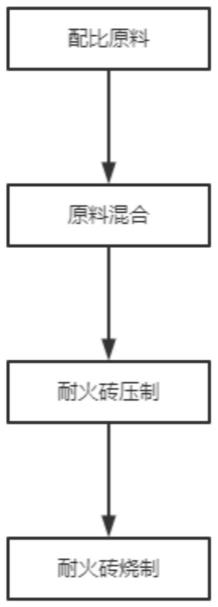
1.本发明涉及耐火砖制备技术领域,具体是涉及石膏制硫酸用回转窑抗结圈的环保型耐火砖的生产方法。
背景技术:
2.耐火材料一般分为两种,即不定型耐火材料和定型耐火材料。不定型耐火材料也叫浇注料,是由多种骨料或集料和一种或多种粘和剂组成的混合粉状颗料,使用时必须和一种或多种液体配合搅拌均匀,具有较强的流动性。定型耐火材料一般指耐火砖,其形状有标准规则,也可以根据需要筑切时临时加工。
3.回转窑结圈,是回转窑内高温带内壁发生的炉料环状粘附现象。轻微的粘附现象称为窑皮,如果发生粘附,影响炉子正常操作时,即谓结圈。
4.现有的耐火砖在防止回转窑结圈上多采用涂抹防结圈涂层,采用这种方式需要定期维护,且效果不佳,结圈原因也多有不同,有因为耐火砖表面粗糙度增加,使物料在窑壁堆积,有因为物料与窑壁温差较大,形成粘壁结圈,现有的耐火砖用于石膏制硫酸的回转窑效果并不理性,多有结圈。
技术实现要素:
5.为解决上述技术问题,本发明提供了石膏制硫酸用回转窑抗结圈的环保型耐火砖的生产方法。
6.本发明的技术方案是:石膏制硫酸用回转窑抗结圈的环保型耐火砖的生产方法,包括以下步骤:
7.s1、配比原料:
8.按以下重量份的成分配制原料:50-70份骨料、21-31份粉料、12-17份结合剂;
9.所述骨料由以下重量份的成分组成:10-13份轻烧白云石、15-21份菱镁矿石、7-11份铬铁矿石、18-25份粘土熟料;
10.所述粉料由以下重量份的成分组成:7-8份氧化镧、5-7份氧化铍、8-13份硅线石粉、1-3份钛酸铝;
11.所述结合剂由以下重量份的成分组成:3-5份轻烧高铝铝土矿粉、7-8份粘土、2-4份磷酸镁胶结材料。
12.s2、原料混合:将骨料中各成分按上述重量份放入混料机中混合均匀,得到骨料混合物,在将粉料中各成分按上述重量份放入混料机中混合均匀,得到粉料混合物,将结合剂中各成分按上述重量份放入混料机中混合均匀,得到结合剂混合物,对结合剂中加水,制备成混合浆液,加水量为骨料重量的3-5%,再将骨料混合物和混合浆液导入混料机中搅拌30-40min,然后将粉料混合物分两批次加入混料机中,粉料混合物每次加入后混料机搅拌时长为40-50min,粉料混合完成后得到耐火砖泥料;
13.s3、耐火砖压制:
14.将耐火泥料导入耐火砖压制模具中,在模具底部铺设陶瓷底板,再将装有泥料的模具放在等静压机中经100-180mpa的压力成型,得到砖型坯料,再对砖型坯料上表面喷涂耐火涂层,然后将喷涂完耐火涂层砖型坯料进行表面烘干处理,表面烘干处理完成后得到待烧砖坯;
15.s4、耐火砖烧制:
16.将待烧砖坯放入高温炉中,在氩气保护气氛下以3-5℃的升温速率将高温炉内的温度升至900-1000℃,恒温保持10-20min,在以5-7℃的升温速率将高温炉内的温度升至1400-1580℃,恒温保持1-2h,再以4-6℃的降温速率将高温炉内温度降至500-600℃,恒温保持1-1.5h,然后随炉自然冷却至室温后取出耐火砖;
17.进一步地,所述骨料中轻烧白云石的粒度为0.1-0.8mm、菱镁矿石的粒度为0.2-0.7mm、铬铁矿石的粒度为0.08-0.12mm、粘土熟料的粒度为0.8-2mm,骨料的粒度适中,不容易开裂,抗压强度高。
