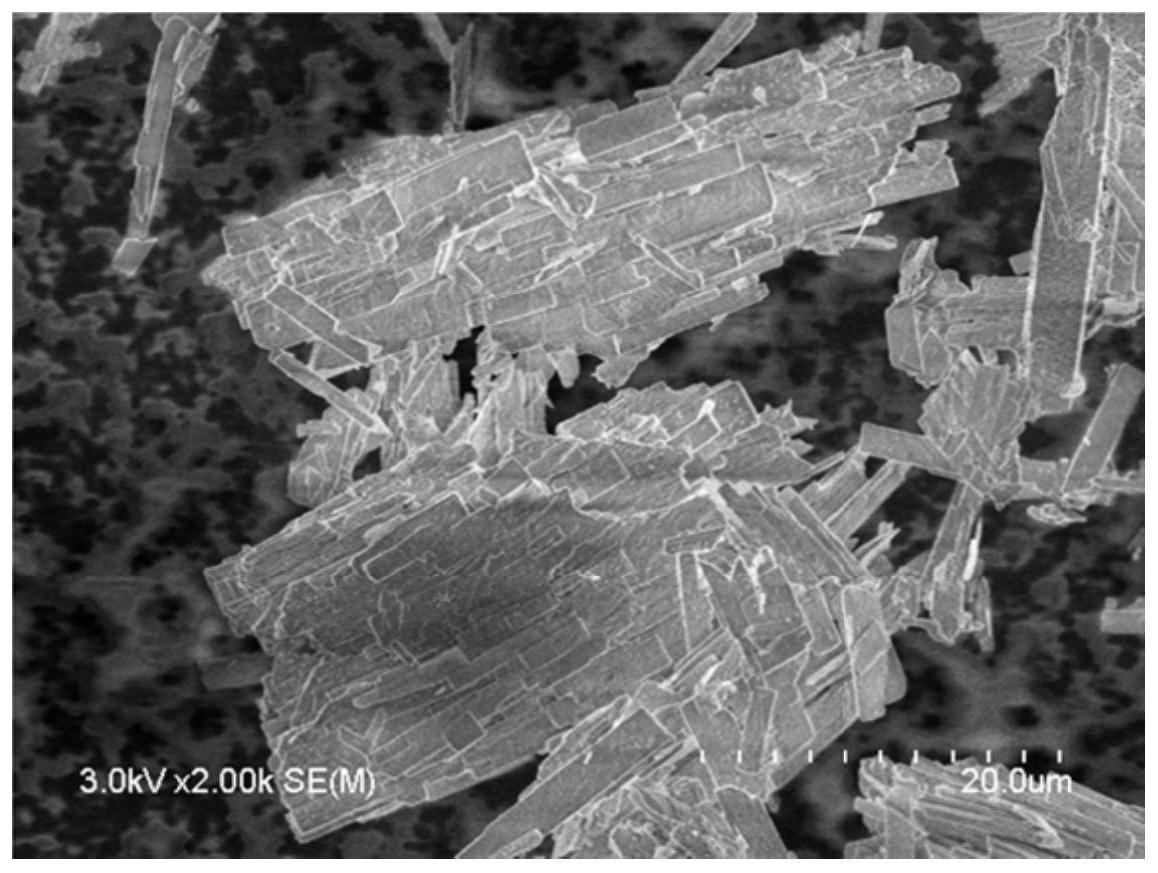
1.本发明涉及催化化学领域,具体地,涉及一种含磷和钴的复合材料及其制备方法,以及在催化转化乙烯与2,5-二甲基呋喃制备对二甲苯中的应用。
背景技术:
2.随着科技的进步,社会的发展,人类对煤、石油、天然气等传统化石能源的需求越来越大,导致地球上化石能源的储量日益枯竭,而且化石能源的燃烧会严重污染环境;相反,生物质作为一种绿色可再生能源,地球储量丰富,转化利用过程不会污染环境,所以许多学者把目光放在用生物质来补充化石能源上。对二甲苯(px)是一种十分重要的化工原料,其主要用途是生产对苯二甲酸和对苯二甲酸酯等聚合物单体产品。px目前主要从石油化工路径制备得到。为了利用生物质资源绿色可持续地生产px,从生物质基2,5-二甲基呋喃(dmf)经diels-alder和脱水反应制备px近年来逐渐成为研究热点(chemsuschem.2016,9,1-14)。
3.dmf作为双烯体,乙烯作为亲双烯体,两者首先发生diels-alder成环反应生成氧杂降冰片烯,再通过脱水反应生成px和水。主要的副反应包括dmf水解为2,5-己二酮、px与乙烯的烷基化反应生成多烷基苯以及dmf与2,5-己二酮的聚合等。dauenhauer课题组(acs catal.2012,2,935-939)研究了不同分子筛对反应性能的影响,实验结果发现当以h-y分子筛为催化剂时效果最佳,在300℃温度下反应,px选择性最高仅为75%,且有大量烷基苯产生,增加了产物提纯分离的成本,难以满足大规模生产的需求。fan课题组(chemcatchem,2017,9,398-402)以磷改性的beta分子筛催化dmf和乙烯在250℃反应24h,dmf转化率完全,产物收率高达97%,但催化稳定性较差,这可能是因为磷元素的流失导致。随后,feng等人(catal.sci.technol.,2017,7,5540-5549;cn109569677a)设计制备了同时含有酸和lewis酸的双功能负载型wo3/sba-15分子筛催化剂,较高选择性地实现了dmf制备px,但负载型催化剂存在但其存在活性组分易流失、循环稳定性能差等缺点,难以实现连续性生产的需求。
4.du课题组(acs sustainable chemistry&engineering,2017,6,1891-1899)采用多孔级nbox催化剂催化dmf和乙烯反应,在250℃下反应6h,dmf转化率为87%,px选择性可达92.7%,同时该催化剂具有良好的稳定性,但nbox催化剂制备过程中需要使用氢氟酸,具有高腐蚀和高污染,对设备要求也较高,大幅度增加了催化剂制备成本。同时,以上报道实验中均采用纯乙烯为原料,而炼厂流化催化裂化干气中的稀乙烯,由于其浓度低(10(v)%-25(v)%),利用难度大,以往通常作为燃料烧掉,浪费了宝贵的资源。若能有效利用这部分乙烯资源,实现稀乙烯资源高价值转化,特别在生物基化学品制备上具有广阔的发展前景。
5.综上所述,现有技术主要存在催化剂制备成本高、循环稳定性差、产品选择性差或制备方法复杂等不利因素,这对工业实际应用带来较大问题。
技术实现要素:
