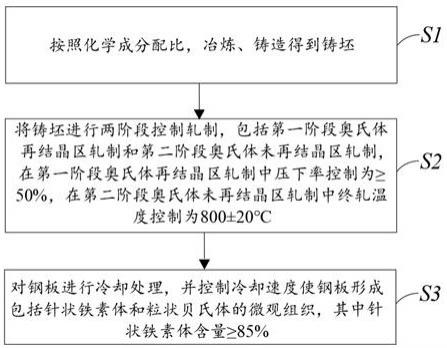
耐腐蚀460mpa级钢板及其生产方法
技术领域
1.本发明涉及合金技术领域,具体地涉及一种耐腐蚀460mpa级钢板及其生产方法。
背景技术:
2.与陆上风电场相比,海上风电具有发电效率高、环境污染小、不占用耕地等优点。然而,海上风电所处腐蚀环境非常苛刻,尤其是处于高湿高盐的海洋大气区的钢结构塔架,海洋大气中的水蒸气在毛细管作用、吸附作用和化学凝结作用等的影响下,附着在钢铁表面形成一层肉眼看不到的导电性很强的电解质溶液,溶液中有溶解氧、氯离子、硫酸根离子和其它一些盐分。其中,氯离子具有很强的穿透作用,造成点蚀、应力腐蚀、晶间腐蚀和缝隙腐蚀等局部腐蚀,使得钢铁表面难以形成长期稳定的致密锈层,导致腐蚀率上升。常用的防腐蚀解决方案是采用长寿命防腐涂层体系,但在服役过程中,会出现涂层失效问题。因此,提高钢材本身的耐腐蚀性,是防腐蚀设计的又一新技术路线。
3.现有耐海洋大气腐蚀钢的生产技术中,主要通过添加大量p和大量ni,但p含量过高钢材的焊接性变差,不适用于生产需大量焊接成型的风电塔筒用钢板;添加大量ni提高耐蚀性,合金成本高,不利于海上风电机组成本控制,推广应用较难,而其他的一些钢板则强度较低,不适用于大型海上风电建设。
技术实现要素:
4.本发明的目的在于提供一种耐腐蚀460mpa级钢板及其生产方法。
5.本发明提供一种耐腐蚀460mpa级钢板生产方法,所述钢板的化学成分以质量百分比计包括:c:0.06~0.09%、si:0.2~0.3%、mn:0.9~1.0%、cr:0.5~0.6%、ni:0.30~0.40%、cu:0.40~0.45%、mo:0.05~0.10%、nb:0.02~0.04%、al:0.02~0.04%、p:0.015~0.025%、稀土元素:0.015~0.025%,其余为fe和不可避免的杂质,部分杂质元素以质量百分比计包括:s≤0.002%、o≤0.002%、n≤0.004%;所述钢板的耐大气腐蚀性指数i≥6.5,其中,耐大气腐蚀性指数i的计算公式为:i=26.01(%cu) 3.88(%ni) 1.20(%cr) 1.49(%si) 17.28(%p)-7.29(%cu)(%ni)-9.10(%ni)(%p)-33.39(%cu)2,其中,括号内元素符号为相应元素的质量百分数,%元素符号表示相应元素的质量百分数乘以100;所述生产方法包括步骤:按照上述化学成分配比,冶炼、铸造得到铸坯;将所述铸坯进行两阶段控制轧制,包括第一阶段奥氏体再结晶区轧制和第二阶段奥氏体未再结晶区轧制,在所述第一阶段奥氏体再结晶区轧制中压下率控制为≥50%,在所述第二阶段奥氏体未再结晶区轧制中终轧温度控制为800
±
20℃;对所述钢板进行冷却处理,并控制冷却速度使所述钢板形成包括针状铁素体和粒状贝氏体的微观组织,其中所述针状铁素体含量≥85%。
6.作为本发明的进一步改进,所述钢板的碳当量ce满足0.39≤ce≤0.42,其中,碳当量ce的计算公式为:ce=(%c) (%mn)/6 (%cr %mo %v)/5 (%ni %cu)/15其中,括号内元素符号为相应元素的质量百分数,%元素符号表示相应元素的质量百分数乘以100。
7.作为本发明的进一步改进,在所述钢板化学成分中,所述稀土元素为la、ce、pr、nd中的一种或多种。
