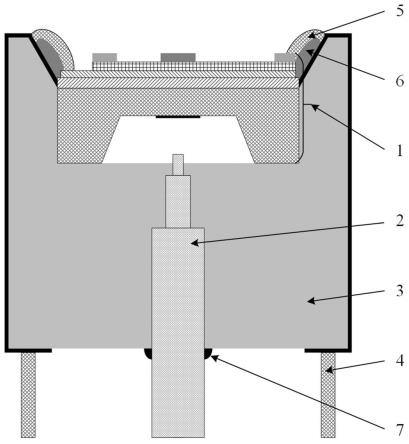
基于光-机-电-热多物理场耦合的mems耐高温压力传感器
技术领域
1.本发明属于压力传感器技术领域,具体涉及一种基于光-机-电-热多物理场耦合的mems耐高温压力传感器。
背景技术:
2.新型含能材料及高能炸药技术是新一代微型化武器和智能化弹药发展的核心基础技术。含能材料在mems火工品等器件中的装药尺寸为毫米或亚毫米量级;在新型高能炸药研制初期,由于合成成本高、危险性高等因素制约,炸药合成量在毫克量级。压力参数对新型含能材料以及高能炸药的状态方程拟合、爆炸效应模拟以及输出性能表征起着至关重要的作用。因此,微尺度装药或微小药量输出爆压测试已成为亟待解决的关键问题。
3.微尺度装药或微小药量爆炸特点有:
①
不同种类炸药具有不同的输出爆压范围,一般在mpa至gpa量级;
②
装药量在毫克级,装药尺寸为毫米或亚毫米级;
③
爆轰波阵面不是一维平面波;
④
爆轰过程为微秒量级,且伴随瞬态高温。国内外学者大多采用间接法(通过测量邻近介质中的冲击波参数,利用阻抗匹配原理反推爆压)来获取爆压,间接法的本质是基于一维平面冲击波的质量、动量守恒定律来推导爆压,忽略了微小药量或微尺度装药爆轰的非一维平面波特性,获得的爆压并不准确。若要测量微尺度装药或微小药量的真实爆压,必须采用直接法(将传感器直接置于爆轰场中获取压力信号)。为了满足上述爆炸特点,直接法涉及的传感器必须满足如下条件:
①
具有较宽的量程范围和较快的响应时间;
②
传感器敏感元件易小型化,其尺寸要与装药尺寸匹配;
③
敏感元件能耐受高温环境,且信号受温度影响较小。因此,亟需开发一种微型耐高温压力传感器来满足要求。
4.耐高温压力传感器根据敏感材料不同主要可分为:soi高温压力传感器、sic高温压力传感器、sos高温压力传感器和光纤高温压力传感器。soi高温压力传感器由于受封装形式、高温下硅压阻系数退化、高温漏电流增大以及硅高温蠕变等因素限制,难以在500℃以上高温环境下长期工作;sos高温压力传感器的外延单晶硅薄膜与蓝宝石的晶格失配大,存在较大失配应力,限制了该类传感器的使用温度;光纤高温压力传感器虽然可以在超高温(》800℃)环境下工作,但是其量程有待提高。目前,sic由于优良的耐高温特性、易加工性以及半导体材料自身优点,已被广泛应用于高温压力传感器研制,但限制sic压阻式高温压力传感器工作温度的因素有:
①
高温下外延6h-sic薄膜的压阻效应退化;
②
sic欧姆接触的使用温度有限。为了进一步突破高温压力传感器性能,满足多种高温恶劣环境下的压力测量,多物理场耦合以及多参数复合的mems压力传感器将成为高温压力传感器未来主流发展方向。
技术实现要素:
5.为了克服上述现有技术的缺点,本发明的目的是提供一种基于光-机-电-热多物理场耦合的mems耐高温压力传感器,能够实现温度自补偿、峰值自校准和压力脉宽检测等功能,且具有体积小、耐高温、宽量程、高频响、高精度等特点。
6.为了实现上述目的,本发明采用的技术方案为:
7.一种基于光-机-电-热多物理场耦合的mems耐高温压力传感器,包括传感器芯片1,传感器芯片1安装在封装壳3内;传感器芯片1变形信号输出和耐高温光纤2连接,耐高温光纤2固定在封装壳3内;传感器芯片1电信号输出和耐高温引线4连接,耐高温引线4连接在封装壳3上。
8.所述的传感器芯片1采用mems工艺制作,包括基底1-1,基底1-1上设有绝缘层1-2,绝缘层1-2上设有底电极1-3,底电极1-3上设有压电薄膜1-4,压电薄膜1-4上设有测温元件1-5和顶电极1-6。
9.所述的基底1-1采用碳化硅或蓝宝石材料,基底1-1包括基体1-1a,基体1-1a内设有腔体1-1c,腔体1-1c顶部设有反射膜1-1b,腔体1-1c通过刻蚀或键合工艺制作,反射膜1-1b采用铝、金或银薄膜结构,反射膜1-1b和耐高温光纤2端面构成f-p腔,通过f-p腔解调获得压力值,通过对比f-p腔与压电薄膜1-4获得的压力值实现峰值自校准,测温元件1-5测量腔体1-1c在压力作用下产生变形时的温度,实现f-p腔测压的温度自补偿。
10.所述的绝缘层1-2采用二氧化硅、氧化铝或氮化硅材料,通过磁控溅射或化学气相沉积工艺制成,厚度为300nm。
11.所述的底电极1-3和顶电极1-6采用铂、金或铑材料,通过磁控溅射工艺制成,厚度为150nm。
12.所述的压电薄膜1-4采用硅酸镓镧、氮化铝、磷酸镓或氧硼酸钇钙材料,通过脉冲激光沉积、磁控溅射或溶胶凝胶法制成,厚度为750nm。
13.所述的测温元件1-5采用铂薄膜热电阻或钨铼薄膜热电偶结构,通过磁控溅射工艺制成。
14.所述的封装壳3包括壳体3-2,壳体3-2采用云母玻璃陶瓷或氧化铝陶瓷材料,壳体3-2通过精密机械加工形成芯片安装槽3-1和光纤固定孔3-4,传感器芯片1通过耐高温绝缘胶6固定在芯片安装槽3-1内,耐高温光纤2通过高温胶7固定在光纤固定孔3-4内;壳体3-2表面通过图形化与电镀工艺形成耐高温导电线路3-3,耐高温导电线路3-3采用铜/金双层复合结构,传感器芯片1电信号输出通过耐高温导电银胶5以及耐高温导电线路3-3与耐高温引线4连接。
15.所述的耐高温光纤2采用蓝宝石光纤或碳化硅光纤。
16.所述的耐高温引线4采用云母玻纤编织耐高温电线。
17.本发明的有益效果为:
18.①
传感器芯片1、耐高温光纤2、封装壳3以及耐高温引线4均采用耐高温材料制作,能够承受600℃以上高温;
②
反射膜1-1b和耐高温光纤2端面构成f-p腔,通过f-p腔解调即可获得压力值,优化腔体1-1c结构尺寸可实现高达100mpa压力测量;此外,压电薄膜1-4的响应速度快,可同时测量压力峰值与脉宽;通过对比f-p腔与压电薄膜1-4获得的压力值能够实现峰值自校准;
③
测温元件1-5可测量腔体1-1c在压力作用下产生变形时的温度,从而能够实现f-p腔测压的温度自补偿;
④
传感器芯片1采用mems工艺制作,最大尺寸小于2mm。
附图说明
19.图1为本发明的结构示意图。
20.图2为本发明传感器芯片的结构示意图。
21.图3为本发明基底的结构示意图。
22.图4为本发明封装壳的结构示意图。
具体实施方式
23.下面结合附图和实施例对本发明做详细说明。