6.本发明所要解决的技术问题是提供一种新的含磷和钴的复合材料及其制备方法,以及在催化转化乙烯与2,5-二甲基呋喃制备对二甲苯中的应用。该复合材料作为催化剂用于乙烯与2,5-二甲基呋喃制备对二甲苯反应中,能够以稀乙烯为原料和在温和反应条件下进行,并且具有2,5-二甲基呋喃的高效转化和产物px选择性高,同时,所述复合材料作为催化剂具有循环使用稳定性突出的特点。
7.本发明第一方面提供了一种含磷和钴的复合材料,所述复合材料包括具有如式“mp2o5·
nco(oh)2·
tco3o
4”所示的示意性化学组成,其中,0.1≤m/(n t)≤4,0.2≤n/t≤6。
8.进一步地,所述复合材料包括具有如式“mp2o5·
nco(oh)2·
tco3o
4”所示的示意性化学组成,其中,0.1≤m/(n t)≤4,比如m/(n t)可以为0.1、0.2、0.3、0.4、0.5、0.8、1.0、1.5、2.0、2.5、3.0、3.5、4.0以及任意两者之间的范围,优选地,0.2≤m/(n t)≤2;0.2≤n/t≤6,比如n/t可以为0.2、0.4、0.5、1.0、1.5、2.0、2.5、3.0、3.5、4.0、4.5、5.0、5.5、6.0以及任意两者之间的范围,优选地,0.5≤n/t≤5。
9.进一步地,所述复合材料中,b酸/l酸的酸量之比≤0.2,优选为0.02-0.2,进一步优选为0.02-0.15;和/或,弱酸含量≥50%,优选为55%-80%。
10.进一步地,所述复合材料中,总酸量为30-400μmol
·
g-1
,优选为50-300μmol
·
g-1
。
11.进一步地,所述复合材料特别适宜用作催化转化稀乙烯与2,5-二甲基呋喃制备对二甲苯的催化剂。
12.本发明第二方面提供了上述复合材料的制备方法,包括:
13.a、将水、模板剂、氧化剂和钴源均匀混合,得到溶液i;
14.b、将磷源与所述溶液i混合,得到溶液ii;
15.c、将所述溶液ii进行晶化处理,制得所述复合材料。
16.进一步地,所述溶液i中,水、模板剂、氧化剂和钴源(以coo计)的质量比为5-80:0.1-5:0.1-2:1,优选为10-30:0.2-2:0.2-1:1;所述溶液ii中,磷源以p2o5计和钴源以coo计的摩尔比为0.1-4:1,优选为0.2-2:1。
17.进一步地,所述水为去离子水;所述模板剂为十六烷基三甲基溴化铵、十二烷基苯磺酸钠、聚环氧乙烷-聚环氧丙烷-聚环氧乙烷三嵌段共聚物(优选地,平均分子量5800)、聚乙烯吡咯烷酮(优选地,分子量为3000-40000)中的一种或几种,优选为十六烷基三甲基溴化铵和聚环氧乙烷-聚环氧丙烷-聚环氧乙烷三嵌段共聚物中的至少一种。所述氧化剂为双氧水、过氧乙酸、过氧丙酸、过戊酸、过氧苯甲酸中的至少一种,优选为双氧水。所述双氧水的浓度为30wt%-70wt%。所述钴盐为硝酸钴、氯化钴、硫酸钴、乙酸钴、乙酰丙酮钴、草酸钴和n,n-二水杨醛乙二胺钴中的至少一种,优选草酸钴和n,n-二水杨醛乙二胺钴中的至少一种。所述磷源为磷酸、磷酸二氢铵、磷酸氢二铵、磷酸铵中的一种或几种。
18.进一步地,所述晶化温度为100-220℃,优选为120-180℃;所述晶化时间为8-72h,优选为12-60h。
