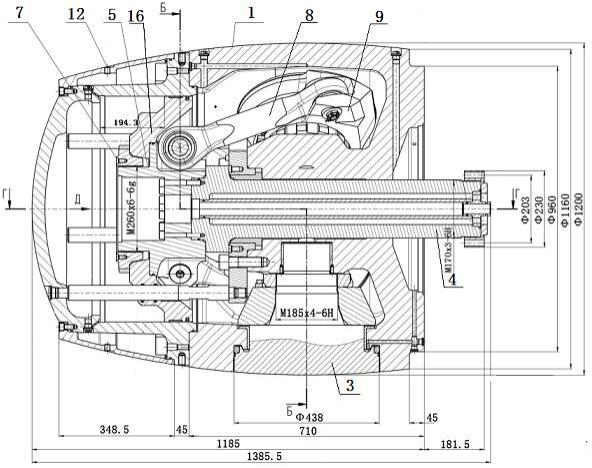
一种cpp变距桨毂组件的精加工方法
技术领域
1.本发明涉及一种cpp变距桨毂组件中各部件间安装区域都采用配作销孔方法来保证加工装配精度,并且能满足锻件和铸件表面质量及超声波探伤应符合rs船级社和《iso484/1-2015 class s》要求的cpp变距桨毂组件的精加工方法。
背景技术:
2.欧洲很多知名的推进器制造商都有着各自成熟的可变距桨及其配套产品,如卡梅瓦、肖特尔、瓦锡兰、man 等都具有多年生产变距桨推进器的开发历史,其产品在船舶行业占有较大的份额。随着海运贸易的蓬勃发展和各国舰船的军事装备竞赛推动下,对于变距桨推进器系统的技术也进行日益完善和多元化发展与应用。
3.瓦锡兰公司制造船舶推进器系统的历史悠久。瓦锡兰推进装置制造厂就已开始向用户提供整套的变距桨推进系统。由于采用了最新科技成果及先进的加工设备,瓦锡兰公司的产品性能优异,其可靠性、经济性及便捷的维护保养性已为用户所津津乐道。
4.man diesel公司生产的cpp变距桨推进器系统已获得多项专利,现在man diesel公司具有成熟的制造阿尔法螺旋桨经验,实用可靠的设计原则已经很好的证明其适应各类船舶,种类包括渡轮、油轮、货柜船、邮轮、近海船、挖泥船和海军舰艇所需的变距调桨操作,它不仅能提供最高速度档自由航行,还要最大限度地发挥拖拽时的动力,机动性好通过alphatronic快速响应控制系统及高功率倒车。现在,阿尔法可调螺距螺旋桨组合处理发动机输出高达30000kw,还配备了轴带发电机。阿尔法螺旋桨主要型号有:vbs860/ 8l27/38主机、vbs1800/ 7s60mc-c主机、vbs1380/ 6l48/60b主机、vbs1680/8s50mc-c等,对于不同的功率、转速和冰级要求,可选用不同尺寸的桨毂,该系列调距桨都具备经济性和操作便捷性的优异表现。
5.卡梅瓦公司在瑞典开始生产了第一套变距桨装置,他的技术全世界首屈一指,目前全球多家公司都引进卡梅瓦的专利进行生产,如日本的三菱公司、美国的伯德-约翰逊公司和我国武汉船用机械有限公司等。现在的卡梅瓦公司已被英国罗尔斯-罗伊斯(roll-royce)公司收购。
6.德国肖特尔公司是世界公认的经典船舶推进系统。可调距推进器(scp)结构简单,设计稳固,维护率低,而且使用寿命长。他一直在开发和制造方位推进器和操纵系统,拥有额定功率值高达30兆瓦的完整推进系统。
7.国内从事变距桨研究的科研机构和人员仍比较少,整体技术实力不强。目前国内外市场绝大多数的结构采用为整体导架滑块结构,导架是由空心轴穿过四方体中心形成整体式导架,四方体的四个角上分别设有一个导槽;空心轴一端与活塞连接,另一端与艉轴的内孔联接;叶片盘根设有一个曲柄销,叶片盘根的曲柄销通过滑块置于的导槽中。通过液压系统控制油压推动活塞把导架的直线往复运动转换成叶片盘根的旋转运动。这种结构的优点是结构简单,便于加工制造,成本低,故障率低。近年来,随着国内外航运业的发展,船舶行业竞争不断加剧,对造船品质及船舶的
航行性能等方面的要求也日益提高,越来越多的船舶装备上了可调距螺旋桨装置。单一的桨毂变距机械装置已无法满足现代化造船业的需求。
技术实现要素:
8.设计目的:设计一种cpp变距桨毂组件,为了改善变距机构的推进功率和稳定性,本研发小组开发了曲柄拉杆式变距桨毂组件的精加工项目,该型桨毂具有稳定的自锁性能,强劲的推进功率,优异的调距性能和较低的故障率。各部件间安装区域都采用配作销孔方法来保证加工装配精度,并且能满足锻件和铸件表面质量及超声波探伤应符合rs船级社和《iso484/1-2015 class s》要求的cpp变距桨毂组件的精加工方法。
