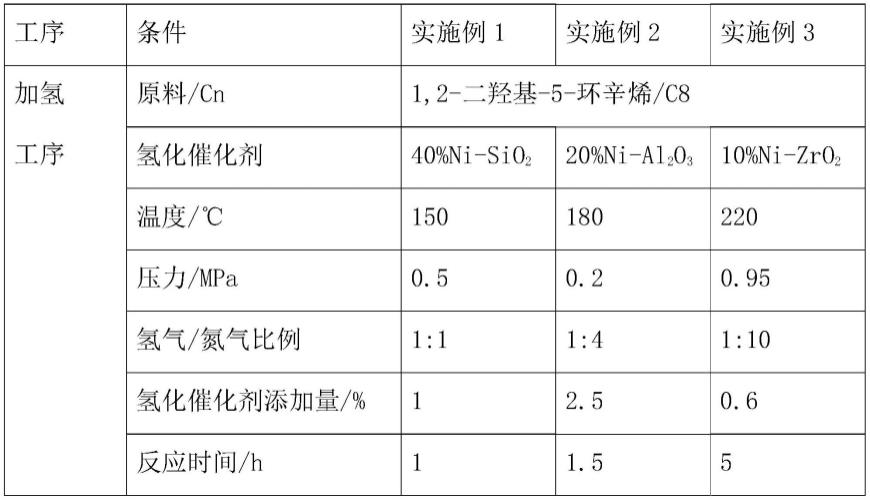
1.本发明创造属于精细化工合成领域,尤其是涉及一种长碳链二元羧酸的制备方法。
背景技术:
2.长碳链二元羧酸是碳链中含有8个以上碳原子的直链二元羧酸,是一类重要的精细化工产品。其中,十二碳二酸是市场用量最大的长碳链二元酸,以十二碳二酸为中间体可以根据不同的胺合成不同的长碳链特种尼龙,如尼龙612、尼龙1012、尼龙1212和尼龙12t等。长碳链尼龙,相对于通用的尼龙6、尼龙66特异性显著,其酰胺基浓度小、碳链长,因而其除具有普通尼龙的大多数通用性外还具有优异的耐磨性、低吸湿率、卓越的耐水解性、低温下保持出色的抗冲击强度、尺寸稳定性、耐候性、耐化学性能、优秀的阻隔性能、抗应力开裂、耐疲劳良好的nvh性能等。因此广泛应用于汽车制造、海底电缆、工业毛刷等多个领域。此外,以十二碳二酸为中间体还可以制备多种高级香料,如环十五酮内酯、麝香酮、5-环十六烯酮、环十五酮、12-甲基-14-羰基双环[9,3,1]十五烷等。
[0003]
十二碳二酸的合成工艺包括以下几种:
[0004]
一、正构烷烃生物发酵法
[0005]
生物发酵法主要是以c11~c18正构烷烃为原料,经过假丝酵母发酵,将单烷烃转化成多种长链二元酸混合物,包括癸二酸、十一碳二酸、十二碳二酸、十三碳二酸、十四碳二酸、十六碳二酸和十八碳二酸等。然后经溶解、脱色、酸化、结晶、过滤、干燥等多个步骤,获得多种长链二元酸结晶产品。生物发酵法反应条件相对温和,但生产的十二碳二酸的单酸纯度仅为97~98.5%、色泽较差、晶体粒度不均匀、残留菌体蛋白难以除净,产品质量低于化学合成法(单酸纯度99.0%以上),同时发酵法需要副产大量硫酸钠,整体设备投资大、废水量较大、生产成本较高、环境问题突出。
[0006]
二、环己酮氧化开环-二聚工艺
[0007]
us2601223公开了由环己酮经双氧水氧化开环-二聚制备十二碳二酸的方法,具体地为以甲醇作为溶剂,fe
2
盐作为催化剂,双氧水氧化环己酮使其开环聚合然后酯化得到十二碳二甲酯,再经naoh皂化-酸化得到十二碳二酸。us3917687和us3907883去除了甲醇溶剂,以fe
2
盐作为催化剂催化此反应,也能得到十二碳二酸产品。cn104610040a公开了不添加fe
2
盐催化剂、在光辐照下进行双氧水与环己酮的开环聚合反应。根据目前公开的专利报道来看,通过上述此类工艺获取的十二碳二酸收率均较低,仅为40-60%,同时催化剂fe
2
盐和双氧水的使用量较大,分别为环己酮摩尔质量的30-50倍和8-10倍,一方面铁含量难以通过后期提纯完全去除干净,严重影响后续聚合反应的分子量调控和聚合物产品性能,另一方面过量的双氧水后处理极易导致高温下易分解,存在较大的安全隐患。因此,此种工艺对于工业化生产是不具有技术优势和成本优势的。
[0008]
三、大环醇酮氧化开环反应工艺
[0009]
cn101970392a公开了以30-70%环十二酮含量的环十二酮/醇混合物为原料,在
铜、钒催化剂作用下经过量硝酸氧化获得十二碳二酸,收率为88%。cn108017533a报道了采用了反应结晶方式通过控制产物十二碳二酸的粒径分布来进行环十二酮与过量硝酸的氧化反应制备十二碳二酸。反应采用65-90wt%的浓硝酸作为氧化剂,且其硝酸/原料摩尔比高达(10-15):1。此类工艺采用的与己二酸类似的工艺流程,但由于分子结构的差异,导致其硝酸需要极大过量,其硝酸/原料摩尔比远高于己二酸工艺,
①
如此大量的硝酸会分解产生大量的氮氧化物no
x
,对环境污染严重,不符合国家的“双碳”政策;
②
导致反应总体积增大、硝酸浓缩回环套用的能耗大大增加;
③
硝酸氧化反应放热量巨大,反应及时移除反应热需要大量的冷却水和安全联锁装置,存在巨大的安全风险隐患;
④
硝酸氧化环十二酮/醇反应机理十分复杂,主副反应是串联反应,反应过程中会生成一定量的硝化二元酸副产物,通过降温结晶无法完全去除,严重影响产品的纯度和品质,间接对以十二碳二酸为单体的聚合物的性能造成不良影响。因此,此工艺仍存在极大的技术缺陷。
[0010]
四、大环烯烃氧化开环工艺
[0011]
ep0438143b1公开了通过ruo
4-ce(so3ch3)
4-甲基磺酸为催化体系实现环十二烯的非均相氧化开环制备十二碳二酸。亲油的ruo4在有机相中将环十二烯氧化成十二碳二酸;还原态的钌在有机相中的溶解度有限,容易形成沉淀物被萃取或溶解到水相中被ce
