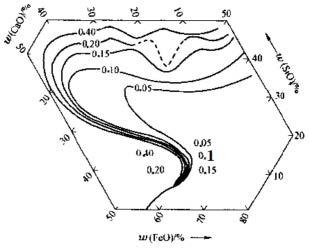
1.本发明属于资源综合利用领域,具体涉及一种液态钢渣的处理,为一种降低高温钢渣粘度提高风碎处理比例的方法。
背景技术:
2.钢渣是炼钢副产物,约占钢产量10%,钢渣的处理与利用不仅是环境问题,也是资源问题。实现钢渣资源化利用的前提是如何实现高温钢渣的冷却与粒化,即钢渣一次处理,高温钢渣冷却粒化后再通过加工成不同用途的材料进行资源化利用,即钢渣二次加工利用。
3.目前,国内外钢铁企业钢渣一次处理技术主要包括热闷法、滚筒法、风碎法及热泼法。其中,热闷法包括常压池式热闷和有压罐式热闷,其优点是可以全量化高温钢渣,包括液态渣和熔融态渣,缺点是需要将约1600℃的高温钢渣通过机械破碎和打水冷却至固态(约500-800℃),再进行热闷处理,这一过程耗时费力,成本高,处理周期长。滚筒和风碎原理类似,利用钢渣在高温下成液态,流动性较好的特点,通过采用压缩空气或者钢球破碎作用,实现高温钢渣的粒化,其优点是处理效率高,节奏快,但存在问题是对高温钢渣流动性要求高,无法在重力作用下从渣罐中自然流出的钢渣不能进入这类处理系统,同时滚筒法与风碎法相比,风碎工艺采用压缩空气作为介质实现对液态钢渣的粒化,比滚筒法采用钢球在机械转动状态下对液态钢渣进行粒化相比,处理效率更高,节奏更快,成本更低。
4.钢渣风碎处理工艺对钢渣的流动性要求较高,即高温钢渣要有较高的过热度,保证钢渣粘度较低,从而保证钢渣保持较好的高温流动性,以使高温钢渣能在渣罐倾翻过程中在重力作用下顺利流入到处理装置中,若流动性较差,钢渣不能从渣罐中流出或者在风碎处理装置中发生粘连,从而导致生产无法顺利进行。
5.2011年3月9日公开的申请号为201010559657.3的专利《钢渣液化升温工艺及装置》其特征在于通过用喷枪向高温液态钢渣中喷吹氧气使渣中低价铁及金属铁液滴的氧化放热,提高液渣温度,熔化渣块,改善钢渣流动性,有利于钢渣热态在线处理,提高钢渣风碎或水淬处理率。该发明采用向液态钢渣中吹氧使渣低价铁氧化放热来提高钢渣温度,改善钢渣流动性,该方案存在缺陷是,钢渣中低价铁及金属铁液滴含量不确定,导致向渣中吹氧能产生多少氧化反应放出的热量不确定,无法保证钢渣温度提升及流动性改善效果,同时向渣中吹氧会产生含尘气体,发明方案中提及对含尘气体的收集与处理,存在环保问题。
6.2006年6月14日公开的申请号为200410089361.4的专利《一种用于滚筒法渣处理装置的动力导流锥盘装置》其特征在于采用一种用于滚筒法渣处理装置的动力导流锥盘装置,该装置包含有辐射状支撑钢板制作的导流盘,呈锥台形,导流盘通过一根轴联接大齿轮,大齿轮由驱动装置带动,驱动装置、大齿轮和轴均安装在轴承座上,导流盘位于轴承座一侧置于或偏置于滚筒进料侧并在受料漏斗的下方。该方案并没有解决钢渣自身流动性问题,而是采用增加导流盘通过机械力的作用将流动性差的钢渣送进滚筒处理装置。该方案存在三个问题:一是没有从根本上提升钢渣流动性,未能为滚筒法钢渣处理装置提供流动
性更好的钢渣;二是导流盘虽然能起到一定作用,但是当钢渣的流动性低到一定程度的时候,导流盘可能会失效而导致设备故障,还可能出现将流动性较差的钢渣强制送进滚筒装置后导致钢渣在装置内部发生粘结、卡死等故障;三是这种导流盘的设计只适用于滚筒法处理流动性钢渣,而对风碎工艺处理流动性钢渣不适用。
7.2015年1月21日公开的申请号为201410526618.1的专利《一种转炉脱磷阶段钢渣改质工艺》其特征在于在转炉脱磷阶段吹炼结束前由高位料仓向炉内添加sio2材料或sio2和al2o3为主要成分的材料或al2o3材料对炉渣进行改质处理,使炉渣的碱度降低,有泡沫渣压渣无泡沫渣稀渣。该技术方案主要是在转炉脱磷阶段控制炉渣碱度在0.8-1.3之间,并没有提出解决钢渣处理时流动性问题,且在实际实施过程中存在炉渣碱度降低会使转炉脱磷效果下降的问题。
