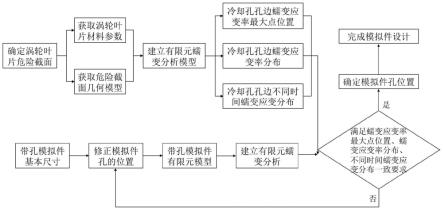
1.本发明属于航空航天发动机技术领域,具体涉及一种航空发动机涡轮叶片后缘冷却孔的蠕变模拟件设计方法。
背景技术:
2.涡轮叶片是航空发动机的关键安全件,在服役过程中承受着复杂交变的力载荷和温度载荷,制约着航空发动机的使用寿命。针对持久性方面,涡轮叶片工作时,遭受着涡轮高速旋转带来的巨大离心载荷,高速燃气冲击叶片带来的气动压力载荷,高温燃气以及温度梯度带来的温度载荷,材料在长时间的高温及离心力、压力载荷作用下,尽管应力水平低于屈服极限,但还是会发生连续的缓慢的不可恢复的变形,不仅会降低发动机的飞行效率还会导致叶片产生径向伸长、扭转和弯曲,且随着变形量增大到超过材料的延性范围时,材料将会蠕变断裂。目前涡轮叶片蠕变寿命预测仍缺少试验数据的支持,需要完整的、可靠的、经过试验验证的发动机强度设计系统。冷却孔是涡轮叶片上比较常见的结构,其尺寸相对较小,会造成应力集中效应,大大降低持久寿命。因此,有必要对冷却孔部位的蠕变性能进行分析。但采用真实叶片试验成本高昂,且缺少冷却孔部位的模拟件设计方法,因此需要提出相应模拟件设计方法。
技术实现要素:
3.为克服现有技术的不足,本发明提供一种航空发动机涡轮叶片后缘冷却孔的蠕变模拟件设计方法,具体包括如下步骤:
4.本发明的解决方案为:一种航空发动机涡轮叶片后缘冷却孔的蠕变模拟件设计方法,以涡轮叶片后缘冷却孔为模拟部位,根据涡轮叶片危险截面后缘及后缘冷却孔几何尺寸确定模拟件为等厚平板,平板的长度为后缘的长度,平板的厚度为后缘最大厚度,模拟件孔为沿着长度方向的柱形通孔,通过优化模拟件孔的位置保证蠕变应变率最大点的位置、蠕变应变率、von mises等效应力与涡轮叶片危险截面后缘冷却孔一致,实现步骤如下:
5.步骤(1):确定涡轮叶片危险截面,获取危险截面的几何模型,测量危险截面后缘及后缘冷却孔的几何尺寸;
6.步骤(2):获取涡轮叶片的工况条件以及工况条件下的材料性能参数;所述工况条件包括涡轮叶片工作的温度、受到的离心载荷和气动载荷;所述材料性能参数包括涡轮叶片材料的密度,在工作温度下的弹性模量、泊松比、膨胀系数和蠕变本构参数;
7.步骤(3):依据步骤(1)中的所述几何模型和所述步骤(2)中的所述工况条件以及工况条件下的材料性能参数,建立涡轮叶片有限元蠕变分析模型,计算获得危险截面后缘冷却孔孔边蠕变应变率最大点,获取该点的蠕变应变率和不同时间蠕变应变分布;
8.步骤(4):基于后缘及后缘冷却孔的几何尺寸确定带孔的模拟件基本形状;依据所述步骤(1)中所述的几何尺寸,确定危险截面后缘到叶身的厚度变化远小于后缘最大厚度,且后缘的厚度远小于后缘的长度;确定后缘冷却孔为沿着后缘长度方向的柱形通孔,且与
涡轮叶片横截面成一定的角度,且模拟件孔的角度、直径与后缘冷却孔的角度、直径相同,至此完成模拟件基本形状的确定;
9.步骤(5):通过调整所述步骤(4)所述的模拟件孔在厚度方向的位置和单轴拉伸载荷,进行有限元蠕变分析,保证所述模拟件孔的孔边蠕变应变率最大点的位置、蠕变应变率分布、不同时间蠕变应变分布与涡轮叶片危险截面后缘冷却孔孔边蠕变应变率最大点的位置、蠕变应变率分布、不同时间蠕变应变分布相同。
