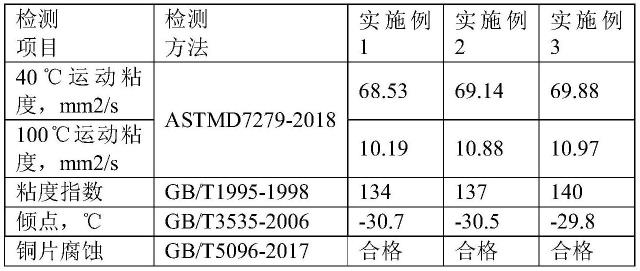
1.本发明涉及润滑材料技术领域,尤其涉及提高轴承质量的微润滑新材料及制备方法和轴承处理方法。
背景技术:
2.轴承作为机械设备中不可或缺的核心零部件,支撑机械旋转体,降低摩擦系数并保证回转精度。无论飞机、汽车、高铁,还是高精密机床、仪器仪表,“凡是旋转的部分,都需要轴承”。当机器或设备运转时,其中作相对运动零件的表面上几乎不可避免地发生摩擦和磨损,润滑则是控制摩擦、减少磨损的常用技术手段。润滑材料是指能够起到减磨、降磨作用,并具有特定的物理、化学性能的物质,这种物质加入到相互作用的对偶表面之间,能够起到承载负荷、降低对偶表面之间的摩擦系数、减少对偶表面材料磨损的作用。
3.目前,国产轴承在尺寸公差与旋转精度、高速性能、润滑介质、振动及噪声控制、轴承材料、服役寿命与可靠性等方面均与进口轴承存在较大差距。润滑介质的优劣是影响轴承质量的重要因素之一,加强对润滑介质的研究,对提高轴承性能、使用寿命等具有重要的意义。
技术实现要素:
4.本发明的目的在于提供一种提高轴承质量的微润滑新材料及制备方法和轴承处理方法,用于克服现有国产普通轴承质量较差、无法满足使用需求的问题。
5.为了实现上述目的,本发明提供如下技术方案:
6.一种提高轴承质量的微润滑新材料,包括以下重量份的组分:精制纳米硼传驱动复合剂0.5~2份、抗磨剂0.5~1.2份、防锈剂0.1~0.3份、分散剂1.0~10.0 份、油性剂0.2~0.8份、摩擦改进剂1.0~5.0份、聚α烯烃0.021~0.208份。
7.优选地,所述精制纳米硼传驱动复合剂包括经杂醇油改性处理的纳米硼酸盐和纳米氮化硼,其中,所述精制纳米硼传驱动复合剂中,纳米硼酸盐的粒径为5nm~50nm,纳米氮化硼的粒径为5nm~50nm,所述精制纳米硼传驱动复合剂中,杂醇油、纳米硼酸盐与纳米氮化硼的重量比为(0.05~0.2):(0.2~1.0): (0.25~0.8)。
8.优选地,所述抗磨剂包括第一抗磨剂和第二抗磨剂;所述第一抗磨剂为长链伯烷基二硫代磷酸锌,所述第二抗磨剂为伯烷基二硫代磷酸锌;所述抗磨剂中,所述第一抗磨剂和第二抗磨剂的重量比为(0.3~0.6):(0.2~0.6)。
9.优选地,包括以下重量份的组分:精制纳米硼传驱动复合剂0.8~1.6份、第一抗磨剂0.32~0.45份、第二抗磨剂0.55~0.6份、防锈剂0.18~0.23份、分散剂 5.0~7.0份、油性剂0.2~0.4份、摩擦改进剂2.5~3.5份、聚α烯烃0.042~0.185 份。
10.优选地,所述防锈剂为二聚酸和磷酸酯、烯基丁二酸、碱性二壬基奈磺酸钡中的任意一种或几种;和/或,所述防锈剂为二聚酸和磷酸酯时,所述二聚酸和磷酸酯重量比为(0.04~0.2):(0.06~0.1);和/或,所述二聚酸中二聚酸的重量百分比≥95%,所述磷酸酯
为二(2-乙基己基)磷酸酯;和/或,所述分散剂为双烯基丁二酰亚胺;和/或,所述摩擦改进剂为磷酸酯,所述磷酸酯中磷酸单酯的重量百分比为25%~45%,磷酸双酯的重量百分比为55%~75%;和/或,所述油性剂为油酸乙二醇酯、苯三唑脂肪胺酸盐、硫化烯烃棉籽油;和/或,所述油性剂中,所述油酸乙二醇酯、苯三唑脂肪胺酸盐、硫化烯烃棉籽油的重量比为(0.05~0.3):(0.1~0.3):(0.05~0.2)。
11.优选地,所述聚α烯烃由低粘度聚α烯烃和中粘度聚α烯烃组成,所述聚α烯烃中,所述低粘度聚α烯烃和中粘度聚α烯烃的重量比为(0.018~0.2): (0.003~0.008)。
12.本发明还提供一种提高轴承质量的微润滑新材料的制备方法,包含以下步骤:
13.将聚α烯烃和精制纳米硼传驱动复合剂混合,于40℃~60℃加温处理 10min~30min,得混合物i;
14.将1/2~3/5重量的抗磨剂、分散剂、摩擦改进剂、1/2~2/3重量的油性剂于 50℃~60℃混合10min~30min,得混合物ii;
15.将剩余的抗磨剂、防锈剂于70℃~80℃混合10min~30min,得混合物ⅲ;
16.将混合物ⅰ、混合物ii、混合物ⅲ混合均匀,加入剩余的油性剂,于80℃~90℃混合30min~40min,自然冷却至50℃,过滤,即得成品。
17.本发明还提供一种功能型润滑脂,包括上述提高轴承质量的微润滑新材料。
18.本发明还提供一种轴承处理方法,包括以下步骤:
19.(1)组装前处理:将轴承配件超声波清洗后,烘干;
20.(2)浸泡处理:在工艺浸泡槽内放入微润滑材料,保持微润滑新材料循环流动,并将步骤(1)处理后的轴承配件浸入工艺浸泡槽内,80℃~180℃浸泡 12h-48h;
21.(3)晶格闭合:将步骤(2)浸泡处理后的轴承配件淋净、擦净、晶格闭合1.5h~24h;
22.(4)组装:将步骤(3)晶格闭合后的轴承配件按照轴承技术规范组装成轴承;
