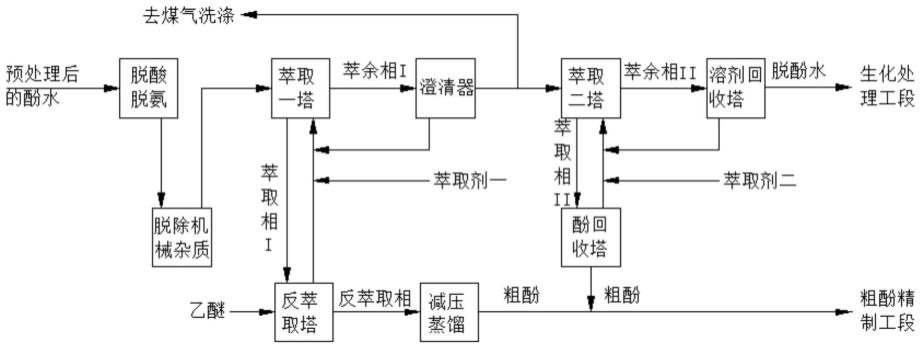
1.本发明属于含酚废水处理技术领域,尤其涉及一种含酚废水萃取脱酚的方法。
背景技术:
2.煤化工是以煤炭为原料进行不同化学产品的加工,煤化工项目耗水量巨大,废水产生量也很高,每处理完1吨煤炭大约会产生1吨含酚废水。煤化工废水中总酚含量可高达5000mg/l以上,而且成分复杂,既有单元酚,又有多元酚,环境危害大,是必须脱除的主要污染物之一。
3.目前,萃取脱酚对单元酚的脱除率较高,可达99%以上,但受到现有萃取剂脱酚能力不足的限制,多元酚的脱除率也仅70%左右,导致最终出水总酚浓度不达指标,仍高达500mg/l。所以,选择合适的萃取剂是提高废水萃取脱酚效率的关键。萃取剂必须考虑其对单元酚和多元酚的溶解度、水溶性以及能耗、价格、操作难易等问题。
技术实现要素:
4.有鉴于此,本发明的目的在于提供一种含酚废水萃取脱酚的方法,该方法的脱酚率较高。
5.本发明提供了一种含酚废水萃取脱酚的方法,包括以下步骤:
6.将含酚废水经脱酸、脱氨和机械杂质处理使废水控制在5~9,先进行一级萃取脱酚;所述一级萃取脱酚采用疏水性离子液体为萃取剂;
7.所述疏水性离子液体具有式ⅰ结构:
[0008][0009]
所述r为乙基或丁基;所述y-为pf
6-或n(tf)
2-;
[0010]
得到的一级萃取脱酚废水进行二级萃取脱酚,所述二级萃取脱酚采用酮-醇协同萃取剂,得到脱酚废水。
[0011]
本发明优选将含酚废水先经重力沉降除油预处理后,再进行脱酸、脱氨、脱除机械杂质处理。脱酸、脱氨在汽提脱酸脱氨塔中进行。
[0012]
在本发明具体实施例中,所述含酚废水为煤化工含酚废水;所述煤化工含酚废水中单元酚的含量为2000~8000mg/l,多元酚的含量为1000~5000mg/l,总氨量为6000~20000mg/l,cod为20000~40000mg/l,ph值为10~12。
[0013]
在本发明中,一级萃取脱酚;所述一级萃取脱酚采用疏水性离子液体为萃取剂;所述疏水性离子液体具有式ⅰ结构:
[0014][0015]
所述r为乙基或丁基;所述y-为pf
6-或n(tf)
2-。
[0016]
在本发明具体实施例中,所述疏水性离子液体选自1-乙基-3-甲基咪唑六氟磷酸盐[emim]pf6、1-丁基-3-甲基咪唑六氟磷酸盐[bmim]pf6、1-乙基-3-甲基咪唑双三氟甲磺酰亚胺盐[emim]n(tf)2和1-丁基-3-甲基咪唑双三氟甲磺酰亚胺盐[bmim]n(tf)2中的一种或多种。
[0017]
在本发明中,所述疏水性离子液体和含酚废水的体积比为1:1~1:4;在本发明中,所述一级萃取脱酚的温度为25~40℃;
[0018]
一级萃取脱酚得到的萃取相ⅰ,进入反萃取塔进行反萃取,得到反萃取相;所述反萃取采用的反萃取剂为乙醚;反萃取在常压下进行,反萃取的温度为25℃。所述反萃取剂和一级萃取相的体积比为1:1~1:4。反萃取相通过减压蒸馏实现乙醚和酚的分离,粗酚进入精制工段,疏水性离子液体萃取剂返回萃取塔循环使用。
[0019]