4
离子氧化成ruo4,ruo4再次溶解在有机相中,与额外的环十二烯反应,形成催化循环。水相中的ce
3
离子再经电解氧化以将ce
3
离子转化为ce
4
离子。通过油水两相能尽量降低ru的损耗,环十二烯转化率95%,十二碳二酸的选择性为87~88%。从公开的信息看,该工艺需要较高含量的ce
4
离子,其摩尔添加量为环十二烯的4~12倍,以保证对ru的充分氧化;而ce的催化循环需要借助电解氧化,进一步增加了设备投资。此外,该专利没有公开该催化体系在多次循环套用后的催化结果。而这对于降低贵金属催化剂成本是十分关键的。
[0012]
us3461160a报道了以oso4和v2o5催化环十二烯与硝酸的氧化反应制备十二碳二酸。反应需要在os与环十二烯原料质量比为1.5-4.0时才能获得70%左右的收率,催化剂用量巨大,且os元素属于贵金属元素,催化剂费用极高,且该专利未提及催化体系循环套用的问题,这对于工业化生产的成本控制至关重要。另外,该工艺涉及到使用硝酸为氧化剂,势必在反应过程中会产生大量no
x
氮氧化物,环保压力巨大。
[0013]
具有高碳数的长碳链二元羧酸如十二碳二酸相对于低碳二元羧酸如己二酸,其合成工艺方面具有以下几个技术难点:
①
反应的复杂性:环己醇硝酸氧化制己二酸,其反应机理是经历一个6-肟基-6-硝基己酸中间体过程,该中间体直接转化为副产物戊二酸和丁二酸,主副反应属于平行反应,催化剂的加入和温度的控制利于提高主反应比例。而以十二碳二酸的大环前驱体进行氧化开环时,以硝酸作为氧化剂为例,需要经历二酸分子羧基α-硝基或亚硝基二酸中间体,然后该中间体通过脱羧进一步氧化成较短碳链的二元酸,如此串联进行脱羧反应,因此其副产物会包括c11、c10、c9、c8、c7、c6及以下的二元羧酸。如何避免此类串联副反应的发生,使氧化反应仅停留在c12或少量到c11,阻止其进一步脱羧氧化生成更低碳数的二元酸,开发新的反应工艺是技术难点。
②
反应的分离难度:相对于己二酸合成中只存在戊二酸和丁二酸两种副产物,主副产物在水中的溶解度曲线差异明显,通过降温结晶即可实现高纯度己二酸的提纯;高碳数的十二碳二酸在合成中会存在c11、c10、c9、c8、c7、c6及以下的二元羧酸。这些二元酸特别是长碳链二元酸,其结构非常相似,在溶剂中的溶解度差距不大,对于结晶分离难度很大。因此需要开发出一种非硝酸法的绿色氧化工
环十二二烯。
[0024]
优选地,本发明所述的氢化工序的双羟基大环烯烃原料是以大环烯烃通过环氧化反应制备环氧大环烯烃时以副产物方式经分离后获得,一方面可以利用此部分副产物通过氢化-氧化的串联工序合成长碳链二元羧酸,充分开发此部分副产物的经济价值,降低生产成本,使其经济效益最大化;另一方面避免了以环氧大环烯烃直接氧化开环制备十二碳二酸收率低的问题(us3657335)。
[0025]
进一步地,所述氢化工序中,氢化催化剂为主金属为镍系、铂族金属中的一种,优选镍系金属;氢化催化剂载体为氧化铝、活性炭、二氧化硅、二氧化钛、二氧化锆、分子筛、水滑石、硅藻土中的一种,优选载体为二氧化硅或二氧化锆中的一种;特别优选二氧化硅。
[0026]
进一步地,所述氢化工序中,氢化催化剂用量为双羟基大环烯烃原料质量的0.01-5%,优选用量为0.1-3%,特别优选用量为0.5-2%。
[0027]
进一步地,所述氢化工序的反应温度为50-250℃,优选反应温度为100-230℃,特别优选反应温度为150-220℃;所述氢化工序的反应压力为0.1-5mpa,优选反应压力为0.1-2mpa,特别优选反应压力为0.1-1mpa。所述氢化工序的反应时间为0.1-5h,优选反应时间为0.5-3h,特别优选反应时间为1-2h。
[0028]
进一步地,所述氢化工序得到的产物包括含有8-12个碳原子且邻位为羟基的大环烷酮、含有8-12个碳原子且邻位为羰基的大环烷酮、少量含有8-12个碳原子且双羟基处于邻位的大环烷烃以及极少量高沸点产物。
[0029]
进一步地,所述的含有8-12个碳原子且邻位为羟基的大环烷酮选自1-羟基环辛酮、1-羟基环癸酮、1-羟基环十二酮中的一种或多种,优选1-羟基环辛酮和1-羟基环十二酮的一种或多种,特别优选为1-羟基环十二酮。所述的含有8-12个碳原子且邻位为羰基的大环烷酮选自1-羰基环辛酮、1-羰基环癸酮、1-羰基环十二酮中的一种或多种,优选1-羰基环辛酮和1-羰基环十二酮的一种或多种,特别优选为1-羰基环十二酮。所述的含有8-12个碳原子且双羟基处于邻位的大环烷烃选自1,2-二羟基环辛烷、1,2-二羟基环癸烷、1,2-二羟基环十二烷中的一种或多种,优选1,2-二羟基环辛烷和1,2-二羟基环十二烷的一种或多种,特别优选为1,2-二羟基环十二烷。