23.(5)轴承磨合运转:将步骤(4)中组装好的轴承安装于轴承专业检测设备,并将安装好的轴承完全浸入微润滑新材料中,磨合运转4h~8h;
24.(6)涂抹功能型润滑脂:将步骤(5)中经过磨合的轴承淋净、擦净、晶格闭合后,涂抹功能型润滑脂;
25.(7)检验、封装。
26.优选地,所述功能型润滑脂的涂抹量为≤轴承空腔的50%。
27.有益技术效果:(1)本发明提供了一种提高轴承质量的微润滑新材料,包括以下重量份的组分:精制纳米硼传驱动复合剂0.5~2份、抗磨剂0.5~1.2份、防锈剂0.1~0.3份、分散剂1.0~10.0份、油性剂0.2~0.8份、摩擦改进剂1.0~5.0 份、聚α烯烃0.021~0.208份。本发明将精制纳米硼传驱动复合剂和聚α烯烃配合使用,使得精制纳米硼传驱动复合剂的分散性和油溶性大幅度提高,配合材料中的其它组分,均匀快速地填充到轴承表面的凹面区域,修复轴承材料表面的微瑕疵,使轴承表面平滑,进而提高轴承的性能和使用寿命。
28.(2)本发明提供的一种提高轴承质量的微润滑新材料,采用杂醇油改性处理纳米硼酸盐和纳米氮化硼,杂醇油主要成分为异戊醇、丁醇、丙醇和庚醇,纳米硼酸盐和纳米氮化硼经杂醇油改性处理后,杂醇油吸附于纳米硼酸盐和纳米氮化硼的表面,使得纳米硼酸盐和纳米氮化硼表面吸附有羟基基团。由于杂醇油中含有不同分子链长的醇,可以起到对纳米硼酸盐和纳米氮化硼表面叠加缠绕的作用,更有利于对纳米硼酸盐和纳米氮化硼表面
进行吸附包覆,使得纳米硼酸盐和纳米氮化硼之间分散更均匀。同时,本发明包覆于纳米硼酸盐和纳米氮化硼表面的杂醇油,通过与聚α烯烃提前混合,使聚α烯烃也更好地包覆于纳米硼酸盐和纳米氮化硼表面,实现对纳米硼酸盐和纳米氮化硼的双层包覆。再与抗磨剂、分散剂、油性剂等其他组份混合后,可以使各组分混合得更加均匀。将本发明所述微润滑新材料用于轴承后,由于纳米硼酸盐和纳米氮化硼被杂醇油和聚α烯烃进行双层全包覆,在轴承高速运转过程中,一方面杂醇油中含有不同链长的分子,由于分子量不同,受轴承高速运转过程中产生的热量影响不同,使得纳米硼酸盐和纳米氮化硼表面始终有杂醇油和聚α烯烃包覆而不易析出,再与其他组份共同作用,可以大大增强了微润滑新材料的抗磨、润滑性能,并且大大降低由于纳米硼酸盐和纳米氮化硼析出对轴承的磨损,提升了微润滑新材料的整体性能;另一方面,本发明微润滑新材料在后续制备功能性润滑脂时,由于体系中提前混合了聚α烯烃,使得本发明的微润滑新材料与基础油的混合更均匀、分散性更好。经试验验证,提前使用杂醇油和聚α烯烃对纳米氮化硼和纳米硼酸盐进行双层全包覆,可显著提高微润滑新材料的摩擦性能,应用于轴承后,可有效降低轴承噪音,提高轴承使用寿命。
29.(3)本发明还提供了一种微润滑新材料的制备方法,与现有技术相比,本发明提供的微润滑新材料的制备方法的有益效果与微润滑新材料的有益效果相同,此处不做赘述。
30.(4)本发明提供的一种轴承处理方法,省略了现有技术在组装时涂抹润滑脂的操作,通过对轴承组件的浸泡及磨合运转,使微润滑新材料渗入轴承表面,不仅可以修复轴承制造及安装过程的表面损伤,还可以使轴承表面均匀附着微润滑新材料,使轴承可以长时间保持润滑状态,提高轴承的性能及寿命,使普通轴承可以达到高端轴承的效果。
具体实施方式
31.为了使本发明所要解决的技术问题、技术方案及有益效果更加清楚明白,以下结合实施例,对本发明进行进一步详细说明。应当理解,此处所描述的具体实施例仅仅用以解释本发明,并不用于限定本发明。
32.本发明实施例中所采用的原料如非特殊说明,均为市售产品。
33.本发明提供一种提高轴承质量的微润滑新材料,包括以下重量份的组分:精制纳米硼传驱动复合剂0.5~2份、抗磨剂0.5~1.2份、防锈剂0.1~0.3份、分散剂1.0~10.0份、油性剂0.2~0.8份、摩擦改进剂1.0~5.0份、聚α烯烃0.021~0.208 份。
34.在本发明中,所述精制纳米硼传驱动复合剂包括经杂醇油改性处理的纳米硼酸盐和纳米氮化硼;所述杂醇油中异戊醇的重量百分比优选为≥55%,更优选为≥60%;通过使用符合上述要求的杂醇油对纳米硼酸盐和纳米氮化硼改性,减少杂醇油中小分子量醇及大分子量醇的含量,进而调整杂醇油对纳米硼酸盐和纳米氮化硼表面的叠加缠绕效果,更有利于对纳米硼酸盐和纳米氮化硼表面进行吸附包覆。所述改性处理后的纳米硼酸盐和纳米氮化硼的粒径优选为 5nm~50nm,更优选为20nm~30nm;所述精制纳米硼传驱动复合剂中,杂醇油、纳米硼酸盐与纳米氮化硼的重量比优选为(0.05~0.2):(0.2~1.0):(0.25~0.8),更优选为(0.12~0.16):(0.6~0.8):(0.45~0.65)。改性处理的纳米硼酸盐和纳米氮化硼被杂醇油吸附包覆,使得纳米硼酸盐和纳米氮化硼之间分散更均匀,在后续处理过程中不易团聚,且可以利用杂醇油中含有不同链长的分子,使其在应用于轴承时,受轴承高速运转过程中产生热量的影响不同,延长对纳米硼酸盐和纳米氮化硼的保护时长,进而降
