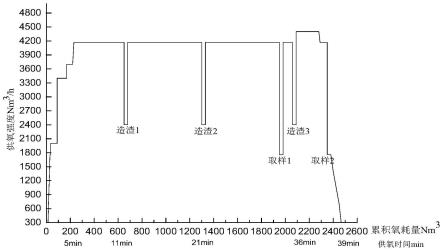
1.本发明属于钢铁冶炼技术领域,具体涉及一种缩短电炉高铁水比冶炼周期的方法。
背景技术:
2.随着钢铁行业的发展和市场竞争的白热化,在钢铁行业面临的压力剧增的严峻形势下,优化钢铁产品的品种结构、提高产品质量和降低产品成本就显得尤为重要。为了提高生产率,改善品种结构,提高产品质量,降低原辅材料和炉料成本,满足高品质钢的生产需要,钢铁企业都在想法设法地开发或者引进先进的炼钢技术,以提高炼钢生产技术水平。
3.采用铁水作为入炉料是现代电弧炉炼钢的一项新工艺,用铁水冶炼的钢种纯净度高,残余元素含量很低,因此,铁水可以作为电弧炉冶炼优质钢的炉料。采用铁水做金属炉料,既可以缓解废钢供给紧张的局面,同时铁水带入的大量物理热和化学热拥有废钢不可替代的优势,铁水作为入炉料在缩短冶炼时间、降低电耗、稀释废钢中的残余元素、降低钢中气体含量方面都起到重要的作用。
4.但在高铁水比电炉生产冶炼过程中,存在着一些问题:
5.(1)铁水比例达到80%以上,实现了电炉转炉化冶炼生产模式,熔池形成较早,使用传统全废钢生产供氧和造渣制度,易造成渣、钢混合流出,导致钢铁料消耗上升。
6.(2)冶炼中后期熔池温度上升快,碳氧反应剧烈,炉渣中铁氧化物含量快速降低,造成炉渣“返干”现象,严重影响脱磷效果和生产的顺行。
7.(3)炉渣“返干”导致钢水喷溅到炉壁及炉盖上,形成粘钢,严重影响炉体设备的正常使用,延长非冶炼周期。
8.(4)铁水比例达到一定程度时,铁水配碳过高,脱碳时间增加,造成冶炼周期延长。
技术实现要素:
9.为解决上述技术问题,本发明提供了一种缩短电炉高铁水比冶炼周期的方法,本发明采用“炉壁 底侧吹”复合供氧技术和高铁水比不通电的操作方法,通过明确留钢、留渣制度确保整个冶炼过程平稳易控,通过优化供氧和造渣制度,提高脱碳、升温和脱磷效率,同时有效的减少烧枪、冶炼喷溅和炉渣“返干”情况的发生,达到了缩短电炉高铁水比冶炼周期的目的。
10.为实现上述目的,本发明采取的技术方案如下:
11.一种缩短电炉高铁水比冶炼周期的方法,所述方法包括以下步骤:
12.(1)按照铁水比80~85wt%和废钢料15~20wt%的比例搭配入炉料;废钢料由料罐先投加到炉内,随后倒入热装铁水;
13.(2)进完料后开始供氧,采用2支炉壁集束氧枪、2支侧吹氧枪及1支炉门氧枪;冶炼1min后,壁集束氧枪和侧吹氧枪均开启低氧;冶炼3min后,壁集束氧枪和侧吹氧枪均开启中氧;冶炼5min后,壁集束氧枪和侧吹氧枪均开启高氧,后续全程高氧供氧操作;在冶炼初期
大量废钢未融化堆积在炉膛内,过早进行高强度的供氧极易造成氧气射流反弹烧损集束氧枪及侧吹氧枪,出现集束氧枪漏水甚至侧吹枪部位炉壁穿钢的事故;
14.(3)冶炼开始至投加第一批石灰期间,可按6~8kg/t钢排渣量进行排渣;用氧量达到600~800nm3时加入第一批石灰,在此耗氧量区间可以保证第一批石灰入炉后有效熔化,过早投加会因熔池温度偏低,石灰入炉后“结坨”导致后续炉渣条件恶化影响脱磷,并且难以快速升温;用氧量达到1200~1400nm3时加入第二批石灰;如果加入第二批石灰后炉渣未完全化开,则在炉内钢水温度达到 1550~1570℃时,加入第三批石灰;
15.(4)在炉渣完全化开后,按4~6kg/t的渣量进行排渣操作,防止后续冶炼发生喷溅,并确保回炉后炉渣不会没过出钢口,以保证能够正常进行出钢口的填砂操作;
16.(5)当钢水温度达到1600~1640℃,磷含量低于0.015%,碳含量高于0.06%时,进行放钢操作。
17.步骤(1)中,铁水温度不低于1250℃,铁水温度过低将导致冶炼过程中热能不足,冶炼终点钢水过氧化严重,并且造成冶炼时间延长。
18.步骤(2)中,炉壁集束氧枪的单支最大氧气流量为1400nm3/h,氧气压力 1.12mpa~1.15mpa;侧吹氧枪的单支最大氧气流量为600nm3/h,氧气压力 0.83mpa~0.85mpa;炉门氧枪的最大氧气流量500nm3/h,氧气压力 0.10mpa~0.12mpa。其中侧吹氧枪安装在下炉底与钢水直接接触,起到脱碳升温和搅拌熔池的作用。