[0030]
本发明通过研究发现,氢化工序得到的产物中,含有不饱和羰基的产物如邻位为羟基的大环烷酮和邻位为羰基的大环烷酮对后续氧化反应制备长碳链二元羧酸会带来出乎意料的效果:含有不饱和羰基的产物比双羟基处于邻位的大环烷烃对于提高产物的选择性、降低串联副反应的发生是十分有利的。因此本发明采用的氢化工序是通过催化剂和反应工艺的控制,使得原料双羟基大环烯烃的氢化产物以含有不饱和羰基的大环烷酮或大环烷醇为主,降低饱和的双羟基大环烷烃产物比例,对后续的氧化反应是明显有利的。
[0031]
进一步地,本发明所述氢化工序是含氢气体氛围下进行,该含氢气体可为纯氢气氛围或含有一定体积氮气的氢气氛围,其中氢气与氮气的比例为1:(0.1-10),优选比例为1:(1-8),特别优选比例为1:(3-5)。
[0032]
催化剂在纯氢氛围下具有更高的催化活性,氢气流量过高,一方面会导致双羟基大环烯烃原料在催化剂床层停留时间过短,不能充分转化,另一方面会使催化剂吸附和解离氢的能力过强,导致加氢反应速率过快,饱和加氢的双羟基大环烷烃副反应速度加快,反应选择性下降,不利于后续氧化工序的进行。氢气流量过低,催化剂的活性较低,对反应转
化率和选择性均有不良影响。因此,在本发明优选的实施例中,通过调节氮气与氢气的比例来控制催化剂的氢化活性,避免较高活性的催化剂引起的氢解副反应,进而能有效抑制原料在氢化生成含不饱和羰基的大环烷酮或大环烷醇后,进一步过度氢化得到饱和的双羟基大环烷烃副产物的发生。
[0033]
进一步地,所述的氢化工序可以在存在或不存在外加溶剂的情况下进行,优选不加入外部溶剂。当加入外加溶剂存在下进行时,则优选在所述氢化反应条件下为惰性的溶剂。
[0034]
进一步地,所述氢化工序的反应器为环流反应器、固定床反应器、反应釜、流化床反应器中的一种,优选环流反应器或固定床反应器,特别优选环流反应器。
[0035]
进一步地,对氢化工序所得的粗产品施以提纯措施,包括精馏法、色谱法、结晶法或综合措施。用于提纯的精馏装置包括任选配备的精馏塔、泡罩塔、板式塔或蒸发器,如薄膜蒸发器、降膜蒸发器、强制循环蒸发器、刮膜蒸发器及其组合。
[0036]
进一步地,本发明所述的氧化工序中氧化剂为过氧化氢溶液,浓度为10-75wt%,优选浓度为30-70wt%,特别优选浓度为50-60%。氢化产物与过氧化氢的摩尔比为1:(1-10),优选摩尔比为1:(1-5),特别优选摩尔比为1:(2-3)。
[0037]
进一步地,所述的氧化工序中氧化助剂为25℃下电离常数为1
×
10-6
≤pka≤5
×
10-3
的有机酸,所述有机酸选自甲酸、乙酸、丙酸、正丁酸、正戊酸、异戊酸、特戊酸、氯乙酸、二氯乙酸、邻苯二甲酸、间氯苯甲酸的一种或多种。所述氧化助剂添加量与氢化产物的摩尔比为(1-20):1,优选摩尔比为(2-10):1,特别优选摩尔比为(3-5):1。
[0038]
进一步地,所述的氧化工序中催化剂为无机酸、固体超强酸、强酸性树脂等,所述催化剂选自硫酸、磷酸、甲基磺酸、苯磺酸、对甲苯磺酸、so
42-/m
x
oy型固体超强酸、keggin结构(h
8-n
x
nm12o40
)杂多酸、大孔强酸性苯乙烯系阳离子交换树脂、全氟磺酸树脂中的一种或多种,优选为硫酸、对甲苯磺酸、磷钨酸、大孔强酸性苯乙烯系阳离子交换树脂。所述氧化催化剂添加量为氢化产物的0.1-10wt%,优选添加量为0.5-6%,特别优选添加量为1-3%。
[0039]
进一步地,所述氧化工序的反应温度为50-120℃,优选反应温度为60-100℃,特别优选反应温度为60-80℃;所述氧化工序的反应时间为0.5-5h,优选反应时间为1-3h。
[0040]
进一步地,所述氧化工序的反应器为环流反应器、反应釜、微通道反应器中的一种,优选环流反应器或微通道反应器,最优选环流反应器。
[0041]
进一步地,对氧化工序所得的粗产品施以提纯措施,包括精馏法、色谱法、结晶法或综合措施。
[0042]
