 (~943℃)的压电材料,是600℃以上高温振动传感器的优选材料。但由于其压电性能差 (d
33
为5~6pc/n),难以满足器件的灵敏度需求;并且电阻率随温度升高急剧下降(< 105ω
·
cm@600℃),漏电流增大,直接导致相关压电器件失效,严重制约了铌酸铋钙压电陶瓷在高温环境下的实际应用,也是我国600℃高温压电振动传感器的研制尚未取得突破的瓶颈之一。
3.目前,本领域通常采用离子掺杂优化组成设计以及织构化工艺调控微结构等手段来提高铌酸铋钙压电陶瓷材料的压电性能以及高温电阻率。如通过(li
0.5
ce
0.25
nd
0.25
)复合离子a位掺杂取代可将铌酸铋钙压电陶瓷的压电系数提高至13.1pc/n,高温电阻率提高至105~106ω
·
cm@600℃(ceram.int.,44,2018:3069-3076),(k
1/2
ce
1/2
)、(w
2/3
cr
1/3
)复合离子a、b位共同掺杂可将铌酸铋钙压电陶瓷的压电系数提高至18.4pc/n,高温电阻率提高至1.16
×
105ω
·
cm@600℃(j.mater.sci-mater.el.,30,2019:11727-11734),通过离子掺杂虽然可以提高压电性能及高温电阻率,但掺杂离子含量少,原料配比复杂,不适合生产化进程,并且压电陶瓷材料的性能往往是相互制约、相互影响的,离子掺杂取代的同时也会降低材料的居里温度(评价材料使用温度的重要参数);通过织构使铌酸铋钙压电陶瓷晶粒定向排布,可将压电系数提高至23pc/n,电阻率提高至》105ω
·
cm@600℃,由于铋层状压电陶瓷的特殊结构,通过织构法难以制备兼具高压电系数和高电阻率的铌酸铋钙压电陶瓷,并且织构化工艺较为复杂、重复性较差。因此,如何在保持其高居里温度的同时,通过简单、易操作的方法获得兼具高压电性能及高电阻率的压电陶瓷材料是高温压电陶瓷领域的研究重点和关键难题。
技术实现要素:
4.本发明针对铌酸铋钙压电陶瓷材料压电性能差、高温电阻率低的问题,提供了一种自组分调控的方法,在保持铌酸铋钙压电陶瓷高居里温度的情况下,同时提高其压电性能和高温电阻率,并提供了一种具有高居里温度、高压电性能、高电阻率的铌酸铋钙组成设计,以满足高温压电振动传感器用压电陶瓷材料的要求,推动其在高温领域的应用。
5.本发明根据铌酸铋钙的特殊化学组成及其结构,在不引入其它离子的前提下,通过自组分调控(调控铌酸铋钙中特定元素的化学计量比),设计铌酸铋钙压电陶瓷化学组成: ca
1-x
bi
2 x
nb2o9(其中,0《x《0.09,x为摩尔百分比),在不降低其居里温度的情况下,同时提高了压电性能和高温电阻率。
6.较佳地,所述铌酸铋钙压电陶瓷在室温下的压电系数为10~15pc/n,居里温度》940℃,600℃下的高温电阻率比cabinb2o9提高1~2个数量级,600℃、1mhz下的介电损耗为0.01~0.07。
7.较佳地,0《x≤0.08,优选0.02≤x≤0.06,更优选0.03≤x≤0.05。
8.本发明的目的是获得最优的调控比,实验已证明在x=0.04时为最优调控,通过如下缺陷方程使得陶瓷内空位减少到最低,电阻率达到最高,而当 x继续增加后,会发生如下反应使得陶瓷内部电子增多,导致电阻率下降,从x》0.04后的电阻率变化也可以看出该变化趋势,当x》0.08时再扩大范围其性能会比纯cbn陶瓷好,但其电阻率将小于5
×
105(@600℃);如图4,随着x增大,其晶胞参数a先减小后增大,在x=0.04时最小,a轴畸变最大(该结果通过xrd数据进行精修得出的结果,一种通过计算拟合获得晶胞参数及晶体结构的方法),由于cbn自发极化主要来自a方向,因而晶胞参数a畸变最大的组成时压电性能最大,x》0.04后,晶胞参数a再次增大,压电系数随之降低。
9.x=0.04组分具有最优的性能,不仅具有上述的优异性能(压电系数提高了近两倍,电阻率提高了一个数量级以上,居里温度基本保持不变),还具有良好的高温稳定性,在25~ 900℃范围内其压电系数变化率仅为10%。
10.第二方面,本发明提供了上述铌酸铋钙压电陶瓷的制备方法,包括:配料、混料、合成、细磨、造粒、成型、排塑、烧结、电极制备、极化,得到所述铌酸铋钙压电陶瓷。