8.作为本发明的进一步改进,还包括:将所述铸坯轧制为厚度≤100mm的钢板。
9.作为本发明的进一步改进,所述对所述钢板进行冷却处理具体包括:将轧制后的所述钢板进行水冷处理,冷却速率控制为10~28℃/s,所述钢板的终冷温度控制为350
±
30℃。
10.一种耐腐蚀460mpa级钢板,采用上述的耐腐蚀460mpa级钢板生产方法制造得到;在gb/t 10125-2012试验标准下,所述钢板的平均腐蚀失重率≤1.315g/(m2·
h);所述钢板屈服强度≥460mpa,抗拉强度为540~720mpa,断后延伸率≥20%,-50℃冲击吸收能量kv2≥100j。
11.作为本发明的进一步改进,所述钢板最大夹杂物的长宽积≤150μm2,在gb/t10561标准下的a、b、c、d类夹杂物评级均≤1.5级,且a、b、c、d类夹杂物评级之和≤3.0级。
12.作为本发明的进一步改进,所述钢板在焊接热输入量≤80kj/cm时,焊后热影响区-50℃冲击吸收能量kv2≥80j。
13.一种耐腐蚀460mpa级钢板,所述钢板的化学成分以质量百分比计包括:c:0.06~0.09%、si:0.2~0.3%、mn:0.9~1.0%、cr:0.5~0.6%、ni:0.30~0.40%、cu:0.40~0.45%、mo:0.05~0.10%、nb:0.02~0.04%、al:0.02~0.04%、p:0.015~0.025%、稀土元素:0.015~0.025%,其余为fe和不可避免的杂质,部分杂质元素以质量百分比计包括:s≤0.002%、o≤0.002%、n≤0.004%;所述钢板微观组织包括针状铁素体和粒状贝氏体,其中所述针状铁素体含量≥85%;在gb/t 10125-2012试验条件下,所述钢板的平均腐蚀失重率≤1.315g/(m2·
h);所述钢板屈服强度≥460mpa,抗拉强度为540~720mpa,断后延伸率≥20%,-50℃冲击吸收能量kv2≥100j。
14.作为本发明的进一步改进,所述钢板最大夹杂物的长宽积≤150μm2,在gb/t10561标准下的a、b、c、d类夹杂物评级均≤1.5级,且a、b、c、d类夹杂物评级之和≤3.0级。
15.作为本发明的进一步改进,所述钢板在焊接热输入量≤80kj/cm时,焊后热影响区-50℃冲击吸收能量kv2≥80j。
16.作为本发明的进一步改进,所述钢板厚度不大于100mm。
17.本发明的有益效果是:本发明采用cr ni mo cu p复合添加的耐蚀合金化成分体系,确保耐腐蚀性能和焊接性能的前提下,节约贵重合金的使用量。在杂质元素严格控制的同时,采用la、ce、pr、nd中的一种或多种稀土元素使钢水纯净化,进一步提升耐腐蚀性。在化学成分的综合设计基础上,通过对轧制和冷却过程工艺参数的精确控制,实现钢板组织、
夹杂物含量和尺寸的精准控制,获得综合性能良好的耐海洋大气腐蚀的460mpa级风电塔筒用钢板。
附图说明
18.图1是本发明一实施方式中的耐腐蚀460mpa级钢板生产方法流程示意图。
具体实施方式
19.为使本发明的目的、技术方案和优点更加清楚,下面将结合本发明具体实施方式及相应的附图对本发明技术方案进行清楚、完整地描述。显然,所描述的实施方式仅是本发明一部分实施方式,而不是全部的实施方式。基于本发明中的实施方式,本领域普通技术人员在没有做出创造性劳动前提下所获得的所有其他实施方式,都属于本发明保护的范围。