在本发明的其中一些实施例中,在氧化工序反应进行过程中,产物如十二碳二酸因其在含水反应体系中的溶解度有限,能够及时以固体形式从反应体系中析出,可有效降低进一步在反应体系脱羧的串联副反应的发生。另外,本发明的氧化反应体系较硝酸氧化体系放热量更小、反应更温和、温度控制更易实现,因此其反应的选择性比硝酸氧化工艺要高。
[0043]
在本发明的其中一些实施例中,在氧化工序使用的有机酸助剂经历与双氧水的氧化反应生成过氧有机酸中间体,然后与氧化工序原料进行反应,最后又生成了有机酸助剂,如此可循环套用,且回收工艺简单,仅需要简单精馏即可。在长碳链二元羧酸生产过程中仅需经过一段时间补充少量有机酸即可,进一步降低了生产成本和设备投资。
[0044]
通过本发明制备的长碳链二元羧酸可用于生产长碳链特种尼龙,如尼龙612、尼龙1012、尼龙1212;高级合成香料,如环十五酮内酯、麝香酮、5-环十六烯酮、环十五酮、12-甲基-14-羰基双环[9,3,1]十五烷等;高端航空润滑油、工业削切液等,应用于汽车制造、海底电缆、工业毛刷、航空制造等多个领域。
[0045]
相对于现有技术,本发明创造所述的长碳链二元羧酸的制备方法具有以下优势:
[0046]
(1)本发明创造所述的长碳链二元羧酸的制备方法采用串联加氢-氧化工序实现长碳链二元羧酸的制备,工艺绿色环保、反应工艺条件温和、反应风险安全可控,避免了硝酸氧化工艺大量氮氧化物no
x
的产生,符合“双碳”政策下化工发展的大趋势;
[0047]
(2)本发明创造所述的长碳链二元羧酸的制备方法在加氢工序中通过调节氢气/氮气比例来调控催化剂的氢化活性,制备含有不饱和羰基的大环烷酮或大环烷醇为主的加氢产物,进而在氧化工序中有利于提高长碳链二元酸的选择性。另外,氧化工序使用的反应工艺相对温和、反应放热较小、温控相对容易,产物在含水体系中及时析出,降低了其进一步脱羧生成较低碳数二元酸的可能性,多重调控手段促使氧化反应具有较高的反应选择性和收率,十二碳二酸的收率可达到90~93%,其副产物主要以十一碳二酸和癸二酸为主,更低碳数的二元羧酸含量极低。这样反应的分离难度大大降低,通过在适当溶剂中进行降温结晶即可获得纯度在99.0%以上的十二碳二酸产品。此外,本发明的制备方法中不涉及fe
2
离子或含氮物料等,因此其产品中也不会含有fe
2
或含氮杂质,这对长碳链二元羧酸的高品质要求是具有明显优势的;
[0048]
(3)本发明创造所述的长碳链二元羧酸的制备方法使用的原料双羟基大环烯烃,其来源优选以大环烯烃通过环氧化反应制备环氧大环烯烃时以副产物方式经分离后获得。利用现有副产物作为原料转化成有较高经济价值的长碳链二元羧酸,提高了原子经济性,实现了变废为宝,降低了生产成本,使其经济效益最大化,并增强了整个长碳链产品产业链的竞争力;本发明氢化工序中使用的氢化催化剂可实现长周期连续化运转,催化剂制造成本和使用成本较低,也降低了长碳链二元羧酸的生产成本;本发明氧化工序中使用的氧化助剂,可循环套用,且回收工艺简单。在长碳链二元羧酸生产过程中仅需经过一段时间少量补充有机酸即可,进一步降低了生产成本和设备投资;
[0049]
(4)本发明创造所述的长碳链二元羧酸的制备方法可以实现连续化反应,反应所需能耗优势明显,生产效率高,适用于工业化生产,且本发明所述的方法适用于具有8-12个碳原子的长碳链二元羧酸的制备,具有较强的适用性。
具体实施方式
[0050]
需要说明的是,在不冲突的情况下,本发明创造中的实施例及实施例中的特征可以相互组合。
[0051]
下面将结合实施例来详细说明本发明创造。
[0052]
在以下实施例中,氢化工序主副产物采用气相色谱进行反应体系中各组分的分析,通过校正归一法进行定量,在此基础上计算反应物的转化率、产物的选择性和收率。氧化工序二元羧酸的主副产物进行酯化衍生化处理后再进行气相色谱分析,通过校正归一法进行定量主产物和副产物的含量。
[0053]
酯化衍生化方法如下:
[0054]
称取约1.0g固体样品置于烧瓶中,分别加入无水甲醇10g、环己烷10g、浓硫酸2-3滴,并分别于60-65℃加热进行酯化反应,同时用分水器及时除去水。反应1h后冷却至室温进行气相色谱gc检测。
[0055]
气相色谱分析条件如下:
[0056]
色谱柱:安捷伦db-wax(规格为30m
×
0.32mm
×
0.25mm);进样口温度:300℃;分流比:30:1;柱流量:1.5ml/min;柱温:100℃0.5min;升温程序:15℃/min升高到300℃,保持8min;检测器温度:300℃,氢气流量:35ml/min,空气流量:350ml/min。
