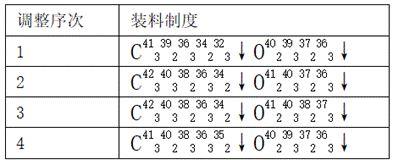
1.本发明涉及高炉炼铁冶金领域,尤其涉及一种处理及预防高炉炉缸严重亏热的方法。
背景技术:
2.高炉炉缸严重亏热是指高炉炉缸内部因热量不足,渣铁由铁口中流出不畅,亏热严重时渣铁凝固,无法流动出炉缸,而造成炉缸冻结的严重工艺事故。目前的处理方式是首先烧通铁口和临近风口的通道然后再送风,随着高炉凉渣铁的逐步排出控制风量和送风风口数量,逐步扩大炉缸面积,最终恢复所有风口送风。传统的铁口和风口通道的烧通方式是上部从风口使用氧气管用氧气烧,下部从铁口往风口烧。这种方式受铁口至风口的距离影响,适用于小型高炉,同时耗时长效率低,不但需要大量氧气管和氧气,而且因烧通时间长往往延误恢复炉况的时机。但是对于2500m3以上的大型高炉,铁口中心线与风口中心线的距离已经超过了4m,风口平台工作空间有限,现场作业环境较差,如高温、煤气、粉尘等等,需要花费大量时间烧通通道,延长了高炉事故恢复时间;实施贯通铁口与风口通道的烧氧作业时,由铁口向风口烧时,烧氧气时间较长,昼夜不停的烧,易将铁口孔道烧大,甚至危及铁口区域的组合碳砖,导致后续的生产过程中铁口孔道变大,易造成铁口大喷焦炭,烧损周围电缆、能源介质管线;该装置较为笨拙,操作人员实施时,体力消耗巨大,易导致抢修暂停,延长事故处理时间。尤其是炉役后期,冷却壁漏水易造成炉缸亏热,长期休风后渣铁排放困难。
技术实现要素:
3.针对上述问题,本发明提供了一种处理及预防高炉炉缸严重亏热的方法,可以解决大型高炉的炉缸亏热严重问题。
4.本发明采用的技术方案如下:一种处理及预防高炉炉缸严重亏热的方法,1)、炉况失常后立即全干焦进行生产;高炉由正常冶炼改为全焦冶炼,停止喷煤与富氧,采用加循环焦的方式,15批正常料加2批净焦的方式,来提高炉缸热量,适当提高铁水中的硅含量,使硅含量保持在2.0以上,控制铁水热量在1500以上,杜绝炉温偏低的现像,炉况好转后逐步取消循环加焦模式,恢复高炉煤量,氧量;2)、装料制度:按照炉缸亏热严重进行处理,连续补焦10批,每批20.4吨,合计204吨,装料制度的调整:一批料,流槽旋转8~12圈,矿和焦的α角差为2
°
~4
°
,α0=αc [2
°
~4
°
],采用合适的批重,保证炉内煤气流顺畅,高炉操作上做到不轻易扩批重,等高炉适
应当前批重一定时间后且高炉比较顺行,走料好,风量、风压稳定后才考虑扩批重,同时加强精确布料的管理,使用声敏探测仪与料罐雷达数据结合,判断布料是否精确,规定矿石与焦碳料流开度范围,保证布料平台合理,使之达到精确布料目的;3)、矿焦负荷: o/a调整顺序至2.818
→
2.914
→
3.006
→
3.128
→
3.248
→
3.311
→
3.4
→
3.735
→
3.935;4)、送风制度:减风至600nm3/min,利用休风机会,调整风口,在休风换漏水小套后,高炉堵3#、4#、12#、13#、25#、26#风口进行送风,缩小送风面积,采用定压操作,逐渐捅开被堵风口,保持合理的鼓风动能,以达到活跃炉缸,吹透中心;5)、冷却制度:由于处理炉况时高炉软水水温差变化较大,一直是处在偏高状态,为了稳定高炉软水温差,保护高炉漏水冷却壁,使之易形成渣皮,于是高炉软水流量由3500m3/h,提高至4000m3/h;6)、造渣制度:提高生铁[s],加锰矿、萤石洗炉,炉渣二元碱度r降至0.85左右,因炉渣r=aao/sio2在0.8-1.2之间时的粘度最低,铁水含s质量分数控制在0.030-0.050左右,提高炉渣和铁水的流动冲刷能力;同时配加萤石,aaf2能显著降低渣的熔化温度和粘度,促进aao的熔化,同时还能与aao形成低熔点1386℃的共熔体,消除渣中难熔的组成。因此含氟的炉渣熔化性温度低,流动性好,在炉渣碱度很高时(r=1.5~3.0),仍能保持良好的流动性。
