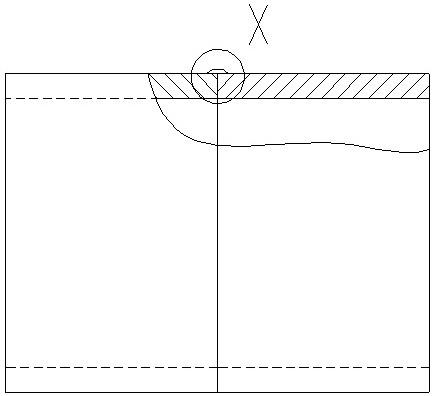
一种用于不锈钢管对接的活性氩弧自动焊根焊方法
1.技术领域
2.本发明属于金属材料焊接技术领域,涉及一种活性钨极氩弧焊焊接方法,尤其涉及一种用于不锈钢管对接的活性氩弧自动焊根焊方法。
背景技术:
3.不锈钢焊管主要用于石化工业、海洋工程等众多对耐腐蚀性要求极高的领域,广泛应用于石化工业、电力工业、城市建设等方面,可以输送液体、气体,也可以作打桩、桥梁、码头、道路和建筑结构用管。
4.现有技术中,在tig焊对管道的对接接头进行焊接时,需先在管道的端部开设v、u型坡口,然后再进行焊接,为了能够焊透,还需要一定的组对间隙。不锈钢管道的焊接由于管件本身的尺寸误差,如存在一定的椭圆度、厚薄不均等,容易导致组对时存在错边大、组对间隙不好控制等现象。所以,目前国内外管道焊接方法仍然采用传统的手工tig(钨极氩弧焊)打底,焊条电弧焊、气保焊或埋弧焊填充、盖面的传统焊接工艺。人工手工tig焊打底可以根据错边量的变化、组对间隙的大小适时调整焊接工艺参数,但手工打底焊工艺稳定性受人为因素影响较大,焊工劳动强度较大,焊接工艺适应性及焊接质量一致性较低,焊接效率及自动化水平低,对焊接工人的技能要求高。而采用自动焊打底焊焊接方法基本采用等离子弧焊paw(图1、图2)、高熔深焊ktig穿孔焊工艺(图3、图4)或传统的tig焊开坡口,留间隙焊接,对坡口的尺寸及组对一致性要求高,设备复杂,操作难度大,极易焊穿。
5.目前,企业招焊工难、焊工成本高等问题日益突出,管道自动焊接技术及设备已逐渐在管道施工中得到推广应用(图5、图6)。由上述可见,采用自动焊机在对不锈钢管道进行自动化焊接时,传统焊接工艺很难实现自动打底焊接,所以程序复杂,人工劳动强度大,对工人的操作技能要求高,不能适应自动化程度越来越高的焊接工艺的发展。因此,寻找一种用于不锈钢管的稳定性好、容错率较高的对接自动根焊工艺方法是业界面对的重要课题。
技术实现要素:
6.本发明的目的在于提供一种用于不锈钢管对接的活性氩弧自动焊根焊方法,以解决现有技术的自动焊接设备打底焊对焊工操作水平要求高、人工劳动强度大、焊接程序复杂的问题。并能够克服管件的尺寸误差和装配精度差的影响,采用a-tig焊技术确保打底成形,减少热影响区,优化焊缝成形,保证焊接效率与焊缝成形的一致性,有效解决不锈钢焊接变形大的问题,适用范围广、兼容性好、工作效率高。
7.为实现上述目的本发明所采用的技术方案是:一种用于不锈钢管对接的活性氩弧自动焊根焊方法,其特征在于:包括以下步骤:s1:对待焊接的不锈钢管进行坡口加工:1.5mm≤壁厚≤7mm时,采用i型坡口;壁厚>7mm时,采用y形坡口;
s2:对待焊区进行清理,之后装配组对并固定;s3:取焊接活性剂与丙酮或无水乙醇混合均匀,然后涂覆在步骤s2清理后的待焊区,待涂覆层干燥;s4:将步骤s3处理后的不锈钢管置于tig焊枪下进行打底焊接,采用熔透工艺焊接。上述的一种用于不锈钢管对接的活性氩弧自动焊根焊方法中,所述步骤s1中,所述y形坡口的角度为75
°
~90
°
,钝边的高度为3~7mm。
8.上述的一种用于不锈钢管对接的活性氩弧自动焊根焊方法中,步骤s2中采用机械方法对待焊件的焊接表面进行打磨处理,露出金属光泽,然后用乙醇清洗焊接件表面;组对间隙为零,错边量小于等于1 .5mm。