8.经检索,目前关于提高钢渣流动性方面的文献主要包括3种方式,一是通过向高温液态钢渣中喷吹氧气使渣中低价铁及金属铁液滴的氧化放热,提高液渣温度,熔化渣块,改善钢渣流动性,存在因钢渣中低价铁及金属铁液滴含量不确定,无法保证钢渣温度提升及流动性改善效果,同时向渣中吹氧会产生含尘气体存在环保问题。第二种是通过向高温钢渣中加入改质剂,加入改质剂的种类,比例及加入方式根据改质后钢渣用途不同的不同,已有技术方案的改质多采取加入sio2、al2o3类材料以改善钢渣在水泥、建材中应用性能为目的,并未明确针对钢渣粘度来设计改质钢渣的具体组成要求;另一种是通过机械装置直接将流动性不好的钢渣强制送入钢渣处理装置,该方案从本质上并未解决钢渣流动性问题,且存在引发设备故障等问题。
技术实现要素:
9.本发明的目的在于提供一种降低高温钢渣粘度提高风碎处理比例的方法,通过分析影响钢渣流动性的关键因素,并结合钢渣自身特性和炼钢生产实际条件,采用铁水脱硫前扒渣、钢包精炼渣等炼钢工序过程产生的高温热态熔渣在线调控钢渣碱度、温度及成分,降低渣系熔点,提高钢渣过热度,从而降低高温钢渣的粘度,实现在线调控钢渣流动性的效果。采用本发明的方法,使风碎工艺实现对高温钢渣的全量化处理,为高温钢渣粒化提供一种高效率、低成本的处理技术。
10.本发明具体技术方案如下:
11.一种降低高温钢渣粘度提高风碎处理比例的方法,具体为:
12.在转炉出渣前,在渣罐中先装入热态铁水脱硫前扒渣和热态钢包精炼渣中的一种或者二者混合物,转炉出渣即可。
13.当只加入热态铁水脱硫前扒渣时,其重量不超过转炉出渣量重量的20%;所述热态铁水脱硫前扒渣cao与sio2质量百分比w
cao
/w
sio2
≤1.5,温度≥1200℃;
14.当只加入热态钢包精炼渣时,其重量不超过转炉出渣量重量的20%;所述热态钢包精炼渣cao与al2o3质量百分比w
cao
/w
al2o3
≤1.5,温度≥1300℃。
15.当加入的是热态铁水脱硫前扒渣和热态钢包精炼渣二者混合物时,混合物总重量不超过转炉出渣量重量的20%;热态铁水脱硫前扒渣和热态钢包精炼渣的成分及温度要求同上;两者的比例不需要限定,前面已说明,单独加入热态铁水脱硫前扒渣或热态钢包精炼渣之一,只需热态铁水脱硫前扒渣或热态钢包精炼渣的相关成分和温度符合要求即可,而
二者混合,只要总比例满足要求,即可满足实现技术方案效果的要求。
16.转炉出渣的钢渣成分满足:cao与sio2质量百分比w
cao
/w
sio2
≤3.5,feo、mno和al2o3质量分数之和与cao质量分数比值w
feo mno al2o3
/w
cao
≥0.30,温度≥1400℃,混合钢渣粘度值低于0.40pa.s。
17.转炉出渣结束后,保证渣罐中混合钢渣的温度及粘度符合要求,具备较好的流动性,进行风碎处理,风碎处理比例≥80%。
18.本发明设计思路如下:
19.铁水前扒渣的二元碱度(cao/sio2)一般在1.0~1.2,转炉钢渣的二元碱度(cao/sio2)一般在3.0~4.0,钢包精炼渣的二元碱度(cao/sio2)虽与转炉钢渣相当,但由于其al2o3含量较高,可以降低渣系的三元碱度(cao/(sio2 al2o3)),因此,无论是铁水前扒渣还是钢包精炼渣或者二者混合物的加入,都可以起到降低渣系碱度作用,而碱度的下降对渣系熔点下降影响较大。
20.转炉钢渣自身cao含量一般在40%左右,sio2含量约10%左右,tfe含量约16%,折算为feo约20%,根据cao-sio
2-feo渣系的粘度曲线,理论上在1400℃,钢渣粘度约在0.40pa.s,而实际生产中,由于排渣后等待过程温降,以及钢渣中自身含油5-10%左右mgo会导致渣系熔点升高而粘度升高,因此为了降低粘度,需要降低cao含量,提高sio2含量和feo含量,同时根据cao-sio
