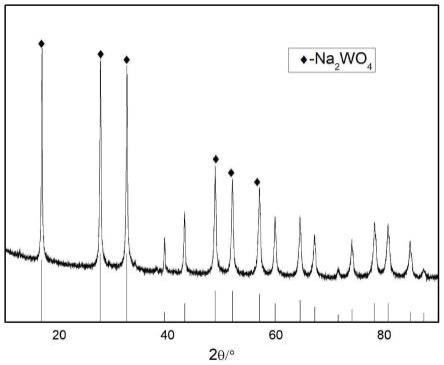
1.本发明涉及钨矿提取技术领域,尤其涉及一种从钨酸钠碱压煮液回收氢氧化钠的方法。
背景技术:
2.目前,赣南地区钨冶炼主要以碱压煮工艺为主,为保证浸出效果,使用的碱液通常需过量1~3倍,此方法导致经碱压煮工艺所得钨酸钠溶液中氢氧化钠含量大大增加,甚至所得钨酸钠溶液中氢氧化钠溶液含量达到与钨酸钠溶液含量相同。而钨酸钠碱压煮液中的氢氧化钠,经离子交换后,将进入交后液外排,在一定程度上造成了资源的浪费,并增加了冶炼成本。
3.目前,钨冶炼上回收钨酸钠碱压煮液中氢氧化钠的方法主要为浓缩结晶法,其原理是对钨酸钠压煮液进行蒸发浓缩,将溶液中的水以水蒸气的形式除去,进而提高溶液中钨酸钠的浓度,使其达到过饱和,最终实现钨酸钠与氢氧化钠分离,所得钨酸钠晶体中wo3含量为50~60wt%,氢氧化钠含量为7~10wt%。然而,虽然浓缩结晶法能在一定程度上实现氢氧化钠与钨酸钠的分离,但其本质为将溶液中的水转化为水蒸气去除,溶液体积一般会浓缩至原溶液的1/3,从浓缩液中分离回收氢氧化钠所消耗的蒸汽能耗较大。
技术实现要素:
4.本发明的目的在于提供一种从钨酸钠碱压煮液回收氢氧化钠的方法,能有效降低能耗,且提高钨酸钠晶体纯度。
5.为了实现上述发明目的,本发明提供以下技术方案:
6.本发明提供了一种从钨酸钠碱压煮液回收氢氧化钠的方法,包括以下步骤:
7.将钨酸钠碱压煮液和固态氢氧化钠混合,进行溶解,得到混合液;
8.将所述混合液与钨酸钠晶种混合,进行结晶后,分离,得到钨酸钠晶体和含氢氧化钠溶液;
9.所述钨酸钠碱压煮液为钨冶炼氢氧化钠压煮所得钨酸钠-氢氧化钠混合溶液。
10.优选的,所述钨酸钠碱压煮液中wo3浓度为120~200g/l,naoh与wo3的浓度比>1:10。
11.优选的,所述混合液中naoh的浓度为240~480g/l。
12.优选的,所述溶解的温度为80~100℃。
13.优选的,所述钨酸钠晶种中wo3与混合液中wo3的质量比≤1:30。
14.优选的,所述结晶的温度为-20~30℃,时间为6~18h。
15.优选的,所述钨酸钠晶体中钨酸钠的含量>60wt%。
16.优选的,所述含氢氧化钠溶液中wo3浓度≤30g/l,naoh浓度>200g/l。
17.本发明提供了一种从钨酸钠碱压煮液回收氢氧化钠的方法,本发明利用同离子效应,向钨酸钠压煮液中加入固体氢氧化钠,利用钠离子的同离子效应,将体系中的钨酸钠优
先析出,然后利用钨酸钠晶种结晶析出并分离钨酸钠晶体,从而回收氢氧化钠。与传统蒸发浓缩分离氢氧化钠与钨酸钠的工艺相比,无需蒸发体系内水分,极大减少了能耗成本,且无需蒸发,因而结晶分离前后体系体积变化不大,结晶过程中压煮液中的杂质将大部分留在溶液中,杂质浓度不会像浓缩结晶工艺一样升高,所得钨酸钠晶体杂质含量更低,有助于后续冶炼工艺。实施例的结果表明,本发明提供的方法能有效将钨酸钠与氢氧化钠进行分离,以原始钨酸钠碱压煮液计算,氢氧化钠回收率>80%,分离所得钨酸钠晶体的含量>60wt%,钨酸钠回收率>90%,同时保证了高氢氧化钠回收率和钨酸钠回收率。
18.本发明方法所得钨酸钠晶体为na2wo4或na2wo4与na2wo4·
