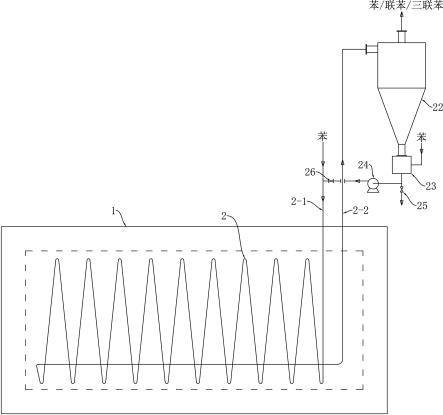
1.本发明涉及含碳物料的干馏生产煤气、焦炭、焦油或类似物的技术领域,具体为烃的蒸气裂解炉装置。
背景技术:
2.联苯由于具有高的热稳定性及低蒸气压,长期以来常单独或与二苯醚混合后作为载热体使用。工业上应用较广的载热体,是由联苯和二苯醚组成质量比为26.5∶73.5的低共熔混合物,可在12~400℃温度范围内使用,但工业上常使用的温度范围是250~360℃。由联苯、三联苯等组成(以质量计联苯13%,三联苯61%)的山都蜡能有效地吸收放射线,适宜作为核电站的载热体。而三联苯正好又是苯热解制联苯时的副产物。联苯的另一个主要用途是在印染工业中作为导染剂,也可用作柑橘包装纸的浸渍剂。
3.1926年,美国陶氏化学公司等开始用苯通过热解法生产联苯:最初是采用苯蒸气鼓泡通过750℃的熔融铅浴,后改用氯化钠和氯化钙盐浴,以后使用催化活性低的金属(如镍铬合金)制成的电阻加热器。
4.目前工业中普遍采用苯高温脱氢的方法来生产联苯,具体而言,苯高温脱氢的方法来生产联苯是利用管式裂解炉将苯蒸气通入到裂解炉的炉管内加热到700-800℃,由两个苯分子各失去一个氢原子互相结合而制得联苯,同时生成氢气。如公开号为cn107641518a的专利申请中公开的一种常压高温裂解系统及其裂解炉,公开号为cn113652246a的专利申请中公开的一种电加热乙烯裂解炉,上述两篇专利中记载的内容虽然不是针对苯高温脱氢的方法来生产联苯,但是其记载的具体设备也适用于苯高温脱氢生产联苯的反应。现有技术的中的裂解炉设备,存在如下问题:结构布局不够合理,炉体的设置结构稳定性、炉体的检修、炉管的具体形状及设置方式等均有待优化。
5.此外,苯高温脱氢的方法来生产联苯的工艺中,主要有三个反应,一是主反应,既生成联苯的反应;二是苯的二次反应,既生成三联苯的反应;三是苯的深度碳化,引起炉管内壁结焦。除主反应以外,其他反应均是非期望的副反应,尤其是苯的碳化结焦。由于炉管内壁焦炭堆积会导致需要更高的炉温和炉管温度的不均匀分布,影响反应效果,在运行一段时间后需要裂化炉停车以烧尽焦炭沉积物。这会导致生产效率的降低。因此在反应中要避免焦炭的沉积,减少结焦或在线除焦(脱焦),以延长设备连续运行的时间,减少停车除焦(脱焦)的频次。
6.避免不期望的副反应的产生方法是,在反应中避免局部过热以及物料在高温区停留过长,以防止生成炭和大量的多联苯,实际生产过程常采用很高的物料流速并加入过热蒸气或高温烟道气进行稀释。当有催化剂(mgo、tho2和coo等)存在时,在较低温度下即可获得较高的联苯产率。
7.现有技术中,典型的除焦(脱焦)方法包括使蒸气和空气的混合物流动通过指定区域。所述的混合物通过解吸(化学和/或物理)、消融(例如包括磨损,腐蚀,碎裂,剥离,气化和蒸发中的一种或多种)和反应(例如包括燃烧,部分燃烧和氢转移中的一种或多种)等中
的一种或多种去除焦炭;或者在炉管内设置特定的结构诱导焦粒在设置的所述结构上附着,避免在炉管内部附着。
8.上述现有技术存在的问题,例如混合物通过解吸除焦,需要设备停车,影响生成效率;利用炉管设置内部结构诱导结焦,由于对应的结构与炉管内部有接触,接触的地方容易形成焦炭的沉积,反而不利于除焦。
技术实现要素:
9.本发明所要解决的技术问题是提供一种便于在线除焦的烃类物质的蒸气裂解炉装置。