低由于纳米硼酸盐和纳米氮化硼析出对轴承的磨损,提升微润滑新材料的整体性能。
35.在本发明中,所述抗磨剂包括第一抗磨剂和第二抗磨剂;所述第一抗磨剂为长链伯烷基二硫代磷酸锌,所述第二抗磨剂为伯烷基二硫代磷酸锌;所述长链伯烷基二硫代磷酸锌优选为t203,所述伯烷基二硫代磷酸锌优选为t202;所述抗磨剂中,所述第一抗磨剂和第二抗磨剂的重量比为(0.3~0.6):(0.2~0.6)。第一抗磨剂和第二抗磨剂协调使用,可以提高增强微润滑新材料在空气中循环使用的稳定性,提高轴承的抗磨性能。
36.在本发明中,优选包括以下重量份的组分:精制纳米硼传驱动复合剂0.8~1.6 份、第一抗磨剂0.32~0.45份、第二抗磨剂0.55~0.6份、防锈剂0.18~0.23份、分散剂5.0~7.0份、油性剂0.2~0.4份、摩擦改进剂2.5~3.5份、聚α烯烃 0.042~0.185份。
37.在本发明中,所述防锈剂为二聚酸和磷酸酯、烯基丁二酸、碱性二壬基奈磺酸钡中的任意一种或几种;所述防锈剂优选为二聚酸和磷酸酯,所述二聚酸和磷酸酯的重量比优选为(0.04~0.2):(0.06~0.1),更优选为(0.09~0.13): (0.08~0.09);所述二聚酸中二聚酸的重量百分比优选为≥95%,更优选为≥97%;所述磷酸酯为二(2-乙基己基)磷酸酯。所述二聚酸和磷酸酯配合使用,能够有效将摩擦表面与水、空气隔开,实现防腐蚀、防锈蚀、防盐雾、防海游生物寄生的作用。
38.在本发明中,所述分散剂为双烯基丁二酰亚胺,所述分散剂既能防止不溶性聚合物的生成,又能防止因氧化和杂质混入产生的不溶解组分分散在油中而形成油泥和漆皮。
39.在本发明中,所述摩擦改进剂为磷酸酯,所述磷酸酯中磷酸单酯的重量百分比优选为25%~45%,更优选为28%~33%;磷酸双酯的重量百分比优选为 55%~75%,更优选为67%~72%。磷酸单酯的水溶性、乳化性和抗静电性较好,磷酸双酯的平滑性较好,通过控制磷酸酯中磷酸单酯和磷酸双酯的比例,使磷酸单酯和磷酸双酯协调作用,各种性能达到最优,更好地与其它组分配合,进而提升轴承的高载荷运转能力,减少摩擦和磨损,延长轴承的使用寿命。
40.在本发明中,所述油性剂为油酸乙二醇酯、苯三唑脂肪胺酸盐、硫化烯烃棉籽油;所述油性剂中,所述油酸乙二醇酯、苯三唑脂肪胺酸盐、硫化烯烃棉籽油的重量比优选为(0.05~0.3):(0.1~0.3):(0.05~0.2),更优选为(0.15~0.2):(0.18~0.25):(0.13~0.18)。通过油酸乙二醇酯、苯三唑脂肪胺酸盐、硫化烯烃棉籽油产生的协同效应,有效阻止摩擦副之间的接触,起到减少摩擦和磨损,防止磨损的作用。
41.在本发明中,所述聚α烯烃由低粘度聚α烯烃和中粘度聚α烯烃组成,所述聚α烯烃中,所述低粘度聚α烯烃和中粘度聚α烯烃的重量比优选为(0.018~0.2):(0.003~0.008),更优选为(0.07~0.15):(0.005~0.006)。聚α烯烃为全合成的高档基础油,粘温指数空间大,适应低温和高温,通过合理控制聚α烯烃中低粘度聚α烯烃和中粘度聚α烯烃的重量比,可以使聚α烯烃更好地包覆于改性纳米硼酸盐和纳米氮化硼的表面,实现对纳米硼酸盐和纳米氮化硼的双层包覆,不仅可以可显著提高微润滑新材料的摩擦性能,应用于轴承后,有效降低轴承噪音,提高轴承使用寿命,还可以使本发明的微润滑新材料在后续制备功能性润滑脂时与基础油的混合更均匀、分散性更好。
42.本发明还提供一种提高轴承质量的微润滑新材料的制备方法的实施例,包含以下步骤:
43.s1、将聚α烯烃和精制纳米硼传驱动复合剂混合,于40℃~60℃加温处理 10min~
30min,得混合物i。
44.上述实施方式中,可以先按如下方法制得精制纳米硼传驱动复合剂:
45.按照比例称取纳米硼酸盐、纳米氮化硼和杂醇油,将纳米硼酸盐和纳米氮化硼加入反应器中,注入加氢汽油使纳米硼酸盐和纳米氮化硼分散均匀,再加入称量好的杂醇油,30℃~40℃恒温水浴反应6h~8h,除去副产物和加氢汽油,得到杂醇油改性的纳米硼酸盐和纳米氮化硼,即精制纳米硼传驱动复合剂。
46.在本发明实施例中,由于杂醇油中含有不同分子链长的醇,可以起到对纳米硼酸盐和纳米氮化硼表面叠加缠绕的作用,更有利于对纳米硼酸盐和纳米氮化硼表面进行吸附包覆,使得纳米硼酸盐和纳米氮化硼之间分散更均匀。
47.再将聚α烯烃和精制纳米硼传驱动复合剂混合,混合温度优选为40℃~60℃,更优选为48℃~53℃;混合时间优选为10min~30min,更优选为20min~28min。
