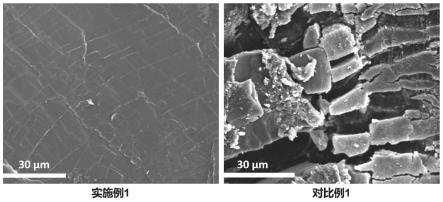
1.本发明属于固态电池的技术领域,具体涉及固态电池用纳米纤维膜型复合电解质的技术领域。
背景技术:
2.传统的液态电解质易发生热失控从而引发电池自燃或者爆炸,存在严重的安全隐患,因此探索高安全、高能量密度和长循环寿命的固态电池已成为当前的研究重点。在固态电池体系中,锂金属负极是满足高能量密度电池的最佳选择,但该类负极材料因存在锂枝晶生长、及与电解质兼容性差等问题而难以投入实际应用,同时,其使用的正极材料也会因充放电中的体积变化使电极与电解质的接触变差,影响电池的循环稳定性和库伦效率。
3.因此,提高固态电池应用性能最为关键的部分是加强固态电解质的设计和界面调控。现有技术中,主要的固态电解质分为有机固态电解质和无机固态电解质,其中,有机固态电解质主要由聚合物基体和锂盐组成,具备较好的灵活性和易加工性,但其在室温下的离子电导率较低、电化学稳定性较差;无机固态电解具有较高的室温本征离子电导率和较宽的电化学窗口,但其与电极之间存在严重的固-固界面问题,从而限制了正极容量的发挥,并为电池带来了锂枝晶穿透电解质的潜在安全风险。另有部分研究通过将聚合物、无机固态电解质和锂盐均匀分散于溶剂中,制备得到有机和无机复合的固态电解质,但该类单一性质的复合电解质无法兼顾正负极对电解质的不同需求,使电解质与不同电极之间的界面问题仍未得到很好的解决。
技术实现要素:
4.鉴于现有技术中存在的问题,本发明提供了一种能同时稳定锂金属负极和浸润正极的复合电解质材料及其制备方法,该材料具有较高的离子电导率、对锂金属稳定性好,能有效抑制锂枝晶的生成和界面副反应的发生,同时与正极材料的接触良好,界面阻抗小,能同时改善正负极界面能,有效提升电池的综合性能。
5.本发明的技术方案如下:
6.一种具有稳定梯度分布结构的复合电解质的制备方法,其包括:
7.步骤一:制备pda修饰的聚合物纺丝纤维膜,其包括:
8.将聚合物纤维基体与溶剂混合,得到纺丝原液;
9.将所述纺丝原液通过静电纺丝得到静电纺丝纤维膜;
10.将所述静电纺丝纤维膜浸渍于聚多巴胺溶液中,静置反应后,得到所述pda修饰的聚合物纺丝纤维膜,其中,聚多巴胺在膜内的质量占比为0.1~0.3mgcm-2
;
11.步骤二:制备电解质前驱体溶液,其包括:
12.向原位聚合前体、锂盐和引发剂中加入有机溶剂,得到基础混合液,所述引发剂和原位聚合前体以及锂盐的质量比为1:60~100:30~60;
13.向所述基础混合液中加入无机陶瓷填料,混合后得到电解质前驱体溶液,其中,所
述无机陶瓷填料和所述原位聚合前体的质量比为1:5~30;
14.步骤三:制备复合电解质材料,其包括:
15.向所述pda修饰的聚合物纺丝纤维膜上滴入所述电解质前驱体溶液,静置得到预聚膜;
16.将所述预聚膜在65~85℃的条件下加热,得到所述具有稳定梯度分布结构的复合电解质。
17.上述制备方法中,采用多巴胺(da)在纳米纤维膜表面氧化自聚合形成具有丰富官能团的黏附层(pda),作为无机陶瓷填料和纳米纤维膜相互作用的桥梁,形成共价键可锚定无机陶瓷填料,保证梯度分布结构的稳定存在,不会出现充放电过程中无机陶瓷填料含量较高一侧与电解质发生分离的现象,使所得材料从一端到另一端的无机陶瓷填料含量呈梯度逐渐降低。该制备方法同时赋予纳米纤维膜与原位聚合前驱体溶液良好的亲和力,通过氢键作用有助于交联网络的形成,能够截留更多电解液。
18.根据上述制备方法得到的电解质膜可在进行电池组装时,将富集在复合电解质的顶部的无机陶瓷填料与电池负极接触,有效抑制锂枝晶和副反应,提高界面稳定性,其原位聚合部分有利于保证复合电解质和正极材料之间的浸润性,适应充放电过程中的体积变化。
19.根据本发明的一些优选实施方式:所述纺丝原液的浓度为5~20wt%。
20.根据本发明的一些优选实施方式:所述静电纺丝纤维膜厚度为80~140μm。
21.根据本发明的一些优选实施方式:所述静置反应包括:将所述静电纺丝纤维膜浸渍于所述聚多巴胺溶液中,室温下放置2~5天,其后洗涤并于60~80℃干燥18~24小时。