[0005]
高炉炼铁冶炼过程中控制炉渣二元碱度r2为0.85-1.15,三元碱度r3为1.15-1.2,四元碱度r4为0.90-1.05;同时控制炉渣中al2o3的含量为<15wt%,mgo的含量为4-5wt%;控制出渣铁时间为90
±
10min,控制出铁流速为10t/min,且出渣率在80%以上;7)、炉前操作:将3个铁口埋3支氧枪,处理渣铁从铁口排放不出时,通过螺杆将氧枪装在开口机上,用开口机把氧枪顶入铁口孔道内,石棉绳封堵住氧枪与铁口孔道间孔隙,从氧气入口接入氧气用以烧熔炉缸内凝固渣铁,将炉缸内凝固的渣铁混合物烧熔后彻底排出,快速活化炉缸,迅速恢复炉缸工作状态,快速恢复正常生产,渣铁排净后,缩小出铁间隔,保证铁口间隔在10分钟之内;保证了出铁的连续性和均衡性;同时用直径55的钻头,提高日平均出铁次数;热洗期间,日平均出铁次数在12次左右,加强了炉缸铁水的循环。制定了严格的出铁重叠标准,从铁口入手,做好铁口的维护。
[0006]
本发明具有以下优点:1、处理重负荷料的时间短,通过鼓风机继续向高炉送风和出铁,炉顶压力保持常压,高炉继续装入轻负荷炉料把高炉内的重负荷炉料置换完毕,提高炉温后,按照阶梯状装入重负荷料,确保高炉顺利恢复炉况。2、通过螺杆将氧枪装在开口机上,用开口机把氧枪顶入铁口孔道内,由高炉铁口通入氧气,快速提高炉缸温度,融化软熔带的渣铁壳,氧气用以烧熔炉缸内凝固渣铁,将炉缸内凝固的渣铁混合物烧熔后彻底排出,快速活化炉缸,迅速恢复炉缸工作状态,快速恢复正常生产。
具体实施方式
[0007]
下面以具体实施方式对本发明作进一步的说明。
[0008]
一种处理及预防高炉炉缸严重亏热的方法,1)、炉况失常后立即全干焦进行生产;高炉由正常冶炼改为全焦冶炼,停止喷煤与富氧,采用加循环焦的方式,15批正常料加2批净焦的方式,来提高炉缸热量,适当提高铁水
中的硅含量,使硅含量保持在2.0以上,控制铁水热量在1500以上,杜绝炉温偏低的现像,炉况好转后逐步取消循环加焦模式,恢复高炉煤量,氧量;2)、装料制度:按照炉缸亏热严重进行处理,连续补焦10批,每批20.4吨,合计204吨,装料制度的调整:一批料,流槽旋转8~12圈,矿和焦的α角差为2
°
~4
°
,α0=αc [2
°
~4
°
],采用合适的批重,保证炉内煤气流顺畅,高炉操作上做到不轻易扩批重,等高炉适应当前批重一定时间后且高炉比较顺行,走料好,风量、风压稳定后才考虑扩批重,同时加强精确布料的管理,使用声敏探测仪与料罐雷达数据结合,判断布料是否精确,规定矿石与焦碳料流开度范围,保证布料平台合理,使之达到精确布料目的;3)、矿焦负荷: o/a调整顺序至2.818
→
2.914
→
3.006
→
3.128
→
3.248
→
3.311
→
3.4
→
3.735
→