48.在本发明实施例中,通过将精制纳米硼传驱动复合剂与聚α烯烃提前混合,使聚α烯烃更好地包覆于纳米硼酸盐和纳米氮化硼表面,实现对纳米硼酸盐和纳米氮化硼的双层包覆。再与抗磨剂、分散剂、油性剂等其他组份混合后,可以使各组分混合得更加均匀。将本发明所述微润滑新材料用于轴承后,由于纳米硼酸盐和纳米氮化硼被杂醇油和聚α烯烃进行双层全包覆,在轴承高速运转过程中,一方面杂醇油中含有不同链长的分子,由于分子量不同,受轴承高速运转过程中产生的热量影响不同,使得纳米硼酸盐和纳米氮化硼表面始终有杂醇油和聚α烯烃包覆而不易析出,再与其他组份共同作用,可以大大增强了微润滑新材料的抗磨、润滑性能,并且大大降低由于纳米硼酸盐和纳米氮化硼析出对轴承的磨损,提升了微润滑新材料的整体性能;另一方面,本发明微润滑新材料在后续制备功能性润滑脂时,由于体系中提前混合了聚α烯烃,使得本发明的微润滑新材料与基础油的混合更均匀、分散性更好。经试验验证,提前使用杂醇油和聚α烯烃对纳米氮化硼和纳米硼酸盐进行双层全包覆,可显著提高微润滑新材料的摩擦性能,应用于轴承后,可有效降低轴承噪音,提高轴承使用寿命。
49.s2、将1/2~3/5重量的抗磨剂、分散剂、摩擦改进剂、1/2~2/3重量的油性剂于50℃~60℃混合10min~30min,得混合物ii。
50.上述实施方式中,抗磨剂可以选择长链伯烷基二硫代磷酸锌和伯烷基二硫代磷酸锌,分散剂可以选择双烯基丁二酰亚胺,摩擦改进剂可以选择磷酸酯,油性剂可以选择油酸乙二醇酯、苯三唑脂肪胺酸盐、硫化烯烃棉籽油,所述混合物ii中优选包括1/2~3/5重量的抗磨剂;优选包括1/2~2/3重量的油性剂;混合物ii的混合温度优选为50℃~60℃,更优选为55℃;混合时间优选为 10min~30min,更优选为28min。
51.s3、将剩余的抗磨剂、防锈剂于70℃~80℃混合10min~30min,得混合物ⅲ。
52.上述实施方式中,防锈剂可以选择二聚酸和磷酸酯、烯基丁二酸、碱性二壬基奈磺酸钡中的任意一种或几种;剩余的抗磨剂优选为2/5~1/2重量的抗磨剂;混合物ⅲ的混合温度优选为70℃~80℃,更优选为74℃~76℃;混合物ⅲ的混合时间优选为10min~30min,更优选为28min。
53.本发明实施例中,s2、s3将抗磨剂分步与其它组分混合,可以使抗磨剂与其它组分的混合更为均匀,保证抗磨性能。
54.s4、将混合物ⅰ、混合物ii、混合物ⅲ混合均匀,加入剩余的油性剂,于 80℃~90℃
混合30min~40min,自然冷却至50℃,过滤,即得成品。
55.上述实施方式中,所述加入剩余的油性剂后的混合温度优选为80℃~90℃,更优选为84℃~86℃;混合时间优选为30min~40min,更优选为34min~37min;所述自然冷却优选为冷却至50℃。在混合物ⅰ、混合物ii、混合物ⅲ中,通过最后加入剩余的油性剂,可进一步增加各原料成分的油溶性,让各成分充分混合均匀。
56.本发明还提供一种功能型润滑脂,包括所述提高轴承质量的微润滑新材料。
57.在本发明中,所述用来生产功能型润滑油系列产品的基础油优选为iv类基础油或
ⅴ
类基础油;所述微润滑新材料优选以质量百分比为5%~25%的添加量与基础油制备成功能型润滑脂。
58.本发明还提供一种轴承处理方法的实施例,包括以下步骤:
59.(1)组装前处理:将轴承配件超声波清洗后,烘干;
60.上述实施方式中,所述超声波清洗的清洗剂优选为溶剂汽油或煤油;所述超声波清洗的振动频率为110khz~130khz,清洗时间为10min~15min;所述烘干为用70℃~80℃的热空气烘干,烘干时间为5min~7min。
61.(2)浸泡处理:在工艺浸泡槽内放入微润滑材料,保持微润滑新材料循环流动,并将步骤(1)处理后的轴承配件浸入工艺浸泡槽内,80℃~180℃浸泡 12h-48h;
62.上述实施方式中,所述浸泡处理的浸泡容器为合金铝工艺槽,所述合金铝工艺槽的容积为100l,槽内壁设置格挡及泵阀,所述泵阀的电机功率为0.55kw;所述微润滑材料的加入量优选为可将轴承配件完全浸入;在本发明中,所述浸泡优选为保持微润滑新材料循环流动,所述循环流动优选为利用液压泵泵送使微润滑新材料不停撞击轴承配件;其中,所述液压泵可以选择双作用叶片泵,工作压力为6.3mpa~21mpa,转速为500r/min~4000r/min,排量为5m3~300m3,容积效率为0.8~0.9,流量稳定性好。循环流动可使轴承与微润滑新材料充分接触,且利用撞击的冲击力,使微润滑新材料更好地渗透轴承表层。
63.上述实施方式中,所述浸泡的浸泡温度优选为80℃~180℃,更优选为150℃~160℃;浸泡时间优选为12h-48h,更优选为28h。
64.(3)晶格闭合:将步骤(2)浸泡处理后的轴承配件淋净、擦净、晶格闭合1.5h~24h;
65.上述实施方式中,所述淋净为用溶剂汽油或煤油淋洗轴承表面;所述擦净为淋净后用干净的软布擦干;所述晶格闭合为常温自然冷却,使金属晶格表面冷缩闭合;所述晶格闭合时间优选为1.5h~24h,更优选为13h。