22.根据本发明的一些优选实施方式:所述预聚膜在65~85℃的条件下真空加热2~4小时,得到所述具有稳定梯度分布结构的复合电解质。
23.根据本发明的一些优选实施方式,所述聚多巴胺溶液的获得包括:
24.将多巴胺加入可溶性溶剂中,调节所得溶液的ph为8.5,使多巴胺在室温下氧化自聚合成聚多巴胺,得到所述聚多巴胺(pda)溶液。
25.根据本发明的一些优选实施方式,所述可溶性溶剂选自乙醇、乙二醇、去离子水、丙酮、正丁醇、异丙醇中的一种或多种。
26.根据本发明的一些优选实施方式,所述多巴胺与所述可溶性溶剂的质量比为1:100~300。
27.根据本发明的一些优选实施方式,所述聚合物纤维基体选自聚四氟乙烯、聚偏氟乙烯-六氟丙烯共聚物、聚丙烯腈、聚酰亚胺、尼龙、不溶于锂离子电池电解液的纤维素材料中的一种或多种。
28.根据本发明的一些优选实施方式,所述纺丝原液的溶剂选自n,n-二甲基甲酰胺、丙酮、四氢呋喃、n-甲基吡咯烷酮、乙腈、乙醇、乙二醇中的一种或多种。
29.根据本发明的一些优选实施方式,所述原位聚合前体选自聚(乙二醇)二丙烯酸酯、聚乙二醇二甲醚、聚乙二醇二甲基丙烯酸酯、聚甲基丙烯酸甲酯、1,3-二氧戊环中的一种或多种。
30.根据本发明的一些优选实施方式,所述锂盐选自四氟硼酸锂、二氟草酸硼酸锂、双氟磺酰亚胺锂、高氯酸锂、双三氟甲烷磺酰亚胺锂中的一种或多种。
31.根据本发明的一些优选实施方式,所述引发剂选自偶氮二异丁腈、偶氮二异丁酸二甲酯、过氧化二苯甲酰胺、四氟硼酸锂、六氟磷酸锂中的任一种。
32.根据本发明的一些优选实施方式,所述有机溶剂选自碳酸乙烯酯、碳酸二甲酯、碳酸丙烯酯、碳酸二乙酯中的一种或多种。
33.根据本发明的一些优选实施方式,所述无机陶瓷填料可以选自li
0.34
la
0.567
tio3、li7la3zr2o
12
、li
6.4
la3zr
1.4
ta
0.6o12
、li
2.88
po
3.73n0.14
、li
1.3
al
0.3
ti
1.7
(po4)3、li
1.5
al
0.5
ge
1.5
p3o
12
中的一种或多种。
34.根据本发明的一些优选实施方式,所述原位聚合前体与所述有机溶剂的质量比为1:5~15。
35.本发明进一步提供了根据上述任一制备方法制备得到的具有稳定梯度分布结构的复合电解质。
36.该复合电解质中含有功能化的纳米纤维膜和含有无机陶瓷填料的原位聚合体,且无机陶瓷填料的含量在复合电解质中呈现稳定的梯度分布,该结构能够充分发挥无机陶瓷填料及聚合体的优势,同时提升电解质与正极和负极的界面性能,并提升电池的综合性能。
37.本发明进一步提供了含有上述制备方法制备得到的具有稳定梯度分布结构的复合电解质的固态电池。
38.根据本发明的一些优选实施方式,所述固态电池的制备方法包括:
39.将所述pda修饰的聚合物纺丝纤维膜上滴入20~40μl所述电解质前驱体溶液,静置20~30min得到预聚膜;
40.将所述预聚膜在65~85℃的条件下真空加热2~4小时,得到所述具有稳定梯度分布结构的复合电解质膜;
41.将所述复合电解质膜组装成全电池,其中,复合电解质膜的顶部即其无机陶瓷填料浓度较高一侧与电池负极接触,较低一侧与电池正极接触,得到所述固态电池。
42.根据本发明的一些优选实施方式,所述固态电池的制备方法包括:
43.将所述pda修饰的聚合物纺丝纤维膜叠加在电池正极上,向该纤维膜上滴入20~40μl所述电解质前驱体溶液,其后将电池负极置于最上层,密封得到电池前驱体;
44.将所述电池前驱体在65~85℃的条件下真空加热2~4小时,得到所述固态电池。
45.根据本发明的一些优选实施方式,所述固态电池中,所述电池负极为金属锂材料,电池正极为lifepo4材料。
46.本发明的制备方法可通过聚合物纺丝纤维膜对无机陶瓷填料的阻碍以及修饰层与无机陶瓷填料的相互作用,实现对复合电解质中静电纺丝纤维膜骨架和无机陶瓷填料分布的调控,得到无机陶瓷填料含量在电解质内从一端到另一端呈稳定的梯度分布的结构,使得在进一步组装成电池时,可将复合电解质的无机陶瓷填料富集端与电池负极接触。同时,本发明的制备方法中,原位聚合电解质有利于确保电极/电解质界面紧密接触,从而针对性地解决电解质和锂金属之间的剧烈反应以及锂枝晶的生长问题,并得益于充分润湿的固固界面,所得电解质可有效有缓解正极材料在充放电过程中体积变化引起的界面失控。