24.参照图1,一种基于光-机-电-热多物理场耦合的mems耐高温压力传感器,包括传感器芯片1,传感器芯片1安装在封装壳3内;传感器芯片1变形信号输出和耐高温光纤2连接,耐高温光纤2固定在封装壳3内,耐高温光纤2采用蓝宝石光纤或碳化硅光纤;传感器芯片1电信号输出和耐高温引线4连接,耐高温引线4采用云母玻纤编织耐高温电线,耐高温引线4连接在封装壳3上。
25.参照图2,所述的传感器芯片1采用mems工艺制作,包括基底1-1,基底1-1上设有绝缘层1-2,绝缘层1-2采用二氧化硅、氧化铝或氮化硅材料,通过磁控溅射或化学气相沉积工艺制成,厚度约为300nm;绝缘层1-2上设有底电极1-3,底电极1-3和顶电极1-6采用铂、金或铑材料,通过磁控溅射工艺制成,厚度约为150nm;底电极1-3上设有压电薄膜1-4,压电薄膜1-4采用硅酸镓镧、氮化铝、磷酸镓或氧硼酸钇钙材料,通过脉冲激光沉积、磁控溅射或溶胶凝胶法制成,厚度约为750nm;压电薄膜1-4上设有测温元件1-5和顶电极1-6,测温元件1-5采用铂薄膜热电阻或钨铼薄膜热电偶结构,通过磁控溅射工艺制成。
26.参照图3,所述的基底1-1采用碳化硅或蓝宝石材料,基底1-1包括基体1-1a,基体1-1a通过刻蚀或键合工艺形成腔体1-1c,腔体1-1c顶部通过磁控溅射或蒸镀工艺获得反射膜1-1b,反射膜1-1b采用铝、金或银薄膜结构。
27.参照图4,所述的封装壳3包括壳体3-2,壳体3-2采用云母玻璃陶瓷或氧化铝陶瓷材料,壳体3-2通过精密机械加工形成芯片安装槽3-1和光纤固定孔3-4,传感器芯片1通过耐高温绝缘胶6固定在芯片安装槽3-1内,耐高温绝缘胶6可以防止底电极1-3与顶电极1-6短路,耐高温光纤2通过高温胶7固定在光纤固定孔3-4内;壳体3-2表面通过图形化与电镀工艺形成耐高温导电线路3-3,耐高温导电线路3-3采用铜/金双层复合结构,传感器芯片1电信号输出通过耐高温导电银胶5以及耐高温导电线路3-3与耐高温引线4连接,耐高温引线4通过锡焊工艺与耐高温导电线路3-3连接。
28.本发明的工作原理为:
29.在高温环境中,脉冲压力信号作用于传感器芯片1上,形成的应力波依次从测温元件1-5和顶电极1-6、压电薄膜1-4、底电极1-3、绝缘层1-2传播至基底1-1,测温元件1-5在高温环境下电阻或输出电压发生变化,通过该变化可获得传感器芯片1的温度值;压电薄膜1-4受到应力波作用时,底电极1-3和顶电极1-6上会产生电荷,通过检测电路即可获得压电薄膜1-4受到的压力值和压力脉宽;抛光良好的耐高温光纤2端面与反射膜1-1b内表面形成f-p腔,基底1-1在应力波作用下会产生变形,从而改变f-p腔腔长,引起干涉谱变化,通过测量干涉光谱,并对干涉光谱进行解调,即可得到作用在基底1-1上的压力值,利用测温元件1-5获得的温度值对该压力值进行温度补偿,可以提高测量精度;由于顶电极1-6、压电薄膜1-4、底电极1-3和绝缘层1-2的厚度均为纳米级别,故可认为作用在压电薄膜1-4和基底1-1的压力相同,通过对比压电薄膜1-4获得的压力值和f-p腔解调的压力值,即可实现压力峰值
自校准。
再多了解一些
本文用于创业者技术爱好者查询,仅供学习研究,如用于商业用途,请联系技术所有人。