66.(4)组装:将步骤(3)晶格闭合后的轴承配件按照轴承技术规范组装成轴承;
67.上述实施方式中,所述轴承技术规范为gb/t 27555-2011滚动轴承带座外球面球轴承技术条件;所述组装的过程不包含常规的涂抹润滑脂。
68.(5)轴承磨合运转:将步骤(4)中组装好的轴承安装于轴承专业检测设备,并将安装好的轴承完全浸入微润滑新材料中,磨合运转4h~8h;
69.上述实施方式中,所述轴承专业检测设备可以选择bts100轴承寿命预测性实验台;bts100轴承寿命预测性实验台,是一种可维持轴承长时间运转并测试轴承早期磨损的实验设备,也可添加预制的故障轴承进行轴承故障模拟仿真等项目,测试各种有缺陷的轴承,应用广泛;bts100轴承寿命预测性实验台的设计可适用于各种外径的轴承座和轴承适配器,能够试验各种尺寸的轴承;轴承支撑在轴的末端,并在轴承额定载荷下,另外可在轴
承上施加负载达2kn。
70.在上述实施方式中,所述磨合运转优选为将安装好的轴承完全浸入微润滑新材料中;所述磨合运转时间优选为4h~8h;更优选为6h~7h。上述实施方式中,所述磨合运转优选为在流动条件下磨合运转;所述流动条件优选为驱动电机和液压泵顺时针喷射工件;所述驱动电机可以选择高效节能abb三相交流电动机,功率2hp,线对线电阻6.0ω@25℃,定子槽数36,转子条数28,电机功率因数 82.5%;所述液压泵可以选择双作用叶片泵,工作压力为6.3mpa~21mpa,转速为500r/min~4000r/min,排量为5m3~300m3,容积效率为0.8~0.9,流量稳定性好。本发明实施例中,磨合运转结合流动条件能够有效提高微润滑新材料的物理、化学渗透吸附效率,进而提升成品轴承的整体性能。
71.(6)涂抹功能型润滑脂:将步骤(5)中经过磨合的轴承淋净、擦净、晶格闭合后,涂抹功能型润滑脂;
72.上述实施方式中,所述淋净、擦净、晶格闭合与步骤(3)中的淋净、擦净、晶格闭合相同;所述功能型润滑脂的涂抹量优选为≤轴承空腔的50%。
73.(7)检验、封装。
74.上述实施方式中,按照常规方法对轴承进行检验、封装。
75.为了更好地理解本发明,下面结合实施例进一步阐明本发明的内容,但本发明的内容不仅仅局限于下面的实施例。
76.实施例1
77.本实施例提高轴承质量的微润滑新材料包括以下重量份的组分:精制纳米硼传驱动复合剂0.5份、抗磨剂1.2份、防锈剂0.1份、分散剂1.0份、油性剂 0.2份、摩擦改进剂5.0份、聚α烯烃0.021份。
78.其中,纳米硼传驱动复合剂中纳米硼酸盐的粒径为5nm,纳米氮化硼的粒径为5nm,杂醇油、纳米硼酸盐与纳米氮化硼的重量比为0.05:0.2:0.25;抗磨剂为长链伯烷基二硫代磷酸锌和伯烷基二硫代磷酸锌,长链伯烷基二硫代磷酸锌和伯烷基二硫代磷酸锌分别为t203和t202,t203和t202的重量比为0.3: 0.2;分散剂为双烯基丁二酰亚胺;摩擦改进剂为磷酸酯,磷酸酯中磷酸单酯的重量百分比为25%,磷酸双酯的重量百分比为75%;油性剂为油酸乙二醇酯、苯三唑脂肪胺酸盐、硫化烯烃棉籽油,油酸乙二醇酯、苯三唑脂肪胺酸盐、硫化烯烃棉籽油的重量比为0.05:0.1:0.05;防锈剂为二聚酸和磷酸酯,二聚酸和磷酸酯的重量比为0.04:0.06,二聚酸中二聚体的重量百分比为95%,磷酸酯为二(2-乙基己基)磷酸酯。
79.提高轴承质量的微润滑新材料的制备方法:
80.先制备精制纳米硼传驱动复合剂:按照比例称取纳米硼酸盐、纳米氮化硼和杂醇油,将纳米硼酸盐和纳米氮化硼加入反应器中,注入加氢汽油使纳米硼酸盐和纳米氮化硼分散均匀,再加入称量好的杂醇油,30℃恒温水浴反应8h,除去副产物和加氢汽油,得到杂醇油改性的纳米硼酸盐和纳米氮化硼,即精制纳米硼传驱动复合剂;再将聚α烯烃和精制纳米硼传驱动复合剂混合,于40℃加温处理30min,得混合物i;将1/2重量的t203和t202、双烯基丁二酰亚胺、磷酸酯、1/2重量的油酸乙二醇酯、苯三唑脂肪胺酸盐、硫化烯烃棉籽油于50℃混合30min,得混合物ii;将剩余的t203和t202、二聚酸和二(2-乙基己基)磷酸酯于70℃混合30min,得混合物ⅲ;将混合物ⅰ、混合物ii、混合物ⅲ混合均匀,加入剩余的油酸乙二醇
酯、苯三唑脂肪胺酸盐、硫化烯烃棉籽油,于 80℃混合40min,自然冷却至50℃,过滤,即得成品。
81.将获得的微润滑新材料以质量百分比为5%的添加量与iv类基础油制备成功能型润滑脂。
