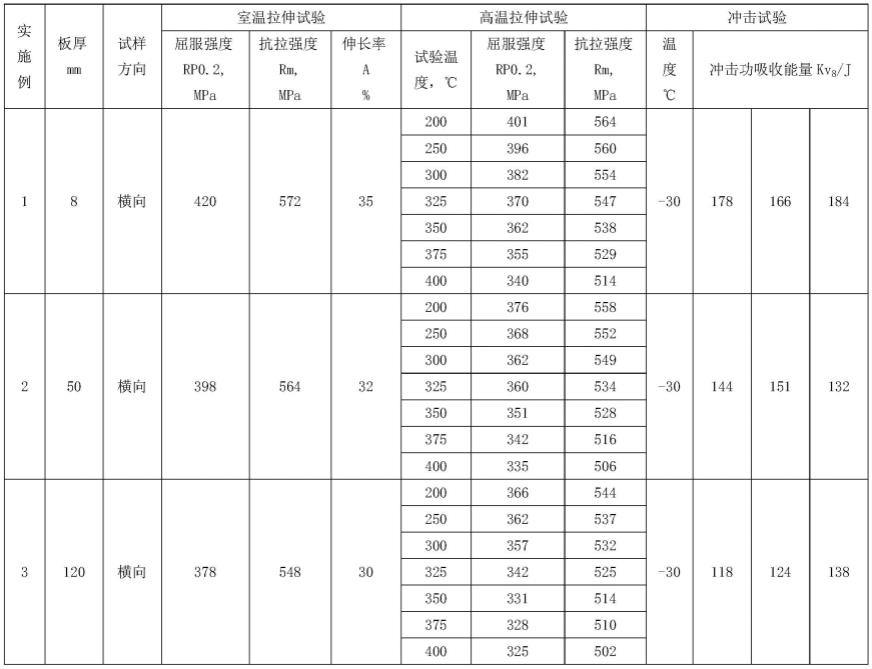
一种200~400
℃
高温强度优异的sa516gr70钢板及其制造方法
技术领域
1.本发明属于钢铁冶金技术领域,尤其涉及一种高温强度优异的钢板及其制造方法。
背景技术:
2.sa516gr70是中、低温压力容器用钢中的典型牌号,广泛应用于石油、化工、电站、锅炉等行业。随着石化行业的快速发展,设备服役的环境温度越来越低,而设备的使用温度越来越高。为了保证高温设备停产检修和高效运行过程中的安全性,设计上对钢板的综合机械性能和高温强度提出了越来越高的要求,进一步来说,就是在高温长时间模拟焊后热处理条件下,低温韧性须满足心部-30℃横向夏比冲击吸收能量≥41j,200~400℃高温拉伸抗拉强度须满足asme第ii卷材料d篇表u中规定:200~375℃高温拉伸的抗拉强度≥483mpa,400℃高温拉伸的抗拉强度≥476mpa。200~400℃高温拉伸的验收值均接近asme sa516/sa516m-2021标准中sa516gr70牌号常温拉伸性能验收标准的下限485mpa。研究表明,经过高温长时间模拟焊后热处理后,钢板的强度和低温韧性明显下降,随着拉伸试验温度的升高,钢板的抗拉强度会进一步下降,因此,研发生产能够满足上述技术要求钢板的技术难度非常大,目前,国内中厚板厂尚无很好的解决方案,如何能够生产兼有良好低温韧性和优异耐热性的钢板是本领域亟待解决的技术问题。
3.目前能够检索到关于钢板高温拉伸性能的专利中绝大多数只关注钢板的高温拉伸屈服强度,而未提及钢板高温拉伸抗拉强度。针对提高或保证钢板高温拉伸抗拉强度的专利很少,尤其是在针对钢板在200~400℃范围内高温拉伸抗拉强度的相关专利更少。公布号为cn108754340a的中国专利涉及一种用于制造压力容器封头的q345r钢板及其生产方法,钢板厚度为8~100mm,所述钢板化学成分组成及其百分含量为:c≤0.20%,si≤0.55%,mn:1.20~1.70%,p≤0.015,s≤0.005%,alt:0.025~0.050%,nb:0.01~0.05%,v:0.02~0.05%,cu:0.10~0.30%,ni:0.15~0.30%,余量为fe和不可避免的杂质。所述生产方法包括加热、轧制和热处理工序,其中轧制工序采用再结晶区 未再结晶区两阶段控轧控冷工艺,热处理采用两次正火 回火。钢板力学性能可以满足-20℃冲击功≥100j,200~400℃高温拉伸抗拉强度≥450mpa。该专利技术未具体关注模拟焊后热处理状态下力学性能,而且实施例中3中的350℃高温拉伸抗拉强度和实施例2中的400℃高温拉伸抗拉强度未达到asme第ii卷材料d篇表u中规定要求。此外,该专利产品的成分设计添加大量的贵重合金,而且热处理工艺复杂,生产效率低,生产周期长。综上,从成分设计、生产工艺到产品性能指标上来看,该专利均不符合目前国家提倡的低碳减排、绿色制造政策导向,也不满足石化设备向大型化、高参数方向发展的需要。
技术实现要素:
4.本发明所要解决的技术问题是针对上述现有技术提供一种200~400℃高温强度
优异的sa516gr70钢板及其制造方法,钢板厚度为8~120mm,适用于在高温和低温环境中使用,具有较高的强度、良好的低温韧性和优异的高温拉伸性能。
