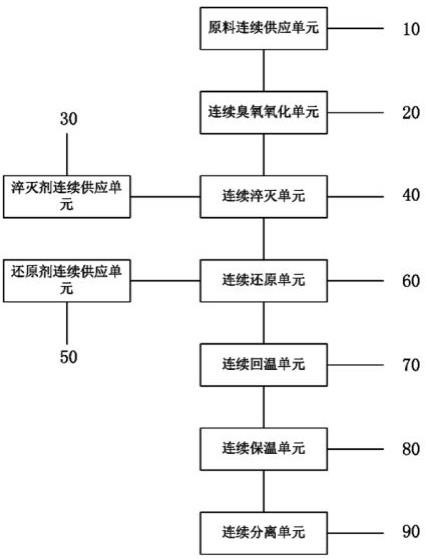
1.本发明涉及4-乙酰氧基氮杂环丁酮的制备技术领域,具体而言,涉及一种连续臭氧氧化制备4-乙酰氧基氮杂环丁酮的系统及方法。
背景技术:
2.培南类抗生素是迄今为止已知的抗菌药物中抗菌谱最广,抗菌作用最强的一类抗生素。由于其在有效的抗菌浓度下对人体的细胞无影响,并且具有超广谱、半衰期长、高效能的抗菌活性和药代动力学特性,培南类抗生素应用范围非常广泛。
3.4-乙酰氧基氮杂环丁酮(4aa)作为培南类抗生素的关键起始原料,在合成碳青霉烯类药物中起到了非常重要的作用,因此具有很大的应用市场。现有制备4aa的方法有很多,其中以l-苏氨酸为原料的方法为市场主流工艺。1984年,m.shiowuki等首次报道该类物质的合成路线。上述方法中,先由主原料l-苏氨酸经过多步反应得到中间体化合物a,之后使用臭氧脱除n-甲氧苯基得到4aa。4aa生产中的关键步骤需要使用臭氧进行氧化,化合物a脱除n-甲氧苯基这一关键步骤的反应式如下所示:。
4.目前商业化生产主要是通过批次反应进行,批次工艺及设备会导致大量的臭氧蓄积,而臭氧十分容易爆炸,反应难于控制,危险系数较高,为高危反应类型。同时产品长时间在臭氧下容易造成变质,纯度和收率下降等质量问题。
技术实现要素:
5.本发明的主要目的在于提供一种连续臭氧氧化制备4-乙酰氧基氮杂环丁酮的系统及方法,以解决现有技术的批次反应制备4-乙酰氧基氮杂环丁酮的纯度和收率较低的问题。
6.为了实现上述目的,根据本发明的一个方面,提供了一种连续臭氧氧化制备4-乙酰氧基氮杂环丁酮的系统,该系统包括:原料连续供应单元,连续臭氧氧化单元,淬灭剂连续供应单元,连续淬灭单元,还原剂连续供应单元,连续还原单元;原料连续供应单元,用于
连续供应主原料溶液和臭氧,主原料溶液为溶液;连续臭氧氧化单元,具有原料入口和臭氧氧化产物体系出口,原料入口与原料连续供应单元相连,连续臭氧氧化单元用于对主原料溶液进行连续臭氧氧化以得到臭氧氧化产物体系;淬灭剂连续供应单元,用于连续供应淬灭剂;连续淬灭单元,具有臭氧氧化产物体系入口、淬灭剂入口和淬灭后体系出口;淬灭剂入口与淬灭剂连续供应单元相连,臭氧氧化产物体系入口与臭氧氧化产物体系出口相连,连续淬灭单元用于将臭氧氧化产物体系在淬灭剂的作用下进行连续淬灭形成淬灭后体系;还原剂连续供应单元,用于连续供应还原剂;连续还原单元,具有淬灭后体系入口、还原剂入口和还原后体系出口,淬灭后体系入口与淬灭后体系出口相连,还原剂入口与还原剂连续供应单元相连,连续还原单元用于对淬灭后体系进行连续还原以形成4-乙酰氧基氮杂环丁酮产物。
7.进一步地,该系统还包括:连续回温单元,连续保温单元和连续分离单元;连续回温单元,具有还原后体系入口、回温后体系出口,还原后体系入口与还原后体系出口相连,连续回温单元用于使4-乙酰氧基氮杂环丁酮产物进行连续回温;连续保温单元,具有回温后体系入口、保温后体系出口,回温后体系入口与回温后体系出口相连,连续保温单元用于使4-乙酰氧基氮杂环丁酮稀释后的产物进行连续保温和浓缩析晶;连续分离单元,具有保温后体系入口、重组分出口以及轻组分出口,保温后体系入口与保温后体系出口相连,连续分离单元用于使4-乙酰氧基氮杂环丁酮产物进行分离纯化。
8.进一步地,原料连续供应单元包括:臭氧连续供应单元和主原料连续供应单元,臭氧连续供应单元用于连续供应臭氧;主原料连续供应单元用于连续供应主原料溶液;臭氧连续供应单元和主原料连续供应单元分别与原料入口相连。
9.进一步地,连续臭氧氧化单元为连续气液反应器;和/或,连续淬灭单元、连续还原单元为连续柱状搅拌反应器;和/或,连续回温单元、连续保温单元为连续釜式搅拌反应器;和/或,连续分离单元为连续分离器。