47.本发明的制备方法可同时满足固态电池正负极的需求,充分发挥各种材料的综合优势和协同效果。
48.本发明制备得到的电解质不仅能满足固态电池正负极界面的需求,且能够发挥无
机固态电解质的本征属性,提供较好的机械性能和较高的离子电导率,获得综合性能优异的复合电解质。
49.本发明进一步具有以下有益效果:
50.(1)本发明的制备方法通过对静电纺丝纤维膜的功能化调控实现稳定梯度分布结构的成型,其中,pda修饰的聚合物纺丝纤维膜表面丰富的官能团与无机陶瓷填料之间的相互作用使其保持稳定的梯度分布结构,使材料在组装电池以及充放电过程中不易发生分层和剥离的现象,还可赋予纳米纤维膜与原位聚合前驱液良好的亲和力,通过修饰层和原位聚合前体之间的氢键作用有助于交联网络的形成,能够有效截留电解液;
51.(2)本发明制备得到的具有梯度分布结构的复合电解质组装成电池时,在负极可具有高密度的无机陶瓷填料,能充分发挥无机陶瓷填料的优势,使得复合电解质膜具有较高的离子电导率,对锂金属稳定性好,能有效抑制锂枝晶的生成和界面副反应的发生;在正极具有原位聚合的聚合体,充分润湿界面,与正极材料的接触良好,界面阻抗小;同时改善正负极界面能有效提升电池的综合性能;
52.(3)本发明的制备方法通过简单的功能化策略即可实现梯度分布结构的稳定存在,在制备过程中不需要辐射设备引发聚合,操作流程简单,能耗低。
附图说明
53.图1为具体实施方式所述梯度分布结构的复合电解质的制备流程图。
54.图2为实施例1所得功能化静电纺丝纤维膜的sem。
55.图3为电解质膜横断面sem以及对应的eds能谱分析:(a)为实施例1所得复合电解质膜;(b)为对比例1所得准固态电解质膜。
56.图4为实施例1所得复合电解质预对比例1的准固态电解质膜的阻抗测试对比图。
57.图5为实施例1所得复合电解质和对比例1的准固态电解质膜对应的全电池的循环性能对比图。
58.图6为实施例1所得复合电解质和对比例1的准固态电解质膜对应的电池循环后阻抗对比图。
59.图7为实施例1所得复合电解质和对比例1的准固态电解质膜对应的电池循环后拆解得到的锂金属负极sem对比图。
具体实施方式
60.以下结合实施例和附图对本发明进行详细描述,但需要理解的是,所述实施例和附图仅用于对本发明进行示例性的描述,而并不能对本发明的保护范围构成任何限制。所有包含在本发明的发明宗旨范围内的合理的变换和组合均落入本发明的保护范围。
61.根据本发明的技术方案,所述具有稳定梯度分布结构的复合电解质的制备方法的一些具体实施方式包括以下步骤:
62.步骤一:制备pda修饰的聚合物纺丝纤维膜,其包括:
63.将聚合物纤维基体与溶剂混合,得到纺丝原液,所述纺丝原液的浓度为5~20wt%;
64.将所得纺丝原液通过高压静电纺丝及干燥得到静电纺丝纤维膜,所述静电纺丝纤
维膜厚度为80~140μm;
65.将所得静电纺丝纤维膜浸渍于聚多巴胺(pda)溶液中,在室温下放置2~5天,其后洗涤并于60~80℃干燥18~24小时,得到pda修饰的聚合物纺丝纤维膜,该修饰膜中,pda在膜内的质量占比为0.1~0.3mgcm-2
。
66.步骤二:制备电解质前驱体溶液,其包括:
67.向原位聚合前体、锂盐和引发剂中加入有机溶剂,得到基础混合液,所述引发剂和原位聚合前体以及锂盐的质量比为1:60~100:30~60;
68.向基础混合液中加入无机陶瓷填料,混合后得到电解质前驱体溶液,其中,所述无机陶瓷填料和所述原位聚合前体的质量比为1:5~30。
69.步骤三:制备复合电解质材料,其包括:
70.向步骤一得到的pda修饰的聚合物纺丝纤维膜上滴入20~40μl步骤二得到的电解质前驱体溶液,静置20~30min得到预聚膜;
71.将所述预聚膜在65~85℃的条件下真空加热2~4小时使电解质前驱体溶液完全聚合,得到所述具有稳定梯度分布结构的复合电解质。