10.为解决上述问题,本发明所采取的技术方案是:一种烃的蒸气裂解炉装置,其包括矩形的炉箱体、炉盘管、分离器和储存罐,所述炉箱体的一侧开口并设置有可打开的炉门,所述炉盘管的盘管主体为横向设置的螺旋盘管结构,炉箱体的内侧壁设置有用于给炉盘管加热的电热带;所述炉盘管的出料管连接分离器,所述分离器底部设置有储存罐,所述储存罐通过管道与炉盘管的进料管连接,所述分离器用于分离添加到炉盘管内的催化剂颗粒和炉盘管内产生的焦炭颗粒,所述储存罐上还设置有物料添加口和排料口,所述储存罐内添加有固体催化剂颗粒,固体催化剂颗粒在裂解炉装置中循环。
11.作为本发明的一种实施方式,所述储存罐与所述进料管之间的管道上设置有用于加压的泵。
12.作为本发明的一种实施方式,所述分离器和储存罐之间还设置有烧焦器,所述烧焦器用于将分离器分离出来的固体颗粒中的焦炭颗粒进行烧焦处理。
13.作为本发明的一种实施方式,所述炉盘管的进料管和出料管均连接同一换热器,进料管中的物料与出料管中的物料进行热交换。
14.作为本发明的一种实施方式,所述炉箱体的底板和/或顶板上设置有若干炉内支撑体,所述炉内支撑体一端与所述炉盘管接触,另一端与超声波换能器连接,若干超声波换能器分别连接超声波发生器。
15.作为本发明的一种实施方式,所述炉箱体的内部底面设置有炉盘管支撑架,所述炉盘管置于所述炉盘管支撑架上,所述炉盘管支撑架包括两根平行设置的主支撑管,所述主支撑管沿着所述炉盘管延伸的方向设置,其第一端与炉箱体的侧板连接,第二端与炉箱体的底板连接。
16.作为本发明的一种实施方式,所述主支撑管的第二端垂直固定设置有挡管,所述挡管与主支撑管的第二端之间设置有斜支撑管。
17.作为本发明的一种实施方式,所述炉箱体的侧板、顶板及底板均包括最外侧的钢板、固定设置在钢板内侧的钢结构的支撑框架以及保温隔热层,所述底板的内侧沿所述主支撑管设置有多个炉内支撑体,所述主支撑管通过所述炉内支撑体支撑。
18.作为本发明的一种实施方式,所述炉箱体的两侧壁开设有多个加热带连接孔,所述加热带连接孔用于设置电热带的引出棒,所述引出棒与加热带连接孔之间设置有胶木座。
19.作为本发明的一种实施方式,所述炉箱体底部设置有多个箱体支撑脚,所述裂解
炉装置所在的地面基础用混凝土浇筑,其中每个箱体支撑脚的底板的上表面与混凝土基础的上表面平齐,所述箱体支撑脚的底板底部固定设置有至少两个预埋件,所述预埋件埋设在所述混凝土基础内。
20.采用上述技术方案所产生的有益效果在于:本发明提供的裂解炉,适用于烃类高温碰撞裂化反应,例如苯蒸气裂化生成联苯。通过在装置中增设分离器和储存罐,进一步利用固体催化剂颗粒加入到裂解炉的炉盘管中进行循环,一方面可以利用催化剂的催化作用降低反应所需要的温度,提高反应的效率,降温可以进一步降低反应炭化的情形,减少结焦和积炭,另一方面,固体催化剂颗粒在随着气流循环的过程中对盘管内壁进行碰撞摩擦,使附着在管壁上的焦炭颗粒脱离,随物料流出,进一步减少了管壁的结焦和积炭,通过上述方式实现在线除焦脱焦,保证炉管内各个位置的温度均匀可控。由于在线脱焦的实现,因此可以使裂解炉能够延长运行的时间,减少停车除焦的频次,可降低生产成本。
附图说明
21.图1是裂解炉装置实施例一的示意图。
22.图2是裂解炉装置实施例二的示意图。
23.图3是裂解炉装置实施例三的示意图。
24.图4是本发明裂解炉的内部结构示意图。
25.图5是图4中a部的局部放大图。
26.图6是炉箱体侧视半剖结构示意图。
27.图7是炉箱体的炉门结构示意图。
28.图8是裂解炉整体侧视半剖结构示意图。
