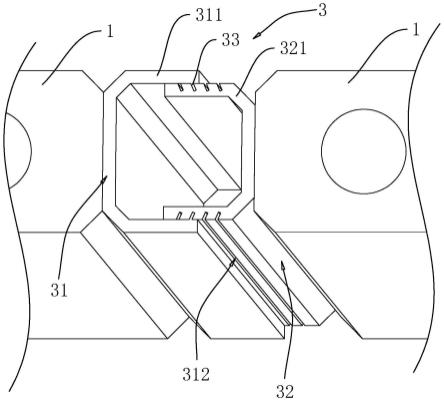
1.本技术涉及建筑施工技术领域,更具体地说,它涉及一种双发泡组分石膏基泡沫混凝土及其制备方法和应用的装配式轻质内隔墙系统。
背景技术:
2.装配式内隔墙板作为一种新型节能墙体材料已广泛应用于建筑工程中,具有增加建筑使用面积、减轻墙体自重、改善使用性能、降低建筑综合造价、减少湿作业、提高建筑施工效率等特点。
3.如申请公布号为cn 108341637a的中国专利公开了一种以轻质陶粒为骨料的装配式内隔墙板,该装配式内隔墙板的由以下原材料制作而成:按重量份数计,作为胶凝材料中水泥占23~24份、粉煤灰占10份,作为粗骨料的轻质陶粒占29~30份,作为细骨料的陶粒砂颗粒占5份,外加剂占0.1份,其余为水;制作方法是将各种原材料混合在一起并搅拌均匀后即可制得以轻质陶粒、陶粒砂为骨料的装配式内隔墙板。该内隔墙板减轻装配式内隔墙板重量。
4.但是该墙板以水泥主要作为胶凝材料,而水泥水化过程中温度收缩和体积收缩严重,导致制得的内隔墙板容易出现开裂现象。因此需要研究一种新的混凝土应用于装配式内隔墙板,不易开裂,而且保证隔墙板轻质的同时保证强度,以满足内隔墙板的使用要求。
技术实现要素:
5.为了制得不易开裂,且轻质同时保证强度的泡沫混凝土,以满足内隔墙板的使用要求,本技术提供一种双发泡组分石膏基泡沫混凝土及其制备方法和应用的装配式轻质内隔墙系统。
6.第一方面,本技术提供一种双发泡组分石膏基泡沫混凝土,采用如下的技术方案:一种双发泡组分石膏基泡沫混凝土,包括以下重量份原料:脱硫石膏500-620份、水泥350-410份、水250-370份、化学发泡剂0.4-7份、物理发泡剂0.5-2.5份、石膏缓凝剂1.5-2.2份、石膏减水剂1.8-2.3份、聚丙烯纤维2-3份、棕榈纤维3.5-4.5份,其中,化学发泡剂选用铝粉或双氧水,所述物理发泡剂选用植物蛋白发泡剂。
7.通过采用上述技术方案,本技术中以石膏和水泥作为胶凝材料,而且是以石膏为主,缓解由于水泥收缩大导致混凝土后续容易开裂,而且石膏硬化快,生产得到的石膏基隔墙板3-5h即可脱模,相较于传统水泥基隔墙板凝结硬化慢,还需要蒸汽养护,本技术中石膏基泡沫混凝土应用降低成本,提高生产效率。此外,由于石膏具有“自呼吸”功能,当室内温度、湿度发生很大变化的时候,石膏制品“自呼吸”功能可以使得环境的温度和湿度得到一定的调节和改善。
8.本技术中采用化学发泡和物理发泡相结合的方式,而且植物蛋白发泡剂,具有优异的气泡性能,泡沫稳定性好,与铝粉化学发泡剂配合后,既保证了混凝土的轻质还保证其
强度,得到混凝土制品的面密度和抗压强度综合性能更优。再配合聚丙烯纤维和棕榈纤维的添加,进一步提高抗裂性能,提高混凝土制品的抗弯承载力,石膏缓凝剂的添加有效控制石膏凝结速度,解决了石膏遇水快速硬化的问题。最终得到的泡沫混凝土制成轻质隔墙板的面密度达到60-70kg/m2,抗压强度不低于3.5mpa,从而可以满足泡沫混凝土在轻质内隔墙中的使用要求。
9.可选的,所述化学发泡剂选用铝粉。
10.通过采用上述技术方案,化学发泡剂选用铝粉时与物理发泡剂相互作用得到混凝土制品的面密度和抗压强度的综合性能更优。
11.可选的,所述双发泡组分石膏基泡沫混凝土还包括1.5-2.5重量份稳泡剂。
12.通过采用上述技术方案,稳泡剂的添加提高泡沫混凝土的稳定性。
13.可选的,所述稳泡剂选用硬脂酸钙。