5.本发明解决上述问题所采用的技术方案为:一种200~400℃高温强度优异的sa516gr70钢板,钢板的化学成分按重量百分比计为c:0.16~0.20%,si:0.20~0.40%,mn:1.20~1.50%,p:≤0.006%,s:≤0.001%,ni:0.10~0.20%,mo:0.04~0.10%,cr:0.10~0.20%,nb:0.01~0.02%,v:0.01~0.03%,ti:0.01~0.03%,alt:0.02~0.05%,b:≤0.0005%,pb:≤0.0005%,sn:≤0.0005%,as:≤0.0005%,sb:≤0.0005%,bi:≤0.0005%,余量为fe及不可避免的杂质元素。
6.本发明属于铁基合金,钢中主要化学元素及其作用如下:
7.c能够显著提高钢板的强度,但对韧性和塑性不利,综合考虑钢板强度和韧性和,本发明中c含量设定为0.16~0.20%。
8.mn通过固溶强化提高钢的强度,但mn容易与s形成mns夹杂,进而降低钢板低温韧性,因此mn含量不易过高,本发明中mn含量设定为1.20~1.50%。
9.si主要作为炼钢时的还原剂和脱氧剂使用,有一定的固溶强化作用,如果含量过高,会导致钢板低温韧性降低,因此本发明中si含量设定为0.20~0.40%。
10.cr、mo、v:强碳化物形成元素,能够增强固溶体中原子间的结合力,cr-mo-v复合强化可以有效提高钢板的热强性,保证高温强度,mo、v属于贵重合金,应限制使用,cr会提高钢的回火脆性转变温度,促进回火脆性,应限制使用,本发明中mo含量设定为0.04~0.10%,cr含量设定为0.10~0.20%,v含量设定为0.01~0.03%。
11.ni镍能显著提高低温冲击韧性,同时ni属于贵重合金,应限制使用,综合考虑钢板性能和生产成本,本发明中ni含量设定为0.10~0.20%。
12.s、p是有害元素,增减钢的脆性,降低冲击韧性和焊接性能,因此,s、p含量控制越低越好,本发明中s含量设定≤0.001%。p含量设定≤0.006%。
13.alt:铝主要用来脱氧和有细化晶粒,本专利alt含量控制在0.02~0.05%。
14.nb:铌可以显著提高钢的奥氏体再结晶温度,扩大再结晶区范围,便于实现高温轧制,铌还可以抑制奥氏体晶粒长大,具有细晶强化和析出强化的作用,本专利nb含量控制在0.01~0.02%。
15.ti:与c、n元素形成碳氮化物,具有推迟奥氏体再结晶,细化铁素体晶粒的作用,可以同时提高钢板强度和韧性,本专利ti含量控制在0.010~0.03%。
16.b:容易与n形成bn,在晶间富集,弱化晶界,因此其含量应越低越好,本发明b含量设定≤0.0005%
17.pb、sn、as、sb、bi是有害元素,容易在晶间富集,弱化晶界,因此其含量应越低越好,本发明设定pb:≤0.0005%,sn:≤0.0005%,as:≤0.0005%,sb:≤0.0005%,bi:≤0.0005%。
18.本发明上述钢板的生产顺序依次为冶炼浇铸、连铸坯加热、轧制和热处理,具体工艺如下:
19.(1)冶炼浇铸:控制钢水中有害元素pb:≤0.0005%,sn:≤0.0005%,as:≤0.0005%,sb:≤0.0005%,bi:≤0.0005%,采用连铸工艺将钢水浇铸成连铸坯;
20.(2)轧前加热:使组织完全奥氏体化,元素充分固溶;
21.(3)轧制:包括粗轧和精轧两个阶段,粗轧阶段采用高渗透轧制工艺,开轧温度为1080~1160℃,终轧温度≥960℃,至少2个轧制道次的压下量≥50mm;精轧阶段待温厚度为成品钢板厚度的2~4倍,终轧温度控制在800~840℃,累计压下率为40~60%,轧后采用acc水冷,终冷返红温度控制在670~730℃,冷却速率为3~5℃/s;