29.图9是裂解炉内部俯视结构示意图。
30.图10是炉门的锁紧机构结构示意图。
31.图11是炉箱体轴图。
32.图12是炉箱体侧板的支撑框架结构示意图。
33.图13是裂解炉基础预埋件结构示意图。
34.图14是裂解炉侧视结构示意图。
35.图15是裂解炉俯视结构示意图。
36.其中:1炉箱体、2炉盘管、2-1进料管、2-2出料管、2-3盘管主体、3炉门、4炉盘管支撑架、5主支撑管、6挡管、7斜支撑管、8炉内支撑体、9固定扣板、10箱体支撑脚、11电热带、12连接臂、13转轴、14连接耳板、15超声波换能器、16竖向支撑杆、17横向支撑杆、18压板、19手轮、20锁紧螺杆、21保温隔热层、22分离器、23储存罐、24泵、25第一阀门、26第二阀门、27烧焦器、28换热器、29吊耳、30支撑框、31连接件、32固定螺栓、33加热带连接孔、34测温孔、35预埋件、100混凝土基础。
具体实施方式
37.为使本发明的目的、技术方案和优点更加清楚,下面结合具体实施例对发明进行清楚、完整的描述。
38.如图1所示的一种烃的蒸气裂解炉装置,本实施例以苯裂解生产联苯为例进行详细说明。在不同的工艺条件下,本装置也可适用于其他烃类物质的裂解反应。
39.所述裂解炉装置包括矩形的炉箱体1、炉盘管2、分离器22和储存罐23,所述炉箱体1(炉箱体1的详细结构参见图4至图7)的一侧开口并设置有可打开的炉门3,所述炉盘管2的盘管主体2-3为横向设置的螺旋盘管结构,炉箱体1的内侧壁设置有用于给炉盘管2加热的电热带11;电热带11用于给炉盘管2进行辐射加热。所述炉箱体1的辐射加热段分为3段,其第一段至第三段的温度依次升高,例如第一段为720-750
°
c,第二段为750-780
°
c,第三段为780-800
°
c。炉盘管2内的压力优选0.25mpa。
40.所述炉盘管2的出料管2-2连接分离器22,分离器22可采用旋风分离器,所述分离器22底部设置有储存罐23,储存罐23和分离器22之间可设置止逆阀(图未示出)。所述储存罐23通过管道与炉盘管2的进料管2-1连接,所述分离器22用于分离添加到炉盘管2内的催化剂颗粒和炉盘管2内产生的焦炭颗粒,固体颗粒(包括催化剂颗粒和焦炭颗粒)在分离器22内沉降从分离器底部流出,气体物料从分离器22顶部流出。固体颗粒进一步流入到所述储存罐23内。
41.所述储存罐23上还设置有物料添加口和排料口,所述储存罐23内添加有固体催化剂颗粒,固体催化剂颗粒在裂解炉装置中循环。所述固体催化剂颗粒例优选tho2,tho2中具有较高的耐火性能,莫氏硬度6.5,优选将tho2制成100μm左右的球状固体颗粒,例如80-120μm。利用固体催化剂颗粒对炉盘管2的内壁的摩擦碰撞作用,使其炉盘管2的内壁上形成的结焦会被固体催化剂颗粒的摩擦和碰撞作用使焦炭与管壁脱离,因此大大缓解了炉盘管2的内壁结焦的问题。由于炉盘管2中随着苯蒸气同时添加有一定量的tho2颗粒作为催化剂,tho2颗粒的浓度为反应体系重量的1%-5%,在催化剂的作用下,反应温度可适当的降低,例如第一段为670-700
°
c,第二段为700-730
°
c,第三段为730-750
°
c。或者,炉箱体1内部的辐射加热段分为4段,4段的温度可采用:第一段为650-670
°
c,第二段为670-700
°
c,第三段为700-730
°
c,第四段为730-750
°
c。