19.进一步地,在晶化步骤结束之后,可以通过常规已知的后处理方式得到含磷和钴的复合材料产品,比如可以对所述获得的晶化产物进行离心、洗涤、干燥和焙烧的方法。所述离心、洗涤和干燥可以按照本领域常规已知的任何方式进行。所述洗涤比如可以举出使用去离子水和/或乙醇进行洗涤。所述干燥条件可以为干燥温度40-180℃,优选60-150℃,
干燥时间3-20小时,优选4-15小时。该干燥可以在常压下进行,也可以在减压下进行。所述焙烧条件可以为焙烧温度400-700℃,优选为450-600℃,焙烧时间1-8小时,优选为2-6小时。所述焙烧一般在含氧气氛下进行,比如空气或者氧气气氛下。
20.本发明第三方面提供了一种对二甲苯的制备方法,该方法是采用本发明上述含磷和钴的复合材料作为催化剂,底物含2,5-二甲基呋喃的有机溶剂与乙烯与作为催化剂的所述含磷和钴的复合材料接触反应,得到对二甲苯。
21.进一步地,所述的有机溶剂包括正己烷、正庚烷、正辛烷、四氢呋喃、1,4-二氧六环、甲基异丁基酮和环己烷中的一种或几种。
22.进一步地,所述反应温度为160-340℃,优选为200-300℃;反应时间为6-64h,优选为8-48h。
23.进一步地,所述底物dmf与催化剂的质量比为0.1-6.0:1,优选为0.2-3.0:1;有机溶剂与底物dmf质量比为5-50:1,优选为10-40:1。
24.进一步地,所述乙烯采用稀乙烯,在反应体系中充入稀乙烯,稀乙烯浓度为10(v)%-25(v)%,压力为1-8mpa,优选为2-5mpa。
25.与现有技术相比,本发明具有如下有益效果:
26.1、本发明提供了一种新的含磷和钴的复合材料,具有如式“mp2o5·
nco(oh)2·
tco3o
4”所示的示意性化学组成,特别适用于催化转化稀乙烯与2,5-二甲基呋喃制备对二甲苯的催化剂。
27.2、本发明通过采用含磷和钴的复合材料作为催化剂,用于催化转化乙烯与2,5-二甲基呋喃制备对二甲苯时,在温和反应条件和以稀乙烯为原料条件下,2,5-二甲基呋喃转化率和产物px选择性均非常高。同时,产物中关键杂质含量极低,例如多烷基乙苯,2,5-己二酮和2-环戊烯酮,大大减少了分离能耗。此外,本发明所采用含磷和钴的复合材料作为催化剂,具有很好的稳定性,可多次循环使用。
附图说明
28.图1为实施例1中所得含磷和钴的复合材料的扫描电子显微镜图(sem);
29.图2为实施例1中所得含磷和钴的复合材料的xrd图;
30.图3为实施例1中所得含磷和钴的复合材料的xps图;
31.图4为实施例1中所得含磷和钴的复合材料的py-ftir图;
32.图5为实施例21采用实施例1所得含磷和钴的复合材料循环使用后的dmf转化率和px选择性。
具体实施方式
33.本发明中,反应产物px用气质联用(gc-ms)分析定性,用气相色谱(gc)分析底物2,5-甲基呋喃地转化率和反应产物px的收率。气质联用仪为美国安捷伦公司的agilent 7890a,色谱柱为hp-5非极性毛细管柱(30m,0.53mm),气相色谱仪为agilent 7890b,检测器为氢焰离子化检测器(fid),色谱柱为se-54毛细管柱(30m,0.53mm)。
34.本发明中,分子筛产品xrd测量方法是:采用日本理学rigaku ultima iv型x-射线粉末衍射仪分析样品的物相,cukα射线源镍滤光片,2θ扫描范围2
°‑
50
°
,操作
电压35kv,电流25ma,扫描速率10