一级萃取脱酚得到的萃余相ⅰ,进入澄清器,澄清分离出一级萃取剂,即疏水性离子液体萃取剂,循环使用。在本发明中,所述一级萃取脱酚后的废水体积总量的1/3~3/5回流作为煤气洗涤水,剩余废水进行二级萃取脱酚。一级萃取脱酚后废水中总酚含量为550~1000mg/l,单元酚基本脱除。产生的一级萃取脱酚废水和酮-醇协同萃取剂混合,进行二级萃取。
[0020]
一级萃取脱酚后,部分脱酚废水回流作为煤气洗涤水,从而使废水中的酚得到富集,减少煤气洗涤新鲜水用量,同时减少了二级萃取处理量。
[0021]
在本发明中,所述酮-醇协同萃取剂中酮和醇的体积比为3:2~4:1;所述酮选自甲基戊烯酮、甲基丙基酮、甲基异丙基酮和甲基异丁基酮中的一种或多种;所述醇选自正丁醇、仲丁醇、正戊醇和异戊醇中的一种或多种。具体实施例中,所述酮-醇协同萃取剂为体积比3:2的甲基异丁基酮和正丁醇的混合物;或体积比4:1的甲基丙基酮和仲丁醇的混合物;或体积比3:2的甲基戊烯酮和正戊醇的混合物。
[0022]
所述酮-醇协同萃取剂和一级萃取脱酚废水的体积比为1:4~1:15。所述二级萃取脱酚的温度为25~40℃。
[0023]
经二级萃取脱酚后得到的萃取相ⅱ送至酚回收塔,得到的粗酚进入粗酚精制工段。经二级萃取脱酚后得到的萃余相ⅱ进入溶剂回收塔,二级萃取脱酚后的废水中总酚含量小于300mg/l,送至生化处理工段。
[0024]
图1为本发明实施例提供的含酚废水处理的工艺流程示意图,由图1可知:煤化工过程产生的高浓度含酚废水经重力沉降除油预处理后,进入汽提脱酸脱氨塔,经过脱酸脱氨脱除机械杂质后,使废水ph值控制在5~9;脱酸脱氨除机械杂质后的酚水进入萃取一塔,以疏水性离子液体为萃取剂,进行一级萃取脱酚。离子液体萃取剂从上部进入萃取一塔,废水与离子液体萃取剂在塔内逆流接触,完成萃取,萃取相i由萃取塔底部采出进入反萃取塔,萃余相i由塔上部溢流入澄清器;萃余相i在澄清分离出离子液体萃取剂,离子液体萃取剂返回萃取塔一循环使用,一级萃取脱酚废水总量的1/3~3/5回流作为煤气洗涤水,剩余废水进入萃取二塔;反萃取塔内以乙醚为反萃取剂,进行苯酚的反萃取和离子液体的再生,使酚从离子液体相转移到乙醚中,得到反萃取相,离子液体萃取剂返回萃取一塔循环使用;乙醚的沸点远低于酚,反萃取相通过减压蒸馏实现乙醚和酚的分离,粗酚送至粗酚精制工段。
[0025]
一级萃取脱酚废水进入萃取二塔,以第二种溶剂(酮-醇协同萃取剂)为萃取剂,进
行二级萃取脱酚,萃取相ii进入酚回收塔,分离萃取剂二和粗酚。萃余相ii进入溶剂回收塔,回收溶于其中的萃取剂。萃取剂循环使用;脱酚水送入生化处理工段,粗酚送至粗酚精制工段。
[0026]
本发明提供了一种含酚废水萃取脱酚的方法,包括以下步骤:将含酚废水经脱酸、脱氨和机械杂质处理使废水控制在5~9,先进行一级萃取脱酚;所述一级萃取脱酚采用疏水性离子液体为萃取剂;得到的一级萃取脱酚废水进行二级萃取脱酚,所述二级萃取脱酚采用酮-醇协同萃取剂,得到脱酚废水。该方法能实现单元酚和多元酚的高效脱除;处理后废水达到生化处理要求,同时还能降低溶剂回收的能耗和损失。
[0027]