2-al2o3渣系粘度曲线图,在cao-sio2二元渣系中引入al2o3有助于渣系熔点下降,基于上述原理,结合铁水脱硫前扒渣、钢渣精炼渣的成分特点及温度特点,最终设计本发明的技术方案。
21.现有技术公开的加sio2、al2o3的目的和加入方式与本发明均有本质区别,现有技术加的是以sio2、al2o3为主要成分的材料,且其目的主要是为了改变钢渣的冶金性能或者是钢渣在建筑材料中的稳定性,因此其对添加剂材料的要求以及加入比例和方式均有别于本发明。本发明的目的是为了降低高温钢渣的熔点,从而使钢渣在同等温度下具有较高的过热度,从而保证高温钢渣的流动性,为提高钢渣风碎处理效果提供前提条件。另外,若单纯从降低钢渣熔点角度出发,可以加的材料很多,比如含f、含be及含碱金属等化合物均有较好的降低熔点作用,但是本发明结合炼钢工序自身特点,考虑铁水脱硫前扒渣和钢包精炼渣本身具有一定的sio2、al2o3的含量,至少较转炉钢渣含量要高,而且铁水脱硫前扒渣中除了含较高sio2之外,也含有较高的al2o3;而钢包精炼渣出了含较高的sio2、al2o3含量外,还含有较高的feo、mno等有利于降低渣系熔点的成分,其排渣初始温度与转炉钢渣相当,同时工序衔接紧密,通过一定比例控制和物流组织,可以直接实现热态渣的混兑,不仅调控了渣系的熔点,也有效利用了热态渣自身的高温热量,本技术方案基于以上考虑,实现炼钢区域热态钢渣混兑后风碎处理的效果,充分利用了炼钢区域不同工序产生钢渣的特性,提高转炉钢渣风碎处理效果。本发明通过以上技术方案,主要通过终渣中对降低渣系熔点有利的成分控制,同时保证渣温较渣系熔点有合理过热度,这样来保证渣系的粘度低于0.40pa.s,从而为提高风碎处理比例提供保证。
22.本发明针对钢渣风碎处理或滚筒处理过程中存在的钢渣流动性不好而无法处理的难题,通过采用采用铁水脱硫前扒渣、钢包精炼渣等炼钢工序过程产生的高温热态熔渣在线调控钢渣碱度、温度及成分,降低渣系熔点,提高钢渣过热度,从而降低高温钢渣的粘度,实现在线调控钢渣流动性的效果。与现有技术相比,本发明实现高温钢渣流动性在线调
控,降低高温钢渣粘度,改善钢渣流动性更好满足钢渣风碎处理工艺要求;且钢渣风碎处理比例显著提升,降低了钢渣处理成本,提高了钢渣资源化利用效率;而且,实现了铁水脱硫前扒渣和钢包精炼渣与钢渣的协同处理。
附图说明
23.图1cao-sio
2-feo渣系的粘度曲线图;
24.图2cao-sio
2-al2o3渣系粘度曲线图。
具体实施方式
25.下面以300t转炉炼钢及其配套上下游工艺装备为例。
26.对比例1
27.一种钢渣处理方法,具体为:
28.转炉出渣,钢渣主要化学成分如下表1,温度1531℃。w
cao
/w
sio2
=3.7,w
feo mno al2o3
/w
cao
=0.33,钢渣粘度为0.49pa.s。
29.表1对比例1转炉钢渣主要化学成分
30.成分pfeosio2al2o3caomgomnotfe含量0.9912.2513.71.6450.185.292.6316.76
31.将该罐钢渣调运至钢渣风碎处理线进行风碎处理,起始重量28吨,渣罐倾翻至风碎处理线中间包开始风碎作业,随着渣流流出逐渐调整渣罐倾翻角度直至没有液态渣流流出为止,结束时渣罐剩余钢渣重12吨,风碎处理16吨,处理率57.1%。
32.对比例2
33.一种钢渣处理方法,具体为:
34.转炉出渣,钢渣主要化学成分如下表2,温度1542℃。w
cao
/w
sio2
=3.8,w
feo mno al2o3
/w
cao
=0.29,钢渣粘度为0.61pa.s。
35.表2对比例2转炉钢渣主要化学成分