°
/min。
35.本发明中,催化剂表面元素结合能由x射线光电子能谱(xps)测定,是在thermo公司的x射线光电子能谱仪esca lab-250)上进行,采用c1s=284.6ev为内标校正所测元素信号。
36.本发明中,采用吡啶吸附红外方法(nicolet model 710光谱仪)对待测试材料酸量、酸种类和酸强度进行测定。具体操作步骤如下:a、样品预处理。将样品(约30mg)压片成型为直径13mm的薄圆片,并装入红外样品槽中。之后,样品在真空池条件和400℃下预处理1h。待样品槽冷却至室温,扫描样品红外数据作为背景;b、吡啶吸附。在室温下和真空环境下,将吡啶蒸气通入至原位直至吸附达到平衡,吸附时间为1h;c、吡啶脱附。吸附结束后,在100℃、200℃下抽真空至内部压力不再变化,脱附时间为40min,并分别扫描记录红外吸收光谱,吡啶吸附前后的差谱即为所得的吡啶吸附-红外吸收光谱图。当脱附温度为100℃时,通过图谱计算所得酸量为总酸量,当脱附温度为200℃时,弱酸位吸附的吡啶将脱附完全,由此可计算得出弱酸含量,从而进一步计算得到弱酸含量百分比。
37.根据图谱对样品的酸量进行了半定量计算:
[0038][0039][0040]
其中,c
l
为酸(b酸)酸量,cb为lewis酸(l酸)酸量;r和w为催化剂薄圆片的直径(cm)和质量(g),a为根据扫描吡啶吸附-红外吸收光谱图在指定波数峰的吸光度积分数值。imec为积分摩尔消光系数,imec
l
为2.22,imecb为1.67。
[0041]
本发明中,2,5-二甲基呋喃转化率公式为:
[0042]
2,5-二甲基呋喃的转化率%=(参加反应的2,5-二甲基呋喃摩尔量)/(反应底物2,5-二甲基呋喃的摩尔量)
×
100%。
[0043]
本发明中,产物px收率计算公式为:
[0044]
产物px的收率%=(反应生成的px摩尔量)/(反应底物2,5-二甲基呋喃的摩尔量)
×
100%。
[0045]
本发明中,产物px的选择性%=(反应生成的px摩尔量)/(反应的2,5-二甲基呋喃摩尔量)
×
100%。
[0046]
为了便于理解本发明,本发明列举实施例如下,但所述实施例仅仅用于帮助理解本发明,不应视为对本发明的具体限制。
[0047]
实施例1
[0048]
按照水、模板剂、氧化剂和钴源的质量比10:1:0.5:1,磷源与钴源摩尔比为0.7进行投料:将40g去离子水、4g十六烷基三甲基溴化铵、4g 50wt%双氧水(以h2o2计)和4g草酸钴混合形成均匀的溶液;将2.2g磷酸二氢铵溶于10g水后,不断滴加至上述溶液中,待搅拌均匀形成凝胶后,在160℃温度下水热晶化24h,经洗涤、干燥,在空气条件下,550℃焙烧5h制得含磷和钴的复合材料。样品的sem电镜图如图1所示,为块状形貌;样品的xrd如图2所示;样品的xps如图3所示,其中元素钴存在两种状态,分别为co(oh)2和co3o4,所得含磷和钴的复合材料化学组成为0.7p2o5·
0.7co(oh)2·
0.3co3o4。样品的py-ftir如图4所示,由此计
算得到的总酸量为192μmol
·
g-1
,b酸/l酸的酸量之比为0.10;其中弱酸含量为67.5%。
[0049]
实施例2
[0050]
