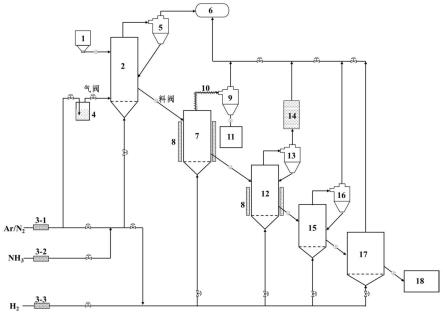
1.本发明属于化工、材料领域,涉及粉体的制备方法,特别是一种高质量氮化硅(si3n4)粉体的制备工艺。
背景技术:
2.si3n4陶瓷被誉为“全能陶瓷”,在机械加工、航空航天、电子信息、生物材料等领域具有广泛的应用。高质量si3n4粉体是制备高性能si3n4陶瓷的基础,且粉体占据了陶瓷成本的1/3~2/3。高质量粉体需要粒径约0.4~1.5μm,α相含量》95%,o含量《0.9wt.%,c含量《0.2wt.%,cl含量《100ppm,金属杂质《500ppm。经过几十年的不断研发,目前制备si3n4粉体主要有以下几大类方法:
3.(1)sio2的碳热氮化法(3sio2(s) 2n2(g) 6c(s)=si3n4(s) 6co(g))。该反应为典型的固相氮化反应,扩散传质是整个反应的限制步骤。这就导致粉体氧含量非常高,一般大于5.0wt.%,且产物物相不纯,通常含有sic,sioynz,以及残留的sio2和游离c。尽管,反复破碎并反复氮化可以在一定程度降低粉体的o杂质,但是粉体中仍然含有sic和c等杂相(j.am.ceram.soc.,1996,82,1635)。此外,由于si3n4硬度大,破碎过程中会引入杂质,而且也难以将粉体的粒径降低到1.0μm以下。
4.(2)si粉直接氮化法(3si(s) 2n2(g)=si3n4(s))。该反应为强放热反应,工业上常采用自蔓延燃烧技术合成si3n4粉体。然而,由于该反应仍然存在传质屏障,且温度梯度大,获得含游离si的si3n4块体,且产物中α含量通常小于70%。尽管提升应容器中n2的压力(约10mpa)或高能球磨能够强化传质,减少游离si的含量,但是无法避免游离si。此外,大量研究采用添加“稀释剂”来调控合成温度,但是α相含量也难以大于95%不满足高质量粉体要求。
5.(3)化学气相沉积法。通常sicl
4-n
2-h2/nh3和sihcl
3 n
2-h2/nh3体系需要高能等离子体辅助才能合成粉体(us 4416863)。但是,合成的粉体非α相粉体,而是β相粉体。。为解决该问题,德国巴斯夫公司开发出无定型种子粉体(bet》50m2/g)辅助流化和强化沉积的流态化气相合成法(us 4859443),在500~1500℃制备出了包覆结构的无定型si3n4粉体以及α相与β相的混合si3n4粉体。但是,粉体中α相含量较少,且其中cl杂质含量较高(》1.0wt%),不满足高质量粉体的要求。相比较而言,相比较而言,sih4和nh3反应更容易合成粉体(3sih4(g) 4nh3(g)=si3n4(s) 12h2(g))。但是,合成的无定型粉体晶化后为si3n4粉体,而不是α相粉体(us 4122155,us4929432,无机材料学报,2006,21,41;浙江理工大学学报,2007,24,36)。同时,粉体中含有大量游离si,不满足高质量粉体的要求。此外,sih4是有毒的危害性气体,且易燃易爆,约45%的事故发生在工艺阶段,21%的事故发生换瓶时。因此,化学气相沉积制备高质量si3n4粉体也还面临较大挑战。
6.(4)硅胺前驱体转化法,即sicl4和nh3首先在低温下合成硅胺前驱体si(nh2)4或si(nh)2,然后分离出副产物,最后晶化合成si3n4粉体。日本宇部(us 4405589,5585084,5595718),日本东洋曹达制造有限公司(us 4387079),美国空军(us 3959446)开发的低温
液相合成工艺获得了α相》95%,bet为约6m2/g,且cl《100ppm的高纯超细si3n4粉体(》99.95%)。但是,该工艺反应条件非常苛刻,且难以连续批量化进行,必须间歇生产,导致粉体产量小,效率低。