10.为了实现上述目的,根据本发明的一个方面,提供了一种连续臭氧氧化制备4-乙酰氧基氮杂环丁酮的方法,采用上述系统,该方法包括:向臭氧在连续臭氧氧化单元中连续提供主原料溶液和臭氧,使其进行连续臭氧氧化反应,得到臭氧氧化产物体系;主原料溶液为溶液;将臭氧氧化产物体系连续通入连续淬灭单元中,在淬灭剂的作用下进行连续淬灭反应,得到淬灭后体系;将淬灭后体系连续通入连续还原单元中,在还原剂的
作用下进行连续还原反应,得到4-乙酰氧基氮杂环丁酮产物。
11.进一步地,连续臭氧氧化反应的温度为-40~-5℃;连续臭氧氧化反应的时间为1~3h;连续臭氧氧化反应中臭氧的浓度为50~200mg/l。
12.进一步地,向臭氧在连续臭氧氧化单元中连续提供主原料溶液时,控制主原料溶液的流速为20~80kg/h。
13.进一步地,淬灭剂选自亚硫酸钠溶液、硫酸钠溶液、亚硫酸氢钠溶液、硫代硫酸钠溶液中的一种或多种;和/或,淬灭反应的温度为-40~-5℃,淬灭剂的流速为5~30kg/h。
14.进一步地,连续还原反应的温度为-40~0℃;和/或,还原剂选自锌粉、镁粉、铁粉、甲酸钠、草酸钠、硫脲中的一种或多种。
15.进一步地,还原剂在使用前配制成还原剂溶液,还原剂溶液的流速为20~100kg/h。
16.进一步地,在淬灭后体系进行还原反应之后还包括:对4-乙酰氧基氮杂环丁酮产物进行回温,回温的温度为-20 ~15℃。
17.进一步地,在淬灭后体系进行还原反应之后还包括:对4-乙酰氧基氮杂环丁酮产物进行保温,得到保温后的4-乙酰氧基氮杂环丁酮,保温的温度为5~10℃;将保温后的4-乙酰氧基氮杂环丁酮进行浓缩,得到浓缩的4-乙酰氧基氮杂环丁酮,浓缩的温度为30~75℃;对浓缩的4-乙酰氧基氮杂环丁酮稀释,然后进行析晶反应,得到析晶产物;将析晶产物进行固液分离,将固相产物进行重结晶,得到纯品4-乙酰氧基氮杂环丁酮。
18.进一步地,析晶反应包括搅拌,搅拌的转速为30~150r/min,析晶反应的温度为-10~10℃,析晶反应的时间为2~4h。
19.应用本发明的技术方案,本技术的连续化反应系统在应用于臭氧氧化制备4-乙酰氧基氮杂环丁酮时,具有反应时间短的优势,避免产品长时间在臭氧存在的条件下导致变质,从而使制备得到的4-乙酰氧基氮杂环丁酮更加稳定,不容易变质,同时有利于提升4-乙酰氧基氮杂环丁酮的收率并提升4-乙酰氧基氮杂环丁酮的纯度;相比批次生产,本技术连续化反应的实施,减少了设备占地并使得设备操作简单,同时减少人员操作,降低了人工成本。并且在反应过程中降低了三废的产出,提高了产能,并具有低成本、高安全性、高经济价值以及能够保持连续稳定生产的优点。
附图说明
20.构成本技术的一部分的说明书附图用来提供对本发明的进一步理解,本发明的示意性实施例及其说明用于解释本发明,并不构成对本发明的不当限定。在附图中:图1示出了根据本发明的一种实施例提供的连续氧化制备4-乙酰氧基氮杂环丁酮的系统示意图;图2示出了本发明实施例1的hplc检测图;图3示出了本发明实施例1的核磁氢谱图;图4示出了本发明实施例1的红外谱图。
21.其中,上述附图包括以下附图标记:10、原料连续供应单元;20、连续臭氧氧化单元;30、淬灭剂连续供应单元;40、连续淬灭单元;50、还原剂连续供应单元;60、连续还原单元;70、连续回温单元;80、连续保温单元;90、连续分离单元。
具体实施方式
22.需要说明的是,在不冲突的情况下,本技术中的实施例及实施例中的特征可以相互组合。下面将参考附图并结合实施例来详细说明本发明。
23.如背景技术所分析的,4aa生产中的关键步骤需要使用臭氧进行氧化,目前商业化生产主要是通过批次反应进行,批次工艺及设备会导致大量的臭氧蓄积,而臭氧十分容易爆炸,反应难于控制,危险系数较高,为高危反应类型。同时产品长时间在臭氧下容易造成变质,纯度和收率下降等质量问题。为了解决这些问题,本技术提供了一种连续臭氧氧化制备4-乙酰氧基氮杂环丁酮的系统及方法。