2h2o混合物,可直接溶解后进行钨冶炼工艺中后续的离子交换或结晶等操作,不会对钨冶炼体系造成较大影响;本发明方法所得含氢氧化钠溶液为高含量的氢氧化钠溶液,可返回压煮工序中作为原料。
附图说明
19.图1为实施例1制备的钨酸钠晶体的xrd图;
20.图2为实施例1制备的钨酸钠晶体的检测报告;
21.图3为实施例3制备的钨酸钠晶体的xrd图;
22.图4为实施例3制备的钨酸钠晶体的检测报告。
具体实施方式
23.本发明提供了一种从钨酸钠碱压煮液回收氢氧化钠的方法,包括以下步骤:
24.将钨酸钠碱压煮液和固态氢氧化钠混合,进行溶解,得到混合液;
25.将所述混合液与钨酸钠晶种混合,进行结晶后,分离,得到钨酸钠晶体和含氢氧化钠溶液;
26.所述钨酸钠碱压煮液为钨冶炼氢氧化钠压煮所得钨酸钠-氢氧化钠混合溶液。
27.在本发明中,若无特殊说明,所需原料或试剂均为本领域技术人员熟知的市售商品。
28.本发明将钨酸钠碱压煮液和固态氢氧化钠混合,进行溶解,得到混合液。
29.在本发明中,所述钨酸钠碱压煮液为钨冶炼氢氧化钠压煮所得钨酸钠-氢氧化钠混合溶液;本发明对所述钨酸钠碱压煮液的来源和获取方式没有特殊的限定,按照本领域熟知的方式获取即可。
30.在本发明中,以wo3表示钨酸钠的浓度,所述钨酸钠碱压煮液中wo3浓度优选为120~200g/l,更优选为124.7~193.7g/l,进一步优选为151.6~~154.0g/l,再进一步优选为153.7g/l,naoh与wo3的浓度比优选>1:10,更优选为(2.2~10):10,进一步优选为(6.7~7.7):10;本发明对所述钨酸钠碱压煮液中naoh的浓度没有特殊的限定,依据具体矿物成分所对应的naoh量即可;本发明所用钨酸钠碱压煮液中naoh浓度优选为44.3~155.3g/l,更优选为83.5~140.7g/l,进一步优选为117.9g/l。
31.本发明对所述钨酸钠碱压煮液和固态氢氧化钠混合的过程没有特殊的限定,按照本领域熟知的过程将物料混合均匀即可。
32.在本发明中,所述溶解的温度优选为80~100℃,更优选为85~95℃,进一步优选为90℃;所述混合液中naoh的浓度优选为240~480g/l,更优选为240~440g/l,进一步优选
为320~400g/l。
33.得到混合液后,本发明将所述混合液与钨酸钠晶种混合,进行结晶后,分离,得到钨酸钠晶体和含氢氧化钠溶液。
34.本发明对所述混合液与钨酸钠晶种混合的过程没有特殊的限定,按照本领域熟知的过程进行即可。
35.在本发明中,所述钨酸钠晶种中wo3与混合液中wo3的质量比优选≤1:30。
36.在本发明中,所述结晶的温度优选为-20~30℃,更优选为0~20℃,进一步优选为10℃;时间优选为6~18h,更优选为9~16h,进一步优选为10h;所述结晶优选在静置条件下进行。
37.完成所述结晶后,本发明优选将所得产物分离,将所得固体干燥,得到钨酸钠晶体;所得溶液即为含氢氧化钠溶液;所述分离的方式优选为固液分离;本发明对所述干燥的过程没有特殊的限定,按照本领域熟知的过程进行即可。
38.在本发明中,所述钨酸钠晶体中钨酸钠的含量>60wt%,更优选为63~67wt%。
39.在本发明中,所述含氢氧化钠溶液中wo3浓度优选≤30g/l,更优选为1.78g/l~14.08g/l,进一步优选为2.30g/l~6.32g/l;naoh浓度优选>200g/l,更优选为264.34g/l~429.15g/l,进一步优选为338.49g/l~427.23g/l。
