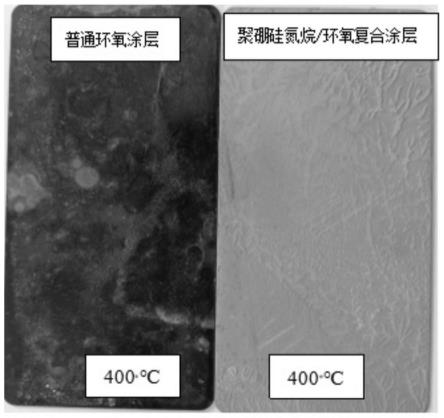
1.本发明涉及抗腐蚀涂层制备技术领域,特别是指一种聚硼硅氮烷/环氧复合耐高温抗腐蚀涂料及其制备方法。
背景技术:
2.随着人类社会科技的进步,各行各业均会存在器物腐蚀的问题。一些传统行业腐蚀如:航洋重防腐、河流湖泊重防腐、户外耐酸雨等腐蚀均已经有了较为优秀的产品。但是,在高温行业的腐蚀还有一些问题有待解决:石油管道的抗热石油腐蚀及渗透(200℃),炼钢炉、热力发电厂等烟囱外侧抗腐蚀(200-300℃),焚烧炉外壁(100-300℃),供暖水路管道内外壁抗腐蚀(50-90℃)等,还存在产品空白、种类单一生产成本较高以及施工工艺困难等问题。因此,随着高温行业对耐高温防腐涂层需求的日益增多,开发耐高温抗腐蚀涂层也成为涂料行业的研究热点之一。
3.环氧树脂作为在抗腐蚀涂层中应用最多的树脂之一,其具有非常优异的机械性能、耐化学品、耐水性以及施工性能。同时,环氧树脂在耐腐蚀领域的使用已经过时间验证,其自身的优异效果得到了社会的广泛认可。但是,普通的环氧树脂及固化剂固化后涂层存在耐湿热性能差、高温残余量低等问题,限制了环氧树脂在高温耐腐蚀领域的使用。
4.聚硅氮烷树脂是一种以si、n、o、c、h等元素组成的树脂,具有高硬度、高耐温、疏水疏油等优异的物理化学性能。现有技术已经对聚硅氮烷/环氧树脂涂料进行了一些研究。比如cn113402974a公开的涂料组合物,包括甲基聚硅氧烷树脂、聚硅氮烷、改性硅油、含氟表面活性剂和溶剂;cn113444446a公开了一种耐腐蚀涂料,包括甲基聚硅氧烷树脂、全氢聚硅氮烷、改性硅油、硅烷偶联剂、氟硅烷和溶剂;其都是通过加入含氟的试剂来降低涂层的表面能,完成涂料的疏水改性,但是其抗盐雾性能和耐高温性能都不佳;cn111961412a公开了一种聚硅氮烷改性环氧防腐涂料,包括聚硅氮烷改性环氧树脂、催化剂、填料和溶剂,其利用si-n键合环氧的开环反应,制得一种主链含有si-o-c、si-n-c的预聚物,含有双键、活泼氢等活性基团,加热条件下发生反应,交联密度增大,提高了耐温性。当水进入涂层,会优先和si-n键水解,缓解腐蚀接枝渗透到基材的速度,达到防腐目的。
5.但是还存在一些问题:1.聚硅氮烷在固化后会形成陶瓷或者类陶瓷质的涂膜,所以会导致聚硅氮烷涂层的膜厚较薄,一般只有3-7μm;2.聚硅氮烷树脂在国内的起步较晚,其量产化的企业较少,主体基本依靠进口,所以价格较贵,目前进口价格在2000元/公斤以上,国内一些公司价格在1500-3000元/公斤;3.聚硅氮烷一般粘度较低,市面上常见的聚硅氮烷树脂的粘度基本与水相近,导致聚硅氮烷树脂抗毛细现象弱,在一些墙面、管道等施工时耗费较大,刷涂、辊涂施工困难等;4.目前聚硅氮烷的大部分实际使用工程在国外,国内除高校外只有少部分企业在使用和研发聚硅氮烷;5.早期聚硅氮烷作为技术封锁,虽然目前一些种类的聚硅氮烷处于开放的状态,但是还有一些种类的聚硅氮烷处于封锁状态,因此聚硅氮烷在国内的发展和使用等受到了一定的限制。
6.随着近几年,越来越多的学者、专家以及工程师将目光投到聚硅氮烷树脂上,国内