按照水、模板剂、氧化剂和钴源的质量比15:0.8:0.2:1,磷源与钴源摩尔比为0.5进行投料:将60g去离子水、3.2g十六烷基三甲基溴化铵、1.6g 50wt%双氧水(以h2o2计)和4g乙酸钴混合形成均匀的溶液;将2.0g磷酸二氢铵溶于10g水后,不断滴加至上述溶液中,待搅拌均匀形成凝胶后,在140℃温度下水热晶化48h,经洗涤、干燥,在空气条件下,550℃焙烧5h制得含磷和钴的复合材料。样品的sem电镜图与图1相类似,为块状形貌;样品的xrd与图2相类似;样品的xps与如图3相似,其中元素钴存在两种状态,分别为co(oh)2和co3o4,所得含磷和钴的复合材料化学组成为0.5p2o5·
0.8co(oh)2·
0.2co3o4。样品的py-ftir如图4相类似,由此计算得到的总酸量为157μmol
·
g-1
,b酸/l酸的酸量之比为0.08;其中弱酸含量为75.1%。
[0051]
实施例3
[0052]
按照水、模板剂、氧化剂和钴源的质量比20:1.5:0.4:1,磷源与钴源摩尔比为1.0进行投料:将80g去离子水、6.0g聚环氧乙烷-聚环氧丙烷-聚环氧乙烷(平均分子量5800)、5.3g 30wt%双氧水(以h2o2计)和4gn,n-二水杨醛乙二胺钴混合形成均匀的溶液;将1.5g磷酸氢二铵溶于10g水后,不断滴加至上述溶液中,待搅拌均匀形成凝胶后,在150℃温度下水热晶化36h,经洗涤、干燥,在空气条件下,500℃焙烧4h制得含磷和钴的复合材料。样品的sem电镜图与图1相类似,为块状形貌;样品的xrd与图2相类似;样品的xps与如图3相似,其中元素钴存在两种状态,分别为co(oh)2和co3o4,所得含磷和钴的复合材料化学组成为1p2o5·
0.6co(oh)2·
0.4co3o4;样品的py-ftir如图4相类似,由此计算得到的总酸量为243μmol
·
g-1
,b酸/l酸的酸量之比为0.13;其中弱酸含量为71.8%。
[0053]
实施例4
[0054]
按照水、模板剂、氧化剂和钴源的质量比15:1.2:0.6:1,磷源与钴源摩尔比为1.5进行投料:将60g去离子水、4.8g十六烷基三甲基溴化铵、8g 30wt%双氧水(以h2o2计)和4gn,n-二水杨醛乙二胺钴混合形成均匀的溶液;将2.3g磷酸氢二铵溶于10g水后,不断滴加至上述溶液中,待搅拌均匀形成凝胶后,在120℃温度下水热晶化60h,经洗涤、干燥,在空气条件下,550℃焙烧4h制得含磷和钴的复合材料。样品的sem电镜图与图1相类似,为块状形貌;样品的xrd与图2相类似;样品的xps与如图3相似,其中元素钴存在两种状态,分别为co(oh)2和co3o4,所得含磷和钴的复合材料化学组成为1.5p2o5·
0.5co(oh)2·
0.5co3o4;样品的py-ftir如图4相类似,由此计算得到的总酸量为208μmol
·
g-1
,b酸/l酸的酸量之比为0.15;其中弱酸含量为65.3%。
[0055]
实施例5
[0056]