18.进一步地,所述粉料中氧化镧的粒度为23-43μm、氧化铍的粒度35-80μm、硅线石粉的粒度45-60μm、钛酸铝的粒度为1-5μm,这样的粉料粒度能够使泥料的表面光滑。
19.进一步地,所述结合剂中轻烧高铝铝土矿粉的粒度为3-8μm、粘土粒度为7-12μm,粘土和轻烧高铝铝土矿粉作为结合剂能够有效提高骨料和粉料的粘合效果,增强耐火砖的抗压强度。
20.进一步地,所述步骤s2中混料机的速度均为120-180r/min,混料温度为50-80℃,这种混料温度能够避免各成分因为空气中的水分而发生结块,而导致的混料不均匀情况。
21.进一步地,所述耐火涂层由粒度为10-20μm的氧化锆、氧化钛、氧化钇、水按质量比1:1:1:3混合配制而成,这种耐火涂层具有抗腐蚀能力,进一步降低耐火砖表面的粗糙度,使回转窑内结圈物质不容易附着粘结。
22.进一步地,所述步骤s3中的表面烘干处理是通过热风烘干,所述热风的风速为2.5m/s,热风温度为70-80℃,热风烘干时长为30-40min,烘干效率高。
23.进一步地,所述步骤s4中先对高温炉进行抽真空处理,抽至真空度为5-10pa,后通入氩气至高温炉内103-110kpa,随着炉温升高,炉内压强大于炉外压强,使各成分之间的粘结更紧固。
24.进一步地,所述骨料中铬铁矿石的碳含量≤0.06%,碳含量过高容易在高温下产生二氧化碳货一氧化碳气体,导致耐火砖内部有气孔,降低耐火砖的使用寿命。
25.进一步地,所述砖型坯料喷涂耐火涂层过程是将放置有砖型坯料的陶瓷底板置于传送带上使砖型坯料经过耐火涂层喷嘴从砖型坯料上方进行喷涂,喷嘴喷射方向与砖型坯料上表面垂直,喷嘴喷出量为16-25g/s,传送带移动速度为20-25cm/s,这样的喷涂方式,喷涂的效率高。
26.本发明的有益效果是:
27.本发明所制备的耐火砖砖用于石膏制硫酸的回转窑中具有很强的抗腐蚀性能,耐火砖的抗冲刷,抗压强度较高,表面粗糙度较低,能够避免回转窑在旋转过程中耐火砖表面因冲击而脱落,耐火砖表面粗糙度低且抗腐蚀能力强,降低了物料在回转窑内壁的摩擦力,进而能够有效避免物料因摩擦力大附着在耐火砖上而造成物料堆积结圈的现象,耐火砖表面的耐火涂层具有良好的导热能力,能够有效避免因物料与窑壁温差而导致的结圈现象。
附图说明
28.图1是本发明的耐火砖的制备流程图。
具体实施方式
29.实施例1:
30.如图1所示,石膏制硫酸用回转窑抗结圈的环保型耐火砖的生产方法,包括以下步骤:
31.s1、配比原料:
32.按以下重量份的成分配制原料:50份骨料、21份粉料、12份结合剂;
33.所述骨料由以下重量份的成分组成:10份轻烧白云石、15份菱镁矿石、7份铬铁矿石、18份粘土熟料;
34.所述粉料由以下重量份的成分组成:7份氧化镧、5份氧化铍、8份硅线石粉、1份钛酸铝;
35.所述结合剂由以下重量份的成分组成:3份轻烧高铝铝土矿粉、7份粘土、2份磷酸镁胶结材料。
36.s2、原料混合:将骨料中各成分按上述重量份放入混料机中混合均匀,得到骨料混合物,在将粉料中各成分按上述重量份放入混料机中混合均匀,得到粉料混合物,将结合剂中各成分按上述重量份放入混料机中混合均匀,得到结合剂混合物,对结合剂中加水,制备成混合浆液,加水量为骨料重量的3-5%,再将骨料混合物和混合浆液导入混料机中搅拌30min,然后将粉料混合物分两批次加入混料机中,粉料混合物每次加入后混料机搅拌时长为40min,粉料混合完成后得到耐火砖泥料;