7.综上所述,sio2的碳热氮化法、si粉直接氮化法,以及化学气相沉积法都难以制备出高质量si3n4粉体。溶剂热液相合成法和硅胺前驱体转化法虽然能制备出较高质量si3n4粉体,但是合成粉体的产量小、效率低、成本高,限制了高质量氮化硅粉体的应用范围。连续化生产可以有效解决间歇生产中的吸湿防护问题,从而降低成本。因此,本领域亟需开发一种低成本、高效率、连续化批量生产高质量si3n4粉体的方法。
技术实现要素:
8.针对以上问题,本发明提出了一种多级流化床制备高质量氮化硅粉体的系统及方法,通过在流化床中合成前驱体,分级脱氯,分解以及晶化,可实现连续规模化生产高质量si3n4粉体,提高效率和产量,降低成本。
9.为了达到这些目的,本发明采用以下技术方案:
10.本发明提供了一种多级流化床制备高质量氮化硅粉体的系统,所述系统包括:粉体加料装置1、前驱体气相合成流化床2、第一气体净化器3-1、第二气体净化器3-2、第三气体净化器3-3、硅源蒸发装置4、第一旋风分离装置5、尾气回收压缩装置6、脱氯流化床7、第一能源供给装置8、第二旋风分离装置9、加热装置10、氯化铵收集装置11、深度脱氯流化床12、第三旋风分离装置13、酸性气体处理器14、分解流化床15、第四旋风分离装置16、晶化装置17、氮化硅粉体收集装置18、第二能源供给装置19;
11.所述粉体加料装置1的出料口与所述前驱体气相合成流化床2上部的进料口通过管道和料阀相连接;ar或n2与所述第一气体净化器3-1的进气口通过管道相连接;所述第一气体净化器3-1的出气口与所述硅源蒸发装置4的进气口通过管道和气阀相连接;所述硅源蒸发装置4的出气口与所述前驱体气相合成流化床2下部的进气口通过管道和气阀相连接;所述第一气体净化器3-1的出气口与所述前驱体气相合成流化床2底部的进气口通过管道和气阀相连接;nh3与所述第二气体净化器3-2的进气口通过管道相连接;所述第二气体净化器3-2的出气口与所述前驱体气相合成流化床2底部的进气口通过管道和气阀相连接;h2与所述第三气体净化器3-3的进气口通过管道相连接;
12.所述前驱体气相合成流化床2上部的出气口与所述第一旋风分离装置5进气口通过管道连接;所述第一旋风分离装置5底部的出料口与所述前驱体气相合成流化床2上部的进料口通过管道相连接;所述第一旋风分离装置5顶部的出气口与所述尾气回收压缩装置6的进气口通过管道相连接;
13.所述前驱体气相合成流化床2下部的出料口与所述脱氯流化床7的进料口通过管道和料阀相连接;所述脱氯流化床7配有所述第一能源供给装置8;所述脱氯流化床7底部的进气口与所述第一气体净化器3-1、第二气体净化器3-2、第三气体净化器3-3的出气口通过管道和气阀相连接;所述脱氯流化床7顶部的出气口与所述第二旋风分离装置9的进气口通过配有所述加热装置10的管道相连接;所述第二旋风分离装置9的出气口与所述尾气回收压缩装置6的进气口通过管道相连接;所述第二旋风分离装置9的出料口与所述氯化铵收集装置11的进料口通过管道和料阀相连接;
14.所述脱氯流化床7下部的出料口与所述深度脱氯流化床12上部的进料口通过管道和料阀相连接;所述深度脱氯流化床12配有所述第二能源供给装置19;所述深度脱氯流化床12顶部的出气口与所述第三旋风分离装置13的进气口通过管道相连接;所述第三旋风分离装置13底部的出料口与所述深度脱氯流化床12上部的进料口通过管道相连接;所述第三旋风分离装置13顶部的出气口与所述酸性气体处理器14的进气口通过管道相连接;所述酸性气体处理器14与所述尾气回收压缩装置6的进气口通过管道和气阀相连接;所述深度脱氯流化床12底部的进气口与所述第一气体净化器3-1、第二气体净化器3-2、第三气体净化器3-3的出气口通过管道和气阀相连接;