19.步骤(2)中,为提高前期的供氧效率,同时避免冶炼前期因废钢未融化造成氧气反弹烧枪的事故出现,具体炉壁集束氧枪的供氧强度如下:冶炼1min 后,开启低氧500nm3/h,冶炼3min后,开启中氧1000nm3/h,冶炼5min后,开启高氧1400nm3/h,后续全程高氧供氧操作。
20.步骤(2)中,为提高前期的供氧效率,同时避免冶炼前期因废钢未融化造成氧气反弹烧枪的事故出现,具体侧吹氧枪的供氧强度如下:冶炼1min后开启低氧380nm3/h,冶炼2min后开启中氧500nm3/h,冶炼3min后开启高氧600 nm3/h,后续全程高氧供氧操作。
21.步骤(3)中,第一批石灰的投加量为10~12kg/t钢,此投加量一方面可以保证冶炼前期的脱磷效果,另一方面可以保证入炉石灰有效熔化。
22.步骤(3)中,第二批石灰的投加量为6~8kg/t钢,投加完毕后开启炉门氧枪高氧进行化渣操作,以保证冶炼中期的炉渣具有较好的流动性。
23.步骤(3)中,在用氧量达到1500~1600nm3,供氧时间达到25~28min时要保证炉渣处于良好的流动状态,若出现“返干”现象则及时将集束氧枪的供氧强度由1400nm3/h调整到1000nm3/h进行化渣,并将炉门氧枪调至高氧档位进行化渣操作,待炉渣化开后进行第一次测温取样操作。
24.步骤(3)中,第三批石灰的投加量为5~6kg/t钢;后续按照5~8℃/min的升温速度继续对钢水进行供氧升温。
25.步骤(5)中,放钢之前集束氧枪调至保护档位150nm3/h,侧吹氧枪气源由氧气切换为氮气,避免出钢过程中炉渣飞溅严重。
26.新炉第1炉无需留钢,便于安装底侧吹氧枪,2~50炉龄留钢5~10t,50~100 炉龄留钢10~15t,100炉龄以上留钢15~18t,不同的炉龄采用其相应的留钢量可有效保证各炉况期间操作平稳进行,避免了因炉容变化及钢液面波动而引起炉渣喷溅(留钢过少)、炉渣“返干”严重(留钢过多)、操作被动和冶炼时间延长等不利情况出现。
27.与现有技术相比,本发明具有以下有益效果:
28.本发明方法实现了电炉转炉化操作,有效的提高了电炉高铁水比冶炼的生产节奏,实现了在铁水比达到80%以上的条件下将电炉的单炉冶炼周期稳定控制在37-40min之内。
附图说明
29.图1为主要供氧枪位图;
30.图2为本发明的冶炼操作曲线图。
具体实施方式
[0031][0032]
本发明提供的一种缩短电炉高铁水比冶炼周期的方法,所述方法包括以下步骤:
[0033]
(1)按照铁水比80~85wt%和废钢料15~20wt%的比例搭配入炉料;废钢料由料罐先投加到炉内,随后倒入热装铁水;
[0034]
(2)进完料后开始供氧,采用2支炉壁集束氧枪、2支侧吹氧枪及1支炉门氧枪;冶炼1min后,壁集束氧枪和侧吹氧枪均开启低氧;冶炼3min后,壁集束氧枪和侧吹氧枪均开启中氧;具体为:
[0035]
炉壁集束氧枪的供氧强度如下:冶炼1min后,开启低氧500nm3/h,冶炼 3min后,开启中氧1000nm3/h,冶炼5min后,开启高氧1400nm3/h,后续全程高氧供氧操作;
[0036]
侧吹氧枪的供氧强度如下:冶炼1min后开启低氧380nm3/h,冶炼2min后开启中氧500nm3/h,冶炼3min后开启高氧600nm3/h,后续全程高氧供氧操作;
[0037]
(3)用氧量达到600~800nm3时加入第一批石灰,第一批石灰的投加量为 10~12kg/t钢;在供氧时长达到18~22min时,用氧量达到1200~1400nm3时加入第二批石灰,第二批石灰的投加量为6~8kg/t钢;在用氧量达到1600nm3,供氧时间达到25~28min时要保证炉渣处于良好的流动状态,若出现“返干”现象则及时将集束氧枪的供氧强度由1400nm3/h调整到1000nm3/h进行化渣,并将炉门氧枪调至高氧档位进行化渣操作,待炉渣化开后进行第一次测温取样操作;炉内钢水温度达到1550~1570℃时,加入第三批石灰,第三批石灰的投加量为 5~6kg/t钢;