单元酚和多元酚分级萃取,尤其是采用疏水性离子液体作为萃取剂,可以整体上降低溶剂回收损,减少回收蒸汽消耗量。一级萃取脱酚后,部分脱酚废水回流作为煤气洗涤水,从而使废水中的酚得到富集,减少煤气洗涤新鲜水用量,同时减少了二级萃取处理量;萃取率提高的同时,也使萃取剂补加的新鲜萃取剂用量降低。
附图说明
[0028]
图1为本发明实施例提供的含酚废水处理的工艺流程示意图。
具体实施方式
[0029]
为了进一步说明本发明,下面结合实施例对本发明提供的一种含酚废水萃取脱酚的方法进行详细地描述,但不能将它们理解为对本发明保护范围的限定。
[0030]
实施例1
[0031]
煤化工过程产生的高浓度含酚废水经重力沉降除油预处理后,进入汽提脱酸脱氨塔,进行脱酸、脱氨、脱除机械杂质,经过脱酸、脱氨、脱除机械杂质后的废水的ph值控制在5~9,总酚含量6270mg/l,其中,单元酚含量3750mg/l,多元酚含量2520mg/l;
[0032]
脱酸脱氨脱除机械杂质后的含酚废水进入萃取一塔,以疏水性离子液体1-乙基-3-甲基咪唑六氟磷酸盐[emim]pf6为萃取剂,进行一级萃取脱酚;疏水性离子液体和脱酸脱氨脱除机械杂质后的含酚废水的体积比为1:2,一级萃取脱酚的温度为25℃,ph值为8;
[0033]
萃取相i进入反萃取塔,以乙醚为反萃取剂,使酚从离子液体相转移到乙醚相中,反萃取的温度为25℃,反萃取剂和萃取相ⅰ的体积比为1:1,得到反萃取相,反萃取相通过减压蒸馏实现乙醚和酚的分离,粗酚进入精制工段,疏水性离子液体萃取剂返回萃取一塔循环使用;
[0034]
萃余相i进入澄清器,澄清分离出疏水性离子液体萃取剂,循环使用;
[0035]
一级萃取脱酚废水进入萃取二塔,以酮-醇协同萃取剂为萃取剂,进行二级萃取脱酚;酮-醇协同萃取剂为体积比3:2的甲基异丁基酮和正丁醇的混合物,酮-醇协同萃取剂与一级萃取脱酚废水的体积比为1:5.5;二级萃取脱酚的温度为25℃,ph值为8,得到二级脱酚废水,总酚含量为190mg/l,单元酚20mg/l,多元酚170mg/l,单元酚脱除率99.47%,多元酚脱除率93.25%,总酚脱除率97.29%;
[0036]
二级脱酚废水送入生化处理工段,粗酚送至粗酚精制工段。
[0037]
实施例2
[0038]
煤化工过程产生的高浓度含酚废水经重力沉降除油预处理后,进入汽提脱酸脱氨
塔,进行脱酸、脱氨、脱除机械杂质,经过脱酸、脱氨、脱除机械杂质后的废水的ph值控制在5~9,总酚含量11400mg/l,其中,单元酚含量6500mg/l,多元酚含量4900mg/l;
[0039]
脱酸脱氨脱除机械杂质后的含酚废水进入萃取一塔,以疏水性离子液体1-丁基-3-甲基咪唑六氟磷酸盐[bmim]pf6为萃取剂,进行一级萃取脱酚;疏水性离子液体和脱酸脱氨脱除机械杂质后的含酚废水的体积比为1:2.5,一级萃取脱酚的温度为30℃,ph值为7;
[0040]
萃取相i进入反萃取塔,以乙醚为反萃取剂,使酚从离子液体相转移到乙醚相中,反萃取的温度为25℃,反萃取剂和萃取相ⅰ的体积比为1:2,得到反萃取相,反萃取相通过减压蒸馏实现乙醚和酚的分离,粗酚进入精制工段,疏水性离子液体萃取剂返回萃取一塔循环使用;
[0041]