3.935;4)、送风制度:减风至600nm3/min,利用休风机会,调整风口,在休风换漏水小套后,高炉堵3#、4#、12#、13#、25#、26#风口进行送风,缩小送风面积,采用定压操作,逐渐捅开被堵风口,保持合理的鼓风动能,以达到活跃炉缸,吹透中心;5)、冷却制度:由于处理炉况时高炉软水水温差变化较大,一直是处在偏高状态,为了稳定高炉软水温差,保护高炉漏水冷却壁,使之易形成渣皮,于是高炉软水流量由3500m3/h,提高至4000m3/h;6)、造渣制度:提高生铁[s],加锰矿、萤石洗炉,炉渣二元碱度r降至0.85左右,因炉渣r=aao/sio2在0.8-1.2之间时的粘度最低,铁水含s质量分数控制在0.030-0.050左右,提高炉渣和铁水的流动冲刷能力;同时配加萤石,aaf2能显著降低渣的熔化温度和粘度,促进aao的熔化,同时还能与aao形成低熔点1386℃的共熔体,消除渣中难熔的组成。因此含氟的炉渣熔化性温度低,流动性好,在炉渣碱度很高时(r=1.5~3.0),仍能保持良好的流动性。
[0009]
高炉炼铁冶炼过程中控制炉渣二元碱度r2为0.85-1.15,三元碱度r3为1.15-1.2,四元碱度r4为0.90-1.05;同时控制炉渣中al2o3的含量为<15wt%,mgo的含量为4-5wt%;控制出渣铁时间为90
±
10min,控制出铁流速为10t/min,且出渣率在80%以上;7)、炉前操作:将3个铁口埋3支氧枪,处理渣铁从铁口排放不出时,通过螺杆将氧枪装在开口机上,用开口机把氧枪顶入铁口孔道内,石棉绳封堵住氧枪与铁口孔道间孔隙,从氧气入口接入氧气用以烧熔炉缸内凝固渣铁,将炉缸内凝固的渣铁混合物烧熔后彻底排出,快速活化炉缸,迅速恢复炉缸工作状态,快速恢复正常生产,渣铁排净后,缩小出铁间隔,保证铁口间隔在10分钟之内;保证了出铁的连续性和均衡性;同时用直径55的钻头,提高日平均出铁次数;热洗期间,日平均出铁次数在12次左右,加强了炉缸铁水的循环。
[0010]
实施例:在高炉炉役后期,高炉水系统不是特别稳定,需要减轻焦炭负荷,同时考虑漏水对
炉缸热制度的影响。
[0011]
1、高炉休风前,对炉料结构进行调整,具体步骤如下:
①
净焦参数计算:高炉休风前,分别设定高炉炉缸、炉腹、炉身预定位,确定高炉炉喉料面分别与高炉炉缸、炉腹、炉身之间容积v预1=2500.53m3,确定高炉的吨焦耗风量q焦=2580m3/t、每批正常料中焦炭的质量g焦=12.8t/批、每批正常料的体积v料=47.3m3/批、高炉小时风量q风=4600m3/min=276000 m3/h,通过公式h=(v预*q焦*g焦)
ꢀ÷
(v料*q风)得,第1段净焦由高炉炉喉料面下达至高炉炉缸预定位所用时间为h1=6.3h、第2段净焦由高炉炉喉料面下达至高炉炉腹上部预定位所用时间为h2=4.6h、第3段净焦由高炉炉喉料面下达至炉身下部预定位所用时间为h3=4.3h;第4段净焦由高炉炉喉料面下达至炉身下部预定位所用时间为h4=4.1h;
②
净焦层设置过程:高炉休风前h1=6.3h在高炉炉喉料面上加入净焦,设置第1段净焦,其后分批加入正常料;至高炉休风前h2=4.6h在高炉炉喉料面上加入净焦,设置第2段净焦;其后再分批加入正常料,至高炉休风前h3=4.3h在高炉炉喉料面上加入净焦,第3段净焦其后,再分批加入正常料,至高炉休风前h4=4.1h在高炉炉喉料面上加入净焦,休风时,第1段净焦位于高炉炉缸,第2段净焦位于高炉炉腹上部,第3段净焦位于高炉炉身下部;第4段净焦位于高炉炉身中部;
③