14.可选的,所述棕榈纤维经过改性后添加,改性方法如下:以重量份计,将50-60份棕榈纤维前处理后与150-200份水混合,然后加入45-60份氯化钙,搅拌混合,然后加入10-18份硅烷偶联剂,在40-45℃下搅拌20-30min后,过滤,然后加入40-50份硅酸钠和180-250份水,在40-45℃下搅拌40-60min,过滤后水洗,然后在60-70℃烘干1-1.5h,得到改性棕榈纤维。
15.通过采用上述技术方案,本技术中将棕榈纤维通过硅酸钠和氯化钙溶液的反应,在棕榈纤维的孔隙内形成硅酸钙纳米粒子,再在硅烷偶联剂的作用下与棕榈纤维的羟基作用,从而改善棕榈纤维的耐热性和内在离散性,而且棕榈纤维与水泥和石膏等更加容易分散,进一步改善泡沫混凝土的开裂性能和力学性能。
16.可选的,所述前处理包括以下步骤:将棕榈纤维经过等离子处理后,再在混合溶液中浸泡,然后水洗后低温烘干,混合溶液浸过棕榈纤维,且混合溶液由10-15份过氧碳酸钠、15-20份磷酸乙二胺和5-10份过氧化氢和50-60份水混合得到。
17.通过采用上述技术方案,将棕榈纤维先经过等离子处理起到一部分的去除胶质的作用,而且使得棕榈纤维表面粗糙,提高表面活性,提高后续硅酸钙纳米粒子与纤维的结合活性点位,在棕榈纤维上负载更多的硅酸钙纳米粒子,进一步提高力学性能,后续经过磷酸乙二胺、过氧化氢以及过氧碳酸钠混合溶液处理后,去除棕榈纤维中木质素、果胶等胶体杂质,进而便于后续氯化钙溶液的浸入,在棕榈纤维的孔隙内生成更多的硅酸钙纳米粒子,进一步改善泡沫混凝土的力学性能。
18.可选的,所述等离子处理参数为:功率200-300w,流量2-3l/min,时间5-10min。
19.第二方面,本技术提供一种双发泡组分石膏基泡沫混凝土的制备方法,采用如下的技术方案:一种双发泡组分石膏基泡沫混凝土的制备方法,包括以下步骤:将石膏缓凝剂、石膏减水剂和水混合均匀,然后加入水泥,制得水泥浆体,然后再在水泥浆体中加入脱硫石膏,搅拌均匀,再加入聚丙烯纤维和棕榈纤维再次搅拌均匀,得到基体材料浆体;将物理发泡剂加水稀释后发泡,形成泡沫液,然后将泡沫液与基体材料浆体混合,得到单发泡组分泡沫混凝土浆体;在单发泡组分泡沫混凝土浆体中加入化学发泡剂,得到双发泡组分石膏基泡沫混
凝土。
20.通过采用上述技术方案,由于石膏遇水会快速凝结硬化,因此本技术在制备混凝土时首先将石膏缓凝剂溶于水中,与石膏混合反应的是溶解有石膏缓凝剂的水溶液,有效控制石膏凝结速度,解决石膏遇水快速硬化问题,最终制得面密度低且强度高的双发泡组分石膏基泡沫混凝土。
21.可选的,将石膏缓凝剂和水混合的时候还添加有1.5-2.5重量份稳泡剂。
22.第三方面,本技术提供一种装配式轻质内隔墙系统,采用如下的技术方案:一种装配式轻质内隔墙系统,包括若干由所述的双发泡组分石膏基泡沫混凝土浇筑得到的轻质隔墙板。
23.通过采用上述技术方案,将本技术中双发泡组分石膏基泡沫混凝土浇筑得到轻质隔墙板应用于轻质内隔墙系统时,满足其质轻、强度高的要求。
24.可选的,所述装配式轻质内隔墙系统还包括调节件和l型隔墙板,所述调节件设置于相邻轻质隔墙板之间,所述调节件包括第一调节板和第二调节板,所述第一调节板与所述第二调节板均由抵接段和处于抵接段两侧的连接段连接形成,所述第一调节板的连接段为第一连接段,所述第二调节板的连接段为第二连接段;所述第一连接段外侧与所述第二连接段内侧贴合,且所述第一连接段外侧开设有若干限位孔,所述第二连接段的内侧连接有倾斜设置的限位板,所述限位板端面与所述第二连接段之间的距离沿着靠近第一连接段逐渐增大。