22.(4)热处理:采用正火 回火工艺。
23.优选地,步骤(1)钢水冶炼涉及kr铁水预处理、lf精炼、rh真空脱气,钢水精炼时控制a类、b类、c类和d类非金属夹杂物类单项≤1.0级,总和≤2.5级;连铸工序采用低过热度全程氩气保护浇注,通过动态轻压下技术控制铸坯偏析c类1.0级以下,控制钢水连铸过热度为10~20℃。
24.优选地,步骤(2)连铸坯采用分段式加热,总加热时间为250~600min,第二加热段温度为1180~1260℃,均热段温度为1220~1250℃,第二加热段和均热段总加热时间≥120min。
25.优选地,步骤(4)中正火温度为880~900℃,保温时间系数为2.0~2.4min/mm,但不低于30min,出炉水冷,回火温度为530~570℃,保温时间系数为2.5min/mm。
26.本发明采用上述工艺措施和工艺参数适用范围的原理如下:
27.钢的化学成分、碳化物颗粒大小和弥散度、显微组织等因素对钢的热强性产生重要影响。一般而言,高温下晶界为薄弱环节,其强度比晶内低,因此强化晶界是增加钢的热强性的关键措施。由于粗晶粒的晶界总面积比细晶粒少,因此粗晶粒的热强性比细晶粒高,但晶粒过粗,钢的低温韧性较差,显然无法通过晶粒度控制同时兼顾钢的高温性能和低温韧性。从组织类型来看,铁素体组织韧性和塑性较好,但强度较低;粒状贝氏体组织的高温强度较好,但韧性较差。研究表明,nb、v、ti、mo等合金元素,在高温时可以复合析出形成碳化物,通过固溶强化和析出强化能够增加晶界的强度,提高钢的高温性能和综合力学性能。综合上述分析,本发明的设计思路是在c、mn钢的基础上添加cr、mo、nb、v、ti微合金元素,同时严格限制b、pb、sn、as、sb、bi等弱化晶界的有害元素含量,通过控轧控冷和正火 回火热处理工艺进行微观组织调控,得到具有合适比例的铁素体 少量珠光体 粒状贝氏体的混合微观组织和弥散、细小的析出相来获得良好的高温性能和综合机械性能。
28.与现有技术相比,本发明的优点在于:
29.本发明一种200~400℃高温强度优异的sa516gr70钢板,适用于在高温和低温环境中使用,该钢板具有较高的强度、良好的低温韧性和优异的高温拉伸性能。经检测,本发明的高温强度优异的sa516gr70钢板在620
±
10℃
×
12h模拟焊后热处理条件下,屈服强度和抗拉强度余量为30mpa以上,心部-30℃横向夏比冲击功单值≥100j,200~400℃高温拉伸的屈服强度≥320mpa,抗拉强度≥500mpa。通过所述正火 回火热处理工序制备的钢板具有(以面积%计)由65~80%的铁素体 10~15%的珠光体 10~20%的粒状贝氏体组成的混合显微组织,其中粒状贝氏体组织呈团簇状分布。其典型形貌详见附图1。
附图说明
30.图1为本发明钢板的典型微观结构图。
具体实施方式
31.以下结合实施例对本发明作进一步详细描述,所述实施例是示例性的,旨在用于解释本发明,而不能理解为对本发明的限制。
32.实施例1
33.本实施例的高温强度优异的sa516gr70钢板厚度为8mm,采用150mm连铸坯生产,其化学成分按重量百分比计为c:0.17%,si:0.28%,mn:1.42%,p:0.005%,s:0.0008%,ni:0.15%,mo:0.07%,cr:0.17%,nb:0.015%,v:0.025%,ti:0.015%,alt:0.032%,b:0.0003%,pb:0.0001%,sn:0.0002%,as:0.0002%,sb:0.0001%,bi:0.0002%,余量为fe及不可避免的杂质元素。