9.设计方案:为了实现上述设计目的。cpp变距桨毂组件基于各桨毂零部件都有严格配合要求,在单个零件加工时工艺要求销孔需留有合铰余量,单件加工结束后,配铰顺序为:推杆—驱动架—伺服活塞—横梁—桨毂本体。任何一个零件的加工精度如果没有达到设计要求,都会使装配过程造成困难,甚至产生报废品而影响工程工期。所以cpp变距桨毂内部的每个零部件必须满足设计精度要求,其制造精度的高低将直接影响螺旋桨的水动力特性、推进效率和船体的振动。制定科学合理的生产工艺路线尤为重要。
10.1、驱动架主要的作用是将伺服油缸带来的轴向力均匀的分给五组桨叶曲柄,它的外形结构由多组深槽和轴承孔组成,是相对重要的尺寸位置,这些区域的设计公差小、加工曲面区域深、配合精度高,加工和测量过程中会因环境温度、工件变形、走刀方式、刀具刚性等因素直接影响产品的精度,造成产品报废。必须根据该零件的特点制订科学合理的加工工艺与测量工艺,设计制作可靠的工装夹具保证产品达到图纸技术指标。
11.2、伺服活塞有五组导柱孔,每组孔内设有二个
∅
60h11宽8mm的环形密封槽,粗糙度要求ra2.5,如采用常规传统镶硬质合金t型刀无法满足其加工精度要求,通过查阅刀具供应商产品手册,最终确定使用泰珂洛可拆卸式铣刀头gh130高温合金t型铣刀来满足精加工严苛的技术要求,为生产出高质量的产品提供保障。
12.3、桨叶曲柄是形状最复杂、加工精度要求最高的部件,内孔
∅
225h8为a基准,后续铣床加工的孔位都需要与它为工艺基准来保证位置度和角度,外形轮廓需加工成曲面来满足桨毂内部有限的活动空间,同时还要具备足够的工作强度满足危险截面的安全系数。镗床加工时需解决安装摇杆的轴承孔与桨叶孔轴线有15
°
的偏转角度,这道工序的加工适合于五轴机床自动转动铣头加工完成。但由于多轴机床有着生产成本昂贵、动力铣头刚性差、加工效率不高等诸多弊端。本发明采用普通三轴数控铣床xka7310c
×
30制作工装来完成加工任务。cpp变距桨毂配套的船为双机双桨设计,分为左旋和右旋。单桨毂为五叶桨即每条船有十个桨叶曲柄,因此需要制定便捷的加工工艺路线和稳定可靠的刀具工装来满足小批量化生产的需求。
13.4、本项目生产难点最主要有几个方面:
14.1)桨毂是调距桨的核心部件,它既是推进功率的承载部件,也是调距的最终执行机构,桨毂本体作为承载着内部变距执行元件的主体,与艉轴采用定位销和螺栓连接,加工时需保证定位销孔与艉轴孔位的一致性,两个部件由不同的数控设备适应各自的形状特性来加工,这往往会导致两部件的销孔有一定偏差而影响安装精度。桨叶安装密封区域轴向和径向的粗糙度需要达到ra0.16μm保证桨叶转动时的水密封性,仅依靠机械加工已无法达
到如此高的光洁度要求,同时还要满足设计要求的平面垂直度、同心度、圆跳动来保证桨毂变距工作时的平稳性。
15.2)驱动架在变距的时功能与导架滑块式桨毂的导架相似,起支撑桨叶曲柄和动力传递作用,区别在于导架滑块是导槽滑动副传动,而驱动架则是球面旋转副传动,它连接摇杆的部位由5组均布的深槽和轴承孔组成。槽的位置度高,尺寸公差小(见图4,槽底部较深,零件为了保证部件足够的工作强度,槽底设计成r25圆弧面,因此刀具尺寸被限制为小于
∅