9.通过采用上述技术方案,待焊接的不锈钢管不需要组对间隙,只有焊缝开坡口的部分由焊丝填充完成,节省了焊接耗材,提高了焊接效率,而且克服了组对间隙不均匀带来的焊接不稳定问题,在自动焊机上容易实现稳定的焊接;而厚度较薄的材料只需i型坡口,不需要组对间隙,焊缝金属中大部分金属由母材自熔填充,只有焊缝表面一小部分由焊丝填充完成,能进一步节省焊接耗材提高焊接效率。
10.上述的一种用于不锈钢管对接的活性氩弧自动焊根焊方法中,步骤s3中活性剂有二种类型,一种为粉末状,一种为灌装喷雾状。
11.进一步地,步骤s3中所述活性剂中氧化铁质量百分数为40-70%,其余为二氧化硅,氧化铁和二氧化硅的混合物总和为100%;使用粉末状的活性剂的方法为:先将活性剂与丙酮或无水乙醇混匀调制为糊状,混合比例为:每200~300ml丙酮或无水乙醇添加10~20g活性剂; 用扁平毛刷刷涂在待焊区域;具体刷涂方法为:以两段管道对接缝为中心,均匀涂覆在两侧,涂覆的宽度为10-20mm,活性剂的涂覆量以恰好遮盖金属光泽为准;使用灌装喷雾状活性剂的方法为:将活性剂均匀喷涂在焊缝两侧,喷涂的宽度为10-20mm,活性剂的涂覆量以恰好遮盖金属光泽为准。
12.上述的一种用于不锈钢管对接的活性氩弧自动焊根焊方法中,步骤s4中打底焊的工艺参数为:1.5mm≤壁厚≤7mm时,焊接电流40~160a,电压9~15v,焊接速度60~80mm/min;壁厚>7mm时,焊接电流160~180a,电压15~18v,焊接速度60~80mm/min。
13.有益效果:1、本技术采用的a-tig根焊方法,由于焊接区涂覆活性剂,令焊接能量和热量向熔池深度方向扩展,焊接熔深大幅度提高,焊缝在深度方向上的熔宽差别减小,减少工件的焊接变形;2、待焊接的不锈钢管不需要组对间隙,只有焊缝开坡口的部分由焊丝填充完成,节省了焊接耗材,提高了焊接效率,而且克服了组对间隙不均匀带来的焊接不稳定问题,在自动焊机上容易实现稳定的焊接;而厚度较薄的材料只需i型坡口,不需要组对间隙,焊缝金属中大部分金属由母材自熔填充,只有焊缝表面一小部分由焊丝填充完成,能进一步节省焊接耗材提高焊接效率;3、采用焊接活性剂,比不采用焊接活性剂有效增加了tig焊的焊接熔深(图7),厚
度小于等于7mm的不锈钢管的焊接可以采用i型坡口,无填加焊丝,节约了成本,也不需要组对间隙,直接用a-tig焊接,使焊接热量更加集中,实现对接焊缝大熔深一次性焊透,有效提高焊接效率,并且单面焊双面成形;4、厚度大于7mm的不锈钢管的焊接,不需要组对间隙,只需开y形坡口,进行a-tig打底焊接后,再进行焊条电弧焊;埋弧焊;tig焊填充、盖面。坡口窄,焊缝截面积小,填充金属量少,节省焊材和能耗,提高生产效率。
附图说明
14.图1、图2为现有技术中采用等离子弧焊paw自动焊打底焊焊接的示意图。
15.图3、图4为现有技术中采用高熔深焊ktig穿孔焊工艺自动焊打底焊焊接的示意图。
16.图5、图6为现有技术中利用管道自动焊接设备焊接管道的示意图。
17.图7为采用焊接活性与不采用焊接活性剂焊接效果的对比示意图。
18.图8为实施例一、实施例二、实施例三中i型坡口、无间隙对接及焊缝的示意图。
19.图9为图8中的x部的局部放大示意图。
20.图10为实施例四中y型坡口、无间隙对接及焊缝的示意图。
21.图11为图10中的y部的局部放大示意图。
22.图12为实施例一、实施例二、实施例三中待焊接的两段不锈钢管的待焊区域的两侧涂覆焊接活性剂的示意图。
23.图13为实施例四中待焊接的两段不锈钢管的待焊区域的两侧涂覆焊接活性剂的示意图。