[0057]
实施例1
[0058]
氢化工序:将原料1,2-二羟基-5-环辛烯(由1,2-环氧-5-环辛烯经水合反应后分离后获得)100g加入500ml高压反应釜中,加入40%ni-sio2氢化催化剂1.0g,并用氮气吹扫反应釜内空气。然后向反应釜内通入氢气和氮气的混合气,所述混合气中的氢气与氮气比例为1:1。反应温度为150℃,反应压力为0.5mpa,反应时间为1h。反应结束后,过滤或离心去除氢化催化剂,反应釜内物料直接用于氧化工序。经气相色谱分析,氢化反应的原料转化率为100%,氢化反应液体系中产物比例分布:1-羟基环辛酮占比80.3%、1-羰基环辛酮占比17.6%,1,2-二羟基环辛烷占比1.9%,其它占比0.2%。
[0059]
氧化工序:将已分离氢化催化剂的氢化工序反应液置于1l反应釜中,加入100g甲酸和1g磷酸。在80℃下缓慢滴加30%双氧水240g,滴加时间为0.5h,然后继续搅拌反应1h。反应过程中产物辛二酸逐渐析出。反应结束后,将反应液降温冷却至室温,过滤出结晶固体,通过酯化衍生化确定反应的转化率和辛二酸收率。经气相色谱分析,氧化反应的原料转化率为99.8%,固体产物比例分布:辛二酸占比92.5%、庚二酸占比6.9%,1己二酸占比0.5%,其它占比0.1%。辛二酸的实际收率为91.1%。
[0060]
实施例2
[0061]
氢化工序:将原料1,2-二羟基-5-环辛烯(由1,2-环氧-5-环辛烯经水合反应后分离后获得)100g加入500ml高压反应釜中,加入20%ni-al2o3氢化催化剂2.5g,并用氮气吹扫反应釜内空气。然后向反应釜内通入氢气和氮气的混合气,所述混合气中的氢气与氮气比例为1:4。反应温度为180℃,反应压力为0.2mpa,反应时间为1.5h。反应结束后,过滤或离心去除氢化催化剂,反应釜内物料直接用于氧化工序。经气相色谱分析,氢化反应的原料转化率为99.8%,氢化反应液体系中产物比例分布:1-羟基环辛酮占比82.5%、1-羰基环辛酮占比16.6%,1,2-二羟基环辛烷占比0.5%,其它占比0.4%。
[0062]
氧化工序:将已分离氢化催化剂的氢化工序反应液置于1l反应釜中,加入210g乙酸和0.5g浓硫酸。在95℃下缓慢滴加50%双氧水240g,滴加时间为1h,然后继续搅拌反应2h。反应过程中产物辛二酸逐渐析出。反应结束后,将反应液降温冷却至室温,过滤出结晶固体,通过酯化衍生化确定反应的转化率和辛二酸收率。经气相色谱分析,氧化反应的原料转化率为99.9%,固体产物比例分布:辛二酸占比93.8%、庚二酸占比5.9%,1己二酸占比0.3%,其它占比<0.1%。辛二酸的实际收率为92.4%。
[0063]
实施例3
[0064]
氢化工序:将原料1,2-二羟基-5-环辛烯(由1,2-环氧-5-环辛烯经水合反应后分离后获得)100g加入500ml高压反应釜中,加入10%ni-zro2氢化催化剂0.6g,并用氮气吹扫反应釜内空气。然后向反应釜内通入氢气和氮气的混合气,所述混合气中的氢气与氮气比
例为1:10。反应温度为220℃,反应压力为0.95mpa,反应时间为5h。反应结束后,过滤或离心去除氢化催化剂,反应釜内物料直接用于氧化工序。经气相色谱分析,氢化反应的原料转化率为100%,氢化反应液体系中产物比例分布:1-羟基环辛酮占比85.6%、1-羰基环辛酮占比13.3%,1,2-二羟基环辛烷占比0.9%,其它占比0.2%。
[0065]
氧化工序:将已分离氢化催化剂的氢化工序反应液置于2l反应釜中,加入907g二氯乙酸和2.5g对甲苯磺酸。在110℃下缓慢滴加60%双氧水92g,滴加时间为0.5h,然后继续搅拌反应0.5h。反应过程中产物辛二酸逐渐析出。反应结束后,将反应液降温冷却至室温,过滤出结晶固体,通过酯化衍生化确定反应的转化率和辛二酸收率。经气相色谱分析,氧化反应的原料转化率为100%,固体产物比例分布:辛二酸占比93.1%、庚二酸占比6.2%,己二酸占比0.9%,其它占比<0.1%。辛二酸的实际收率为91.9%。
[0066]
表1以1,2-二羟基-5-环辛烯为原料通过串联氢化-氧化工序制备辛二酸
[0067]
[0068][0069]
实施例4
[0070]
