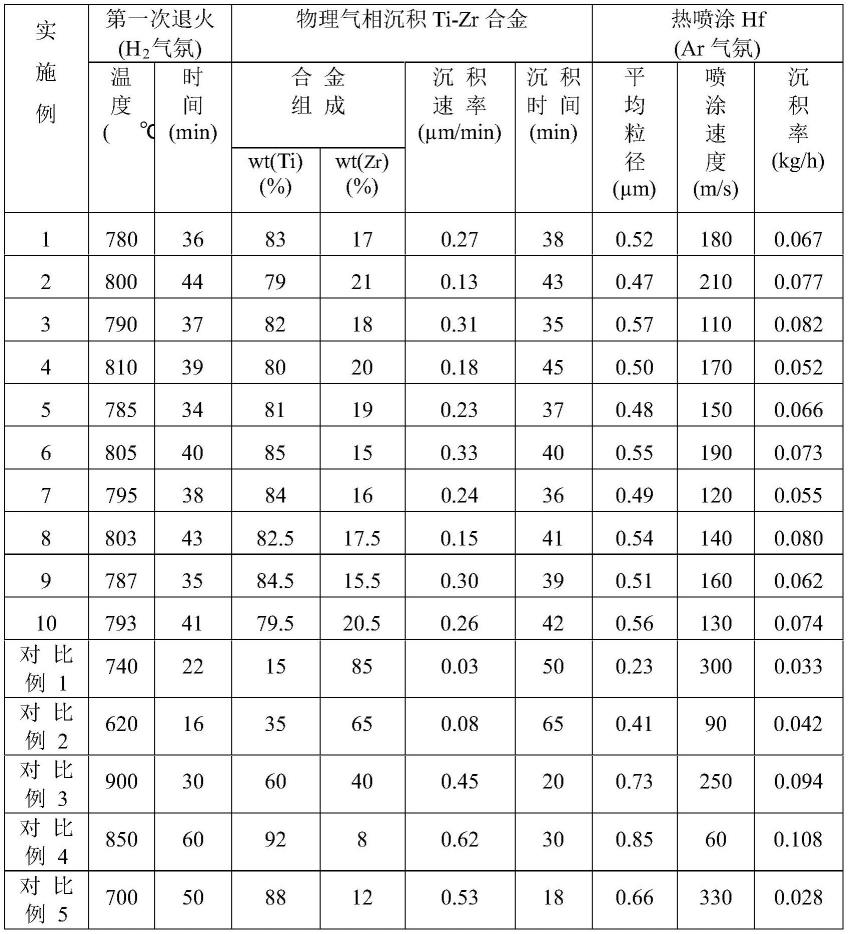
1.本发明属于材料表面处理技术领域,具体地涉及一种钢带表面钽-钨合金镀层的制备方法。
背景技术:
2.钽(ta)和钨(w)均属于难熔金属,具有熔点高、硬度大、强度高、耐蚀性好、耐热性强、资源储量丰富、价格适中等特点,其组成的钽-钨合金更是广泛用于制造导弹、火箭、飞机等航天航空飞行器的零部件、电光源及硬质合金等,尤其适用于长时间在高温环境下服役。但是,单纯钽-钨合金的缺点也很明显:质地坚硬、脆性大、塑性低、延展性差、不易进行变形加工。特别是大尺寸、大规格的固态成品制备过程中往往需要大量的原料金属,极大增加了冶炼、轧制、热处理及冲压成型等诸多工序的制造难度与生产成本,污染了环境,从而限制了钽-钨合金的进一步推广与应用。
3.经检索:
4.中国专利公开号为cn111763839a的文献,公开了《一种提高成品率的钽钨合金板加工成型工艺》。其工艺具体步骤如下:以平均粒度为3μm~5μm的钽粉和平均粒度为3μm的钨粉作为原料,将两者以一定的所需比例进行混合,然后将混合后的钽粉和钨粉放入高能球磨机内进行充分混合,得到混合粉。然后再依次进行压坯、坯料破碎、坯料筛选、电弧熔炼及锻造型轧等工序。其中,通过筛选机对坯料颗粒进行筛选得到质地均匀的坯料颗粒,让钽钨合金板的组织分布更加的均匀,提高钽钨合金板加工成型成品率。同时,热压可让钽钨合金板组织密实,力学性能得到改善。三次冷轧提高了钽钨合金板的屈服点,四次退火步骤消除钽钨合金板残余应力,避免钽钨合金板在日后切割中出现变形和裂纹。尽管如此,该文献的不足在于:一是原料直接采用单纯的钽粉和钨粉,产品为块状的板材,显然金属原料消耗量很大,成本高,形成的粉尘容易污染环境,环保性不足;二是该合金板的加工成型工艺过于冗长和复杂。包括:混料时,球磨时间为2~3h;坯料破碎时,球磨时间为2~3h。至少涉及三次冷轧和四次退火,冷轧和退火交替进行。每次退火的温度都至少在1250℃以上,保温时间不少于80min。每次冷轧前都需要对板坯进行表面处理,包括铣削、磨削、打磨等步骤。每次真空退火前,都要进行碱洗、水洗等步骤。再加上3~4次大电流(400~500a)电弧熔炼。整个生产流程能耗极大,生产成本极高;三是该文献所展示的实施例中,所得产品的晶粒度不低于20μm,硬度不超过150hv,抗拉强度不超过400mpa,屈服强度不超过350mpa,延伸率不低于48%。产品的塑性很好,延展性很高,但硬度和强度却明显偏低,综合使用性能仍然不足,很难满足长时间高温环境服役的要求。
5.中国专利公开号为cn113319292a的文献,公开了《基于激光选区熔化成形的钽钨合金制备工艺及钽钨合金》。其工艺具体步骤如下:对钽钨粉末和基材进行预处理;采用激光选区熔化成形获得钽钨合金构件;对成形的钽钨合金构件进行热处理;对热处理后的钽钨合金构件进行切割处理,使基材和试验件分离。其中,对激光选区熔化成形的参数进行优化处理,获得不同结构如内填充、结构体、网格支撑、上表面、下表面试验件的最优成形参