按照水、模板剂、氧化剂和钴源的质量比10:0.5:0.8:1,磷源与钴源摩尔比为0.8进行投料:将60g去离子水、4.8g聚乙烯吡咯烷酮(分子量27000-40000)、4.6g 70wt%双氧水(以h2o2计)和4g草酸钴混合形成均匀的溶液;将2.9g磷酸氢二铵溶于10g水后,不断滴加至上述溶液中,待搅拌均匀形成凝胶后,在180℃温度下水热晶化24h,经洗涤、干燥,在空气条件下,550℃焙烧5h制得含磷和钴的复合材料。样品的sem电镜图与图1相类似,为块状形貌;样品的xrd与图2相类似;样品的xps与如图3相似,其中元素钴存在两种状态,分别为co(oh)2和co3o4,所得含磷和钴的复合材料化学组成为0.8p2o5·
0.7co(oh)2·
0.3co3o4;样品
的py-ftir如图4相类似,由此计算得到的总酸量为171μmol
·
g-1
,b酸/l酸的酸量之比为0.11;其中弱酸含量为70.7%。
[0057]
实施例6
[0058]
按照水、模板剂、氧化剂和钴源的质量比20:1.0:0.3:1,磷源与钴源摩尔比为0.4进行投料:将80g去离子水、4.0g聚乙烯吡咯烷酮(分子量27000-40000)、4g 30wt%双氧水(以h2o2计)和4g乙酸钴混合形成均匀的溶液;将0.9g磷酸溶于10g水后,不断滴加至上述溶液中,待搅拌均匀形成凝胶后,在150℃温度下水热晶化30h,经洗涤、干燥,在空气条件下,550℃焙烧6h制得含磷和钴的复合材料。样品的sem电镜图与图1相类似,为块状形貌;样品的xrd与图2相类似;样品的xps与如图3相似,其中元素钴存在两种状态,分别为co(oh)2和co3o4,所得含磷和钴的复合材料化学组成为0.4p2o5·
0.6co(oh)2·
0.4co3o4;样品的py-ftir如图4相类似,由此计算得到的总酸量为132μmol
·
g-1
,b酸/l酸的酸量之比为0.05;其中弱酸含量为76.4%。
[0059]
实施例7-12
[0060]
采用正庚烷为反应溶剂,正庚烷与dmf质量比为20,dmf与作为催化剂的含磷和钴的复合材料质量比为0.5,反应温度为250℃,反应时间为16h。将0.5g上述实施例1-6中的催化剂、0.25gdmf和5g正庚烷加入带搅拌的高压反应釜中,并充入4.0mpa稀乙烯(15(v)%)。采用程序升温加热套升至预设温度,并采用磁力搅拌然后搅拌。在250℃条件下反应16h,将反应液气相分析计算dmf转化率和px选择性,见表1。
[0061]
表1实施例7-12的催化评价结果
[0062][0063]
实施例13
[0064]
本实施例采用正庚烷为反应溶剂,正庚烷与dmf质量比为15,dmf与作为催化剂的含磷和钴的复合材料质量比为0.8,反应温度为240℃,反应时间为24h。将0.5g上述实施例1中的催化剂、0.4gdmf和6.0g正庚烷加入带搅拌的高压反应釜中,并充入4.0mpa稀乙烯(15(v)%)。采用程序升温加热套升至预设温度,并采用磁力搅拌然后搅拌。在240℃条件下反应24h,将反应液气相分析计算dmf转化率为92%,px选择性为96%。
[0065]
实施例14
[0066]
本实施例采用正庚烷为反应溶剂,正庚烷与dmf质量比为30,dmf与作为催化剂的含磷和钴的复合材料质量比为0.3,反应温度为220℃,反应时间为12h。将0.5g上述实施例1中的催化剂、0.15gdmf和4.5g正庚烷加入带搅拌的高压反应釜中,并充入2.0mpa稀乙烯(15(v)%)。采用程序升温加热套升至预设温度,并采用磁力搅拌然后搅拌。在220℃条件下反