24.在本技术一种典型的实施方式中,提供了一种连续臭氧氧化制备4-乙酰氧基氮杂环丁酮的系统,该系统包括:原料连续供应单元10、连续臭氧氧化单元20、淬灭剂连续供应单元30、连续淬灭单元40、还原剂连续供应单元50、连续还原单元60,原料连续供应单元10用于连续供应主原料溶液和臭氧,主原料溶液为溶液;连续臭氧氧化单元20具有原料入口和臭氧氧化产物体系出口,原料入口与原料连续供应单元10相连,连续臭氧氧化单元20用于对主原料溶液进行连续臭氧氧化以得到臭氧氧化产物体系;淬灭剂连续供应单元30用于连续供应淬灭剂;连续淬灭单元40具有臭氧氧化产物体系入口、淬灭剂入口和淬灭后体系出口;淬灭剂入口与淬灭剂连续供应单元30相连,臭氧氧化产物体系入口与臭氧氧化产物体系出口相连,连续淬灭单元40用于将臭氧氧化产物体系在淬灭剂的作用下进行连续淬灭形成淬灭后体系;还原剂连续供应单元50用于连续供应还原剂;连续还原单元60具有淬灭后体系入口、还原剂入口和还原后体系出口,淬灭后体系入口与淬灭后体系出口相连,还原剂入口与还原剂连续供应单元相连,连续还原单元60用于对淬灭后体系进行连续还原以形成4-乙酰氧基氮杂环丁酮产物。
25.本技术的连续化反应系统在应用于臭氧氧化制备4-乙酰氧基氮杂环丁酮时,具有反应时间短的优势,避免产品长时间在臭氧的存在下导致变质,从而使制备得到的4-乙酰氧基氮杂环丁酮更加稳定,不容易变质,同时有利于提升4-乙酰氧基氮杂环丁酮的收率并提升4-乙酰氧基氮杂环丁酮的纯度;相比批次生产,本技术连续化反应的实施,减少了设备占地并使得设备操作简单,同时减少人员操作,降低了人工成本。并且在反应过程中降低了三废的产出,提高了产能,并具有低成本、高安全性、高经济价值以及能够保持连续稳定生产的优点。
26.在连续臭氧氧化制备4-乙酰氧基氮杂环丁酮的方法中还包括对产品4-乙酰氧基氮杂环丁酮的后处理,因此,如图1所示,上述系统还包括:连续回温单元70、连续保温单元80和连续分离单元90;连续回温单元70,具有还原后体系入口、回温后体系出口,还原后体系入口与还原后体系出口相连,连续回温单元70用于使4-乙酰氧基氮杂环丁酮产物进行连续回温;连续保温单元80,具有回温后体系入口、保温后体系出口,回温后体系入口与回温
后体系出口相连,连续保温单元80用于使4-乙酰氧基氮杂环丁酮产物进行连续保温和浓缩析晶;连续分离单元90,具有保温后体系入口、重组分出口以及轻组分出口,保温后体系入口与保温后体系出口相连,连续分离单元90用于使4-乙酰氧基氮杂环丁酮产物进行分离纯化。
27.为了实现原料的连续供应,并减少人员操作,在一些实施例中,上述原料连续供应单元10包括:臭氧连续供应单元和主原料连续供应单元;臭氧连续供应单元用于连续供应臭氧;主原料连续供应单元用于连续供应主原料溶液;臭氧连续供应单元和主原料连续供应单元分别与原料入口相连。其中,主原料连续供应单元与原料入口通过第一自动打料泵相连。本技术对臭氧连续供应单元所采用的反应器没有特别的限制,优选上述臭氧连续供应单元为臭氧发生器。
28.上述连续淬灭单元40中,臭氧氧化产物体系入口与臭氧氧化产物体系出口通过第二自动打料泵相连,以向连续淬灭单元连续提供臭氧氧化产物,淬灭剂入口与淬灭剂连续供应单元30通过第三打料泵相连,以向连续淬灭单元提供淬灭剂。
29.上述连续还原单元60中,还原剂入口与还原剂连续供应单元50通过第四打料泵相连,以向连续还原单元60连续提供还原剂。
30.在一些实施例中,上述连续臭氧氧化单元20为连续气液反应器,和/或,连续淬灭单元40、连续还原单元60为连续柱状搅拌反应器,和/或,连续回温单元70、连续保温单元80为连续釜式搅拌反应器;和/或,连续分离单元90为连续分离器。通过上述连续气液反应器的内部换热结构和夹套,可以满足系统整体的控温要求,并解决了反应过程中的散热问题,避免了批次生产过程中急剧放热等安全隐患。
31.在一些实施例中,上述连续分离单元90为连续薄膜分离器。