具体实施方式
24.为能清楚说明本方案的技术特点,下面通过非限定性的实施例并结合附图对本发明做进一步的说明。
25.实施例一:tp304不锈钢管道,直径89mm,标称厚度4.0mm,i型坡口无间隙对接接头,请见图5、图6,采用以下步骤和工艺参数焊接制作:s1: 采用金鲁鼎环缝自动焊接设备进行焊接,设备型号为h3661-t。
26.s2: 使用的钨极直径3.2mm;焊丝牌号er308,直径φ1.0mm;氩气纯度为99.99%。
27.s3:对待焊接的不锈钢管需要相对焊接的端面加工/修整成90
°
的平直切面,使需要相对焊接的两个坡口面构成i型坡口。
28.s4:对待焊区进行清理,之后装配组对并固定;采用机械方法对待焊件的焊接表面进行打磨处理,露出金属光泽,然后用乙醇清洗焊接件表面;组对间隙为零,错边量小于等于1.5mm。
29.s5:取焊接活性剂与丙酮或无水乙醇混合均匀,用毛刷均匀涂刷在步骤s4清理后的待焊区,待涂覆层干燥;具体地,本实施例采用粉末状活性剂,活性剂中氧化铁质量百分数为60%,其余为
二氧化硅,氧化铁和二氧化硅的混合物总和为100%;先将活性剂与丙酮或无水乙醇混匀调制为糊状,混合比例为:每200~300ml丙酮或无水乙醇添加10~20g活性剂;用扁平毛刷刷涂在待焊区域;以两段管道对接缝为中心,用扁平毛刷将混合后的活性剂均匀涂覆在待焊区域的两侧,涂覆的宽度为10-20mm,活性剂的涂覆量以恰好遮盖金属光泽为准。
30.s6:将步骤s5处理后的不锈钢管置于tig焊枪下进行熔透工艺打底焊接;具体地,采用钨极氩弧自动焊环缝焊机焊接一次性成型,将焊枪钨极尖端置于待焊部位正上方距离活性剂涂敷层3~4mm。a-tig 焊接工艺规范:焊接电流60a,电压9~8.4v,焊接速度80mm/min,电弧长度3mm,钨极直径3.2mm,氩气流量8~12l/min。
31.s7:a-tig 焊接完成后,将活性剂用钢丝刷清理干净,进行盖面焊接工艺,焊接电流90a,电压11-10.4v,焊接速度100mm/min,摆动速度800mm/min,摆动幅度5mm,两侧停留时间0.3s,送丝速度800mm/min。
32.s8:步骤s6和s7进行打底和盖面焊接时,需将管道两侧封堵,管道内部充氩气保护,氩气纯度为99.99%,氩气流量5l/min。
33.焊后检测结果:对焊接完成工件进行外观及x射线探伤检验,按照标准i级片要求,本次焊接接头一次探伤合格。
34.实施例二:tp304不锈钢管道,直径89mm,标称厚度6.0mm,i型坡口无间隙对接接头,请见图5、图6,采用以下步骤和工艺参数焊接制作:s1: 采用金鲁鼎环缝自动焊接设备进行焊接,设备型号为h3661-t。
35.s2: 使用的钨极直径3.2mm;焊丝牌号er308,直径φ1.0mm;氩气纯度为99.99%。
36.s3:对待焊接的不锈钢管需要相对焊接的端面加工/修整成90
°
的平直切面,使需要相对焊接的两个坡口面构成i型坡口。
37.s4:对待焊区进行清理,之后装配组对并固定;采用机械方法对待焊件的焊接表面进行打磨处理,露出金属光泽,然后用乙醇清洗焊接件表面;组对间隙为零,错边量小于等于1.5mm。