聚硅氮烷树脂的性能已经逐渐向国外产品靠近,我司生产的的聚硼硅氮烷是硅氮烷树脂的一种衍生产品,具有比聚硅氮烷更好的耐高温性(陶瓷化后耐1700℃)、厚涂性(膜厚10-15μm)、高硬度(常温固化7-8h,陶瓷化>10h),且价格也具有很大的优势。因此,如何利用聚硼硅氮烷和环氧树脂结合,制备出一种能够在高温条件下抗腐蚀的涂层,已经成为一个急需解决的问题。
技术实现要素:
7.为了解决现有技术中高温耐腐蚀涂料存在的一些缺陷,本发明先将微纳米结构的耐高温粉体与环氧树脂通过研磨设备研磨成稳定存放的浆料,然后利用聚硼硅氮烷、环氧树脂、硅烷偶联剂和含纳米粉体的环氧色浆交联固化形成一层耐高温的涂层。由于涂料中添加了具有耐高温的纳米粉体,从而在一定程度上使涂层更加致密,在面对各种腐蚀时,能够有效地阻隔腐蚀物对涂层的渗透。同时,涂料中环氧树脂的高粘性使得整个涂层体系能够很好的在墙体、腐蚀后的管道、水泥等毛细现象严重的基材上施工。另外,环氧树脂的使用也保证了整个涂层体系的膜厚,从而避免了聚硅氮烷的抗毛细现象弱、涂膜厚度薄、粉体承载效果差等缺陷。另一方面,通过引入聚硼硅氮烷,极大程度上提高了环氧树脂体系的耐温性能,同时,与环氧树脂复配又降低了聚硼硅氮烷树脂的使用量,使得整个涂料不仅具有聚硼硅氮烷树脂的种种优点,而且价格又获得了很大程度的降低,从而使该涂料体系具有很好的商业价值。
8.一种聚硼硅氮烷/环氧复合耐高温抗腐蚀涂料,包括以下质量份的原料:15-25份聚硼硅氮烷预聚体,10-20份环氧树脂,3-5份环氧树脂浆料,1-5份硅烷偶联剂,45-73份溶剂,所述环氧树脂浆料包括以下质量份的原料:20-40份环氧树脂,10-20份耐高温纳米粉体,1-5份分散剂,35-65份溶剂;所述聚硼硅氮烷预聚体是由包括以下单体聚合得到:二烃基二氯硅烷、含有烯基的二氯硅烷、硅氮烷以及氯化硼。
9.进一步地,所述环氧树脂的环氧当量为180-230g/eq,环氧树脂选自双酚型环氧树脂,比如双酚a、双酚af、双酚s、双酚f等,优选为双酚a型环氧树脂,比如e-35、e38,e-44、e-51中的至少一种。
10.进一步地,所述硅烷偶联剂选自带有环氧基硅烷偶联剂、带有氨基硅烷偶联剂、带有双键的硅烷偶联剂中的至少一种;所述带有环氧基硅烷偶联剂选自3-缩水甘油醚氧基丙基三甲氧基硅烷、3-(2,3-环氧丙氧)丙基三乙氧基硅烷、3-(2,3-环氧丙氧)丙基甲基二甲氧基硅烷中的至少一种;所述带有氨基的硅烷偶联剂选自γ-氨丙基三甲氧基硅烷、γ-氨丙基三乙氧基硅烷、γ-二乙烯三胺丙基甲基二甲氧基硅烷、n-2-氨乙基-3-氨丙基三甲氧基硅烷中的至少一种;所述带有双键的硅烷偶联剂选自乙烯基三甲氧基硅烷、乙烯基三乙氧基硅烷、乙烯基三(β-甲氧基乙氧基)硅烷中的至少一种。
11.优选地,所述硅烷偶联剂为带有环氧基硅烷偶联剂、带有氨基硅烷偶联剂、带有双键的硅烷偶联剂按照质量比4-6:1-2:1-2的混合硅烷偶联剂,并且硅烷偶联剂用量为2.5-3.5份。发明人发现,按照上述比例复配的偶联剂制备得到的涂料综合性能最优。其中,环氧基可以和硅氮烷中的硅氮键反应,增加交联密度的同时增加涂层与基材的附着力或者与纳米粒子之间的粘接性;双键的加入可以在高温下与硅硼氮烷中的双键进一步交联,增加涂层的交联密度,提高涂层的强度,也可以增加附着力和粘接性;氨基可以加快聚硅氮烷的固