42.其中,催化剂固体颗粒随着物料的流向在炉盘管2内部循环,分离器22可将出料管2-2中随物料流出的催化剂固体颗粒与气态的物料进行分离,催化剂固体颗粒在分离器22中下降落入到储存罐23中。所述储存罐23与所述进料管2-1之间的管道上设置有用于加压的泵24,在储存罐23中或其下游的管道中可通入高温蒸气,再通过泵24加压将催化剂固体颗粒反复输送至进料管2-1中,高温蒸气的温度和压力均略高于进料管2-1内的温度和压力,高温蒸气可选用苯蒸气或水蒸气。
43.参见图2所示的实施例二,由于反应过程中产生的焦炭会随着反应物料和催化剂一同从出料管2-2流出,并在分离器22的作用下同催化剂一同被分离,为了避免反应生成的焦炭颗粒被循环进入炉盘管2内,在所述分离器22和储存罐23之间还设置有烧焦器27,所述烧焦器27用于将分离器22分离出来的固体颗粒中的焦炭颗粒进行烧焦处理,在高温(例如800-1000
°
c)下焦炭颗粒生成co和co2,同时对固体催化剂颗粒上附着的炭也一并进行了清理,在一定程度上使固体催化剂颗粒得到了再生。在烧焦器27和分离器22之间设置止逆阀或隔离阀,在烧焦器工作时对其内部进行补气,补充一定量的空气,并设置排气管将生成的co和co2排出。补气管和排气管图中未示出。
44.参见图3所示的实施例三,所述炉盘管2的进料管2-1和出料管2-2均连接同一换热
器28,进料管2-1中的物料与出料管2-2中的物料进行热交换。裂解炉的末段物料温度大约为750
°
c左右,物料在出料管2-2排出后需要进行冷却降温,利用出料管2-2的余热给进料端的苯蒸气进行加热或预热,可节省能量。
45.如图4至图15,为一种优选的炉箱体1的具体结构示意。炉箱体1整体呈长方体结构,卧式设置,其较小的两个侧面中,其中一个为敞口,并在该敞口处设置所述炉门3。
46.炉门3的设置结构参见图4、图7、图8和图9,在炉箱体1敞口端的左侧固定设置两个连接耳板14,两所述连接耳板14之间设置有转轴13,转轴13与连接耳板14之间设置有轴承。炉门3通过两个连接臂12与转轴13固定连接,使炉门3可以随所述转轴13转动。在炉箱体1敞口端的右侧设置有两锁紧螺杆20,所述锁紧螺杆20铰连在炉箱体1上,使锁紧螺杆20可左右摆动。所述锁紧螺杆20上套装有压板18,锁紧螺杆20上还设置有手轮19,手轮19与锁紧螺杆20之间通过螺纹配合,旋转手轮19可推动压板18压紧炉门3右侧的自由端,实现对炉门3的锁止,向另一方向旋转手轮19可松开压板18,摆动锁紧螺杆20,即可打开炉门3。通过上述结构设置炉门,使其打开和关闭操作简单,方便检修。
47.如图4所示为裂解炉的内部结构示意图,炉箱体1的内部底面设置有炉盘管支撑架4,所述炉盘管2置于所述炉盘管支撑架4上。所述炉盘管支撑架4包括两根平行设置的主支撑管5,所述主支撑管5沿着所述炉盘管2延伸的方向设置,其第一端与炉箱体1的侧板连接,第二端与炉箱体1的底板连接,主支撑管5的第二端即炉门3的一侧;如图4和图5所示,主支撑管5的第二端两侧设置有固定螺栓32,所述固定螺栓32与炉箱体1的底板固定连接,固定扣板9两端连接在所受固定螺栓32上,并通过螺母锁紧,使固定扣板9压紧所述主支撑管5的第二端,可使炉盘管支撑架4结构更加牢固稳定,避免主支撑管5翘曲变形。
48.所述主支撑管5的第二端垂直固定设置有挡管6,所述挡管6与主支撑管5的第二端之间设置有斜支撑管7,所述斜支撑管7为弧形结构,用于支撑挡管6,避免挡管6受到炉盘管2挤压倾斜变形。