20.下面详细描述本发明的实施方式,实施方式的示例在附图中示出,其中自始至终相同或类似的标号表示相同或类似的元件或具有相同或类似功能的元件。下面通过参考附图描述的实施方式是示例性的,仅用于解释本发明,而不能理解为对本发明的限制。
21.本实施方式提供一种耐腐蚀460mpa级钢板及其生产方法,所生产得到的钢板特别适用于作为耐海洋大气腐蚀钢板使用,本实施方式提供的钢板采用cr ni mo cu p复合添加的耐蚀合金化成分体系,并且相比于现有的耐海洋大气腐蚀钢板,本实施方式采用低p和低ni的合金成分体系,提高钢板的焊接性能的同时降低合金成本。在p、ni添加量较低的情况下,在生产过程中,本发明通过添加少量稀土元素提高钢液纯净度,并通过轧制和冷却流程参数的控制,使钢板形成以针状铁素体为主的微观组织,从而提高钢板的耐腐蚀性,并提高钢板的强度。
22.本实施方式提供的钢板化学成分以质量百分比计包括:c:0.06~0.09%、si:0.2~0.3%、mn:0.9~1.0%、cr:0.5~0.6%、ni:0.30~0.40%、cu:0.40~0.45%、mo:0.05~0.10%、nb:0.02~0.04%、al:0.02~0.04%、p:0.015~0.025%、稀土元素:0.015~0.025%,其余为fe和不可避免的杂质,部分杂质元素以质量百分比计包括:s≤0.002%、o≤0.002%、n≤0.004%。
23.具体地,钢板的化学成分的设计原理说明如下:c:c为强化元素,c含量能显著影响钢材的组织结构从而直接影响钢板的强度,但c含量较高时,会使钢材的低温韧性和焊接性能变差;因此,在本发明中,将c含量控制在0.06~0.09%,结合其他元素的整体设计,不仅可以保证强化效果,还可以改善钢板低温韧性和焊接性能。
24.si:si为固溶强化、脱氧元素,当前学界与业界对于si在钢中对于其耐蚀性所起到作用的机理存在不同观点,但通常认为添加si所形成的三维网络结构sio2可以促进α-feooh的形成与晶粒细化,并且,锈层的fe3o4中的fe可以被si取代,形成更稳定的sio2。另外,当si与cu联合使用时,锈层中的sio2也可提高cu的富集度,从而提高耐工业大气腐蚀性能。但si含量较大时,会提高p元素的在晶界处的偏聚,降低钢板的低温韧性和焊接性,削弱p的耐腐蚀效果。因此,在本发明中,将si含量控制在0.2~0.3%,在保证脱氧效果的前提下,避免p的偏聚。
25.mn:mn为固溶强化元素,可以提高钢板的淬透性,从而提高其强度,同时mn还可以与有害元素s结合以降低钢板的热脆性。但过多的mn会加剧c、p等元素的偏析,在钢板心部
形成mns夹杂,进而减弱钢板的耐腐蚀性,劣化钢板心部低温韧性和焊接性能。因此,在本发明中,将mn含量控制在0.9~1.0%,一方面可以弥补低碳造成的强度损失,另一方面可以减轻偏析、减少夹杂物生成,提高钢板心部的低温韧性和焊接性能。
26.cr:cr为常用的耐腐蚀元素之一,cr可以促进钢表面锈层中疏松不稳定的γ-feooh转化为稳定的α-feooh,减少锈层中孔隙、裂纹的出现,提高钢的耐蚀性。cr在锈层靠近基体端会发生聚集,形成钝化膜,降低锈层的阴离子选择性,阻挡外来阴离子的渗入,保护钢板基体。并且,cr可与cu协同作用细化锈层晶粒,提高锈层的致密性和稳定性,且cr会替代feooh中部分fe的位置形成crxfe(1-x)ooh,使得锈层具备阳离子选择能力,有效阻止氯离子和硫酸根离子的渗透。但当cr含量较大时,易形成碳化物,造成点蚀,降低钢材的耐蚀性;因此,在本发明中,将cr含量控制在0.5~0.6%,使钢板的耐腐蚀性不随时间延长而降低。