38.s5:取焊接活性剂与丙酮或无水乙醇混合均匀,用毛刷均匀涂刷在步骤s4清理后的待焊区,待涂覆层干燥;具体地,本实施例采用粉末状活性剂,活性剂中氧化铁质量百分数为60%,其余为二氧化硅,氧化铁和二氧化硅的混合物总和为100%;先将活性剂与丙酮或无水乙醇混匀调制为糊状,混合比例为:每200~300ml丙酮或无水乙醇添加10~20g活性剂;用扁平毛刷刷涂在待焊区域;以两段管道对接缝为中心,用扁平毛刷将混合后的活性剂均匀涂覆在待焊区域的两侧,涂覆的宽度为10-20mm,活性剂的涂覆量以恰好遮盖金属光泽为准。
39.s6:将步骤s5处理后的不锈钢管置于tig焊枪下进行熔透工艺打底焊接;具体地,采用钨极氩弧自动焊环缝焊机焊接一次性成型,将焊枪钨极尖端置于待焊部位正上方距离活性剂涂敷层3~4mm。a-tig 焊接工艺规范:焊接电流150a,电压13~12.4v,焊接速度60mm/min,电弧长度3mm,钨极直径3.2mm,氩气流量8~12l/min。
40.s7:a-tig 焊接完成后,将活性剂用钢丝刷清理干净,进行盖面焊接工艺,焊接电
流110a,电压12-11.4v,焊接速度80mm/min,摆动速度800mm/min,摆动幅度8mm,两侧停留时间0.3s,送丝速度800mm/min。
41.s8:步骤s6和s7进行打底和盖面焊接时,需将管道两侧封堵,管道内部充氩气保护,氩气纯度为99.99%,氩气流量5l/min。
42.焊后检测结果:对焊接完成工件进行外观及x射线探伤检验,按照标准i级片要求,本次焊接接头一次探伤合格。
43.实施例三:tp304不锈钢管道,直径325mm,标称厚度7.0mm,i型坡口无间隙对接接头,请见图5、图6,采用以下步骤和工艺参数焊接制作:s1: 采用金鲁鼎环缝自动焊接设备进行焊接,设备型号为h3661-t。
44.s2: 使用的钨极直径3.2mm;焊丝牌号er308,直径φ1.0mm;氩气纯度为99.99%。
45.s3:对待焊接的不锈钢管需要相对焊接的端面加工/修整成90
°
的平直切面,使需要相对焊接的两个坡口面构成i型坡口。
46.s4:对待焊区进行清理,之后装配组对并固定;采用机械方法对待焊件的焊接表面进行打磨处理,露出金属光泽,然后用乙醇清洗焊接件表面;组对间隙为零,错边量小于等于1.5mm。
47.s5:取焊接活性剂与丙酮或无水乙醇混合均匀,用毛刷均匀涂刷在步骤s4清理后的待焊区,待涂覆层干燥;具体地,本实施例采用粉末状活性剂,活性剂中氧化铁质量百分数为60%,其余为二氧化硅,氧化铁和二氧化硅的混合物总和为100%;先将活性剂与丙酮或无水乙醇混匀调制为糊状,混合比例为:每200~300ml丙酮或无水乙醇添加10~20g活性剂;用扁平毛刷刷涂在待焊区域;以两段管道对接缝为中心,用扁平毛刷将混合后的活性剂均匀涂覆在待焊区域的两侧,涂覆的宽度为10-20mm,活性剂的涂覆量以恰好遮盖金属光泽为准。
48.s6:将步骤s5处理后的不锈钢管置于tig焊枪下进行熔透工艺打底焊接;具体地,采用钨极氩弧自动焊环缝焊机焊接一次性成型,将焊枪钨极尖端置于待焊部位正上方距离活性剂涂敷层3~4mm。a-tig 焊接工艺规范:焊接电流160a,电压14~13.4v,焊接速度80mm/min,电弧长度3mm,钨极直径3.2mm,氩气流量8~12l/min。
49.s7:a-tig 焊接完成后,将活性剂用钢丝刷清理干净,进行盖面焊接工艺,焊接电流120a,电压13-12.4v,焊接速度80mm/min,摆动速度800mm/min,摆动幅度8mm,两侧停留时间0.3s,送丝速度1000mm/min。
50.s8:步骤s6和s7所述打底和盖面焊接时,需将管道两侧封堵,管道内部充氩气保护,氩气纯度为99.99%,氩气流量5l/min。