49.本实施例中,炉盘管2的盘管主体2-3为横向设置的螺旋盘管结构,其形状类似弹簧,这样可使盘管主体2-3部分的炉管连续延伸,其各个位置的曲率相同且能够保持较小的曲率,与蛇形的盘管相比,没有拐点,使物料流动顺畅,避免了拐点处容易积炭的缺陷。
50.由于盘管主体2-3形似弹簧,因此在停车状态和反应过程中受到热胀冷缩的影响,其整体可以横向伸缩,减少应力对炉管的破坏,本实施例中,炉盘管2的盘管主体2-3是搁置在炉盘管支撑架4上,因此其一定程度上能够实现自由形变,而不受炉盘管支撑架4的约束。
51.炉盘管2的进料管2-1和出料管2-2均位于远离所述炉门3的一侧,进料管2-1从炉箱体1的顶板垂直进入到内部后与盘管主体2-3连接,在盘管主体2-3的末端处炉盘管2折返从盘管主体2-3形成筒体内延伸至进料管2-1处,从炉箱体1的顶板垂直伸出形成所述的出料管2-2,进料管2-1和出料管2-2位于炉箱体1的同一侧,便于连接所述换热器28。
52.由于进料管2-1和出料管2-2穿过炉箱体1的顶板,因此进料管2-1和出料管2-2与炉箱体1的顶板之间相互约束,使炉盘管2在进料管2-1(和出料管2-2)的一侧被固定。而炉盘管2的另一侧与炉箱体1和炉盘管支撑架4之间均没有连接关系,即炉盘管2的另一侧(靠近炉门3的一侧)为自由端,随着温度的变化,炉盘管2的盘管主体2-3整体伸缩时期自由端沿着炉盘管支撑架4的主支撑管5移动一定距离。两个主支撑管5平行设置,其与炉箱体1的底板之间形成“凹”字形的结构,使形似弹簧状的螺旋状的盘管主体2-3能够搁置在两个主
支撑管5上,弹簧状(圆筒状)的盘管主体2-3在两个主支撑管5的支撑下,其底部最低端不接触所述炉箱体1的底板,盘管主体2-3与主支撑管5无固定的连接关系,便于盘管主体2-3热胀冷缩自由形变。
53.本实施例中,优选的所述炉箱体的外围长度约5000mm,高度和宽度均在2500-2800mm,所述盘管主体2-3所形成的筒体的外径约1400mm,所述炉盘管2的管体外径约90mm。炉管采用hk4m合金材质。
54.如图11和图12所示,所述炉箱体1的侧板、顶板及底板均包括最外侧的钢板、固定设置在钢板内侧的钢结构的支撑框架以及保温隔热层21,所述底板的内侧沿所述主支撑管5设置有多个炉内支撑体8,所述主支撑管5通过所述炉内支撑体8支撑。所述支撑框架包括矩形的支撑框30,以及阵列设置在所述支撑框30内的竖向支撑杆16和设置在所述竖向支撑杆16之间的横向支撑杆17,在所述支撑框30的角部以及竖向支撑杆16和横向支撑杆17的连接处设置有连接件31,连接件31起到固定连接和加强固定的作用。其中竖向支撑杆16和横向支撑杆17采用角钢或槽钢,其连接点可采用焊接,焊接时通过所述连接件31起到加固的作用。所述支撑框架形成炉箱体1侧板、顶板及底板的骨架结构,在侧板、顶板及底板的内侧设置保温隔热层21,保温隔热层21的厚度约350mm,采用耐高温的保温棉材料,所述支撑框架同时具有固定所述保温隔热层21的作用。保温隔热层21用于对炉体的内部进行保温,防止热量损失,也避免裂解炉内部高温对周围环境造成重大影响。
55.如图4和图14所示,所述炉箱体1的辐射加热段分为3段或4段,每段辐射加热段都由若干电热带11进行加热。电热带11安装在保温隔热层21上。所述炉箱体1的两侧壁开设有多个加热带连接孔33,所述加热带连接孔33用于设置加热带的引出棒,使加热带连接电源,所述引出棒与加热带连接孔33之间设置有胶木座。如图15所示,所述炉箱体1的顶板上设置有若干测温孔34,用于在测温孔34内设置温度传感器,对各个辐射段的温度进行检测控制。