72.根据以上复合电解质可进一步得到含有该电解质的固态电池,其具体的一些组装方式如:
73.方式一:
74.将步骤一得到的pda修饰的聚合物纺丝纤维膜置于干净的玻璃板上,用注射器向其中滴入20~40μl步骤二得到的电解质前驱体溶液,静置20~30min得到预聚膜;
75.将所述预聚膜在65~85℃的条件下真空加热2~4小时,得到所述具有稳定梯度分布结构的复合电解质膜;
76.将得到的复合电解质膜组装成全电池,其中,电池正极采用lifepo4,负极采用金属锂,复合电解质膜的顶部即其无机陶瓷填料浓度较高一侧与负极接触,较低一侧与正极接触,得到所述固态电池。
77.方式二:
78.将步骤一得到的pda修饰的聚合物纺丝纤维膜叠加在lifepo4正极片上,其用注射器向纤维膜上滴入20~40μl步骤二得到的电解质前驱体溶液,其后将锂金属负极置于最上层,密封得到电池前驱体;
79.将所述电池前驱体在65~85℃的条件下加热2~4小时,使电解质前驱体溶液完全聚合,制备得到所述固态电池。
80.进一步的,上述具有稳定梯度分布结构的复合电解质的制备方法和/或含有该电解质的固态电池的组装方式中:
81.优选的,
82.所述聚合物纤维基体选自聚四氟乙烯(pvdf)、聚偏氟乙烯-六氟丙烯共聚物(pvdf-hfp)、聚丙烯腈(pan)、聚酰亚胺(pi)、尼龙、不溶于锂离子电池电解液的纤维素材料中的一种或多种。
83.所述纺丝原液的溶剂选自n,n-二甲基甲酰胺、丙酮、四氢呋喃、n-甲基吡咯烷酮、乙腈、乙醇、乙二醇中的一种或多种。
84.所述聚多巴胺(pda)溶液的获得包括:
85.将多巴胺加入可溶性溶剂中,调节所得溶液的ph为8.5,其后多巴胺在室温下氧化自聚合成聚多巴胺(pda),得到所述聚多巴胺(pda)溶液。
86.其中,所述可溶性溶剂选自乙醇、乙二醇、去离子水、丙酮、正丁醇、异丙醇中的一种或多种。
87.多巴胺与可溶性溶剂的质量比为1:100~300。
88.所述原位聚合前体选自聚(乙二醇)二丙烯酸酯(pegda)、聚乙二醇二甲醚(pegdme)、聚乙二醇二甲基丙烯酸酯(pegdma)、聚甲基丙烯酸甲酯(pmma)、1,3-二氧戊环(dol)中的一种或多种。
89.所述锂盐选自四氟硼酸锂(libf4)、二氟草酸硼酸锂(liodfb)、双氟磺酰亚胺锂(lifsi)、高氯酸锂(liclo4)、双三氟甲烷磺酰亚胺锂(litfsi)中的一种或多种。
90.所述引发剂选自偶氮二异丁腈、偶氮二异丁酸二甲酯、过氧化二苯甲酰胺、四氟硼酸锂、六氟磷酸锂中的任一种。
91.步骤二中,所述有机溶剂选自碳酸乙烯酯(ec)、碳酸二甲酯(dmc)、碳酸丙烯酯(pc)、碳酸二乙酯(dec)中的一种或多种。
92.所述原位聚合前体与所述有机溶剂的质量比为1:5~15。
93.所述无机陶瓷填料可以选自li
0.34
la
0.567
tio3(llto)、li7la3zr2o
12
(llzo)、li
6.4
la3zr
1.4
ta
0.6o12
(llzto)、li
2.88
po
3.73n0.14
(lipon)、li
1.3
al
0.3
ti
1.7
(po4)3(latp)、li
1.5
al
0.5
ge
1.5
p3o
12
(lagp)中的一种或多种。
94.参照附图1,在更具体的一些实施方式中,所述具有稳定梯度分布结构的复合电解质的制备方法包括:
95.步骤一:静电纺丝纤维膜的制备
96.(1)在充满氩气的手套箱中称取一定质量的聚合物纤维基体,加入透明玻璃瓶中;其中,所述聚合物纤维基体选自聚四氟乙烯(pvdf)、聚偏氟乙烯-六氟丙烯共聚物(pvdf-hfp)、聚丙烯腈(pan)、聚酰亚胺(pi)、尼龙、不溶于锂离子电池电解液的纤维素材料中的一种或多种;
97.(2)向玻璃瓶中加入适量的溶剂,得到混合溶液,将该溶液在50~80℃的条件下磁力搅拌8~12小时,以获得浓度约为5~20wt%的均匀透明的纺丝原液;其中,所述溶剂选自n,n-二甲基甲酰胺、丙酮、四氢呋喃、n-甲基吡咯烷酮、乙腈、乙醇、乙二醇中的一种或几种;所述聚合物纤维基体与溶剂的质量比为1:5~20;