32.上述系统还包括plc自动控制装置,该plc自动控制装置与系统中的各单元电连接,用于控制设备中的反应温度、原料流速、反应时间等,具体控制方式时本领域技术人员都清楚的,在此不再赘述。通过plc自动化控制手段,实现了温度的精确控制及反馈,从而减少了4-乙酰氧基氮杂环丁酮的降解及副反应。
33.在本技术另一种典型的实施方式中,提供了一种连续臭氧氧化制备4-乙酰氧基氮杂环丁酮的方法,采用上述系统,该方法包括:向臭氧在连续臭氧氧化单元20中连续提供主原料溶液和臭氧,使其进行连续臭氧氧化反应,得到臭氧氧化产物体系;主原料溶液为溶液;将臭氧氧化产物体系连续通入连续淬灭单元40中,在淬灭剂的作用下进行连续淬灭反应,得到淬灭后体系;将淬灭后体系连续通入连续还原单元60中,在还原剂的作用下进行连续还原反应,得到4-乙酰氧基氮杂环丁酮产物。
34.采用上述系统,本技术的反应时间减少,物料浓度降低,后处理时间相应缩短,因此本技术的制备方法可以更好地避免副产物或杂质的产生,同时控制产品的降解,从而提
高反应纯度和收率。并且,由于副产物和杂质的减少,产物提纯消耗的能源以及试剂也随之减少,进而降低了产品提纯的能耗以及废物排放和处理的成本。
35.在一些实施例中,上述方法还包括:在进行连续臭氧氧化反应之前进行预处理,预处理的步骤包括:通过管路向反应柱内打入溶剂,控制夹套降温至-25~-10℃,启动臭氧发生器通入臭氧。对上述溶剂没有特别的限制,常用的有机溶剂如甲醇、丙酮、乙腈等均可以应用至本技术。
36.为了使主原料溶液与臭氧充分进行氧化反应并加快反应速率,在一些实施例中,连续臭氧氧化反应的温度为-40~-5℃,优选为-30~-10℃,更优选为-25~-10℃,连续臭氧氧化反应的时间为1~3h。对主原料溶液中的溶剂没有特别的限制,只要能将主原料溶解即可,常用的有机溶剂如甲醇、丙酮、乙腈等均可以应用至本技术。优选本技术主原料溶液的质量百分比浓度为20~30%。
37.在一些实施例中,连续臭氧氧化反应过程中,控制反应体系中的臭氧浓度为50~200mg/l。臭氧浓度过低会导致反应速度下降,臭氧浓度过高会导致臭氧氧化的副产物增多,收率下降。
38.为了使主原料溶液与臭氧充分接触传质,在一些实施例中,向臭氧在连续臭氧氧化单元20中连续提供主原料溶液时,控制主原料溶液的流速为20~80kg/h。流速过高,会导致臭氧与主原料溶液传质不充分,从而导致物料堆积,流速过低会导致反应不充分。
39.上述连续淬灭反应包括,将臭氧氧化产物体系连续输送至连续淬灭单元40,并向淬灭剂连续供应单元30中加入淬灭剂,对臭氧氧化产物体系进行连续淬灭反应。本技术对淬灭剂没有特别的限制,在一些实施例中,淬灭剂选自亚硫酸钠溶液、硫酸钠溶液、亚硫酸氢钠溶液、硫代硫酸钠溶液中的一种或多种,优选为硫代硫酸钠溶液。
40.为了使臭氧氧化反应终止,上述淬灭剂的质量百分比浓度为20~40%,优选为30%。
41.为了提高连续淬灭反应速率,在一些实施例中,连续淬灭反应的温度为-40~-5℃,优选为-30~-10℃,更优选为-15~-5℃,淬灭剂的流速为5~30kg/h。淬灭剂流速可以根据主原料溶液的流速进行调整。
42.为了使淬灭后体系充分还原并提高反应速率,在一些实施例中,连续还原反应的温度为-40~0℃,优选为-20~-5℃,更优选为-15~-5℃。
43.上述还原反应包括,将淬灭后体系连续输送至连续还原单元60,并向还原剂连续供应单元50中加入还原剂溶液,得到4aa。本技术对还原剂没有特别的限制,在一些实施例中,还原剂选自锌粉、镁粉、铁粉、甲酸钠、草酸钠、硫脲中的一种或多种。优选还原反应采用的还原剂溶液为硫脲溶液。
44.还原剂在使用前需要配制成还原剂溶液,例如将上述硫脲溶于甲醇溶剂中形成硫脲甲醇溶液。在一些实施例中,上述还原剂溶液的流速为20~100kg/h。还原剂溶液流速过高会增加三废以及提高后处理成本,还原剂溶液流速过低会有中间态未被完全还原成产品影响收率。