82.轴承处理方法包括:将轴承配件用溶剂汽油于110khz超声波清洗15min 后,用70℃热空气烘干7min;将烘干后的轴承配件放入设置有格挡和泵阀的工艺浸泡槽内,并在工艺浸泡槽内放入可使轴承配件完全浸入的微润滑材料,开启泵阀,保持微润滑新材料循环流动,80℃浸泡48h;将浸泡处理后的轴承配件用汽油淋净,干净软布擦净后常温自然冷却1.5h;将冷却后的轴承配件按照gb/t 27555-2011滚动轴承带座外球面球轴承技术条件组装成轴承;将组装好的轴承安装于bts100轴承寿命预测性实验台,并将安装好的轴承完全浸入微润滑新材料中,磨合运转4h;将经过磨合的轴承淋净、擦净、晶格闭合后,涂抹上述的功能型润滑脂;检验、封装。
83.实施例2
84.本实施例提高轴承质量的微润滑新材料包括以下重量份的组分:精制纳米硼传驱动复合剂2份、抗磨剂0.5份、防锈剂0.3份、分散剂10.0份、油性剂 0.8份、摩擦改进剂1.0份、聚α烯烃0.208份。
85.其中,纳米硼传驱动复合剂中纳米硼酸盐的粒径为50nm,纳米氮化硼的粒径为50nm,杂醇油、纳米硼酸盐与纳米氮化硼的重量比为0.2:1.0:0.8;抗磨剂为长链伯烷基二硫代磷酸锌和伯烷基二硫代磷酸锌,长链伯烷基二硫代磷酸锌和伯烷基二硫代磷酸锌分别为t203和t202,t203和t202的重量比为0.3: 0.6;分散剂为双烯基丁二酰亚胺;摩擦改进剂为磷酸酯,磷酸酯中磷酸单酯的重量百分比为40%,磷酸双酯的重量百分比为50%;油性剂为油酸乙二醇酯、苯三唑脂肪胺酸盐、硫化烯烃棉籽油,油酸乙二醇酯、苯三唑脂肪胺酸盐、硫化烯烃棉籽油的重量比为0.3:0.3:0.2;防锈剂为二聚酸和磷酸酯、烯基丁二酸,二聚酸和磷酸酯的重量比为0.2:0.1,二聚酸中二聚体的重量百分比为96%,磷酸酯为二(2-乙基己基)磷酸酯。
86.提高轴承质量的微润滑新材料的制备方法:
87.先制备精制纳米硼传驱动复合剂:按照比例称取纳米硼酸盐、纳米氮化硼和杂醇油,将纳米硼酸盐和纳米氮化硼加入反应器中,注入加氢汽油使纳米硼酸盐和纳米氮化硼分散均匀,再加入称量好的杂醇油,40℃恒温水浴反应6h,除去副产物和加氢汽油,得到杂醇油改性的纳米硼酸盐和纳米氮化硼,即精制纳米硼传驱动复合剂;再将聚α烯烃和精制纳米硼传驱动复合剂混合,于60℃加温处理10min,得混合物i;将3/5重量的t203和t202、双烯基丁二酰亚胺、磷酸酯、2/3重量的油酸乙二醇酯、苯三唑脂肪胺酸盐、硫化烯烃棉籽油于60℃混合10min,得混合物ii;将剩余的t203和t202、二聚酸和二(2-乙基己基)磷酸酯、烯基丁二酸于80℃混合10min,得混合物ⅲ;将混合物ⅰ、混合物ii、混合物ⅲ混合均匀,加入剩余的油酸乙二醇酯、苯三唑脂肪胺酸盐、硫化烯烃棉籽油,于90℃混合30min,自然冷却至50℃,过滤,即得成品。
88.将获得的微润滑新材料以质量百分比为25%的添加量与v类基础油制备成功能型润滑脂。
89.轴承处理方法包括:将轴承配件用溶剂汽油于120khz超声波清洗12min 后,用75
℃热空气烘干6min;将烘干后的轴承配件放入设置有格挡和泵阀的工艺浸泡槽内,并在工艺浸泡槽内放入可使轴承配件完全浸入的微润滑材料,开启泵阀,保持微润滑新材料循环流动,180℃浸泡12h;将浸泡处理后的轴承配件用汽油淋净,干净软布擦净后常温自然冷却24h;将冷却后的轴承配件按照 gb/t 27555-2011滚动轴承带座外球面球轴承技术条件组装成轴承;将组装好的轴承安装于bts100轴承寿命预测性实验台,并将安装好的轴承完全浸入微润滑新材料中,磨合运转8h;将经过磨合的轴承淋净、擦净、晶格闭合后,涂抹上述的功能型润滑脂;检验、封装。
90.实施例3
91.本实施例提高轴承质量的微润滑新材料包括以下重量份的组分:精制纳米硼传驱动复合剂1.5份、抗磨剂0.8份、防锈剂0.2份、分散剂6.0份、油性剂 0.5份、摩擦改进剂3.2份、聚α烯烃0.13份。
92.其中,纳米硼传驱动复合剂中纳米硼酸盐的粒径为30nm,纳米氮化硼的粒径为20nm,杂醇油、纳米硼酸盐与纳米氮化硼的重量比为0.12:0.6:0.45;抗磨剂为长链伯烷基二硫代磷酸锌和伯烷基二硫代磷酸锌,长链伯烷基二硫代磷酸锌和伯烷基二硫代磷酸锌分别为t203和t202,t203和t202的重量比为0.5: 0.3;分散剂为双烯基丁二酰亚胺;摩擦改进剂为磷酸酯,磷酸酯中磷酸单酯的重量百分比为28%,磷酸双酯的重量百分比为72%;油性剂为油酸乙二醇酯、苯三唑脂肪胺酸盐、硫化烯烃棉籽油,油酸乙二醇酯、苯三唑脂肪胺酸盐、硫化烯烃棉籽油的重量比为0.3:0.3:0.2;防锈剂为二聚酸和磷酸酯、碱性二壬基奈磺酸钡,二聚酸和磷酸酯的重量比为0.13:0.09,二聚酸中二聚体的重量百分比为98%,磷酸酯为二(2-乙基己基)磷酸酯。
93.其中,纳米硼传驱动复合剂中纳米硼酸盐的粒径为30纳米,纳米氮化硼的粒径为30纳米,杂醇油、纳米硼酸盐与纳米氮化硼添加量比为0.12:0.6:0.45;抗磨剂为长链伯烷基二硫代磷酸锌和伯烷基二硫代磷酸锌,分散剂为双烯基丁二酰亚胺,摩擦改进剂为磷酸酯,油性剂为油酸乙二醇酯、苯三唑脂肪胺酸盐、硫化烯烃棉籽油;防锈剂为二聚酸和磷酸酯、碱性二壬基奈磺酸钡。