15.所述深度脱氯流化床12下部的出料口与所述分解流化床15的进料口通过管道和料阀相连接;所述分解流化床15的上部的出气口与所述第四旋风分离装置16的进气口通过管道相连接;所述第四旋风分离装置16顶部的出气口与所述尾气回收压缩装置6的进气口通过管道和气阀相连接;所述第四旋风分离装置16底部的出料口与所述分解流化床15的上部进料口通过管道相连接;所述分解流化床15底部的进气口与所述第一气体净化器3-1、第二气体净化器3-2、第三气体净化器3-3的出气口通过管道和气阀相连接;
16.所述分解流化床15下部的出料口与所述晶化装置17通过管道和料阀相连接;所述晶化装置17上部的出气口与所述尾气回收压缩装置6的进气口通过管道和气阀相连接;所述晶化装置17底部的进气口与所述第一气体净化器3-1、第二气体净化器3-2、第三气体净化器3-3的出气口通过管道和气阀相连接;所述晶化装置17下部的出料口与所述氮化硅粉体收集装置18的进料口通过管道和料阀相连接。
17.第一气体净化器3-1、第二气体净化器3-2、第三气体净化器3-3分别与相应的气源的出气口连通。
18.本发明基于上述系统制备高质量氮化硅粉体的方法包括以下步骤:
19.所述粉体加料装置1中的物料经过ar或n2清洗后,通过管道和料阀进入被ar或n2清洗过后的所述前驱体气相合成流化床2中并保持流化;ar或n2携带所述硅源蒸发装置4中硅源进入所述前驱体气相合成流化床2中,同时nh3随ar或n2通过管道进入所述前驱体气相合成流化床2中发生前驱体合成反应;所述前驱体气相合成流化床2中的细粉经过所述第一旋风分离装置5分离后再次进入所述前驱体气相合成流化床2中;所述第一旋风分离装置5分离出的尾气进入所述尾气回收压缩装置6,实现尾气的回收再利用;
20.所述前驱体气相合成流化床2中的物料经过管道和料阀进入所述脱氯流化床7,同时,一定量的nh3或h2随ar或n2气体进入所述脱氯流化床7,并确保其中物料处于流化状态;在所述第一能源供给装置8的作用下,所述脱氯流化床7中物料中的nh4cl分解成nh3和hcl,并随尾气经过配有所述加热装置10的管道进入所述第二旋风分离装置9中,nh3和hcl经过冷凝结晶后形成nh4cl固体颗粒进入所述氯化铵收集装置11,尾气进入所述尾气回收压缩装置6,实现尾气的回收再利用;
21.所述脱氯流化床7中脱完nh4cl的物料经过管道和料阀进入所述深度脱氯流化床12,同时一定量的nh3或h2随ar或n2气体进入所述深度脱氯流化床12,并确保其中物料处于流化状态;在所述第二能源供给装置19的作用下,所述深度脱氯流化床12中物料深度脱氯,尾气中的细粉经过所述第三旋风分离装置13分离后进入所述深度脱氯流化床12;所述第三旋风分离装置13分离出的尾气经过所述酸性气体处理器14后进入所述尾气回收压缩装置
6,实现尾气的回收再利用;
22.所述深度脱氯流化床12中的物料经过管道和料阀进入所述分解流化床15,同时一定量的nh3或h2随ar或n2气体进入所述分解流化床15,在一定温度条件下,物料转化为非晶粉体;尾气中的细粉经过所述第四旋风分离装置16分离后进入所述分解流化床15;所述第四旋风分离装置16分离出的尾气进入所述尾气回收压缩装置6,实现尾气的回收再利用;
23.所述分解流化床15中的物料经过管道和料阀进入所述晶化装置17,同时一定量的nh3或h2随ar或n2气体进入所述晶化装置17,在一定温度条件下,非晶粉体转化为晶态粉体并经过管道和料阀进入所述氮化硅粉体收集装置18;所述晶化装置17中的尾气进入所述尾气回收压缩装置6,实现尾气的回收再利用。
24.优选地,所述粉体加料装置1中的物料为非晶或结晶氮化硅粉体的任意一种或任意比例组合,纯度大于99.9%,粒径大于0.5μm。
25.优选地,ar、n2、nh3、h2纯度大于99.9%,且经过所述第一气体净化器3-1、第二气体净化器3-2、第三气体净化器3-3处理后氧和水蒸汽含量均小于500ppm。