25.通过采用上述技术方案,本技术中调节件的设置可以调节第一调节板和第二调节板之间连接尺寸,从而可以扩大第一调节板和第二调节板宽度之和,从而解决轻质隔墙板组装时产生的留空问题,而且通过拉伸调节到需要宽度,相较于传统采用切割工具切割或类似现浇方式更加简单方便。
26.综上所述,本技术具有以下有益效果:1、本技术中以石膏和水泥作为胶凝材料,而且是以石膏为主,缓解由于水泥收缩大导致混凝土后续容易开裂,而且石膏硬化快,生产得到的石膏基隔墙板3-5h即可脱模,相较于传统水泥基隔墙板凝结硬化慢,还需要蒸汽养护,本技术中石膏基泡沫混凝土应用降低成本,提高生产效率;2、本技术中采用化学发泡和物理发泡相结合的方式,而且植物蛋白发泡剂,具有优异的气泡性能,泡沫稳定性好,与铝粉化学发泡剂配合后,既保证了混凝土的轻质还保证其强度,得到的泡沫混凝土制成轻质隔墙板的面密度达到60-70kg/m2,抗压强度不低于3.5mpa;3、本技术中将棕榈纤维通过硅酸钠和氯化钙溶液的反应,在棕榈纤维的孔隙内形成硅酸钙纳米粒子,再在硅烷偶联剂的作用下与棕榈纤维的羟基作用,从而改善棕榈纤维的耐热性和内在离散性,而且棕榈纤维与水泥和石膏等更加容易分散,进一步改善泡沫混凝土的开裂性能和力学性能;4、本技术中将棕榈纤维先经过等离子处理起到一部分的去除胶质的作用,而且使得棕榈纤维表面粗糙,提高表面活性,提高后续硅酸钙纳米粒子与纤维的结合活性点位,在棕榈纤维上负载更多的硅酸钙纳米粒子,进一步提高力学性能,后续经过磷酸乙二胺、过氧化氢以及过氧碳酸钠混合溶液处理后,去除棕榈纤维中木质素、果胶等胶体杂质,进而便于
后续氯化钙溶液的浸入,在棕榈纤维的孔隙内生成更多的硅酸钙纳米粒子,进一步改善泡沫混凝土的力学性能。
附图说明
27.图1是本技术装配式轻质内隔墙系统的整体结构示意图;图2是本技术中调节件的结构示意图。
28.附图标记:1、轻质隔墙板;2、l形隔墙板;3、调节件;31、第一调节板;311、第一连接段;312、限位孔;32、第二调节板;321、第二连接段;33、限位板。
具体实施方式
29.以下结合附图和实施例对本技术作进一步详细说明,予以特别说明的是:以下实施例中未注明具体条件者,按照常规条件或制造商建议的条件进行,以下实施例中所用原料除特殊说明外均可来源于普通市售。
30.以下实施例中,石膏缓凝剂选用阿克思建筑科技河北有限公司;石膏减水剂选用上海英杉新材料科技有限公司,型号为pg-310石膏减水剂;水泥选用o.o42.5r普通硅酸盐水泥。
31.以下制备例是改性棕榈纤维的制备例制备例1一种棕榈纤维的改性方法,包括以下步骤:s1、将棕榈纤维经过等离子处理,等离子处理参数为:功率300w,流量2l/min,时间10min;将12kg过氧碳酸钠、18kg磷酸乙二胺和8kg过氧化氢和55kg水混合得到混合溶液;s2、将s1中等离子处理后的棕榈纤维在s2中得到的混合溶液中浸泡2.5h,混合溶液浸过棕榈纤维,然后将浸泡后的棕榈纤维水洗后在50℃下烘干1h,得到初级改性棕榈纤维;s3、取55kg步骤s2中初级改性棕榈纤维与180kg水混合,然后加入50kg氯化钙,搅拌混合,然后加入14kg硅烷偶联剂,在45℃下搅拌20min后,过滤,然后加入45kg硅酸钠和200kg水,在40℃下搅拌50min,过滤后水洗,然后在65℃烘干1h,得到改性棕榈纤维。