50的铣刀来加工深槽,无法使用大直径铣刀来高效率加工,该零件外形结构复杂、切削加工余量多、槽壁狭窄且精度要求高,采用细长柄径刀具加工会产生振纹和让刀现象,不利于对槽壁的加工精度控制。此外由于需要去除大部分加工余量,会因产生加工应力而导致车床已完成内孔的变形,难以保证最终的尺寸精度。
16.3)技术分析中提到了桨毂内部各执行元件有精密的配合要求,如推杆与驱动架除了通过m20螺栓固定,还需要配铰
∅
30h8销孔来保证安装精度,两个零件装配以后需要加工配铰的
∅
30h8销孔孔壁因两个部件重叠而变的很深,加工有效深度达到了310mm,对需要切削刀具的长径比要达到10:1。对于如此深度的配铰孔加工必然存在着刀具刚性差、切削不均匀、排削困难、不易于观察等诸多难度,最终的孔径质量不可控。
17.4)桨叶曲柄是形状最复杂、加工精度要求较高的部件,内孔
∅
225h8为a基准,后续铣床加工的孔位都需要以它为基准来保证位置度和角度,外形轮廓设计成曲面来适应桨毂内部有限的活动空间,需要借助数控编程软件(cam)来分析、计算及生成程序完成加工。镗铣设备加工需解决安装摇杆的轴承孔与桨叶孔轴线有15
°
的偏转角度,这个偏转角度的加工精度会影响叶片实际变距的精度。这道工序的加工适合于五轴机床自动转动铣头加工完成。但由于多轴机床有着生产成本昂贵、动力铣头刚性差、加工效率不高等诸多弊端。本发明cpp变距桨毂配套的船为双机双桨设计,分为左旋和右旋。单桨毂为五叶桨即每条船有十个桨叶曲柄,因此需要制定便捷的加工工艺路线和稳定可靠的刀具工装来满足小批量化生产的需求。
18.桨毂组件内部有着结构复杂、曲面多、配合精度高等特点。主要组成部件有桨毂本体1、叶片3、推杆4、驱动架5、伺服油缸6、伺服活塞16、摇杆8、桨叶曲柄9和连接螺栓等,如图1所示。基于各桨毂零部件都有严格配合要求,在单个零件加工时工艺要求销孔需留有合铰余量,单件加工结束后,配铰顺序为:推杆—驱动架—伺服活塞—横梁—桨毂本体。任何一个零件的加工精度如果没有达到设计要求,都会使装配过程造成困难,甚至产生报废品而影响工程工期。所以cpp变距桨毂内部的每个零部件必须满足设计精度要求,其制造精度的高低将直接影响螺旋桨的水动力特性、推进效率和船体的振动。图6 cpp变距桨毂组装过程图。
19.本发明与背景技术相比,一是桨毂本体(hub):实现了材质为cu3,工件最大外圆直径φ1200mm,与推杆配合内孔精度为φ215h7,与桨轴安装面端面跳动0.03mm,配合止口尺寸精度φ625h7,该止口相对于内孔a基准跳动为0.04mm,安装桨叶的5处沉孔加工精度为φ185h8、φ430h8,小端面粗糙度要求ra0.8,大端面止口密封区域粗糙度为ra0.16,已达到镜面要求,见图2;二是叶片(blades):实现了材质为cu3,单片叶片高1839mm,重1081kg,采用大侧斜桨叶叶型,叶片根部有m220x4-6g螺纹,密封区域粗糙度ra0.8。桨叶根部与桨毂安装外圆尺寸精度有φ225h8、φ165f8、φ410f8、φ499h9、φ535f9,与a基准跳动0.07mm参数要
求;三是推杆(rod):实现了材质是35#,长度1115mm,重255.2kg,滑动外圆尺寸精度φ215g6,圆柱度0.015,粗糙度ra0.8。轴内部为φ115深孔,船艏端头设计了m210x4-6g螺纹,艉端与驱动架连接销孔φ30h8需要一起配铰来保证安装精度参数要求,见图3;四是驱动架(carrier):实现了材质为40nicrmo6,一端设计有m320x4-6g螺纹,用于固定伺服活塞,外径配合密封尺寸是
∅