45.为了使淬灭后体系充分还原为4aa,在一些实施例中,在淬灭后体系进行连续还原反应之后还包括:对4-乙酰氧基氮杂环丁酮产物进行回温,回温的温度为-20~15℃,优选为-15~10℃,更优选为0~10℃。
46.在一些实施例中,在淬灭后体系进行还原反应之后还包括:对4-乙酰氧基氮杂环
丁酮产物进行保温,得到保温后的4-乙酰氧基氮杂环丁酮,保温的温度为5~10℃;将保温后的4-乙酰氧基氮杂环丁酮进行浓缩,得到浓缩的4-乙酰氧基氮杂环丁酮。本技术对上述浓缩的方式没有特别的限制,可以为薄膜浓缩。浓缩的温度为30~75℃,优选为40~50℃。对浓缩的4-乙酰氧基氮杂环丁酮稀释,然后进行析晶反应,得到析晶产物;将析晶产物进行固液分离,将固相产物进行重结晶,得到纯品4-乙酰氧基氮杂环丁酮。
47.对浓缩的4-乙酰氧基氮杂环丁酮稀释的溶剂可以采用水。上述固液分离的方式没有特别的限制,离心,抽滤等方式均可以应用至本技术。
48.在一些实施例中,析晶反应包括搅拌,搅拌的转速为30~150r/min,析晶反应的温度为-10~10℃,优选为0~5℃,析晶反应的时间为2~4h。析晶反应时间过短会增加母液残留,从而导致收率下降,析晶反应时间过长会导致生产效率下降。
49.为了得到纯度更高的4-乙酰氧基氮杂环丁酮,在得到粗品4-乙酰氧基氮杂环丁酮之后还需要进行重结晶。将粗品用正庚烷:乙酸乙酯=10:1质量比的混合溶液升降温进行重结晶,过滤得到纯品4-乙酰氧基氮杂环丁酮。
50.以下结合具体实施例对本技术作进一步详细描述,这些实施例不能理解为限制本技术所要求保护的范围。
51.实施例1通过管路向反应柱内打入甲醇100kg,控制夹套乙醇降温至-25~-10℃,启动臭氧发生器,通入臭氧,臭氧流速40m
³
/h,控制臭氧浓度120mg/l。
52.配主原料溶液,控温15~25℃,向干燥洁净的搪瓷釜中加入200kg(2r,3r)-3-[(r)-1-叔丁基二甲基氧代-乙基]-1-(4-甲氧基苯基)-4-乙酰氧基-2-氮杂环丁酮(购买自江苏汉阔公司),再向体系中加入1000kg甲醇,搅拌,搪瓷釜的下口通氮气至固体全部溶解形成主原料溶液待用。
[0053]
配淬灭剂,在200l搪瓷釜中加入282kg纯化水,搅拌下加入120.6kg硫代硫酸钠,搅拌至全部溶解后形成30%的淬灭剂待用。
[0054]
配还原剂溶液,向洁净的搪瓷釜中加入1360kg甲醇和135.2kg硫脲,控温25~30℃,搅拌全溶后形成还原剂溶液待用。
[0055]
连续臭氧氧化反应:控制连续气液反应器中的臭氧反应柱温度-25℃~-10℃,将主原料甲醇溶液预冷-15℃~-5℃,通过质量流量计向反应柱中以40kg/h速度打入主原料溶液,臭氧浓度为120mg/l,主原料溶液与臭氧进行反应形成臭氧氧化产物体系,并以相同速度排出。
[0056]
连续淬灭反应:以连续柱状搅拌反应器作为连续淬灭单元,控制其温度为-15℃~-5℃,以15kg/h速度打入30%的硫代硫酸钠溶液,进行连续淬灭反应形成淬灭后体系。
[0057]
连续还原反应:上述淬灭后体系从连续淬灭单元中柱状反应器的淬灭后体系出口溢流进入连续还原单元中柱状反应器的淬灭后体系入口,自还原剂入口连续泵入硫脲甲醇溶液,流速为60kg/h,控制其温度为-15℃~-5℃,进行连续还原反应形成4-乙酰氧基氮杂环丁酮产物。
[0058]
连续回温反应:上述4-乙酰氧基氮杂环丁酮产物进入回温连续反应搅拌器(cstr),夹套打循环水将体系缓慢回温0~10℃,以形成回温后体系。
[0059]
连续保温反应:将上述回温后体系连续打料至溢流体系进入保温cstr,控温5~10
℃反应,以形成保温后体系。
[0060]
浓缩:控制薄膜热水温度40~50℃浓缩至体系1300l,得到浓缩的4-乙酰氧基氮杂环丁酮,向浓缩的4-乙酰氧基氮杂环丁酮中加入850kg纯化水稀释,以100r/min的转速进行析晶反应,降温至0~5℃,保温3h。