11.较佳地,以caco3、bi2o3、nb2o5粉体按照ca
1-x
bi
2 x
nb2o9的化学计量比配制原料粉体;其中0《x≤0.08。
12.较佳地,所述混料和细磨的方式为湿法球磨混合2~6小时;其中,原料粉体:球磨介质:酒精的质量比=1:1.2~1.8:0.5~0.9。
13.较佳地,所述合成采用固相法,以1~3℃/min的升温速率升至700~950℃,保温合成2~4小时,然后随炉温冷却至室温,获得陶瓷粉体。
14.较佳地,所述造粒为:向陶瓷粉体中加入陶瓷粉体质量5%~10%的粘结剂进行造粒,优选地,所述粘结剂为聚乙烯醇、羧甲基纤维素、羟丙基甲基纤维素中的至少一种;更优选地,所述粘结剂为4~8wt.%聚乙烯醇。
15.较佳地,所述排塑为:以不高于2℃/min的升温速率升温至600~800℃,保温3小时以下。
16.较佳地,所述烧结为普通固相法烧结,将陶瓷坯体以1~3℃/min升温速率升至 1100~1300℃进行烧结1~3小时。
17.较佳地,所述电极制备的烧结温度为800~900℃,升温速率为1~3℃/min;保温时间为60分钟以下。
18.较佳地,所述极化条件为在180~200℃条件下施加18~22kv/mm极化10~30分钟。
附图说明
19.图1示出本发明对比例1和实施例1-4所制备的铌酸铋钙压电陶瓷的xrd图及局部放大图。
20.图2示出本发明对比例1和实施例1-4所制备的铌酸铋钙压电陶瓷不同温度下的电阻率变化关系图及600℃下不同组分的电阻率。
21.图3示出本发明实施例1-4所制备的铌酸铋钙压电陶瓷不同温度退火后的压电系数及室温下不同组分的压电系数。
22.图4示出了本发明对比例1和实施例1-4所制备的铌酸铋钙压电陶瓷xrd精修所得的晶胞参数变化。
具体实施方式
23.以下结合附图和实施例,对本发明的具体实施方式作进一步详细描述。应理解,以下附图和实施例用于说明本发明,而非限制本发明。
24.以下示例性地说明本发明所述自组分调控具有高压电性能及高温电阻率的铌酸铋钙压电陶瓷的制备方法。
25.配料。以caco3、bi2o3、nb2o5粉体为原料,按照自组分调控设计的铌酸铋钙化学组成(ca
1-x
bi
2 x
nb2o9,其中,0《x《0.09,优选0《x≤0.08,更优选0.02≤x≤0.06,进一步优选0.03≤x≤0.05,最优选x=0.04)进行配料并混料烘干。
26.混料。可采用湿法球磨的方式进行混料。其中,原料:球磨介质:酒精的质量比= 1:1.2~1.8:0.5~0.9,行星球磨混合2~6小时,球磨介质可为玛瑙球。
27.合成。所述的合成为固相法合成,合成条件包括:1~3℃/min的升温速率升至700~ 950℃,保温合成2~4小时,获得陶瓷粉体。
28.细磨。可采用湿法球磨的方式进行细磨。其中,原料:球磨介质:酒精的质量比= 1:1.2~1.8:0.5~0.9,行星球磨混合2~6小时,球磨介质可为玛瑙球。
29.造粒。向陶瓷粉体中加入陶瓷粉体质量5%~10%的粘结剂进行造粒。粘结剂可为4~ 8wt.%聚乙烯醇。
30.成型。以1~3mpa的单轴压力将陶瓷粉体压制成直径12~14mm、厚度1~2mm的陶瓷配体。
31.排塑。所述排塑条件为以不高于2℃/min的升温速率升温至600~800℃,保温3小时以下。排出造粒过程中加入的聚乙烯醇粘结剂并使陶瓷配体具有一定强度。烧结。所述烧结的方式可为普通固相法烧结,陶瓷坯体以1~3℃/min升温速率升至1100~1300℃,保温烧结1~3小时。
32.电极制备、极化。将上述烧结后得到的陶瓷片双面磨平,通过丝网印刷进行双面电
极制备,可以1~3℃/min的升温速率升至800~900℃,保温时间为60分钟以下。然后施行电极进行极化,极化条件为180~200℃,18~22kv/mm,极化10~30分钟,即得所述的铌酸铋钙压电陶瓷。
33.下面进一步例举实施例以详细说明本发明。同样应理解,以下实施例只用于对本发明进行进一步说明,不能理解为对本发明保护范围的限制,本领域的技术人员根据本发明的上述内容作出的一些非本质的改进和调整均属于本发明的保护范围。下述示例具体的工艺参数等也仅是合适范围中的一个示例,即本领域技术人员可以通过本文的说明做合适的范围内选择,而并非要限定于下文示例的具体数值。