氢化工序:将原料1,2-二羟基-3-环辛烯(由1,2-环氧-3-环辛烯经水合反应后分离后获得)100g加入500ml高压反应釜中,加入25%ni-分子筛氢化催化剂3.0g,并用氮气吹扫反应釜内空气。然后向反应釜内通入氢气和氮气的混合气,所述混合气中的氢气与氮气比例为1:6。反应温度为195℃,反应压力为0.3mpa,反应时间为2.5h。反应结束后,过滤或离心去除氢化催化剂,反应釜内物料直接用于氧化工序。经气相色谱分析,氢化反应的原料转化率为100%,氢化反应液体系中产物比例分布:1-羟基环辛酮占比96.8%、1-羰基环辛酮
占比0.6%,1,2-二羟基环辛烷占比2.3%,其它占比0.3%。
[0071]
氧化工序:将已分离氢化催化剂的氢化工序反应液置于1l反应釜中,加入416g丙酸和3g杂多酸。在65℃下缓慢滴加27.5%双氧水348g,滴加时间为1.5h,然后继续搅拌反应0.5h。反应过程中产物辛二酸逐渐析出。反应结束后,将反应液降温冷却至室温,过滤出结晶固体,通过酯化衍生化确定反应的转化率和辛二酸收率。经气相色谱分析,氧化反应的原料转化率为99.6%,固体产物比例分布:辛二酸占比90.8%、庚二酸占比8.1%,1己二酸占比0.9%,其它占比小于0.1%。辛二酸的实际收率为88.3%。
[0072]
实施例5
[0073]
氢化工序:将原料1,2-二羟基-5,9-环十二二烯(由1,2-环氧-5,9-环十二二烯经水合反应后分离后获得)200g加入1l高压反应釜中,加入30%ni-sio2氢化催化剂3.0g,并用氮气吹扫反应釜内空气。然后向反应釜内通入氢气和氮气的混合气,所述混合气中的氢气与氮气比例为1:3。反应温度为160℃,反应压力为0.6mpa,反应时间为2h。反应结束后,过滤或离心去除氢化催化剂,反应釜内物料直接用于氧化工序。经气相色谱分析,氢化反应的原料转化率为99.9%,氢化反应液体系中产物比例分布:1-羟基环十二酮占比86.7%、1-羰基环十二酮占比12.5%,1,2-二羟基环十二烷占比0.7%,其它占比小于0.1%。
[0074]
氧化工序:将已分离氢化催化剂的氢化工序反应液置于1l反应釜中,加入244g乙酸和3g甲磺酸。在85℃下缓慢滴加50%双氧水207.8g,滴加时间为1h,然后继续搅拌反应0.5h。反应过程中产物十二碳二酸逐渐析出。反应结束后,将反应液降温冷却至室温,过滤出结晶固体,通过酯化衍生化确定反应的转化率和十二碳二酸收率。经气相色谱分析,氧化反应的原料转化率为1006%,固体产物比例分布:十二碳二酸占比94.3%、十一碳二酸占比5.1%,癸二酸占比0.5%,其它占比小于0.1%。十二碳二酸的实际收率为93.1%。
[0075]
实施例6
[0076]
氢化工序:将原料1,2-二羟基-5,9-环十二二烯(由1,2-环氧-5,9-环十二二烯经水合反应后分离后获得)200g加入1l高压反应釜中,加入60%ni-al2o3氢化催化剂3.0g,并用氮气吹扫反应釜内空气。然后向反应釜内通入氢气和氮气的混合气,所述混合气中的氢气与氮气比例为1:2。反应温度为200℃,反应压力为0.8mpa,反应时间为1.5h。反应结束后,过滤或离心去除氢化催化剂,反应釜内物料直接用于氧化工序。经气相色谱分析,氢化反应的原料转化率为100%,氢化反应液体系中产物比例分布:1-羟基环十二酮占比84.9%、1-羰基环十二酮占比14.1%,1,2-二羟基环十二烷占比0.8%,其它占比0.2%。
[0077]
氧化工序:将已分离氢化催化剂的氢化工序反应液置于1l反应釜中,加入539g丁酸和10g苯磺酸。在100℃下缓慢滴加55%双氧水126g,滴加时间为1h,然后继续搅拌反应1h。反应过程中产物十二碳二酸逐渐析出。反应结束后,将反应液降温冷却至室温,过滤出结晶固体,通过酯化衍生化确定反应的转化率和十二碳二酸收率。经气相色谱分析,氧化反应的原料转化率为99.9%,固体产物比例分布:十二碳二酸占比93.5%、十一碳二酸占比5.7%,癸二酸占比0.7%,其它占比小于0.1%。十二碳二酸的实际收率为91.9%。
[0078]
实施例7
[0079]
氢化工序:将原料1,2-二羟基-5,9-环十二二烯(由1,2-环氧-5,9-环十二二烯经水合反应后分离后获得)200g加入1l高压反应釜中,加入40%ni-sio2氢化催化剂5.0g,并用氮气吹扫反应釜内空气。然后向反应釜内通入氢气和氮气的混合气,所述混合气中的氢