数。通过合理设计激光成形参数,不仅能够成形,获得无层间结合不良、气孔、裂纹等缺陷的钽钨合金构件,且基于增材制造的钽钨合金比采用传统粉末冶金的钽钨合金材料效费比更高,加工成本更低,效率更高。尽管如此,该文献的不足在于:一是其所采用的激光选区熔化成形方法属于一种增材制造(3d打印)技术,其设备价格高昂,每台设备售价约500~700万元人民币,难以大范围推广。此外,由于激光器功率和扫描振镜偏转角度的限制,能够成形零件尺寸范围有限,无法成形较大尺寸的金属零件,限制了该技术的推广应用。再者,加工过程中容易出现球化和翘曲现象,影响产品性能。此外,正如说明书陈述的那样,合金制备过程中,要采用三维扫描仪测量典型特征件的尺寸,根据成形出的典型钽钨构件尺寸数据,通过局部结构优化、模型尺寸补偿和扫描光斑偏移技术进行尺寸精度校正。设备运行参数设置过程极为复杂,需要设计不同的支撑结构及使基材和试验件分离的线切割方式。在基材与试验件分离后,还要对试验件进行去支撑、清洗、打磨和喷砂等后续处理,样品表面不得有任何损伤和缺陷,要求极高(参见实施例的相关陈述)。这些因素大幅增加了制备工艺的复杂性和难度,导致工作效率不会太高;二是除去打印设备及工序成本高昂外,打印过程中,通过激光将熔点在3000℃以上的钽钨合金进行熔化;进行真空退火处理,温度为1500℃,时间为2h。这两点就导致加工过程的能耗不会太低,生产成本高;三是原料采用粒径为10μm~60μm的钽钨粉末,这就意味着金属原料的消耗量较多,成本较高,形成的粉尘容易污染环境,环保性不足。四是热处理后,所得产品的抗拉强度一般为900mpa左右,但屈服强度不低于850mpa(参见说明书中的表3),屈强比不低于94.4%,说明合金的塑性依然不足,不易进行变形加工。此外,产品的抗拉强度也仅达到900mpa,对已与基材分离的钽钨合金本体而言,仍然偏低,高温环境下长时间服役依然存在一定不足。
技术实现要素:
6.本发明在于克服现有技术存在的生产成本高、环保性低、产品性能差等不足,提供一种能显著降低成本、减少污染、提高产品性能的钢带表面钽-钨合金镀层的制备方法。
7.实现上述目的的措施:
8.一种钢带表面钽-钨合金镀层的制备方法,其步骤如下:
9.1)以if钢冷轧钢带作为基材,进行常规的碱液脱脂除油;
10.2)常规水洗并烘干至钢带表面无水分;
11.3)在h2保护气氛下进行第一次退火,控制退火温度为780~810℃,保温时间为34~44min;
12.4)进行镀覆:
13.a、物理气相沉积ti-zr合金,控制ti的质量百分比为79~85%,zr的质量百分比为21~15%,控制沉积速率为0.13~0.33μm/min,沉积时间为35~45min;
14.b、热喷涂hf,其间:采用ar作为保护气体;控制hf的平均粒径为0.47~0.57μm,喷涂速度为110~210m/s,沉积率为0.052~0.082kg/h;
15.c、双离子注入ta与w,控制注入能量为370~380kev,ta的注入剂量为(6.0~7.0)
×
10
22
/cm2,w的注入剂量为(4.0~5.0)
×
10
22
/cm2;
16.d、在ar保护气氛下进行第二次退火,控制退火温度为810~830℃,保温时间为5~8min;
17.e、自然空冷至室温。