40.下面将结合本发明中的实施例,对本发明中的技术方案进行清楚、完整地描述。显然,所描述的实施例仅仅是本发明一部分实施例,而不是全部的实施例。基于本发明中的实施例,本领域普通技术人员在没有做出创造性劳动前提下所获得的所有其他实施例,都属于本发明保护的范围。
41.实施例1
42.取1l钨酸钠碱压煮液,其中wo3浓度为154.0g/l,氢氧化钠浓度为140.7g/l,在80℃向其中加入固体氢氧化钠,使氢氧化钠浓度为240g/l,待氢氧化钠全部溶解以后,向所得混合液中加入钨酸钠晶种,加入的钨酸钠晶种中wo3质量与混合液中wo3质量比为1:30,将所得溶液置入10℃环境温度中进行结晶,静置10h后,固液分离,将所得固体烘干后,得到215.3g钨酸钠晶体和含氢氧化钠溶液,其中,钨酸钠晶体中wo3含量为65.64%;含氢氧化钠溶液中氢氧化钠含量为264.34g/l、wo3含量为14.08g/l;计算可得钨酸钠回收率为91.77%;
43.将所述钨酸钠晶体溶解在1l水中,所得溶液中氢氧化钠浓度为2.03g/l,计算可知,氢氧化钠回收率为98.56%(以原始钨酸钠碱压煮液计算),氢氧化钠的综合回收率为99.15%(以钨酸钠碱压煮液中加入固体氢氧化钠后的溶液计算)。
44.实施例2
45.取2l钨酸钠碱压煮液,其中wo3浓度为124.7g/l,氢氧化钠浓度为83.5g/l,在95℃向其中加入固体氢氧化钠,使氢氧化钠溶度为440g/l,待氢氧化钠全部溶解以后,向所得混合液中加入钨酸钠晶种(加入的钨酸钠晶种中wo3质量与混合液中wo3质量比为1:30),随后置入20℃的环境温度中进行结晶,静置16h后,固液分离,将所得固体烘干后,得到384.8g钨酸钠晶体和含氢氧化钠溶液,其中,钨酸钠晶体中wo3含量为63.74%;含氢氧化钠溶液中氢氧化钠含量为427.23g/l、wo3含量为2.30g/l;计算可得钨酸钠回收率为98.34%;
46.将所述钨酸钠晶体溶解在2l水中,溶液中氢氧化钠浓度为12.77g/l,计算可知,氢
氧化钠回收率为84.70%(以原始钨酸钠碱压煮液计算),氢氧化钠的综合回收率为97.10%(以钨酸钠碱压煮液中加入固体氢氧化钠后的溶液计算)。
47.实施例3
48.取2l钨酸钠碱压煮液,其中wo3浓度为151.6g/l,氢氧化钠浓度为155.3g/l,在85℃向其中加入固体氢氧化钠,使氢氧化钠浓度为400g/l,待氢氧化钠全部溶解以后,向所得混合液中加入钨酸钠晶种(加入的钨酸钠晶种中wo3质量与混合液中wo3质量比为1:30),随后置入0℃的环境温度中进行结晶,静置18h后,固液分离,将所得固体烘干后,得到470.8g钨酸钠晶体和含氢氧化钠溶液,其中,钨酸钠晶体中wo3含量为63.74%;含氢氧化钠溶液中氢氧化钠含量为429.15g/l、wo3含量为1.78g/l;计算可得钨酸钠回收率为98.97%;
49.将所述钨酸钠晶体溶解在2l水中,溶液中氢氧化钠浓度为13.76g/l,计算可知,氢氧化钠回收率为91.14%(以原始钨酸钠碱压煮液计算),氢氧化钠的综合回收率为96.56%(以钨酸钠碱压煮液中加入固体氢氧化钠后的溶液计算)。
50.实施例4