[0038]
(4)在炉渣完全化开后,按4~6kg/t的渣量进行排渣操作;
[0039]
(5)当钢水温度达到1600~1640℃,磷含量低于0.015%,碳含量高于0.06%时,进行放钢操作,放钢之前集束氧枪调至保护档位150nm3/h,侧吹氧枪气源由氧气切换为氮气,避免出钢过程中炉渣飞溅严重;新炉第1炉无需留钢,便于安装底侧吹氧枪,2~50炉龄留钢5~10t,50~100炉龄留钢10~15t,100炉龄以上留钢15~18t
[0040]
下面结合实施例对本发明进行详细说明。
[0041]
实施例1
[0042]
使用公称容量为50吨的电弧炉,拥有2支炉壁氧枪,2支侧吹氧枪及一支炉门氧枪。所兑铁水主要成分为c:4.5%,si:0.468%,mn:0.378%,s:0.025%, p:0.138%,铁水温度为1273℃;废钢装入量11.4t,铁水装入量43.3t;炉龄116 炉,留钢、留渣15t。
[0043]
具体电炉冶炼操作步骤如下:
[0044]
(1)旋出炉盖后用料篮加入废钢,随后用行车倒入热装铁水,旋回炉盖开始冶炼。
[0045]
(2)将侧吹氧枪由氮气切换到供氧,集束氧枪在供氧时长为1min时开启低氧500nm3/h;供氧时长3min时,开启中氧1000nm3/h;供氧时长5min时,开启高氧1400nm3/h。侧吹氧枪按照冶炼1min后开启低氧380nm3/h,冶炼2min 后开启中氧500nm3/h,冶炼3min后开启高氧600nm3/h。
[0046]
(3)冶炼开始至投加第一批石灰之间按6~8kg/t排渣量进行排渣,在氧耗达到720nm3时,原始渣碱度显著降低,炉渣变稀,此时加入第一批石灰580kg,在石灰化开之前不排渣,在供氧量达到1300nm3时,向炉内加入第二批石灰 380kg,在供氧量达到1950nm3时炉渣已化透,进行第一次测温取样,钢水测温1545℃,取样分析结果为c:0.563%,p:0.024%。随后继续投加石灰350kg,继续供氧升温,期间炉门氧枪档位调至高氧档位进行强化化渣操作,待炉内石灰彻底化开后,喷粉排渣,按4~6kg/t的渣量进行排渣操作,然后进行第二次测温、取样操作,钢水测温1608℃,取样分析结果为c:0.083%,p:0.013%。
[0047]
(4)随后将集束氧枪调至保护档位,侧吹氧枪由供氧切换到氮气,完成冶炼操作进行放钢。从进料到出钢完毕共用时40min,供氧时长36min。
[0048]
实施例2
[0049]
使用公称容量为50吨的电弧炉,拥有2支炉壁氧枪,2支侧吹氧枪及一支炉门氧枪。所兑铁水主要成分为c:4.5%,si:0.482%,mn:0.355%,s:0.024%, p:0.138%,铁水温度为1306℃;废钢装入量12.1t,铁水装入量42.4t;炉龄214 炉,留钢、留渣18t。
[0050]
具体电炉冶炼操作步骤如下:
[0051]
(1)旋出炉盖后加入废钢、倒入铁水后,旋回炉盖开始冶炼。
[0052]
(2)将侧吹氧枪由氮气切换到供氧,集束氧枪在供氧时长为1min时开启低氧500nm3/h;供氧时长3min时,开启中氧1000nm3/h;供氧时长5min时,开启高氧1400nm3/h。侧吹氧枪按照冶炼1min后开启低氧380nm3/h,冶炼2min 后开启中氧500nm3/h,冶炼3min后开启高氧600nm3/h。
[0053]
(3)冶炼开始至投加第一批石灰之间按6~8kg/t排渣量进行排渣,在氧耗达到600nm3时,加入第一批石灰600kg,在石灰化开之前不排渣,在供氧量达到1200nm3左右时,向炉内加入第二批石灰400kg,在供氧量达到1800nm3时进行第一次测温取样,钢水测温1567℃,取样分析结果为c:0.682%,p: 0.021%。随后继续投加石灰320kg,继续供氧升温,将炉门氧枪档位调至高氧档位进行强化化渣操作,炉内石灰彻底化开后,喷粉排渣,按4~6kg/t的渣量进行排渣操作,进行第二次测温、样操作,钢水测温1620℃,取样分析结果为c: 0.12%,p:0.013%。