萃余相i进入澄清器,澄清分离出疏水性离子液体萃取剂,循环使用;
[0042]
一级萃取脱酚废水进入萃取二塔,以酮-醇协同萃取剂为萃取剂,进行二级萃取脱酚;酮-醇协同萃取剂为体积比4:1的甲基丙基酮和仲丁醇的混合物,酮-醇协同萃取剂与一级萃取脱酚废水的体积比为1:8;二级萃取脱酚的温度为30℃,ph值为7得到二级脱酚废水,总酚285mg/l,单元酚26mg/l,多元酚259mg/l,单元酚脱除率99.60%,多元酚脱除率94.71%,总酚脱除率97.73%;
[0043]
二级脱酚废水送入生化处理工段,粗酚送至粗酚精制工段。
[0044]
实施例3
[0045]
煤化工过程产生的高浓度含酚废水经重力沉降除油预处理后,进入汽提脱酸脱氨塔,进行脱酸、脱氨、脱除机械杂质,经过脱酸、脱氨、脱除机械杂质后的废水的ph值控制在5~9,总酚含量9630mg/l,其中,单元酚含量5750mg/l,多元酚含量3880mg/l;
[0046]
脱酸脱氨脱除机械杂质后的含酚废水进入萃取一塔,以疏水性离子液体1-乙基-3-甲基咪唑双三氟甲磺酰亚胺盐[emim]n(tf)2为萃取剂,进行一级萃取脱酚;疏水性离子液体和脱酸脱氨脱除机械杂质后的含酚废水的体积比为1:3,一级萃取脱酚的温度为35℃,ph值为6;
[0047]
萃取相i进入反萃取塔,以乙醚为反萃取剂,使酚从离子液体相转移到乙醚相中,反萃取的温度为25℃,反萃取剂和萃取相ⅰ的体积比为1:3,得到反萃取相,反萃取相通过减压蒸馏实现乙醚和酚的分离,粗酚进入精制工段,疏水性离子液体萃取剂返回萃取一塔循环使用;
[0048]
萃余相i进入澄清器,澄清分离出疏水性离子液体萃取剂,循环使用;
[0049]
一级萃取脱酚废水进入萃取二塔,以酮-醇协同萃取剂为萃取剂,进行二级萃取脱酚;酮-醇协同萃取剂为体积比3:2的甲基戊烯酮和正戊醇的混合物,酮-醇协同萃取剂与一级萃取脱酚废水的体积比为1:12;二级萃取脱酚的温度为35℃,ph值为6,得到二级脱酚废水,总酚95mg/l,单元酚15mg/l,多元酚80mg/l,单元酚脱除率99.74%,多元酚脱除率97.94%,总酚脱除率99.17%;
[0050]
二级脱酚废水送入生化处理工段,粗酚送至粗酚精制工段。
[0051]
由以上实施例可知,本发明提供了一种含酚废水萃取脱酚的方法,包括以下步骤:将含酚废水经脱酸、脱氨和机械杂质处理使废水控制在5~9,先进行一级萃取脱酚;所述一级萃取脱酚采用疏水性离子液体为萃取剂;得到的一级萃取脱酚废水进行二级萃取脱酚,所述二级萃取脱酚采用酮-醇协同萃取剂,得到脱酚废水。该方法能实现单元酚和多元酚的
高效脱除率;处理后废水达到生化处理要求,同时还能降低溶剂回收的能耗和损失。实验结果表明:单元酚的脱除率高达99.74%,多元酚的脱除率高达97.94%,总酚的脱除率高达99.17%。
[0052]
以上所述仅是本发明的优选实施方式,应当指出,对于本技术领域的普通技术人员来说,在不脱离本发明原理的前提下,还可以做出若干改进和润饰,这些改进和润饰也应视为本发明的保护范围。
再多了解一些
本文用于创业者技术爱好者查询,仅供学习研究,如用于商业用途,请联系技术所有人。