37.s3、耐火砖压制:
38.将耐火泥料导入耐火砖压制模具中,在模具底部铺设陶瓷底板,再将装有泥料的模具放在等静压机中经100mpa的压力成型,得到砖型坯料,再对砖型坯料上表面喷涂耐火涂层,然后将喷涂完耐火涂层砖型坯料进行表面烘干处理,表面烘干处理完成后得到待烧砖坯;
39.s4、耐火砖烧制:
40.将待烧砖坯放入高温炉中,在氩气保护气氛下以3℃的升温速率将高温炉内的温度升至900℃,恒温保持10min,在以5-7℃的升温速率将高温炉内的温度升至1400℃,恒温保持1h,再以4℃的降温速率将高温炉内温度降至500℃,恒温保持1h,然后随炉自然冷却至室温后取出耐火砖;
41.所述骨料中轻烧白云石的粒度为0.1-0.8mm、菱镁矿石的粒度为0.2-0.7mm、铬铁矿石的粒度为0.08-0.12mm、粘土熟料的粒度为0.8-2mm,骨料的粒度适中,不容易开裂,抗压强度高。
42.所述粉料中氧化镧的粒度为23-43μm、氧化铍的粒度35-80μm、硅线石粉的粒度45-60μm、钛酸铝的粒度为1-5μm,这样的粉料粒度能够使泥料的表面光滑。
43.所述结合剂中轻烧高铝铝土矿粉的粒度为3-8μm、粘土粒度为7-12μm,粘土和轻烧高铝铝土矿粉作为结合剂能够有效提高骨料和粉料的粘合效果,增强耐火砖的抗压强度。
44.所述步骤s2中混料机的速度均为120r/min,混料温度为50℃,这种混料温度能够
避免各成分因为空气中的水分而发生结块,而导致的混料不均匀情况。
45.所述耐火涂层由粒度为10-20μm的氧化锆、氧化钛、氧化钇、水按质量比1:1:1:3混合配制而成,这种耐火涂层具有抗腐蚀能力,进一步降低耐火砖表面的粗糙度,使回转窑内结圈物质不容易附着粘结。
46.所述步骤s3中的表面烘干处理是通过热风烘干,所述热风的风速为2.5m/s,热风温度为70℃,热风烘干时长为30min,烘干效率高。
47.所述步骤s4中先对高温炉进行抽真空处理,抽至真空度为5pa,后通入氩气至高温炉内103kpa,随着炉温升高,炉内压强大于炉外压强,使各成分之间的粘结更紧固。
48.所述骨料中铬铁矿石的碳含量为0.06%,碳含量过高容易在高温下产生二氧化碳货一氧化碳气体,导致耐火砖内部有气孔,降低耐火砖的使用寿命。
49.所述砖型坯料喷涂耐火涂层过程是将放置有砖型坯料的陶瓷底板置于传送带上使砖型坯料经过耐火涂层喷嘴从砖型坯料上方进行喷涂,喷嘴喷射方向与砖型坯料上表面垂直,喷嘴喷出量为16g/s,传送带移动速度为20cm/s,这样的喷涂方式,喷涂的效率高。
50.实施例2:
51.如图1所示,石膏制硫酸用回转窑抗结圈的环保型耐火砖的生产方法,包括以下步骤:
52.s1、配比原料:
53.按以下重量份的成分配制原料:59份骨料、25.5份粉料、14.5份结合剂;
54.所述骨料由以下重量份的成分组成:12份轻烧白云石、18份菱镁矿石、9份铬铁矿石、20份粘土熟料;
55.所述粉料由以下重量份的成分组成:7.5份氧化镧、6份氧化铍、10份硅线石粉、2份钛酸铝;
56.所述结合剂由以下重量份的成分组成:4份轻烧高铝铝土矿粉、7.5份粘土、3份磷酸镁胶结材料。