32.制备例2一种棕榈纤维的改性方法,包括以下步骤:s1、将棕榈纤维经过等离子处理,等离子处理参数为:功率200w,流量2l/min,时间10min;将10kg过氧碳酸钠、15kg磷酸乙二胺和5kg过氧化氢和50kg水混合得到混合溶液;s2、将s1中等离子处理后的棕榈纤维在s2中得到的混合溶液中浸泡2h,混合溶液浸过棕榈纤维,然后将浸泡后的棕榈纤维水洗后在45℃下烘干1.5h,得到初级改性棕榈纤维;s3、取50kg步骤s2中初级改性棕榈纤维与150kg水混合,然后加入45kg氯化钙,搅拌混合,然后加入10kg硅烷偶联剂,在40℃下搅拌30min后,过滤,然后加入40kg硅酸钠和180kg水,在40℃下搅拌60min,过滤后水洗,然后在60℃烘干1.5h,得到改性棕榈纤维。
33.制备例3一种棕榈纤维的改性方法,包括以下步骤:s1、将棕榈纤维经过等离子处理,等离子处理参数为:功率300w,流量3l/min,时间5min;将15kg过氧碳酸钠、20kg磷酸乙二胺和10kg过氧化氢和60kg水混合得到混合溶液;s2、将s1中等离子处理后的棕榈纤维在s2中得到的混合溶液中浸泡3h,混合溶液浸过棕榈纤维,然后将浸泡后的棕榈纤维水洗后在55℃下烘干1h,得到初级改性棕榈纤维;s3、取60kg步骤s2中初级改性棕榈纤维与200kg水混合,然后加入60kg氯化钙,搅拌混合,然后加入18kg硅烷偶联剂,在45℃下搅拌20min后,过滤,然后加入50kg硅酸钠和250kg水,在45℃下搅拌40min,过滤后水洗,然后在70℃烘干1h,得到改性棕榈纤维。
34.制备例4一种棕榈纤维的改性方法,按照制备例1中的方法进行,不同之处在于,未进行步骤s2的操作,将等离子处理后的棕榈纤维直接进行步骤s3的处理,与氯化钙和水混合。
35.制备例5一种棕榈纤维的改性方法,按照制备例1中的方法进行,不同之处在于,步骤s1的混合溶液中未添加过氧碳酸钠。
36.制备例6一种棕榈纤维的改性方法,按照制备例1中的方法进行,不同之处在于,步骤s1中的混合溶液中未添加磷酸乙二胺。
37.制备例7一种棕榈纤维的改性方法,按照制备例1中的方法进行,不同之处在于,未进行步骤s3,将步骤s2中得到的初级改性棕榈纤维直接作为改性棕榈纤维使用。
38.实施例1一种双发泡组分石膏基泡沫混凝土的制备方法,包括以下步骤:将1.6kg石膏缓凝剂、1.8kg石膏减水剂、1.5-2.5kg稳泡剂和270kg水混合均匀,然后加入360kg水泥,制得水泥浆体,然后再在水泥浆体中加入540kg脱硫石膏,搅拌,再加入2.5kg聚丙烯纤维和3.8kg棕榈纤维,再次搅拌均匀,得到基体材料浆体;将1.2kg物理发泡剂加水稀释30质量倍后,采用高压空气压缩发泡剂发泡,形成泡沫液,然后将泡沫液与基体材料浆体混合均匀,得到单发泡组分泡沫混凝土浆体;在单发泡组分泡沫混凝土浆体中加入0.9kg化学发泡剂,混合均匀,得到双发泡组分石膏基泡沫混凝土;其中,物理发泡剂选用植物蛋白发泡剂,化学发泡剂选用30wt%浓度双氧水,稳泡剂选用硬脂酸钙。
39.实施例2一种双发泡组分石膏基泡沫混凝土的制备方法,包括以下步骤:将1.5kg石膏缓凝剂、1.8kg石膏减水剂、1.5kg稳泡剂和250kg水混合均匀,然后加入350kg水泥,制得水泥浆体,然后再在水泥浆体中加入500kg脱硫石膏,搅拌均匀,再加入2kg聚丙烯纤维和3.5kg棕榈纤维,再次搅拌均匀,得到基体材料浆体;