34.该钢板的制造工艺如下:
35.(1)冶炼浇铸工艺:选用优质冶炼原料,控制有害元素pb:≤0.0005%,sn:≤0.0005%,as:≤0.0005%,sb:≤0.0005%,bi:≤0.0005%。冶炼原料依次经kr铁水预处理、lf精炼、rh真空脱气和连铸工序。精炼工序采用超纯净钢冶炼工艺,控制a类、b类、c类和d类非金属夹杂物类单项≤1.0级,其总和≤2.5级;连铸工序采用低过热度全程氩气保护浇注,通过动态轻压下技术控制铸坯偏析c类1.0级以下,本实施例中连铸钢水过热度为18℃。
36.(2)加热工艺:连铸坯采用分段式加热,总加热时间为250min,第二加热段温度为1180~1260℃,均热段温度为1220~1250℃,第二加热段和均热段总加热时间为130min。
37.(3)轧制工艺:轧制分为粗轧和精轧两个阶段。粗轧阶段采用高渗透轧制工艺,开轧温度为1120℃,终轧温度为980℃,压下量≥50mm的轧制道次为2个,分别为52mm、50mm。精轧阶段待温厚度为成品钢板厚度的4.0倍,终轧温度为820℃,累计压下率为56%,轧后采用acc水冷,终冷返红温度为710℃,冷却速率为4.2℃/s。
38.(4)热处理工艺:采用正火 回火工艺,正火温度为890℃,保温时间系数为30min,出炉水冷,回火温度为560℃,保温时间系数为2.5min/mm。
39.经由上述制造工艺制得的8mm厚sa516gr70钢板具有匹配良好的力学性能和优异的高温拉伸性能,其力学性能详见表1,钢板探伤满足asme sa578/sa578m标准c级要求。
40.实施例2
41.本实施例的高温强度优异的sa516gr70钢板厚度为50mm,采用370mm连铸坯生产,其化学成分按重量百分比计为c:0.17%,si:0.35%,mn:1.43%,p:0.004%,s:0.0006%,ni:0.17%,mo:0.08%,cr:0.17%,nb:0.018%,v:0.026%,ti:0.012%,alt:0.035%,b:0.0002%,pb:10.0001%,sn:≤0.0001%,as:≤0.0002%,sb:≤0.0002%,bi:≤0.0001%,余量为fe及不可避免的杂质元素。
42.该钢板的制造工艺如下:
43.(1)冶炼浇铸工艺:选用优质冶炼原料,控制有害元素pb:≤0.0005%,sn:≤0.0005%,as:≤0.0005%,sb:≤0.0005%,bi:≤0.0005%。冶炼原料依次经kr铁水预处理、lf精炼、rh真空脱气和连铸工序。精炼工序采用超纯净钢冶炼工艺,控制a类、b类、c类和d类非金属夹杂物类单项≤1.0级,其总和≤2.5级;连铸工序采用低过热度全程氩气保护浇注,通过动态轻压下技术控制铸坯偏析c类1.0级以下,本实施例中连铸钢水过热度为16℃。
44.(2)加热工艺:连铸坯采用分段式加热,总加热时间为480min,第二加热段温度为1180~1260℃,均热段温度为1220~1250℃,第二加热段和均热段总加热时间为220min。