27.ni:加入ni元素可以使钢的自腐蚀电位正移,增大阳极溶解反应发生的阻力,而促进锈层中α-feooh相形成,细化内锈层晶粒,提高锈层稳定性。并且,ni元素可能在锈层内部富集,使得锈层阴离子选择性降低,减缓钢板基体腐蚀。另外,添加ni可提高钢板的低温韧性和焊接性能,但添加过多的ni会造成合金成本较高。因此,在本发明中,将ni含量控制在0.3~0.4%,保证钢板耐腐蚀性能、低温韧性和焊接性能的同时,能够合理控制合金成本。
28.cu:在钢中加入cu对其耐蚀性有较好提高作用,且其价格低廉,被广泛用于耐蚀钢中,其主要作用机制有多种:cu可阻碍锈层的晶体化,促进α-feooh和非晶态fe3o4的形成;并且,cu可在锈层薄弱处富集,在腐蚀过程中形成氧化物,紧密连接锈层和钢基体,减少锈层中的裂纹、空隙等,提高耐点蚀性能;另外,cu元素有活化阴极的作用,使得钢基体被钝化,腐蚀速率下降。但cu含量较高时,不利于钢板的焊接性能。因此、在本发明中,将cu含量控制在0.40~0.50%,既提高钢板耐腐蚀性,又不影响焊接性能。
29.mo:mo能够细化晶粒,提高钢的淬透性,另外,mo可在钢材锈层中形成moo
42-,使内锈层具备阳离子选择性,从而抑制cl-的侵入。mo与cu联合使用,可促进cu在锈层薄弱处富集,抑制点蚀发生,提高耐腐蚀性。并且,mo的加入还能使形成针状铁素体的冷速降低。但添加过多的mo会造成合金成本较高。因此,在本发明中,将mo含量控制在0.05~0.10%,在保证钢板强度、耐腐蚀性能的同时,合理控制合金成本。
30.nb:nb为细晶元素和强碳化物形成元素,其能够避免c与cr结合影响钢板耐腐蚀性,并且nb能够促进α-feooh的快速形成和含量的增加。另外,nb可提高稀土元素在钢中的固溶量,从而提高钢板耐蚀性。当nb含量较大时,其会劣化焊接接头热影响区低温韧性,并会对耐腐蚀性造成反作用,因此,在本发明中将nb含量控制在0.02~0.04%,在保证晶粒细化效果和耐腐蚀性的同时,不会对焊接接头热影响区低温韧性产生不利影响。
31.al:al为重要的脱氧元素,含量较高时,浇铸时易堵塞水口。本发明中将al控制在0.02~0.04%,保证al的有益效果的同时,降低冶炼难度。
32.p:p为典型的提高钢耐腐蚀性能的元素,p可以起到阳极去极化剂的作用,加快fe
2
的氧化速率以及钢的均匀溶解,能有效帮助钢板表面形成均匀的α-feooh锈层。并且,p能够形成po
43-,一方面,po
43-能够络合h
改善界面ph值,减缓阴极析氢还原反应并减缓对锈层的溶解,另一方面,po
43-能够在阳极溶解过程中与fe
2
和mn
2
结合,形成难溶的磷酸盐膜,阻挡阳极溶解反应,起到缓蚀剂作用。另外,p和cu之间也有较好的协同耐蚀作用,从而综合起到
提高钢耐腐蚀性能的作用。同时,p也为易偏析元素,其含量过高时,会显著降低钢板心部的低温韧性和焊接性能。因此,在本发明中将p含量控制在0.015-0.025%,保证耐腐蚀性能的同时,不会产生严重的偏析,劣化钢板的低温韧性和焊接性能。
