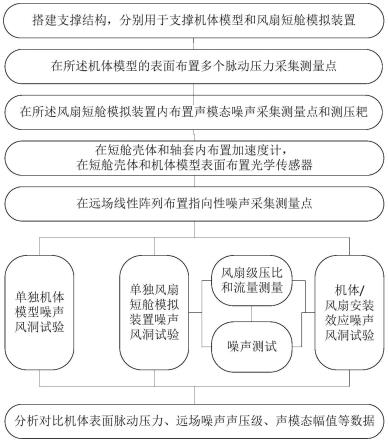
1.本发明属于噪声测量技术领域,涉及一种机体/风扇安装效应噪声风洞试验方法。
背景技术:
2.机体安装效应噪声是指机体与发动机相互干扰而产生的噪声。安装效应噪声为涉及空气动力学、声学多学科交叉的复杂问题,其降噪及验证技术涉及风扇旋转部件、机体等相互作用的特种风洞试验技术。准确认识机体/风扇安装效应导致的气动特性和声学特性,是开展机体与发动机一体化布局的设计基础。风洞试验是研究机体/风扇安装效应噪声问题的重要手段。由于涡扇飞机气动噪声受机体与发动机干涉影响显著,需建立一种机体/风扇安装效应噪声风洞试验方法。
技术实现要素:
3.本发明的目的是提供一种机体/风扇安装效应噪声风洞试验方法,可实现对机体表面、短舱内部以及远场的气动及声学特性测试,用以更全面和精确的反映机体/风扇安装效应噪声特性,为机体/发动机气动布局设计和降噪方案提供验证和修正。
4.本发明所采用的技术方案如下:一种机体/风扇安装效应噪声风洞试验方法,包括如下步骤:
5.步骤1、搭建支撑结构,分别用于支撑机体模型和风扇短舱模拟装置,支撑结构包括四自由度平台和液压支撑系统,机体模型竖直安装在四自由度平台上,液压支撑系统用于支撑并调整风扇短舱模型的迎角变化,风扇短舱模拟装置中的风扇的转动通过液压支撑前端电机和其连接的传动轴实现;
6.步骤2、在所述机体模型的表面布置多个脉动压力采集测量点;
7.步骤3、在所述风扇短舱模拟装置的唇口附近涵道壁面布置声模态噪声采集测量点,用于测量风扇前传声模态,在风扇前和导叶后布置测压耙,用于测量标定风扇级增压比和流量;
8.步骤4、在短舱壳体和传动轴套内布置加速度计,用于检测风扇短舱模拟装置振动量,在风扇短舱模拟装置的短舱壳体和机体模型表面布置光学传感器,用于检测机体模型和风扇短舱模拟装置相对距离;
9.步骤5、在远场线性阵列布置多个远场指向性噪声采集测量点;
10.步骤6、确定单独机体模型噪声风洞试验的输入工况条件,包括,来流风速、机体模型迎角;在输入工况条件下进行风洞试验,测量远场线性阵列、机体表面脉动压力;
11.步骤7、确定单独风扇短舱模拟装置噪声风洞试验的输入工况条件,包括,来流风速、风扇转速、风扇短舱模拟装置迎角;在输入工况条件下进行风洞试验,测量风扇级增压比、流量、远场线性阵列、风扇前传声模态;
12.步骤8、确定机体/风扇安装效应噪声风洞试验的输入工况条件,包括:来流风速,风扇转速、机体模型迎角、机体模型和风扇短舱模拟装置相对距离;在输入工况条件下进行
风洞试验,测量机体表面脉动压力、风扇级增压比、流量、远场线性阵列、风扇前传声模态;
13.步骤9、根据测压耙数据计算风扇级增压比和流量,标定及校准风扇短舱模拟装置气动状态参数;根据机体模型表面脉动压力测量点时域数据计算机体表面的脉动压力;根据涵道壁面声模态测量点时域数据计算风扇前传声模态阶次;根据远场线性阵列采集点时域数据计算远场噪声声压级及指向性特点;
14.步骤10、分别对比机体/风扇安装效应噪声风洞试验数据与单独机体模型噪声风洞试验数据、单独风扇短舱模拟装置噪声风洞试验数据,对比内容包括:机体表面脉动压力、远场噪声声压级。
15.进一步的,步骤2中,所述脉动压力采集测量点布置,以风扇短舱模拟装置尾喷口直径的1.5倍作为尾喷流影响区域参考范围,分别在缝翼、主翼、襟翼下翼面布置脉动压力采集测量点。