18.进一步地:物理气相沉积ti-zr合金过程中,ti的质量百分比为81~85%,zr的质量百分比为19~15%,沉积速率为0.16~0.31μm/min,沉积时间为37~42min。
19.进一步地:热喷涂hf过程中,控制hf的平均粒径为0.47~0.53μm,喷涂速度为117~205m/s,沉积率为0.056~0.079kg/h。
20.进一步地:双离子注入ta与w过程中,ta的注入剂量为(6.3~6.8)
×
10
22
/cm2,w的注入剂量为(4.3~4.8)
×
10
22
/cm2。
21.进一步地:在ar保护气氛下进行第二次退火过程中,退火温度为813~825℃。
22.本发明为了实现上述目的,针对行业需要,以if钢冷轧钢带作为基材,进行了大量的试验及分析,经过优化选择,采用“碱液脱脂除油 第一次退火(h2气氛) 物理气相沉积ti-zr合金 热喷涂金属hf(ar气氛) 双离子注入ta-w 第二次退火(ar气氛)”工艺进行表面处理。
23.之所以这样选择,是因为:
24.第一,总的来说,在钢带表面制备一薄层ta-w合金镀层,与单纯的大尺寸、大规格固态ta-w合金相比,在能保证合金本体优异性能的前提下,有利于大幅降低ta、w等金属原料的消耗,有利于控制生产成本。
25.第二,选择if钢(无间隙原子钢)冷轧钢带作为基材,是因为这种钢的c含量≤0.005%,n含量≤0.003%,钢中加入了一定量的nb或ti,使钢中的c、n原子被固定为碳化物和氮化物,从而使钢中没有间隙原子的存在。同时,冶炼过程中采用rh真空处理等先进技术,if钢的钢质非常洁净,夹杂物极少。加之其超低的c、n含量,且添加的nb或ti能细化晶粒,提高组织的均匀性,故if钢具有较好的表面质量及优异的延展性和冲压性能,材质相对柔软,有利于后续的镀覆及成型工序。因此,将ta-w合金沉积在if钢冷轧钢带表面,既可以维持合金本体的优异性能,又能借助基材良好的塑性进行后续加工,克服其本体脆性大的缺点,所以是一种两全其美的合理选择。
26.第三,冷轧钢带在进行镀覆前,必须保证其表面是洁净的,要进行适当的前处理。其中,碱液脱脂主要用来除去钢带表面的油污,而在h2保护气氛下进行退火有三个作用:一是将钢带表面残存的极少量油脂全部高温挥发掉;二是强还原性的h2可将钢带表面少量的氧化物全部去除;三是适当软化钢带,降低钢带的内应力,减少产生裂纹的概率,提高复合镀层的稳定性。
27.第四,冷轧钢带在完成前处理后,在钢带表面物理气相沉积一层ti-zr合金作为内镀层。这里有三个原因:一是ti-zr合金是一种高强度、高硬度的耐热及耐蚀合金,将其覆盖在钢带表面,有利于防止后续镀覆工序所带来的冲击或热量传导至钢带表面使基材软化,保护钢基不被氧化和腐蚀,从而提高整个复合镀层的稳定性;二是ti-zr合金中,ti元素与钢中的fe元素亲和性较强,两相界面间可形成稳定牢固的ti-fe合金;而zr元素与钢中的fe元素同样具有较强的亲和性,两相界面之间的原子可以发生合金化反应,形成稳定的连续固溶体,即zr-fe单相合金;ti-zr合金本身是一种连续固溶体,也是单相合金。这三点使内镀层牢固地附着在基材表面,整个复合镀层的稳定性得到显著提高;三是ti和zr均属于无害物质,因而ti-zr合金的环保性较好。之所以选择物理气相沉积工艺,是因为:一是作为内镀层一般要求致密、平整、缺陷少、均匀性好,采用成膜速度相对较慢的物理气相沉积工艺,