化速率,增加涂层的交联密度和力学性能。
12.所述耐高温纳米粉体的粒径为10-400nm,优选50-200nm;具体选自纳米氮化硅、纳米碳化硼、纳米氧化铝、纳米氮化铝、纳米氮化硼、纳米碳化硅、纳米氧化镁、纳米氧化锌、纳米二氧化钛中的至少一种。
13.进一步地,所述聚硼硅氮烷预聚体是由包括以下质量份单体聚合得到:10-15份二烃基二氯硅烷、8-13份含有烯基的二氯硅烷、30-40份硅氮烷以及10-15份氯化硼。
14.进一步地,所述二烃基二氯硅烷选自二甲基二氯硅烷、二乙基二氯硅烷、二丙基二氯硅烷、二苯基二氯硅烷、甲基乙基二氯硅烷中的至少一种;所述含有烯基的二氯硅烷选自甲基乙烯基二氯硅烷、甲基丙烯基二氯硅烷、乙基乙烯基二氯硅烷中的至少一种;所述硅氮烷选自六甲基二硅氮烷、四甲基二乙烯基二硅氮烷、六甲基环三硅氮烷、八甲基环四硅氮烷中的至少一种。
15.所述溶剂和分散剂没有特别的限定,本领域常用即可。比如所述溶剂选自丙二醇甲醚醋酸酯、乙酸正丁酯、乙酸戊酯、甲基异丁基酮、甲基戊基酮中的至少一种;所述分散剂为聚氨酯类油性分散剂,比如silok7423、silok7007、silok7096、silok7421中的至少一种。
16.本发明是先将微纳米结构的耐高温粉体与环氧树脂通过研磨设备研磨成稳定存放的浆料,然后利用聚硼硅氮烷预聚体、环氧树脂、硅烷偶联剂和含纳米粉体的环氧浆料配置为耐高温防腐涂料。该耐高温防腐涂料可选择喷涂、辊涂、刷涂等多种涂覆方式,并且可以在金属、木材、混凝土、玻璃、塑料、陶瓷等多种基材上涂覆。均匀涂覆后在80-130℃条件下固化10-30min,之后养护3-5天即可得到高品质的耐高温防腐涂层。本发明所得涂层具有优异的耐高温性,能够在350℃下不会出现皲裂、脱落等不良现象;具有优异的防腐性能和耐盐雾性,能够有效抗中性盐雾500-600h,不会出现锈迹。
17.对于聚硅硼氮烷的反应得到的化学结构,其反应机理复杂,发生了多种反应,目前还没有统一的定论。有现有技术报道其反应机理如下:
[0018][0019]
还有现有技术认为所得结构主链上有一个-(b-n)
3-的六元环结构存在。产物结构如下:
[0020][0021]
但是申请人认为其还包括如下结构:
[0022][0023]
其中,r1和r2相同或不同,r1和r2中至少有一个是活性基团-ch=ch2,另一个为-h、c
1-c4烷基、-ch=ch2、-c6h5或-nh2中的一种,n是3~3000之间的整数。波浪线代表与上述所画出结构相似的结构,即硅硼氮烷中含氮部分nh与硼元素b之间的键合。由于硼元素的稳定化合价一般为 3价,具有3个反应活性位点,易于与体系中同样活泼的nh基团反应形成交联的三维网络结构。
[0024]
本发明第二个目的是提供上述聚硼硅氮烷/环氧复合耐高温抗腐蚀涂料的制备方法,包括以下步骤:
[0025]
(s1)聚硼硅氮烷预聚体的制备:将单体二烃基二氯硅烷、含有烯基的二氯硅烷、以及氯化硼正己烷溶液按照配比投料,降温至0-5℃,逐渐加入硅氮烷,恢复至室温,继续搅拌5-10h,反应结束后,升温至200-240℃,除去副产物三甲基氯硅烷、正己烷溶剂以及未参与反应的单体,真空干燥,得到聚硼硅氮烷预聚体;
[0026]
(s2)环氧树脂浆料的制备:将环氧树脂,耐高温纳米粉体,分散剂,溶剂混合均匀,进行研磨,研磨至细度<10μm,得到环氧树脂浆料;
[0027]
(s3)耐高温抗腐蚀涂料的制备:将步骤(s1)所得聚硼硅氮烷预聚体,步骤(s2)所得环氧树脂浆料,环氧树脂,硅烷偶联剂,溶剂搅拌均匀即得所述耐高温抗腐蚀涂料。
[0028]
本发明的耐高温抗腐蚀涂料施用方式简单,在洁净的基材表面,均匀涂覆上述耐高温抗腐蚀涂料,控制湿涂层厚度在30-50μm,在80-130℃条件下固化10
ꢀ‑
30min,之后养护3-5天即可得到高品质的耐高温防腐涂层。所述均匀涂覆的方式没有特别的限定,只要能够达到是涂料以规定厚度均匀覆盖在基材表面即可,包括但不限于喷涂、辊涂、刷涂。
[0029]
相对于现有技术,本发明取得了以下有益效果:
[0030]
一、本发明的耐高温防腐涂料的成膜物质采用聚硼硅氮烷树脂和硅烷偶联剂固化环氧树脂,利用极性si-n键和环氧基团发生开环反应,从而固化形成一种含有si-o-c、si-n-c结构的稳定涂层。同时聚硼硅氮烷树脂侧链含有活泼性的乙烯基等基团,这些活泼性的基团在加热或催化剂的作用下可进一步发生加成反应,使得涂层交联密度明显增大,从而为固化后的涂层提供了高的阻隔屏蔽性。其次,n-b键的引入增加了涂层的耐温性,在设计
一种室温或中低温固化的防腐涂层配方时,环氧树脂的种类和分子量的选择可以不受温度的限制,使得选择更加灵活多变。因此,基于该复合树脂的涂层具有防腐性能优异、涂膜厚度易于调节、基材适用性强等特点,为高温防腐涂层的制备提供了新的材料选择和思路。
[0031]
二、本发明能够扩展环氧树脂抗腐蚀涂料的应用范围,尤其在耐高温抗腐蚀涂层方面,其生产制备工艺简单,可适用于多种不同的基底和规模化生产,热稳定性和化学稳定性好,能够很好地改善环氧树脂的耐候性能,涂层的耐温性有助于实现涂层在基材内部涂覆,从而大大延长了基材的使用寿命。同时,该涂料的施工工艺简单、质量可控。涂覆前,无需对基材进行特殊化学处理、等离子处理、火焰或热处理等。另外,以乙酸丁酯为溶剂更加节能环保,适合商业化推广,涂层厚度调节范围宽、适用面广、附着力好、防腐性能优异,可作为一种浸涂液从工艺和性能等方面完全替代热镀锌,未来在石油运输管道、供暖管道、炼钢炉或高温炉的烟囱内壁等均具有重要的潜在应用价值。
[0032]
三、本发明提供的耐高温抗腐蚀涂料是利用环氧树脂的高粘度增强涂料的抗毛细现象,同时也利用环氧树脂的高机械性能、强粘贴性能,使制备出的涂料能够很好地适用于墙面、水泥面、粗陶面等吸油量大的基材;而添加硅烷偶联剂和聚硼硅氮烷树脂能够提高涂层的硬度、耐磨性、耐高温性能,同时硅烷偶联剂与环氧树脂在固化后能够很好地交联使涂层更加致密,从而能够使涂层具有更好的抗腐蚀性能;在涂料中添加耐高温色浆能够提升整体涂层的硬度、以及耐温性能,使得涂层在面对高温颗粒物冲击、高速腐蚀流体时能够保证涂层的完整度,同时这些微纳米粉体也能够在微观结构中,填充树脂间隙,从而进一步加强了涂层的抗腐蚀性能。