10.进一步地,所述步骤(1)中的涡轮叶片危险截面通过有限元仿真或试验确定。
11.进一步地,所述几何模型指通过计算机辅助设计软件设计完成的涡轮叶片三维几何模型。
12.进一步地,所述后缘及后缘冷却孔的几何尺寸包括危险截面后缘的厚度、后缘到叶身之间变化的厚度、后缘的长度、后缘冷却孔的直径、后缘冷却孔的长度和后缘冷却孔相对于后缘的空间位置。
13.进一步地,所述步骤(4)中,所述模拟件采用等厚平板,所述等厚平板的长度为后缘的长度,厚度为后缘最大厚度。
14.本发明与现有技术相比的优点在于:本发明在现有模拟件设计方法的基础上,提出了一种航空发动机涡轮叶片后缘冷却孔的蠕变模拟件设计方法,用以研究后缘冷却孔对航空发动机涡轮叶片蠕变寿命的影响,能够模拟真实涡轮叶片后缘冷却孔部位的蠕变试验效果。本发明在反映涡轮叶片后缘冷却孔部位几何特征的情况下,进一步实现蠕变应变率最大点的位置、蠕变应变率分布、不同时间蠕变应变分布与涡轮叶片危险截面后缘冷却孔一致,满足涡轮叶片后缘冷却孔蠕变试验模拟的需求,服务与支撑航空发动机涡轮叶片模拟件设计与寿命预测技术。目前相关技术未见报道,本发明弥补了相关研究不足。
附图说明
15.图1为本发明的一种航空发动机涡轮叶片后缘冷却孔的蠕变模拟件设计方法实施流程;
16.图2为某涡轮叶片危险截面后缘部分示意图;
17.图3为不同温度和载荷条件下蠕变应变随时间的变化曲线;
18.图4为模拟件初始形状和几何尺寸;
19.图5为优化后的模拟件形状和几何尺寸;
20.图6为涡轮叶片和模拟件孔边蠕变应变率沿轴线方向分布对比;
21.图7为涡轮叶片和模拟件孔边蠕变应变在100,200和300小时沿轴线方向的分布对比。
具体实施方式
22.为了使本发明的目的、技术方案及优点更加清楚明白,以下结合附图及实施例,对本发明进行进一步详细说明。应当理解,此处所描述的具体实施例仅仅用以解释本发明,并不用于限定本发明。此外,下面所描述的本发明各个实施方式中所涉及到的技术特征只要彼此之间未构成冲突就可以相互组合。
23.下面结合附图,对本发明一种航空发动机涡轮叶片后缘冷却孔的蠕变模拟件设计
方法技术方案做进一步说明。
24.如图1所示,本发明涉及一种航空发动机涡轮叶片后缘冷却孔的蠕变模拟件设计方法,实现步骤如下:
25.第一步,确定涡轮叶片危险截面,获取所述危险截面的几何模型,测量危险截面后缘及后缘冷却孔的几何尺寸;所述涡轮叶片危险截面通过有限元仿真或试验确定;所述几何模型指通过计算机辅助设计软件设计完成的涡轮叶片三维几何模型;所述后缘及后缘冷却孔尺寸包括危险截面后缘的厚度、后缘到叶身之间变化的厚度、后缘的长度、后缘冷却孔的直径、后缘冷却孔的长度、后缘冷却孔相对于后缘的空间位置。例如,如图2所示的某涡轮叶片危险截面后缘部分,其后缘的厚度从边缘到叶身逐渐从0.8mm增加到1.8mm,后缘的长度为5.9mm,后缘冷却孔的直径为0.6mm,冷却孔的长度为6mm,冷却孔与后缘截面夹角为10
°
。