26.优选地,所述前驱体气相合成流化床2的温度范围为-10~200℃,流化气体为ar、n2和h2中的任意一种或任意比例组合,且床内nh3与气相硅源进料摩尔比大于等于6,合成时间大于1min,小于等于600min。
27.优选地,所述硅源蒸发装置4中的硅源为纯度大于99.9%的sicl4、sihcl3、sih2cl2、sibr4、sif4等常见硅的卤化物中的任意一种或任意比例组合,且所述硅源蒸发装置4的温度为-10~100℃。
28.优选地,所述脱氯流化床7中物料温度范围为300~800℃,流化气体为ar、n2、nh3和h2中的任意一种或任意比例组合,且物料停留时间大于等于3min,小于等于600min。
29.优选地,所述第一能源供给装置8和第二能源供给装置19为常规电阻加热或微波加热的任意一种或两种加热方式的组合。
30.优选地,所述加热装置10维持温度在400~600℃。
31.优选地,所述深度脱氯流化床12中的温度为600~1000℃,流化气体为ar、n2、nh3和h2中的任意一种或任意比例组合,物料停留时间大于等于10min,小于等于600min。
32.优选地,所述分解流化床15的温度为800~1200℃,且流化气体为ar、n2、nh3和h2气体中的任意一种或任意比例组合,物料停留时间大于等于5min,小于等于600min。
33.优选地,所述晶化装置17的内壁为高纯石墨、氮化硅、碳化硅或氮化硼等高熔点惰性材质,晶化温度为1350~1600℃,物料在床层中堆积密度大于等于0.2g/cm3,物料停留时间大于等于10min,小于等于180min,所述晶化装置17中气体为ar、n2、nh3和h2气体中的任意一种或任意比例组合。
34.气相硅源在流化床中与氨气反应后,依次经过脱氯、深度脱氯、分解、晶化等步骤可制备杂质含量低、α相含量高、粒径细且分布窄的高质量氮化硅粉体。
35.本发明与现有技术相比具有如下优点:
36.与传统sio2的碳热氮化法和si粉直接氮化法相比,本发明制备的氮化硅粉体纯度和α物相含量更高,粒径更细;与传统化学气相沉积法相比,本发明制备的氮化硅粉体效率和α物相含量更高;与硅胺前驱体转化法中气相合成路线相比,本发明攻克了难以合成cl杂质含量低的氮化硅粉体难题,且与传统溶剂热液相合成法和硅胺前驱体转化法中液相合成
路线相比,本发明可实现连续批量化制备高质量氮化硅粉体,生产效率更高,能够大幅度降低高质量氮化硅粉体的价格,扩展粉体的应用范围。
附图说明
37.附图用来提供对本发明的进一步阐释,并且构成说明书的一部分,与本发明的实施例一起用于解释本发明,并不构成对本发明的限制。
38.图1为本发明制备高质量氮化硅粉体的制备系统配置示意图;
39.图2为实施例3制备氮化硅粉体的xrd图;
40.图3为实施例4制备氮化硅粉体的sem图;
41.图4为实施例5制备氮化硅粉体的xrd图;
42.附图标记:
43.1、粉体加料装置;2、前驱体气相合成流化床;3-1、第一气体净化器;3-2、第二气体净化器;3-3、第三气体净化器;4、硅源蒸发装置;5、第一旋风分离装置;6、尾气回收压缩装置;7、脱氯流化床;8、第一能源供给装置;9、第二旋风分离装置;10、加热装置;11、氯化铵收集装置;12、深度脱氯流化床;13、第三旋风分离装置;14、酸性气体处理器;15、分解流化床;16、第四旋风分离装置;17、晶化装置;18、氮化硅粉体收集装置;19、第二能源供给装置。
具体实施方式
44.本说明书中公开地任一特征,除非特别叙述,均可被其他等效或具有类似目的的替代特征加以替换。除非特别叙述,每个特征只是一系列等效或者类似特征中的一个例子而已。所述仅仅是为了帮助理解本发明,不应该视为对本发明的具体限制。
45.下面以附图和具体实施方式对本发明作进一步详细的说明。