94.提高轴承质量的微润滑新材料的制备方法:
95.先制备精制纳米硼传驱动复合剂:按照比例称取纳米硼酸盐、纳米氮化硼和杂醇油,将纳米硼酸盐和纳米氮化硼加入反应器中,注入加氢汽油使纳米硼酸盐和纳米氮化硼分散均匀,再加入称量好的杂醇油,35℃恒温水浴反应5h,除去副产物和加氢汽油,得到杂醇油改性的纳米硼酸盐和纳米氮化硼,即精制纳米硼传驱动复合剂;再将聚α烯烃和精制纳米硼传驱动复合剂混合,于50℃加温处理20min,得混合物i;将3/5重量的t203和t202、双烯基丁二酰亚胺、磷酸酯、2/3重量的油酸乙二醇酯、苯三唑脂肪胺酸盐、硫化烯烃棉籽油于55℃混合20min,得混合物ii;将剩余的t203和t202、二聚酸和二(2-乙基己基)磷酸酯、碱性二壬基奈磺酸钡于75℃混合20min,得混合物ⅲ;将混合物ⅰ、混合物ii、混合物ⅲ混合均匀,加入剩余的油酸乙二醇酯、苯三唑脂肪胺酸盐、硫化烯烃棉籽油,于85℃混合35min,自然冷却至50℃,过滤,即得成品。
96.将获得的微润滑新材料以质量百分比为15%的添加量与v类基础油制备成功能型润滑脂。
97.轴承处理方法包括:将轴承配件用煤油于130khz超声波清洗10min后,用80℃热空
气烘干5min;将烘干后的轴承配件放入设置有格挡和泵阀的工艺浸泡槽内,并在工艺浸泡槽内放入可使轴承配件完全浸入的微润滑材料,开启泵阀,保持微润滑新材料循环流动,150℃浸泡24h;将浸泡处理后的轴承配件用汽油淋净,干净软布擦净后常温自然冷却18h;将冷却后的轴承配件按照gb/t 27555-2011滚动轴承带座外球面球轴承技术条件组装成轴承;将组装好的轴承安装于bts100轴承寿命预测性实验台,并将安装好的轴承完全浸入微润滑新材料中,磨合运转6h;将经过磨合的轴承淋净、擦净、晶格闭合后,涂抹上述的功能型润滑脂;检验、封装。
98.对比例1
99.与实施例1相比,本对比例中不添加杂醇油,即纳米氮化硼和纳米硼酸盐不经杂醇油改性处理,其余组分及操作与实施例1相同。
100.对比例2
101.本对比例将实施例1中的聚α烯烃替换为poe酯类,其余组分及操作与实施例1相同。
102.对比例3
103.本对比例的微润滑新材料的组成与实施例1相同,区别在于微润滑新材料在制备时将各组分直接于80℃~90℃混合1h~3h,自然冷却至50℃,过滤,即得成品。本对比例的轴承处理方法也与实施例1相同。
104.对比例4
105.本对比例将实施例1中所得的微润滑新材料替换为32#透平油,轴承处理方法与实施例1相同。
106.对比例5
107.本对比例的微润滑新材料与实施例1相同,区别在于轴承处理方法为常规的轴承处理方法。
108.试验例1
109.下面对上述实施例1~3所得的微润滑新材料进行理化测试,理化检测方法及测试结果见表1。
110.表1润滑材料的理化测试结果
[0111][0112]
试验例2
[0113]
以长城高级润滑油为基础油,分别加入重量百分比为5%的上述实施例1~3 所得的微润滑新材料及对比例1~4的润滑材料调配后,以长城高级润滑油为对照,进行抗磨性能试验:(1)国产sq-3摩擦磨损试验机,钢球为φ12.7mm上海球,试验机转速为1420rpm,室
温17℃,分别经四球长磨30min试验,得到 pb、pd及zmz值,试验结果见表2;(2)falex-6摩擦磨损试验机,钢球材质为gcr15,试验机转速为1420rpm,载荷40kg,加热温度80℃,以点接触的形式,分别进行四球长磨试验30min,试验结果见表3。
[0114]
表2润滑材料的抗磨测试结果1
[0115]
检测项目实施例1实施例2实施例3对比例1对比例2对比例3对比例4pb,n9819811049593782815441pd,n1961245225311425152817621236zmz,n424424428317352394191
[0116]
由表2可以看出,实施例1~3的pb(最大无卡咬负荷)最高可达1049n, pd(烧结负荷)最高可达2531n,zmz(综合磨损指数)最高可达428n,均由于对比例1~4。
[0117]
表3润滑材料的抗磨测试结果2
[0118]
检测项目实施例1实施例2实施例3对比例1对比例2对比例3对比例4x向直径,mm0.570.560.571.731.250.681.79y向直径,mm0.560.560.561.671.250.621.72d平均直径,mm0.570.570.561.71.250.651.755摩擦系数μ0.0960.0890.0920.1220.1090.1030.125温升,℃3531914921
[0119]
由表3可以看出,实施例1~3的微润滑新材料的抗磨减摩性能较对比例1~4 有较为明显的改善,x向直径、y向直径、d平均直径、摩擦系数及温升均显著降低。