26.第二步,获取涡轮叶片的工况条件以及工况条件下的材料性能参数;所述工况条件包括涡轮叶片工作的温度,受到的离心载荷和气动载荷;所述材料性能参数包括涡轮叶片的材料的密度,在工作温度下的弹性模量、泊松比和蠕变本构参数;对涡轮叶片起飞状态进行分析,涡轮叶片起飞状态温度场的温度范围为525℃-1068℃,转速为45450rpm,材料采用dd6单晶镍基高温合金,依据中国航空材料手册,密度为8.78g/cm3,随温度变化的弹性模量如表1所示,随温度变化的泊松比如表2所示,采用norton蠕变本构模型,基于如图3所示的不同温度下的蠕变应变随时间变化曲线拟合获得norton蠕变本构材料参数。
27.表1单晶镍基高温合金在不同温度、不同取向下的弹性模量
[0028][0029]
表2单晶镍基高温合金在不同温度、不同取向下的泊松比
[0030][0031]
第三步,依据第一步中的几何模型,第二步中的工况条件以及工况条件下的材料性能参数,建立涡轮叶片有限元蠕变分析模型,计算获得危险截面后缘冷却孔孔边蠕变应变率最大点,获取该点沿轴向的蠕变应变率分布、不同时间蠕变应变分布;蠕变应变率通过
对应变进行时间微分获得,计算孔边缘应变率最大的点的节点坐标,提取应变率分布和100h、200h、300h的蠕变应变分布。
[0032]
第四步,基于后缘及后缘冷却孔尺寸确定带孔模拟件基本形状;依据第一步的几何尺寸,确定危险截面后缘到叶身的厚度变化远小于后缘最大厚度,且后缘的厚度远小于后缘的长度,模拟件采用等厚平板,平板的长度为后缘的长度,平板的厚度为后缘最大厚度;确定后缘冷却孔为沿着后缘长度方向的柱形通孔,且与叶片横截面成一定的角度,模拟件孔为沿着长度方向的柱形通孔,且孔的角度、直径与后缘冷却孔的角度、直径相同,至此完成模拟件基本形状的确定。如图4所示,模拟件的考核段平板的宽度l为5.9mm,厚度为1.8mm,孔的直径d为0.6mm,孔与平板边缘夹角θ为80
°
,孔的长度为6mm。
[0033]
第五步,通过调整第四步的模拟件孔在厚度方向的位置和平板的形状尺寸,进行有限元蠕变分析,保证模拟件孔的孔边蠕变应变率最大点的位置、蠕变应变率分布、不同时间蠕变应变分布与涡轮叶片危险截面后缘冷却孔孔边蠕变应变率最大点的位置、蠕变应变率分布、不同时间蠕变应变分布相同。首先对模拟件孔在厚度中心和靠近平板边缘的情况进行有限元蠕变分析,获得孔边蠕变应变率最大点的位置、蠕变应变率分布和不同时间蠕变应变分布,由于蠕变应变率梯度无法满足要求,在靠近孔的平板边缘添加圆弧缺口,对圆弧缺口的半径r和深度c进行优化,如图5所示。当半径r为4.5mm,深度c为0.5mm,模拟件蠕变应变率最大点的位置、蠕变应变率分布、不同时间蠕变应变分布与叶片一致,蠕变应变率分布如图6所示,不同时间蠕变应变分布如图7所示,至此完成模拟件的设计。
[0034]
提供以上实施例仅仅是为了描述本发明的目的,而并非要限制本发明的范围。本发明的范围由所附权利要求限定。不脱离本发明的精神和原理而做出的各种等同替换和修改,均应涵盖在本发明的范围之内。
再多了解一些
本文用于创业者技术爱好者查询,仅供学习研究,如用于商业用途,请联系技术所有人。