480h9,各档内外圆跳动要求为0.05mm,最外侧是摇杆轴承支撑架,设计成五组
∅
70h8的销孔和76h14卡槽来安装摇杆轴承,按矢量方向拉动摇杆,见图4;五是伺服活塞(piston of servomotor):它通过由推杆提供的轴向运动沿着五根导柱支撑平行滑移达到工作目的,与驱动架外侧用
∅
20h8销孔配做定位连接,设计的五组
∅
50h12的导柱孔,位置度要求为
∅
0.07mm,每组导柱孔中有2处
∅
60h11宽8h14的环形槽跳动要求0.07mm。活塞工作面粗糙度ra1.25来保证加装o型圈稳定的动密封;六是摇杆(rocker):材质34crnimo6,零件一端通过球轴承与驱动架装配连接,它的主要作用是将推杆的轴向运动转换为曲柄需要旋转的切线矢量运动。部件的两端轴承孔呈60
°
分布,轴承孔径尺寸
∅
105h7(0~ 0.035)mm,圆柱度0.017mm,粗糙度ra0.8,两组轴承安装孔距尺寸560(0~-0.4)mm;七是桨叶曲柄(crank):材质为42crmo4 qt,它的工作原理是将拉杆和驱动架带动摇杆传递的直线运动转换成旋转运动,与桨叶根部用定位销连接,转动桨叶达到变距的目的。由于受桨毂内部空间的限制,其外形设计成多个曲面和圆弧线条。内孔
∅
225h8与叶片根部配合,6组
∅
40h9销孔定位连接,孔位置度要求
∅
0.07mm。安装摇杆的轴承孔与桨叶安装轴孔线有15
°
的偏转来满足装配需要,轴承孔加工公差
∅
60h7,与孔垂直方向有一处安装槽,槽宽70h14,槽口和外形过渡部分设计由曲面r角过渡来避免应力集中,见图6和图7;八是伺服油缸(housing of servomotor):材质和桨毂相同为cu3,顶部有5个
∅
38h9导柱孔,位置度
∅
0.07mm,主缸壁尺寸
∅
830h7,跳动0.05mm粗糙度ra0.32,工作时与伺服活塞配合。因为要与桨毂本体装配后要浸泡海水中工作,它有设计共有3处径向密封槽,船艏端安装平面跳动0.03mm,粗糙度ra1.25;九是锻件和铸件表面质量及超声波探伤应符合rs船级社和《iso484/1-2015 class s》要求;十是所加工的桨毂具有稳定的自锁性能,强劲的推进功率,优异的调距性能和非常之低的故障率。
附图说明
20.图1是cpp变距桨毂组件总装图。
21.图2是图1中桨毂本体(hub)加工图。
22.图3是图1中推杆(rod)加工图。
23.图4是图1中驱动架(carrier)加工图。
24.图5是桨叶曲柄(crank)加工图。
25.图6是cpp变距桨毂组装过程图。
26.图7是驱动架轴承槽加工示意图。
27.图8是配铰加工示意图。
28.图9是曲柄和桨叶安装示意图。
29.图10是曲柄与工装装配加工图。
30.图11是球刀加工示意图。
31.图12是曲柄加工刀路模拟示意图。
32.图13是切削参数和刀具类型表。
33.图14是曲柄三坐标检测合格报告。
34.图15是工装治具板示意图。
35.图16是桨毂本体加工模板工装主视图。
36.图17是图5中a-a部剖视示意图。
37.图18是图17中f部的放大示意图。
38.图19是表。
具体实施方式
39.参照说明书附图1
‑‑‑
18,对本发明实现方法作如下说明:
40.1)桨毂本体加工工装的设计,保证了桨毂与艉轴法兰孔的安装精度。
41.制作模板工装是为了保证桨毂本体与艉轴配合销孔的精准定位,确保零件装配后桨毂回转中心跳动精度达到设计要求,降低桨毂工作时的旋转惯量和振幅;