[0054]
(3)随后将集束氧枪调至保护档位,侧吹氧枪由供氧切换到氮气,完成冶炼操作进行放钢。从进料到出钢完毕共用时38min,供氧时长35min。
[0055]
对比例1
[0056]
使用公称容量为50吨的电弧炉,拥有2支炉壁氧枪,2支侧吹氧枪及一支炉门氧枪。所兑铁水主要成分为c:4.5%,si:0.436%,mn:0.375%,s:0.022%, p:0.136%,铁水温度为1314℃;废钢装入量11.9t,铁水装入量42.7t;炉龄207 炉,炉内留钢、留渣5t。
[0057]
由于未进行正常的留钢、留渣操作,后期炉役仅留钢、留渣5t,正常装料后开始供
氧冶炼,由于是后期炉役,炉膛容量显著变大,加之留钢、留渣量不足(炉龄207炉仅5t),造成炉内钢液面与集束氧枪距离显著增加,冶炼过程中氧气对钢水冲击深度降低,造成脱碳强度下降;而由于渣面接受氧量增大,造成过度化渣,渣层含氧量过高与钢液面接触后不断产生剧烈反应,导致炉渣携带钢水大量往炉外喷涌,严重影响操作的顺行,为抑制炉渣喷涌,只能提前并多次投加石灰,造成熔剂浪费,钢水流失严重,并且脱碳时间长,从进料到出钢完毕共用时48min,供氧时长42min。
[0058]
对比例2
[0059]
使用公称容量为50吨的电弧炉,拥有2支炉壁氧枪,2支侧吹氧枪及一支炉门氧枪。所兑铁水主要成分为c:4.5%,si:0.414%,mn:0.326%,s:0.024%, p:0.136%,铁水温度为1289℃;废钢装入量12.3t,铁水装入量43.1t;炉龄126 炉,留钢、留渣15t。
[0060]
由于操作人员一昧的追求快节奏,多次提前开氧,在本次冶炼供氧时间为 1—2min内便打开了侧吹和集束氧枪的高氧档位,数分钟后,炉膛内频繁出现“噼啪”的闷响声,且冶炼后期炉内温度长时间停留在1550~1570℃,后续难于升温。冶炼结束后对炉内进行检查发现一支集束氧枪已漏水,且侧吹枪口附近的耐材侵蚀较为严重,出现凹洞。后续停炉对漏水集束氧枪进行了更换,并对侧吹位进行了喷补。
[0061]
对比例3
[0062]
使用公称容量为50吨的电弧炉,拥有2支炉壁氧枪,2支侧吹氧枪及一支炉门氧枪。所兑铁水主要成分为c:4.5%,si:0.472%,mn:0.309%,s:0.024%, p:0.137%,铁水温度为1278℃;废钢装入量12.6t,铁水装入量42.8t;炉龄108 炉,留钢、留渣15t。
[0063]
前期按实施案例1的供氧制度进行操作,但在氧耗为450nm3时,便加入第一批石灰600kg,投加完第一批石灰后炉膛内炉渣碱度未明显得到提升,炉渣依然偏稀,随后便在氧耗为900nm3时便投加了第二批石灰400kg,在短暂的供氧之后,炉渣开始返干,开启炉门氧枪高氧进行化渣也未能有效化开炉渣,后经查看炉膛发现两批石灰大量“结坨”浮在钢液面,石灰未能有效熔化覆盖钢液面,导致供氧过程中钢水飞溅严重,无法有效进行冶炼操作。后分析原因主要是由于石灰投加过早,熔池内的石灰无法及时融化,成坨浮在钢液面,后续投加的石灰缺乏熔融炉渣的助熔效果,导致后续石灰继续成坨浮在钢液面,致使渣况急剧恶化,无法进行正常的冶炼。随后继续开启炉门氧枪高氧,将集束氧枪调至1000nm3/h进行强化化渣操作,并使用手氧枪伸入炉门内对准“结坨”的石灰进行吹氧熔化,将炉渣化开后再进行后续的冶炼操作。此次操作由于过早投加石灰导致后续冶炼条件持续恶化,造成冶炼用时共52min,供氧时间47min。
[0064]
上述参照实施例对一种缩短电炉高铁水比冶炼周期的方法进行的详细描述,是说明性的而不是限定性的,可按照所限定范围列举出若干个实施例,因此在不脱离本发明总体构思下的变化和修改,应属本发明的保护范围之内。
再多了解一些
本文用于创业者技术爱好者查询,仅供学习研究,如用于商业用途,请联系技术所有人。