57.s2、原料混合:将骨料中各成分按上述重量份放入混料机中混合均匀,得到骨料混合物,在将粉料中各成分按上述重量份放入混料机中混合均匀,得到粉料混合物,将结合剂中各成分按上述重量份放入混料机中混合均匀,得到结合剂混合物,对结合剂中加水,制备成混合浆液,加水量为骨料重量的4%,再将骨料混合物和混合浆液导入混料机中搅拌35min,然后将粉料混合物分两批次加入混料机中,粉料混合物每次加入后混料机搅拌时长为45min,粉料混合完成后得到耐火砖泥料;
58.s3、耐火砖压制:
59.将耐火泥料导入耐火砖压制模具中,在模具底部铺设陶瓷底板,再将装有泥料的模具放在等静压机中经150mpa的压力成型,得到砖型坯料,再对砖型坯料上表面喷涂耐火涂层,然后将喷涂完耐火涂层砖型坯料进行表面烘干处理,表面烘干处理完成后得到待烧砖坯;
60.s4、耐火砖烧制:
61.将待烧砖坯放入高温炉中,在氩气保护气氛下以4℃的升温速率将高温炉内的温度升至950℃,恒温保持15min,在以6℃的升温速率将高温炉内的温度升至1500℃,恒温保持1.5h,再以5℃的降温速率将高温炉内温度降至550℃,恒温保持1.3h,然后随炉自然冷却
至室温后取出耐火砖;
62.所述骨料中轻烧白云石的粒度为0.1-0.8mm、菱镁矿石的粒度为0.2-0.7mm、铬铁矿石的粒度为0.08-0.12mm、粘土熟料的粒度为0.8-2mm,骨料的粒度适中,不容易开裂,抗压强度高。
63.所述粉料中氧化镧的粒度为23-43μm、氧化铍的粒度35-80μm、硅线石粉的粒度45-60μm钛酸铝的粒度为1-5μm,这样的粉料粒度能够使泥料的表面光滑。
64.所述结合剂中轻烧高铝铝土矿粉的粒度为3-8μm、粘土粒度为7-12μm,粘土和轻烧高铝铝土矿粉作为结合剂能够有效提高骨料和粉料的粘合效果,增强耐火砖的抗压强度。
65.所述步骤s2中混料机的速度均为150r/min,混料温度为60℃,这种混料温度能够避免各成分因为空气中的水分而发生结块,而导致的混料不均匀情况。
66.所述耐火涂层由粒度为10-20μm的氧化锆、氧化钛、氧化钇、水按质量比1:1:1:3混合配制而成,这种耐火涂层具有抗腐蚀能力,进一步降低耐火砖表面的粗糙度,使回转窑内结圈物质不容易附着粘结。
67.所述步骤s3中的表面烘干处理是通过热风烘干,所述热风的风速为2.5m/s,热风温度为75℃,热风烘干时长为35min,烘干效率高。
68.所述步骤s4中先对高温炉进行抽真空处理,抽至真空度为7pa,后通入氩气至高温炉内108kpa,随着炉温升高,炉内压强大于炉外压强,使各成分之间的粘结更紧固。
69.所述骨料中铬铁矿石的碳含量为0.05%,碳含量过高容易在高温下产生二氧化碳货一氧化碳气体,导致耐火砖内部有气孔,降低耐火砖的使用寿命。
70.所述砖型坯料喷涂耐火涂层过程是将放置有砖型坯料的陶瓷底板置于传送带上使砖型坯料经过耐火涂层喷嘴从砖型坯料上方进行喷涂,喷嘴喷射方向与砖型坯料上表面垂直,喷嘴喷出量为20g/s,传送带移动速度为23cm/s,这样的喷涂方式,喷涂的效率高。
71.实施例3:
72.如图1所示,石膏制硫酸用回转窑抗结圈的环保型耐火砖的生产方法,包括以下步骤:
73.s1、配比原料:
74.按以下重量份的成分配制原料:70份骨料、31份粉料、17份结合剂;
75.所述骨料由以下重量份的成分组成:13份轻烧白云石、21份菱镁矿石、11份铬铁矿石、25份粘土熟料;
76.所述粉料由以下重量份的成分组成:8份氧化镧、7份氧化铍、13份硅线石粉、3份钛酸铝;
77.所述结合剂由以下重量份的成分组成:5份轻烧高铝铝土矿粉、8份粘土、4份磷酸镁胶结材料。