34.对比例1
35.1)采用传统的固相烧结法制备铌酸铋钙ca
1-x
bi
2 x
nb2o9压电陶瓷,其中x=0,即 ca:bi=1:2。首先以caco3、bi2o3、nb2o5为原料按目标化学组成进行配料并混合,采用湿法球磨将其混合均匀并烘干,按照原料:玛瑙球:酒精=1:1.5:0.65~0.7比例混合,行星球磨4小时。
36.2)80℃烘干后,过40目筛,在3mpa压力下成型。然后放置在氧化铝坩埚中利用固相法合成,以2℃/min升温至850℃保温2小时,随炉温冷却至室温。将合成生料进行机械粉碎,过40目筛后,采用混料相同的工艺进行细磨。
37.3)然后加入合成粉体质量6%的粘结剂(聚乙烯醇pva)进行造粒,5mpa压力下成型,陈化24小时,过40目筛,在1.5mpa压力下压制成直径为13mm、厚度1~2mm的生坯。
38.4)将生坯以2℃/min升温至750℃保温2小时进行排塑。排塑后,以2℃/min升温至 1100~1200℃保温2小时进行烧结,随炉冷却至室温,得到铌酸铋钙压电陶瓷。
39.5)将获得的陶瓷片双面磨平至0.5mm,通过丝网印刷进行双面铂电极制备,以2℃ /min的升温速率升至850℃,保温30分钟烧结。然后施行电极进行极化,极化条件为 200℃,9~10kv/mm,极化30分钟,即得所述的铌酸铋钙压电陶瓷。
40.实施例1
41.实施例1与对比例1基本相同,区别仅在于:x=0.02,即ca:bi=0.98:2.02。
42.实施例2
43.实施例2与对比例1基本相同,区别仅在于:x=0.04,即ca:bi=0.96:2.04。
44.实施例3
45.实施例3与对比例1基本相同,区别仅在于:x=0.06,即ca:bi=0.94:2.06。
46.实施例4
47.实施例4与对比例1基本相同,区别仅在于:x=0.08,即ca:bi=0.92:2.08。
48.表1为本发明对比例1及实施例1-4中铌酸铋钙压电陶瓷的各项性能测试,其结果如表1所示。
49.xrd图采用日本rigaku公司的d/max-2550v型x射线衍射仪测试所得,高温电阻率均采用佰力博公司生产的rms-1000高温电阻测试系统测试所得,压电系数采用中科院声学所生产的zj-3a型准静态d
33
测试仪测试所得,居里温度tc按照gb/t 3389.3中的有关要求进行测试所得,高温介电损耗采用西安交通大学研制的高温介电测试系统测试所得。
50.表1结果可以看出,自组分调控后的铌酸铋钙压电陶瓷居里温度没有显著变化,均大于940℃,对于材料的最大使用温度无显著影响;在600℃下,自组分调控后的铌酸铋钙压
电陶瓷介电损耗显著降低。
51.图1为本发明对比例1和实施例1-4所制备的铌酸铋钙压电陶瓷的xrd图及局部放大图。可以看出,通过自组分调控改变ca/bi比对铌酸铋钙压电陶瓷的相组成没有影响。局部放大图可以看出,随着x增大(即ca/bi比减小),逐渐合并,相结构由正交相向伪四方相过渡,表明自组分调控使得bi
3
进入钙钛矿层中的a位置,使其结构发生畸变。
52.图2为本发明对比例1和实施例1-4所制备的铌酸铋钙压电陶瓷不同温度下的电阻率变化关系图及600℃下不同组分的电阻率。可以看出,通过自组分调控后的铌酸铋钙压电陶瓷在150-700℃温度范围内,电阻率相较未调控组分提高了1-2个数量级,表明bi
3
取代ca
2
的缺陷调控:减少了及h-的生产,降低了载流子浓度,提高电阻率。并且在x=0.04组分下,获得了最优电阻率值,在600℃温度下,电阻率高达 1.9
×
106ω
·
cm。
53.图3为本发明实施例1-4所制备的铌酸铋钙压电陶瓷不同温度退火后的压电系数及室温下不同组分的压电系数。通过自组分调控后的铌酸铋钙压电陶瓷在25-900℃温度范围内,具有良好的压电稳定性,其中x=0.04组分,压电系数变化率仅有10%,并且具有较高的压电系数15.1pc/n,压电系数提高了近两倍。
54.表1为不同自组分调控铌酸铋钙陶瓷的性能参数对比:表1为不同自组分调控铌酸铋钙陶瓷的性能参数对比:
再多了解一些
本文用于创业者技术爱好者查询,仅供学习研究,如用于商业用途,请联系技术所有人。