应12h,将反应液气相分析计算dmf转化率》99%,px选择性为95%。
[0067]
实施例15
[0068]
本实施例采用正己烷为反应溶剂,正己烷与dmf质量比为40,dmf与作为催化剂的含磷和钴的复合材料质量比为1.2,反应温度为260℃,反应时间为20h。将0.5g上述实施例1中的催化剂、0.6gdmf和24.0g正己烷加入带搅拌的高压反应釜中,并充入4.0mpa稀乙烯(15(v)%)。采用程序升温加热套升至预设温度,并采用磁力搅拌然后搅拌。在260℃条件下反应20h,将反应液气相分析计算dmf转化率为89%,px选择性为97%。
[0069]
实施例16
[0070]
本实施例采用正辛烷为反应溶剂,正辛烷与dmf质量比为20,dmf与作为催化剂的含磷和钴的复合材料质量比为0.7,反应温度为250℃,反应时间为12h。将0.5g上述实施例1中的催化剂、0.35gdmf和7.0g正辛烷加入带搅拌的高压反应釜中,并充入3.0mpa稀乙烯(15(v)%)。采用程序升温加热套升至预设温度,并采用磁力搅拌然后搅拌。在250℃条件下反应12h,将反应液气相分析计算dmf转化率为95%,px选择性为94%。
[0071]
实施例17
[0072]
本实施例采用四氢呋喃为反应溶剂,四氢呋喃与dmf质量比为10,dmf与作为催化剂的含磷和钴的复合材料质量比为1.5,反应温度为280℃,反应时间为20h。将0.5g上述实施例1中的催化剂、0.75gdmf和7.5g四氢呋喃加入带搅拌的高压反应釜中,并充入5.0mpa稀乙烯(15(v)%)。采用程序升温加热套升至预设温度,并采用磁力搅拌然后搅拌。在280℃条件下反应20h,将反应液气相分析计算dmf转化率为87%,px选择性为93%。
[0073]
实施例18
[0074]
本实施例采用四氢呋喃为反应溶剂,四氢呋喃与dmf质量比为20,dmf与作为催化剂的含磷和钴的复合材料质量比为1.0,反应温度为260℃,反应时间为12h。将0.5g上述实施例1中的催化剂、0.5gdmf和10.0g四氢呋喃加入带搅拌的高压反应釜中,并充入5.0mpa稀乙烯(15(v)%)。采用程序升温加热套升至预设温度,并采用磁力搅拌然后搅拌。在260℃条件下反应12h,将反应液气相分析计算dmf转化率为90%,px选择性为95%。
[0075]
实施例19
[0076]
本实施例采用四氢呋喃为反应溶剂,四氢呋喃与dmf质量比为30,dmf与作为催化剂的含磷和钴的复合材料质量比为0.5,反应温度为230℃,反应时间为12h。将0.5g上述实施例1中的催化剂、0.25gdmf和7.5g四氢呋喃加入带搅拌的高压反应釜中,并充入4.0mpa稀乙烯(15(v)%)。采用程序升温加热套升至预设温度,并采用磁力搅拌然后搅拌。在230℃条件下反应12h,将反应液气相分析计算dmf转化率为98%,px选择性为95%。
[0077]
实施例20
[0078]
本实施例采用环己烷为反应溶剂,环己烷与dmf质量比为25,dmf与作为催化剂的含磷和钴的复合材料质量比为0.6,反应温度为250℃,反应时间为16h。将0.5g上述实施例1中的催化剂、0.3gdmf和7.5g环己烷加入带搅拌的高压反应釜中,并充入3.0mpa稀乙烯(15(v)%)。采用程序升温加热套升至预设温度,并采用磁力搅拌然后搅拌。在250℃条件下反应16h,将反应液气相分析计算dmf转化率为92%,px选择性为95%。