可以保证内镀层具有较高的表面质量和较强的附着力;二是其在真空条件下进行合金沉积,没有空气、水和其它杂质的存在,保证了合金的纯净度和表面质量;三是镀层厚度可以精确控制,可以减少原料浪费,控制成本;四是ti-zr合金不能从水溶液中进行电沉积,故无法采用电镀工艺。
28.第五,物理气相沉积ti-zr合金完成后,继续在ar保护气氛下热喷涂一层金属hf作为中间镀层。这里有六个原因:一是ta与ti,w与ti、zr很难形成稳定的连续固溶体,原子间结合力不足,因而不能直接将ta-w合金镀覆在ti-zr内镀层上,必须要添加中间镀层作为衔接内外镀层的过渡;二是以hf作为中间镀层,是因为hf元素和内镀层中的ti、zr同属于ivb族,是同族元素,化学性质相似,相互间亲和性比较强,可以形成稳定的连续固溶体,即ti-hf和zr-hf单相合金。因此,这两点可以使中间镀层牢固地附着在内镀层表面,整个复合镀层的稳定性得到显著提高;三是高纯度hf具有一定的延展性,可以提高整个合金镀层的塑性;四是hf是一种难熔金属,其熔点高、硬度大、强度高、耐蚀性好、耐热性强,有利于保证整个复合镀层的使用性能,适合作为中间镀层;五是hf属于无害物质,环保性好;六是hf的矿藏储量比较丰富,价格比较适中,不会显著增加生产成本。之所以选择在ar保护气氛下进行热喷涂工艺,是因为:一是hf的沸点为4602℃,采用真空气态镀膜的物理气相沉积工艺会导致能耗大幅增加。而hf的熔点为2227℃,如果采用熔融液态镀膜的热喷涂工艺,从能耗的角度而言,则会大幅下降;二是中间镀层需要有一定厚度,物理气相沉积工艺成膜速度慢,膜层薄,不易满足使用要求,而热喷涂工艺成膜速度快,所形成的膜层相对较厚,可以保证镀层性能;三是hf不能从水溶液中进行单质电沉积,因而无法采用电镀工艺;四是hf在高温下容易和o2、n2等物质发生化学反应,生成氧化物、氮化物等,导致硬度增加,脆性变大。以惰性气体ar为保护气体,就可以避免这些杂质的干扰,保证hf的纯度,进而确保镀层质量。
29.第六,热喷涂hf完成后,继续双离子注入ta-w作为外镀层。之所以采用离子注入的方式,是因为:一是ta的熔点为2996℃,沸点为5425℃;w的熔点为3410℃,沸点为5660℃,两者的熔、沸点过高,属于难熔金属。若采用真空气态镀膜的物理气相沉积工艺或熔融液态镀膜的热喷涂工艺,能耗将急剧增加,成本会显著上升;二是ta-w合金不能从水溶液中进行电沉积,因而无法采用电镀工艺。而离子注入则可以有效克服上述三种方式的缺点,其优点在于:可精确控制掺杂离子种类、数量和深度,工作效率高;所形成的镀层均匀性好,没有其它离子的干扰,纯度高;不改变钢件尺寸,方便后续工序处理。尤其是在真空条件下,其通过离子束轰击金属固体,使金属电离出离子,经电场加速后获得很高的速度,从而打入或沉积在钢件表面。整个过程能耗较低,且金属固体使用量极少,因而极大地降低了生产成本,避免了环境污染。这里,中间镀层中的hf与外镀层中的ta、w属于第6周期的连续相邻元素(原子序数分别为72、73和74),且均为难熔金属,化学性质相似,相互间亲和性也比较强,可以形成稳定的连续固溶体,即ta-hf和w-hf单相合金。而ta-w合金本身也是连续固溶体,是一种单相合金。因此,这三点可以使外镀层牢固地附着在中间镀层表面,整个复合镀层的稳定性得到显著提高。