[0061]
离心淋洗:将体系放入离心机,离心得到产品使用2000kg纯化水进行淋洗。得到4-乙酰氧基氮杂环丁酮粗品收率90%。
[0062]
重结晶:使用50kg乙酸乙酯500kg正庚烷,升温50℃溶解粗品,缓慢降温0~5℃,搅拌养晶3h,压滤,最后在45℃真空条件下,干燥得到纯品。4aa成品收率85.6%,hplc检测纯度≥99%,最大单一杂质含量≤0.1%,参见图2,图2中保留时间、相对保留时间、峰高、峰面积和峰面积比值如表1所示。
[0063]
通过连续化生产所得的产品4aa均通过核磁氢谱,红外分别参见图3、图4,旋光度,以及熔点进行了结构确认,并与4aa标准品进行了hpcl出峰时间对比,所有信息均与4aa标准品一致。结果如下:1h-nmr(400 mhz, chloroform-d):0.06(d, j = 5.5 hz 6h) ,0.85 (s, 9h), 1.24 (d, j = 6.4, 3h), 2.09 (s, 3h), 3.17 (dd, j = 3.5, 1.3hz, 1h), 4.21 (qd, j = 6.3, 3.4hz, 1h), 5.83 (d, j = 1.3hz, 1h), 6.56 (s, 1h);ir (kbr) : v3199, 3125, 2958, 2930, 2895, 2857, 1783, 1746, 1471, 1464, 1376, 1361, 1342, 1299, 1254, 1236, 1190, 1163, 1134, 1108, 1079, 1041, 1008, 998, 984, 946, 897, 874, 838, 812, 776, 715, 664cm-[α]
20d
: 51.3
°
(c=1.0 chcl3);m.p. : 105℃实施例2通过管路向反应柱内打入甲醇100kg,控制夹套乙醇降温至-25~-10℃,启动臭氧发生器,通入臭氧,臭氧流速40m
³
/h,控制臭氧浓度50mg/l。
[0064]
配主原料溶液,控温15~25℃,向干燥洁净的搪瓷釜中加入200kg(2r,3r)-3-[(r)-1-叔丁基二甲基氧代-乙基]-1-(4-甲氧基苯基)-4-乙酰氧基-2-氮杂环丁酮,再向体系中加入1000kg甲醇,搅拌,搪瓷釜的下口通氮气至固体全部溶解形成主原料溶液待用。
[0065]
配淬灭剂,在200l搪瓷釜中加入282kg纯化水,搅拌下加入120.6kg硫代硫酸钠,搅拌至全部溶解后形成30%的淬灭剂待用。
[0066]
配还原剂溶液,向洁净的搪瓷釜中加入1360kg甲醇和135.2kg硫脲,控温25~30℃,搅拌全溶后形成还原剂溶液待用。
[0067]
连续臭氧氧化反应:控制连续气液反应器中的臭氧反应柱温度-40℃~-25℃,将原料预冷-15℃~-5℃,通过质量流量计向反应柱中以20kg/h速度打入主原料溶液,臭氧浓度为50mg/l,主原料溶液与臭氧进行反应形成臭氧氧化产物体系,并以相同速度排出。
[0068]
连续淬灭反应:以连续柱状搅拌反应器作为连续淬灭单元,控制其温度为-40℃~-15℃,以5kg/h速度打入30%的硫代硫酸钠溶液,进行连续淬灭反应形成淬灭后体系。
[0069]
连续还原反应:上述淬灭后体系从连续淬灭单元中柱状搅拌反应器的淬灭后体系出口溢流进入连续还原单元中柱状反应器的淬灭后体系入口,自还原剂入口连续泵入硫脲甲醇溶液,流速为20kg/h,控制其温度为-40℃~-15℃,进行连续还原反应形成4-乙酰氧基
乙酰氧基氮杂环丁酮粗品。
[0086]
重结晶:使用50kg乙酸乙酯500kg正庚烷,升温50℃溶解粗品,缓慢降温0~5℃,搅拌养晶3h,压滤,最后在45℃真空条件下,干燥得到纯品。
[0087]
实施例4通过管路向反应柱内打入甲醇100kg,控制夹套乙醇降温至-25~-10℃,启动臭氧发生器,通入臭氧,臭氧流速40m
³
/h,控制臭氧浓度120mg/l。