46.实施例1
47.结合图1,本实施例高质量氮化硅粉体的制备系统包括粉体加料装置1、前驱体气相合成流化床2、第一气体净化器3-1、第二气体净化器3-2、第三气体净化器3-3、硅源蒸发装置4、第一旋风分离装置5、尾气回收压缩装置6、脱氯流化床7、第一能源供给装置8、第二旋风分离装置9、加热装置10、氯化铵收集装置11、深度脱氯流化床12、第三旋风分离装置13、酸性气体处理器14、分解流化床15、第四旋风分离装置16、晶化装置17、氮化硅粉体收集装置18、第二能源供给装置19;
48.所述粉体加料装置1的出料口与所述前驱体气相合成流化床2上部的进料口通过管道和料阀相连接;ar或n2与所述第一气体净化器3-1的进气口通过管道相连接;所述第一气体净化器3-1的出气口与所述硅源蒸发装置4的进气口通过管道和气阀相连接;所述硅源蒸发装置4的出气口与所述前驱体气相合成流化床2下部的进气口通过管道和气阀相连接;所述第一气体净化器3-1的出气口与所述前驱体气相合成流化床2底部的进气口通过管道和气阀相连接;nh3与所述第二气体净化器3-2的进气口通过管道相连接;所述第二气体净化器3-2的出气口与所述前驱体气相合成流化床2底部的进气口通过管道和气阀相连接;
49.所述前驱体气相合成流化床2上部的出气口与所述第一旋风分离装置5进气口通过管道连接;所述第一旋风分离装置5底部的出料口与所述前驱体气相合成流化床2上部的进料口通过管道相连接;所述第一旋风分离装置5顶部的出气口与所述尾气回收压缩装置6
的进气口通过管道相连接;
50.所述前驱体气相合成流化床2下部的出料口与所述脱氯流化床7的进料口通过管道和料阀相连接;所述脱氯流化床7配有所述第一能源供给装置8;所述脱氯流化床7底部的进气口与所述第一气体净化器3-1、第二气体净化器3-2、第三气体净化器3-3的出气口通过管道和气阀相连接;所述脱氯流化床7顶部的出气口与所述第二旋风分离装置9的进气口通过配有所述加热装置10的管道相连接;所述第二旋风分离装置9的出气口与所述尾气回收压缩装置6的进气口通过管道相连接;所述第二旋风分离装置9的出料口与所述氯化铵收集装置11的进料口通过管道和料阀相连接;
51.所述脱氯流化床7下部的出料口与所述深度脱氯流化床12上部的进料口通过管道和料阀相连接;所述深度脱氯流化床12配有所述第二能源供给装置19;所述深度脱氯流化床12顶部的出气口与所述第三旋风分离装置13的进气口通过管道相连接;所述第三旋风分离装置13底部的出料口与所述深度脱氯流化床12上部的进料口通过管道相连接;所述第三旋风分离装置13顶部的出气口与所述酸性气体处理器14的进气口通过管道相连接;所述酸性气体处理器14与所述尾气回收压缩装置6的进气口通过管道和气阀相连接;所述深度脱氯流化床12底部的进气口与所述第一气体净化器3-1、第二气体净化器3-2、第三气体净化器3-3的出气口通过管道和气阀相连接;
52.所述深度脱氯流化床12下部的出料口与所述分解流化床15的进料口通过管道和料阀相连接;所述分解流化床15的上部的出气口与所述第四旋风分离装置16的进气口通过管道相连接;所述第四旋风分离装置16顶部的出气口与所述尾气回收压缩装置6的进气口通过管道和气阀相连接;所述第四旋风分离装置16底部的出料口与所述分解流化床15的上部进料口通过管道相连接;所述分解流化床15底部的进气口与所述第一气体净化器3-1、第二气体净化器3-2、第三气体净化器3-3的出气口通过管道和气阀相连接;
53.所述分解流化床15下部的出料口与所述晶化装置17通过管道和料阀相连接;所述晶化装置17上部的出气口与所述尾气回收压缩装置6的进气口通过管道和气阀相连接;所述晶化装置17底部的进气口与所述第一气体净化器3-1、第二气体净化器3-2、第三气体净化器3-3的出气口通过管道和气阀相连接;所述晶化装置17下部的出料口与所述氮化硅粉体收集装置18的进料口通过管道和料阀相连接。