36.成分pfeosio2al2o3caomgomnotfe含量1.1611.1513.431.4151.635.682.1715.65
37.将该罐钢渣调运至钢渣风碎处理线进行风碎处理,起始重量29吨,渣罐倾翻至风碎处理线中间包开始风碎作业,随着渣流流出逐渐调整渣罐倾翻角度直至没有液态渣流流出为止,结束时渣罐剩余钢渣重16吨,风碎处理13吨,处理率44.8%。
38.实施例1
39.一种降低高温钢渣粘度提高风碎处理比例的方法,具体为:
40.将准备接受转炉出渣的渣罐预先在铁水脱硫作业区接受热态铁水脱硫前扒渣3.1吨,铁水脱硫前扒渣主要化学成分如下表3,w
cao
/w
sio2
=1.1,温度1279℃,然后将渣罐调运至转炉炉下接受转炉出渣,累计出渣30.0吨,铁水脱硫前扒渣重量占钢渣重量比10.3%,混合后钢渣主要化学成分如下表4,w
cao
/w
sio2
=3.1,w
feo mno al2o3
/w
cao
=0.40,温度为1475℃,钢渣粘度值0.33pa.s。
41.表3实施例1铁水脱硫前扒渣主要化学成分
42.成分pfeosio2al2o3caomgomnotfe含量0.010.2633.2516.135.37.82.30.65
43.表4实施例1混合后钢渣主要化学成分
44.成分pfeosio2al2o3caomgomnotfe含量1.0611.9815.232.7547.425.874.0614.29
45.将该罐混合钢渣调运至钢渣风碎处理线进行风碎处理,起始重量33.1吨,渣罐倾翻至风碎处理线中间包开始风碎作业,随着渣流流出逐渐调整渣罐倾翻角度直至没有液态渣流流出为止,结束时渣罐剩余钢渣重5.2吨,风碎处理27.9吨,处理率84.3%。
46.实施例2
47.一种降低高温钢渣粘度提高风碎处理比例的方法,具体为:
48.将准备接受转炉出渣的渣罐预先在铁水脱硫作业区接受热态铁水脱硫前扒渣5.3吨,铁水脱硫前扒渣主要化学成分如下表5,w
cao
/w
sio2
=1.2,温度1283℃,然后将渣罐调运至转炉炉下接受转炉出渣,累计出渣30吨,铁水脱硫前扒渣重量占钢渣重量比17.7%,混合后钢渣主要化学成分如下表6,w
cao
/w
sio2
=2.9,w
feo mno al2o3
/w
cao
=0.35,温度为1432℃,钢渣粘度值0.32pa.s。
49.表5实施例2铁水脱硫前扒渣主要化学成分
50.成分pfeosio2al2o3caomgomnotfe含量0.010.2732.6316.0738.307.500.190.69
51.表6实施例2混合后钢渣主要化学成分
52.成分pfeosio2al2o3caomgomnotfe含量0.9911.2216.313.6147.085.951.8713.40
53.将该罐混合钢渣调运至钢渣风碎处理线进行风碎处理,起始重量35.3吨,渣罐倾翻至风碎处理线中间包开始风碎作业,随着渣流流出逐渐调整渣罐倾翻角度直至没有液态渣流流出为止,结束时渣罐剩余钢渣重5吨,风碎处理30.3吨,处理率85.8%。
54.实施例3
55.一种降低高温钢渣粘度提高风碎处理比例的方法,具体为:
56.将准备接受转炉出渣的渣罐预先在精炼作业区接受热态钢包精炼渣3.5吨,钢包精炼渣主要化学成分如下表7,w
cao
/w
al2o3
=1.0,温度1513℃,然后将渣罐调运至转炉炉下接受转炉出渣,累计出渣27吨,热态钢包精炼渣重量占钢渣重量比12.9%,混合后钢渣主要化学成分如下表8,w
cao
/w
sio2
=3.5,w
feo mno al2o3
/w
cao
=0.40,温度为1532℃,钢渣粘度值0.21pa.s。
57.表7实施例3钢包精炼渣主要化学成分
58.成分pfeosio2al2o3caomgomnotfe含量0.011.311.432.032.76.01.32.9