高炉长期休风时,钒钛矿必须停止使用,且停止使用周期必须大于2个周期,防止发生炉缸渣铁粘结严重,降低开风后渣铁排放系数,确保渣铁能够及时排出;长期休风15-24小时或(休风时间过半时)打开1个铁口,捅开3-4个风口,查看风口情况,做到对炉缸工作状态的全程跟踪。
[0012]
2、休风前,对水路及冷却壁的管理技术,具体步骤如下:
①
在休风检修情况下,炉壳温度发生变化,热胀冷缩冷却水管发生剪切位移漏水。休风时密切关注软水补水量,发现补水量异常时,及时汇报信息并进行查漏,查清是内漏还是外漏,做好预防措施;如漏水原因查不出时,将有出水区域的上部冷却水管(10-15根)全部关闭,逐个进行冷却水管排查,并按照信息汇报制度及时汇报。
[0013]
②
完善建立高炉长期休风时冷却水专项管理制度,休风后2h降低水压至0.6mpa(改造前),并将膨胀罐压力排卸掉与大气连通,减少异常情况下高炉漏水量。
[0014]
③
对泵房软水系统进行检查,每座高炉外排水量及正常补水分开数据记录清楚,高炉在休风情况下,工业水、软水降压后,将软水压力控制在0.45-0.50mpa,准备泵房杜绝炉体冷却水外漏,泵房操作工及时通报高炉补水情况。
[0015]
④
高炉长期休风时间调整为白天,便于进行冷却壁查漏,建立健全养护水的管理办法,针对养护水的开关,看水班长、作业长必须现场签字确认,作业区对看水工定期做好培训,建立软水、高压工业水查漏培训机制,提高看水工的查漏技能。
[0016]
⑤
统一膨胀罐液位的补水要求,膨胀罐液位统一标准为:2.0-2.5米,液位下降至最低时才允许补水,建立健全膨胀罐补水标准,中控电脑增加软水补水趋势及报警上下限值。
[0017]
⑥
每月对高炉的冷却壁水管进行一次全面查漏工作,将漏水的冷却壁水管做好标记,休风后关闭并进行确认,确认漏水后及时进行养护。
[0018]
复风效果验证
1、在高炉炉役后期,高炉水系统不是特别稳定,需要减轻焦炭负荷,休风前1个冶炼周期内设置4段净焦层,并保证第1段净焦层体积占净焦总体积的50%,第2、3、4段净焦体积占净焦预料层总质量的30%、20%、10%,增加第一净焦预料层比例,相应减少第2、3、4段焦炭比例,利于高炉上部热交换率的提高和下部渣铁物理热迅速恢复,从而改善渣铁流动性,缩短炉况恢复时间1-2天。
[0019]
2、高炉长期休风时,第1段净焦层填充至炉缸,减少了休风期间炉缸热量损失,复风后第1段净焦层焦炭能够迅速燃烧释放热量,确保了高炉休风期间凝固渣铁在短时间内熔化,避免了长期休风复风后炉缸冻结的危险,同时第一净焦预料层填充至炉缸,炉缸透气透液性改善,保证了休风前和送风后渣铁能够及时排出,大大降低复风后炉前出铁难度,降低劳动强度。
[0020]
3、休风前精准计算净焦由高炉炉喉料面下达至各预定面所用时间,并在时间依次向高炉炉喉料面添加净焦,能够保证休风时净焦准确下达至预定位置,避免因估算不准确导致净焦不能下达至指定位置,影响高炉复风后炉况恢复进程。
[0021]
4、复风后,渣铁温度充足,流动性较好,炉前渣铁清理量较少;传统方法复风后,铁水温度偏低,渣铁流动性变差,渣铁排放困难,炉前主沟、铁口积渣较多,清理量较多,劳动强度大;5、复风后24小时内风口全开,各项操作参数恢复至正常生产水平;传统方法复风后需要76小时,节约恢复时间52小时。
再多了解一些
本文用于创业者技术爱好者查询,仅供学习研究,如用于商业用途,请联系技术所有人。