98.(3)将(2)中得到的纺丝原液转移到注射器中,高压静电纺丝得到聚合物纤维膜;在60~80℃的条件下真空干燥12~24小时后,得到厚度约为80~140μm的静电纺丝纤维膜待用;
99.(4)在充满氩气的手套箱中称取一定质量的多巴胺(da)于另一透明玻璃瓶中,并将其溶解在一定量的溶剂中,所述溶剂选自乙醇、乙二醇、去离子水、丙酮、正丁醇、异丙醇中的一种或几种;多巴胺与溶剂的质量比为1:100~300;其后调节溶液ph为8.5,室温下磁力搅拌4~6小时,使多巴胺氧化自聚合成聚多巴胺(pda),将获得透明的溶液倒入玻璃培养皿中待用;
100.(5)将(3)中的静电纺丝纤维膜浸渍在(4)得到的溶液中,在室温下放置2~5天,取出后用丙酮和去离子水冲洗涤4~5次,转移至真空干燥箱中在60~80℃的条件下干燥18~
24小时后取出,制备得到pda修饰的聚合物纺丝纤维膜,其中pda在膜内的质量占比为0.1~0.3mgcm-2
。
101.步骤二:电解质前驱体溶液的制备
102.(1)在充满氩气的手套箱中称取一定质量的原位聚合前体、锂盐和引发剂于透明玻璃瓶中,其中,所述原位聚合前体选自聚(乙二醇)二丙烯酸酯(pegda)、聚乙二醇二甲醚(pegdme)、聚乙二醇二甲基丙烯酸酯(pegdma)、聚甲基丙烯酸甲酯(pmma)、1,3-二氧戊环(dol)中的一种或多种;所述锂盐为四氟硼酸锂(libf4)、二氟草酸硼酸锂(liodfb)、双氟磺酰亚胺锂(lifsi)、高氯酸锂(liclo4)、双三氟甲烷磺酰亚胺锂(litfsi)中的一种或多种;所述引发剂为偶氮二异丁腈、偶氮二异丁酸二甲酯、过氧化二苯甲酰胺、四氟硼酸锂、六氟磷酸锂中的一种;所述引发剂和原位聚合前体以及锂盐的质量比为1:60~100:30~60;
103.(2)向步骤(1)得到的混合物中加入有机溶剂,加入溶剂后在室温下磁力搅拌6~8小时,得到均匀透明的溶液;其中,原位聚合前体与有机溶剂的质量比为1:5~15;有机溶剂选自碳酸乙烯酯(ec)、碳酸二甲酯(dmc)、碳酸丙烯酯(pc)、碳酸二乙酯(dec)中的一种或多种;
104.(3)向(2)中混合溶液中加入无机陶瓷填料,室温下搅拌5~8小时后得到白色均匀前驱体溶液;其中,无机陶瓷填料和原位聚合前体的质量比优选为1:5~30,所述无机陶瓷填料选自li
0.34
la
0.567
tio3(llto)、li7la3zr2o
12
(llzo)、li
6.4
la3zr
1.4
ta
0.6o12
(llzto)、li
1.3
al
0.3
ti
1.7
(po4)3(latp)、li
1.5
al
0.5
ge
1.5
p3o
12
(lagp)中的一种或多种。
105.步骤三:组装电池
106.方式一:
107.(1)将步骤一中得到的pda修饰的聚合物纺丝纤维膜置于干净的玻璃板上,用注射器向其中滴入20~40μl步骤二中得到的白色均匀前驱体溶液,静置20~30min得到预聚膜;
108.(2)将上述步骤中的预聚膜转移至真空干燥箱,在65~85℃的条件下加热2~4小时使得电解质前体溶液完全聚合;其中,由于聚合物纺丝纤维膜对无机陶瓷填料的阻碍以及修饰层与无机陶瓷填料的相互作用而形成具有梯度分布结构的复合电解质膜,备用;
109.(3)将得到的复合电解质膜组装成阻塞电池,测试其离子电导;
110.(4)将得到的复合电解质膜组装成全电池,所述电池正极采用lifepo4,负极采用金属锂,上述复合电解质膜的顶部即无机陶瓷填料浓度较高一侧与负极接触,较低一侧与正极接触,测试其全电池的电化学性能。
111.方式二:
112.(1)电池正极采用lifepo4,负极采用金属锂,所述正极片放置在电池负极壳底部,将步骤一得到的pda修饰的聚合物纺丝纤维膜依次叠加,用注射器向其中滴入20~40μl步骤二中得到的白色均匀前驱体溶液,负极锂金属置于最上层,密封电池;
113.(2)将上述组装的电池在65~85℃的条件下加热2~4小时使得电解质前体溶液完全聚合,制备得到全电池待测。
114.以下结合实施例对本发明的技术方案做进一步的展示。
115.实施例1