将0.5kg物理发泡剂加水稀释30质量倍后,采用高压空气压缩发泡剂发泡,形成泡沫液,然后将泡沫液与基体材料浆体混合均匀,得到单发泡组分泡沫混凝土浆体;在单发泡组分泡沫混凝土浆体中加入0.4kgkg化学发泡剂,混合均匀,得到双发泡组分石膏基泡沫混凝土;其中,物理发泡剂选用植物蛋白发泡剂,化学发泡剂选用30wt%浓度双氧水,稳泡剂选用硬脂酸钙。
40.实施例3一种双发泡组分石膏基泡沫混凝土的制备方法,包括以下步骤:将2.2kg石膏缓凝剂、2.3kg石膏减水剂、2.5kg稳泡剂和370kg水混合均匀,然后加入410kg水泥,制得水泥浆体,然后再在水泥浆体中加入620kg脱硫石膏,搅拌均匀,再加入3kg聚丙烯纤维和4.5kg棕榈纤维,再次搅拌均匀,得到基体材料浆体;将2.5kg物理发泡剂加水稀释30质量倍后,采用高压空气压缩发泡剂发泡,形成泡沫液,然后将泡沫液与基体材料浆体混合均匀,得到单发泡组分泡沫混凝土浆体;在单发泡组分泡沫混凝土浆体中加入7kgkg化学发泡剂,混合均匀,得到双发泡组分石膏基泡沫混凝土;其中,物理发泡剂选用植物蛋白发泡剂,化学发泡剂选用30wt%浓度双氧水,稳泡剂选用硬脂酸钙。
41.实施例4一种双发泡组分石膏基泡沫混凝土的制备方法,按照实施例1中的方法进行,不同之处在于,化学发泡剂选用铝粉。
42.实施例5一种双发泡组分石膏基泡沫混凝土的制备方法,按照实施例1中的方法进行,不同之处在于,化学发泡剂30wt%浓度双氧水的添加量为6.8kg。
43.实施例6-8一种双发泡组分石膏基泡沫混凝土的制备方法,按照实施例4中的方法进行,不同之处在于,将棕榈纤维等量替换为制备例1-3中制备得到的改性棕榈纤维。
44.实施例9-12一种双发泡组分石膏基泡沫混凝土的制备方法,按照实施例6中的方法进行,不同之处在于,将棕榈纤维等量替换为制备例4-7中得到的改性棕榈纤维。
45.对比例1一种双发泡组分石膏基泡沫混凝土的制备方法,按照实施例4中的方法进行,不同之处在于,原料中未添加棕榈纤维。
46.对比例2一种双发泡组分石膏基泡沫混凝土的制备方法,按照实施例4中的方法进行,不同之处在于,将棕榈纤维等量替换为聚丙烯纤维。
47.对比例3一种双发泡组分石膏基泡沫混凝土的制备方法,按照实施例4中的方法进行,不同之处在于,将脱硫石膏等量替换为水泥。
48.对比例4
一种双发泡组分石膏基泡沫混凝土的制备方法,按照实施例4中的方法进行,不同之处在于,水泥添加量为540kg,脱硫石膏添加量为360kg。
49.性能检测对上述实施例和对比例中制得的双发泡组分石膏基泡沫混凝土进行浇筑入模,等待4h,得到轻质隔板墙,对轻质隔板墙进行面密度和抗压强度的检测,同时对实施例和对比例中制得的双发泡组分石膏基泡沫混凝土进行圆环试验开裂时间,检测结果如下表1所示:表1:表1:由上表1可知,本技术中得到轻质隔墙板1的面密度为60-70kg/m2,抗压强度不低于3.5mpa,满足jc/t169-2016中相关规定。
50.再结合实施例1与实施例4和实施例5的检测结果,可以看到,化学发泡剂选用铝粉相较于双氧水具有更好的发泡效果,得到轻质隔墙板1的面密度更小,再结合实施例5,即便双氧水的添加量增大,轻质隔墙板1的面密度依然较大,而选用铝粉时虽然抗压强度有所降低,但是依然达到4.5mpa以上,满足产品要求,而且面密度显著降低,其综合效果更好。
51.再结合实施例4与实施例6-8的检测结果,可以看出,将棕榈纤维替换为改性棕榈纤维的时候,轻质隔墙板1的抗压强度有所增大,面密度影响较小,可能是由于棕榈纤维质轻,而生成的纳米硅酸钙也质轻,轻质隔墙板1的综合性能更优,而且混凝土的抗裂性能显著提升。