56.如图4和图13所示,所述炉箱体1底部设置有多个箱体支撑脚10,所述裂解炉装置所在的地面基础用混凝土浇筑,其中每个箱体支撑脚10的底板的上表面与混凝土基础100的上表面平齐,所述箱体支撑脚10的底板底部固定设置有至少两个预埋件35,所述预埋件35埋设在所述混凝土基础内,所述预埋件35呈l型或j型,其高度h为250mm。通过混凝土基础100不仅能够保持地面坚固平整用于放置裂解炉,避免由于地面的塌陷造成炉体的倾斜。同时,通过箱体支撑脚10底部的预埋件35使炉体和混凝土基础100牢固连接,避免运行过程中炉体发生位移。
57.基于前述的裂解炉炉体的结构,并且进一步改善装置在线除焦的效果,在所述炉箱体1的底板和/或顶板上设置有若干炉内支撑体8,所述炉内支撑体8一端与所述炉盘管2接触,另一端与超声波换能器15连接,若干超声波换能器15分别连接超声波发生器(图未示出)。所述炉盘管2的盘管主体2-3的相邻砸(圈)的炉管紧密接触,便于超声波的传导。
58.本实施例中,由于炉箱体1的底板上设置有若干炉内支撑体8,主支撑管5通过所述炉内支撑体8支撑,且主支撑管5用于支撑整个炉盘管2,因此超声波在固体之间进行传递,由炉内支撑体8通过主支撑管5传递给炉盘管2,使炉盘管2受到超声波的冲击发生振动,促使反应生成的焦炭颗粒脱离管壁。作为优选,在炉箱体1的顶板上设置有若干炉内支撑体8,顶部的炉内支撑体8直接与炉盘管2接触,在顶部的炉内支撑体8外部设置超声波换能器15。
59.所述超声波换能器15的频率优选30-50khz,超声波换能器15将超声波的振动通过
炉内支撑体8传递给炉盘管2,使炉盘管2在反应过程中不断受到超声波的振动,进而促进焦炭散列,是焦炭颗粒难以附着或从炉盘管2的内壁脱离。通过超声波换能器15和催化剂固体颗粒的共同作用,可大大延长裂解炉连续工作的时间,在一个较长的期限内,可减少停车除焦的频次。所述炉内支撑体8可采用实心的圆钢,其顶部设置连接块与炉盘管2紧密接触,实心结构能够一定程度上避免超声波的衰减,对超声波具有较好的传导效果。由于超声波换能器15的工作温度不能太高(不超过85
°
c),因此需要将其设置在裂解炉炉体的外部,避免高温影响其性能,外部设置的超声波换能器15通过炉内支撑体8将超声波传导给炉盘管2。
60.本发明所提出的采用超声波换能器15使炉盘管2在物料反应的过程中不断振动,避免焦炭颗粒的附着和沉积,能够有效的降低炉盘管2内壁结焦的形成,并且由于超声波换能器15是设置在炉盘管的外部,因此在结构上更容易实施,并且不影响炉盘管内部结构,具有更大的可操作性和发挥的空间,并且在运行过程中可以适时选择超声波换能器15的启停和调整其功率。
61.作为一种改进的实施方式,可参考图1至图4所示的结构示意,在炉盘管2的中间为,例如在第一辐射加热段和第二辐射加热段之间,和/或,第二辐射加热段和第三辐射加热段之间,和/或,第三辐射加热段和第四辐射加热段之间,在上述位置处开口连接补压管(图未示出),通过补压管通入经过预热的苯蒸气或水蒸气,补压管的压力和温度略高于其与炉盘管2连接处内物料的压力和温度。在补压管处可设置温度传感器实时监测该处炉盘管内的温度。通过补压管的补压能够克服物料在炉盘管2内的压力的衰减,导致流速减缓、反应时间过长的问题。在相邻的两个辐射段之间,可设置矮板形成隔档,减少相邻的辐射段之间互相干扰,确保温度可控。
再多了解一些
本文用于创业者技术爱好者查询,仅供学习研究,如用于商业用途,请联系技术所有人。