51.焊后检测结果:对焊接完成工件进行外观及x射线探伤检验,按照标准i级片要求,本次焊接接头一次探伤合格。
52.实施例四:tp304不锈钢高颈法兰及相应同材质接管,直径273mm,壁厚8mm,y形坡口无间隙对
接接头,请见图7至图8,图中t为壁厚8mm,h为钝边5mm;采用以下步骤和工艺参数焊接制作:s1: 采用金鲁鼎环缝自动焊接设备进行焊接,设备型号为h3661-t。
53.s2: 使用的钨极直径3.2mm;焊丝牌号er308,直径φ1.0mm;氩气纯度为99.99%。
54.s3:对待焊接的不锈钢管进行坡口加工:采用y形坡口,坡口单边的角度为37.5
°
,钝边的高度为5mm。
55.s4:对待焊区进行清理,之后装配组对并固定;采用机械方法对待焊件的焊接表面进行打磨处理,露出金属光泽,然后用乙醇清洗焊接件表面;组对间隙为零,错边量小于等于1.5mm。
56.s5:取焊接活性剂与丙酮或无水乙醇混合均匀,用毛刷均匀涂刷在步骤s4清理后的待焊区,待涂覆层干燥;具体地,本实施例采用粉末状活性剂,活性剂中氧化铁质量百分数为60%,其余为二氧化硅,氧化铁和二氧化硅的混合物总和为100%;先将活性剂与丙酮或无水乙醇混匀调制为糊状,混合比例为:每200~300ml丙酮或无水乙醇添加10~20g活性剂;用扁平毛刷刷涂在待焊区域;以两段管道对接缝为中心,用扁平毛刷将混合后的活性剂均匀涂覆在待焊区域的两侧,涂覆的宽度为10-20mm,活性剂的涂覆量以恰好遮盖金属光泽为准。
57.s6:将步骤s5处理后的不锈钢管置于tig焊枪下进行熔透工艺打底焊接;具体地,采用钨极氩弧自动焊环缝焊机焊接一次性成型,将焊枪钨极尖端置于待焊部位正上方距离活性剂涂敷层3~4mm。a-tig 焊接工艺规范:焊接电流160a,电压14~13.4v,焊接速度80mm/min,电弧长度3mm,钨极直径3.2mm,氩气流量8~12l/min。
58.s7:a-tig 焊接完成后,将活性剂用钢丝刷清理干净,进行盖面焊接工艺,焊接电流120a,电压13-12.4v,焊接速度80mm/min,摆动速度800mm/min,摆动幅度8mm,两侧停留时间0.3s,送丝速度1500mm/min。
59.s8:步骤s6和s7所述打底和盖面焊接时,需将管道两侧封堵,管道内部充氩气保护,氩气纯度为99.99%,氩气流量5l/min。
60.焊后检测结果:对焊接完成工件进行外观及x射线探伤检验,按照标准i级片要求,本次焊接接头一次探伤合格。
61.上述实施例中的活性剂还可以采用本发明人201010117476.5号发明专利的汽雾罐装型活性剂,活性剂中氧化铁质量百分数为40-70%,其余为二氧化硅,氧化铁和二氧化硅的混合物总和为100%;将活性剂均匀喷涂在焊缝两侧,喷涂的宽度为10-20mm,活性剂的涂覆量以恰好遮盖金属光泽为准。
62.上述的各实施例中,活性剂的涂覆量以恰好遮盖金属光泽为准,还可以进一步量化为100-300mg/cm
²
。
63.除说明书所述的技术特征外,均为本专业技术人员的已知技术。
64.以上所列举的实施方式仅供理解本发明之用,并非是对本发明所描述的技术方案的限定,有关领域的普通技术人员,在权利要求所述技术方案的基础上,还可以作出多种变化或变形,所有等同的变化或变形都应涵盖在本发明的权利要求保护范围之内。
再多了解一些
本文用于创业者技术爱好者查询,仅供学习研究,如用于商业用途,请联系技术所有人。