30.第七,双离子注入ta-w完成后,继续在ar保护气氛下进行第二次退火。这是因为:一是ti-zr合金、金属hf、ta-w合金都是高硬度物质,整个复合镀层构建完成后,再进行一次退火处理,有利于适当降低整个镀层的内应力,提高镀层的塑性和延展性;二是在高温下进行退火热处理,可以促进各镀层两相界面之间的原子继续发生合金化反应,使各镀层之间
的结合力变强,从而进一步提高整个镀层的稳定性。之所以选择ar而不是h2或n2作保护气,是因为在高温下,ti、zr、hf、ta、w等组分容易和h2或n2发生化学反应,生成间隙化合物,导致镀层脆性增加,故而放弃h2或n2。
31.总体来看,本发明所构建的ti-zr/hf/ta-w复合镀层,具有如下优点:一是所采用的if冷轧钢带作基材,既可以保证整个合金镀层具有较好的塑性和延展性,克服了单纯块状合金脆性大的缺点,加工性能好,冲压制件时,不会出现脱落和裂纹,整个复合镀层的稳定性极高。而且在维持合金本体优异性能的前提下,可以大幅减少金属原料的用量,降低生产成本,是一种两全其美的选择;二是内镀层、中间镀层和外镀层的力学及加工性能、耐蚀性能、耐热性能、抗高温氧化性能都较强,保证了产品性能完全满足使用要求。整个复合镀层所采用的ti、zr、hf、ta、w等均属于难熔金属,物理和化学性质十分相似,因此整个复合镀层的性能接近于单纯的ta-w合金,产品成色很足;三是各个镀层中的合金元素大多彼此无限互溶,形成连续固溶体,呈现单相合金的性质,性能均匀性好。且各镀层之间的金属元素彼此亲和性强,容易在界面处发生合金化反应。这说明整个复合镀层的构建是基于很强的金属原子内部作用力,而不是较弱的外部环境,因而就保证了整个镀层具有很高的稳定性;四是整个复合镀层的设计合理有序,流程简单高效,能耗低。四是内镀层和中间镀层所使用的ti、zr、hf等金属均为无害物质,显著降低了对环境的污染。因此,整个复合镀层做到了性能、成本、环保三者的完美结合。
32.与现有技术相比,本发明钢带表面生成一层厚度为35~40μm的ti-zr/hf/ta-w复合镀层,孔隙率不超过1个/cm2,镀层表面质量良好;镀层表面硬度为320~340hv,抗拉强度为1100~1130mpa,延伸率为7.0~8.0%,应变硬化指数为0.17~0.20,塑性应变比为1.8~2.1,力学及加工性能良好;在1
×
104n压力下,反复擦拭1
×
105次后,镀层硬度值变化率不超过0.01%,磨损率不超过0.007%,耐磨性能良好;常温下,在10m hcl、10m naoh溶液、正常海水及大气环境中连续放置9.6
×
104h后,镀层表面不发生任何腐蚀,耐蚀性能良好;在1
×
103℃下连续放置7.2
×
103h,镀层表面氧化面积不超过0.3%,无裂纹及脱落情况产生,硬度值变化率不超过0.07%,强度值变化率不超过0.1%,抗高温氧化及耐热性能良好;置于水冷循环试验条件下,循环次数为430~440次,无裂纹及脱落情况产生,抗热震性能良好;在200khz超声波环境下连续放置1