45.(3)轧制工艺:轧制分为粗轧和精轧两个阶段。粗轧阶段采用高渗透轧制工艺,开轧温度为1100℃,终轧温度980℃,压下量≥50mm的轧制道次为3个,分别为55mm、55mm、50mm。精轧阶段待温厚度为成品钢板厚度的3.0倍,终轧温度为820℃,累计压下率为60%,轧后采用acc水冷,终冷返红温度为720℃,冷却速率为3.6℃/s。
46.(4)热处理工艺:采用正火 回火工艺,正火温度为900℃,保温时间系数为2.2min/mm,出炉水冷,回火温度为550℃,保温时间系数为2.5min/mm。
47.经由上述制造工艺制得的50mm厚sa516gr70钢板具有匹配良好的力学性能和优异的高温拉伸性能,其力学性能详见表1,钢板探伤满足asme sa578/sa578m标准c级要求。
48.实施例3
49.本实施例的高温强度优异的sa516gr70钢板厚度为120mm,采用450mm连铸坯生产,其化学成分按重量百分比计为c:0.17%,si:0.32%,mn:1.44%,p:0.0005%,s:0.0005%,ni:0.18%,mo:0.08%,cr:0.14%,nb:0.016%,v:0.028%,ti:0.017%,alt:0.032%,b:0.0004%,pb:0.0001%,sn:0.0002%,as:0.0001%,sb:0.0001%,bi:0.0001%,余量为fe及不可避免的杂质元素。
50.该钢板的制造工艺如下:
51.(1)冶炼浇铸工艺:选用优质冶炼原料,控制有害元素pb:≤0.0005%,sn:≤0.0005%,as:≤0.0005%,sb:≤0.0005%,bi:≤0.0005%。冶炼原料依次经kr铁水预处理、lf精炼、rh真空脱气和连铸工序。精炼工序采用超纯净钢冶炼工艺,控制a类、b类、c类和d类非金属夹杂物类单项≤1.0级,其总和≤2.5级;连铸工序采用低过热度全程氩气保护浇注,通过动态轻压下技术控制铸坯偏析c类1.0级以下,本实施例中连铸钢水过热度为17℃。
52.(2)加热工艺:连铸坯采用分段式加热,总加热时间为600min,第二加热段温度为1180~1260℃,均热段温度为1220~1250℃,第二加热段和均热段总加热时间为280min。
53.(3)轧制工艺:轧制分为粗轧和精轧两个阶段。粗轧阶段采用高渗透轧制工艺,开轧温度为1150℃,终轧温度为1000℃,压下量≥50mm的轧制道次为4个,分别为51mm、51mm、50mm、50mm。精轧阶段待温厚度为成品钢板厚度的2.0倍,终轧温度控制在810℃,累计压下率为52%,轧后采用acc水冷,终冷返红温度为710℃,冷却速率为4.6℃/s。
54.(4)热处理工艺:采用正火 回火工艺,正火温度为900℃,保温时间系数为2.4min/mm,出炉水冷,回火温度为550℃,保温时间系数为2.5min/mm。
55.经由上述制造工艺制得的120mm厚sa516gr70钢板具有匹配良好的力学性能和优异的高温拉伸性能,其力学性能详见表1,钢板探伤满足asme sa578/sa578m标准c级要求。
56.表1各实施例所生产钢板的模拟焊后热处理状态下的力学性能
[0057][0058]
注:模拟焊后热处理制度:620
±
10℃
×
12h,≤400℃进出炉,升降温速度≤55℃/h。
[0059]
取样位置:钢板厚度1/2处。
[0060]
除上述实施例外,本发明还包括有其他实施方式,凡采用等同变换或者等效替换方式形成的技术方案,均应落入本发明权利要求的保护范围之内。
再多了解一些
本文用于创业者技术爱好者查询,仅供学习研究,如用于商业用途,请联系技术所有人。