[0088]
配主原料溶液,控温15~25℃,向干燥洁净的搪瓷釜中加入200kg(2r,3r)-3-[(r)-1-叔丁基二甲基氧代-乙基]-1-(4-甲氧基苯基)-4-乙酰氧基-2-氮杂环丁酮,再向体系中加入1000kg甲醇,搅拌,搪瓷釜的下口通氮气至固体全部溶解形成主原料溶液待用。
[0089]
配淬灭剂,在200l搪瓷釜中加入282kg纯化水,搅拌下加入120.6kg硫代硫酸钠,搅拌至全部溶解后形成30%的淬灭剂待用。
[0090]
配还原剂溶液,向洁净的搪瓷釜中加入1360kg甲醇和135.2kg硫脲,控温25~30℃,搅拌全溶后形成还原剂溶液待用。
[0091]
连续臭氧氧化反应:控制连续气液反应器中的臭氧反应柱温度-25℃~-10℃,将主原料甲醇溶液预冷-15℃~-5℃,通过质量流量计向反应柱中以40kg/h速度打入主原料溶液,臭氧浓度为120mg/l,主原料溶液与臭氧进行反应形成臭氧氧化产物体系,并以相同速度排出。
[0092]
连续淬灭反应:以连续柱状搅拌反应器作为连续淬灭单元,控制其温度为-55℃~-45℃,以15kg/h速度打入30%的硫代硫酸钠溶液,进行连续淬灭反应形成淬灭后体系。
[0093]
连续还原反应:上述淬灭后体系从连续淬灭单元中柱状反应器的淬灭后体系出口溢流进入连续还原单元中柱状反应器的淬灭后体系入口,自还原剂入口连续泵入硫脲甲醇溶液,流速为60kg/h,控制其温度为-15℃~-5℃,进行连续还原反应形成4-乙酰氧基氮杂环丁酮产物。
[0094]
连续回温反应:上述4-乙酰氧基氮杂环丁酮产物进入回温连续反应搅拌器(cstr),夹套打循环水将体系缓慢回温0~10℃,以形成回温后体系。
[0095]
连续保温反应:将上述回温后体系连续打料至溢流体系进入保温cstr,控温5~10℃反应,以形成保温后体系。
[0096]
浓缩:控制薄膜热水温度40~50℃浓缩至体系1300l,得到浓缩的4-乙酰氧基氮杂环丁酮,向浓缩的4-乙酰氧基氮杂环丁酮中加入850kg纯化水稀释,以100r/min的转速进行析晶反应,降温至0~5℃,保温3h。
[0097]
离心淋洗:将体系放入离心机,离心得到产品使用2000kg纯化水进行淋洗。得到4-乙酰氧基氮杂环丁酮粗品。
[0098]
重结晶:使用50kg乙酸乙酯500kg正庚烷,升温50℃溶解粗品,缓慢降温0~5℃,搅拌养晶3h,压滤,最后在45℃真空条件下,干燥得到纯品。
[0099]
实施例5通过管路向反应柱内打入甲醇100kg,控制夹套乙醇降温至-25~-10℃,启动臭氧发生器,通入臭氧,臭氧流速40m
³
/h,控制臭氧浓度120mg/l。
[0100]
配主原料溶液,控温15~25℃,向干燥洁净的搪瓷釜中加入200kg(2r,3r)-3-[(r)-1-叔丁基二甲基氧代-乙基]-1-(4-甲氧基苯基)-4-乙酰氧基-2-氮杂环丁酮,再向体系中
加入1000kg甲醇,搅拌,搪瓷釜的下口通氮气至固体全部溶解形成主原料溶液待用。
[0101]
配淬灭剂,在200l搪瓷釜中加入282kg纯化水,搅拌下加入120.6kg硫代硫酸钠,搅拌至全部溶解后形成30%的淬灭剂待用。
[0102]
配还原剂溶液,向洁净的搪瓷釜中加入1360kg甲醇和135.2kg硫脲,控温25~30℃,搅拌全溶后形成还原剂溶液待用。
[0103]
连续臭氧氧化反应:控制连续气液反应器中的臭氧反应柱温度-25℃~-10℃,将主原料甲醇溶液预冷-15℃~-5℃,通过质量流量计向反应柱中以40kg/h速度打入主原料溶液,臭氧浓度为120mg/l,主原料溶液与臭氧进行反应形成臭氧氧化产物体系,并以相同速度排出。
[0104]
连续淬灭反应:以连续柱状搅拌反应器作为连续淬灭单元,控制其温度为-5℃~0℃,以15kg/h速度打入30%的硫代硫酸钠溶液,进行连续淬灭反应形成淬灭后体系。
[0105]