52.结合实施例6与实施例9-11的检测结果,可以看出,实施例9中棕榈纤维改性步骤中等离子处理后棕榈纤维直接负载纳米硅酸钙时,得到混凝土的抗裂性能有所降低,而且
面密度也更大,可能是由于棕榈纤维中的胶质杂质较多;实施例10和实施例11中在混合溶液中未添加过氧碳酸钠或磷酸乙二胺的时候,混凝土的抗裂性能均有所降低;再结合实施例12中的检测结果,混凝土中添加的改性棕榈纤维只做等离子处理和混合溶液处理,未进行纳米硅酸钙负载时,混凝土的抗裂性能和抗压强度均有所降低。
53.再结合实施例4与对比例1和对比例2的检测结果,可以看出,原料中添加有棕榈纤维和聚丙烯纤维两者复配的时候,混凝土的抗裂性能以及制得隔墙板的面密度综合性能更优;再结合对比例3和对比例4的检测结果,可以看出,本技术体系中只将水泥作为胶粘材料或水泥添加量较大时,制得的混凝土的抗裂性能较差。
54.应用例将本技术实施例中得到的混凝土应用于装配式轻质内隔墙系统,如图1所示,应用的装配式轻质内隔墙系统包括轻质隔墙板1、调节件3和l型隔墙板,轻质隔墙板1为本技术实施例中制得的双发泡组分石膏基泡沫混凝土浇筑入模,静停3-5后拆模即可得到,很显然,将本技术中制得的石膏基泡沫混凝土应用于轻质隔墙板1的浇筑成型,无需蒸养,直接静停3-5h即可,大大降低成本,初凝时间仅仅1h左右,时间大大缩短。
55.由于传统轻质隔墙的走线方法为在墙板表面开槽安装线管,但是这样一方面墙板表面开槽容易引起墙面开裂,另一方面,现场开槽会产生更多的粉尘和建筑垃圾,而且现场施工难度较大,因此本技术中的轻质内隔墙系统为由若干轻质隔墙板1装配形成,且拐角处通过l形隔墙板2连接而成,形成具有空腔的轻质内隔墙系统,如此可以在拼装叠合安装前进行管线安装于空腔内。
56.但是如此在轻质隔墙板1装配过程中,由于轻质隔墙板1的尺寸固定,会出现留空问题,有一种解决方式会采用切割工具切割或用类似现场浇筑的方法,但是如此会产生更多的粉尘和建筑垃圾,因此,本技术中在形成有留空位置的相邻轻质隔墙板1之间设置有调节件3。
57.如图1和图2所示,调节件3设置于相邻轻质隔墙板1之间,调节件3包括第一调节板31和第二调节板32,第一调节板31与第二调节板32均由抵接段和处于抵接段两侧的连接段连接形成,第一调节板31的连接段为第一连接段311,第二调节板32的连接段为第二连接段321;第一连接段311外侧与第二连接段321内侧贴合,且第一连接段311外侧开设有若干限位孔312,第二连接段321的内侧连接有倾斜设置的限位板33,限位板33端面与第二连接段321之间的距离沿着靠近第一连接段311逐渐增大。
58.在装配轻质内隔墙系统的时候,将若干轻质隔墙板1组装,拐角处采用l形板连接,形成具有空腔的轻质内隔墙系统,在轻质隔墙板1留空位置处设置有调节板,通过限位板33沿着限位孔312滑动,插接在不同位置的限位孔312内,从而可以调节第一调节板31和第二调节板32的重合面积,进而实现第一调节板31和第二调节板32调宽,使得第一调节板31和第二调节板32相互远离的一侧与相邻轻质隔墙板1抵接,实现留空位置的填充。
59.本具体实施例仅仅是对本技术的解释,其并不是对本技术的限制,本领域技术人员在阅读完本说明书后可以根据需要对本实施例做出没有创造性贡献的修改,但只要在本技术的权利要求范围内都受到专利法的保护。
再多了解一些
本文用于创业者技术爱好者查询,仅供学习研究,如用于商业用途,请联系技术所有人。