16.进一步的,步骤3中,在包含风扇短舱模拟装置的噪声风洞试验前均需测量风扇级前后增压比和流量,声模态采集点沿周向等间距布置,布置截面在声衬安装区前,测压耙分为两组,包括:分别在风扇前和导叶后选取静压测点,每组沿周向等间距迎风布置4个测点;在距离风扇前一倍直径位置布置流量测压点,如短舱长度不满足一倍直径条件,则利用数值模拟方法得出涵道内中心区的压力稳定区域布置流量测压点;附面层范围内布置至少3个测压点,流动中心区布置1个测压点,利用文丘里管原理计算出涵道内流量。
17.进一步的,步骤5中,远场线性阵列测量间隔度数为5
°
,阵列能够沿轴向移动。
18.本发明的优点及有益效果:本发明提供了一种机体/风扇安装效应噪声风洞试验方法,通过在缩比机体与风扇短舱模拟装置模型表面布置脉动压力传感器和传声器,实现机体与发动机风扇安装效应气动噪声特性测试,为飞机安装效应噪声测量提供了可靠的方法,并为飞机气动噪声数值仿真和降噪方案提供验证和修正。同时,通过合理布置远场测试点,可以实现远场噪声指向性测试。经过不同种试验状态工况对比,可以更为全面地评估机体/风扇安装效应噪声受风扇转速、来流风速、相对位置距离等参数的影响,用于机体/发动机一体化降噪设计的指导。
附图说明
19.图1是机体/风扇安装效应噪声风洞试验方法流程图。
20.图2是机体/风扇安装效应噪声风洞试验设备示意图。
21.图3是风扇短舱模拟装置示意图。
22.图4是机体模型与风扇短舱模拟装置示意图。
23.图5是远场线性阵列位置关系示意图。
24.其中,1-声模态采集点,2-测压耙,3-短舱壳体,4-传动轴套,5-风扇,6-导叶,7-传动轴,8-风扇短舱模拟装置,9-机体模型,10-风洞收集器,11-机体模型,12-风洞喷口,13-液压支撑系统,14-四自由度平台。
具体实施方式
25.下面将结合附图举例,对本发明的技术方案进行更加详细的描述。
26.实施例1
27.如图1所示,一种机体/风扇安装效应噪声风洞试验方法,步骤如下:
28.步骤1、如图2所示,搭建支撑结构,分别用于支撑机体模型和风扇短舱模拟装置,支撑结构包括四自由度平台和液压支撑系统,机体模型竖直安装在四自由度平台上,四自由度平台结构包括:滚珠丝杠、直线单元和转盘,机体模型自由度通过滚珠丝杠、直线单元、转盘共同调节实现变化,液压支撑系统用于支撑并调整风扇短舱模型的迎角变化,液压支撑结构包括拐臂结构、升降立柱、升降导轨、随动线缆以及井道,风扇短舱模拟装置中的风扇的转动通过液压支撑前端电机和其连接的传动轴实现,风扇短舱模拟装置迎角变化通过拐臂结构实现;
29.步骤2,在所述机体模型的表面布置多个脉动压力采集测量点,以风扇短舱模拟装置尾喷口直径的1.5倍作为尾喷流影响区域参考范围,分别在缝翼、主翼、襟翼下翼面布置脉动压力采集测量点,如图4所示;
30.步骤3,如图3所示,在所述风扇短舱模拟装置唇口附近涵道壁面布置声模态噪声采集测量点,用于测量风扇前传声模态。在风扇前和导叶后布置测压耙,用于测量标定风扇级增压比和流量,试验前均需测量风扇级前后增压比和流量,声模态采集点沿周向等间距布置,布置截面在声衬安装区前,测压耙分为两组,包括:分别在风扇前和导叶后选取静压测点,每组沿周向等间距迎风布置4个测点;在距离风扇前一倍直径位置布置流量测压点,如短舱长度不满足一倍直径条件,则利用数值模拟方法得出涵道内中心区的压力稳定区域布置流量测压点;附面层范围内布置至少3个测压点,流动中心区布置1个测压点,利用文丘里管原理计算出涵道内流量;