连续还原反应:上述淬灭后体系从连续淬灭单元中柱状反应器的淬灭后体系出口溢流进入连续还原单元中柱状反应器的淬灭后体系入口,自还原剂入口连续泵入硫脲甲醇溶液,流速为60kg/h,控制其温度为-15℃~-5℃,进行连续还原反应形成4-乙酰氧基氮杂环丁酮产物。
[0106]
连续回温反应:上述4-乙酰氧基氮杂环丁酮产物进入回温连续反应搅拌器(cstr),夹套打循环水将体系缓慢回温0~10℃,以形成回温后体系。
[0107]
连续保温反应:将上述回温后体系连续打料至溢流体系进入保温cstr,控温5~10℃反应,以形成保温后体系。
[0108]
浓缩:控制薄膜热水温度40~50℃浓缩至体系1300l,得到浓缩的4-乙酰氧基氮杂环丁酮,向浓缩的4-乙酰氧基氮杂环丁酮中加入850kg纯化水稀释,以100r/min的转速进行析晶反应,降温至0~5℃,保温3h。
[0109]
离心淋洗:将体系放入离心机,离心得到产品使用2000kg纯化水进行淋洗,得到4-乙酰氧基氮杂环丁酮粗品。
[0110]
重结晶:使用50kg乙酸乙酯500kg正庚烷,升温50℃溶解粗品,缓慢降温0~5℃,搅拌养晶3h,压滤,最后在45℃真空条件下,干燥得到纯品。
[0111]
对比例1将(2r,3r)-3-[(r)-1-叔丁基二甲基氧代-乙基]-1-(4-甲氧基苯基)-4-乙酰氧基-2-氮杂环丁酮加入反应釜,加入甲醇,室温搅拌溶清后,降温至-20℃,以60m
³
/h速度通入臭氧,浓度140mg/l,保持反应温度-20~-15℃之间,tlc点板至原料点消失,控温-20~-15℃滴加30%硫代硫酸钠水溶液至体系无氧化性,保温搅拌之后滴加10%硫脲甲醇溶液进行还原,hplc跟踪至中间体≤0.1%,40~50℃浓缩至7v加5v水析晶得到产品。
[0112]
上述各实施例和对比例中反应原料转化率、产品的纯度和收率如表2所示。
[0113]
4aa hplc检测条件如下:色谱仪——美国agilent 1260高效液相色谱仪,色谱柱——lichrospher 100 rp-18, 250*4mm, 5um,柱温——40℃,流速——1.3ml/min,检测波长——uv at 220nm,
流动相——10% h3po4:acetonitrile:water-1:600:400稀释剂——1%h3po
4 : acetonitrile-3:40004aa 氢谱检测条件:检测仪——varian mercury plus400mhz bruker avance neo 400mhz测定条件——cdcl3作为溶剂。
[0114]
4aa 红外检测条件:检测仪——bruker tensor 27,检测条件——kbr 压片。
[0115]
表1表1根据实施例1~5和对比例1可以看出,对比例1采用现有技术中的批次反应,相比实
施例采用本技术的连续化反应,对比例1中的产品的收率较低,可见,本技术的连续化反应可以有效提高产品收率。
[0116]
从以上的描述中,可以看出,本发明上述的实施例实现了如下技术效果:本技术的连续化反应系统在应用于臭氧氧化制备4-乙酰氧基氮杂环丁酮时,具有反应时间短的优势,避免产品长时间在臭氧下变质,从而使制备得到的4-乙酰氧基氮杂环丁酮更加稳定,不容易变质,同时有利于提升4-乙酰氧基氮杂环丁酮的收率并提升4-乙酰氧基氮杂环丁酮的纯度;相比批次生产,本技术连续化反应的实施,减少了设备占地并使得设备操作简单,同时减少人员操作,降低了人工成本。并且在反应过程中降低了三废的产出,提高了产能,并具有低成本、高安全性、高经济价值以及能够保持连续稳定生产的优点。
[0117]
以上所述仅为本发明的优选实施例而已,并不用于限制本发明,对于本领域的技术人员来说,本发明可以有各种更改和变化。凡在本发明的精神和原则之内,所作的任何修改、等同替换、改进等,均应包含在本发明的保护范围之内。
再多了解一些
本文用于创业者技术爱好者查询,仅供学习研究,如用于商业用途,请联系技术所有人。