42.使用方法:
43.①
桨毂本体的配合φ75销孔预加工成φ73;
44.②
工装φ625凸止口安装在桨毂凹止口,配合间隙为0.01~0.05保证同轴度,工装贴合面平面用0.02塞尺检查是否贴实;
45.③
将桨毂本体和工装模板一起装夹在加工设备上,制作2个6160铝材质台阶工艺销进行粗定位,确保待加工孔位与工作模板孔位圆心重合;
46.④
用钟式百分表对模板的φ76基准孔进行圈圆找中,找正误差控制在0.005以内;
47.⑤
以模板销孔实际坐标精镗桨毂本体,尺寸控制在φ75h7,粗糙度控制在ra1.25以内;
48.桨毂与艉轴采用6个
∅
75h7销孔定位连接,桨毂本体和艉轴法兰装配的孔位置度需保持良好的一致性,为保证定位精度设计出一款实用简便的定位治具工装。
49.制作模板工装是为了保证桨毂本体与艉轴配合销孔的精准定位,确保零件装配后桨毂回转中心跳动精度达到设计要求,降低桨毂工作时的旋转惯量和振幅;
50.使用方法如下:
51.设计原理是将图纸的名义尺寸制作精度较高的孔位模板,并利用凹凸止口定位,工装贴合面平面度<0.015mm,端面跳动<0.03mm,6
‑∅
75孔径设计成
∅
76(0~ 0.02)mm以方便圈表校正和防止切削运动时干涉刀具刀尖。制作3付台阶销,两件用于定位模板限制其自由度,另一件作为检验塞规,检查零件孔位与模板孔位的位置度是否合格。
52.2)驱动架加工工艺、cnc刀具路径的创新,使零件加工工艺更为科学合理,刀具路径得到优化后切削工况稳定,产品的加工表面质量良好,避免了因刀具柄细长产生振纹和让刀现象。
53.a)零件常规的加工工艺路线为:粗车
→
半精车
→
精车
→
粗铣
→
精铣;按此路线加工会存在因五组深槽铣削量较大产生的加工应力和加工热量而导致已精车尺寸发生变形超差,为了避免质量风险,采用新的工艺路线为:粗车
→
半精车
→
粗铣
→
时效
→
精车
→
精铣;目的是在精车前去除大量的余料,显著降低铣削产生的加工应力对工件的形位公差和尺寸产生影响。
54.b)在切削刀具路径的规划中需要充分考虑切削过程的稳定性,避免切削力突然增大,为了保证切出铁削最薄,应保持刀具处在加工过程待切削表面为不对称顺铣。具体刀具路径规划如下:
55.①
选用d63r8和d40防震铣刀采用不对称顺铣粗加工留量0.1mm;
56.②
精铣时避免切削圆角处刀具与材料大面积接触而产生加工振动;
57.③
加工深槽和形腔时,采用螺旋铣削的方式,保证切削过程中的载荷稳定;
58.④
遵循切出最薄切削原则,开放区域采用圆弧进到和退刀方式;
59.⑤
刀具中心路径在工件被加工切宽范围 ae》dc的75%,切入时的初始冲击沿着切削刃逐渐上移,远离敏感的刀尖;
60.3)桨毂各组件配铰加工的创新,优化了配铰前安装工艺,通过增加2个定位销定位和切削刀具的参数制定解决了刀具刚性差、切削不均匀、排屑困难、不易于观察等诸多困难,有效把控配铰孔品质。
61.推杆与驱动架装配具有严格的位置度要求,单个部件加工结束后需要装配配铰连接销孔。配铰前八组
∅
30h8底孔加工留余量单边1mm,由于装配时螺栓与螺孔存在一定的间隙值,单靠螺栓预紧后不能使待加工底孔壁完全重合,会存在一定的偏差,造成的偏差因扩孔钻和铰刀都没有定心功能,切削时刀具会往余量少的一侧让刀而导致配铰加工后的销孔质量不良或超差。鉴于存在加工的风险,技术小组一起分析了配铰工艺思路,需要解决零件底孔安装不重合问题和切削刀具刚性问题。通过制作二个
∅