气与氮气比例为1:5。反应温度为190℃,反应压力为0.1mpa,反应时间为3h。反应结束后,过滤或离心去除氢化催化剂,反应釜内物料直接用于氧化工序。经气相色谱分析,氢化反应的原料转化率为100%,氢化反应液体系中产物比例分布:1-羟基环十二酮占比87.2%、1-羰基环十二酮占比12.3%,1,2-二羟基环十二烷占比0.4%,其它占比小于0.1%。
[0080]
氧化工序:将已分离氢化催化剂的氢化工序反应液置于1l反应釜中,加入226.2g丙酸和2g大孔强酸性苯乙烯系阳离子交换树脂。在90℃下缓慢滴加70%双氧水297g,滴加时间为2h,然后继续搅拌反应1h。反应过程中产物十二碳二酸逐渐析出。反应结束后,将反应液降温冷却至室温,过滤出结晶固体,通过酯化衍生化确定反应的转化率和十二碳二酸收率。经气相色谱分析,氧化反应的原料转化率为100%,固体产物比例分布:十二碳二酸占比93.0%、十一碳二酸占比6.2%,癸二酸占比0.7%,其它占比小于0.1%。十二碳二酸的实际收率为90.8%。
[0081]
表2以1,2-二羟基-5,9-环十二二烯为原料通过串联氢化-氧化工序制备十二碳二酸
[0082]
[0083]
[0084][0085]
对比例1大环醇/酮硝酸氧化法
[0086]
在500ml圆底瓶中加入65wt%硝酸266g,加入硝酸铜和钒酸铵使cu和v的含量分别为0.5wt%和0.2wt%,体系经油浴加热到反应温度75℃,环十二醇/酮混合物以熔融状态持续加入到烧瓶中,保持搅拌状态,通过控制油浴温度维持反应温度恒定,60min后共加入50.5g环十二醇/酮混合物(硝酸/环十二醇酮的摩尔比=10:1),有晶体析出,反应停止。所得反应液降温至室温,然后过滤出固体产物,用脱盐水洗涤滤饼2~3次,所得固体在80℃真空干燥箱中干燥8~12h,最后烘干后所得固体混合物经酯化衍生化后进行色谱分析,确定反应选择性。
[0087]
反应产物比例分布如下表3所示:
[0088]
表3实施例5与对比实施例1反应结果对比
[0089][0090][0091]
通过表3可知,传统的硝酸氧化工艺因需要经历二酸分子羧基α-硝基或亚硝基二酸中间体,然后该中间体通过脱羧进一步氧化成较短碳链的二元酸,如此串联进行脱羧反应,因此其副产物会包括c11、c10、c9、c8、c7、c6及以下的二元羧酸。同时硝酸氧化法放热量巨大,反应局部温度会过高,也会促进副反应的进一步发生。因此,其副产物较多,实际收率仅有84-88%左右。而本发明采用的非硝酸的绿色氧化工艺,其氧化剂为双氧水,反应条件相对温和、反应放热较小、温控相对容易,产物在含水体系中及时析出,降低了其进一步脱羧生成较低碳数二元酸的可能性,因此其产物中的十二碳二酸选择性高于硝酸氧化工艺,
具有一定的技术优势。
[0092]
对比实施例2
[0093]
氢化工艺中用纯氢气体代替氢氮混合气体,其它与实施例5相同
[0094]
氢化工序:将原料1,2-二羟基-5,9-环十二二烯(由1,2-环氧-5,9-环十二二烯经水合反应后分离后获得)200g加入1l高压反应釜中,加入30%ni-sio2氢化催化剂3.0g,并用氮气吹扫反应釜内空气。然后向反应釜内通入纯氢气体。反应温度为160℃,反应压力为0.6mpa,反应时间为2h。反应结束后,过滤或离心去除氢化催化剂,反应釜内物料直接用于氧化工序。经气相色谱分析,氢化反应的原料转化率为99.9%,氢化反应液体系中产物比例分布:1-羟基环十二酮占比20.6%、1-羰基环十二酮占比4.7%,1,2-二羟基环十二烷占比74.6%,其它占比小于0.1%。
[0095]
氧化工序:将已分离氢化催化剂的氢化工序反应液置于1l反应釜中,加入244g乙酸和3g甲磺酸。在85℃下缓慢滴加50%双氧水207.8g,滴加时间为1h,然后继续搅拌反应0.5h。反应过程中产物十二碳二酸逐渐析出。反应结束后,将反应液降温冷却至室温,过滤出结晶固体,通过酯化衍生化确定反应的转化率和十二碳二酸收率。经气相色谱分析,氧化反应的原料转化率为100%,固体产物比例分布:十二碳二酸占比83.5%、十一碳二酸占比9.2%,癸二酸占比2.5%,其它占比4.8%。十二碳二酸的实际收率为81.2%。
[0096]
表4实施例5与对比实施例2反应结果对比
[0097]
[0098][0099]