附图说明
[0033]
图1是普通环氧涂层和实施例1所得涂层在400℃高温烘烤10h的照片;
[0034]
图2分别是普通环氧涂层和实施例1所得涂层经过260℃高温烘烤10h后经过560h耐盐雾试验后的图片。
具体实施方式
[0035]
下面通过实施例对本技术进行进一步的阐述。
[0036]
本发明所用试剂均可采购自常规商业途径。
[0037]
本发明实施例中所述“份”,若无特别说明,均为质量份,所述“%”,若无特别说明,均为质量百分比。
[0038]
实施例1
[0039]
(s1)制备聚硼硅氮烷预聚物
[0040]
称取12.5份甲基二氯硅烷、11.3份甲基乙烯基二氯硅烷、11.7份氯化硼(1m的正己烷溶液)混合均匀,并降温至0℃,搅拌的条件下,逐滴向上述溶液中滴入36.8份六甲基二硅氮烷,滴加完毕后将温度恢复至室温,继续搅拌6h,然后逐渐升温至200℃去除副产物三甲基氯硅烷、正己烷溶剂以及未参与反应的单体,最后在120℃的真空中干燥1h,获得聚硼硅氮烷预聚体;
[0041]
(s2)制备环氧浆料
[0042]
称取30份环氧树脂e44,15份氮化硅纳米粉体(平均粒径为200nm),3份分散剂
silok7423以及62份丙二醇甲醚醋酸酯置于研磨罐中,添加研磨锆珠,将研磨罐密封后开启高速研磨机,在2500rpm转速下研磨1h,细度<10μm时,用不锈钢滤网过滤除掉锆珠,得到环氧浆料;
[0043]
(s3)制备耐高温抗腐蚀涂料
[0044]
称取20份环氧树脂e44、20份步骤(s1)制得的聚硼硅氮烷、3.5份步骤(s2)制得的耐高温环氧浆料、2.5份硅烷偶联剂(kh560、kh-550和a171按照质量比4:1:1的复配硅烷偶联剂),加入到45份丙二醇甲醚醋酸酯中,用高速搅拌机搅拌30min,待所有成分均混合完成以后即得到耐高温抗腐蚀涂料。
[0045]
图1和图2分别是普通环氧涂层和实施例所得涂层在400℃高温烘烤10h,以及经过260℃高温烘烤10h后经过耐盐雾试验的图片。可以看出,本发明防腐涂层经过400℃高温烘烤后,没有明显的脱落,变色现象;经过260℃烘烤10h后,还能保持很好的耐盐雾性能。
[0046]
实施例2
[0047]
其他条件和操作与实施例1相同,区别在于步骤(s1)的聚硼硅氮烷预聚物制备过程中,单体用量改为10份甲基二氯硅烷、13份甲基乙烯基二氯硅烷、15份氯化硼,30份六甲基二硅氮烷。
[0048]
实施例3
[0049]
其他条件和操作与实施例1相同,区别在于步骤(s1)的聚硼硅氮烷预聚物制备过程中,单体用量改为10份甲基二氯硅烷、15份甲基乙烯基二氯硅烷、10份氯化硼,40份六甲基二硅氮烷。
[0050]
实施例4
[0051]