×
104h后,镀层厚度没有明显变化,无裂纹及脱落情况产生,稳定性高。整个复合镀层性能完全满足行业要求。
具体实施方式
33.下面对本发明予以详细描述:
34.表1为本发明各实施例及对比例的主要工艺参数列表;
35.表2为本发明各实施例及对比例的性能检测情况列表。
36.本发明各实施例按照以下步骤生产:
37.1)以if钢冷轧钢带作为基材,进行常规的碱液脱脂除油;
38.2)常规水洗并烘干至钢带表面无水分;
39.3)在h2保护气氛下进行第一次退火,控制退火温度为780~810℃,保温时间为34~44min;4)进行镀覆:
40.a、物理气相沉积ti-zr合金,控制ti的质量百分比为79~85%,zr的质量百分比为
21~15%,控制沉积速率为0.13~0.33μm/min,沉积时间为35~45min;
41.b、热喷涂hf,其间:采用ar作为保护气体;控制hf的平均粒径为0.47~0.57μm,喷涂速度为110~210m/s,沉积率为0.052~0.082kg/h;
42.c、双离子注入ta与w,控制注入能量为370~380kev,ta的注入剂量为(6.0~7.0)
×
10
22
/cm2,w的注入剂量为(4.0~5.0)
×
10
22
/cm2;
43.d、在ar保护气氛下进行第二次退火,控制退火温度为810~830℃,保温时间为5~8min;
44.e、自然空冷至室温。
45.表1本发明各实施例及对比例的工艺参数
[0046][0047]
续表1
[0048][0049]
表2本发明各实施例及对比例的镀层性能
[0050]
[0051][0052]
续表2-1
[0053][0054]
续表2-2
[0055][0056]
从表2可以看到,按照本发明提出的方法制备钽-钨合金镀层,钢带表面生成一层厚度为35~40μm的ti-zr/hf/ta-w复合镀层,孔隙率不超过1个/cm2,镀层表面质量良好;镀层表面硬度为320~340hv,抗拉强度为1100~1130mpa,延伸率为7.0~8.0%,应变硬化指数为0.17~0.20,塑性应变比为1.8~2.1,力学及加工性能良好;在1
×
104n压力下,反复擦拭1
×
105次后,镀层硬度值变化率不超过0.01%,磨损率不超过0.007%,耐磨性能良好;常温下,在10m hcl、10m naoh溶液、正常海水及大气环境中连续放置9.6
×
104h后,镀层表面不发生任何腐蚀,耐蚀性能良好;在1
×
103℃下连续放置7.2
×
103h,镀层表面氧化面积不超过0.3%,无裂纹及脱落情况产生,硬度值变化率不超过0.07%,强度值变化率不超过0.1%,抗高温氧化及耐热性能良好;置于水冷循环试验条件下,循环次数为430~440次,无裂纹及脱落情况产生,抗热震性能良好;在200khz超声波环境下连续放置1
×
104h后,镀层厚度没有明显变化,无裂纹及脱落情况产生,稳定性高。整个复合镀层性能完全满足行业要求。
[0057]
上述实施例仅为最佳例举,而并非是对本发明实施方式的限定。
再多了解一些
本文用于创业者技术爱好者查询,仅供学习研究,如用于商业用途,请联系技术所有人。