29mm尼龙定位销来定位两个工件的孔位,使得待加工孔壁较好的重合后再收紧把合螺栓。使用模式锥柄扩孔钻扩孔至
∅
29.7~
∅
29.8,最后用
∅
30镶合金铰刀转速60rpm走刀5mm/min精铰到设计尺寸要求。按照此方法加工出来的配铰孔质量稳定,位置精度能得到有效保障。
62.4)设计曲柄工装治具结构示意图见图12和加工程序的创新,用普通三轴数控设备代替了昂贵的五轴机床加工,降低生产成本。借助数控编程软件(cam)选择刀具参数来分析、优化、计算及生成程序,使生产效率显著提升。
63.曲柄在桨毂中的作用是将直线运动转换成旋转运动带动叶片执行变距(图11,其主要的连接部分是安装摇杆的轴承孔与桨叶根部安装轴孔基准a,相互之间有15
°
偏转角度。与轴承孔垂直方向设计了摇杆安装槽。它的外形轮廓为了适应桨毂内腔的狭小运动空间和减轻重量降低能耗均采用曲面和各段圆弧流线设计。
64.a)曲柄内孔
∅
225h8为a基准,在数控立车上加工,外形轮廓和斜孔则由立式铣床和卧式镗床加工,后序加工的孔位都需要以
∅
225内孔为工艺基准来保证位置度和角度的精度,为了便于各工序基准的定位现将各工序基准统一,设计制作了定位工装治具板,即附图15工装治具板图,工装治具板的功能是以曲柄原有设计的安装销孔作为工艺销孔来定位零件来完成后续加工。采用一面两销定位,使设计基准与工艺基准巧妙的重合,该工装治具不仅能在三轴立式数控铣床使用,也能在卧式tk6113数控镗床加工使用,可以做到一具两用;功能使用方法同下(具体工艺步骤)
↓
65.其主要优势有:
66.①
使立式铣床与卧式镗床加工基准重合,消除重复定位误差;
67.②
安装、拆卸、校正工件便捷,适应小批量生产;
68.③
加工15
°
斜孔、槽时与a基准位置方便切换坐标,确保加工精度;
69.④
采用一面两销定位,具有较好装夹刚性,可适应小切深快进给铣削;
70.具体工艺步骤如下:
71.1)立车精车上下端面、内孔和锥孔,外形按最大回转体轮廓车出,保证底面跳动0.07,粗糙度ra1.25μm;
72.2)上xk7310三轴立式数控铣床以内孔a基准用寻边器找中,建立机床坐标系,将工件底面上6
‑∅
40h9销孔按h8公差加工(为了保证后续定位精度,将公差提高一个等级)做定位准备。因变距桨毂分为左旋和右旋,作为桨毂内部组件曲柄区分为5件左旋和5件右旋,6
‑∅
40销孔呈镜像分布,本工序加工结束后做好零件x、y向标识来防止差错;
73.3)制作2件
∅
40h8圆柱销,将零件翻面插入圆柱销并与工装治具装配紧密贴合,使6
‑∅
40销孔孔位与待加工区域的坐标重合。内孔上端面采用盘式压板固定,此时的工件已用一面两销定位,加工刚性稳定,能适应圆弧刀片的重载切削加工。用nx软件分析剩余毛坯余量,制定加工程序粗、精铣外形曲面。整个批次都按此方法装夹完成加工,检验合格后转序到镗床加工;
74.4)采用与上道工序一样的装夹方式校正工装板的基准边,粗、精铣15
°
开口槽,保证良好的位置度、开口尺寸公差和粗糙度,这些最终获得的数据与多方面因素相关,如工装的精度、校调零件的误差值、对刀寻中的偏差、加工刀具的刚性、每层的切深和程序的走刀路径,这些因素都是需要经过不断的调试和验证后获得正确的参数来确保最终产品的合格;
75.5)最后一道加工工序是将工装板竖起安装在方箱的侧面,目的是使工件待加工轴承孔的轴线与机床主轴平行。在工装板的上沿设计了
∅
12基准销,这样便可以在工作台偏转到需加工的角度后按基准销打百分表测得的坐标值经过换算获得最终的加工坐标。例如(图10:工件与工装装夹校正后工作台初始位置在0