78.s2、原料混合:将骨料中各成分按上述重量份放入混料机中混合均匀,得到骨料混合物,在将粉料中各成分按上述重量份放入混料机中混合均匀,得到粉料混合物,将结合剂中各成分按上述重量份放入混料机中混合均匀,得到结合剂混合物,对结合剂中加水,制备成混合浆液,加水量为骨料重量的5%,再将骨料混合物和混合浆液导入混料机中搅拌40min,然后将粉料混合物分两批次加入混料机中,粉料混合物每次加入后混料机搅拌时长为50min,粉料混合完成后得到耐火砖泥料;
79.s3、耐火砖压制:
80.将耐火泥料导入耐火砖压制模具中,在模具底部铺设陶瓷底板,再将装有泥料的模具放在等静压机中经180mpa的压力成型,得到砖型坯料,再对砖型坯料上表面喷涂耐火涂层,然后将喷涂完耐火涂层砖型坯料进行表面烘干处理,表面烘干处理完成后得到待烧砖坯;
81.s4、耐火砖烧制:
82.将待烧砖坯放入高温炉中,在氩气保护气氛下以5℃的升温速率将高温炉内的温度升至1000℃,恒温保持20min,在以7℃的升温速率将高温炉内的温度升至1580℃,恒温保持2h,再以6℃的降温速率将高温炉内温度降至600℃,恒温保持1.5h,然后随炉自然冷却至室温后取出耐火砖;
83.所述骨料中轻烧白云石的粒度为0.1-0.8mm、菱镁矿石的粒度为0.2-0.7mm、铬铁矿石的粒度为0.08-0.12mm、粘土熟料的粒度为0.8-2mm,骨料的粒度适中,不容易开裂,抗压强度高。
84.所述粉料中氧化镧的粒度为23-43μm、氧化铍的粒度35-80μm、硅线石粉的粒度45-60μm、钛酸铝的粒度为1-5μm,这样的粉料粒度能够使泥料的表面光滑。
85.所述结合剂中轻烧高铝铝土矿粉的粒度为3-8μm、粘土粒度为7-12μm,粘土和轻烧高铝铝土矿粉作为结合剂能够有效提高骨料和粉料的粘合效果,增强耐火砖的抗压强度。
86.所述步骤s2中混料机的速度均为180r/min,混料温度为80℃,这种混料温度能够避免各成分因为空气中的水分而发生结块,而导致的混料不均匀情况。
87.所述耐火涂层由粒度为10-20μm的氧化锆、氧化钛、氧化钇、水按质量比1:1:1:3混合配制而成,这种耐火涂层具有抗腐蚀能力,进一步降低耐火砖表面的粗糙度,使回转窑内结圈物质不容易附着粘结。
88.所述步骤s3中的表面烘干处理是通过热风烘干,所述热风的风速为2.5m/s,热风温度为80℃,热风烘干时长为40min,烘干效率高。
89.所述步骤s4中先对高温炉进行抽真空处理,抽至真空度为10pa,后通入氩气至高温炉内110kpa,随着炉温升高,炉内压强大于炉外压强,使各成分之间的粘结更紧固。
90.所述骨料中铬铁矿石的碳含量为0.03%,碳含量过高容易在高温下产生二氧化碳货一氧化碳气体,导致耐火砖内部有气孔,降低耐火砖的使用寿命。
91.所述砖型坯料喷涂耐火涂层过程是将放置有砖型坯料的陶瓷底板置于传送带上使砖型坯料经过耐火涂层喷嘴从砖型坯料上方进行喷涂,喷嘴喷射方向与砖型坯料上表面垂直,喷嘴喷出量为25g/s,传送带移动速度为25cm/s,这样的喷涂方式,喷涂的效率高。
92.对比实施例1-实施例3,实施例3所制备出的耐火砖,抗压强度最高,抗冲击强度最高,表面粗糙度最低,表面抗腐蚀效果最好,在实际应用中,抗结圈效果最好,因此实施例3为最佳实施例。
再多了解一些
本文用于创业者技术爱好者查询,仅供学习研究,如用于商业用途,请联系技术所有人。