54.实施例2
55.本实施例利用上述实施例1中系统制备高质量氮化硅粉体的方法具体包括以下步骤:
56.所述粉体加料装置1中的物料经过ar或n2清洗后,通过管道和料阀进入被ar或n2清洗过后的所述前驱体气相合成流化床2中并保持流化;ar或n2携带所述硅源蒸发装置4中硅源进入所述前驱体气相合成流化床2中,同时nh3随ar或n2通过管道进入所述前驱体气相合成流化床2中发生前驱体合成反应;所述前驱体气相合成流化床2中的细粉经过所述第一旋风分离装置5分离后再次进入所述前驱体气相合成流化床2中;所述第一旋风分离装置5分离出的尾气进入所述尾气回收压缩装置6,实现尾气的回收再利用;
57.所述前驱体气相合成流化床2中的物料经过管道和料阀进入所述脱氯流化床7,同时,一定量的nh3或h2随ar或n2气体进入所述脱氯流化床7,并确保其中物料处于流化状态;在所述第一能源供给装置8的作用下,所述脱氯流化床7中物料中的nh4cl分解成nh3和hcl,
并随尾气经过配有所述加热装置10的管道进入所述第二旋风分离装置9中,nh3和hcl经过冷凝结晶后形成nh4cl固体颗粒进入所述氯化铵收集装置11,尾气进入所述尾气回收压缩装置6,实现尾气的回收再利用;
58.所述脱氯流化床7中脱完nh4cl的物料经过管道和料阀进入所述深度脱氯流化床12,同时一定量的nh3或h2随ar或n2气体进入所述深度脱氯流化床12,并确保其中物料处于流化状态;在所述第二能源供给装置19的作用下,所述深度脱氯流化床12中物料深度脱氯,尾气中的细粉经过所述第三旋风分离装置13分离后进入所述深度脱氯流化床12;所述第三旋风分离装置13分离出的尾气经过所述酸性气体处理器14后进入所述尾气回收压缩装置6,实现尾气的回收再利用;
59.所述深度脱氯流化床12中的物料经过管道和料阀进入所述分解流化床15,同时一定量的nh3或h2随ar或n2气体进入所述分解流化床15,在一定温度条件下,物料转化为非晶粉体;尾气中的细粉经过所述第四旋风分离装置16分离后进入所述分解流化床15;所述第四旋风分离装置16分离出的尾气进入所述尾气回收压缩装置6,实现尾气的回收再利用;
60.所述分解流化床15中的物料经过管道和料阀进入所述晶化装置17,同时一定量的nh3或h2随ar或n2气体进入所述晶化装置17,在一定温度条件下,非晶粉体转化为晶态粉体并经过管道和料阀进入所述氮化硅粉体收集装置18;所述晶化装置17中的尾气进入所述尾气回收压缩装置6,实现尾气的回收再利用。
61.实施例3
62.本实施例在上述实施例2的基础上,所述粉体加料装置1中物料为平均粒径约0.5μm的α相的氮化硅粉体,造粒后呈30μm多孔颗粒,纯度为99.95%;所述硅源蒸发装置4中的硅源为纯度99.99%的sicl4,温度为-5℃;ar,n2,nh3,h2纯度为99.99%,且经过所述第一气体净化器3-1、第二气体净化器3-2、第三气体净化器3-3处理后氧和水蒸汽含量均为60ppm;所述前驱体气相合成流化床2的温度为0℃,流化气体为n2,纯度为99.99%,单位时间进入所述前驱体气相合成流化床2中的nh3与sicl4的摩尔比为等于8,合成时间为600min;所述脱氯流化床7中物料温度范围为400℃,流化气体为ar,脱氯600min;所述第一能源供给装置8和第二能源供给装置19为常规电阻加热;所述加热装置10温度维持在450℃;所述深度脱氯流化床12中的温度为800℃,流化气体为n2和h2的混合气体,其摩尔比为100/1,物料停留时间为100min;所述分解流化床15的温度为1000℃,且流化气体为ar与nh3的混合气体,其摩尔比为100/1,物料停留时间为等于5min;所述晶化装置17的内壁为高纯石墨,晶化温度为1350℃,气体为n2,晶化180min获得了氮化硅粉体。图2为制备氮化硅粉体的xrd图,从图中可以看出,仅检测到α相氮化硅的衍射峰,即表明合成了100%的α-si3n4粉体,。此外,粉体呈现无规则形貌,粉体的平均粒径约0.48μm,粉体cl杂质约80ppm。