[0120]
试验例3
[0121]
下面对上述实施例1~3及对比例1~5所得轴承进行测试,轴承型号为6305,额定动载荷(c)为22.2kn,当量动载荷/测定动载荷(p/c)为0.2980,径向载荷(fr)为6615n,试验转速为6300r/min,基本额定寿命100h,包括轴承寿命可靠性、轴承游隙、振动(加速度)、振动(速度)、启动摩擦力矩、动态摩擦力矩的测试,测试结果见表4~9。
[0122]
表4轴承寿命可靠性测试结果
[0123]
项目试验通过时间/h失效零件实施例1500无实施例2500无实施例3500无对比例1151.7内圈对比例2205内圈对比例3251内圈对比例4135内圈对比例5375.5内圈
[0124]
由表4可以看出,实施例1~3的轴承运转寿命均达到500h,且无失效零件,而对比例1~5的轴承运转寿命则较低,尤以以32#透平油替换的对比例4的轴承运转寿命最低,仅为135h。从对比例1~5的轴承运转寿命来看,纳米氮化硼和纳米硼酸盐用杂醇油改性、纳米传驱动复合剂与聚α烯烃复配、聚α烯烃与纳米传驱动复合剂提前混合以及轴承处理方法均
会对轴承的运转寿命及运转状态产生影响。
[0125]
表5轴承游隙测试结果
[0126][0127]
注:k
ia
为成套轴承内圈径向跳动;s
ia
为成套轴承内圈轴向跳动;k
ea
为成套轴承外圈径向跳动;s
ea
为成套轴承外圈轴向跳动;gr为径向游隙。
[0128]
由表5可以看出,实施例1~3轴承游隙的各项参数均较小,且0~500h的变化幅度不大,说明实施例1~3的轴承稳定性较高。
[0129]
表6轴承振动(加速度)(单位:db)测试结果
[0130][0131]
表7轴承振动(速度)(单位:μm/s)测试结果
[0132]
[0133][0134]
注:l为低频,m为中频,h为高频
[0135]
由表6~7可以看出,实施例1~3轴承的振动加速度、振动速度在0~500h变化较小,说明实施例1~3的轴承运转500h状态仍保持良好。
[0136]
表8轴承启动摩擦力矩(单位:mn
·
m)测试结果
[0137][0138]
表9轴承动态摩擦力矩(单位:mn
·
m)测试结果
[0139][0140][0141]
注:max为最大值;为平均值。
[0142]
由表8~9可以看出,实施例1~3轴承的启动摩擦力矩、振动摩擦力矩在 0~500h变化较小,说明实施例1~3的轴承的运转精度及灵活度较好。
[0143]
试验例4
[0144]
噪音及温升测试:选择中煤张家口煤机有限公司测试中心,型号为43js/01 减速器,环境温度29℃,试验分为采用本发明实施例1获得的微润滑材料及轴承处理方法处理的试验组1、使用320#齿轮油但经过本发明轴承处理方法处理试验组2、使用320#齿轮油且未经过本发明轴承处理方法处理的试验组3三组,试验过程为空载正反向连续各运转30min,加装循环冷却系统,反向加载到额定负载,连续运行达到热平衡温度后,分别检测减速器油池油温及综合噪声。经检测,试验组1的减速器油池油温为65.1℃,综合噪声为92.8db;试验组2的减速器油池油温为67.0℃,综合噪声为93.3db;试验组3的减速器油池油温为 71.8℃,综合噪声为95.5db。因此,本发明的微润滑新材料配合轴承处理方法可以有效降低轴承运行过程中的温升及噪音。
[0145]
试验例5
[0146]
将本发明实施例1所得的微润滑新材料记为kb抗磨节能剂,将实施例1 中的轴承处理方法记为kb工艺。
[0147]
将本发明kb抗磨节能剂及kb工艺于首钢总公司第一线材厂的螺纹钢生产线切分轴承试用,原螺纹钢生产线切分轴承,在生产中的更换周期4小时/批;使用kb抗磨节能剂及kb工艺加工后,上线的轴承寿命从4小时延长到32小时,在860℃高温条件下的工作寿命提高8倍。
[0148]
将本发明kb抗磨节能剂及kb工艺于西山煤电集团公司杜儿坪煤矿的 sgz900/1050型运输机的43js/01型减速器中试用,原sgz900/1050型运输机的 43js/01型减速器,在生产中安全运行200h需要更换一次润滑油,以后每1000h 更换,一年更换六次,使用本发明kb抗磨节能剂及kb工艺后,连续安全运行达6000h,噪声及温度均未出现异常。
[0149]
综上所述,由本发明产品及工艺在不同型号的轴承上的使用结果可以看出,本发明产品及工艺可以有效降低轴承使用过程中的噪音,延长轴承的使用寿命。
[0150]
以上所述,仅为本发明的具体实施方式,但本发明的保护范围并不局限于此,任何熟悉本技术领域的技术人员在本发明揭露的技术范围内,可轻易想到变化或替换,都应涵盖在本发明的保护范围之内。因此,本发明的保护范围应以所述权利要求的保护范围为准。
再多了解一些
本文用于创业者技术爱好者查询,仅供学习研究,如用于商业用途,请联系技术所有人。