[0079]
为更直观的描述上述实施例13-20的反应条件和结果,将各项参数及结果列于表2中。
[0080]
表2实施例13-20催化性能结果
[0081][0082]
实施例21
[0083]
采用正庚烷为反应溶剂,正庚烷与dmf质量比为20,dmf与催化剂质量比为0.5,反应温度为250℃,反应时间为16h。将0.5g上述实施例1中的催化剂、0.25gdmf和5g正庚烷加入带搅拌的高压反应釜中,并充入4.0mpa稀乙烯(15(v)%)。采用程序升温加热套升至预设温度,并采用磁力搅拌然后搅拌。在250℃条件下反应16h,将反应液气相分析计算dmf转化率和px选择性。将使用后的催化剂经洗涤后烘干后投入下一个反应,共循环4次反应,结果如图5所示。结果显示,4次反应后dmf转化率保持在90%以上,px选择性保持在97%,说明本发明催化剂具有良好的循环稳定性。
[0084]
对比例1(商业磷酸钴)
[0085]
采用商业磷酸钴(ii)co3(po4)2为催化剂(均为co
2
),正庚烷为反应溶剂,正庚烷与dmf质量比为20,dmf与催化剂质量比为0.5,反应温度为250℃,反应时间为16h。将0.5g商业磷酸钴催化剂(ii)、0.25gdmf和5g正庚烷加入带搅拌的高压反应釜中,并充入4.0mpa稀乙烯(15(v)%)。采用程序升温加热套升至预设温度,并采用磁力搅拌然后搅拌。在250℃条件下反应16h,将反应液气相分析计算dmf转化率为72%,px选择性仅为75%。
[0086]
对比例2
[0087]
采用cn108946692a中描述的方法,制备得到了磷酸钴纳米材料,具体步骤如下:将钴源、表面活性剂聚乙烯吡咯烷酮(pvp,分子量为27000-40000)和水混合,搅拌2h。混合均匀后加入磷源水溶液,配比为co(no3)2:pvp:h2o:(nh4)3po4=2.5:1:6:0.85,并再次搅拌4h,形成初始凝胶混合物,将初始凝胶混合物密封于30ml的聚四氟乙烯内衬的水热反应釜中,放入箱式电阻炉中,在200℃晶化6小时后,经过滤、清洗、干燥,得到紫色片状磷酸钴纳米材料。其化学式为co3(oh)2(hpo4)2。
[0088]
本对比例采用正庚烷为反应溶剂,正庚烷与dmf质量比为15,dmf与上述磷酸钴纳米材料质量比为0.8,反应温度为240℃,反应时间为24h。将0.5g上述对比例2中的磷酸钴纳米材料、0.4gdmf和6.0g正庚烷加入带搅拌的高压反应釜中,并充入4.0mpa稀乙烯(15
(v)%)。采用程序升温加热套升至预设温度,并采用磁力搅拌然后搅拌。在240℃条件下反应24h,将反应液气相分析计算dmf转化率为65%,px选择性为83%。
[0089]
以上详细描述了本发明的具体实施方式,但是,本发明并不限于此。在本发明的技术构思范围内,可以对本发明的技术方案进行多种简单变型,包括各个技术特征以任何其它的合适方式进行组合,这些简单变型和组合同样应当视为本发明所公开的内容,均属于本发明的保护范围。
再多了解一些
本文用于创业者技术爱好者查询,仅供学习研究,如用于商业用途,请联系技术所有人。