63.实施例4
64.本实施例在上述实施例2的基础上,所述粉体加料装置1中物料为一次粒径约0.2μm的无定型氮化硅粉体,造粒后粉体成约10μm多孔颗粒,粉体纯度为99.99%;所述硅源蒸发装置4中的硅源为纯度为99.95%的sihcl3,温度为50℃;ar,n2,nh3,h2纯度为99.999%,且经过所述第一气体净化器3-1、第二气体净化器3-2、第三气体净化器3-3处理后氧和水蒸汽含量均为30ppm;所述前驱体气相合成流化床2的温度为25℃,流化气体为ar,纯度为99.99%,单位时间进入所述前驱体气相合成流化床2中的nh3与sihcl3的摩尔比为等于6,合
成时间为5min;所述脱氯流化床7中物料温度范围为750℃,流化气体为n2,其中含有体积含量20%的nh3,脱氯3min;所述第一能源供给装置8和第二能源供给装置19为微波加热;所述加热装置10温度维持在550℃;所述深度脱氯流化床12中的温度为650℃,流化气体为n2和h2的混合气体,其摩尔比为100/1,物料停留为等于600min;所述分解流化床15的温度为800℃,且流化气体为n2与h2的混合气体,其摩尔比为100/1,物料停留时间为等于600min;所述晶化装置17内壁为氮化硅,晶化温度为1550℃,气体为n2,晶化10min获得了氮化硅粉体。图3为制备氮化硅粉体的sem图,从图中可以看出,粉体呈现等轴状六方形貌,粉体的平均粒径约0.96μm,粉体cl杂质约60ppm,且粉体中α相含量大于95%。
65.实施例5
66.本实施例在上述实施例2的基础上,所述粉体加料装置1中物料为平均800μm氮化硅粉体,粉体纯度为99.99%;所述硅源蒸发装置4中的硅源为99.99%的sibr4,温度为80℃;ar,n2,nh3,h2纯度为99.999%,且经过所述第一气体净化器3-1、第二气体净化器3-2、第三气体净化器3-3处理后氧和水蒸汽含量均小于10ppm;所述前驱体气相合成流化床2的温度为150℃,流化气体为n2,纯度为99.999%,单位时间进入所述前驱体气相合成流化床2中的nh3与sibr4的摩尔比为等于10,合成时间为100min;所述脱氯流化床7中物料温度范围为650℃,流化气体为n2,其中含有体积含量10%的h2,脱氯60min;所述第一能源供给装置8和第二能源供给装置19为常规电阻加热;所述加热装置10温度维持在400℃;所述深度脱氯流化床12中的温度为950℃,流化气体为n2和nh3的混合气体,其摩尔比为100/1,物料停留为等于10min;所述分解流化床15的温度为1150℃,且流化气体为n2气体,物料停留时间为等于400min;所述晶化装置17的温度为1450℃,其中气体为n2,晶化90min获得了氮化硅粉体。图4为制备氮化硅粉体的xrd图,从图中可以看出,仅检测到α相氮化硅的衍射峰,即表明合成了100%的α-si3n4粉体。此外,粉体呈现等轴状,粉体的平均粒径约0.58μm,粉体br杂质约90ppm。
67.本发明未详细阐述部分属于本领域公知技术。
68.最后所应说明的是,以上实施例仅用以说明本发明的技术方案而非限制。尽管参照实施例对本发明进行了详细说明,本领域的普通技术人员应该理解,对本发明的技术方案进行修改或者等同替换,都不脱离本发明技术方案的精神和范围,其均应涵盖在本发明的权利要求范围当中。
再多了解一些
本文用于创业者技术爱好者查询,仅供学习研究,如用于商业用途,请联系技术所有人。