33.稀土元素:稀土元素可净化钢液,细化钢材中的夹杂物,使长条的硫化锰变质为球状稀土硫化物或硫氧化物,使高硬度的氧化铝夹杂变质为球状硫氧化物及铝酸稀土。稀土与p联合使用,有利于在钢板表面形成均匀的α-feooh锈层,使锈层与基体的结合力变强,提升耐腐蚀性。考虑到成本因素,本发明中将稀土控制在0.015-0.025%,同时起到净化钢液和提高钢板耐腐蚀性的作用。
34.在本实施方式中,稀土元素可为la、ce、pr、nd中的一种或多种,la、ce、pr和nd均为轻稀土元素,离子半径相近,在钢中的作用机理相同,在自然界密切共生,提纯单一稀土金属的成本较高。本实施方式采用la、ce、pr、nd中的一种或多种,在确保耐腐蚀性能的前提下,降低稀土金属的成本。
35.s、o和n:为杂质元素,加入钢中的稀土元素首先会与杂质元素反应,如杂质元素含量较高,则加入的稀土将被大量消耗,减弱稀土的耐腐蚀性作用。而进一步对杂质元素进行限定,则会加大生产难度,本发明中控制s≤0.002%、o≤0.002%、n≤0.004%,结合整体化学成分的设计,既保证稀土元素的有效作用,又避免杂质元素含量控制要求过严导致的生产难度大、生产成本高。
36.进一步的为,钢板的耐大气腐蚀性指数i≥6.5,其中,耐大气腐蚀性指数i的计算公式为:i=26.01(%cu) 3.88(%ni) 1.20(%cr) 1.49(%si) 17.28(%p)-7.29(%cu)(%ni)-9.10(%ni)(%p)-33.39(%cu)2,其中,括号内元素符号为相应元素的质量百分数,%元素符号表示相应元素的质量百分数乘以100。
37.钢板的碳当量ce满足0.39≤ce≤0.42,以确保钢板具有良好的焊接性,其中,碳当量ce的计算公式为:ce=(%c) (%mn)/6 (%cr %mo %v)/5 (%ni %cu)/15其中,括号内元素符号为相应元素的质量百分数,%元素符号表示相应元素的质量百分数乘以100。
38.综上所述,本实施方式采用cr ni mo cu p复合添加的耐蚀合金化成分体系,并且,相比于现有的耐海洋大气腐蚀钢板,本实施方式采用低p和低ni的合金成分体系,可提高钢板的强度和焊接性能的同时降低合金成本。在p、ni添加量较低的情况下,通过添加少量稀土元素提高钢液纯净度,进一步提升耐腐蚀性。
39.如图1所示,生产方法包括步骤:s1:按照上述化学成分配比,冶炼、铸造得到铸坯;s2:将铸坯进行两阶段控制轧制,包括第一阶段奥氏体再结晶区轧制和第二阶段奥氏体未再结晶区轧制,在第一阶段奥氏体再结晶区轧制中压下率控制为≥50%,在第二阶段奥氏体未再结晶区轧制中终轧温度控制为800
±
20℃;s3:对钢板进行冷却处理,并控制冷却速度使钢板形成包括针状铁素体和粒状贝氏体的微观组织,其中针状铁素体含量≥85%。
40.在步骤s1中,其具体包括:按照化学成分配比依次进行转炉冶炼工序、lf精炼工序、rh精炼工序和连铸工序得到铸坯。
41.在铁水预脱硫工序中,对铁水进行kr脱硫,控制铁水中硫含量,在扒除脱硫渣后将铁水兑入转炉进行转炉冶炼。
42.在转炉冶炼中,使用预脱硫后的铁水和废钢等为原料进行转炉冶炼得到钢水,在冶炼过程中,在钢水中依次加入硅铁合金、金属锰和碳粉等对钢水进行脱氧合金化。
43.将钢水精炼至满足预定要求后抽真空进行循环脱气处理。
44.将精炼后钢水抽真空进行循环脱气处理,去除夹杂物,进行进一步精炼。