116.本实施例提供一种具有梯度分布结构设计的复合电解质,所述复合电解质包括静电纺丝纤维膜和含有无机陶瓷填料的原位聚合电解液;所述静电纺丝纤维膜为pvdf纺丝纤
维膜,无机陶瓷填料为llzto,原位聚合前驱体为pegda。
117.具体制备步骤如下:
118.步骤一:静电纺丝纤维膜的制备
119.(1)在充满氩气的手套箱中称取2gpvdf颗粒,加入透明璃瓶中,向上述玻璃瓶中加入18gn,n-二甲基甲酰胺(dmf)和丙酮的混合溶液(体积比为1:1),将上述溶液在60℃的条件下磁力搅拌12小时,以获得均匀透明的纺丝原液,浓度约为10wt%;
120.(2)将(1)中得到的纺丝原液转移到注射器中,高压静电纺丝得到聚合物纤维膜;在80℃的条件下真空干燥24小时后,得到厚度约为80~140μm的静电纺丝纤维膜待用;
121.(3)在充满氩气的手套箱中称取0.3g多巴胺(da)于另一透明玻璃瓶中,向其中加入70g无水乙醇,调节ph至8.5,加入溶剂后室温下磁力搅拌6小时获得透明的溶液倒入玻璃培养皿中待用;
122.(4)将(2)中的静电纺丝纤维膜浸渍在(3)得到的溶液中,在室温下放置4天,取出后用丙酮和去离子水冲洗涤4次,转移至真空干燥箱中在80℃的条件下干燥24小时后取出,制备得到pda修饰的pvdf纺丝纤维膜(pda@pvdf),其中pda在膜内的质量占比为0.1~0.3mgcm-2
。
123.所得pda修饰的pvdf纺丝纤维膜的sem图如附图2所示,可以看出聚多巴胺均匀的黏附在pvdf纺丝纤维膜上,而不是堆积在纳米纤维膜的孔隙中,修饰前后纺丝纤维膜的形貌无明显差别。
124.步骤二:电解质前驱体溶液的制备
125.(1)在充满氩气的手套箱中称取一定质量原位聚合前体、锂盐和引发剂于透明玻璃瓶中,所述原位聚合前体为聚(乙二醇)二丙烯酸酯(pegda)、锂盐为lidfob,引发剂为偶氮二异丁腈(aibn),三者的质量比为60:40:1;
126.(2)向上述混合物中加入有机溶剂,原位聚合前体与有机溶剂的质量比为1:10,有机溶剂优选为碳酸乙烯酯(ec)和碳酸二甲酯(dmc)的混合溶液(体积比为1:1),加入溶剂后在室温条件下搅拌8小时得到均匀混合溶液;
127.(3)向(2)中的混合溶液加入无机陶瓷填料,所述无机陶瓷填料优选为llzto,与原位聚合前体的质量比为1:20,加入后继续在室温下搅拌6小时后得到白色均匀前驱体溶液。
128.步骤三:将复合电解质膜组装电池
129.(1)将步骤一中得到的pda@pvdf纤维膜置于干净的玻璃板上,用注射器向其中滴入30μl步骤二中得到的白色均匀前驱体溶液,静置30min得到预聚膜;
130.(2)将上述步骤中的预聚膜转移至真空干燥箱,在80℃的条件下加热4小时使得电解质前体溶液完全聚合;其中,由于pda@pvdf纤维膜对llzto的阻碍以及修饰层与llzto的相互作用而形成具有梯度分布结构的复合电解质膜。如图3(a)所示,结合eds能谱图可以看到复合电解质膜呈现明显的梯度结构;
131.(3)将得到的复合电解质膜组装成阻塞电池,测试其离子电导率,并将所得结果与现有技术中的商用隔膜制备的准固态电解质进行对比,其结果如附图4所示;
132.(4)将得到的复合电解质膜组装成全电池,所述电池正极采用lifepo4,负极采用金属锂,上述复合电解质膜的顶部即llzto浓度较高一侧与负极接触,浓度较低一侧与正极接触,测试其全电池的电化学性能,并与现有技术中的商用隔膜进行对比,其结果如附图5
~6所示。
133.(5)将完成循环测试后的电池进行拆解,对拆解得到的锂金属与使用现有技术中的商业隔膜的电池拆解后锂金属进行sem表征对比,如附图7所示。
134.实施例2
135.本实施例提供一种具有梯度分布结构设计的复合电解质,所述复合电解质包括静电纺丝纤维膜和含有无机陶瓷填料的原位聚合电解液;所述静电纺丝纤维膜为pvdf纺丝纤维膜,无机陶瓷填料为llzto,原位聚合前驱体为pegda。
136.复合电解质膜的具体制备步骤以及相应的物质比例与实施例1相同,区别仅在于固态电池的制备步骤。本实施例使用如下的固体电池制备步骤:
137.(1)电池正极采用lifepo4,负极采用金属锂,将正极片放置在电池负极壳底部,将步骤一得到的pda修饰的聚合物纺丝纤维膜依次叠加,用注射器向其中滴入30μl步骤二中得到的白色均匀前驱体溶液,其中,由于pda@pvdf纤维膜对llzto的阻碍以及修饰层与llzto的相互作用而形成具有梯度分布结构的复合电解质膜,负极锂金属置于最上层与浓度较高的llzto一侧接触,密封电池;
138.(2)将上述组装的电池在80℃的条件下加热4小时使得电解质前体溶液完全聚合,制备得到全电池,待测。
139.实施例3
140.本实施例提供一种具有梯度分布结构设计的复合电解质,所述复合电解质包括静电纺丝纤维膜和含有无机陶瓷填料的原位聚合电解液;所述静电纺丝纤维膜为pvdf-hfp纤维膜,无机陶瓷填料为latp,原位聚合前体为dol,锂盐为litfsi,引发剂为aibn。其中,无机陶瓷填料与原位聚合前体的质量比为1:5,其余物质比例和具体的制备步骤与实施例1相同。
141.实施例4
142.本实施例提供一种具有梯度分布结构设计的复合电解质,所述复合电解质包括静电纺丝纤维膜和含有无机陶瓷填料的原位聚合电解液;所述静电纺丝纤维膜为pvdf纤维膜,无机陶瓷填料为llto,原位聚合前体为pegdme,锂盐为litfsi,引发剂为lipf6,其中,无机陶瓷填料与原位聚合前体的质量比为1:10,其余物质比例和具体的制备步骤与实施例1相同。
143.实施例5
144.本实施例提供一种具有梯度分布结构设计的复合电解质,所述复合电解质包括静电纺丝纤维膜和含有无机陶瓷填料的原位聚合电解液;所述静电纺丝纤维膜为pi纤维膜,无机陶瓷填料为llzo,原位聚合前体为pegdma,锂盐为litfsi,引发剂为lipf6,其中,无机陶瓷填料与原位聚合前体的质量比为1:30,其余物质比例和具体的制备步骤与实施例1相同。
145.实施例6
146.本实施例提供一种具有梯度分布结构设计的复合电解质,所述复合电解质包括静电纺丝纤维膜和含有无机陶瓷填料的原位聚合电解液;所述静电纺丝纤维膜为尼龙纤维膜,无机陶瓷填料为lagp,原位聚合前体为pmma,锂盐为lidfob,引发剂为aibn。其中,无机陶瓷填料与原位聚合前体的质量比为1:50,其余物质比例和具体的制备步骤与实施例1相
同。
147.对比例1
148.本对比例提供一种准固态电解质,所述准固态电解质采用商用聚丙烯(pp)作为隔膜,加入原位聚合前体溶液,具体制备工艺如下:
149.步骤一:电解质前驱体溶液的制备
150.(1)在充满氩气的手套箱中称取一定质量原位聚合前体、锂盐和引发剂于透明玻璃瓶中,所述原位聚合前体为聚(乙二醇)二丙烯酸酯(pegda)、锂盐为lidfob,引发剂为偶氮二异丁腈(aibn),三者的质量比为60:40:1;
151.(2)向上述混合物中加入有机溶剂,原位聚合前体与有机溶剂的质量比为1:10,有机溶剂优选为碳酸乙烯酯(ec)和碳酸二甲酯(dmc)的混合溶液(体积比为1:1),加入溶剂后在室温条件下搅拌8小时得到均匀混合溶液;
152.(3)向(2)中的混合溶液加入无机陶瓷填料,所述无机陶瓷填料优选为llzto,与原位聚合前体的质量比为1:20,加入后继续在室温下搅拌6小时后得到白色均匀前驱体溶液。
153.步骤二:组装电池
154.(1)将商用pp隔膜置于干净的玻璃板上,用注射器向其中滴入30μl步骤一中得到的白色均匀前驱体溶液,静置30min得到预聚膜;
155.(2)将上述步骤中的预聚膜转移至真空干燥箱,在80℃的条件下加热4小时使得电解质前体溶液完全聚合,得到准固态电解质膜,如图3(b)所示,所述电解质膜中的无机陶瓷填料呈现相对较为均匀的分布;
156.(3)将对比例1的准固态电解质膜组装的阻塞电池与实施例1的阻塞电池进行离子电导率测试,所得对比图如附图4所示;
157.(4)将得到的准固态电解质膜组装成全电池,所述电池正极采用lifepo4,负极采用金属锂,与实施例1所得全电池进行全电池性能测试和电池循环后阻抗测试,所得对比图如附图5~6所示;