31.步骤4,在短舱壳体和传动轴套内布置加速度计,用于检测风扇模拟装置振动量。在短舱壳体和机体模型表面布置光学传感器,用于检测机体模型和风扇短舱模拟装置相对距离;当传动轴套内加速度计振动量超标或者短舱与机体相对距离超标,需紧急停车;
32.步骤5,如图5所示,在远场线性阵列布置多个远场指向性噪声采集测量点,远场线性阵列测量周向指向性范围为50
°
~115
°
,间隔度数为5
°
,阵列可沿轴向移动;
33.步骤6,确定单独机体模型噪声风洞试验的输入工况条件,包括,来流风速、机体模型迎角,在输入工况条件下进行风洞试验,测量远场线性阵列、机体表面脉动压力;
34.步骤7,确定单独风扇短舱模拟装置噪声风洞试验的输入工况条件,包括,来流风速、风扇转速、风扇短舱模拟装置迎角。在输入工况条件下进行风洞试验,测量风扇级增压比、流量、远场线性阵列、风扇前传声模态;
35.步骤8,确定机体/风扇安装效应噪声风洞试验的输入工况条件,包括:来流风速,风扇转速、机体模型迎角、机体模型和风扇短舱模拟装置相对距离。在输入工况条件下进行风洞试验,测量机体表面脉动压力、风扇级增压比、流量、远场线性阵列、风扇前传声模态;
36.步骤9,根据测压耙数据计算风扇级增压比和流量,标定及校准风扇短舱模拟装置气动状态参数;根据机体模型表面脉动压力测量点时域数据计算机体表面的脉动压力;根据涵道壁面声模态测量点时域数据计算风扇前传声模态阶次;根据远场线性阵列采集点时域数据计算远场噪声声压级及指向性特点;
37.步骤10,分别对比机体/风扇安装效应噪声风洞试验数据与单独机体模型噪声风洞试验数据、单独风扇短舱模拟装置噪声风洞试验数据,对比内容包括:机体表面脉动压力、远场噪声声压级。
38.实施例2
39.试验前,进行风扇短舱模拟装置地面调试,包括风扇动平衡测试、电机传动测试。此外,还对试验支撑设备表面进行表面消声处理,以减小声反射影响。采用校准器对所述声学测量设备进行校准。试验时,将风扇短舱模拟装置中心正对风洞喷口中心,并调整机体模型支撑相应高度。模型安装到位后,检查模型安装情况,检查试验装置运转情况,确保模型安装准确,试验装置能正常运转后。确定试验设备和模型状态后,可开展声学试验,风洞风速和风扇转速由低逐渐增大,确定安全后,按试验内容进行正式的试验,采用pxi总线数据采集系统采集数据,处理并输出结果,完成所有的试验点,机体/风扇安装效应噪声风洞试验具体包括:风扇驱动电机启动,使风扇转速升到某一工作转速;风洞开车,使风速升到固定工作点;采集风扇级增压比和流量,输出并校准测试结果,确定风扇级气动状态;采集噪声及脉动压力测量点,并输出结果;改变风扇转速、风速、机体/风扇相对位置,采集数据,处理输出结果,完成所有试验点;风洞停车。获得机体/风扇安装效应噪声风洞试验数据后,分别与单独机体模型噪声风洞试验数据、单独风扇短舱模拟装置噪声风洞试验数据进行差量对比,得出机体/风扇安装效应气动噪声特点。
40.试验的注意事项包括:1.安全监视:试验过程中,要特别注意监视模型振动特性,达到安全阈值时自动启动保护,同时以声音报警,并实时监视洞外摄像机显示的情况,以确保各系统安全;2.应急措施:在风洞试验的过程中,严格按照正确的启动和停车步骤进行,避免破坏试验模型。
再多了解一些
本文用于创业者技术爱好者查询,仅供学习研究,如用于商业用途,请联系技术所有人。