45.精炼后钢水喂入合金线实现合金化后,将钢液浇铸成铸坯,并对铸坯进行加热及均热保温,准备进行轧制处理。
46.在步骤s2中,具体包括:采用两阶段控制轧制,包括第一阶段奥氏体再结晶区轧制和第二阶段奥氏体未再结晶区轧制,在第一阶段奥氏体再结晶区轧制中压下率控制为≥50%,在大的压下量下,通过反复交错进行形变、再结晶使原奥氏体晶粒充分再结晶,并通过大压下量使奥氏体晶粒逐渐细化,最终获得细小等轴奥氏体晶粒,增加奥氏体有效晶界总面积,为奥氏体向铁素体相变形核提供更多位置。
47.第二阶段轧制在再结晶温度以下进行大压下量轧制,增加再结晶的形核点和再结晶驱动力,使原奥氏体晶粒细化,并促进微合金元素的应变诱导析出并实现奥氏体晶粒的细化和加工硬化,奥氏体晶粒被拉长的同时产生了变形带和大量位错,使奥氏体晶粒内积累足够的形变能,为相变提供更多的形核位置,从而细化晶粒。
48.具体的,在第二阶段轧制中,终轧温度控制在820
±
15℃,将铸坯轧制为厚度≤100mm的钢板,结合前述的微合金元素成分及添加量,可以有效细化晶粒,并提高钢板的低温韧性。
49.在步骤s2中,具体包括:将轧制后的钢板进行水冷处理,冷却速率控制为10~28℃/s,钢板的终冷温度控制为350
±
30℃,控制冷却速度使钢板形成包括针状铁素体和粒状贝氏体的微观组织,其中针状铁素体含量≥85%。
50.通过大的冷却速度,使钢板冷却形成以针状铁素体为主的微观组织。针状铁素体呈板条形,是具有复相结构特征的混合型组织,其晶界为富碳层,电位较高,难以被腐蚀,能够起到保护内部铁素体的作用,因此,以针状铁素体组织为主的钢板具有优秀的耐腐蚀性能,并且针状铁素体在形成过程中形成过饱和固溶和细小亚结构,以及多位向析出的形态,能够显著提高钢板强韧性。针状铁素体在保证钢板高强度的同时,还具有最低的韧脆转变温度,通过控轧控冷工艺,充分利用钢的固溶强化、晶粒细化,析出强化等强化手段,有效综合提高钢板综合性能。
51.本实施方式还提供一种耐腐蚀460mpa级钢板,其采用上述的耐腐蚀460mpa级钢板生产方法制造得到,钢板屈服强度≥460mpa,抗拉强度为540~720mpa,断后延伸率≥20%,-50℃冲击吸收能量kv2≥100j。
52.在添加了稀土元素对钢液进行净化后,钢板最大夹杂物的长宽积≤150μm2,在gb/t10561标准下的a、b、c、d类夹杂物评级均≤1.5级,且a、b、c、d类夹杂物评级之和≤3.0级。
53.在gb/t 10125-2012试验条件下,钢板的平均腐蚀失重率≤1.315g/(m2·
h)。
54.钢板在焊接热输入量≤80kj/cm时,焊后热影响区-50℃冲击吸收能量kv2≥80j。
55.综上所述,本实施方式采用cr ni mo cu p复合添加的耐蚀合金化成分体系,确保耐腐蚀性能和焊接性能的前提下,节约贵重合金的使用量。在杂质元素严格控制的同时,采用la、ce、pr、nd中的一种或多种稀土元素使钢水纯净化,进一步提升耐腐蚀性。在化学成分的综合设计基础上,通过对轧制和冷却过程工艺参数的精确控制,实现钢板组织、夹杂物含量和尺寸的精准控制,获得综合性能良好的耐海洋大气腐蚀的460mpa级风电塔筒用钢板。
56.以下通过4个实施例和3个对比例,进一步对本发明的具体实施方式予以介绍。
57.实施例1~4和对比例1~3的钢板的化学成分如表1所示。