°
,测得x值为261.5mm,z值为29.4mm,机床工作台旋转15
°
后可根据旋转前采集的数值计算出销子中心距工件轴孔距离为278.575mm,孔端面起始距离为92.298 mm。在三维软件中复验数据后加工轴承孔,按此方法找正操作简便,孔位精度高;
76.b)曲柄外形曲面加工的工艺方法是用nx软件造型加工零件,创建毛坯轮廓,确定切削参数、刀具类型、走刀策略后进行仿真加工。并分析和优化加工参数和刀路轨迹,最终生成加工程序。
77.1)切削参数和刀具类型方面:
78.曲面传统加工的方法是先用较大直径铣刀进行粗铣,再用小直径球头刀精铣来完成的。由于球刀的切深ap参数往往比较浅,实际切削到零件材料表面的最大刃径会随着曲面形状发生变化,编程时都会按刀具名义计算转速和进给速度,可实际加工时却是有效直径在切削,以
∅
25r12.5球刀为例,在平面工况下切削时的有效直径如(图11所示,若定义vc按名义直径
∅
25的切削速度,但此时实际切削直径是
∅
5.4,是名义直径的21%,需要把进给速度降低和增加转速才能达到零件表面粗糙度的目标值相符,而实际零件要加工的区域有平坦、陡峭的斜面和弧面组成,切削时有效直径在加工过程中会不断发生变化,所以不可能用同一切削参数加工出稳定一致的表面质量,经过试切和验证后发现零件表面质量确实有较大差异,决定用d63r8圆角铣刀代替球刀完成精铣轮廓的任务,只在狭小区域因刀具直径无法加工到的曲面才用球刀清根加工。采用大直径圆角铣刀加工时,实际切削直径受曲面坡
度变化影响较小,加工效率也得到大幅提高。
79.2)加工程序编制方面:
80.根据制定的立车节点图导入siemens.ug创建工件毛坯,与需要加工的零件模型坐标重合。它可以提供互交式编程和后处理等功能,在软件中设定待加工区域的毛坯形状来通过移除垂直于固定刀轴的平面切削层中的材料具体操作方法如下:
①
进入加工模块选择型腔铣削方式,设置机床坐标系在零件圆心,指定加工部件为最终零件轮廓,指定毛坯为已经导入的立车节点图;
②
将序1)中选用好的d63r8刀具规格输入在参数表中,圆弧刀片即可以提高在长时间的粗铣轮廓使用寿命又能提供稳定的切屑质量;
③
刀路轨迹设置,通过在这里的参数设置,可以对进刀方式、步距、层深、余量控制。将切削方式设为[跟随部件],步距平面直径百分比设为刀轴的75%,每刀公共切削深度为0.5mm;
④
经过前面一系列的准备后在操作模块生成仿真刀路,通过刀轨可视化界面来验证刀路是否合格如图12),进入3d可视化模拟加工观察切削顺序和下刀路径的逻辑性是否科学合理;
⑤
把确认好的刀路导出为加工程序,我们的加工系统是西门子 sinumerik 840d所以需要西门子840d.pui的后处理来导出程序,操作中需要注意的是把输出单位设置成公制,因为有的软件会默认为英制尺寸和随后处理定义。这样生成的数据才是安全可靠的。
[0081]
跟随部件切削方式又称为沿零件切削,通过对指定零件几何体进行偏置来产生刀位轨迹,跟随部件切削是零件几何体所定义的所有外围环(包括岛屿、内腔)进行偏置创建刀轨)。需要理解到的是:上述实施例虽然对本发明的设计思路作了比较详细的文字描述,但是这些文字描述,只是对本发明设计思路的简单文字描述,而不是对本发明设计思路的限制,任何不超出本发明设计思路的组合、增加或修改,均落入本发明的保护范围内。
再多了解一些
本文用于创业者技术爱好者查询,仅供学习研究,如用于商业用途,请联系技术所有人。