其他条件和操作与实施例1相同,区别在于步骤(s3)中,硅烷偶联剂为3.5份kh561、kh-540和a151按照质量比6:1:2的复配硅烷偶联剂。
[0052]
实施例5
[0053]
其他条件和操作与实施例1相同,区别在于步骤(s3)中,硅烷偶联剂为kh560和kh-550按照质量比4:1的复配硅烷偶联剂。
[0054]
实施例6
[0055]
其他条件和操作与实施例1相同,区别在于步骤(s3)中,硅烷偶联剂为kh560和a171按照质量比4:1的复配硅烷偶联剂。
[0056]
实施例7
[0057]
其他条件和操作与实施例1相同,区别在于步骤(s3)中,硅烷偶联剂为kh-550和a171按照质量比1:1的复配硅烷偶联剂。
[0058]
应用例
[0059]
采用75mm*150mm*1.0mm的碳素钢板(符合iso 3574的cr4级冷轧碳素钢)用乙酸丁酯进行擦拭,将其表面的油污、灰尘、颗粒物等清洗干净,然后再用乙醇进行擦洗,清理干净的基材放进50-60℃的烘箱中进行烘烤干燥待用;取适量的耐高温抗腐蚀涂料置于空气喷枪的料斗中,取出钢板基材,将钢板基材放置于适当位置对其进行喷涂,控制喷涂湿膜厚度在30μm左右,表干后将喷涂好的钢板放于100℃的烘箱中烘烤10min,取出后养护3d,即可得到耐高温抗腐蚀涂层,测试涂层附着力为0级(测试方法gb/t9286百格法)。
[0060]
对上述实施例和对比例的涂料按照上述方法,得到涂层后,进行以下性能测试:
[0061]
1)耐盐雾试验:将表面经聚硼硅氮烷/环氧复合涂层涂敷的样板和仅经环氧树脂涂敷的基材样板置于中性盐雾试验箱中进行耐盐雾性能测试。盐雾试验按照gb/t10125-2021中的相关要求进行,盐雾测试采用中性盐雾,盐水采用5%的nacl溶液ph值在7左右。盐雾试验中采用24h观察一次的频率观察样板的腐蚀情况,待发现有起泡、粉化、或者划伤处腐蚀超2mm时即可以终止试验,取出样板。
[0062]
2)耐高温实验:将表面经聚硼硅氮烷/环氧复合涂层涂敷的样板和仅经环氧树脂涂敷的基材样板置于马弗炉中,以5℃/min的升温速度将炉内温度上升为400℃,保持400℃连续烘烤10h,然后取出样板观察涂层外观变化。结果如下表1所示。
[0063]
表1涂层性能测试
[0064][0065]
通过上述表1的数据可以看出,本发明提供的涂料具有优异的耐高温,抗腐蚀能力。常规涂料在高温条件下,涂层出现氧化、脱落等缺陷,防腐蚀性会极大下降,限制了涂料的某些领域的应用。本发明利用了聚硼硅氮烷预聚体复配环氧树脂,在耐高温纳米粉体及硅烷偶联剂的相互配合作用下,制备得到了综合性能优异的耐高温防腐涂料。
[0066]
目前市面上盐雾试验以及耐盐雾性能较长的产品,基本是针对常温环境。而目前在200-400℃的环境下的耐腐蚀性能的产品其防腐性能则会大大降低。针对该温度区间的产品大多需要进行100-200℃的高温固化,这就限制了某些领域的使用。所以针对本产品既能在400℃下进行烘烤10h无变色又能耐盐雾,且固化方式灵活多样,在耐高温防腐领域具有优势。
再多了解一些
本文用于创业者技术爱好者查询,仅供学习研究,如用于商业用途,请联系技术所有人。