59.表8实施例3混合后钢渣主要化学成分
60.成分pfeosio2al2o3caomgomnotfe含量1.0311.7913.204.9246.805.722.0714.19
61.将该罐混合钢渣调运至钢渣风碎处理线进行风碎处理,起始重量30.5吨,渣罐倾
翻至风碎处理线中间包开始风碎作业,随着渣流流出逐渐调整渣罐倾翻角度直至没有液态渣流流出为止,结束时渣罐剩余钢渣重2吨,风碎处理28.5吨,处理率93.4%。
62.实施例4
63.一种降低高温钢渣粘度提高风碎处理比例的方法,具体为:
64.将准备接受转炉出渣的渣罐预先在精炼作业区接受热态钢包精炼渣4.9吨,钢包精炼渣主要化学成分如下表9,w
cao
/w
al2o3
=0.50,温度1508℃,然后将渣罐调运至转炉炉下接受转炉出渣,累计出渣28吨,热态钢包精炼渣重量占钢渣重量比17.5%,混合后钢渣主要化学成分如下表10,w
cao
/w
sio2
=3.1,w
feo mno al2o3
/w
cao
=0.48,温度为1526℃,钢渣粘度值0.18pa.s。
65.表9实施例4钢包精炼渣主要化学成分
66.成分pfeosio2al2o3caomgomnotfe含量0.012.618.441.720.85.73.26.9
67.表10实施例4混合后钢渣主要化学成分
68.成分pfeosio2al2o3caomgomnotfe含量0.9911.5814.177.4144.495.682.3214.35
69.将该罐混合钢渣调运至钢渣风碎处理线进行风碎处理,起始重量32.9吨,渣罐倾翻至风碎处理线中间包开始风碎作业,随着渣流流出逐渐调整渣罐倾翻角度直至没有液态渣流流出为止,结束时渣罐剩余钢渣重1.9吨,风碎处理31吨,处理率94.2%。
70.实施例5
71.一种降低高温钢渣粘度提高风碎处理比例的方法,具体为:
72.将准备接受转炉出渣的渣罐预先在铁水脱硫作业区接受热态铁水脱硫前扒渣3.3吨,铁水脱硫前扒渣主要化学成分如下表11,w
cao
/w
sio2
=1.3,温度1279℃,再将热态钢包精炼渣通过小渣罐受渣后倒入已装有热态铁水脱硫前扒渣的转炉渣罐中,累计重量约2.1吨,钢包精炼渣主要化学成分如下表12,w
cao
/w
al2o3
=0.52,温度1456℃,然后将预先装入热态铁水脱硫前扒渣和钢包精炼渣(累计5.4吨)的渣罐调运至转炉炉下接受转炉出渣,累计出渣29吨,预先装入热态铁水脱硫前扒渣和钢包精炼渣占钢渣重量比18.6%,混合后钢渣主要化学成分如下表13,w
cao
/w
sio2
=3.1,w
feo mno al2o3
/w
cao
=0.44,温度为1492℃,钢渣粘度值0.25pa.s。
73.表11实施例5铁水脱硫前扒渣主要化学成分
74.成分pfeosio2al2o3caomgomnotfe含量0.010.2231.3615.9739.37.82.10.72
75.表12实施例5钢包精炼渣主要化学成分
76.成分pfeosio2al2o3caomgomnotfe含量0.011.912.540.821.13.53.34.4
77.表13实施例5混合后钢渣主要化学成分
78.成分pfeosio2al2o3caomgomnotfe含量0.9811.2215.095.2146.055.754.0513.53
79.将该罐混合钢渣调运至钢渣风碎处理线进行风碎处理,起始重量34.4吨,渣罐倾
翻至风碎处理线中间包开始风碎作业,随着渣流流出逐渐调整渣罐倾翻角度直至没有液态渣流流出为止,结束时渣罐剩余钢渣重3吨,风碎处理31.4吨,处理率91.3%。
再多了解一些
本文用于创业者技术爱好者查询,仅供学习研究,如用于商业用途,请联系技术所有人。