通过表4可知,纯氢环境下氢化催化剂的催化活性较高,使催化剂吸附和解离氢的能力过强,导致加氢反应速率过快,饱和加氢产物双羟基大环烷烃占主要成分。但该组份在后续的氧化反应过程中,不利于反应选择性的提高。因此,需要在氢化工序阶段通过调节氮气与氢气的比例来控制催化剂的氢化活性,避免较高活性的催化剂引起的氢解副反应,进而能有效抑制原料在氢化生成含不饱和羰基的大环烷酮或大环烷醇后,进一步过度氢化得到饱和的双羟基大环烷烃副产物的发生,从而保证后续氧化工序高选择性,避免副反应的发生。
[0100]
实施例8
[0101]
以1,5,9-环十二碳三烯与70wt%的双氧水在钨酸钠和磷酸催化剂进行环氧化反应,反应生成1,2-环氧-5,9-环十二二烯(选择性为88~92%)和1,2-二羟基-5,9-环十二二烯(选择性为8~10%)和少量高沸点产物。经过精馏提纯后,即可获得1,2-二羟基-5,9-环十二二烯用于十二碳二酸的制备。
[0102]
氢化工序:将上述获得的1,2-二羟基-5,9-环十二二烯500g加入1l高压反应釜中,加入30%ni-sio2氢化催化剂10g,并用氮气吹扫反应釜内空气。然后向反应釜内通入氢气和氮气的混合气,所述混合气中的氢气与氮气比例为1:5。反应温度为180℃,反应压力为0.3mpa,反应时间为2h。反应结束后,过滤或离心去除氢化催化剂,反应釜内物料直接用于氧化工序。经气相色谱分析,氢化反应的原料转化率为99.9%,氢化反应液体系中产物比例分布:1-羟基环十二酮占比87.7%、1-羰基环十二酮占比11.2%,1,2-二羟基环十二烷占比0.9%,其它占比0.2%。
[0103]
氧化工序:将已分离氢化催化剂的氢化工序反应液置于3l反应釜中,加入943g丙酸和5g浓硫酸。在85℃下缓慢滴加50%双氧水520g,滴加时间为1h,然后继续搅拌反应1h。反应过程中产物十二碳二酸逐渐析出。反应结束后,将反应液降温冷却至室温,过滤出结晶固体,通过酯化衍生化确定反应的转化率和十二碳二酸收率。经气相色谱分析,氧化反应的原料转化率为100%,固体产物比例分布:十二碳二酸占比94.1%、十一碳二酸占比5.3%,癸二酸占比0.5%,其它占比小于0.1%。十二碳二酸的实际收率为92.6%。通过将所得固体在适当溶剂如甲醇或乙酸中进行简单的降温结晶,即可获得产品高品质的十二碳二酸产品,其单酸纯度为99.6%,水分含量为0.032%,总氮含量为12ppm,fe离子含量为0.1ppm,灰分18ppm。
[0104]
聚合工序:取上述精制的十二碳二酸500g溶解在4~8倍质量重量的无水乙醇中,加热至80℃,使十二碳二酸全部溶解。在搅拌情况下加入70%的己二胺-乙醇溶液进行成盐(己二胺与十二碳二酸等摩尔比例)。在成盐过程中,使温度维持在80℃左右,终点时的ph值为7.4,冷却至室温,经过滤、干燥后即可得到白色结晶的尼龙612盐750g。将上述尼龙612盐、水130g、分子调节剂2g和抗氧化剂0.6g加入聚合反应釜中,氮气置换后开始升温至200℃,釜内压力升至1.5mpa,维持反应2-3h。然后降压至大气压,同时温度升至250℃,常压放空2h。最后放气完毕后抽真空20~60min,真空度为0.5~0.6mpa。反应完毕后,将熔融态聚合物经过挤出、冷却后切粒,即可得到尼龙612树脂,其产品性能见表5。
[0105]
表5实施例8聚合制备尼龙612与市售尼龙612产品性能对比
[0106]
测试项目市售尼龙612实施例8制备尼龙612密度(g/cm3)1.071.069熔点(℃)218217.2拉伸强度(mpa)7462.3弹性模量(mpa)19002154断裂伸长率23℃(%)≥200267弯曲强度(mpa)8279.4弯曲弹性模量(mpa)29002965缺口冲击强度(j/m)7576.2热变形温度0.46mpa(℃)180183.8洛氏硬度(r)114112吸水性(23℃,水中,24h)(%)0.250.32
[0107]
由实施例8可知,当原料以大环烯烃通过环氧化反应制备环氧大环烯烃时以副产物方式经分离后获得的情况下,经过本发明阐述的串联氢化-氧化工序也能获得较好的长碳链二元羧酸的选择性和收率,并优于硝酸氧化工艺。利用现有副产物作为原料转化成有较高经济价值的长碳链二元羧酸,提高了原子经济性,实现了变废为宝,降低了生产成本,使其经济效益最大化,并增强了整个长碳链产品产业链的竞争力。此外,通过简单的结晶即可获得聚合级的长碳链二元酸产品,通过与己二胺的熔融聚合,得到的尼龙612树脂的各项产品性能参数与目前市售产品的性能参数一致。
再多了解一些
本文用于创业者技术爱好者查询,仅供学习研究,如用于商业用途,请联系技术所有人。