58.对比例1的稀土含量低于本发明要求的0.02~0.03%。
59.对比例2的p含量低于本发明要求的0.015~0.025%,cr含量低于本发明要求的0.50~0.60%,ni含量低于本发明要求的0.30~0.40%,cu含量低于本发明要求的0.40~0.45%,耐大气腐蚀性指数i低于本发明要求的6.5。
60.对比例3是普通q460高强钢,不含ni、cu、mo、稀土耐腐蚀性元素,p和cr的含量也低于本发明要求。
61.实施例1~4和对比例1~3的钢板,均采用上述生产方法进行生产,在轧制工序中,采用两阶段控制轧制制备成厚度如表2所示的钢板。
62.在控制冷却工序中,实施例1~4和对比例1~3的粗轧阶段压下率、终轧温度、终冷温度和冷却速率如表2所示。
63.在实施例1~4和对比例1~3的各个钢板冷却后,进行取样检测:实施例1~4和对比例1~3的夹杂物检测结果如表3所示,实施例1~4和对比例2钢中最大夹杂物的长宽积≤150μm2,a、b、c、d类夹杂物评级均≤1.5级,且四类夹杂物评级之和a b c d≤3.0级。对比例1和对比例3不含稀土元素,钢板中四类夹杂物评级之和高于3.0级,钢板中最大夹杂物的长宽积高于150μm2。
64.实施例1~4和对比例1~3钢板的屈服强度、抗拉强度、断后伸长率、低温-50℃冲击吸收能量kv2如表4所示,实施例1~4、对比例1和对比例3钢板的屈服强度≥460mpa,抗拉强度为540~720mpa,断后延伸率≥20%,-50℃冲击吸收能量kv2≥100j。对比例2的碳当量低于0.39,因此钢板的屈服强度低于60mpa,抗拉强度低于540mpa。对比例3是普通q460高强钢,微观组织是针状铁素体 粒状贝氏体,但其中针状铁素体含量不符合本发明要求的≥85%,因此钢板-50℃冲击吸收能量kv2低于100j。
65.参考gb/t 10125-2012《人造气氛腐蚀试验盐雾试验》,在环境温度35
±
2℃的50
±
5g/l中性nacl盐雾腐蚀条件下,检测实施例1~4和对比例1~3钢板的耐海洋大气腐蚀性能,经72h试验后,钢板的平均腐蚀失重率见表4,实施例1~4钢板的平均腐蚀失重率为1.079~1.315g/(m2·
h)。对比例1钢板点蚀严重,平均腐蚀失重率为1.946 g/(m2·
h),高于实施例。
对比例2平均腐蚀失重率为2.975g/(m2·
h),高于实施例。对比例3是普通q460高强钢,平均腐蚀失重率最高,达3.428g/(m2·
h)。实施例1~4与对比例3普通q460高强钢相比,腐蚀速率降低50%以上。
66.对实施例4进行双丝埋弧焊,焊接热输入量77
±
3kj/cm,焊接接头热影响区熔合线fl、fl 2、fl 5、fl 20处的-50℃低温冲击功检测结果如表5所示。
67.应当理解,虽然本说明书按照实施方式加以描述,但并非每个实施方式仅包含一个独立的技术方案,说明书的这种叙述方式仅仅是为清楚起见,本领域技术人员应当将说明书作为一个整体,各实施方式中的技术方案也可以经适当组合,形成本领域技术人员可以理解的其他实施方式。
68.上文所列出的一系列的详细说明仅仅是针对本发明的可行性实施方式的具体说明,并非用以限制本发明的保护范围,凡未脱离本发明技艺精神所作的等效实施方式或变更均应包含在本发明的保护范围之内。
再多了解一些
本文用于创业者技术爱好者查询,仅供学习研究,如用于商业用途,请联系技术所有人。