51.取1l钨酸钠碱压煮液,其中wo3浓度为153.7g/l,氢氧化钠浓度为117.9g/l,在90℃向其中加入固体氢氧化钠,使氢氧化钠浓度为320g/l,待氢氧化钠全部溶解以后,向所得混合液中加入钨酸钠晶种(加入的钨酸钠晶种中wo3质量与混合液中wo3质量比为1:30),随后置入-20℃的环境温度中进行结晶,静置10h后,固液分离,将所得固体烘干后,得到279.7g钨酸钠晶体和含氢氧化钠溶液,其中,钨酸钠晶体中wo3含量为64.11%;含氢氧化钠溶液中氢氧化钠含量为338.49g/l、wo3含量为6.32g/l;计算可得钨酸钠回收率为96.30%;
52.将所述钨酸钠晶体溶解在1l水中,溶液中氢氧化钠浓度为15.36g/l,计算可知,氢氧化钠回收率为86.97%(以原始钨酸钠碱压煮液计算),氢氧化钠的综合回收率为95.20%(以钨酸钠碱压煮液中加入固体氢氧化钠后的溶液计算)。
53.实施例5
54.取1l钨酸钠碱压煮液,其中wo3浓度为193.7g/l,氢氧化钠浓度为44.3g/l,在95℃向其中加入固体氢氧化钠,使氢氧化钠浓度为360g/l,待氢氧化钠全部溶解以后,向所得混合液中加入钨酸钠晶种(加入的钨酸钠晶种中wo3质量与原溶液wo3质量比值为1:30),随后置入10℃的环境温度中进行结晶,静置9h后,固液分离,将所得固体烘干后,得到281.7g钨酸钠晶体和含氢氧化钠溶液,其中,钨酸钠晶体中wo3含量为66.7%;含氢氧化钠溶液中氢氧化钠含量为393.58g/l、wo3含量为6.46g/l;计算可得钨酸钠回收率为97.00%;
55.将所述钨酸钠晶体溶解在1l水中,溶液中氢氧化钠浓度为5.78g/l,计算可知,氢氧化钠回收率为86.95%(以原始钨酸钠碱压煮液计算),氢氧化钠的综合回收率为98.39%(以钨酸钠碱压煮液中加入固体氢氧化钠后的溶液计算)。
56.表征及检测
57.1)对实施例1和实施例3制备的钨酸钠晶体进行xrd表征,结果见图1和图3,图1和图3中底部线条为钨酸钠标准卡片;从图1和图3可知,实施例1和实施例3制备的钨酸钠晶体的xrd检测结果与钨酸钠标准卡片的峰一一对应。
58.2)对实施例1和实施例3制备的钨酸钠晶体进行杂质检测,结果分别如图2和图4所示;图2中xrd图谱为图1,图4中xrd图谱为图3;
59.图2和图4表明,实施例1所得钨酸钠晶体中wo3含量为65.64%,实施例3所得钨酸
钠晶体中wo3含量为63.74%,均高于60%,钨冶炼中较难分离的杂质mo,经过本发明方法处理后符合分析纯(ar)级钨酸钠要求(q/12hg 6508-2016)与apt-1标准(gb/t 10116-88),充分表明了本发明所得的钨酸钠晶体的纯度较高。
60.现有技术(钨冶金学,李洪桂著)第76页第二段记载了:对于wo3与naoh质量比为1:1左右的碱分解母液,所得na2wo3晶体中含有naoh7~10wt%,含有wo350~60wt%。因此,与该现有技术相比,本技术的方法能够得到更高纯度的钨酸钠晶体(含量高于60wt%)。
61.以上所述仅是本发明的优选实施方式,应当指出,对于本技术领域的普通技术人员来说,在不脱离本发明原理的前提下,还可以做出若干改进和润饰,这些改进和润饰也应视为本发明的保护范围。
再多了解一些
本文用于创业者技术爱好者查询,仅供学习研究,如用于商业用途,请联系技术所有人。