158.(5)将对比例1的准固态电解质膜组装的全电池与实施例1所得全电池完成循环测试后进行拆解,对拆解得到的锂金属进行sem表征对比,对比结果如附图7所示。
159.对比例2
160.本对比例提供一种准固态电解质,所述准固态电解质采用商用聚丙烯(pp)作为隔膜,加入原位聚合前体溶液,区别在于未加无机陶瓷填料,具体制备工艺如下:
161.步骤一:电解质前驱体溶液的制备
162.(1)在充满氩气的手套箱中称取一定质量原位聚合前体、锂盐和引发剂于透明玻璃瓶中,所述原位聚合前体为聚(乙二醇)二丙烯酸酯(pegda)、锂盐为lidfob,引发剂为偶氮二异丁腈(aibn),三者的质量比为60:40:1;
163.(2)向上述混合物中加入有机溶剂,原位聚合前体与有机溶剂的质量比为1:10,有机溶剂优选为碳酸乙烯酯(ec)和碳酸二甲酯(dmc)的混合溶液(体积比为1:1),加入溶剂后在室温条件下搅拌8小时得到均匀透明前驱体溶液备用;
164.步骤二:组装电池
165.(1)将商用pp隔膜置于干净的玻璃板上,用注射器向其中滴入30μl步骤一中得到的均匀透明前驱体溶液,静置30min得到预聚膜;
166.(2)将上述步骤中的预聚膜转移至真空干燥箱,在80℃的条件下加热4小时使得电解质前体溶液完全聚合,得到准固态电解质膜;
167.(3)将(2)中得到的准固态电解质膜组装成阻塞电池进行离子电导率测试;
168.(4)将(2)中得到的准固态电解质膜组装成全电池,所述电池正极采用lifepo4,负极采用金属锂,进行全电池性能测试和电池循环后阻抗测试。
169.对以上实施例1-6及对比例1-2进行测试,包括:
170.对实施例1-6和对比例1-2制备得到的电解质膜进行的离子电导率测试,如下:将电解质膜夹在两个对称的不锈电极之间,使用电化学工作站进行交流阻抗测试,频率范围在0.1hz-1000000hz,将测试得到的阻抗值r代入公式σ=l/(s
·
r)计算得到相应电解质膜的离子电导率,其中l为电解质膜的厚度,s为不锈钢电极的表观面积。
171.对实施例1-5和对比例1-2进行全电池性能测试,如下:
172.使用新威电池测试系统,在倍率为1c,电压范围为2.5v-3.8v即充电到3.8v,放电到2.5v的条件下测试。
173.其中,实施例1和对比例1的测试结果如附图所示,各实施例和对比例的测试结果如下表1所示。
174.表1各实施例和对比例电解质膜的全电池性能比较
[0175][0176]
根据上述表内容和附图可以看出:
[0177]
(1)本发明实施例1-6提供的复合电解质膜的锂离子电导率明显高于对比例1-2提供的准固态电解质膜的离子电导率;
[0178]
(2)综合实施例1和对比例1可以看出,本发明提供的复合电解质膜电池的放电比容量和循环次数均有所提高,使用本发明制备的梯度分布结构复合电解质的锂金属表面光滑(附图7),说明所得复合电解质与电极界面兼容性好,且能抑制副反应的发生,梯度结构的设计能够显著抑制锂枝晶的生成,从而改善电池的循环稳定性。对比例1中的无机陶瓷填料在电解质中的分布相对较为均匀(附图3),但是无法充分发挥所加入的无机陶瓷填料的优势,界面副反应及锂枝晶的生长导致电池容量急剧衰减。本发明提供的复合电解质电池
循环后电荷转移阻抗明显低于对比例1提供的电解质膜组装的电池,说明本发明提供的方法能有效缓解正极材料在充放电过程中体积变化引起的界面失控,减小极化。
[0179]
(3)综合实施例1-6可以看出可以看出,本发明提供的复合电解质膜能够显著提高电池的综合性能,但是当无机陶瓷含量的引入量较多时(实施例6),在一定程度上影响锂沉积的均匀性,从而使得电池的综合性能下降,因此本发明优选的无机陶瓷填料的加入量与原位聚合前体的质量比为1:5~30。
[0180]
以上实施例仅是本发明的优选实施方式,本发明的保护范围并不仅局限于上述实施例。凡属于本发明思路下的技术方案均属于本发明的保护范围。应该指出,对于本技术领域的普通技术人员来说,在不脱离本发明原理的前提下的改进和润饰,这些改进和润饰也应视为本发明的保围。
再多了解一些
本文用于创业者技术爱好者查询,仅供学习研究,如用于商业用途,请联系技术所有人。